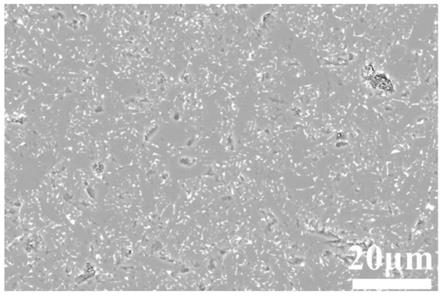
1.本发明属于陶瓷材料制备技术领域,涉及一种两步烧结制备高强高导热氮化硅陶瓷的方法。
背景技术:2.氮化硅陶瓷具有绝缘、耐化学腐蚀、优异的力学性能和热性能,在冶金、机械、航空航天和医学等领域有广泛应用。特别是高强、高导热和优异的抗热震性,氮化硅非常适合用在纯电动和混合电动汽车上半导体功率器件的散热基板,像比亚迪和丰田普锐斯等车用igbt散热模块都已采用氮化硅陶瓷散热基板。
3.氮化硅气压烧结方法是在烧结过程中附加0.9~10mpa氮气压力,一方面抑制氮化硅高温下的分解,另一方面促进陶瓷致密化。气压烧结可有效避免像热压烧结或放电等离子烧结因轴向压力造成的晶粒定向排列,不会引起陶瓷各向性能不同;同时,气压烧结可大批量制备复杂零部件。因此,高导热氮化硅陶瓷多采用气压烧结的方式。影响氮化硅陶瓷导热性能的三个主要因素为致密度、晶格氧含量和第二相含量。如果陶瓷致密度低,内部气孔多形成的绝热区严重影响传热;氧进入氮化硅晶格中形成晶格畸变,成为声子的传输散射中心,进而降低陶瓷热导;而第二相本身热导非常低(约1w/m
·
k),较多第二相不仅影响陶瓷热导,高温下也会造成陶瓷耐氧化性和强度的恶化。但共价键为主的氮化硅在烧结过程中难以致密化,往往需要加入特定的烧结助剂,利用烧结助剂与氮化硅表面二氧化硅或氮化硅本身形成低温液相,以此促进陶瓷致密化。但过多液相量会造成制品收缩不均匀;且高温时液相的挥发也会形成气孔,造成产品不致密;陶瓷第二相含量多也会影响后续表面金属化。因此,控制第二相含量是获得高强高导热氮化硅陶瓷的关键。
4.研究证明,稀土氧化物和氧化镁作为复合烧结助剂可制备高导热氮化硅陶瓷,利用稀土氧化物不仅可防止晶界相中的氧进入晶格,且其强固氧能力可减少氮化硅晶格内氧含量,而氧化镁可与氮化硅表面二氧化硅或氮化硅本身形成低温液相,以此促进陶瓷致密化。但目前市场中氮化硅粉体氧含量多数大于1.0wt%,烧结助剂的添加量尤为重要。烧结助剂含量低,液相量少不能达到致密化目的,稀土氧化物的固氧效果得不到体现;烧结助剂含量多,形成过多液相量会造成制品收缩不均匀,陶瓷致密度低、第二相含量高造成陶瓷热导率低。氧化镁与二氧化硅可在约1280℃反应,形成低温液相(mgsio3或mg2sio4)促进反应,在略高的温度(约1350℃)下,sio2在mgsio3或mg2sio4活度较高,mgsio3或mg2sio4会以气相形式蒸发。因此,通过调控烧结助剂含量,并以烧结助剂本身的作用机理进行烧结前处理,降低氧含量、控制陶瓷烧结过程中收缩,有望获得高致密、高强度氮化硅陶瓷的同时提高导热性能。
技术实现要素:5.针对现有技术中存在的问题,本发明提出一种两步烧结制备高强高导热氮化硅陶瓷的方法。通过第一步对坯体的低温、常压、通氮气的预处理,利用烧结助剂本身的作用机
理,在烧结前期降低氮化硅氧含量,在保证陶瓷致密化同时减少第二相含量,以此获得高致密、高强度氮化硅陶瓷的同时提高导热性能。另外,在整个过程是烧结助剂在起作用,并没有引入其他物质,工艺流程简单,成本低。
6.为解决上述问题,本发明所采用的技术方案如下:
7.一种两步烧结制备高强高导热氮化硅陶瓷的方法,包括以下步骤:
8.(1)将氮化硅粉体、烧结助剂和有机溶剂混合均匀,其氮化硅粉体与烧结助剂的质量比为95~90:10~5。
9.(2)将步骤(1)中混合料进行喷雾造粒,得到球形造粒粉。
10.(3)将步骤(2)中造粒粉称量、模压、等静压,经脱脂后再进行两步烧结。
11.优选地,步骤(1)中所述氮化硅粉体金属杂质含量小于1wt%,α相含量大于90wt%,氧含量为0.6~2.0wt%。
12.优选地,步骤(1)中所述烧结助剂为稀土氧化物和碱土金属氧化物混合;其中稀土氧化物为氧化镱、氧化钇、氧化铌或氧化镧中的一种,其含量是氮化硅粉体的3~6wt%;碱土金属氧化物为氧化镁,其含量是氮化硅粉体氧含量的2.5~4倍。
13.优选地,步骤(2)中所述的造粒粉粒径为30~120μm。
14.优选地,步骤(3)中所述两步烧结包括:第一步将脱脂后坯体在1300℃~1450℃常压预处理1~5h,并伴有流动的氮气;第二步是在1800℃~1950℃、0.9~10mpa氮气压力下进行高温烧结5~20h。
15.本发明技术关键点在于:
16.1、本发明根据氮化硅粉体氧含量调节氧化镁烧结助剂添加量。氮化硅陶瓷中的第二相主要是由氮化硅粉体表面二氧化硅与烧结助剂反应形成的,因此氮化硅粉体氧含量越高,所形成的第二相含量越多。本发明主要针对如何减少第二相含量。氧化镁与二氧化硅可在1280℃反应,可形成低温液相(mgsio3或mg2sio4)促进反应,在略高的温度(约1350℃)下,sio2在mgsio3或mg2sio4活度较高,mgsio3或mg2sio4会以气相形式蒸发。因此本发明所述第一步预处理是利用氧化镁降低二氧化硅含量,但没有氧化镁,氮化硅烧结难以致密化。针对氧含量为0.6~2.0wt%氮化硅粉体,氧化镁含量是氮化硅粉体氧含量的2.5~4倍,在保证降低二氧化硅含量同时确保陶瓷致密化。所制备陶瓷第二相含量减少,相应的总氧含量降低,热导率提高。
17.2、发明人通过检索并对比3篇文件,表述本发明独特之处。
18.其中对比文件1、cn201310129987.2一种制备高热导率、高强度氮化硅陶瓷的方法烧结助剂以yb2o3为主烧结助剂,以y2o3、lu2o3、nd2o3、er2o3、mgo中的至少一种为辅烧结助剂的混合物。且坯体是埋入si3n4粉体中进行烧结,si3n4埋粉剂一方面是为增加氮化硅分解的饱和蒸气压,抑制氮化硅在烧结过程分解;另一方面可作为高温下吸收挥发的液相。但薄壁复杂零件不适合埋粉烧结,这样会造成零件收缩不均匀,导致零件开裂等现象。本发明是经过前处理后进行气压烧结,可批量制备薄壁、异形零部件。
19.对比文件2、cn201910318851.3提供了一种高强度氮化硅陶瓷的低温制备方法,使用烧结助剂种类与本发明不同;采用放电等离子烧结,其本身可快速制备高致密度氮化硅陶瓷,但陶瓷导热性能并不高,本发明是在获得高致密度、高强度氮化硅陶瓷的同时,拥有高导热性能;且采用放电等离子烧结需要施加轴向压力,不能批量制备大尺寸、异形零部
件,需要进行后续的机加工,增加工序和成本。
20.对比文件3、cn201710335834.1一种高热导率、高强度氮化硅陶瓷材料及其制备方法,以si3n4粉体为原料,通过选择hfo2、hfn和zrn中的一种作为烧结助剂,并加入稀土氧化物和mgo,选取了至少三种物质作为烧结助剂,与本专利相比,烧结助剂多了hfo2、hfn和zrn中的至少一种,增加了制备成本;hfo2、hfn和zrn的加入为了控制晶界相组分与微观结构,增强β
‑
si3n4晶粒的双峰分布,与本发明具有根本性的不同。
21.另外对比文件3、cn201710335834.1中提到将所得素坯先在1300~1550℃下进行氮化处理,这是因为选取硅粉或含有硅粉的si3n4粉体,如果直接进行烧结,其硅是作为杂质被引入,进行氮化处理是为了将硅粉氮化为氮化硅,所述原料不同,处理的作用不同,且本发明氧化镁含量是氮化硅粉体氧含量的2.5~4倍,是与所选氮化硅粉体的氧含量息息相关的,这样才能在保证减少液相量的同时获得高致密氮化硅陶瓷,以此有效提高导热性能。制备得到高强高导热氮化硅陶瓷。
22.本发明的有益效果:通过第一步对坯体的低温、常压、通氮气的预处理,这个过程可消除部分二氧化硅,在烧结过程中液相含量相对减少;通过第二步气压烧结,获得高致密氮化硅陶瓷同时,有效降低氧含量和第二相含量,显著提高陶瓷热导率;在整个过程中是烧结助剂在起作用,并没有引入其他物质,工艺流程简单,成本低。
附图说明
23.图1为对比例中未做预处理所制备的氮化硅陶瓷微观组织照片;
24.图2为实施例1中所制备的氮化硅陶瓷微观组织照片。
具体实施方式
25.为更进一步阐述本发明为达成预定发明目的所采取的技术手段及功效,以下结合较佳实施例,对依据本发明提出的一种两步烧结制备高强高导热氮化硅陶瓷的方法其具体实施方式、步骤、特征详细说明如后。
26.实施例1
27.1.称取920g氧含量为1.0wt%的氮化硅粉体、24g氧化镁和56g氧化镱,在无水乙醇中与粘结剂进行球磨,混合均匀后获得浆料;
28.2.将上述浆料进行喷雾造粒,获得造粒粉粒径为60μm;
29.3.将造粒料压制成100
×
100
×
2mm的方形板,再进行200mpa等静压15min,得到生坯。
30.4.将生坯在600℃进行脱脂;随后进行两步烧结,以5℃/min升至1350℃保温2h,伴有1l/min氮气流速;继续升温至1900℃保温5h,氮气压力升至1.2mpa;
31.5.将烧结制品进行磨、抛后获得最终氮化硅陶瓷。其陶瓷热导率为96.4w/m
·
k,抗弯强度为792mpa。
32.实施例2
33.1.称取920g氧含量为1.0wt%的氮化硅粉体、24g氧化镁和56g氧化镱,在无水乙醇中与粘结剂进行球磨,混合均匀后获得浆料;
34.2.将上述浆料进行喷雾造粒,获得造粒粉粒径为60μm;
35.3.将造粒料压制成100
×
100
×
2mm的方形板,再进行200mpa等静压15min,得到生坯。
36.4.将生坯在600℃进行脱脂;随后进行两步烧结,以5℃/min升至1350℃保温2h,伴有1l/min氮气流速;继续升温至1900℃保温10h,氮气压力升至1.2mpa;
37.5.将烧结制品进行磨、抛后获得最终氮化硅陶瓷。其陶瓷热导率为108.6w/m
·
k,抗弯强度为758mpa。
38.实施例3
39.1.称取920g氧含量为1.0wt%的氮化硅粉体、24g氧化镁和56g氧化钇,在无水乙醇中与粘结剂进行球磨,混合均匀后获得浆料;
40.2.将上述浆料进行喷雾造粒,获得造粒粉粒径为80μm;
41.3.将造粒料压制成100
×
100
×
2mm的方形板,再进行200mpa等静压15min,得到生坯;
42.4.将生坯在600℃进行脱脂;随后进行两步烧结,以5℃/min升至1350℃保温2h,伴有1l/min氮气流速;继续升温至1900℃保温5h,氮气压力升至1.2mpa;
43.5.将烧结制品进行磨、抛后获得最终氮化硅陶瓷。其陶瓷热导率为95.2w/m
·
k,抗弯强度为796mpa。
44.实施例4
45.1.称取920g氧含量为0.6wt%的氮化硅粉体、24g氧化镁和56g氧化钇,在无水乙醇中与粘结剂进行球磨,混合均匀后获得浆料;
46.2.将上述浆料进行喷雾造粒,获得造粒粉粒径为80μm;
47.3.将造粒料压制成100
×
100
×
2mm的方形板,再进行200mpa等静压15min,得到生坯;
48.4.将生坯在600℃进行脱脂;随后进行两步烧结,以5℃/min升至1450℃保温2h,伴有1l/min氮气流速;继续升温至1900℃保温5h,氮气压力升至1.2mpa;
49.5.将烧结制品进行磨、抛后获得最终氮化硅陶瓷。其陶瓷热导率为101.1w/m
·
k,抗弯强度为787mpa。
50.对比例1(未做预处理)
51.将实施例1脱脂后的坯体直接升温至1900℃保温5h,氮气压力为1.2mpa。不同实施例1
‑
4及对比例1中氮化硅陶瓷的氧含量、致密度、热导率和抗弯强度见表1。
52.表1氮化硅陶瓷的氧含量、致密度、热导率和抗弯强度
[0053][0054]
从表1可知,本发明所述一种两步烧结制备高强高导热氮化硅陶瓷的方法,在第一步低预处理中,利用烧结助剂与氮化硅表面二氧化硅形成低熔点相,通过低温、常压、通氮气条件,可降低烧结前坯体氧含量,在保证陶瓷致密化同时减少第二相含量,以此获得高致密、高强度氮化硅陶瓷的同时提高导热性能。
[0055]
以上所述,仅是本发明的较佳实施例而已,并非对本发明作任何形式上的限制,虽然本发明已以较佳实施例揭露如上,然而并非用以限定本发明,任何熟悉本专业的技术人员,在不脱离本发明技术方案范围内,当可利用上述揭示的方法及技术内容做出些许的更动或修饰为等同变化的等效实施例,但凡是未脱离本发明技术方案的内容,依据本发明的技术实质对以上实施例所作的任何修改、等同变化与修饰,均仍属于本发明技术方案的范围内。