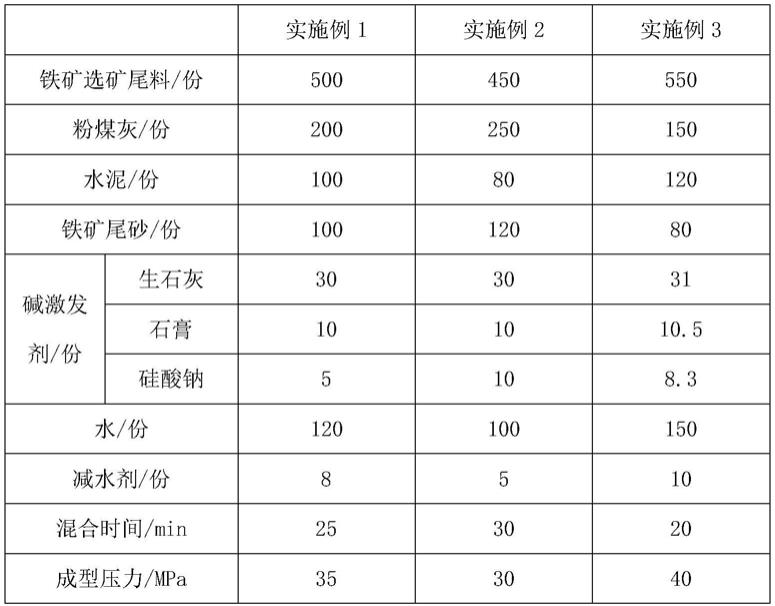
1.本发明属于建筑材料技术领域,具体涉及一种碱激发高掺量尾泥水泥砖及其制备方法。
背景技术:2.现代社会经济的高速发展、工业化的加快推进、城镇化水平的提高及人们消费水平的升级等各种因素导致了现代社会对钢铁需求的快速增长,钢铁工业随之取得了突飞猛进的发展。但是,由于铁矿的大量开采,铁矿开采后产生的尾料矿渣也日益增多。目前对铁矿尾料的利用率较低,大部分的铁矿尾料被丢弃、堆存,而铁矿尾料的丢弃、堆存不仅占用了大量的土地资源,同时也会给周围的生态环境造成很大伤害,而且还需投入大量的人力、财力对其进行处理;其堆放边坡也存在坍塌风险,存在安全隐患。因此,如何进一步实现对铁矿尾料更大程度的回收与利用,是摆在我们面前亟待解决的问题。
3.水泥砖是指利用粉煤灰、煤渣、煤矸石、尾矿渣、化工渣或者天然砂、海涂泥等(以上原料的一种或数种)作为原料,用水泥做凝固剂,不经高温煅烧而制造的一种新型墙体材料。水泥砖因其自重较轻,无须烧制,外形完好、漂亮,用电厂的污染物粉煤灰做材料,具有节能、环保等优势而受到了日益广泛的重视。现有水泥砖制备工艺中采用铁矿尾料作为原料时,其添加量较少,一般含量仅为10wt%左右,之所以没有大量添加铁矿尾料,是由于因为铁矿尾料含量较高时,会显著降低胶凝性能,无法很好地实现胶凝或者即使胶凝得到了水泥砖,其抗压强度和抗裂强度也均较低,不能很好地被应用,因此,开发一种可增大铁矿尾料掺杂量、同时能够使所得水泥砖具有高力学性能的水泥砖制备工艺,无论是对于水泥砖的制备,还是对于铁矿尾料的合理利用,均具有重大意义。
技术实现要素:4.为克服现有技术存在的上述技术问题,本发明提供了一种碱激发高掺量尾泥水泥砖及其制备方法,通过采用合适的碱激发剂对铁矿尾料进行激发,能使其转变为具有较佳胶结性能的物质,因此能在保证所得水泥砖具有良好性能的基础上,显著增加水泥砖原料中铁矿尾料的掺加量,促进铁矿尾料的开发利用。
5.为实现上述目的,本发明提供了如下技术方案:
6.本发明提供了一种碱激发高掺量尾泥水泥砖,原料按重量份计包括:尾泥450~550份、粉煤灰150~250份、水泥80~120份、铁矿尾砂80~120份、水100~150份、碱激发剂40~50份及减水剂5~10份;
7.所述尾泥为铁矿选矿尾料;所述碱激发剂由生石灰、石膏及硅酸钠组成。
8.进一步地,所述碱激发剂中,生石灰、石膏及硅酸钠的质量比为3∶1∶(0.5~1)。
9.进一步地,所述粉煤灰的cao含量≥6wt%,sio2含量≥48wt%,吸水率≥95%。
10.进一步地,所述水泥为p.o.42.5水泥。
11.进一步地,所述减水剂的减水率≥20.0%。
12.进一步地,所述石膏中caso4的含量≥82wt%;所述生石灰中cao的含量≥85wt%。
13.本发明还提供了一种上述碱激发高掺量尾泥水泥砖的制备方法,包括以下步骤:按重量份称取各原料并进行混合得到胶凝材料,之后成型即得所述碱激发高掺量尾泥水泥砖。
14.进一步地,所述混合在搅拌下进行,时间为20~30min,所述成型压力为30~40mpa。
15.与现有技术相比,本发明具有以下有益效果:
16.本发明利用生石灰、石膏及硅酸钠配合得到碱激发剂,能有效激发铁矿选矿尾料中的有效成分,使其转变为具有较佳胶结性能的物质,进而使其能与粉煤灰、铁矿尾砂和水泥有效胶凝,且得到的水泥砖的力学性能优异。
17.本发明在制备水泥砖时,掺入大量铁矿尾料,将其变废为宝,且所得水泥砖对人体和环境无毒无害;本发明可高效促进对铁矿尾料的回收、利用,有效缓解铁矿尾料对土地及生态环境的污染,消除安全隐患,还可以节省大量资金,实现资源效益、经济效益、社会效益和环境效益的有效统一。
具体实施方式
18.现详细说明本发明的多种示例性实施方式,该详细说明不应认为是对本发明的限制,而应理解为是对本发明的某些方面、特性和实施方案的更详细的描述。应理解本发明中所述的术语仅仅是为描述特别的实施方式,并非用于限制本发明。
19.另外,对于本发明中的数值范围,应理解为还具体公开了该范围的上限和下限之间的每个中间值。在任何陈述值或陈述范围内的中间值以及任何其他陈述值或在所述范围内的中间值之间的每个较小的范围也包括在本发明内。这些较小范围的上限和下限可独立地包括或排除在范围内。
20.除非另有说明,否则本文使用的所有技术和科学术语具有本发明所述领域的常规技术人员通常理解的相同含义。虽然本发明仅描述了优选的方法和材料,但是在本发明的实施或测试中也可以使用与本文所述相似或等同的任何方法和材料。本说明书中提到的所有文献通过引用并入,用以公开和描述与所述文献相关的方法和/或材料。在与任何并入的文献冲突时,以本说明书的内容为准。
21.在不背离本发明的范围或精神的情况下,可对本发明说明书的具体实施方式做多种改进和变化,这对本领域技术人员而言是显而易见的。由本发明的说明书得到的其他实施方式对技术人员而言是显而易见的。本发明说明书和实施例仅是示例性的。
22.关于本文中所使用的“包含”、“包括”、“具有”、“含有”等等,均为开放性的用语,即意指包含但不限于。
23.以下实施例中所采用的铁矿选矿尾料的主要成分及质量百分比为:sio2(38.12%),al2o3(13.24%),mgo(8.05%),cao(31.25%),so3(1.67%),fe2o3(2.31%),事先对其进行粉碎、磨细,得到细度为300~400m2/kg的粉状尾料后备用;
24.所采用的水泥为市售p.o.42.5水泥,所采用的粉煤灰吸水量范围为89~130%,平均吸水量为106%,其密度范围为1.95~2.87g/cm3,平均密度为2.16g/cm3,其sio2含量为53.24wt%、cao含量为8.4wt%、al2o3含量为27.1wt%、fe2o3含量为4.12wt%、mgo含量为
3.01wt%;所采用的铁矿尾砂为铁矿采矿粗尾砂经磨细得到的,粒径范围为0.3~0.5mm;所采用的减水剂为聚羧酸高效减水剂,是由山东省莱阳市宏祥建筑外加剂厂生产,其减水率≥23%,活性成分含量≥90%,所采用的石膏中caso4的含量为85.7wt%;所采用的生石灰中cao的含量为88.1wt%;
25.以下不再重复描述。
26.实施例1~3
27.碱激发高掺量尾泥水泥砖的制备,包括以下步骤:
28.将生石灰、石膏及硅酸钠混合得到碱激发剂,之后将碱激发剂与铁矿选矿尾料、粉煤灰、水泥、铁矿尾砂、减水剂和水搅拌混合,得到胶凝材料,然后将其放入模具中,压制成型,即得碱激发高掺量尾泥水泥砖。其中实施例1~3所采用的各原料的用量、搅拌混合时间及成型压力如表1所示:
29.表1
[0030][0031]
实施例4
[0032]
各原料用量同实施例1,制备步骤为:先将铁矿选矿尾料、粉煤灰、碱激发剂和20份水混合搅拌15min,再加入水泥、铁矿尾砂、剩余水和减水剂,搅拌混合20min。
[0033]
实施例5
[0034]
同实施例1,区别在于,在碱激发剂中还加入表面活性剂月桂醇醚硫酸铵5份。
[0035]
实施例6
[0036]
同实施例1,区别在于,在碱激发剂中还加入远红外线粉体材料电气石粉(规格:3000目,购自灵寿县丰聚矿产品加工厂)5份。
[0037]
实施例7
[0038]
同实施例5,区别在于,在实施例5的碱激发剂中还加入远红外线粉体材料电气石
粉(规格:3000目,购自灵寿县丰聚矿产品加工厂)5份。
[0039]
对比例1
[0040]
同实施例1,区别在于,碱激发剂中不加入石膏。
[0041]
对比例2
[0042]
同实施例1,区别在于,碱激发剂中不加入硅酸钠。
[0043]
效果验证
[0044]
将实施例1~7及对比例1~2所得的水泥砖置于标准养护室中养护,检测3d、7d及28d的抗压强度,结果如表2所示;养护28d后,对其劈裂抗拉强度及抗折强度进行检测,结果如表2所示:
[0045]
表2
[0046][0047]
由表2可以看出,本发明中的碱激发剂配方合理,能使大量掺杂铁矿选矿尾料的混合材料有效凝结,且所得水泥砖的早期强度及后期强度均较高,抗裂性能及抗折性能优异;且首先对粉煤灰、铁矿选矿尾料及碱激发剂等进行预混合,之后再与水泥、铁矿尾砂、减水剂混合所得的水泥砖的强度更佳,这是由于预混合过程水用量少,得到的混合体系碱性大,能够更高效地发挥碱激发作用,更好地促使铁矿尾料中si
‑
o及al
‑
o键的断裂,更有利于后期与水泥的胶凝;预混合后再进行混合可以提高和易性,同时又可以合理调控混合物的碱性,以确保尾泥粉煤灰的持续激发及其与水泥水化反应的匹配,利于水泥砖成形;而且,在碱激发剂中额外加入表面活性剂月桂醇醚硫酸铵可提高碱激发剂的激发效果,而额外添加远红外线粉体材料电气石粉时,提高效果不明显,但是,同时加入表面活性剂月桂醇醚硫酸铵和远红外线粉体材料电气石粉时,效果却显著提升,说明二者配合能更好地激发铁矿尾料中的有效成分,使所得水泥砖的力学性能更佳。
[0048]
以上所述,仅为本发明较佳的具体实施方式,本发明的保护范围并不局限于此,任何熟悉本技术领域的技术人员在本发明披露的技术范围内,根据本发明的技术方案及其发明构思加以等同替换或改变,都应涵盖在本发明的保护范围内。