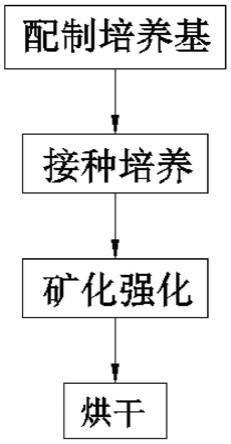
1.本发明涉及生物技术领域,更具体地说,它涉及一种再生混凝土的强化方法。
背景技术:2.2018年,全球水泥总产量近40亿吨。硅酸盐水泥(即国外通称的波特兰水泥)的生产过程会消耗大量的能源和资源,并排放大量的灰尘和废气,对生态环境造成严重的影响。因此,亟需开发节能、环保、耐久的绿色水泥材料。生物水泥是利用微生物诱导矿化形成矿物的凝胶化,由于其环境友好性等优势已成为国内外多领域的研究热点。其中最被熟知和广泛研究的当属微生物诱导碳酸钙矿化micp。而在碳酸钙的微生物矿化中,通过脲酶水解尿素从而产生矿化产物的模型是最简单且被研究最为深入的一种,并经常被用于micp的应用技术中。巴氏芽孢杆菌凭借其高效的脲酶活性,成为micp相关研究中最为热门的细菌之一。
3.巴氏芽孢杆菌属于芽孢杆菌目球菌科芽孢八叠球菌属(也被称为巴氏芽孢八叠球菌),是一种从土壤中分离出的非致病性革兰氏阳性菌。巴氏芽孢杆菌细胞外形呈杆状,长度约为2~3μm,具有很强的生存能力,能够在15~37℃下生长,并能够在缺少营养物质时以芽孢的形式继续存活,其芽孢呈圆形,直径约为0.5~1.5μm。巴氏芽孢杆菌形成芽孢的特性成为众多学者将其开发为自修复混凝土(水泥)的核心要素之一。
4.目前,市场上已经出现了将巴氏芽孢杆菌应用在再生混凝土的案例,但是普遍存在巴氏芽孢杆菌培养过程繁琐,不能连续培养,且再生混凝土强化效果欠佳等问题。
技术实现要素:5.针对现有技术存在的不足,本发明的目的在于提供一种再生混凝土的强化方法,具有可连续培养、工艺简单、强化效果较好的优点。
6.为实现上述目的,本发明提供了如下技术方案:
7.一种再生混凝土的强化方法,包括以下步骤:
8.s1、配制培养基
9.培养基由以下组分及其浓度组成:酵母提取物5
‑
10g/l、大豆蛋白胨5
‑
15g/l、葡萄糖10
‑
30g/l、硫酸铵3
‑
8g/l、一水硫酸镁10
‑
15mg/l、氯化镍六水合物15
‑
20mg/l;称取上述组分,并用0.5mol/l氢氧化钠溶液调制ph值为8.0,配制2.5l培养基装于容积5l的发酵罐并升温至120℃消毒,保温15min,冷却至30℃,得到培养基;
10.s2、接种培养
11.按接种量0.5
‑
2.0%将巴氏芽孢杆菌种子液接入培养基中,在30℃、搅拌转速180rpm下恒温培养3
‑
7天;通入压缩空气好氧培养,培养前期通气比为1:0.5(v/v.min),当相对溶解氧低于50%时,提高通气比至1:1(v/v.min)以上,并开始连续流加补料质量浓度为25%的葡萄糖液;调节压缩空气流量保持相对溶解氧30%以上,当相对溶解氧不断上升时,停止补料,培养全程流加氨水恒定ph值8.0,培养结束后,得到巴氏芽孢杆菌培养液;将
巴氏芽孢杆菌培养液稀释至od600为0.6
‑
1.2,待用;
12.s3、矿化强化
13.将混凝土再生颗粒通过步骤s2中稀释后的巴氏芽孢杆菌培养液浸泡1
‑
3h,然后进行矿化处理,矿化过程中,通过料液泵循环巴氏芽孢杆菌培养液,同时加入尿素和硝酸钙,从而得到含尿素和硝酸钙浓度均为0.6
‑
0.9mol/l的矿化溶液,矿化溶液温度为25
‑
30℃;
14.s4、烘干
15.将步骤s3得到的矿化溶液进行烘干处理,得到含水率为8
‑
9%的再生矿化颗粒。
16.进一步优选为:在步骤s2中,葡萄糖液每小时流加补料量为50
‑
100ml/2.5l培养基,共流加补料6
‑
10h。
17.进一步优选为:在步骤s1中,所述培养基装液量为50%。
18.进一步优选为:在步骤s1中,所述发酵罐包括罐体、磁力搅拌装置、灭菌灯、驱动机构和设置在所述罐体一侧的箱门,所述罐体上设置有蒸汽管和排气阀,所述蒸汽管由上往下插入所述罐体内,所述蒸汽管圆周表面开设有出气孔,所述磁力搅拌装置安装在所述罐体底部;
19.所述灭菌灯包括第一灭菌灯和第二灭菌灯,所述第一灭菌灯和第二灭菌灯分别位于所述蒸汽管和所述罐体侧壁之间,所述驱动机构用于驱动所述第一灭菌灯和所述第二灭菌灯相互靠近或远离。
20.进一步优选为:所述驱动机构包括导向杆、固定板、移动台、活动盘、连杆和气缸;
21.所述移动台包括第一移动台和第二移动台,所述第一灭菌灯安装在所述第一移动台上,所述第二灭菌灯安装在所述第二移动台上,所述导向杆为竖直设置且两端分别固定在所述罐体的侧壁上,所述第一移动台和所述第二移动台分别与所述导向杆滑动配合;
22.所述固定板固定在所述导向杆中部,所述第一移动台和所述第二移动台分别位于所述固定板的相对两侧,所述固定板在靠近所述蒸汽管一侧设置有转轴,所述转动一端固定在所述固定板上,另一端穿过所述活动盘中部,所述连杆包括第一连杆和第二连杆,所述第一连杆一端与所述第一移动台转动连接,另一端与所述活动盘转动连接,所述第二连杆一端与所述第二移动台转动连接,另一端与所述活动盘转动连接,所述第一连杆和所述第二连杆分别连接在所述活动盘两端;
23.所述气缸固定在所述罐体顶部,所述气缸包括活塞杆,所述气缸活塞杆与所述固定板固定。
24.进一步优选为:所述第一灭菌灯和所述第二灭菌灯均设置有两个,两个所述第一灭菌灯和两个所述第二灭菌灯分别位于所述蒸汽管相对两侧。
25.进一步优选为:所述出气孔设置有多个,多个所述出气孔均布在所述蒸汽管表面。
26.进一步优选为:所述罐体俯视投影为圆形,所述蒸汽管为竖直设置且插入所述罐体底部。
27.综上所述,本发明具有以下有益效果:本发明提供的培养基中加入有利于培养物吸收的镁离子,有利于巴氏芽孢杆菌对金属离子的吸收,具有促进生长的作用。本发明提供的培养基中加入大豆蛋白胨、葡萄糖,有助于糖类、蛋白及维生素的快速吸收,从而促进巴氏芽孢杆菌的快速繁殖和生长。本发明提供的巴氏芽孢杆菌高密度培养方法,得到的巴氏芽孢杆菌芽孢形成率可在95%以上,芽孢密度最低为1.5
×
10
10
cfu/ml,且具有连续性好、工
艺简单、操作方便的优点,便于大规模培养。巴氏芽孢杆菌能够分泌高活性的脲酶,凭借其高效的脲酶活性催化细菌内部的尿素分解,迅速提高细菌周围微环境的碳酸根浓度和ph值;其次,巴氏芽孢杆菌表面(包括细胞壁及胞外聚合物)比非矿化细菌具有更多的表面负电荷,对阳离子有更强的吸附作用,因此环境中带有正电荷的ca
2+
能够大量吸附于巴氏芽孢杆菌表面,在高浓度的碳酸根和碱性条件下,ca
2+
就会以细胞为晶核,沉降形成caco3结晶,因此巴氏芽孢杆菌能够诱导碳酸钙沉淀,强化矿化混凝土再生颗粒(细骨料等)。
附图说明
28.图1是实施例的流程框图,主要用于体现巴氏芽孢杆菌的高密度培养方法;
29.图2是实施例的结构示意图,主要用于体现发酵罐的内部结构;
30.图3是实施例的结构示意图,主要用于体现驱动机构的结构。
31.图中,1、罐体;2、出气孔;3、磁力搅拌装置;4、支腿;5、蒸汽管;6、排气阀;71、第一灭菌灯;72、第二灭菌灯;81、导向杆;82、固定板;83、移动台;831、第一移动台;832、第二移动台;84、活动盘;85、连杆;851、第一连杆;852、第二连杆;86、气缸;9、空气进管。
具体实施方式
32.下面结合附图和实施例,对本发明进行详细描述。
33.实施例1:一种再生混凝土的强化方法,如图1所示,包括以下步骤:
34.s1、配制培养基
35.培养基由以下组分及其浓度组成:酵母提取物8g/l、大豆蛋白胨10g/l、葡萄糖18g/l、硫酸铵5g/l、一水硫酸镁12mg/l、氯化镍六水合物18mg/l;称取上述组分,并用0.5mol/l氢氧化钠溶液调制ph值为8.0,配制2.5l培养基装于容积5l的发酵罐并升温至120℃消毒,保温15min,冷却至室温,得到培养基;优选的,培养基装液量为50%,即在5000ml体积下,装液量为2500ml。
36.s2、接种培养
37.在无菌操作条件下,按接种量1%将巴氏芽孢杆菌种子液接入培养基中,在30℃、搅拌转速180rpm下恒温培养4天;通入压缩空气好氧培养,培养前期通气比为1:0.5(v/v.min),当相对溶解氧低于50%时,提高通气比至1:1(v/v.min)以上,并开始连续流加补料质量浓度为25%的葡萄糖液,每小时流加补料量为80ml/2.5l培养基,共流加补料7h;调节压缩空气流量保持相对溶解氧30%以上,当相对溶解氧不断上升时,说明菌体繁殖速度下降,停止补料,培养全程流加氨水恒定ph值8.0,培养结束后,得到巴氏芽孢杆菌培养液,芽孢杆菌密度为1.9
×
10
10
cfu/ml;将巴氏芽孢杆菌培养液稀释至od600为1.0,待用;
38.s3、矿化强化
39.将粒径5—15mm的混凝土再生颗粒通过步骤s2中稀释后的巴氏芽孢杆菌培养液浸泡2h,然后进行矿化处理,矿化过程中,通过料液泵循环巴氏芽孢杆菌培养液,以使巴氏芽孢杆菌培养液在料液泵的抽吸下循环起来,提高了巴氏芽孢杆菌培养液的流动性;同时加入尿素和硝酸钙,从而得到含尿素和硝酸钙浓度均为0.8mol/l的矿化溶液,矿化溶液温度保持在28℃;优选的,矿化过程中,先在第一个矿化池的混凝土再生颗粒浸泡矿化2h后,再将矿化溶液排空至另一矿化池浸泡2h,依次循环共15次;优选的,矿化过程中,巴氏芽孢杆
菌培养液从矿化池底部通入矿化池,并从顶部通过料液泵抽出。
40.s4、烘干
41.将步骤s3得到的矿化溶液进行烘干处理,得到含水率为8%的再生矿化颗粒。
42.在上述技术方案中,本发明提供的培养基中加入有利于培养物吸收的镁离子,有利于巴氏芽孢杆菌对金属离子的吸收,具有促进生长的作用。本发明提供的培养基中加入大豆蛋白胨、葡萄糖,有助于糖类、蛋白及维生素的快速吸收,从而促进巴氏芽孢杆菌的快速繁殖和生长。本发明提供的巴氏芽孢杆菌高密度培养方法,得到的巴氏芽孢杆菌芽孢形成率可在95%以上,芽孢杆菌密度最低为1.5
×
10
10
cfu/ml,且工艺简单,连续性强,便于大规模培养。巴氏芽孢杆菌能够分泌高活性的脲酶,凭借其高效的脲酶活性催化细菌内部的尿素分解,迅速提高细菌周围微环境的碳酸根浓度和ph值;其次,巴氏芽孢杆菌表面(包括细胞壁及胞外聚合物)比非矿化细菌具有更多的表面负电荷,对阳离子有更强的吸附作用,因此环境中带有正电荷的ca
2+
能够大量吸附于巴氏芽孢杆菌表面,在高浓度的碳酸根和碱性条件下,ca
2+
就会以细胞为晶核,沉降形成caco3结晶,因此巴氏芽孢杆菌能够诱导碳酸钙沉淀,强化矿化混凝土再生颗粒(细骨料等)。
43.参照图2
‑
3,在步骤s中,发酵罐包括罐体1、灭菌灯、磁力搅拌装置3、驱动机构和设置在罐体1一侧的箱门。罐体1为圆筒状且俯视投影为圆形,箱门安装在罐体1一侧且外部固定有把手,以便打开或关上箱门。磁力搅拌装置3安装在罐体1底部中心,罐体1底部固定有支腿4,支腿4设置有两个,两个支腿4对称设置在罐体1的底部两侧。罐体1上设置有蒸汽管5、排气阀6和用于空气进入的空气进管9,空气进管9伸入罐体1内底部,蒸汽管5由上往下插入罐体1内,蒸汽管5为竖直设置且插入罐体1底部。排气阀6安装在罐体1顶部,优选的,可在罐体1顶部安装压力表和温度计,以便观察罐体1内的压力和温度。蒸汽管5下部的圆周表面开设有圆形出气孔2,出气孔2位于罐体1内,出气孔2设置有多个,多个出气孔2均布在蒸汽管5圆周表面。
44.在上述技术方案中,本发酵罐采用蒸汽灭菌和紫外灭菌两种组合灭菌方式,外界蒸汽可通过蒸汽管5进入罐体1底部,进入罐体1内的蒸汽将通过出气孔2排出。蒸汽通过出气孔2排出后可迅速且均匀的与培养基接触,且配合灭菌灯的使用,可起到消毒全面、灭菌效率高的作用。
45.参照图2
‑
3,灭菌灯包括第一灭菌灯71和第二灭菌灯72,第一灭菌灯71和第二灭菌灯72分别位于蒸汽管5和罐体1侧壁之间,第一灭菌灯71和第二灭菌灯72均为紫外灯。驱动机构用于驱动第一灭菌灯71和第二灭菌灯72相互靠近或远离,优选的,驱动机构包括导向杆81、固定板82、移动台83、活动盘84、连杆85和气缸86。移动台83包括第一移动台831和第二移动台832,第一灭菌灯71安装在第一移动台831靠近蒸汽管5一侧,第二灭菌灯72安装在第二移动台832靠近蒸汽管5一侧。导向杆81为竖直设置且两端分别固定在罐体1上下两侧的侧壁上,导向杆81平行设置有两个,两个导向杆81分别对称设置在蒸汽管5的相对两侧。第一移动台831和第二移动台832分别与导向杆81滑动配合,具体的,两个导向杆81均穿过第一移动台831和第二移动台832,以使第一移动台831和第二移动台832沿导向杆81长度方向相互靠近或远离。
46.参照图2
‑
3,固定板82固定在导向杆81中部,第一移动台831和第二移动台832分别位于固定板82的相对两侧,具体的,第一移动台831位于第二移动台832上方,第一灭菌灯71
位于第二灭菌灯72上方。固定板82在靠近蒸汽管5一侧设置有转轴,转动一端固定在固定板82上,另一端穿过活动盘84中部。连杆85包括第一连杆851和第二连杆852,第一连杆851位于第二连杆852上方且一端与第一移动台831转动连接,另一端与活动盘84转动连接。第二连杆852一端与第二移动台832转动连接,另一端与活动盘84转动连接,第一连杆851和第二连杆852分别连接在活动盘84两端。气缸86固定罐体1顶部上方,气缸86包括活塞杆,气缸86活塞杆端部与固定板82固定。为起到全面消毒作用,优选的,第一灭菌灯71和第二灭菌灯72均设置有两个,两个第一灭菌灯71和两个第二灭菌灯72分别位于蒸汽管5的相对两侧。
47.在上述技术方案中,消毒时,气缸86启动,由于固定板82固定在导向杆81上,而第一移动台831和第二移动台832均滑动连接在导向杆81上,因此气缸86活塞杆来回收缩时,第一移动台831和第二移动台832将带动第一灭菌灯71和第二灭菌灯72相互靠近和远离,从而第一灭菌灯71和第二灭菌灯72能在竖直方向上进行来回移动,提高了灭菌均匀性和全面性,消毒效果较好,自动化程度高。
48.实施例2:一种再生混凝土的强化方法,与实施例1的区别在于,包括以下步骤:
49.s1、配制培养基
50.培养基由以下组分及其浓度组成:酵母提取物5g/l、大豆蛋白胨5g/l、葡萄糖10g/l、硫酸铵3g/l、一水硫酸镁10mg/l、氯化镍六水合物15mg/l;称取上述组分,并用0.5mol/l氢氧化钠溶液调制ph值为8.0,配制2.5l培养基装于容积5l的发酵罐并升温至120℃消毒,保温15min,冷却至30℃,得到培养基;优选的,培养基装液量为50%,即在5000ml体积下,装液量为2500ml。
51.s2、接种培养
52.在无菌操作条件下,按接种量0.5%将巴氏芽孢杆菌种子液接入培养基中,在30℃、搅拌转速180rpm下恒温培养3天;通入压缩空气好氧培养,培养前期通气比为1:0.5(v/v.min),当相对溶解氧低于50%时,提高通气比至1:1(v/v.min)以上,并开始连续流加补料质量浓度为25%的葡萄糖液,每小时流加补料量为50ml/2.5l培养基,共流加补料6h;调节压缩空气流量保持相对溶解氧30%以上,当相对溶解氧不断上升时,说明菌体繁殖速度下降,停止补料,培养全程流加氨水恒定ph值8.0,培养结束后,得到巴氏芽孢杆菌培养液;将巴氏芽孢杆菌培养液稀释至od600为0.6,待用;
53.s3、矿化强化
54.将粒径5—15mm的混凝土再生颗粒通过步骤s2中稀释后的巴氏芽孢杆菌培养液浸泡1h,然后进行矿化处理,矿化过程中,通过料液泵循环巴氏芽孢杆菌培养液,以使巴氏芽孢杆菌培养液在料液泵的抽吸下循环起来,提高了巴氏芽孢杆菌培养液的流动性;同时加入尿素和硝酸钙,从而得到含尿素和硝酸钙浓度均为0.6mol/l的矿化溶液,矿化溶液温度保持在25℃;优选的,矿化过程中,先在第一个矿化池的混凝土再生颗粒浸泡矿化2h后,再将矿化溶液排空至另一矿化池浸泡2h,依次循环共12次;优选的,矿化过程中,巴氏芽孢杆菌培养液从矿化池底部通入矿化池,并从顶部通过料液泵抽出。
55.s4、烘干
56.将步骤s3得到的矿化溶液进行烘干处理,得到含水率为9%的再生矿化颗粒。
57.实施例3:一种再生混凝土的强化方法,与实施例1的区别在于,包括以下步骤:
58.s1、配制培养基
59.培养基由以下组分及其浓度组成:酵母提取物10g/l、大豆蛋白胨15g/l、葡萄糖30g/l、硫酸铵8g/l、一水硫酸镁15mg/l、氯化镍六水合物20mg/l;称取上述组分,并用0.5mol/l氢氧化钠溶液调制ph值为8.0,配制2.5l培养基装于容积5l的发酵罐并升温至120℃消毒,保温15min,冷却至室温,得到培养基;优选的,培养基装液量为50%,即在5000ml体积下,装液量为2500ml。
60.s2、接种培养
61.在无菌操作条件下,按接种量2.0%将巴氏芽孢杆菌种子液接入培养基中,在30℃、搅拌转速180rpm下恒温培养3天;通入压缩空气好氧培养,培养前期通气比为1:0.5(v/v.min),当相对溶解氧低于50%时,提高通气比至1:1(v/v.min)以上,并开始连续流加补料质量浓度为25%的葡萄糖液,每小时流加补料量为100ml/2.5l培养基,共流加补料10h;调节压缩空气流量保持相对溶解氧30%以上,当相对溶解氧不断上升时,说明菌体繁殖速度下降,停止补料,培养全程流加氨水恒定ph值8.0,培养结束后,得到巴氏芽孢杆菌培养液;将巴氏芽孢杆菌培养液稀释至od600为1.2,待用;
62.s3、矿化强化
63.将粒径5—15mm的混凝土再生颗粒通过步骤s2中稀释后的巴氏芽孢杆菌培养液浸泡3h,然后进行矿化处理,矿化过程中,通过料液泵循环巴氏芽孢杆菌培养液,以使巴氏芽孢杆菌培养液在料液泵的抽吸下循环起来,提高了巴氏芽孢杆菌培养液的流动性;同时加入尿素和硝酸钙,从而得到含尿素和硝酸钙浓度均为0.9mol/l的矿化溶液,矿化溶液温度保持在30℃;优选的,矿化过程中,先在第一个矿化池的混凝土再生颗粒浸泡矿化2h后,再将矿化溶液排空至另一矿化池浸泡2h,依次循环共20次;优选的,矿化过程中,巴氏芽孢杆菌培养液从矿化池底部通入矿化池,并从顶部通过料液泵抽出。
64.s4、烘干
65.将步骤s3得到的矿化溶液进行烘干处理,得到含水率为9%的再生矿化颗粒。
66.为检验实施例1至3强化后的再生混凝土颗粒所制成的混凝土试块的抗压强度,本发明进行了对照试验,具体方法如下:
67.空白组
68.将未经强化处理的再生混凝土颗粒,配制混凝土试块按以下配方:42.5水泥250g,矿粉80g,未强化再生混凝土颗粒500g,河砂300g,碎石100g,水140g。
69.试验1组
70.配制混凝土试块按以下配方:42.5水泥250g,矿粉80g,实施例1再生强化混凝土颗粒500g,河砂300g,碎石100g,水140g。
71.试验2组
72.配制混凝土试块按以下配方:42.5水泥250g,矿粉80g,实施例2再生强化混凝土颗粒500g,河砂300g,碎石100g,水140g。
73.试验3组
74.配制混凝土试块按以下配方:42.5水泥250g,矿粉80g,实施例3再生强化混凝土颗粒500g,河砂300g,碎石100g,水140g。
75.每组试块制备3个边长150mm的立方体混凝土试块,于标准条件养护28d测试抗压强度。本发明测试空白组、试验1组、2组、3组的混凝土试块样品的抗压强度性能,抗压强度
参照gb/t 50081
‑
2019《混凝土物理力学性能试验方法标准》进行,3个试样抗压强度平均值分别是空白组27.0mpa、试验1组32.3mpa、试验2组31.8mpa、试验3组33.4mpa。
76.由此可见,本发明实施例1至3强化后的再生混凝土颗粒所制成的混凝土试块的抗压强度均高于未强化再生混凝土颗粒所制成的混凝土试块的抗压强度。
77.以上所述仅是本发明的优选实施方式,本发明的保护范围并不仅局限于上述实施例,凡属于本发明思路下的技术方案均属于本发明的保护范围。应当指出,对于本技术领域的普通技术人员来说,在不脱离本发明原理前提下的若干改进和修饰,这些改进和修饰也应视为本发明的保护范围。