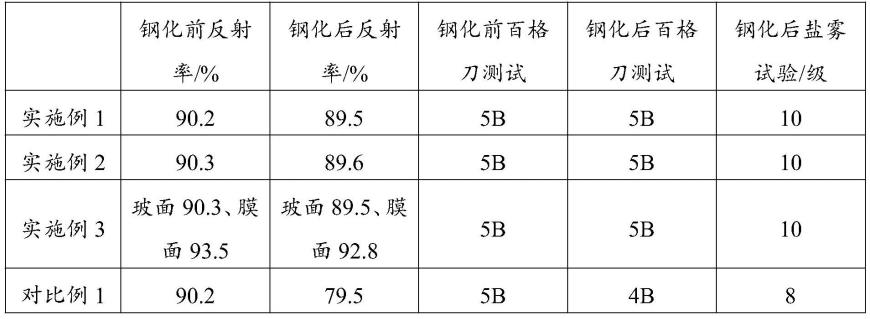
1.本发明属于玻璃技术领域,具体涉及一种可钢化玻璃镜及其制备方法。
背景技术:2.现有玻璃镜主要有玻璃铝镜、玻璃银镜。其中,玻璃铝镜主要靠玻璃表面镀铝薄膜实现反射,但铝薄膜在使用环境中易氧化、腐蚀,导致玻璃铝镜的寿命较短。为保护玻璃表面的铝薄膜,通常的作法是在铝薄膜层外表面再喷上一层很厚(20~50μm)的保护漆。保护漆通常为油漆,物质组成包括包括成膜物质(合成高分子树脂、天然树脂或改性油脂)、颜料、染料、助剂以及有机溶剂,但油漆危害人体健康,造成大气污染;而且,现有玻璃铝镜无法进行钢化处理,玻璃铝镜强度低。
技术实现要素:3.有鉴于此,本发明的目的在于提供一种可钢化玻璃镜及其制备方法,本发明提供的可钢化玻璃镜具有抗氧化能力强、无污染的特点,可异地钢化加工。
4.为了实现上述发明的目的,本发明提供以下技术方案:
5.本发明提供了一种可钢化玻璃镜,包括玻璃基底和在玻璃基底表面依次层叠的增强反射层、金属层和保护层;
6.所述增强反射层包括若干增强反射单元层;按照玻璃基底向外表面的方向,所述增强反射单元层为层叠的第一增强反射膜和第二增强反射膜;所述第一增强反射膜的材质为氧化铌或氧化钛;所述第二增强反射膜的材质为氧化硅;
7.所述金属层的材质包括铝、铝合金、银、银合金、钼、钼合金、铂、金、铑、铱和不锈钢中的一种或多种;
8.所述保护层包括氧化铝层、氧化硅层、氧化铌层、氧化钛层、氧化锆层和氮化硅层中的一种或几种。
9.优选的,所述第一增强反射膜和第二增强反射膜的厚度独立地为20~200nm;所述增强反射层的厚度为40~400nm。
10.优选的,所述金属层的厚度为20~300nm。
11.优选的,所述保护层的厚度为20~200nm;所述保护层为一层或多层;所述多层为二层、三层、四层或五层。
12.优选的,所述保护层为二层时,按照玻璃基底向外表面的方向,所述保护层为依次层叠的第一保护层和第二保护层;所述第一保护层为氧化铝层;所述第二保护层为氧化硅层、氧化钛层、氧化铌层、氧化锆层或氮化硅层。
13.优选的,所述保护层为三层时,按照玻璃基底向外表面的方向,所述保护层为依次层叠的氧化铝层、氧化硅层和氧化铌层,或者为依次层叠的氧化铝层、氧化硅层和氧化钛层,或者为依次层叠的氧化铝层、氧化硅层和氧化锆层,或者为依次层叠的氧化铝层、氧化硅层和氮化硅层,或者为依次层叠的氧化铝层、氧化钛层和氧化硅层,或者为依次层叠的氧
化铝层、氧化铌层和氧化硅层。
14.优选的,所述保护层为四层时,按照玻璃基底向外表面的方向,所述保护层为依次层叠的氧化铝层、氧化硅层、氧化铌层和氧化锆层,或者为依次层叠的氧化铝层、氧化硅层、氧化钛层和氧化锆层,或者为依次层叠的氧化铝层、氧化硅层、氮化硅层和氧化锆层,或者为依次层叠的氧化铝层、氧化钛层、氧化硅层和氧化锆层,或者为依次层叠的氧化铝层、氧化铌层、氧化硅层和氧化锆层。
15.优选的,所述保护层为五层时,按照玻璃基底向外表面的方向,所述保护层为依次层叠的氧化铝层、氧化硅层、氧化铌层、氧化硅层和氧化锆层,或者为依次层叠的氧化铝层、氧化硅层、氧化锆层、氧化硅层和氧化锆层,或者为依次层叠的氧化铝层、氧化硅层、氧化铌层、氧化硅层和氧化铌层。
16.本发明还提供了上述技术方案所述可钢化玻璃的制备方法,包括以下步骤:
17.利用磁控溅射,在玻璃基底上依次制备增强反射层、金属层和保护层。
18.优选的,所述磁控溅射的本底真空度为5
×
10-5
~1
×
10-3
pa。
19.本发明提供了一种可钢化玻璃镜,包括玻璃基底和在玻璃基底表面依次层叠的增强反射层、金属层和保护层;所述增强反射层包括若干增强反射单元层;按照玻璃基底向外表面的方向,所述增强反射单元层为层叠的第一增强反射膜和第二增强反射膜;所述第一增强反射膜的材质为氧化铌或氧化钛;所述第二增强反射膜的材质为氧化硅;所述金属层的材质包括铝、铝合金、银、银合金、钼、钼合金、铂、金、铑、铱和不锈钢中的一种或多种;所述保护层包括氧化铝层、氧化硅层、氧化铌层、氧化钛层、氧化锆层和氮化硅层中的一种或几种。本发明以增强反射层、金属层和保护层形成金属层复合保护层,替代常规保护漆,其中,所述保护层可以很好的隔绝水氧对金属层的侵袭,保护金属层不被外界氧化腐蚀,抗氧化能力强、寿命长;各层具有优良的高温稳定性,在高温钢化的条件下,膜层之间不会有不良反应。本发明提供的可钢化玻璃镜可实现异地钢化加工。而且,所述可钢化玻璃镜各层均无污染,安全环保。
20.此外,传统玻璃镜中保护漆和功能膜物质种类差异大,界面结合能力差、光学效果差;本发明提供的可钢化玻璃镜避免了传统保护漆的使用,各层组成界面结合能力优良,膜层牢固度高,镜面反射率高。
21.实验结果表明,本发明提供的可钢化玻璃镜钢化前反射率为90.2~93.5%,钢化后反射率为89.5~92.8%,钢化后反射率仍较高;钢化前和钢化后百格刀测试均可达到5b级别,层结构牢固度高;400h中性盐雾试验评级为10级,抗氧化性能优异,寿命长。
具体实施方式
22.本发明提供了一种可钢化玻璃镜,包括玻璃基底和在玻璃基底表面依次层叠的增强反射层、金属层和保护层;
23.所述增强反射层包括若干增强反射单元层;按照玻璃基底向外表面的方向,所述增强反射单元层为层叠的第一增强反射膜和第二增强反射膜;所述第一增强反射膜的材质为氧化铌或氧化钛;所述第二增强反射膜的材质为氧化硅;
24.所述金属层的材质包括铝、铝合金、银、银合金、钼、钼合金、铂、金、铑、铱和不锈钢中的一种或多种;
25.所述保护层包括氧化铝层、氧化硅层、氧化铌层、氧化钛层、氧化锆层和氮化硅层中的一种或几种。
26.在本发明中,所述可钢化玻璃镜包括玻璃基底。
27.本发明对所述玻璃基底没有特殊限定,采用本领域技术人员熟知的玻璃基底即可,具体的,如普通玻璃基底或超白玻璃基底。
28.在本发明中,所述可钢化玻璃镜包括在玻璃基底表面的增强反射层。
29.在本发明中,所述增强反射层包括若干增强反射单元层;按照玻璃基底向外表面的方向,所述增强反射单元层为层叠的第一增强反射膜和第二增强反射膜;所述第一增强反射膜的材质为氧化铌或氧化钛;所述第二增强反射膜的材质为氧化硅。在本发明中,所述增强反射层中的增强反射单元层优选为相同或不同。在本发明中,所述第一增强反射膜和第二增强反射膜的厚度独立地优选为20~200nm,更优选为30~150nm。在本发明中,所述增强反射层的厚度优选为40~400nm,更优选为60~450nm。
30.在本发明中,所述可钢化玻璃镜包括增强反射层表面的金属层。
31.在本发明中,所述金属层的材质包括铝、铝合金、银、银合金、钼、钼合金、铂、金、铑、铱和不锈钢中的一种或多种。在本发明中,所述金属层的厚度优选为20~300nm,更优选为30~250nm。
32.在本发明中,所述可钢化玻璃镜包括金属层表面的保护层。
33.在本发明中,所述保护层包括氧化铝层、氧化硅层、氧化铌层、氧化钛层、氧化锆层和氮化硅层中的一种或几种。在本发明中,所述保护层的厚度优选为20~200nm,更优选为30~170nm。
34.在本发明中,所述保护层优选为一层或多层;所述多层优选为二层、三层、四层或五层。
35.在本发明中,所述保护层为一层时,所述保护层优选为氧化铝层、氧化硅层、氧化铌层、氧化钛层、氧化锆层或氮化硅层。
36.在本发明中,所述保护层为二层时,按照玻璃基底向外表面的方向,所述保护层优选为依次层叠的第一保护层和第二保护层;所述第一保护层优选为氧化铝层;所述第二保护层优选为氧化硅层、氧化钛层、氧化铌层、氧化锆层或氮化硅层。
37.在本发明中,所述保护层为三层时,按照玻璃基底向外表面的方向,所述保护层优选为依次层叠的氧化铝层、氧化硅层和氧化铌层,或者为依次层叠的氧化铝层、氧化硅层和氧化钛层,或者为依次层叠的氧化铝层、氧化硅层和氧化锆层,或者为依次层叠的氧化铝层、氧化硅层和氮化硅层,或者为依次层叠的氧化铝层、氧化钛层和氧化硅层,或者为依次层叠的氧化铝层、氧化铌层和氧化硅层。
38.在本发明中,所述保护层为四层时,按照玻璃基底向外表面的方向,所述保护层优选为依次层叠的氧化铝层、氧化硅层、氧化铌层和氧化锆层,或者为依次层叠的氧化铝层、氧化硅层、氧化钛层和氧化锆层,或者为依次层叠的氧化铝层、氧化硅层、氮化硅层和氧化锆层,或者为依次层叠的氧化铝层、氧化钛层、氧化硅层和氧化锆层,或者为依次层叠的氧化铝层、氧化铌层、氧化硅层和氧化锆层。
39.在本发明中,所述保护层为五层时,按照玻璃基底向外表面的方向,所述保护层优选为依次层叠的氧化铝层、氧化硅层、氧化铌层、氧化硅层和氧化锆层,或者为依次层叠的
氧化铝层、氧化硅层、氧化锆层、氧化硅层和氧化锆层,或者为依次层叠的氧化铝层、氧化硅层、氧化铌层、氧化硅层和氧化铌层。
40.本发明还提供了上述技术方案所述可钢化玻璃镜的制备方法,包括以下步骤:
41.利用磁控溅射,在玻璃基底上依次制备增强反射层、金属层和保护层。
42.在本发明中,所述磁控溅射的本底真空度优选为5
×
10-5
~1
×
10-3
pa,更优选为1
×
10-4
~5
×
10-4
pa。
43.本发明优选根据增强反射层、金属层和保护层的材质依次磁控溅射膜相应化学组成的膜层。
44.本发明利用磁控溅射,在玻璃基底上制备增强反射层。
45.在本发明中,当所述第一增强反射膜的材质为氧化铌时,所述磁控溅射的靶材优选为五氧化二铌;溅射气体优选为氩气和氧气的混合气。在本发明中,磁控溅射形成氧化铌时所述混合气中氧气的占比优选为5~30vol.%,更优选为10~25vol.%。在本发明中,所述氩气的流量优选为800~1200sccm,更优选为850~1150sccm,再优选为900~1100sccm。在本发明中,氩原子电离后撞击在五氧化二铌靶材上,五氧化二铌被溅射出来沉积形成氧化铌层;因溅射过程中五氧化二铌中有部分氧会逃逸,所以溅射气体包括一定量的氧气。
46.在本发明中,当所述第一增强反射膜的材质为氧化钛时,所述磁控溅射的靶材优选为二氧化钛;溅射气体优选为氩气和氧气的混合气。在本发明中,磁控溅射形成氧化钛时所述混合气中氧气的占比优选为5~30vol.%,更优选为10~25vol.%。在本发明中,所述氩气的流量优选为800~1200sccm,更优选为850~1150sccm,再优选为900~1100sccm。在本发明中,氩原子在电离状态下撞击二氧化钛靶材,二氧化钛被溅射出来沉积形成氧化钛层;因溅射过程中氧化钛中有部分氧会逃逸,所以溅射气体包括一定量的氧气。
47.在本发明中,所述第二增强反射膜的材质为氧化硅,当制备所述第二增强反射膜时,所述磁控溅射的靶材优选为硅铝合金靶材;所述硅铝合金靶材中硅和铝的摩尔比优选为98:2;溅射气体优选为氩气和氧气的混合气。在本发明中,磁控溅射形成氧化硅时所述混合气中氧气的占比优选为20~70vol.%,更优选为30~60vol.%。在本发明中,所述氩气的流量优选为400~600sccm,更优选为450~550sccm,再优选为480~520sccm。在本发明中,氩原子在电离状态下撞击硅铝合金靶材,硅原子被溅射出来遇到氧气被氧化形成二氧化硅,沉积形成氧化硅层;硅铝合金靶材中铝的含量小,在氧化过程中氧化铝的含量可忽略不计,沉积所得氧化硅层中氧化铝含量也极低且对氧化硅膜层性能几乎无影响。
48.本发明利用磁控溅射,在所述增强反射层表面制备金属层。
49.在本发明中,当所述金属层的材质为铝时,制备材质为铝的金属层时,所述磁控溅射的靶材优选为铝靶材,溅射气体优选为氩气。在本发明中,所述氩气的流量优选为800~1500sccm,更优选为900~1400sccm。在本发明中,氩原子在电离状态下撞击铝靶材,铝原子被溅射出来沉积形成铝层。
50.在本发明中,当所述金属层的材质为铝合金时,制备材质为铝合金的金属层时,所述磁控溅射的靶材优选为铝合金靶材,溅射气体优选为氩气。在本发明中,所述氩气的流量优选为800~1500sccm,更优选为900~1400sccm。在本发明中,氩原子在电离状态下撞击铝合金靶材,铝合金中的原子被溅射出来沉积形成铝合金层。
51.在本发明中,当所述金属层的材质为银时,制备材质为银的金属层时,所述磁控溅
射的靶材优选为银靶材,溅射气体优选为氩气。在本发明中,所述氩气的流量优选为800~1500sccm,更优选为900~1400sccm。在本发明中,氩原子在电离状态下撞击银靶材,银原子被溅射出来沉积形成银层。
52.在本发明中,当所述金属层的材质为银合金时,制备材质为银合金的金属层时,所述磁控溅射的靶材优选为银合金靶材,溅射气体优选为氩气。在本发明中,所述氩气的流量优选为800~1500sccm,更优选为900~1400sccm。在本发明中,氩原子在电离状态下撞击银合金靶材,银合金中的原子被溅射出来沉积形成银合金层。
53.在本发明中,当所述金属层的材质为钼时,制备材质为钼的金属层时,所述磁控溅射的靶材优选为钼靶材,溅射气体优选为氩气。在本发明中,所述氩气的流量优选为800~1500sccm,更优选为900~1400sccm。在本发明中,氩原子在电离状态下撞击钼靶材,钼原子被溅射出来沉积形成钼层。
54.在本发明中,当所述金属层的材质为钼合金时,制备材质为钼合金的金属层时,所述磁控溅射的靶材优选为钼合金靶材,溅射气体优选为氩气。在本发明中,所述氩气的流量优选为800~1500sccm,更优选为900~1400sccm。在本发明中,氩原子在电离状态下撞击钼合金靶材,钼合金中的原子被溅射出来沉积形成钼合金层。
55.在本发明中,当所述金属层的材质为铂时,制备材质为铂的金属层时,所述磁控溅射的靶材优选为铂靶材,溅射气体优选为氩气。在本发明中,所述氩气的流量优选为800~1500sccm,更优选为900~1400sccm。在本发明中,氩原子在电离状态下撞击铂靶材,铂原子被溅射出来沉积形成铂层。
56.在本发明中,当所述金属层的材质为金时,制备材质为金的金属层时,所述磁控溅射的靶材优选为金靶材,溅射气体优选为氩气。在本发明中,所述氩气的流量优选为800~1500sccm,更优选为900~1400sccm。在本发明中,氩原子在电离状态下撞击金靶材,金原子被溅射出来沉积形成金层。
57.在本发明中,当所述金属层的材质为铑时,制备材质为铑的金属层时,所述磁控溅射的靶材优选为铑靶材,溅射气体优选为氩气。在本发明中,所述氩气的流量优选为800~1500sccm,更优选为900~1400sccm。在本发明中,氩原子在电离状态下撞击铑靶材,铑原子被溅射出来沉积形成铑层。
58.在本发明中,当所述金属层的材质为铱时,制备材质为铱的金属层时,所述磁控溅射的靶材优选为铱靶材,溅射气体优选为氩气。在本发明中,所述氩气的流量优选为800~1500sccm,更优选为900~1400sccm。在本发明中,氩原子在电离状态下撞击铱靶材,铱原子被溅射出来沉积形成铱层。
59.在本发明中,当所述金属层的材质为不锈钢时,制备材质为不锈钢的金属层时,所述磁控溅射的靶材优选为不锈钢靶材,溅射气体优选为氩气。在本发明中,所述氩气的流量优选为800~1500sccm,更优选为900~1400sccm。在本发明中,氩原子在电离状态下撞击不锈钢靶材,不锈钢中的原子被溅射出来沉积形成不锈钢层。
60.本发明利用磁控溅射,在所述金属层表面制备保护层。
61.在本发明中,当所述保护层中含有氧化铌层时,所述氧化铌层的制备方法与第一增强反射膜为氧化铌时的制备方法一致,在此不再赘述。
62.在本发明中,当所述保护层中含有氧化钛层时,所述氧化钛层的制备方法与第一
增强反射膜为氧化钛时的制备方法一致,在此不再赘述。
63.在本发明中,当所述保护层中含有氧化硅层时,所述氧化硅层的制备方法与第二增强反射膜为氧化硅时的制备方法一致,在此不再赘述。
64.在本发明中,当所述保护层中含有氧化铝层时,制备所述氧化铝层的条件包括:磁控溅射的靶材优选为铝靶材,溅射气体优选为氩气和氧气的混合气。在本发明中,磁控溅射形成氧化铝层时所述混合气中氧气的占比优选为5~30vol.%,更优选为10~25vol.%。在本发明中,所述氩气的流量优选为800~1200sccm,更优选为850~1150sccm,再优选为900~1100sccm。在本发明中,氩原子在电离状态下撞击铝靶材,铝原子被溅射出来,遇到氧气形成氧化铝,沉积形成氧化铝层。
65.在本发明中,当所述保护层中含有氧化锆层时,制备所述氧化锆层的条件包括:磁控溅射的靶材优选为氧化锆靶材,溅射气体优选为氩气和氧气的混合气。在本发明中,磁控溅射形成氧化锆层时所述混合气中氧气的占比优选为5~30vol.%,更优选为10~25vol.%。在本发明中,所述氩气的流量优选为800~1200sccm,更优选为850~1150sccm,再优选为900~1100sccm。在本发明中,氩原子在电离状态下撞击氧化锆靶材,氧化锆原子被溅射出来,沉积形成氧化锆层;因溅射过程中氧化锆中有部分氧会逃逸,所以溅射气体包括一定量的氧气。
66.在本发明中,当所述保护层中含有氮化硅层时,制备所述氮化硅层的条件包括:磁控溅射的靶材优选为硅铝合金靶材,所述硅铝合金靶材中硅和铝的摩尔比优选为98:2;溅射气体优选为氩气和氮气的混合气。在本发明中,磁控溅射形成氮化硅层时所述混合气中氮气的占比优选为20~40vol.%,更优选为25~35vol.%。在本发明中,所述氩气的流量优选为400~600sccm,更优选为450~600sccm,再优选为500~600sccm。在本发明中,氩原子在电离状态下撞击硅铝合金靶材,硅铝合金靶材中的硅原子被溅射出来,遇到氮气形成氮化硅,沉积形成氮化硅层;硅铝合金靶材中铝的含量小,在氮化过程中氮化铝的含量可忽略不计,沉积所得氮化硅层中氮化铝含量也极低且对氮化硅层性能几乎无影响。
67.为了进一步说明本发明,下面结合实施例对本发明提供的可钢化玻璃镜及其制备方法进行详细地描述,但不能将它们理解为对本发明保护范围的限定。显然,所描述的实施例仅是本发明一部分实施例,而不是全部的实施例。基于本发明中的实施例,本领域普通技术人员在没有做出创造性劳动前提下所获得的所有其他实施例,都属于本发明保护的范围。
68.实施例所用试剂均为市售。
69.实施例1
70.将普通玻璃基底放入磁控溅射设备的腔室,将腔室抽至真空度1.0
×
10-4
pa,以五氧化二铌靶为靶材,按照氩气和氧气体积比为10:1(氩气流量为1000sccm、氧气流量为100sccm)通入氩气和氧气的混合气,在普通玻璃基底表面进行磁控溅射,得到厚度为35nm的氧化铌膜;以硅铝合金靶(si和al摩尔比为98:2)为靶材,按照氩气和氧气体积比为1:1(氩气流量为500sccm、氧气流量为500sccm)通入氩气和氧气的混合气,在氧化铌膜表面进行磁控溅射,得到厚度为70nm的氧化硅膜,在普通玻璃基底表面形成增强反射层;
71.以铝靶为靶材,在1000sccm的氩气条件下,在增强反射层表面进行磁控溅射,得到厚度为100nm的金属层;
72.以铝靶为靶材,按照氩气和氧气体积比为10:1(氩气流量为1000sccm、氧气流量为100sccm)通入氩气和氧气的混合气,在金属层表面进行磁控溅射,得到厚度为30nm的氧化铝层;以硅铝合金靶(si和al摩尔比为98:2)为靶材,按照氩气和氧气体积比为1:1(氩气流量为500sccm、氧气流量为500sccm)通入氩气和氧气的混合气,在氧化铝层表面进行磁控溅射,得到厚度为30nm的氧化硅层;以五氧化二铌靶为靶材,按照氩气和氧气体积比为10:1(氩气流量为1000sccm、氧气流量为100sccm)通入氩气和氧气的混合气,在氧化硅层表面进行磁控溅射,得到厚度为30nm的氧化铌层,完成保护层的制备,得到所述可钢化玻璃镜。
73.实施例2
74.将普通玻璃基底放入磁控溅射设备的腔室,将腔室抽至真空度1.0
×
10-4
pa,以五氧化二铌靶为靶材,按照氩气和氧气体积比为10:1(氩气流量为1000sccm、氧气流量为100sccm)通入氩气和氧气的混合气,在普通玻璃基底表面进行磁控溅射,得到厚度为35nm的氧化铌膜;以硅铝合金靶(si和al摩尔比为98:2)为靶材,按照氩气和氧气体积比为1:1(氩气流量为500sccm、氧气流量为500sccm)通入氩气和氧气的混合气,在氧化铌膜表面进行磁控溅射,得到厚度为70nm的氧化硅膜,在普通玻璃基底表面形成增强反射层;
75.以铝靶为靶材,在1000sccm的氩气条件下,在增强反射层表面进行磁控溅射,得到厚度为100nm的金属层;
76.以铝靶为靶材,按照氩气和氧气体积比为10:1(氩气流量为1000sccm、氧气流量为100sccm)通入氩气和氧气的混合气,在金属层表面进行磁控溅射,得到厚度为30nm的氧化铝层;以硅铝合金靶(si和al摩尔比为98:2)为靶材,按照氩气和氧气体积比为1:1(氩气流量为500sccm、氧气流量为500sccm)通入氩气和氧气的混合气,在氧化铝层表面进行磁控溅射,得到厚度为30nm的氧化硅层;以硅铝合金靶(si和al摩尔比为98:2)为靶材,按照氩气和氮气体积比为1.2:1(氩气流量为600sccm、氮气流量为500sccm)通入氩气和氮气的混合气,在氧化硅层表面进行磁控溅射,得到厚度为30nm的氮化硅层,完成保护层的制备,得到所述可钢化玻璃镜。
77.实施例3
78.将普通玻璃基底放入磁控溅射设备的腔室,将腔室抽至真空度1.0
×
10-4
pa,以五氧化二铌靶为靶材,按照氩气和氧气体积比为10:1(氩气流量为1000sccm、氧气流量为100sccm)通入氩气和氧气的混合气,在普通玻璃基底表面进行磁控溅射,得到厚度为35nm的氧化铌膜;以硅铝合金靶(si和al摩尔比为98:2)为靶材,按照氩气和氧气体积比为1:1(氩气流量为500sccm、氧气流量为500sccm)通入氩气和氧气的混合气,在氧化铌膜表面进行磁控溅射,得到厚度为70nm的氧化硅膜,在普通玻璃基底表面形成增强反射层;
79.以铝靶为靶材,在1000sccm的氩气条件下,在增强反射层表面进行磁控溅射,得到厚度为100nm的金属层;
80.以铝靶为靶材,按照氩气和氧气体积比为10:1(氩气流量为1000sccm、氧气流量为100sccm)通入氩气和氧气的混合气,在金属层表面进行磁控溅射,得到厚度为30nm的氧化铝层;以硅铝合金靶(si和al摩尔比为98:2)为靶材,按照氩气和氧气体积比为1:1(氩气流量为500sccm、氧气流量为500sccm)通入氩气和氧气的混合气,在氧化铝层表面进行磁控溅射,得到厚度为70nm的氧化硅层;以五氧化二铌靶为靶材,按照氩气和氧气体积比为10:1(氩气流量为1000sccm、氧气流量为100sccm)通入氩气和氧气的混合气,在氧化硅层表面进
行磁控溅射,得到厚度为35nm的氧化铌层,完成保护层的制备,得到所述可钢化玻璃镜。
81.对比例1
82.将普通玻璃基底放入磁控溅射设备的腔室,将腔室抽至真空度1.0
×
10-4
pa,以五氧化二铌靶为靶材,按照氩气和氧气体积比为10:1(氩气流量为1000sccm、氧气流量为100sccm)通入氩气和氧气的混合气,在普通玻璃基底表面进行磁控溅射,得到厚度为35nm的氧化铌膜;以硅铝合金靶(si和al摩尔比为98:2)为靶材,按照氩气和氧气体积比为1:1(氩气流量为500sccm、氧气流量为500sccm)通入氩气和氧气的混合气,在氧化铌膜表面进行磁控溅射,得到厚度为70nm的氧化硅膜,在普通玻璃基底表面形成增强反射层;
83.以铝靶为靶材,在1000sccm的氩气条件下,在增强反射层表面进行磁控溅射,得到厚度为100nm的金属层;
84.以铝靶为靶材,按照氩气和氮气体积比为2:1(氩气流量为800sccm、氮气流量为400sccm)通入氩气和氮气的混合气,在金属层表面进行磁控溅射,得到厚度为30nm的氮化铝层;以硅铝合金靶(si和al摩尔比为98:2)为靶材,按照氩气和氮气体积比为1.2:1(氩气流量为600sccm、氮气流量为500sccm)通入氩气和氮气的混合气,在氧化硅层表面进行磁控溅射,得到厚度为10nm的氮化硅层,完成保护层的制备,得到玻璃镜。
85.对实施例1~3和对比例1制备的玻璃镜进行钢化前和钢化后的测试,其中,钢化条件为:在680~700℃保温240~270s,在冷却风压为1.8kpa/cm2条件下冷却160~200s;
86.反射率测试方法为:采用的反射检测仪器为gstr光谱透反射在线扫描测量系统;百格刀测试方法为:gb/t 9286-1998;盐雾试验的测试方法为gb/6458-86(中性盐雾试验标准)、评价方法为gb/t6461-2002(金属基体上和其他无机覆盖层经腐蚀试验后的试样和试件的评级),实验时间为400h。
87.测试结果见表1。
88.表1对实施例1~3和对比例1制备的玻璃镜钢化前后性能
[0089][0090]
由表1可见,本发明提供的可钢化玻璃镜在钢化后的反射率仍较高,说明本发明提供的玻璃镜可钢化,钢化效果好;本发明提供的可钢化玻璃镜在钢化前后膜层牢固度都比较好,可以有效的保护增强反射层和金属层(5b判定为优,4b为合格);本发明提供的玻璃镜可钢化,且钢化后使用寿命比较长(8级以上为合格,10级为优)。
[0091]
以上所述仅是本发明的优选实施方式,应当指出,对于本技术领域的普通技术人员来说,在不脱离本发明原理的前提下,还可以做出若干改进和润饰,这些改进和润饰也应视为本发明的保护范围。