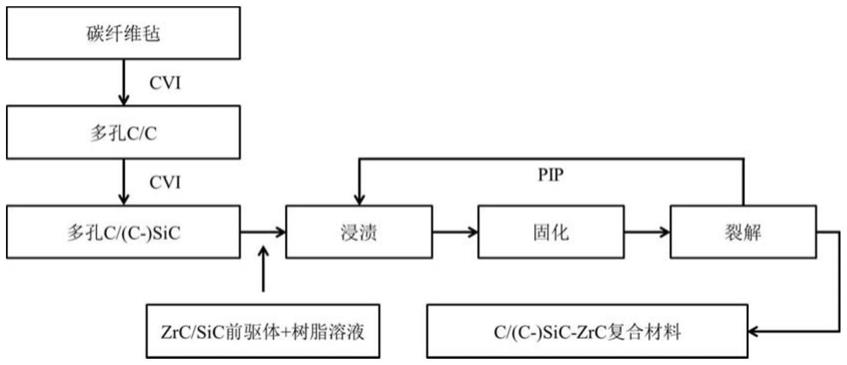
一种树脂改性的c/(c-)sic-zrc复合材料的制备方法
技术领域:
1.本发明涉及超高温陶瓷基复合材料制备技术领域,具体为一种树脂改性的c/(c-)sic-zrc复合材料的制备方法。
背景技术::
2.高超声速飞行器再入过程中,鼻锥、机翼前缘等部件将产生严重的气动加热,因此要求材料具有很好的力学、抗氧化和耐烧蚀性能。c/(c-)sic复合材料虽然具有优异的力学和抗氧化性能,但由于1650℃以上,sic发生活性氧化,限制了该类材料的进一步应用。超高温陶瓷材料不仅熔点高(一般在2500~3000℃),而且具有优异的抗氧化和耐烧蚀性能。大量研究已表明,将超高温陶瓷(如zrc、zrb2、hfc、hfb2等)引入到c/c、c/(c-)sic复合材料内,可显著提高材料的抗氧化和抗烧蚀性能。
3.在c/(c-)sic-zrc复合材料制备过程中,常采用pip工艺将zrc和sic前驱体溶液引入到复合材料内部,并在高温下裂解转化为zrc-sic基体。其中,zrc前驱体在裂解过程中发生有机向无机的转变,首先生成zro2和无定形的c,随着温度的升高,zro2和c发生碳热还原反应生成zrc。由于zrc前驱体内自身含有较高含量的氧,高温裂解过程中会形成co、ch4、co2等气体,导致前驱体缺c,从而不能使得zro2完全转化为zrc,过量的zro2则会与相接触的碳纤维、pyc界面和基体发生反应生成zrc,对其造成损伤,降低材料的力学性能。
4.如何解决上述问题,并精确控制碳热还原反应过程成为科研人员研究的重点和难点。
技术实现要素::
5.针对现有技术中存在的上述不足之处,本发明的目的在于提供一种树脂改性的c/(c-)sic-zrc复合材料的制备方法,基于树脂改性陶瓷前驱体的思想,通过精准控制碳热还原反应进程,有效避免了过量zro2对碳纤维、pyc界面和基体刻蚀;制备出具有化学计量比的zrc-sic基体,同时具有优异力学性能和烧蚀性能的c/(c-)sic-zrc复合材料的方法。
6.为实现上述目的,本发明所采用的技术方案如下:
7.一种树脂改性的c/(c-)sic-zrc复合材料的制备方法,包括如下步骤:
8.(1)采用cvi工艺在碳纤维预制体内沉积热解碳界面/基体,得到多孔c/c复合材料;
9.(2)采用cvi工艺在多孔c/c复合材料内沉积sic基体,得到多孔c/(c-)sic复合材料;
10.(3)改性前驱体制备;
11.(4)采用pip工艺将改性前驱体溶液引入到多孔c/(c-)sic复合材料内部,经多次固化-裂解后,制备出c/(c-)sic-zrc复合材料。
12.上述步骤(1)中,所述cvi工艺参数:沉积温度850~1100℃,ar流量0.06~0.4m3/h,丙烷流量0.06~0.4m3/h,所得多孔c/c复合材料密度在0.6~1.5g/cm3之间。
13.上述步骤(2)中,所述cvi工艺参数:沉积温度1000~1200℃,ar流量0.03~0.3m3/h,h2流量0.03~0.3m3/h,mts流量50~250g/h,所得多孔c/(c-)sic复合材料密度在1.0~1.8g/cm3之间。
14.上述步骤(3)中,所述改性前驱体的制备过程:首先,将zrc前驱体和pcs分别溶于有机溶剂中,浓度范围均为50~70wt.%,并进行磁力搅拌2~10h,得到zrc前驱体溶液和聚碳硅烷pcs溶液;其次,将树脂溶于有机溶剂中,树脂浓度范围为50~70wt.%,并进行磁力搅拌2~15h后得树脂溶液;然后,按一定比例将所述zrc前驱体溶液、聚碳硅烷pcs溶液和树脂溶液混合,并进行磁力搅拌1~5h,获得树脂改性的zrc前驱体和pcs混合溶液,即为所述改性前驱体。
15.上述步骤(3)中,所述改性前驱体的制备过程中,zrc前驱体与聚碳硅烷pcs的量根据所制备c/(c-)sic-zrc复合材料中zrc与sic的比例进行选择,pcs与碳源(树脂)的质量比为1:0.6~1:6之间;所制备c/(c-)sic-zrc复合材料中zrc与sic的体积比为0.5:1~5:1。
16.上述步骤(3)中,所述改性前驱体的制备过程中,选用的碳源为石油树脂、古马隆树脂、醇酸树脂、丙烯酸树脂和沥青树脂中的一种或几种。
17.上述步骤(3)中,所述改性前驱体的制备过程中,选用的有机溶剂为二甲苯、二乙烯基苯或四氢呋喃等。
18.上述步骤(4)pip工艺过程包括如下步骤(a)-(d):
19.(a)浸渍:将改性前驱体溶液引入到多孔c/(c-)sic复合材料内部,先真空浸渍再压力浸渍;其中:真空浸渍的时间1~5h、真空度为≤-0.1mpa;压力浸渍的时间2~3h、压力为2~4mpa;
20.(b)固化:固化温度为80~180℃,保温时间10~24h;
21.(c)裂解:裂解温度为1450~1550℃,保温时间为0.5~2h,气氛为ar或n2等惰性气氛;
22.(d)重复步骤(a)-(c)的过程3-20次。
23.本发明的有益效果如下:
24.通过树脂改性zrc和sic前驱体,获得了化学计量比的zrc-sic基体(如图2所示),有效避免了zro2在高温裂解过程中对碳纤维、pyc界面和基体的刻蚀,显著提高了材料的力学性能和烧蚀性能。
附图说明:
25.图1为树脂改性c/(c-)sic-zrc复合材料制备流程图。
26.图2为树脂改性zrc和sic前驱体的xrd。
27.图3为对比例1制备的c/(c-)sic-zrc复合材料的截面sem照片。
28.图4为对比例2制备的c/(c-)sic-zrc复合材料的截面sem照片。
29.图5为实施例1制备的c/(c-)sic-zrc复合材料的截面sem照片。
30.图6为实施例2制备的c/(c-)sic-zrc复合材料的截面sem照片。
具体实施方式:
31.为使本领域技术人员更好地理解本发明的技术方案,下面结合对比例和实施例对
本发明作进一步详细介绍。
32.对比例1
33.按照图1所示工艺流程,首先,采用cvi工艺制备pyc基体,沉积温度900℃,ar流量0.1m3/h,丙烷流量0.1m3/h,制备出密度为1.2g/cm3的多孔c/c复合材料;采用cvi工艺制备sic基体,沉积温度1000℃,ar流量0.05m3/h,h2流量0.05m3/h,mts流量100g/h,获得密度为1.6g/cm3的多孔c/(c-)sic复合材料。
34.其次,将zrc前驱体和pcs分别溶于二甲苯中,配置成50wt%的溶液,并分别磁力搅拌2h;将50wt%的zrc前驱体二甲苯溶液与50wt%的pcs二甲苯溶液按照最终制备复合材料中zrc与sic体积比1:1进行配置并混合,并充分磁力搅拌2h。最后,采用pip工艺制备c/(c-)sic-zrc复合材料,浸渍时的真空度为-0.1mpa,真空浸渍2h;压力浸渍2h,压力2mpa;100~160℃固化10h,并于1500℃裂解2h,重复上述浸渍-固化-裂解工艺5次,制备出密度为1.77g/cm3的c/(c-)sic-zrc复合材料,材料的弯曲强度为216mpa。图3为材料的微观结构。
35.对比例2
36.按照图1所示工艺流程,首先,采用cvi工艺制备pyc基体,沉积温度900℃,ar流量0.1m3/h,丙烷流量0.1m3/h,制备出密度为1.0g/cm3的多孔c/c复合材料;采用cvi工艺制备sic基体,沉积温度1000℃,ar流量0.05m3/h,h2流量0.05m3/h,mts流量100g/h,获得密度为1.4g/cm3的多孔c/(c-)sic复合材料。
37.其次,将zrc前驱体和pcs分别溶于二乙烯基苯中,配置成60wt%的溶液,并分别磁力搅拌5h;将60wt%的zrc前驱体二乙烯基苯溶液与60wt%的pcs二乙烯基苯溶液按照所制备复合材料中zrc与sic体积比5:1配置并混合,并充分磁力搅拌4h。最后,采用pip工艺制备c/(c-)sic-zrc复合材料,浸渍时的真空度为-0.1mpa,真空浸渍4h;压力浸渍2h,压力3mpa;80~140℃固化20h,并于1500℃裂解1h,重复上述浸渍-固化-裂解工艺10次,制备出密度为2.08g/cm3的c/(c-)sic-zrc复合材料,材料的弯曲强度为162mpa。图4为材料的微观结构。
38.实施例1
39.按照图1所示工艺流程,首先,采用cvi工艺制备pyc基体,沉积温度900℃,ar流量0.1m3/h,丙烷流量0.1m3/h,制备出密度为1.2g/cm3的多孔c/c复合材料;采用cvi工艺制备sic基体,沉积温度1000℃,ar流量0.05m3/h,h2流量0.05m3/h,mts流量100g/h,获得密度为1.6g/cm3的多孔c/(c-)sic复合材料。
40.其次,将zrc前驱体和pcs分别溶于二甲苯中,配置成50wt%的溶液,并分别磁力搅拌2h;将50wt%的zrc前驱体二甲苯溶液与50wt%的pcs二甲苯溶液按照所制备复合材料中zrc与sic体积比1:1配置并混合,并充分磁力搅拌2h,得到zrc前驱体和pcs混合溶液。将石油树脂溶于二甲苯中,配置成50wt%的溶液,并磁力搅拌2h;将50wt%的石油树脂二甲苯溶液按照pcs与石油树脂质量比1:0.8加入到混合好的所述zrc前驱体和pcs混合溶液中,并充分磁力搅拌3h。通过树脂改性zrc和sic前驱体,获得了化学计量比的zrc-sic基体(如图2所示)。
41.最后,采用pip工艺制备c/(c-)sic-zrc复合材料,浸渍时的真空度为-0.1mpa,真空浸渍2h;压力浸渍2h,压力2mpa;100~160℃固化10h,并于1500℃裂解2h,重复上述浸渍-固化-裂解工艺5次,制备出密度为1.79g/cm3的c/(c-)sic-zrc复合材料。材料的弯曲强度为227mpa,相比对比例1强度提高5%。图5为材料的微观结构。
42.实施例2
43.按照图1所示工艺流程,首先,采用cvi工艺制备pyc基体,沉积温度900℃,ar流量0.1m3/h,丙烷流量0.1m3/h,制备出密度为1.0g/cm3的多孔c/c复合材料;采用cvi工艺制备sic基体,沉积温度1000℃,ar流量0.05m3/h,h2流量0.05m3/h,mts流量100g/h,获得密度为1.4g/cm3的多孔c/(c-)sic复合材料。其次,将zrc前驱体和pcs分别溶于二乙烯基苯中,配置成60wt%的溶液,并分别磁力搅拌5h;将60wt%的zrc前驱体二乙烯基苯溶液与60wt%的pcs二乙烯基苯溶液按照所制备复合材料中zrc与sic体积比5:1配置并混合,并充分磁力搅拌4h,得到zrc前驱体和pcs混合溶液;将古马隆树脂溶于二甲苯中,配置成60wt%的溶液,并磁力搅拌4h;将60wt%的古马隆树脂二甲苯溶液按照pcs与古马隆树脂质量比1:6加入到混合好的所述zrc前驱体和pcs混合溶液中,并充分磁力搅拌4h。最后,采用pip工艺制备c/(c-)sic-zrc复合材料,浸渍时的真空度为-0.1mpa,真空浸渍4h;压力浸渍2h,压力3mpa;80~140℃固化20h,并于1500℃裂解1h,重复上述浸渍-固化-裂解工艺10次,制备出密度为1.96g/cm3的c/(c-)sic-zrc复合材料。材料的弯曲强度为247mpa,相比对比例2强度提高53%。图6为材料的微观结构。
44.以上对比例与实施例相应数据如表1。
45.表1
46.实施例zrc/sic体积比pcs/树脂质量比pip次数弯曲强度/mpa对比例11:1-5216对比例25:1-10162实施例11:11:0.85227实施例25:11:610247