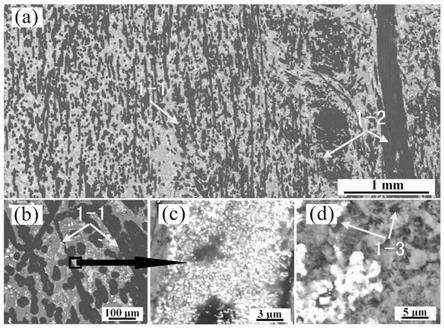
一种夹层结构c/c超高温陶瓷复合材料及其制备方法
技术领域
1.本发明涉及陶瓷复合材料制备技术领域,具体涉及一种夹层结构c/c超高温陶瓷复合材料及其制备方法。
背景技术:2.c/c复合材料具有密度低、比强度高、耐腐蚀、抗热震、高温稳定性好等特性,尤其是在≤2300℃的高温环境中,其力学性能不降反升;因此c/c复合材料独特的高温性能使其在航空航天领域受到了特别的关注。目前,它已成为理想的高温结构材料,在航空航天领域存在巨大的应用潜力。炭材料在有氧环境下,高于400℃便开始氧化,且氧化速率随温度快速增加,从而导致材料结构被破坏,性能下降严重。因此,c/c复合材料在有氧环境中易氧化的缺点制约了其工程化应用推广。
3.超高温陶瓷(uhtc)基体改性是提高c/c复合材料高温抗氧化耐烧蚀性能的有效方法。目前采用的超高温陶瓷基体改性技术包括化学气相渗透、高温熔渗反应、先驱体浸渍裂解、料浆浸渍改性等。因难熔金属铪、锆、钽的前驱体分子量较大,化学气相渗透过程中,较难实现hfc、zrc、tac的均匀渗透,且易在表层发生封孔现象,因此应用推广受到一定的限制。料浆浸渍改性法虽然可以将超细陶瓷颗粒引入c/c多孔骨架中,但引入的陶瓷颗粒在基体中分布不均匀,且浸渍过程中易产生封孔现象,阻碍了后续材料的进一步致密化。先驱体浸渍裂解与高温熔渗反应技术虽然已日趋成熟,但同样存在缺点。先驱体浸渍裂解工艺存在周期长、成本高等缺点,且目前开发的超高温陶瓷先驱体裂解后陶瓷收得率低且含有一定的炭相,因此,导致制备的材料中,实际超高温陶瓷含量较低,材料的高温耐烧蚀性能提高程度有限。高温熔渗反应虽然能制备高陶瓷相含量的c/c超高温陶瓷复合材料,但熔渗过程中,由于熔渗料与炭基体反应不充分,制备的陶瓷基体中往往存在熔渗残余单质相(如si、zr等),这些低熔点的残余单质相往往成为烧蚀的薄弱环节,影响了材料耐烧蚀性能的进一步提高。
技术实现要素:4.针对上述技术问题,提高复合材料的超高温陶瓷相含量,进一步提升材料的高温耐烧蚀性能,本发明通过对超高温陶瓷碳纤维基体进行改进,形成内密外疏的夹层碳纤维预制体,再通过碳沉积以及超高温陶瓷材料的引入获得包括c/c超高温陶瓷内层及高含量超高温陶瓷外层,该夹层结构实现了超高温陶瓷外层优异耐烧蚀性能与c/c超高温陶瓷内层良好高温力学性能的融合,且外层陶瓷结构中含有碳纤维,显著提高了陶瓷外层的抗热震性能。
5.针对上述目的,本发明实施例提供了一种夹层结构c/c超高温陶瓷复合材料的制备方法,所述制备方法具体包括以下步骤:s1:将短纤维铺展在碳纤维预制体的两侧,采用针刺工艺制备获得“短纤维层+普通碳纤维层+短纤维层”夹层纤维预制体;
s2:将所述夹层纤维预制体置于化学气相沉积炉中,采用化学气相沉积法沉积热解炭或碳化硅中的一种或两种,获得夹层结构c/c多孔骨架;s3:采用先驱体浸渍
‑
裂解、化学气相沉积或高温熔渗反应中的一种或多种昂方法,将超高温陶瓷相引入至所述夹层结构c/c多孔骨架,获得夹层结构c/c超高温陶瓷复合材料。
6.进一步的,所述碳纤维预制体为碳纤维编织或缠绕体,具体为碳布叠层、针刺毡、穿刺三维、针刺和缝合结构的多维纤维预制体。
7.进一步的,所述夹层纤维预制体中短纤维层的体积密度低于普通碳纤维层,短纤维层的体积密度≤0.3 g/cm3。
8.进一步的,所述短纤维的纤维长度为2
‑
15cm。
9.进一步的,所述短纤维层的厚度为0.2
‑
10mm。
10.进一步的,所述步骤s2中采用化学气相沉积法沉积热解炭过程具体包括:以丙烯为碳源气体,氮气为载气,沉积压力≤10kpa,沉积温度为850~1100℃。
11.所述步骤s2中采用化学气相沉积法沉积碳化硅过程具体包括:以三氯甲基硅烷为先驱体原料,以氢气为载气通过鼓泡方式将三氯甲基硅烷蒸汽带入混合罐中,ar和氢气作为稀释气体,沉积压力≤1kpa,沉积温度为1150℃。
12.进一步的,所述超高温陶瓷为sic、zrc、hfc、tac、zrb2、hfb2中的一种或多种。
13.进一步的,所述步骤s3中先驱体浸渍
‑
裂解方法具体为:以超高温陶瓷前驱体为浸渍剂,将所述c/c多孔骨架进行反复浸渍、烘干以及高温裂解;在所述浸渍
‑
裂解过程中出现结壳封孔现象时,进行开孔处理,再进行下一轮浸渍、烘干以及高温裂解。
14.所述步骤s3中高温熔渗过程具体为:以锆、铪、硅金属或其合金中的一种或多种为熔渗剂,通过熔渗反应在c/c多孔骨架内形成超高温陶瓷相;抽真空至0.8kpa以下,以2℃/min~15℃/min的升温速率升温至1400~2300℃,保温≥0.5h以上后自然降温至室温。
15.基于同一发明构思的,一种夹层结构c/c超高温陶瓷复合材料,,所述复合材料由上述述的制备方法制备获得。
16.进一步的,所述复合材料包括c/c超高温陶瓷内层和高含量超高温陶瓷外层,所述高含量超高温陶瓷外层厚度为0.2
‑
7mm。
17.有益效果:(1)本发明通过制备夹层结构碳纤维预制体,将短纤维铺展在普通碳纤维预制体的两侧,形成内外层密度完全不同的夹层结构,经后续化学气相沉积和高温陶瓷的引入,使得超高温陶瓷相在外层中的含量提升,从而起到了类似超高温陶瓷涂层的抗氧化耐烧蚀防护效果,且超高温陶瓷外层的厚度可达0.2
‑
7mm,较普通超高温陶瓷涂层厚,在提高涂层抗热震性能的同时,能够显著提高复合材料的耐烧蚀性能,尤其是在动态燃气冲刷条件下的服役寿命。
18.(2)夹层结构c/c超高温陶瓷复合材料实现了超高温陶瓷外层优异耐烧蚀性能与c/c超高温陶瓷内层良好高温力学性能的融合,在保证c/c内层良好的高温力学性能的同时,有效解决了材料高温耐烧蚀性能不足的问题。
19.(3)夹层结构c/c超高温陶瓷复合材料中的超高温陶瓷外层通过纤维针刺与内层相连,且由于短纤维增强增韧作用,因此与普通的超高温陶瓷涂层相比,外层具有更好的结
合性能与高温抗热震性能,克服了现有超高温陶瓷涂层抗热震与结合性能的不足。
20.(4)本发明的夹层结构c/c超高温陶瓷复合材料的制备方法适合于工业化生产,该方法具有结构可控(内外层厚度可调控)、可制备大尺寸、形状复杂异形件等优点。
附图说明
21.图1为本发明实施例1提供的夹层结构c/c
‑
zrc
‑
sic复合材料微观形貌图;其中(a)为夹层结构c/c
‑
zrc
‑
sic复合材料超高温陶瓷外层及内层微观形貌图;(b)为夹层结构c/c
‑
zrc
‑
sic复合材料外层中短纤维和zrc
‑
sic陶瓷相的形貌图;(c)为夹层结构c/c
‑
zrc
‑
sic复合材料外层中填充在短纤维周围的zrc
‑
sic陶瓷相微观放大形貌图;(d)为夹层结构c/c
‑
zrc
‑
sic复合材料靠近内层区域的zrc
‑
sic陶瓷相微观放大形貌图;图2为本发明实施例1提供的夹层结构c/c
‑
zrc
‑
sic复合材料内层微观形貌图及能谱分析结果;其中(a)为夹层结构c/c
‑
zrc
‑
sic复合材料内层微观形貌图;(b)为夹层结构c/c
‑
zrc
‑
sic复合材料内层材料中陶瓷相的能谱分析图;图3为本发明实施例1提供的夹层结构c/c
‑
zrc
‑
sic复合材料氧乙炔焰烧蚀60s后的截面微观形貌图;其中(a)为夹层结构c/c
‑
zrc
‑
sic复合材料氧乙炔焰烧蚀60s后的截面分区微观形貌图,(b)为烧蚀后最外层1区zro2外层放大形貌图,(c)为烧蚀后2区sio2富集层微观放大形貌图;(d)为烧蚀后3区zro2颗粒堆积内层微观放大形貌图;图4为本发明实施例2提供的夹层结构c/c
‑
zrc
‑
sic复合材料外层及内层微观形貌图;其中(a)为夹层结构c/c
‑
zrc
‑
sic复合材料外层微观形貌图;(b)为夹层结构普通针刺c/c
‑
zrc
‑
sic复合材料内层的微观形貌图;(c)为夹层结构c/c
‑
zrc
‑
sic复合材料外层局部微观放大形貌图;(d)为夹层结构c/c
‑
zrc
‑
sic复合材料外层中陶瓷相的微观放大形貌图。
22.附图标记说明1
‑
1、短纤维;1
‑
2、纤维布;1
‑
3、靠近陶瓷基体内层zrc
‑
sic陶瓷颗粒;3
‑
1、sio2;3
‑
2、树脂;3
‑
3、zro2细颗粒;4
‑
1、纤维布;4
‑
2、cvisic界面层;4
‑
3、碳纤维;4
‑
4热解炭层;4
‑
5、zrc
‑
sic陶瓷颗粒。
具体实施方式
23.为了更加清楚阐述本发明的技术内容,在此结合具体实施例和附图予以详细说明,显然,所列举的实施例只是本技术方案的优选实施方案,本领域的技术人员可以根据所公开的技术内容显而易见地得出的其他技术方案仍属于本发明的保护范围。
24.在本发明实施例中,采用的化学试剂均为分析级的试剂,通过购买或现有方法制备获得。
25.实施例1以针刺炭纤维预制体为内层,将短纤维铺展在针刺炭纤维预制体上下两面,采用针刺方式将内外层结构连接以制备夹层结构炭纤维预制体,其中内层普通针刺炭纤维预制体密度为0.45g/cm3,短纤维外层体积密度≤0.3g/cm3,针刺连接短纤维外层后,制备的夹层结构炭纤维预制体整体密度为0.35g/cm3左右,短纤维外层厚度约为6mm。
26.采用化学气相沉积工艺对夹层结构炭纤维预制体进行增密。增密工艺以丙烯为碳源气体,氮气为载气,沉积温度为980℃,沉积压力小于3kpa。经120h化学气相沉积后,制得
密度为1.07g/cm3的夹层结构c/c多孔材料。
27.将聚碳硅烷和烷氧基锆二者以1:2质量比混合溶于二甲苯中形成有机陶瓷先驱体溶液,采用陶瓷先驱体浸渍
‑
裂解工艺对夹层结构c/c多孔体进行反复的超高温陶瓷增密处理。具体工艺为:将化学气相沉积制备的夹层结构c/c多孔体放入浸渍罐中,抽真空至2kpa以下,放入有机陶瓷先驱体溶液浸没夹层结构c/c多孔体,真空浸渍0.5h后取出毛坯;将烘干后的夹层结构c/c多孔体放入石墨化炉中进行高温裂解处理,通氩气作为保护气体,升温至1400~1600℃进行裂解处理,保温时间为60min。增密过程中,当材料表面出现结壳封孔现象时,需对材料进行表面机加工开孔处理,随后方可进行下一轮的增密处理,重复以上先驱体浸渍
‑
裂解过程。经机加工和反复的浸渍
‑
裂解增密后,最终制得的夹层结构c/c
‑
zrc
‑
sic复合材料密度为2.01g/cm3,其最外层纤维增强zrc
‑
sic层的厚度达到了4mm。
28.实施例1制得的夹层结构c/c
‑
zrc
‑
sic复合材料实物图主要由短纤维增强zrc
‑
sic超高温陶瓷外层及c/c
‑
zrc
‑
sic复合材料内层组成。由于外层中炭纤维含量低于c/c
‑
zrc
‑
sic复合材料内层,因此,经后续的超高温陶瓷基体改性工艺后,可在表面制备超高温陶瓷含量较高的致密外层,且炭纤维增强超高温陶瓷外层厚度达到了数毫米量级。
29.图1为实施例1制得的夹层结构c/c
‑
zrc
‑
sic复合材料微观结构形貌图。图1a为制备的夹层结构c/c
‑
zrc
‑
sic复合材料超高温陶瓷外层及内层微观形貌图,由图可知,短纤维增强zrc
‑
sic外层总体厚度在4mm左右,经反复的先驱体浸渍裂解基体改性工艺后,外层中的短纤维周围填充了大量的衬度较高的zrc
‑
sic陶瓷相,且白亮相的面积明显要大于灰黑色炭纤维相的面积,说明外层中超高温陶瓷相含量较普通c/c
‑
zrc
‑
sic复合材料内层高。超高温陶瓷外层中短纤维的存在能够起到增强增韧的作用,有利于提高超高温陶瓷外层的高温抗热震性能。图1b为外层中短纤维和zrc
‑
sic陶瓷相的形貌图,图1c为图1b框选的放大图,即为外层中填充在短纤维周围的zrc
‑
sic陶瓷相微观放大形貌图,可以看出,zrc
‑
sic陶瓷相主要以细小的颗粒形式填充在短纤维周边,且颗粒间结合较紧密,结构较致密;能谱分析结果显示,这些细小的陶瓷颗粒主要含有zr、si、c三种元素,与材料的物相组成相符。图1d为靠近内层区域的zrc
‑
sic陶瓷相微观放大形貌图,可以看出,与外层中的陶瓷相相比,靠近内层区域的zrc
‑
sic陶瓷存在较多的微孔缺陷。图2a为c/c
‑
zrc
‑
sic复合材料内层微观放大形貌图,可以看出内层中存在大量的连续长纤维层,且内层中纤维的含量明显高于外层,由于连续长纤维层中的微孔尺寸及数量均低于外层,因此,连续长纤维层中填充的zrc
‑
sic超高温陶瓷含量较低,造成c/c
‑
zrc
‑
sic复合材料内层中zrc
‑
sic陶瓷相含量明显低于外层。图2b为内层材料中陶瓷相的能谱分析结果,由图可知,陶瓷相主要含有zr,si,c三种元素,进一步说明了zrc
‑
sic陶瓷相的形成。
30.为考察具有超厚炭纤维增强zrc
‑
sic外层的夹层结构c/c
‑
zrc
‑
sic复合材料的高温耐烧蚀性能,采用热流密度为3.2mw/m2的氧乙炔焰对外层厚度为4mm的夹层结构c/c
‑
zrc
‑
sic复合材料和普通针刺c/c
‑
zrc
‑
sic复合材料进行高温耐烧蚀性能对比测试。烧蚀结果证实,经60s的氧乙炔焰烧蚀后,普通针刺c/c
‑
zrc
‑
sic复合材料的线烧蚀率和质量烧蚀率分别为0.011mm/s,0.0019g/s,而外层厚度为4mm的夹层结构c/c
‑
zrc
‑
sic复合材料的线烧蚀率和质量烧蚀率分别为0.0038mm/s,0.0013g/s,相比之下,由于炭纤维增强zrc
‑
sic外层能起到类似涂层的氧化烧蚀防护作用,因此,具有夹层结构的c/c
‑
zrc
‑
sic复合材料的线烧蚀率下降了一个数量级,且质量烧蚀率也降低了31.6%。烧蚀后由于材料表面未形成类似
涂层的连续致密氧化物保护层,烧蚀中心区局部裸露了一定数量的炭纤维,说明表面形成的氧化物保护膜起到的防护效果有限,而外层厚度为4mm的夹层结构c/c
‑
zrc
‑
sic复合材料烧蚀后,烧蚀中心区形成了一层连续致密的白色氧化物保护层,且材料整体完好,对内部基体起到了很好的防护效果,进一步说明炭纤维增强zrc
‑
sic外层对材料基体具有优异的烧蚀防护作用。图3为外层厚度为4mm的夹层结构c/c
‑
zrc
‑
sic复合材料烧蚀后的截面形貌图,由图3a可知,由于4mm的炭纤维增强zrc
‑
sic外层能起到类似涂层的防护效果,烧蚀后,材料表层的烧蚀中心区截面只形成了约210μm的氧化物保护层,且氧化物保护层与下方的炭纤维增强zrc
‑
sic外层结合紧密,外层未出现脱落失效现象,说明炭纤维的引入可有效提升超高温陶瓷层的高温抗热震性能。此外,还可以明显看出,烧蚀后,烧蚀中心表层的氧化物保护层由内向外形成了3层不同的氧化物保护层,由外向内,最外层的1区主要为zro2外层(图3b),2区为sio2富集层(图3c),3区则主要为zro2颗粒堆积内层(图3d,其为图3c中框选的放大图);而氧化层下方的炭纤维增强zrc
‑
sic层结构连续致密,烧蚀后未发生明显的氧化烧蚀迹象,进一步证实了超厚炭纤维增强zrc
‑
sic外层在烧蚀过程中能起到类似涂层的烧蚀防护作用,从而使得夹层结构c/c
‑
zrc
‑
sic复合材料具有优异的高温耐烧蚀性能和长时间的耐烧蚀潜力。
31.实施例2以针刺炭纤维预制体为内层,将短纤维铺展在针刺炭纤维预制体上下两面,采用针刺方式将内外层结构连接以制备夹层结构炭纤维预制体,其中内层普通针刺炭纤维预制体密度为0.45g/cm3,短纤维外层体积密度≤0.3g/cm3,针刺连接短纤维外层后,制备的夹层结构炭纤维预制体密度为0.35g/cm3左右,短纤维外层厚度约为5mm。
32.采用化学气相沉积工艺对炭纤维预制体进行增密。增密工艺以丙烯为碳源气体,氮气为载气,沉积温度为980℃,沉积压力小于3kpa。经100h化学气相沉积后,制得密度为0.96g/cm3的夹层结构c/c多孔材料。采用化学气相沉积工艺引入sic基体,以三氯甲基硅烷(ch3sicl3)为先驱体原料,以氢气为载气通过鼓泡方式将mts蒸汽带入混合罐中,以ar和氢气作为稀释气体。沉积压力为1kpa,沉积温度为1150℃,沉积时间为25h。经sic化学气相沉积后,制得的夹层结构c/c
‑
sic多孔材料密度为1.1g/cm3。
33.采用先驱体浸渍裂解工艺进一步增密。具体工艺为:将聚碳硅烷和烷氧基锆二者以1:2质量比混合溶于二甲苯中形成有机陶瓷先驱体溶液,采用陶瓷先驱体浸渍
‑
裂解工艺对夹层结构c/c
‑
sic多孔体进行反复的超高温陶瓷增密处理。具体工艺为:将化学气相沉积制备的夹层结构c/c
‑
sic多孔材料放入浸渍罐中,抽真空至2kpa以下,放入有机陶瓷先驱体溶液浸没夹层结构c/c
‑
sic多孔体,真空浸渍0.5h后取出毛坯;将烘干后的夹层结构c/c
‑
sic多孔体放入石墨化炉中进行高温裂解处理,通氩气作为保护气体,升温至1400~1600℃进行裂解处理,保温时间为60min。增密过程中,当材料表面出现结壳封孔现象时,需对材料进行表面机加工开孔处理,随后方可进行下一轮的增密处理。重复以上先驱体浸渍
‑
裂解过程,经机加工和反复的浸渍
‑
裂解增密后,最终制得的制得的夹层结构c/c
‑
zrc
‑
sic复合材料密度为2.02g/cm3,其最外层纤维增强zrc
‑
sic层的厚度达到了3mm;其最外层纤维增强zrc
‑
sic层的厚度达到了3mm,密度达到了2.04g/cm3,而内层普通c/c
‑
zrc
‑
sic复合材料密度仅为1.95g/cm3。
34.图4为实施例2制得的夹层结构c/c
‑
zrc
‑
sic复合材料实物图。由图4a可知,制备的
夹层结构c/c
‑
zrc
‑
sic复合材料外层主要由短纤维增强zrc
‑
sic超高温陶瓷外层组成,且其厚度明显超过了1mm(实际厚度为3mm)。图4b为夹层结构普通针刺c/c
‑
zrc
‑
sic复合材料内层的微观形貌图,可以看出,内层中存在明显的纤维布层,且纤维含量明显高于外层中的纤维含量。图4c为外层局部放大形貌图,可以看出,在黑色的炭纤维和热解炭区域与白亮的zrc
‑
sic陶瓷区域之间,形成了较明显的cvisic界面层,且sic界面层紧密包裹在热解炭外表面。图4d为外层中陶瓷相的微观放大形貌图,可以看出,炭纤维表面依次包裹了黑色的热解炭和灰色的sic界面层,而在纤维之间的孔隙处,填充了大量的zrc
‑
sic陶瓷颗粒。图4的微观结构表征结果进一步证实了超厚炭纤维增强zrc
‑
sic超高温陶瓷外层的形成,且夹层结构外层中炭纤维含量明显低于普通针刺c/c
‑
zrc
‑
sic复合材料内层。由于超高温陶瓷外层厚度达毫米量级,烧蚀过程中,相比普通超高温陶瓷涂层(≤0.3mm),其更具长时间耐烧蚀防护的潜力。
35.实施例 3以穿刺炭纤维预制体为内层,将短纤维铺展在针刺炭纤维预制体上下两面,采用针刺方式将内外层结构连接以制备夹层结构炭纤维预制体,其中穿刺炭纤维预制体密度为0.75g/cm3,短纤维外层体积密度≤0.3g/cm3,针刺连接短纤维外层后,制备的夹层结构炭纤维预制体密度为0.65g/cm3,短纤维外层厚度约为5mm。首先采用化学气相沉积工艺对炭纤维预制体进行增密。增密工艺以丙烯为碳源气体,氮气为载气,沉积温度为980℃,沉积压力小于3kpa。经240h化学气相沉积后,制得密度为1.35g/cm3的夹层结构c/c多孔材料。将烷氧基铪溶于二甲苯中形成有机陶瓷先驱体溶液,采用陶瓷先驱体浸渍
‑
裂解工艺对夹层结构c/c多孔体进行反复的超高温陶瓷增密处理。具体工艺为:将化学气相沉积制备的夹层结构c/c多孔体放入浸渍罐中,抽真空至2kpa以下,放入有机陶瓷先驱体溶液浸没夹层结构c/c多孔体,真空浸渍0.5h后取出毛坯;将烘干后的夹层结构c/c多孔体放入石墨化炉中进行高温裂解处理,通氩气作为保护气体,升温至1500~1600℃进行裂解处理,保温时间为60min。重复以上先驱体浸渍
‑
裂解过程6次,制得的低密度夹层结构c/c
‑
hfc复合材料密度为1.6g/cm3。将上述低密度夹层结构c/c
‑
hfc复合材料机加工切成块,以zr
‑
si金属粉为熔渗剂,通过熔渗反应进行进一步的增密处理。具体工艺为:将低密度夹层结构c/c
‑
hfc复合材料包埋在zr
‑
si金属粉中,一起放入石墨坩埚中,再将石墨坩埚置于高温石墨化炉中。抽真空至0.8kpa以下,以2℃/min~15℃/min的升温速率升温至1700~2100℃,保温≥0.5h以上后自然降温至室温。经高温熔渗反应后,制备的夹层结构c/c
‑
hfc
‑
zrc
‑
sic复合材料最终密度为2.3g/cm3,其最陶瓷外层厚度为3mm。
36.以上所述实施例,仅为本发明较佳的具体实施方式,但本发明的保护范围并不局限于此,任何熟悉本技术领域的技术人员在本发明的技术范围内,根据本发明的技术方案及其构思加以等同替换或改变,都应涵盖在本发明的保护范围内。