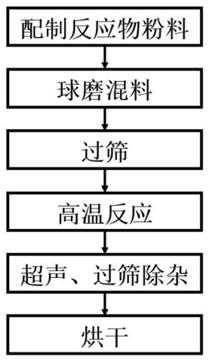
1.本发明属于新材料的制备技术领域,涉及一种采用碳化锆籽晶制备碳化锆晶须的方法。
背景技术:2.碳化锆(zrc)陶瓷是超高温陶瓷材料的一种,具有熔点高(3540℃左右)、强度高、硬度高、模量高、抗烧蚀性良好,导热和导电性好等特点。碳化锆陶瓷在热防护、热结构材料、超硬陶瓷、电极材料、核电材料等领域具有广阔的应用前景。碳化锆晶须不仅具有碳化锆陶瓷优异的本征性能,还因其一维单晶结构而具有接近理论极限的超高强度。碳化锆晶须是一种理想的复合材料增强体,可以广泛地应用于陶瓷基、金属基和树脂基复合材料中,提高复合材料的力学性能、导电性能、导热性能、电磁性能等。目前,制备碳化锆晶须的方法主要有碳热还原法和化学气相沉积法。在已报道的众多碳化锆晶须制备方法中,大多数方法都要引入金属催化剂(fe、co、ni、ni(no3)2·
6h2o、ni(no3)2等)以实现碳化锆的一维生长,由此制备得到具有一维单晶结构的碳化锆晶须。
3.如文献“study on the synthesis and growth mechanisms of the refractory zrc whiskers,liang xu,chuanzhen huang,hanlian liu,bin zou,hongtao zhu,guolong zhao,jun wang.int.journal of refractory metals and hard materials,2014,42:116-119.”提到以氧化锆、碳黑、氟化钠为原料,以金属ni颗粒为催化剂,用碳热还原法制备碳化锆晶须。该方法制备的晶须为单晶结构,晶须顶端存在催化剂ni颗粒,晶须长径比较小、晶须产量较低、尺寸难以控制。专利“一种采用化学气相沉积法制备碳化锆晶须的方法(cn111549378a)”公布了一种以zrcl
4-ch4(c3h6)-h
2-ar为反应物体系,以ni(no3)2为催化剂,采用化学气相沉积法制备碳化锆晶须的方法。该方法制备的晶须纯度较高、形貌较好,晶须顶端也存在较大的催化剂ni颗粒。文献“in-situ homogeneous growth of zrc nanowires on carbon cloth and their effects on flexural properties of carbon/carbon composites,ningning yan,xiaohong shi,kun li,qiangang fu,wei xie,hongrui zhang,qiang song.composites part b,2018,154:200-208.”公开了一种以前驱体热解在碳布上合成碳化锆晶须的方法。该方法采用碳化锆前驱体为锆源和碳源,以ni(no3)2·
6h2o为催化剂制备出了碳化锆晶须。该方法制备的晶须形貌卷曲、产量较低,晶须顶端仍存在催化剂ni颗粒。
4.上述方法都是通过在反应物体系中引入金属催化剂实现了碳化锆晶须的制备,但都不可避免地产生了如下关键问题,即低熔点的金属催化剂将成为杂质存在于每根晶须的顶端,对碳化锆晶须的使用性能(如力学性能、电磁性能等)造成不利影响。为了保证碳化锆晶须的使用性能,往往需要对晶须产物进行酸洗等操作,而酸洗又有可能对碳化锆晶须造成一定损伤,影响质量,且增加了酸洗除杂的制备步骤,使工艺步骤变得更加复杂,不符合经济高效的原则,同时酸洗溶液还会对环境造成不利影响,不符合环保的原则。因此发展无金属催化剂制备碳化锆晶须的方法具有重要意义。
5.专利“一种碳化锆晶须的制备方法(cn 108560058 b)”公布了一种以中间相沥青和四氯化锆为反应物,无金属催化剂制备碳化锆晶须的方法。该方法操作简单、产量较高,但由于四氯化锆在高温下挥发严重,反应难以控制,因此该方法制备的晶须直径不均匀,晶须尺寸不可控。
6.综上所述,目前尚未见报道可有效控制晶须尺寸和形貌、不使用金属催化剂、工艺简单、成本低、产量高的碳化锆晶须制备方法。
技术实现要素:7.要解决的技术问题
8.为了避免现有技术的不足之处,本发明提出一种采用碳化锆籽晶制备碳化锆晶须的方法,克服现有技术所制碳化锆晶须含有金属催化剂、尺寸不可控、形貌蜷曲且不规则、均匀性差、纯度低等缺点,制备出不含金属催化剂、尺寸可控、形貌直立且为标准四棱柱状、分布均匀、纯度高、生产周期短的碳化锆晶须。
9.技术方案
10.一种采用碳化锆籽晶制备碳化锆晶须的方法,其特征在于步骤如下:
11.步骤1、配制原料进行球磨:将体系
①
包括氧化锆、炭黑、氟化钠与碳化锆籽晶按比例混料,将体系
②
包括聚碳锆烷、炭黑、氟化钠与碳化锆籽晶按比例混料,球磨得到混合均匀的反应物前驱体粉料;
12.所述体系
①
中氧化锆、炭黑、氟化钠与碳化锆籽晶的摩尔比为1:3~8:0.1~2:0.1~1;
13.所述体系
②
中聚碳锆烷中锆元素、炭黑、氟化钠与碳化锆籽晶的摩尔比为1:2~6:0.1~2:0.1~1;
14.步骤2:将前驱体粉料进行过筛,获得粒径均匀一致的粉体;
15.步骤3、碳热还原:将步骤2得到的粉体放入石墨坩埚,在管式炉中进行碳热还原反应,得到碳化锆晶须;反应温度:1500℃,保温时间:2~4h,升温速率:5k/min,气氛:氩气,流量:20~200sccm;
16.步骤4、超声、筛滤:将碳化锆晶须放入去离子水中超声4h,再进行过筛,之后烘干,得到纯净碳化锆晶须。
17.所述步骤1中碳化锆籽晶为单晶碳化锆颗粒。
18.所述聚碳锆烷为碳化锆有机物前驱体粉末,聚碳锆烷中锆元素与碳元素之比为1:1。
19.所述步骤1中的氟化钠以无机盐氯化钠、氯化钾、氯化锂、氯化镁、氯化锌、氯化铝、氯化钙、氟化锂、氟化钾中的一种替代。
20.所述步骤1中单晶碳化锆颗粒尺寸为10~1000nm,氧化锆颗粒尺寸为200nm,炭黑尺寸为13nm,氟化钠颗粒尺寸为2-3μm。
21.所述步骤1中球磨混料的球料比为3:1。
22.所述步骤1中球磨转速为50~200r/min。
23.所述步骤2中过筛采用100目
24.所述步骤4中过筛处理的筛网目数要根据晶须长度确定,筛网网孔尺寸要小于晶
须长度。
25.一种采用所述的制备方法制备碳化晶须,其特征在于:当将碳化锆籽晶换成碳化铪籽晶、碳化钛籽晶、碳化钽籽晶或碳化铌籽晶时,并将氧化锆和聚碳锆烷替换成hf、ti、ta、nb的氧化物和对应的有机聚合物,制备得到碳化铪晶须、碳化钛晶须、碳化钽晶须或碳化铌晶须。
26.有益效果
27.本发明提出的一种采用碳化锆籽晶制备碳化锆晶须的方法,为了解决目前方法制备的碳化锆晶须顶端含有金属催化剂、晶须尺寸不可控、形貌较差等问题,本发明提出一种不使用金属催化剂,使用碳化锆籽晶生长碳化锆晶须的方法。本发明的技术方案为将碳化锆籽晶与反应物粉末混合,并在高温下通过碳热还原反应合成碳化锆晶须,通过改变碳化锆籽晶的尺寸和含量可有效调控碳化锆晶须的尺寸。本发明的有益效果是通过本方法制备的碳化锆晶须不含金属催化剂、尺寸可控、形貌直立且为标准四棱柱状、分布均匀、纯度高。本发明制备的碳化锆晶须可以作为陶瓷基、金属基和树脂基复合材料的增强相,也可用于超硬陶瓷、电极材料、核电材料等领域。
28.与现有技术相比,本发明的有益效果有以下几点:
29.(1)本发明采用碳化锆籽晶代替金属催化剂,利用v-s机理实现碳化锆颗粒的各向异性生长来制备碳化锆晶须,使得碳化锆晶须不含金属催化剂杂质,避免了金属催化剂对碳化锆晶须使用性能的不利影响。
30.(2)本发明制备的碳化锆晶须呈四棱柱状,直立生长,形貌良好。碳化锆晶须尺寸均匀,改变加入碳化锆籽晶的尺寸和含量可有效控制碳化锆晶须的尺寸,制备的碳化锆晶须的直径可在100~5000nm、长度可在1~1000μm范围内调控。
31.(3)本发明制备的碳化锆晶须纯度接近100%,产率(n(zr
zrcw
)/n(zr
zro2
),定义产率为碳化锆晶须中锆元素的摩尔量与氧化锆原料中锆元素的摩尔量之比)最高可达35%。
32.(4)本发明发展的碳化锆晶须制备方法工艺简单,设备要求低,操作方便,生产周期短,适合大规模工业化生产。
33.(5)本发明涉及的晶须提纯工艺为超声和过筛,提纯工艺简单,对晶须无损伤。
附图说明
34.图1是本发明的工艺流程图。
35.图2是本发明实施例1碳化锆籽晶的tem图。
36.图3是其他方法制备的碳化锆晶须的扫描电子显微镜(sem)照片。
37.图4是本发明实施例1碳化锆晶须的扫描电子显微镜(sem)照片。
38.图5是本发明实施例1碳化锆晶须的选区电子衍射(tem)照片。
39.图6是本发明实施例1碳化锆晶须的x射线衍射(xrd)图谱。
具体实施方式
40.现结合实施例、附图对本发明作进一步描述:
41.下面将对本发明实施例中的技术方案进行清晰地描述,很显然,所描述实施例只是本发明的实施例中的一部分。基于本发明中的实施例,本领域普通技术人员在没有做出
创造性劳动、不脱离本发明所提供的方法前提下所获得的其他实施例,都属于本发明的保护范围。
42.采用碳化锆籽晶制备碳化锆晶须的实施例中:
43.步骤1,配制原料进行球磨:将体系
①
氧化锆、炭黑、氟化钠与碳化锆籽晶按一定比例混料,将体系
②
聚碳锆烷、炭黑、氟化钠与碳化锆籽晶按一定比例混料,球磨得到混合均匀的反应物粉料。
44.步骤2,过筛:将步骤1得到的前驱体粉料进行100目过筛,获得粒径均匀一致的粉体;
45.步骤3,碳热还原:将步骤2得到的粉体放入石墨坩埚,在管式炉中进行碳热还原反应,得到碳化锆晶须。反应温度:1500℃,保温时间:2~4h,升温速率:5k/min,气氛:氩气,流量:20~200sccm;
46.步骤4,超声、筛滤:将碳化锆晶须放入去离子水中超声4h,再进行过筛,之后烘干,得到纯净的碳化锆晶须。
47.所述步骤1中氧化锆、炭黑、氟化钠与碳化锆籽晶的摩尔比为1:3~8:0.1~2:0.1~1,聚碳锆烷中锆元素、炭黑、氟化钠与碳化锆籽晶的摩尔比为1:2~6:0.1~2:0.1~1。
48.所述步骤1中碳化锆籽晶为单晶碳化锆颗粒,颗粒尺寸为10~1000nm。当籽晶尺寸较小时,制备的碳化锆晶须直径较小,长度较长;当籽晶尺寸较大时,合成的晶须直径较大,长度较短。当碳化锆籽晶尺寸不变时,籽晶的加入量越高,碳化锆晶须的直径越小,长度越长;籽晶的加入量越低,碳化锆晶须的直径越大,长度越短。即调控加入碳化锆籽晶的尺寸和含量可有效控制生成的碳化锆晶须的尺寸。
49.所述步骤1中氧化锆颗粒尺寸为200nm左右,炭黑尺寸为13nm左右,氟化钠颗粒尺寸为2-3μm左右。聚碳锆烷为碳化锆有机物前驱体粉末,聚碳锆烷中锆元素与碳元素之比为1:1左右。
50.所述步骤1中球磨混料的球料比为3:1。
51.所述步骤1中球磨转速为50~200r/min。
52.所述步骤4中过筛处理的筛网目数要根据晶须长度确定,筛网网孔尺寸要小于晶须长度。
53.实施例1
54.步骤1,配制原料进行球磨:
55.将反应物体系
①
按照摩尔比氧化锆:炭黑:氟化钠:碳化锆籽晶=1:5:0.6:0.1配制球磨原料5g,按照球料质量比=3:1、转速100r/min进行球磨,球磨时间为4h。得到混合均匀的反应物粉料。本实施例中碳化锆籽晶颗粒为20nm左右。
56.步骤2,过筛:
57.将步骤1得到的反应物粉料进行100目过筛,获得粒径均匀一致的反应物混合粉体。
58.步骤3,碳热还原
59.将步骤2得到的粉体放入石墨坩埚,在的管式炉中进行碳热还原反应。反应温度:1500℃,保温时间:4h,升温速率:5k/min,气氛:氩气,气流量:50sccm,利用碳热还原反应制备碳化锆晶须。
60.步骤4,将步骤3得到的碳化锆晶须放入去离子水中进行超声4h,过滤除去氧化锆和炭黑等剩余杂质。最后将提纯的碳化锆晶须烘干。如图4所示,本发明制备的碳化锆晶须形貌为四棱柱状,表面光滑,不含杂质;图3所示为其它方法制备的碳化锆晶须,其晶须顶端存在大量的金属催化剂颗粒杂质,纯净度低。因此本发明制备的碳化锆晶须具有明显的纯度优势。
61.实施例2
62.步骤1,配制原料进行球磨:
63.将反应物体系
①
按照摩尔比氧化锆:炭黑:氟化钠:碳化锆籽晶=1:5:0.6:0.2配制球磨原料5g,球料质量比=3:1、转速100r/min进行球磨,球磨时间为4h。得到混合均匀的反应物粉料。本实施例中碳化锆籽晶颗粒为20nm左右。
64.步骤2,过筛:
65.将步骤1得到的反应物粉料进行100目过筛,获得粒径均匀一致的反应物混合粉体。
66.步骤3,碳热还原
67.将步骤2得到的粉体放入石墨坩埚,在的管式炉中进行碳热还原反应。反应温度:1500℃,保温时间:4h,升温速率:5k/min,气氛:氩气,气流量:50sccm,利用碳热还原反应制备碳化锆晶须。
68.步骤4,将步骤3得到的碳化锆晶须放入去离子水中进行超声4h,过滤除去氧化锆和炭黑等剩余杂质。最后将提纯的碳化锆晶须烘干。
69.实施例3
70.步骤1,配制原料进行球磨:
71.将反应物体系
②
按照摩尔比锆元素:炭黑:氟化钠:碳化锆籽晶=1:3:0.4:0.1配制球磨原料5g,球料质量比=3:1、转速100r/min进行球磨,球磨时间为4h。得到混合均匀的反应物粉料。本实施例中碳化锆籽晶颗粒为20nm左右。
72.步骤2,过筛:
73.将步骤1得到的反应物粉料进行100目过筛,获得粒径均匀一致的反应物混合粉体。
74.步骤3,碳热还原
75.将步骤2得到的粉体放入石墨坩埚,在的管式炉中进行碳热还原反应。反应温度:1500℃,保温时间:4h,升温速率:5k/min,气氛:氩气,气流量:50sccm,利用碳热还原反应制备碳化锆晶须。
76.步骤4,将步骤3得到的碳化锆晶须放入去离子水中进行超声4h,过滤除去氧化锆和炭黑等剩余杂质。最后将提纯的碳化锆晶须烘干。
77.实施例4
78.步骤1,配制原料进行球磨:
79.将反应物体系
②
按照摩尔比锆元素:炭黑:氟化钠:碳化锆籽晶=1:3:0.4:0.2配制球磨原料5g,球料质量比=3:1、转速100r/min进行球磨,球磨时间为4h。得到混合均匀的反应物粉料。本实施例中碳化锆籽晶颗粒为20nm左右。
80.步骤2,过筛:
81.将步骤1得到的反应物粉料进行100目过筛,获得粒径均匀一致的反应物混合粉体。
82.步骤3,碳热还原
83.将步骤2得到的粉体放入石墨坩埚,在的管式炉中进行碳热还原反应。反应温度:1500℃,保温时间:4h,升温速率:5k/min,气氛:氩气,气流量:50sccm,利用碳热还原反应制备碳化锆晶须。
84.步骤4,将步骤3得到的碳化锆晶须放入去离子水中进行超声4h,过滤除去氧化锆和炭黑等剩余杂质。最后将提纯的碳化锆晶须烘干。