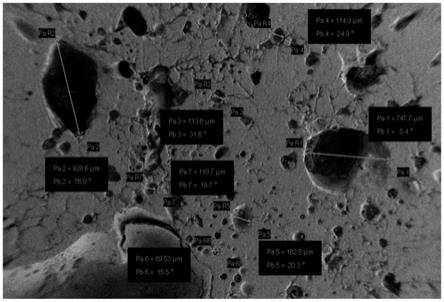
1.本发明属于高温结合剂技术领域,具体涉及一种烧结渗水砖用固废基结合剂及其制备方法。
背景技术:2.烧结型渗水砖,是将渗水砖的原料经过破碎、筛分、配料、混料、成型、脱模、高温烧制等一系列工序,制成具有透水性能和符合标准的路面铺装材料。烧结型渗水砖可以选用各种类型的固体废弃物来制备,因为在高温煅烧的情况下会除去大多数有害物质,减少对环境的污染,可以将重金属离子固化在渗水砖中,防止其流入土壤和城市地下水中。利用工业废渣制备烧结型渗水砖的优点是渗水砖生产周期较短,固体废弃物原料来源广泛,不仅能减少固体废弃物对环境的污染,又减缓了大量固体废弃物在堆放时浪费土地资源的问题,提升经济效益和环境效益。高显气孔率和合适的孔径是烧结型渗水砖具备高透水能力的关键。然而烧结型渗水砖的强度因其显气孔率的提高而大幅度下降,导致其应用受到局限。因此,使用合适的结合剂在提高烧结型渗水砖的力学性能时不会降低渗水砖的透水性能是产品的关键。
3.目前制备烧结渗水砖使用的结合剂,通常是利用天然矿物原料和化工原料配制的,对于利用固废制备烧结型渗水砖来说,用于其中的结合剂成本较高,并且需要进行矿山开采、化工原料生产,带来一系列环境问题。因此,急需开发一种成本更低、具有良好环保效益的用于烧结渗水砖的新型固废基结合剂。
技术实现要素:4.针对现有技术的不足,本发明的目的是提供一种烧结渗水砖用固废基结合剂及其制备方法。
5.为了实现上述目的,本发明所采用的技术方案是:
6.一种烧结渗水砖用固废基结合剂,按重量百分比计,成分组成为:cao 7
‑
20%、al2o310
‑
18%、sio
2 50
‑
62%、mgo 2
‑
6%、k2o 1
‑
5.5%、na2o 1
‑
4%、fe2o
3 0.5
‑
4.0%、b2o
3 0
‑
4%、reo 0
‑
0.5%。
7.包括以下重量百分比的原料:42
‑
47%的高炉渣、28
‑
32%的膨润土、18
‑
22%的长石、4
‑
8%的废玻璃。
8.包括以下重量百分比的原料:40
‑
47%的金尾矿、10
‑
15%的膨润土、20
‑
22%的长石、8
‑
12%的煤矸石、13
‑
18%的高炉渣。
9.包括以下重量百分比的原料:51
‑
54%的粉煤灰、20
‑
23%的高炉渣、12
‑
17%的膨润土、5
‑
10%的废玻璃、2
‑
8%的硼砂、3
‑
8%的长石。
10.所述的固废基结合剂的制备方法,包括以下步骤:
11.(1)按配比称取各原料;
12.(2)将原料加入球磨机均化,充分混合后加入原料量50
‑
70%(wt%)的水,球磨6
‑
8h,然后静置3
‑
4h后,将水倒出;
13.(3)将均化后的原料在90
‑
105℃条件下烘干,再经0.5
‑
1.5h球磨、过筛,即得。
14.所述结合剂的粒径为45
‑
90μm。
15.所述固废基结合剂制备渗水砖的方法,包括以下步骤:
16.(1)将金矿废石或废陶瓷或废耐火材料破碎成粒径为1mm<粒度1≤3mm、粒度2≤1mm的两种颗粒料,两种颗粒料按8:2的重量比混合,备用;
17.(2)向步骤(1)的颗粒料中加入占颗粒料重量10%的固废基结合剂,及占颗粒料重量5
‑
10%的水,在混料机中混料3
‑
5min,使各原料混合均匀;
18.(3)根据所制砖坯大小称取混合料,放入模具中并施以10
‑
30mpa的压力压制成型,制得生砖坯;
19.(4)将生砖坯取出放入干燥窑中,在110℃条件下保温24h,以脱除生砖坯中水分;
20.(5)将干燥后的生砖坯放入隧道窑中烧制,即得。
21.所述烧制具体工艺包括:(1)预烧结:以4℃/min的升温速率,将生砖坯温度从常温升至850℃,至850℃后保温2h;(2)烧结:以1℃/min的升温速率,将温度从850℃升至1120℃
‑
1170℃,至1120℃
‑
1170℃后保温4h;(3)退火:以5℃/min的降温速率将温度降至200℃,出窑,即得。
22.本发明有益效果:
23.1、本发明利用固废高炉渣、金尾矿、粉煤灰、煤矸石、废玻璃等为主要原料制备固废型结合剂,并进一步得到渗水砖,实现了对烧结型渗水砖孔隙率、孔径和强度的有效调控,降低了生产成本。
24.2、本发明采用的高炉渣、金尾矿、粉煤灰、废玻璃等原料中cao、mgo碱土金属氧化物及fe2o3,具有增加烧结液相流动性与烧结体结合强度的特点,有利于烧结助剂性能的提升;高炉渣中含有少量稀土(reo),可以降低结合剂熔点,促进烧结。
25.3、本发明固废原料中含有一定量的na2o、k2o等碱金属氧化物,特别是长石、废玻璃中na2o、k2o等碱金属氧化物的含量较高,一定含量的na2o、k2o能降低液相出现的温度,在较低温度下就可以产生液相,促进颗粒重排和传质过程,进而促进低温下固
‑
液反应而形成低温烧结,起到降低烧结温度的作用,本发明固废型结合剂可降低烧结温度30℃~50℃。
26.4、利用本发明所得固废型结合剂进一步制成渗水砖,所得渗水砖性能良好,其透水系数≥0.01cm/s,抗压强度≥30mpa;抗折强度≥4mpa;25次冻融循环后质量损失率≤5%,抗压强度损失率≤20%。
27.5、本发明利用固废为主要原料制备结合剂,预先充分均化,使其组成和性能尽可能地稳定下来,制备工艺简单,使用方便,可减少矿物原料和化工原料用量,代替助熔剂、增塑剂和粘结剂使用。
28.6、本发明主要利用固体废弃物制备烧结渗水砖用结合剂,实现了废物的有效利用,节能环保,大大节约生产成本,提升了经济和环境效益。
附图说明
29.图1为本发明实施例4所得渗水砖在扫描电镜下放大30倍的微观形貌图。
30.图中,pa为取点标识,pb为测量时旋转的角度。图中可以看出,样品内部呈现出大
小不一、杂乱分布的多孔形貌,孔径成大、中、小分布,最大孔径828.6μm,大孔径数量较少,60μm、100μm左右孔径相对分布较多,部分区域形成连通孔隙结构,使样品具有良好的透水性能。
31.图2为本发明实施例4所得渗水砖在ct下以孔形式展示的样品形貌图。
32.图中,a、b、c三图为对同一块样品的ct图;a.包括通孔和闭孔;b.通孔;c.闭孔。从图中可以看出,样品通孔占有比例较大,ct检测数据分析表明,其中通孔占有总体积的20.99%,闭孔占有总体积的0.62%,说明材料表现出良好的透水性能。
33.图3为本发明实施例4所得渗水砖在扫描电镜下放大1000倍的微观形貌图。
34.图中可以看出,样品内部柱状晶体交织,起到骨架作用,提高制品强度;分布在晶粒间的液相使晶粒之间粘连,提高晶粒结合能力,使制品产生较高强度,同时液相流动会产生孔隙结构。结合剂对液相量的控制、孔隙结构控制、骨料与基质结合、晶体生长至关重要,在一定温度下发生熔融,与骨架材料发生粘结,使制品产生较高强度,同时废渣本身的孔洞及骨料的堆积作用,产生大量在三维上相互贯通的孔洞,是解决好强度与透水性能矛盾的关键。
35.图4为本发明实施例4所得渗水砖的eds分析(x射线能谱分析)。
36.图中,图b是对图a白色亮点处的能谱分析。微区分析显示,材料中有稀土元素存在,高炉渣中的少量稀土,可以降低结合剂熔点,促进烧结。
具体实施方式
37.以下结合实施例对本发明的具体实施方式作进一步详细说明。
38.本发明实施例所用各原料的主要成分含量如下表1所示。
39.表1原料主要成分组成(wt%)
40.原料组成caoal2o3sio2mgona2ok2ofe2o3reo高炉渣39.1412.7035.459.140.710.441.050.82粉煤灰9.2224.4154.552.231.011.145.28
‑
金尾矿3.669.5669.11.381.004.386.50
‑
长石0.2918.1965.620.922.0412.810.09
‑
膨润土1.9814.0069.312.691.591.942.71
‑
废玻璃8.20
‑
71.564.0014.380.240.10
‑
煤矸石0.2625.6748.200.130.130.060.49
‑
废陶瓷1.1618.7074.300.711.162.860.62
‑
金矿废石3.9213.6559.492.922.072.90
‑‑
废耐火材料1.0041.2055.140.310.040.021.20
‑
41.实施例1
42.一种烧结渗水砖用固废基结合剂,包括以下重量百分比的原料:45%的高炉渣、30%的膨润土、20%的长石、5%的废玻璃。
43.该固废基结合剂的制备方法,包括以下步骤:
44.(1)按各原料配比关系称取各原料;
45.(2)将原料加入球磨机均化,充分混合后加入原料量65%(wt%)的水,球磨6h,然
后静置4h后,将水倒出;
46.(3)将球磨好的原料在100℃条件下烘干,再经0.5h球磨、过筛,即得粒径为45
‑
90μm的结合剂。
47.实施例2
48.一种烧结渗水砖用固废基结合剂,包括以下重量百分比的原料:42%的金尾矿、12%的膨润土、21%的长石、10%的煤矸石、15%的高炉渣。
49.该固废基结合剂的制备方法,包括以下步骤:
50.(1)按各原料配比关系称取各原料;
51.(2)将原料加入球磨机均化,充分混合后加入原料量60%(wt%)的水,球磨7h,然后静置3h后,将水倒出;
52.(3)将球磨好的原料在90℃条件下烘干,再经1.5h的球磨、过筛,即得粒径为45
‑
90μm的结合剂。
53.实施例3
54.一种烧结渗水砖用固废基结合剂,包括以下重量百分比的原料:52%的粉煤灰、21%的高炉渣、14%的膨润土、7%的废玻璃、3%的硼砂、3%的长石。
55.该固废基结合剂的制备方法,包括以下步骤:
56.(1)按各原料配比称取原料;
57.(2)将原料加入球磨机均化,充分混合后加入原料量55%(wt%)的水,球磨8h,然后静置4h后,将水倒出;
58.(3)将球磨好的原料在105℃条件下烘干,再经1h球磨、过筛,即得粒径为45
‑
90μm的结合剂。
59.实施例4
60.一种渗水砖的制备方法,包括以下步骤:
61.(1)将金矿废石破碎成粒径为1mm<粒度1≤3mm、粒度2≤1mm的颗粒料,两种颗粒料按8:2的重量比混合,备用;
62.(2)向步骤(1)的颗粒料中加入占颗粒料重量10%的固废基结合剂(实施例1所得),占颗粒料重量8%的水,在混料机中混料5min,使各原料混合均匀;
63.(3)根据所制砖坯大小称重混合料,放入模具中并施以30mpa的压力压制成型,制得生砖坯;
64.(4)将生砖坯取出放入干燥窑中,在110℃条件下保温24h,脱除生砖坯中水分;
65.(5)将干燥后的生砖坯放入隧道窑中烧制,即得。
66.其中烧制具体工艺包括:(1)预烧结:以4℃/min的升温速率,将生砖坯温度从常温升至850℃,至850℃后保温2h;(2)烧结:以1℃/min的升温速率,将温度从850℃升至1120℃,至1120℃后保温4h;(3)退火:以5℃/min的降温速率将温度降至200℃,出窑,即得。
67.所得渗水砖的透水系数0.04cm/s,抗压强度72mpa;抗折强度4.5mpa;25次冻融循环后质量损失率3.5%,抗压强度损失率12%。
68.实施例5
69.一种渗水砖的制备方法,包括以下步骤:
70.(1)将废陶瓷破碎成粒径为1mm<粒度1≤3mm、粒度2≤1mm的颗粒料,两种颗粒料按
照8:2的重量比混合,备用;
71.(2)向步骤(1)的颗粒料中加入占颗粒料重量10%的固废基结合剂(实施例2所得),占颗粒料重量7%的水,在混料机中混料5min,使各原料混合均匀;
72.(3)根据所制砖坯大小称重混合料,放入模具中并施以30mpa的压力压制成型,制得生砖坯;
73.(4)将生砖坯取出放入干燥窑中,在110℃条件下保温24h,以脱除生砖坯中的水分;
74.(5)将干燥后的生砖坯放入隧道窑中烧制,即得。
75.其中烧制的具体工艺包括:(1)预烧结:以4℃/min的升温速率,将生砖坯温度从常温升至850℃,至850℃后保温2h;(2)烧结:以1℃/min的升温速率,将温度从850℃升至1140℃,至1140℃后保温4h;(3)退火:以5℃/min的降温速率将温度降至200℃,出窑,即得。
76.所得渗水砖的透水系数0.03cm/s,抗压强度81mpa;抗折强度6.2mpa;25次冻融循环后质量损失率2.3%,抗压强度损失率10%。
77.实施例6
78.一种渗水砖的制备方法,包括以下步骤:
79.(1)将废耐火材料破碎成粒径为1mm<粒度1≤3mm、粒度2≤1mm的颗粒料,两种颗粒料按照8:2的重量比混合,备用;
80.(2)向步骤(1)的颗粒料中加入占颗粒料重量10%的固废基结合剂(实施例3所得),占颗粒料重量8%的水,在混料机中混料5min,使各原料混合均匀;
81.(3)根据所制砖坯大小称重混合料,放入模具中并施以30mpa的压力压制成型,制得生砖坯;
82.(4)将生砖坯取出放入干燥窑中,在110℃条件下保温24h,以脱除生砖坯中的水分;
83.(5)将干燥后的生砖坯放入隧道窑中烧制,即得。
84.其中烧制的具体工艺包括:(1)预烧结:以4℃/min的升温速率,将生砖坯温度从常温升至850℃,至850℃后保温2h;(2)烧结:以1℃/min的升温速率,将温度从850℃升至1170℃,至1170℃后保温4h;(3)退火:以5℃/min的降温速率将温度降至200℃,出窑,即得。
85.所得渗水砖的透水系数0.03cm/s,抗压强度52mpa;抗折强度4.2mpa;25次冻融循环后质量损失率2.5%,抗压强度损失率11%。