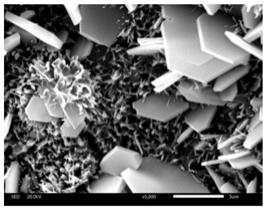
1.本发明属于工业废渣资源化利用技术领域,具体涉及利用钢铁厂固废的复合掺合料及其制备方法。
背景技术:2.钢铁厂在钢铁生产的过程中,产生了很多除矿渣外的低水化活性的固体废弃物,如钢渣、炉渣、塔底灰、低级粉煤灰、建筑垃圾、铁尾矿等。
3.矿渣是在炼铁过程中熔渣排入水中急冷所得的副产物,其化学成分cao、sio2、al2o3和mgo成分占80%以上,还含有少量的fe2o3、mno2以及tio2,矿物组成以硅酸盐和硅铝酸盐为主,且含有大量非晶态玻璃体结构的物质,其具有较高的潜在水化活性。多年来,矿渣微粉由于其优异的特性,一直作为优质的辅助胶凝材料用于水泥和混凝土的制备,且随着水泥、混凝土产量的逐年增长,矿渣微粉的需求量也逐年增长,甚至在一些地区出现供不应求的紧张现象,某些地区矿渣微粉的价格甚至与水泥不相上下。
4.钢渣是炼钢过程中排出的固体废弃物,富含c3s和c2s等矿物,是一种类似于劣质硅酸盐水泥熟料的工业废渣,但其易磨性较差,安定性差,难以大规模实现资源化利用。低等级粉煤灰是燃煤烟气中收捕下来的细灰,主要成分为:sio2、al2o3、fe2o3、fe2o3、cao、tio2等,其颗粒较粗,甚至含有一定量未燃尽的碳粉,水化活性差。塔底灰为烟气脱硫生成的固体粉末,其成分复杂,并且组成成分有很大一部分是极不稳定的亚硫酸钙,综合利用较为困难,大部分用于堆放或填埋处置,但这会造成二次污染且损失大量硫资源。上述钢渣、粉煤灰、塔底灰等水化活性相比矿渣很低、生产附加值低、处理困难,逐步形成困扰钢铁企业主业发展的负担。
5.在此背景条件下,结合钢铁企业的实际情况,将易获得的固体废弃物(如钢渣、炉渣、塔底灰、低级粉煤灰、建筑垃圾、铁尾矿、石屑等)与矿渣复合,制备经济型复合掺合料,替代s95矿渣微粉,可在一定程度上缓解矿粉供应紧张问题,同时可提高固体废弃物综合利用率,减少环境污染,变废为宝,提高矿渣的经济价值的同时节约社会资源,具有巨大的经济效益和环境效益。
6.专利《多固废水泥耦合掺合料及其制备方法》(cn 112358215 a)提供了一种多固废水泥耦合掺合料及其制备方法,虽然制备方法也采用了化学活化的方式,但又需要热活化过程,生产工艺复杂、能耗高,制备成本高。专利《一种钢渣粉
‑
锰铁矿渣粉复合掺合料及其制备工艺》(cn 111302691 a)提供了一种钢渣粉
‑
锰铁矿渣粉复合掺合料及其制备工艺,其制备工艺为钢渣、锰铁矿渣需分别粉磨至一定细度,该工艺粉磨设备投资大,生产效率不高,且所获得复合掺合料符合据gb/t20491
‑
2017《用于水泥和混凝土中的钢渣粉》标准,活性较低,应用有限;此外,其钢渣掺量过高,存在制品后期体积稳定性不良的风险。
技术实现要素:7.本发明目的在于提供一种利用钢铁厂固废制备的经济型复合掺合料及其生产方
法。该复合掺合料主要采用钢铁企业生产过程的固体废弃物,不仅能够资源化利用钢渣、低等级粉煤灰、塔底灰等固体废弃物,增加矿粉的供应量,降低矿渣粉的生产成本,而且利于理顺钢铁生产过程中主产品和副产废弃物的关系,促进主业发展。
8.为达到上述目的,采用技术方案如下:
9.利用钢铁厂固废的复合掺合料,其组成按重量份数计如下:
10.矿渣80~90份、钢渣5~10份、塔底灰3~9份、粉煤灰1~5份、化学活化剂1~3份;所述矿渣、钢渣、塔底灰、粉煤灰均来自钢铁厂固废。
11.按上述方案,所述矿渣、钢渣、塔底灰、粉煤灰组成的混合料的成分按照重量百分数计:
12.sio
2 29%~34%、cao 35%~40%、al2o
3 10%~18%、fe2o
3 1.5%~3%、so
3 2.5%~4%,烧失量≤2.5%。
13.按上述方案,所述矿渣按照重量百分比计包括下列组分:sio
2 30%~35%、cao 35%~40%、al2o
3 8%~20%、fe2o
3 0.1%~2%、mgo 6%~12%、so
3 2%~5%,经粉磨后达到国标中s95级以上的活性要求。
14.按上述方案,所述钢渣按照重量百分比计包括下列组分:sio
2 15%~25%、cao 30%~40%、al2o
3 3%~8%、fe2o
3 10%~25%、mgo 10%~15%、so
3 0.2%~2%,烧失量≤8%。
15.按上述方案,所述粉煤灰按照重量百分比计包括下列组分:sio
2 40%~55%、cao 5%~10%、al2o
3 25%~40%、fe2o
3 2%~10%、so
3 2%~5%,烧失量≤10%。
16.按上述方案,所述塔底灰按照重量百分比计包括下列组分:sio
2 3%~5%、cao 25%~40%、al2o
3 0%~3%、fe2o
3 3%~10%、so
3 15%~25%,烧失量≤30%。
17.按上述方案,所述化学活化剂由元明粉:铵明矾:异丙醇胺:酯基季铵盐:改性多元醇按照质量比(4~8):(2~6):(0.1~0.5):(0.2~0.6):(0.1~0.3)配比混合而成,其中所述改性多元醇由乙二醇:二乙二醇:季戊四醇:甘油按照质量比(1~3):(2~4):(1~2):(3~6)混合而成。
18.上述利用钢铁厂固废的复合掺合料的制备方法,包括以下步骤:
19.将所述矿渣、钢渣、粉煤灰、塔底灰分别进行化学成分分析;
20.配料保证混合物的化学组成:sio
2 29%~34%、cao 35%~40%、al2o
3 10%~18%、fe2o
3 1.5%~3%、so
3 2.5%~4%,烧失量≤2.5%;
21.将所述矿渣、钢渣分别破碎,控制粒径<5mm,然后与粉煤灰、塔底灰一起投入磨机;
22.粉磨的同时,加入化学活化剂一起粉磨30~40min,通过选粉机控制比表面积≥450m2/kg,即得到复合掺合料。
23.与现有技术相比,本发明的优点及有益效果是:
24.本发明利用钢铁厂固废制备的经济型复合掺合料以钢铁厂的固体废弃物矿渣、钢渣、粉煤灰、塔底灰等为主要生产原料,能够消耗大量固体废弃物,包含难以处理的低水化活性的钢渣、塔底灰等,同时可以降低矿渣粉的生产成本、增加s95矿渣粉的供应量。
25.本发明从基于各原材的化学成分设计复合掺合料合理的原料组成,首先保证矿渣的活性不低于s95级,同时采用物理机械磨细控制细度、塔底灰的硫酸盐激发、化学活化剂
的碱激发等手段提高掺合料水化活性,既避免高活性矿渣粉的“活性”浪费,又提高低活性固废的利用价值。
附图说明
26.图1是本发明实施例2对应净浆的7d水化产物xrd图谱;
27.图2是本发明实施例2对应净浆的28d水化产物xrd图谱;
28.图3是本发明实施例2对应净浆7d水化产物的sem图;
29.图4是本发明实施例2对应净浆28d水化产物的sem图。
具体实施方式
30.以下实施例进一步阐释本发明的技术方案,但不作为对本发明保护范围的限制。
31.本发明通过将钢铁厂的高活性矿渣与低活性固废复合,利用机械磨细活化、组分间协同激发、外加活化剂激发等手段,制备出经济型的符合国标s95矿渣粉要求的复合掺合料。
32.具体实施方式中采用的矿渣、钢渣、塔底灰、粉煤灰均来自钢铁厂固废,其组成按重量份数计如下:矿渣80~90份、钢渣5~10份、塔底灰3~9份、粉煤灰1~5份、化学活化剂1~3份。
33.其中,矿渣按照重量百分比计包括下列组分:sio
2 30%~35%、cao 35%~40%、al2o
3 8%~20%、fe2o
3 0.1%~2%、mgo 6%~12%、so
3 2%~5%,经粉磨后达到国标中s95级以上的活性要求。
34.钢渣按照重量百分比计包括下列组分:sio
2 15%~25%、cao 30%~40%、al2o
3 3%~8%、fe2o
3 10%~25%、mgo 10%~15%、so
3 0.2%~2%,烧失量≤8%。
35.粉煤灰按照重量百分比计包括下列组分:sio
2 40%~55%、cao 5%~10%、al2o
3 25%~40%、fe2o
3 2%~10%、so
3 2%~5%,烧失量≤10%。
36.塔底灰按照重量百分比计包括下列组分:sio
2 3%~5%、cao 25%~40%、al2o
3 0%~3%、fe2o
3 3%~10%、so
3 15%~25%,烧失量≤30%。
37.所述化学活化剂由元明粉:铵明矾:异丙醇胺:酯基季铵盐:改性多元醇按照质量比(4~8):(2~6):(0.1~0.5):(0.2~0.6):(0.1~0.3)配比混合而成,其中所述改性多元醇由乙二醇:二乙二醇:季戊四醇:甘油按照质量比(1~3):(2~4):(1~2):(3~6)混合而成。
38.本发明复合掺合料的具体制备过程如下:
39.将所述矿渣、钢渣、粉煤灰、塔底灰分别进行化学成分分析;
40.配料保证混合物的化学组成:sio
2 29%~34%、cao 35%~40%、al2o
3 10%~18%、fe2o
3 1.5%~3%、so
3 2.5%~4%,烧失量≤2.5%;
41.将所述矿渣、钢渣分别破碎,控制粒径<5mm,然后与粉煤灰、塔底灰一起投入磨机;
42.粉磨的同时,加入化学活化剂一起粉磨30~40min,通过选粉机控制比表面积≥450m2/kg,即得到复合掺合料。
43.表1为实施例1、2、3所得复合掺合料各固废的重量份。
44.表1
45.实施例矿渣钢渣粉煤灰塔底灰活化剂实施例180.09.03.06.02.0实施例284.07.03.05.01.0实施例385.08.01.04.51.5
46.将表1各实施例对应的复合掺合料分别和水泥组成的混合物依次与标准砂按照1:3的重量配比混合,再按照0.5的水胶比,得到水泥砂浆,然后依据gb/t18046—2017《用于水泥和混凝土中的粒化高炉矿渣粉》标准进行矿渣粉胶砂试验的试验结果。作为比较,同时配制了纯普硅水泥作为胶凝材料的基准组s、50%普硅水泥+50%矿渣粉作为胶凝材料的对照组s0。表2反映,实施例s1
‑
s3对应的复合掺合料强度大部分超过基准组s的强度,s1
‑
s3均超过对照组s0的强度。
47.表2各实施例、基准组、对照组对应胶砂强度的试验结果
[0048][0049]
将表2的数据结果依据gb/t18046—2017《用于水泥和混凝土中的粒化高炉矿渣粉》标准中的活性计算方法处理之后得到的活性指数,见表3。可以看出,与使用纯普硅水泥及使用s95矿渣粉的水泥胶砂s组、s0组相比,实施例s1
‑
s3的7d、28d活性指数均满足gb/t18046—2017《用于水泥和混凝土中的粒化高炉矿渣粉》标准中s95的技术要求。
[0050]
表3各实施例、基准组、对照组的活性指数的试验结果
[0051][0052]
同时选取表1中的实施例2、依据gb/t1346
‑
2011《水泥标准稠度用水量、凝结时间、安定性检验方法标准》制成净浆试块,标准养护7d及28d后制成试样,分别用xrd衍射仪测定不同龄期水化产物的物相,见图1、图2;分别用扫描电子显微镜电镜(sem)以真空模式分别观察不同水化龄期样品新鲜断面的微观形貌,见图3、图4。
[0053]
根据图1和图3,可以看出实施例2对应净浆的7d水化产物主要为针状的钙矾石、絮状的c
‑
s
‑
h凝胶及片状的ca(oh)2。除普通水泥的发生水化反应外,又由于化学活化剂为碱
性,它会使oh
‑
浓度增大从而析出晶体,与矿物掺合料中活性氧化硅、氧化铝、硫酸根离子一起反应生成的钙矾石、c
‑
s
‑
h凝胶等(即碱激发)。随着水化反应的继续进行,从图2、图4可见,试样28d水化产物中基本看不到片状ca(oh)2,但钙矾石、c
‑
s
‑
h凝胶明显增多。这是由于随着水化反应不断进行,矿物掺合料的潜在活性慢慢地被激发,氢氧化钙的量不断被消耗,体系中形成了以钙矾石为骨架、c
‑
s
‑
h凝胶和其他水化产物填充在骨架和孔隙之中,使结构更加密实,宏观上表现为力学性能得到显著提高。
[0054]
根据当前原料价格,采用实施例1
‑
3生产复合型掺合料的成本及其与s95纯矿渣粉的成本对比,见表4所示。当前各原材的价格分别为:矿渣为230元/t,钢渣为25元/t,塔底灰为25元/t,粉煤灰为100元/t,活化剂为1200元/t,各实施例的配方成本分别为,s1为214.75元/t,s2为217.75元/t,s3为218.93元/t,分别比s95矿渣粉的配方成本降低15.25元/t,12.25元/t,11.07元/t,不仅降低生产成本,同时消耗低活性固废,提高矿渣粉产量,经济效果显著。
[0055]
表4实施例1
‑
3对应复合掺合料的配方成本
[0056][0057]
以上所述是本发明的优选实施方式而已,当然不能以此来限定本发明之权利范围,应当指出,对于本技术领域的普通技术人员来说,在不脱离本发明原理的前提下,还可以做出若干改进和变动,这些改进和变动也视为本发明的保护范围。