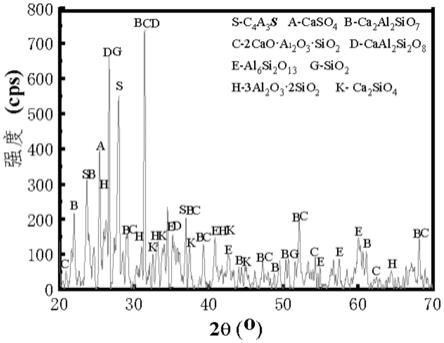
1.本文涉及但不限于新型建筑材料技术领域,尤其涉及但不限于一种石膏基干混砂浆及其制备方法。
背景技术:2.脱硫石膏是一种电厂固体废弃物,品质和质量因电厂脱硫技术、设备条件等不同而存在巨大差异。目前,我国近50%的火电企业产出的脱硫石膏存在含水量高、品位低、氯离子及钠离子含量高的现象。杂质离子含量高的脱硫石膏对石膏制品的性能有不良的影响,例如,用杂质离子含量高的脱硫石膏制备的石膏基制品表面容易出现返霜等问题。因此,研究如何利用杂质含量较高的低品质石膏制备性能良好的石膏基制品具有重要的意义。
技术实现要素:3.以下是对本文详细描述的主题的概述。本概述并非是为了限制本技术的保护范围。
4.本技术利用杂质含量较高的低品质石膏为基材,制备了性能良好的石膏基砂浆,为杂质离子含量高的低品质石膏资源化利用提供了新途径。
5.本技术提供了一种石膏基干混砂浆材料,所述石膏基干混砂浆材料包括低品质石膏熟料、基材和生石灰;
6.所述基材包括氧化铝、氧化硅和硫;
7.所述硫选自有机硫化物、无机硫化物和单质硫中的任意一种或更多种。
8.在本技术提供的一种实施方式中,所述石膏基干混砂浆还包括沸石,所述低品质石膏熟料、所述基材与所述沸石的重量比为(75至85):(5至50):(0至5);
9.在本技术提供的一种实施方式中,所述生石灰的用量通过以下方式确定:
10.测定所述低品质石膏熟料、所述沸石与所述基材混合后得到的混合物的标准稠度用水量,通过所述生石灰调节所述混合物的ph值至7至10时的生石灰用量即为所述生石灰的用量。
11.在本技术提供的一种实施方式中,所述基材中还包括氧化钙、氧化铁、氧化钛、氧化镁、氧化钾和氧化钠中的任意一种或更多种;
12.在本技术提供的一种实施方式中,所述基材中的氧化钙、氧化铝、氧化硅、氧化铁、硫、氧化钛、氧化镁、氧化钾、氧化钠的重量比为(0至20):(10至60):(30至70):(0至14):(0.5至20):(0至2):(0至2):(0至0.8):(0至0.7);
13.在本技术提供的一种实施方式中,所述碳酸钙可以为分析纯化学试剂,也可以为主要成分为碳酸钙的矿物质或是矿渣;所述氧化铝可以为分析纯化学试剂,也可以为主要成分为氧化铝的矿物质或是矿渣。
14.在本技术提供的一种实施方式中,所述基材的粒度为60目至200目;
15.在本技术提供的一种实施方式中,所述沸石的粒度为200目至1500目。
16.在本技术提供的一种实施方式中,所述低品质石膏熟料由低品质石膏制备得到的石膏熟料;
17.在本技术提供的一种实施方式中,所述低品质石膏中cl-含量在0.03wt.%至0.9wt.%,na
+
离子含量在0.02wt.%至0.07wt.%;
18.在本技术提供的一种实施方式中,所述低品质石膏熟料中,无水石膏(aiii石膏)含量不高于5wt.%;二水石膏(dh)含量不高于3wt.%;
19.在本技术提供的一种实施方式中,所述低品质石膏熟料的粒度为100目至400目;优选地,所述低品质石膏熟料的d50可以为40μm至50μm。
20.在本技术提供的一种实施方式中,所述石膏基干混砂浆材料还包括减水剂和保水剂中的任意一种或两种。
21.在本技术提供的一种实施方式中,所述低品质石膏熟料、所述减水剂和所述保水剂的重量比为(75至85):(0至0.07):(0至0.18);
22.在本技术提供的一种实施方式中,所述低品质石膏熟料、所述减水剂和所述保水剂的重量比为(75至85):(0.02至0.06):(0.05至0.15)。
23.在本技术提供的一种实施方式中,减水剂选自嘧胺树脂系减水剂、聚羧酸系减水剂和马来酸酐系减水剂中的任意一种或更多种。
24.在本技术提供的一种实施方式中,所述保水剂选自羟丙基甲基纤维素醚、甲基纤维素醚和羟乙基甲基纤维素醚中的任意一种或更多种;
25.在本技术提供的一种实施方式中,所述保水剂为粘度为20000mpa.s至100000mpa.s的羟丙基甲基纤维素醚。
26.又一方面,本技术提供了上述的石膏基干混砂浆材料的制备方法,包括如下步骤:
27.1)将所述基材和所述石膏熟料以及所述沸石混合均匀,粉磨得到混合物1;
28.2)将所述混合物1与生石灰混合均匀,得到预混粉;
29.3)将所述预混粉与所述减水剂、所述保水剂混合均匀,得到所述石膏基干混砂浆材料。
30.在本技术提供的一种实施方式中,所述生石灰的用量按照以下方法确定:测试所述混合物1、所述减水剂和所述保水剂混合均匀得到的混合物2的标准稠度用水量,按照所述标准稠度用水量与所述混合物2混合,得到混合物3,使用所述生石灰调节所述混合物3的ph值至7至10,以确定调节ph值所使用的生石灰的用量;
31.在本技术提供的一种实施方式中,步骤1)中的基材先经过煅烧,所述煅烧的温度为1100℃至1350℃,所述煅烧的时间为0.3h至6h,所述煅烧后保温时间为10min至90min。
32.在本技术提供的一种实施方式中,若所述煤灰渣为固硫后的煤灰渣,即煤灰渣包括含硫煤、碳酸钙和氧化铝混合后,或包括含硫煤、碳酸钙混合后,或包括含硫煤、氧化铝混合后制备的型煤煅烧后得到的煤灰渣,则无需再次煅烧;优选地,所述煤灰渣粉磨至60目至100目;
33.在本技术提供的一种实施方式中,标准稠度用水量的确定可以按照本领域中常用的方法确定,例如,根据国家标准gb/t28627-2012中的“标准扩散度用水量的测定”的方法测定。
34.在本技术提供的一种实施方式中,当本技术提供的一种石膏基干混砂浆材料用于3d打印时,所述石高基干混砂浆材料还包括粘结剂;
35.在本技术提供的一种实施方式中,所述粘结剂为聚乙烯醇,可选地,所述粘结剂为聚乙烯醇pva2488或聚乙烯醇pva1788;
36.在本技术提供的一种实施方式中,可以将uv胶黏剂、环氧树脂胶黏剂溶于溶剂中配制成的溶液,所述溶剂为不溶解石膏的无毒、易挥发的溶剂,例如,乙醇。
37.所述石膏熟料与所述粘结剂的重量比为(75至85):(0至1.5);优选重量比为(75至85):(0.5至1.5);
38.所述粘结剂在最后各原料混合时加入;
39.当砂浆用于3d打印时还引入了无水乙醇,用于避免石膏砂浆中石膏基材吸湿品质发生变化。所述乙醇的用量为所述标准稠度用水量的1/3至1/2。
40.本技术具有以下优点:
41.1.以杂质(氯离子、钠离子)含量高的低品质石膏为主体材料,不但实现了低品质石膏的资源化利用,而且提高了石膏基材料的蓄热、调湿能力;
42.2.有效了解决了目前3d打印技术中使用混凝土材料或粘土质等打印材料在打印高度较高(超过2cm)的制品时,打印过程中制品容易坍塌的问题;
43.3.用杂质(氯离子、钠离子)含量高的低品质石膏制备出了性能优良的石膏基砂浆;
44.4.有效的实现了同时对杂质离子(氯离子、钠离子)的固化,有利于提高石膏基砂浆的耐久性能和施工性能。
45.5.在不降低砂浆力学性能的同时,实现了轻质、保温,提高了砂浆的涂布率;
46.6.在砂浆施工过程中使砂浆具有锁水功能,调整了砂浆的凝结硬化和干燥时间,改善了砂浆的抗裂性能。
47.本技术的其它特征和优点将在随后的说明书中阐述,并且,部分地从说明书中变得显而易见,或者通过实施本技术而了解。本技术的其他优点可通过在说明书中所描述的方案来发明实现和获得。
附图说明
48.附图用来提供对本技术技术方案的理解,并且构成说明书的一部分,与本技术的实施例一起用于解释本技术的技术方案,并不构成对本技术技术方案的限制。
49.图1为本技术的实施例1中的含硫煤充分燃烧(1200℃)后形成的煤灰渣x射线衍射图谱。
50.图2为本技术的对比例3中的含硫煤充分燃烧(1050℃)后形成的煤灰渣x射线衍射图谱。
具体实施方式
51.为使本技术的目的、技术方案和优点更加清楚明白,下文对本技术的实施例进行详细说明。需要说明的是,在不冲突的情况下,本技术中的实施例及实施例中的特征可以相互任意组合。
52.以下实施例中和对比例中所使用的碳酸钙、氧化铝、氧化钙均为分析纯化学试剂,购自国药集团化学试剂有限公司。沸石粉购自国投盛世科技股份有限公司,325目;含硫煤样为徐州环宇焦化有限公司含硫煤,所述含硫煤的成分分析如表1所示。
53.表1:实施例中含硫煤的成分分析
54.煤样%s,dc,dh,dn,d含硫煤2.0478.663.793.79
55.(注:国土资源实物地质资料中心化验室分析,d:干燥基,化验时煤样所处的状态为无水分状态)
56.实施例1至4、对比例1所用脱硫石膏生料中cl-含量为0.29wt.%,na
+
含量为700ppmw。实施例5、对比例2所用脱硫石膏生料中cl-含量为0.195wt%,na
+
含量为200ppmw。
57.所述保水剂为粘度为羟丙基甲基纤维素醚,购自广东龙湖科技有限公司公司,牌号hpmc-75000mpa.s。所述减水剂为聚羧酸系减水剂,巴斯夫公司生产的r+d melflux eco 5691f。粘结剂为聚乙烯醇pva2488购自可乐丽国际贸易上海有限公司。
58.实施例1
59.(1)将100kg含硫煤与1.74kg的碳酸钙混合均匀后制成型煤,在1200℃下充分燃烧后形成的煤灰渣,测定其中的主要化学成分含量为:
[0060][0061]
将煤灰渣粉粹至80目。
[0062]
(2)将低品质脱硫石膏煅烧制备低品质石膏熟料(制备的熟料是β型半水石膏),陈化后的低品质脱硫熟料中二水石膏含量(dh)为1.6wt.%,无水石膏(aⅲ)为1.3wt.%;粉磨,密封备用,得到粒度为200目,d50为40μm至50μm的低品质石膏熟料;
[0063]
(3)将步骤(2)制备的低品质石膏熟料粉100kg、沸石粉0.5kg和制备的煤灰渣10kg混合均匀,得到混合物1;
[0064]
(4)测试混合粉末(将低品质石膏熟料粉100kg、沸石粉0.5kg、上述制备的煤灰渣10kg、0.05kg减水剂、0.05kg保水剂混合均匀得到的混合物)的标准稠度用水量,测试标准稠度用水量制备的料浆的ph值;根据混合粉末的料浆的ph值在料浆中添加生石灰,控制料浆的ph值在9.5;
[0065]
(5)将步骤(3)制备的混合物1、与控制料浆的ph值在9.5的用量的生石灰混合均匀,制备预混粉;
[0066]
(6)将步骤(5)制备的预混粉、0.05kg减水剂、0.05kg保水剂混合均匀,然后溶于乙醇中得到混合物2,乙醇的浓度为100%,乙醇的用量为拌合水用量的0.4;
[0067]
(7)将步骤(6)制备的混合物2、粘结剂(1kg)、按混合粉末(将低品质石膏熟料粉100kg、沸石粉0.5kg、上述制备的煤灰渣10kg、0.05kg减水剂、0.05kg保水剂混合均匀得到的混合物)测定的标准稠度用水量的拌合水混合均匀,得到所述3d打印的石膏基干混砂浆。
[0068]
实施例2
[0069]
实施例2与实施例1的区别仅在于步骤(3)。步骤(3):将步骤(1)制备的石膏粉
100kg、沸石粉0.5kg和制备的煤灰渣15kg混合均匀;
[0070]
实施例3
[0071]
实施例2与实施例1的区别仅在于步骤(3)。步骤(3):将步骤(1)制备的石膏粉100kg、沸石粉0.5kg和制备的煤灰渣5kg混合均匀;
[0072]
实施例4
[0073]
实施例4与实施例1的区别在于步骤(4)。
[0074]
步骤(4):测试混合粉末(将低品质石膏熟料粉100kg、沸石粉0.5kg、上述制备的煤灰渣10kg、0.05kg减水剂、0.05kg保水剂混合均匀得到的混合物)的标准稠度用水量,测试标准稠度用水量制备的料浆的ph值;根据混合粉末的料浆的ph值在料浆中添加生石灰,控制料浆的ph值在7.2;
[0075]
实施例5
[0076]
实施例5与实施例1的区别除脱硫石膏中杂质离子含量不同外,区别在于步骤(3)。步骤(3):将步骤(1)制备的石膏粉100kg、沸石粉0.5g和制备的煤灰渣5kg混合均匀;
[0077]
实施例6
[0078]
实施例6与实施例1的区别在于,使用与实施例1相同的含硫煤,含硫煤在1200℃下完全煅烧后生成煤灰渣后,向所述煤灰渣中添加cao 0.97kg混合均匀,使得煤灰渣中氧化钙、氧化铝和氧化硅的比例为10.7:28.82:38.62,在1200℃下再次煅烧4h,保温60min,粉磨至200目。其余步骤和原料与实施例1相同。
[0079]
实施例7
[0080]
本技术与实施例1的区别仅在于,不使用煤灰渣,取分析纯氧化钙、氧化铝、分析纯氧化硅、分析纯二水硫酸钙、氧化铁(用量比例与实施例1相同)置于马弗炉,逐渐升温至1200℃,在1200℃的温度下煅烧2h,保温60min,之后将得到的固体物质粉磨至80目,取10kg,替换实施例1中的煤灰渣。其他制备方法和原料与实施例1完全相同。
[0081]
所述分析纯氧化钙、分析纯氧化铝、分析纯氧化硅、分析纯二水硫酸钙、分析纯氧化铁的重量比为10.7:28.8:38.6:11:13.1。
[0082]
对比例1
[0083]
(1)选取与实施例1相同的低品质石膏熟料粉100kg;测试混合物1(所述低品质石膏熟料粉100kg、0.05kg减水剂、0.05kg保水剂混合均匀得到的混合物)的标准稠度用水量;
[0084]
(2)将所述低品质石膏粉与0.05kg减水剂、0.05kg保水剂混合均匀,然后溶于乙醇中得到混合物2;乙醇的浓度为100%,乙醇的用量为拌合水用量的0.4;
[0085]
(3)将步骤(2)制备的混合物2、1kg粘结剂、低品质石膏熟料粉的标准稠度用水量的拌合水混合均匀,得到所述3d打印的石膏基干混砂浆。
[0086]
对比例2
[0087]
(1)选取与实施例5相同的低品质石膏熟料粉100kg;测试混合物1(所述低品质石膏熟料粉100kg、0.05kg减水剂、0.05kg保水剂混合均匀得到的混合物)的标准稠度用水量;
[0088]
(2)将所述低品质石膏粉与0.05kg减水剂、0.05kg保水剂混合均匀,然后溶于乙醇中得到混合物2;乙醇的浓度为100%,乙醇的用量为拌合水用量的0.4;
[0089]
(3)将步骤(2)制备的混合物2、1kg粘结剂、拌合水混合均匀,得到所述3d打印的石膏基干混砂浆。
[0090]
对比例3
[0091]
本对比例3与实施例1的区别仅在于步骤(1)中的煅烧温度不同:
[0092]
步骤(1):将100kg含硫煤与1.74kg的碳酸钙混合均匀后制成型煤,在1050℃下充分燃烧后形成的煤灰渣。
[0093]
对比例4
[0094]
本对比例4与实施例1的区别仅在于步骤(4)不调节混合粉末的ph值和步骤(5)中不添加生石灰。
[0095]
对比例5
[0096]
本对比例5与实施例1的区别仅在于原料中无煤灰渣、其他原料和工艺与实施例1完全相同。
[0097]
对比例6
[0098]
本对比例与实施例1的区别仅在于,使用普通脱硫石膏,脱硫石膏中氯离子含量为100ppmw、钠离子含量为200ppmw,选用的脱硫石膏不属于低品质石膏。
[0099]
性能测试
[0100]
1.将实施例1中制备的煤灰渣进行xrd测试,测试得到的煤灰渣的x射线衍射图谱,测试结果请见图1。
[0101]
图1中,主要特征峰为s,b,c,s为3cao
·
3al2o3·
caso4(简写为c4a3s),b为ca2al2sio7,c为2cao
·
al2o3·
sio2的特征峰。次强特征峰为d、a和g,d caal2si2o8,a为caso4,g为sio2的特征峰。除此之外还含有一定量的e、h,少量的k,e为al6si2o
13
,h为3al2o3·
sio2,k为casio4特征峰。
[0102]
2.将对比例3中制备的煤灰渣进行xrd测试,测试得到的煤灰渣的x射线衍射图谱,测试结果请见图2。
[0103]
图2中,主要特征峰:a为caso4,b为ca2al2sio7,还有特征峰:g为sio2,l为al2o3,f为fe2o3。
[0104]
3、按照gb/t17669.3-1999《建筑石膏力学性能的测定》测试实施例与对比例制备的石膏基材料的抗压强度性能参数;软化系数测试:根据《石膏基建材与应用》(王祁青编著,化学工业出版社)书中的第一章第四节中的第六小节进行测试。测试结果请见表3和表4。
[0105]
表3
[0106] 28天抗压强度(mpa)软化系数实施例120.50.45实施例223.60.52实施例318.70.36实施例417.80.31实施例518.90.37实施例620.30.45实施例720.10.44对比例117.30.30对比例217.60.32
对比例317.50.32对比例417.00.30对比例516.50.30对比例617.30.32
[0107]
表4
[0108][0109][0110]
4.根据gb/t37785-2019《烟气脱硫石膏》标准要求测试砂浆(砂浆形成的料浆硬化后,将硬化后的物质粉磨)中的水溶性的氯离子和钠离子含量,结果见表5。
[0111]
表5
[0112] 水溶性氯离子含量ppmw水溶性钠离子含量ppmw实施例12190230实施例22050165实施例32440420实施例42780280实施例51695110实施例62570240
实施例72215195对比例12875690对比例21880188对比例32810520对比例42798340对比例52840590对比例690195
[0113]
5.导热系数测试:将实施例1至7和对比例1至6的胶凝材料与适量(标准稠度用水量)拌合水混合搅拌均匀后,制成10cm
×
10cm
×
9.5cm的板材;分别测试其导热系数。测试仪器为湘科
tm
drpl-i导热系数测试仪,由湘潭市仪器仪表有限公司制造。结果见表6。
[0114]
表6
[0115] 导热系数w/m
·
k(25℃)实施例10.071实施例20.045实施例30.085实施例40.070实施例50.087实施例60.072实施例70.082对比例10.210对比例20.221对比例30.052对比例40.069对比例50.210对比例60.073
[0116]
通过表3可以发现,本技术可以有效提高石膏胶凝材料的长期强度并且可以改善石膏基材料的耐水性能。通过表5可以意外发现,本技术可以有效的减少石膏基砂浆中的游离杂质离子的含量,可以有效固化氯离子和钠离子。通过表6可以发现,本技术实施例的导热系数大幅减小。
[0117]
虽然本技术所揭露的实施方式如上,但所述的内容仅为便于理解本技术而采用的实施方式,并非用以限定本技术。任何本技术所属领域内的技术人员,在不脱离本技术所揭露的精神和范围的前提下,可以在实施的形式及细节上进行任何的修改与变化,但本技术的保护范围,仍须以所附的权利要求书所界定的范围为准。