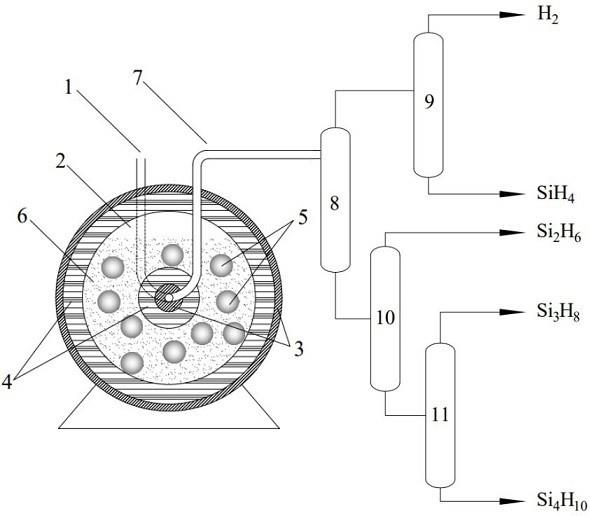
1.本发明涉及高阶硅烷合成领域,尤其涉及一种利用等离子球磨裂解合成高阶硅烷的方法。
背景技术:2.硅烷类气体是半导体及光伏行业的重要原料,主要用于沉积各种含硅元素的薄膜,尤其以非晶硅和多晶硅薄膜为主。目前应用最广泛的硅烷气体为甲硅烷,但甲硅烷用于沉积多晶硅薄膜的分解温度较高,沉积速率较慢,在一定程度上制约了多晶硅薄膜的应用。高阶硅烷具备更低的分解温度,更快的沉积速率,并且沉积生长的薄膜具有更规则的晶格排列,更有利于生长形成大晶粒多晶硅薄膜。例如,乙硅烷沉积生长多晶硅薄膜的温度可低至约500℃,低于普通玻璃的软化温度,因此可实现在玻璃基底表面直接沉积多晶硅薄膜的过程;而丙硅烷沉积生长多晶硅薄膜的温度可低至300℃以下,有望实现在柔性基底上直接沉积多晶硅薄膜,或与其它材质如石墨烯等相结合制备特种复合薄膜材料的工艺过程。对比现有工艺,一般先以甲硅烷为原料沉积非晶硅薄膜再进行激光诱导晶型转化形成多晶硅薄膜,制备效率较低,严重制约了相关应用技术的发展。
3.现有用于工业化生产乙硅烷的工艺路线主要有六氯乙硅烷氢化法、硅化镁法和甲硅烷裂解法。
4.其中,六氯乙硅烷氢化法一般以氢化铝锂或氢化铝钠为还原剂,在有机溶剂中与六氯乙硅烷发生还原反应,生成乙硅烷和盐,同时伴有副产物氯气。该工艺的优点是可实现连续化生产,生产规模易于放大,但六氯乙硅烷提纯工艺复杂,难度较大,还原剂氢化铝锂或氢化铝钠制备条件苛刻,整个工艺流程复杂,能耗较高,控制难度大,设备投资及运行成本都较高。
5.硅镁法一般以硅化镁和氯化铵为原料,在液氨溶剂内进行反应,反应一般在微正压的条件下进行,温度控制在-20~-30℃的范围内。该工艺主要用来制备高纯甲硅烷,同时副产约3~5%的乙硅烷及微量的丙硅烷。该工艺的优点是工艺流程短、设备简单、易于控制,且所获得的硅烷气体产品纯度高,后期纯化较为容易。该工艺中,第一个步骤是要将硅粉与镁粉混合,然后加热至500℃以上进行合金化反应生成硅化镁粉体。由于市场上工业级硅粉一般约为200目,而镁粉由于粒径过细时易燃易爆,市场购买一般为约为40目,而该合金化过程较为适宜的粉体粒径为600~1000目,且由于其为固-固相反应,需两种粉体进行充分搅拌及压合,保证其具有足够的接触面积,因此该步骤首先需进行长时间的合金化处理。且由于其反应发生在固相表面,当反应生成硅化镁后,硅化镁占据反应原位将阻碍反应的进一步发生,因此粉体内部很难实现充分反应,故该合金化反应的转化率偏低。
6.甲硅烷裂解法是以甲硅烷为原料,使其发生裂解反应形成自由基后进行重排,结合生成高阶硅烷的方法。该方法使用高纯甲硅烷为原料,一般会结合辉光放电的反应条件,在较低的压力下进行反应,可以同时生成乙硅烷、丙硅烷及丁硅烷等多种高阶硅烷。由于该方法采用的原料仅为甲硅烷,且甲硅烷易于提纯,因此生成的高阶硅烷纯度极高且易于分
离。但为了使辉光放电稳定,该方法需在低压下进行,因此高阶硅烷生产效率极低,并且反应过程副产硅粉,极大地浪费了原料甲硅烷。而如果需要提高反应压力,则反应温度随之升高,将加速高阶硅烷分解,导致副产物硅粉增多且高阶硅烷转化率明显降低。
7.综上所述,现有技术的六氯乙硅烷氢化法工艺复杂运行难度大,硅镁法工艺仅能间歇操作,操作时间长,转化率低,导致总体产能小,而甲硅烷裂解法需要在低压下进行,生产效率低,产能难以放大,且辉光放电设备结构复杂,维护成本较高。
8.在研究了甲硅烷裂解法的反应机理以及各种高阶硅烷物性参数的基础上,本发明提出采用等离子球磨对硅粉和催化剂进行加工,同时使甲硅烷裂解并与粉体接触进行反应生成高阶硅烷。
技术实现要素:9.为解决上述问题,本发明提供一种利用等离子球磨裂解合成高阶硅烷的方法,通过等离子球磨对硅粉进行活化,并同时令甲硅烷发生裂解产生自由基,促进自由基在硅粉表面发生重组反应并连续生成高阶硅烷。
10.本发明的目的是提供一种利用等离子球磨裂解合成高阶硅烷的方法,包括以下步骤:步骤一:在密闭的等离子球磨机腔室内装填入硅粉与催化剂粉体,在球磨腔室内施加电场形成等离子区域,辅助进行球磨;步骤二:将甲硅烷气体连续通入等离子球磨机腔室内发生反应,并将反应后的气体连续排出腔室,反应后的气体为高阶硅烷,包括乙硅烷、丙硅烷及丁硅烷;等离子球磨机腔室内的压力为0.05~1mpa、温度为150~400℃。
11.进一步改进在于:所述等离子球磨腔室内施加的电场采用介质阻挡放电的方式。
12.进一步改进在于:所述等离子球磨机腔室的放电气体为氢气、氦气、氖气、氩气、氪气及氙气中的一种或几种。
13.进一步改进在于:所述硅粉平均粒径为1~500μm。
14.进一步改进在于:所述催化剂粉体为锂、铁、钴、镍、铜、钯中的一种或几种。
15.进一步改进在于:所述催化剂粉体的平均粒径范围1~500μm。
16.进一步改进在于:所述催化剂粉体与所述硅粉的质量比为1:2~1:20。
17.进一步改进在于:所述甲硅烷气体温度为0~250℃。
18.本发明的有益效果:根据本发明连续合成高阶硅烷的方法,以等离子球磨辅助裂解反应的形式克服了现有甲硅烷裂解合成高阶硅烷工艺的主要瓶颈问题,即采用介质阻挡放电形式可在接近常压的条件下进行反应,提升了反应速率,并且球磨式反应器可克服现有工艺生成大量硅粉对设备造成危害的障碍。
19.根据本发明连续合成高阶硅烷的方法,通过添加硅粉参与裂解反应,促使甲硅烷裂解产生的自由基与活性硅粉表面结合,从而使反应向生成更多高阶硅烷的方向进行。
20.根据本发明连续合成高阶硅烷的方法,等离子球磨腔室内装填的硅粉与甲硅烷裂解的副产物硅粉可形成动态平衡,因此工艺可实现连续化长周期的稳定运行。
附图说明
21.图1是具体实施方式的合成系统示意图。
22.其中:1-甲硅烷进口,2-等离子球磨腔室,3-电极,4-介质阻挡层,5-磨球,6-硅粉与催化剂粉体,7-硅烷出口,8-粗分精馏塔,9-甲硅烷精馏塔,10-乙硅烷精馏塔,11-重组分精馏塔。
具体实施方式
23.为了加深对本发明的理解,下面将结合实施例对本发明作进一步详述,该实施例仅用于解释本发明,并不构成对本发明保护范围的限定。
24.实施例一如图1所示,采用腔室容积为15l、额定功率为10kw的等离子球磨机,往等离子球磨腔室2内装填5kg硅粉与0.5kg铜粉,以0.07mpa的氩气作为初始放电气体。开启等离子球磨60分钟后,从甲硅烷进口1以1.5g/min的流量通入压力为0.07mpa的甲硅烷,连续运行24小时。之后得到的气体从硅烷出口7出来先通过粗分精馏塔8进行精馏;粗分精馏塔8顶的气体进入到甲硅烷精馏塔9内,甲硅烷精馏塔9底采出甲硅烷,甲硅烷精馏塔9顶采出氢气;粗分精馏塔8底的气体进入乙硅烷精馏塔10内,乙硅烷精馏塔10顶采出乙硅烷;乙硅烷精馏塔10底的气体进入到重组分精馏塔11内,重组分精馏塔11顶采出丙硅烷、重组分精馏塔11底采出丁硅烷;结果如下:甲硅烷进料总质量:2160克;甲硅烷总采出:1392克乙硅烷总采出:596克丙硅烷总采出:347克丁硅烷总采出:149克产物硅烷总质量:2484克反应结果表明,有320克硅粉参与反应生成了硅烷类气体。
25.实施例二如图1所示,采用腔室容积为15l、额定功率为10kw的等离子球磨机,往等离子球磨腔室2内装填5kg硅粉与0.5kg钯粉,以0.09mpa的氢气作为初始放电气体。开启等离子球磨60分钟后,从甲硅烷进口1以2g/min的流量通入压力为0.09mpa的甲硅烷,连续运行24小时。之后得到的气体从硅烷出口7出来先通过粗分精馏塔8进行精馏;粗分精馏塔8顶的气体进入到甲硅烷精馏塔9内,甲硅烷精馏塔9底采出甲硅烷,甲硅烷精馏塔9顶采出氢气;粗分精馏塔8底的气体进入乙硅烷精馏塔10内,乙硅烷精馏塔10顶采出乙硅烷;乙硅烷精馏塔10底的气体进入到重组分精馏塔11内,重组分精馏塔11顶采出丙硅烷、重组分精馏塔11底采出丁硅烷;结果如下:甲硅烷进料总质量:2880克;甲硅烷总采出:1827克乙硅烷总采出:984克丙硅烷总采出:422克丁硅烷总采出:281克产物硅烷总质量:3514克反应结果表明,有611克硅粉参与反应生成了硅烷类气体。
26.由以上实施例结果可知:利用等离子球磨裂解合成高阶硅烷的方法,甲硅烷的利用率高,合成得到的乙硅烷、丙硅烷和丁硅烷的总质量相比于原料硅粉的质量,利用率高,产出率高。
27.以上实施例采用等离子球磨对硅粉和催化剂进行加工,同时使甲硅烷裂解并与粉体接触进行反应生成高阶硅烷。一方面,通过研究发现,甲硅烷裂解制备高阶硅烷的反应过程中,自由基重排形成高阶硅烷的反应与高阶硅烷受热分解的反应同时进行,而反应温度升高可同时促进甲硅烷裂解生成自由基以及高阶硅烷热分解生成硅粉的过程。因此,提出利用非平衡状态的介质阻挡放电等离子体促进甲硅烷的裂解,使反应区域整体宏观温度较低,可抑制生成的高阶硅烷分解,而同时又可在等离子体内高能粒子轰击作用下产生足够数量的自由基。另一方面,利用等离子球磨的方式对硅粉及催化剂同时进行机械破碎以及局部的不断熔爆、碎裂等过程,使硅粉纳米化且具备较高的表面能和化学反应活性,可促进与甲硅烷裂解产生的自由基发生化学键合并进入气相主体并结合生成高阶硅烷。通过研究发现,由于甲硅烷裂解反应过程将同时生成副产物硅粉,其与球磨腔室内的硅粉消耗可形成动态平衡,反应过程可连续稳定运行,从而实现长周期连续化生产。