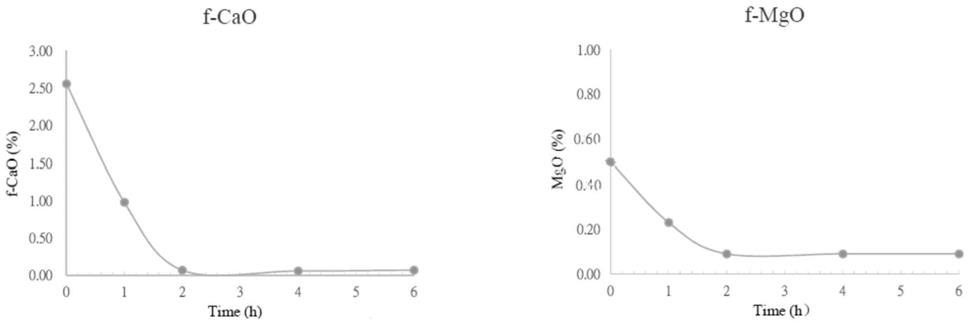
1.本发明涉及钢渣安定化处理方法,属于钢渣处理领域。
背景技术:2.钢渣是在1550℃以上的炼钢过程中,由金属炉料中各种元素被氧化后生成的氧化物、被侵蚀的炉衬和补炉材料、金属炉料带入的杂质如泥砂和特意加入的造渣材料,如石灰石、白云石、萤石、铁矿石、硅石等所形成的固体废物。在此温度下,一些造渣材料(如石灰石、白云石、萤石等)中的cao和mgo会生成一些早已成为死烧的f-cao和f-mgo,加之钢渣坚硬致密,故在常温较短时间内,这些烧死了的f-cao和f-mgo基本不会吸水消化反应成ca(oh)2和mg(oh)2,故钢渣制品不会产生膨胀开裂。但随着时间推移和延长,暴露在大气中的钢渣制品内的f-cao和f-mgo会慢慢吸收大气中的水分消化生成ca(oh)2和mg(oh)2,因cao吸水反应生成ca(oh)2时会产生1-3倍的体积膨胀,mgo吸水反应成mg(oh)2时会产生100~200%的体积膨胀,造成钢渣的体积不安定性,使已制成的钢渣制品发生膨胀开裂。
3.目前国内钢渣处理主要工艺有:热泼法、风淬法、滚筒法、粒化轮法、热闷法等,但是上述方法存在各种问题,普遍存在处理后的钢渣安定性不合格,导致应用面很窄而主要以堆存为主。
4.住友金属曾经采用过高温低压蒸汽下对钢渣进行陈化处理的方案,蒸汽压为0.5mpa。虽然该方案使钢渣的浸水膨胀率控制在了0.5%以下,但是处理后的钢渣压蒸粉化率会大于3%,仅能用于道路基层材料和沥青路面材料,不能用于建材及建材制品,因此,日本住友开发的钢渣处理工艺现在已经被渐渐停用。
技术实现要素:5.为消除钢渣体积不安定性,本发明提出一种钢渣处理方法,使钢渣中的f-cao和f-mgo在制成钢渣制品前吸水反应完成体积膨胀。
6.钢渣安定化处理方法:在高温高压饱和蒸气下,对钢渣进行蒸压处理;其中,蒸气压≥2.0mpa,温度为≥211.38℃。
7.在一种实施方式中:所述蒸气为水蒸气。
8.在一种实施方式中:蒸气压为2.0~2.5mpa。
9.在一种实施方式中:蒸压时,先升温至211.38℃以上,再恒温至少2h,再降至常温。
10.在一种实施方式中:蒸压恒温时间为4~6h。
11.在一种实施方式中:蒸压过程中,升温时间为1~1.5h,降温时间为1~1.5h。
12.在一种实施方式中:钢渣包括各种炉型的钢渣原渣和钢渣尾渣、或通过热泼法、风淬法、滚筒法、粒化轮法、热闷法处理后的钢渣尾渣。
13.在一种实施方式中,钢渣处理前,破碎至粒度≤10mm。
14.本发明的有益效果:
15.1、产品处理彻底:钢渣尾渣体积膨胀彻底消除,到达材料使用的要求,克服了热闷
法、热泼法、风淬法、滚筒法、粒化轮法处理钢渣无法达到安定性使用要求的问题。
16.2、大幅降低生产成本:采用密闭高压蒸汽养护工艺,使处理能耗最低,大幅降低生产成本。
17.3、生产规模生产场地不受限制:热闷法、热泼法、风淬法、滚筒法、粒化轮法等必须在钢铁企业内部设置,高压蒸压工艺可以在钢铁企业内部,也可单独集中处置。
18.4、文明生产,洁净排放:钢渣尾渣工业废弃物综合利用本是环保项目,安定化处理生产线没有废气废渣排放,压蒸装置冷凝水处理后可使用。
19.说明书附图
20.图1为钢渣用2.0mpa饱和蒸气蒸压时,f-cao、f-mgo含量与蒸压时间的关系图。
具体实施方式
21.钢渣安定化处理方法:在高温高压饱和蒸气下,对钢渣进行蒸压处理;其中,蒸气压≥2mpa,温度为≥211.38℃。
22.本发明首次采用饱和蒸汽高温高压养护钢渣,快速促进钢渣尾渣中的f-cao和f-mgo吸收水分完成生成ca(oh)2和mg(oh)2的过程,使其体积只在预处理过程中膨胀,后期不再膨胀,彻底消除钢渣大规模综合利用的最大障碍。并且钢渣在膨胀力、热胀应力和水的锲入力等作用下破裂成颗粒或粉状,也大大减少粉碎磨细的电耗,节约了能源。
23.如果蒸气压低于2mpa,会有2点问题:
①
f-cao、f-mgo水化反应不充分,达不到建筑材料应用要求;
②
达到同样质量需要处理时间大大增加,工业化生产不经济。
24.在一种实施方式中:所述蒸气为水蒸气。
25.在一种实施方式中:蒸气压为2.0~2.5mpa。
26.在一种实施方式中:蒸压时,先升温至211.38℃以上,再恒温至少2h,再降至常温。
27.在一种实施方式中:蒸压恒温时间为4~6h。
28.在一种实施方式中:升温时间为1~1.5h;降温时间为1~1.5h。
29.在一种实施方式中,钢渣包括各种炉型的钢渣原渣和钢渣尾渣、或通过热泼法、风淬法、滚筒法、粒化轮法、热闷法处理后的钢渣尾渣;其中,各种炉型包括转炉和电炉。
30.在一种实施方式中,钢渣处理前,破碎至粒度≤10mm,目的是为了加速饱和蒸汽渗透,加快安定化处理时间。
31.本发明处理后的钢渣,其蒸压粉化率≤1.5%(目前国家标准≤5.9%),浸水膨胀率≤0.5%(目前gb/t25824—2010道路用钢渣≤2.0%);钢渣安定性处理后生产产品的压蒸膨胀率≤0.8%(根据gb/t32546—2016《钢渣应用技术要求》中技术要求:压蒸膨胀率≤0.8%)。
32.安定化处理后的钢渣用途:(1)用于水泥混凝土的细骨料;(2)普通预拌砂浆用主要原料;(3)钢渣微粉;(4)道路基层材料和沥青路面材料;(5)混凝土多孔砖和路面砖用主要原料;(6)泡沫混凝土砌块用主要原料等。
33.下面结合实施例对本发明的具体实施方式做进一步的描述,并不因此将本发明限制在所述的实施例范围之中。
34.实施例
35.1、将钢渣尾渣经过初碎、细碎、除铁等一系列加工,使钢渣尾渣颗粒粒度≤10mm;
36.2、将步骤1处理后的钢渣尾渣送到压蒸装置,控制压蒸装置的蒸气压为2mpa;蒸压温度为211.38℃,蒸压时间为6h(升温时间为1.5h,恒温时间为3.5h,降温时间为1h),得到体积安定化的钢渣。
37.结果评估:
38.a、环保:无废气废水排放,粉尘大气排放≤30mg/nm3。
39.b、成本:蒸汽用量为120kg/t钢渣,电耗3.6kwh/t钢渣,水耗0.2t/t钢渣。
40.c、处理后的钢渣性能:压蒸粉化率为1.1%;浸水膨胀率为0.45%;压蒸膨胀率为0.6%。
41.其中,压蒸粉化率、浸水膨胀率按照《钢渣稳定性试验方法》gb/t24175-2009进行测定;压蒸膨胀率按照yb/t4228-2010测定。
42.由本发明的试验数据可知,本发明的压蒸粉化率符合标准yb/t 4201《普通预拌砂浆用钢渣砂》中要求的压蒸粉化率≤5.9%;浸水膨胀率符合标准gb/t25824—2010《道路用钢渣》和yb/t 801-2008《工程回填用钢渣》中要求的浸水膨胀率≤2.0%;压蒸膨胀率符合yb/t4228-2010《混凝土多孔砖和路面砖用钢渣》以及gb/t32546—2016《钢渣应用技术要求》中的技术要求压蒸膨胀率≤0.8%。
43.本发明的试验方法已经多次试验并得到验证,处理后的钢渣指标大大优于压蒸粉化率≤5.9%;浸水膨胀率≤2.0%;压蒸膨胀率≤0.8%标准。除了用于道路基层材料和沥青路面材料外,钢渣的资源化利用应以消纳钢渣的巨大产量为目的,应着重放在建筑和建材行业,在骨料、水泥混凝土掺和料、干混砂浆、路面和建材制品中的利用。特别是骨料行业和干混砂浆不仅适用范围广,而且需求量大,能够消化钢渣的巨大产量。本发明成为可能。