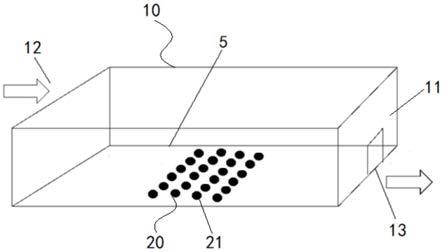
1.本发明涉及玻璃熔化澄清技术领域,具体涉及一种适用超高铝盖板玻璃和透明微晶玻璃的熔化澄清方法。
背景技术:2.2007年之后,智能手机和平板电脑开始大量涌现,带动了电容式触控屏的蓬勃发展,为了增强触控屏表面的抗划伤性能,减少智能手机和平板电脑的跌落损伤,一种可化学增强的超薄碱铝硅酸盐玻璃迅速成为玻璃新宠,引起全球玻璃科技工作者和生产商的广泛关注和工业生产及应用。
3.化学增强型超薄碱铝硅酸盐玻璃主要用于屏幕保护功能,使用在显示屏幕表面,俗称盖板保护玻璃,碱成盖板玻璃;根据化学强化次数,也会称作一强玻璃(进行一次化学强化处理)和二强玻璃(进行两次化学强化处理),这类玻璃体系均属于碱铝硅玻璃,主要依靠al2o3、zro2、mgo等氧化物来获得高弹性模量和高维氏硬度。sio2主要用来提供必要的网络结构和必要的理化性能,碱金属氧化物(r2o,包括li2o、na2o、k2o)促进玻璃熔化,提供离子交换的必要物质基础,其它组成是根据玻璃性能需要进行优化选择。
4.随着整机厂商和消费者对盖板保护玻璃的抗摔性能和抗划伤性能不断提出新的要求,玻璃研发者和生产制造商大多通过提升al2o3用量的技术方案来解决;以至于al2o3在玻璃中的用量从最初的5wt%提升到25wt%-27wt%,未来将有可能提升至氧化铝临界用量35wt%。基于氧化铝在盖板玻璃中的质量含量不同,将盖板保护玻璃分为低铝盖板玻璃(5wt%≤m<8wt%)、中铝盖板玻璃(8wt%≤m<13wt%)、高铝盖板玻璃(13wt%≤m<24wt%)、超高铝盖板玻璃(≥24wt%),所以超高铝盖板玻璃就成了屏幕保护材料发展主流趋势。为了进一步提升与改善超高铝盖板玻璃的硬度与抗摔性能,研发者提出透明微晶玻璃解决方案,同样基于碱铝硅盖板玻璃组成体系,在玻璃组成中添加晶核剂,并对其进行晶化处理,内部形成不超过50nm的微小晶体,可以大幅改善玻璃材料的断裂韧性,使断裂韧性提升3倍-6倍,既能保持玻璃的良好透明性,又能解决了盖板玻璃抗摔性能;将厚度0.6mm透明微晶玻璃应用在智能手机保护盖板,整机跌落破损高度可以超过2米。
5.al2o3固然可以实现超高铝盖板玻璃与微晶盖板保护玻璃的抗划伤性能与抗跌落性能改善,但是由于al2o3熔点高达2045℃,依据玻璃性能加和理论,自然会导致盖板保护玻璃的熔化温度提高。按目前全球所掌握的玻璃熔化技术手段,熔窑的耐火材料极大地限制了玻璃的最高熔化温度,一般很难超过1650℃;另外,al2o3也是大幅增加玻璃熔体表面张力重要成分,随着玻璃中al2o3用量增加,必然导致上述两类盖板保护玻璃的熔体表面张力参数增加,普通钠钙玻璃的熔体表面张力仅为(330-340)mn/m(毫牛每米),而超高铝盖板玻璃或透明微晶玻璃的熔体表面张力则高达(410-430)mn/m(毫牛每米);相对于高铝盖板保护玻璃的表面张力(370-390)mn/m(毫牛每米)增加10%以上,这会对对玻璃的超薄成型产生很大的影响,因为薄型化生产过程必须克服表面张力的回缩作用,另外还会导致玻璃的澄清不良,玻璃制品中的气泡缺陷增多。
6.目前,设计开发的超高铝盖板保护玻璃和透明微晶玻璃的熔化温度上限一般控制在1610℃-1630℃,几乎是现有玻璃熔窑的极限熔化温度,所以超高铝盖板保护玻璃和透明微晶玻璃在生产制造过程中,普遍会遇到玻璃黏度大、熔化温度高、澄清困难、料性短、成形难等一系列技术难题。
7.为了促进超高铝盖板保护玻璃和透明微晶玻璃的熔化与澄清,普遍依赖于电助熔和澄清剂这两种主要技术手段。电助熔技术诞生于20世纪初期,成熟应用于20世纪20年代,通常将钼金属电极插入玻璃液,通入工频(50hz)交流50v-200v电源,利用玻璃液在高温时离子导电特性,产生焦耳热效应,促进玻璃自身熔化,提高了熔化效率。
8.虽然钼电极具有很多优良特性,但是其致命缺点就是容易氧化,在空气或氧化条件450℃以上就会快速氧化,如果配合料使用了氧化型澄清剂或氧化性原料,将会导致钼电极快速氧化消耗掉。为了规避钼电极的氧化问题,澄清剂仅能选择使用氯化物澄清剂,比如氯化钠、氯化钙等,但是氯化钠澄清作用机理属于高温挥发型,一般需要熔化温度大于1465℃才能发挥作用,由于氯化钠在玻璃熔体的饱和度相对较低,氯化钠产生过量气体会以气泡形式滞留在玻璃熔体中,不能被快速吸收,最终导致玻璃内产生较多大小不一的气泡,应用于显示屏的盖板保护玻璃的气泡尺寸必须小于0.1mm,这是显示像素点的最大尺寸,并且每平方米要求小于3个,因此氯化钠澄清就不能应用在超高铝盖板保护玻璃和透明微晶玻璃。在低铝盖板玻璃、中铝盖板玻璃、高铝盖板玻璃的在火焰炉或全氧炉熔化条件下,常使用硫酸钠作为澄清剂,但是硫酸钠属于氧化型澄清剂,分解温度范围为1288℃~1428℃,而对于超高铝盖板保护玻璃和透明微晶玻璃的熔化澄清温度范围处在1540℃-1630℃,两者之间没有任何温度重合范围,即使采用纯火焰熔化方式,硫酸钠也不能满足超高铝盖板保护玻璃和透明微晶玻璃的澄清需要。
9.如果采用钼电极对超高铝盖板保护玻璃和透明微晶玻璃进行电助熔熔化,硫酸盐的分解形成的氧化性气体的二氧化硫(so2)和氧气(o2)也必然会导致钼电极会被很快氧化消耗掉,因此,钼电极在熔化具有氧化性配合料是不可行的,现在常用的氧化性澄清剂包括硫酸钙、硫酸钠、氧化锡、硝酸盐、氧化铈等。
10.为了促进难熔玻璃的澄清,很多机构提出使用复合澄清剂方案,将不同种类的澄清剂,比如氧化型、挥发型、分解型进行混合,分别在玻璃配合料熔化的低温、中温、高温阶段发挥作用,比如将氯化钠、硫酸盐(硫酸钙)、变价氧化物(氧化铈及氧化锡)、氧化锌进行复合使用,使用比例为(0.15~0.35):(0.1~3.0):(0.1~0.5):(1~3),其加入量为玻璃液质量2%~4.5%,这样一个较为复杂的澄清剂方案,用于超高铝盖板保护玻璃和透明微晶玻璃,发现其澄清效果并不理想,根本无法达到超高铝盖板保护玻璃和透明微晶玻璃的光学级质量要求。
11.目前,国内外在低铝盖板保护玻璃、中铝盖板保护玻璃、高铝盖板保护玻璃生产制造方面已经基本解决了上述难题,但是超高铝盖板保护玻璃和透明微晶玻璃的熔化澄清问题未能取得很好的突破。
技术实现要素:12.针对现有技术中存在的上述问题,本发明提供一种适用超高铝盖板玻璃和透明微晶玻璃的熔化澄清方法。
13.本发明公开了一种适用超高铝盖板玻璃和透明微晶玻璃的熔化澄清方法,该熔化澄清方法在超高铝盖板保护玻璃和透明微晶玻璃池窑中进行,包括:
14.在距池窑后墙30%-60%范围内的池壁和/或池底上,布设4排~8排氧化锡电极且相邻两排氧化锡电极的间距为300mm-600mm;
15.向超高铝盖板玻璃或透明微晶玻璃配合料中加入硫酸锶澄清剂,且硫酸锶澄清剂的加入量为配合料质量的0.2%~1.0%。
16.作为本发明的进一步改进,多排所述氧化锡电极垂直于玻璃液的流向横向布设。
17.作为本发明的进一步改进,每排所述氧化锡电极的电极块之间连通或分离设置,若分离设置,则相邻所述电极块之间的距离为300mm~500mm。
18.作为本发明的进一步改进,所述氧化锡电极采用交流供电,电压为50v~200v,交流频率为10khz~100khz。
19.与现有技术相比,本发明的有益效果为:
20.本发明通过选择氧化锡电极以及氧化锡电极布设位置、参数等设计,并配合使用硫酸锶澄清剂,使超高铝盖板保护玻璃和透明微晶玻璃澄清效果可以达到最佳;经过系统应用与验证,超高铝盖板保护玻璃和透明微晶玻璃气泡数量可以稳定地控制在(4-8)个/10kg玻璃,有效实现了超高铝盖板保护玻璃和透明微晶玻璃高质量熔化澄清目标,使困扰超高铝盖板保护玻璃和透明微晶玻璃熔化澄清问题得到了很好地解决。
附图说明
21.图1为本发明一种实施例公开的氧化锡电极在池窑中的布设示意图;
22.图2为硫酸锶澄清剂的受热分解示意图;
23.图3为本发明实施例1熔化澄清后所制得玻璃试样的显微示意图;
24.图4为本发明比较例1熔化澄清后所制得玻璃试样的显微示意图。
25.图中:
26.10、池窑;11、池窑后墙;12、投料口;13、流液洞;20、氧化锡电极;21、电极块。
具体实施方式
27.为使本发明实施例的目的、技术方案和优点更加清楚,下面将结合本发明实施例中的附图,对本发明实施例中的技术方案进行清楚、完整地描述,显然,所描述的实施例是本发明的一部分实施例,而不是全部的实施例。基于本发明中的实施例,本领域普通技术人员在没有做出创造性劳动的前提下所获得的所有其他实施例,都属于本发明保护的范围。
28.下面结合附图对本发明做进一步的详细描述:
29.本发明提供一种适用超高铝盖板玻璃和透明微晶玻璃的熔化澄清方法,该熔化澄清方法在超高铝盖板保护玻璃和透明微晶玻璃池窑中进行,其包含必要的熔化方式和合理的澄清剂及用量;
30.具体的:
31.如图1所示,本发明的池窑10包含池窑前墙和池窑后墙11,池窑前墙上设有投料口12、池窑后墙11上设有流液洞13;本发明采用氧化锡电极20作为电助熔电极,应用于超高铝盖板保护玻璃和透明微晶玻璃池窑中。本发明选用氧化锡电极20的原因在于:氧化锡电极
属于无机非金属材料,具有极强抗氧化能力,能够适用具有氧化性的配合料,为使用氧化性澄清剂创造了先决条件,另外氧化锡电极的熔点高达1630℃,沸点1800℃,其熔点温度与超高铝盖板保护玻璃和透明微晶玻璃的熔化温度1610℃~1630℃相当,因此氧化锡电极是超高铝盖板保护玻璃和透明微晶玻璃电熔化最佳电极材料。
32.本发明的氧化锡电极20的布设方式为:
33.如图1所示,在距池窑后墙11的30%-60%范围内的池底上布设4排~8排氧化锡电极20,同时,也可布设在30%-60%范围内的池壁上或布设在30%-60%范围内的池壁和池底上;其中,30%-60%的范围是指距池窑后墙0.3l~0.6l的范围,l为前墙与后墙的距离。本发明的多排氧化锡电极20垂直于玻璃液的流向横向布设,相邻两排氧化锡电极的间距为300mm-600mm。本发明每排氧化锡电极20的电极块21之间可连通或分离设置,若分离设置,则相邻电极块21之间的距离为300mm~500mm。
34.本发明的氧化锡电极采用交流供电,电压为50v~200v,交流频率为10khz~100khz;由于低频交流电会导致玻璃熔体中的离子(li
+
、na
+
、k
+
、mg
2+
等)产生极化现象,采用高频交流熔化玻璃可以有效抑制玻璃熔体在电极表面的极化作用,防止玻璃熔体中的羟基产生气泡富集在电极表面,最终形成较大气泡时受浮力作用进入到玻璃液中,进而破坏玻璃液澄清质量。
35.多排布置的氧化锡电极可以延缓了玻璃液流向前移动速度,能够有效延长熔化时间,有利于玻璃熔化池内产生环流,迫使气泡上浮,锡电极周边属于强电场作用,产生较强的焦耳作用,玻璃熔体温度较高,产生向上环流作用,将气泡上浮速率提高,起到类似鼓泡的澄清作用。
36.本发明选用硫酸锶澄清剂作为超高铝盖板玻璃和透明微晶玻璃的澄清剂,其选择原理为:
37.经研究发现适用超高铝盖板保护玻璃和透明微晶玻璃澄清剂的分解温度应与玻璃液熔化澄清温度范围相一致,玻璃液熔化澄清温度范围一般以t2温度(玻璃黏度100泊对应的温度)及t2.5温度(玻璃黏度320泊对应的温度)之间的温度为基准,按此基准,超高铝盖板保护玻璃和透明微晶玻璃的最适宜的澄清温度范围应为1540℃~1630℃,经过研究发现硫酸锶刚好在1480℃之后开始快速分解,释放so2气体,直至1580℃全部分解(见附图2所示);因此硫酸锶分解温度范围1480℃-1580℃与超高铝盖板保护玻璃和透明微晶玻璃的澄清温度1540℃~1630℃,具有40℃(1540℃~1580℃)重合区域范围。而传统硫酸钠澄清剂的分解温度不能与超高铝盖板保护玻璃和透明微晶玻璃的澄清温度产生重合区域范围,所以导致其不能对超高铝盖板保护玻璃和透明微晶玻璃澄清的原因。
38.除了硫酸锶澄清剂分解温度与超高铝盖板保护玻璃和透明微晶玻璃澄清温度具有重合区域范围,这是满足澄清的必要条件之一,另外还需要控制硫酸锶的最佳用量也十分关键,硫酸锶澄清剂在超高铝盖板保护玻璃和透明微晶玻璃配合料最佳用量0.2wt%~1.0wt%。
39.实施例:
40.41.[0042][0043]
实验:
[0044]
本发明将实施例1与比较例1的澄清方法所澄清后的玻璃液制成玻璃试样,本发明10kg玻璃中的气泡数量共计8个;而,比较例中10kg玻璃中的气泡数量共计47个。
[0045]
同时,为便于对实验结果的直接比对以及显微图的清楚显示,如图3所示,在一块300g的玻璃试样中,本发明的玻璃试样中无气泡;而,如图4所示,在一块300g的玻璃试样中,比较例1的玻璃试样中的气泡数量为3个。
[0046]
同时,按照上述相同的测试方法,依次观测记录实施例2~15、比较例2~3中的气泡数量。
[0047]
结论:
[0048]
本发明通过选择氧化锡电极以及氧化锡电极布设位置、参数等设计,并配合使用硫酸锶澄清剂,使超高铝盖板保护玻璃和透明微晶玻璃澄清效果可以达到最佳;经过系统应用与验证,超高铝盖板保护玻璃和透明微晶玻璃气泡数量可以稳定地控制在(4-8)个/10kg玻璃,有效实现了超高铝盖板保护玻璃和透明微晶玻璃高质量熔化澄清目标,使困扰超高铝盖板保护玻璃和透明微晶玻璃熔化澄清问题得到了很好地解决。
[0049]
以上仅为本发明的优选实施例而已,并不用于限制本发明,对于本领域的技术人员来说,本发明可以有各种更改和变化。凡在本发明的精神和原则之内,所作的任何修改、等同替换、改进等,均应包含在本发明的保护范围之内。