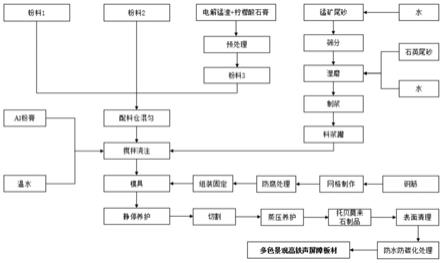
1.本发明属于高铁声屏障技术领域,尤其涉及一种利用固废制备富含硅酸钙相 多色景观高铁声屏障的方法。
背景技术:2.由于列车在高速运行时,车头快速挤压两边及其前方的空气,会使气流会对 列车底部形成一定的上升压力,造成列车一定程度上的悬浮。这不仅影响了居民 的生活环境,还给列车的运行带来了安全隐患。而在铁路两旁设置声屏障,形成 相对封闭的空间改善车底的上升空气压力,同时降低列车沿线交通噪声的污染。
3.根据声屏障材料的相关特性可分为不透明类和透明类。其中,透明类声屏障 由于环境的适应性弱且成本高,不宜大规模应用。不透明类声屏障分为金属类和 非金属类。金属声屏障在长期的雨水及化学介质等的侵蚀下,逐渐腐蚀生锈,使 得声屏障内部结构遭到破坏影响了其正常工作,需要经常维修和维护,大大增加 了工人工作量,增加运营成本。非金属声屏障与金属声屏障相比较,具有制作工 艺简单、制作和维护费用低、适应环境能力强且坚固牢靠的优点。总之,非金属 声屏障隔音强度高、造价低、具有广阔的市场前景和发展空间,发展非金属声屏 障项目势在必行。混凝土声屏障是非金属声屏障中最常用的一种。而目前通用的 混凝土声屏障厚度均为0.1m左右,其单位长度的重量能达到200~300kg/m左右, 这类的声屏障安装十分不便,必须配备重型机械才能完成。
4.如何制备出一种轻质绿色高强、全天候露天防腐且满足各方面性能的声屏障 成为亟待我们解决的技术问题。
技术实现要素:5.本发明为了克服现有声屏障技术中的不足,提供一种利用固废制备富含硅酸 钙相多色景观高铁声屏障的方法,所制备的高铁声屏障材料美观大方,制作精致, 运输、安装方便,造价低,使用寿命长,隔声降噪性能优异,特别适用于高速铁 路、高速道路和城市轻轨、地铁的防噪声使用,是现代化交通理想的隔声降噪材 料。
6.本发明一种利用固废制备富含硅酸钙相多色景观高铁声屏障的方法,包括以 下步骤:
7.s1、双氰胺废渣的预处理:首先将双氰胺废渣置于电热干燥箱烘干,然后在 干燥空气中冷却,再经粉磨使物料的比表面积达到300~400m2/kg;
8.s2、废光伏板预处理:将废光伏板的玻璃破碎至2~5mm颗粒,破碎后的颗粒 粉磨至比表面积200~350m2/kg;
9.s3、精炼渣预处理:将精炼渣置于105℃烘箱内烘干12h至恒重,再采用 行星式球磨机进行分散,使物料的比表面积达到200~350m2/kg;
10.s4、高炉瓦斯灰预处理:将高炉瓦斯灰堆放阴凉通风处晾干,使其含水量小 于10%,再将其置于电热干燥箱烘干,然后在干燥空气中冷后采用行星式球磨机 进行分散,
使物料的比表面积达到300~450m2/kg;
11.s5、钢渣预处理:钢渣经颚式破碎机破碎至2~5mm颗粒后,置于电热干燥箱 烘干,然后置于球磨机中粉磨至比表面积200~350m2/kg;
12.s6、压制成型:将预处理后的双氰胺废渣粉、废光伏板粉、精炼渣、高炉瓦 斯灰和钢渣按重量百分比:76~82%:6~11%:5~8%:0.1~4%:0.1~3.5%的比例混 合,采用行星式球磨机进行混匀,将搅拌均匀干料混合物加入其质量8~11%的水, 然后将混合料放入模具,经液压压力机压制成尺寸φ30mm
×
20mm的球团, 将球团置于100℃电热烘干箱中烘干40min;
13.s7、高温煅烧:干燥后的球团置于马弗炉内煅烧,煅烧制度为:由室温升至 800℃,升温速率为0.5℃/min,而后保温20min;再由800℃升至1150℃~1300℃, 升温速率为3.5℃/min,而后保温30~60min;煅烧完成后降温至1000℃~1100℃ 时取出试样,取出的试样经鼓风急冷至室温,得到烧制成型的试样;
14.s8、球磨处理:将磷石膏置于电热干燥箱中烘干,与步骤s7中烧制成型的 试样混合,所述磷石膏用量为烧至成型试样质量的6~10%,再置于水泥球磨机中 粉磨至比表面积350~400m2/kg,得到粉料1备用;
15.s9、废贝壳的预处理:首先将废贝壳进行筛选,筛除废贝壳中杂质,而后将 废贝壳放入转筒洗石机中进行清洗,清洗后的废贝壳晾干后置于电热干燥箱烘 干,烘干后的贝壳经颚式破碎机中破碎至1~3cm,而后置于马弗炉内煅烧,煅烧 制度为:由室温升至300℃,升温速率为1℃/min,而后保温30min;再由300℃ 升至800℃~900℃,升温速率为3℃/min,而后保温60~120min;煅烧完成后鼓 风冷却至100℃时取出试样;再将冷却至室温的废贝壳放入水泥球磨机中粉磨至 比表面积350~500m2/kg,得到粉料2;
16.s10、电解锰渣+柠檬酸石膏的预处理:将电解锰渣和柠檬酸石膏分别置于电 热干燥箱中烘干1,烘干后的电解锰渣和柠檬酸石膏按照质量比1:1放入水泥球 磨机中粉磨至比表面积300~400m2/kg,得到粉料3;
17.s11、锰矿尾砂+石英尾砂的预处理:首先将锰矿尾砂使用水力旋流器进行筛 分,保持其料浆浓度为30-40%,而后将筛分后颗粒尺寸大于0.074mm锰矿尾砂 和石英尾砂按比例50~70%:30~50%混合后,进行湿法混磨,保持料浆浓度为 65-75%,湿磨至比表面积350~500m2/kg,得到尾矿料浆;
18.s12、钢筋的预处理:将φ4钢筋经过冷拉、除锈、调直、切断后,点焊5cm
ꢀ×
5cm钢筋网,而后将钢筋网放入防腐涂料池中浸泡15~30min,取出后晾干;将 经过防腐处理的钢筋网,按相对位置和工艺尺寸放入磨具中,并将其固定;
19.s13、浇注成型:将粉料1、粉料2、粉料3和尾矿料浆分别按质量比7~12: 20~26:4~8:78~100加入搅拌缸中,混合均匀,加入干料总量50-65%的温水, 再加入总用水量4.5~11.5
‰
的稳泡剂,搅拌90~160s,之后加入干料总重量 0.5~0.65
‰
的铝粉膏再搅拌30~60s,得到混合均匀的料浆,搅拌过程中设置保 温措施,保证料浆浇注时的入模温度在45~50℃,浇注入模具中;
20.s14、制品养护:将s13中浇注入模的料浆,进行静停发气、预养护、坯体 切割,高温蒸压养护,得到富含硅酸钙相的板材制品;其中,静停发气和预养护 时间为3-5小时,预养护温度为45~70℃;高温蒸压养护的流程为:密闭、抽真 空、升温至170~195℃,蒸压压力
1.2~1.4mpa,保持5~9h,再降至常温常压;
21.s15、防水防碳化处理:首先将硅酸钙相板材制品风干,表面清理,然后进 行防水防碳化处理,再用彩色渗透型有机加固剂进行雾化喷涂2遍,喷涂后晾干 的制品即为景观高铁声屏障板材。
22.可选地,所述步骤s1中双氰胺废渣干基粒度0.01~0.1mm,主要矿物组成为 方解石,其主要化学成分和含量为:sio25~15%,al2o31~10%,cao 45~70%,fe2o
3 1~5%,mgo 0.01~3%,k2o+na2o 0.01~2%,c 5~20%,烧失量20~40%;所述步骤 s2中废光伏板主要化学成分和含量为:cao 65~85%,sio21~10%,al2o32~6%, feo 0.01~3%,fe2o30.01~5%,mgo 0.01~1%,k2o+na2o 0.01~2%,烧失量15~30%; 所述步骤s3中精炼渣矿物组成为钙铝石(c
12
a7)和水钙铝榴石(c3ah6),主要 化学成分和含量为:主要成分和含量为:cao 35~50%,al2o330~45%,sio21~5%, mgo 2~8%,fe2o31~5%,so31~4%。
23.可选地,所述步骤s4中高炉瓦斯灰的主要化学成分和含量为:sio210~30%, al2o310~30%,fe2o315~45%,mgo 0.1~2%,cao 10~20%,k2o 0.01~1%,na2o 0.1~5%, tio21~8%,烧失量9~15%;所述步骤s5中钢渣的主要化学成分和含量为:sio
2 10~20%,al2o31~7%,fe2o32~33%,mgo 3~12%,cao 30~50%,feo 3~15%,na2o 0.01~3%, k2o 0.01~3%,so30.26%,p2o5 1~6%,烧失量2~10%。
24.可选地,所述步骤s3、s4和s6行星式球磨机分散时间为15~30min,磨机 速率为200r/min。
25.可选地,所述步骤s6中,压制成型的压力为15~30mpa。
26.可选地,所述步骤s8中磷石膏的主要化学成分和含量为:cao35~50%,sio
2 1~4%,al2o30~1.5%,mgo 1~4%,so330~45%,p2o51~6%;所述步骤s9中废贝壳 的主要矿物相为方解石和文石,其主要组成为:caco380~92%,mgco31~10%, ca3(po4)20.01~2%,sio20.01~2%,al2o3+cao+fe2o30.01~2%,烧失量1~12%; 所述步骤s10中电解锰渣的主要化学成分和含量为:sio225~40%,cao 5~15%, al2o35~15%,fe2o30.1~7%,mgo 0.1~3%,mno 0.1~5%,so320~40%,k2o 0.1~3%, na2o 0.01~1%,p2o50.01~1%,tio20.01~1%;所述步骤s10中柠檬酸石膏的主要 化学成分和含量为:cao 32~40%,sio20.1~5%,al2o30.1~3%,mgo 0.1~1%,so
3 35~55%,caf22~7%,k2o 0.01~1%,p2o50.01~1%。
27.可选地,所述步骤s11中锰矿尾砂的主要化学成分和含量为:cao 1~10%, sio235~60%,al2o31~7%,mgo 0.1~4%,mno 10~25%,fe2o35~12%,k2o+na2o 0.01~2%, 烧失量5~10%;所述步骤s11中石英尾砂主要矿物组成为石英,杂质矿物组成为 钠长石、钙长石、黑云母和赤铁矿。主要化学成分和含量为:cao 0.01~3%,sio
2 70~95%,al2o30.1~5%,mgo 0.01~3%,fe2o30.01~2%,so30.01~1%,k2o+na2o 0.01~1%,烧失量0.1~3%。
28.可选地,所述步骤s12中防腐剂由钒钛矿渣、钼尾矿、镍渣、磷酸锌、环氧 锌黄、复合乳液、六偏硅酸钠、助剂、去离子水组成,其对应比例为11.7:4.1: 13.9:0.9:0.6:32.9:1.5:6.1:28.3,ph值9.0~9.5;所述复合乳液由中苯丙 三元共聚物、聚醋酸乙烯和环氧树脂组成,其重量百分比分别对应为 50~65:20~40:5~10,钒钛矿渣、镍渣、钼尾矿的比表面积控制在300~400m2/kg。
29.可选地,所述步骤s13中稳泡剂由三乙醇胺、油酸、去离子水配制而成,其 对应比例为3.1:1.2:38。
30.可选地,所述步骤s15中彩色渗透型有机加固剂为高渗透性界面处理剂,ph 值6~10,由环保型乳液和改性助剂组成,不挥发物≤6%,其表干时间≤2h,拉 伸粘结强度≥0.5mpa,浸水处理的拉伸粘结强度≥0.5mpa。
31.本发明利用固废制备富含硅酸钙相多色景观高铁声屏障,其美观大方,制作 精致,运输、安装方便,造价低,使用寿命长,隔声降噪性能优异,特别适用于 高速铁路、高速道路和城市轻轨、地铁的防噪声使用,是现代化交通理想的隔声 降噪材料。
32.本发明的有益技术效果如下:
33.(1)本发明提供一种高速铁路、高速道路和城市轻轨、地铁用声屏障用板 材的制备方法,以特定的硅酸钙配方直接浇注成匀质声屏障板,经防水防碳化处 理后,可实现机械自动化的联系生产,一体成型,大大降低生产难度和人工的使 用,产品质量稳定,生产成本有效降低。
34.(2)本发明利用多种工业固体废弃物的特性,充分发挥多元固废间的协同 效应。粉料1的制备中能耗较高,利用双氰胺废渣和高炉瓦斯灰中含碳组分特性 (双氰胺废渣热值2000~4500kj,高炉瓦斯灰热值2000~8000kj),有效降低烧 制温度50~150℃,有效降低了能耗;利用双氰胺废渣中富含caco3的特性,以及 废光伏板中高硅特性,有效调控了粉料中目标矿物c3s和c2s的生成,使双氰胺 废渣和废光伏板能得到有效的高值利用;利用精炼渣的高铝特性,补充原料中的 al组分,有效调控了粉料1中c3a生成,使精炼渣中的al组分得到利用;此外, 本发明利用炼钢废弃物高炉瓦斯灰和钢渣中的高铁特性,调控了粉料1中c4af 的生成,同时钢渣中的f-cao也被有效利用。
35.(3)本发明提供一种用于高铁声屏障用板材产品,在物理力学性能(强度 和密度)上,耐久性能(防渗、抗冻性、抗碳化)都有所提高,同时在隔音、吸 声效果上优于市场现有产品。
36.(4)本发明提供一种用于高铁声屏障用板材产品,制备中使用的主要原料 都为工业固体废弃物(双氰胺废渣、废弃光伏板、精炼渣、高炉瓦斯灰、钢渣、 磷石膏、废贝壳、电解锰渣、柠檬酸石膏、锰矿尾砂、石英尾砂),符合国家提 倡的“双碳”发展目标,产品的应用可以促进高铁铁路、高速道路和城市轻轨、 地铁的绿色发展,为工业固体废弃物的大宗和高附加值利用提供新的模式,促进 矿区的可持续和谐发展。
附图说明
37.图1为本发明粉料1的制备流程图。
38.图2为本发明粉料2的制备流程图。
39.图3为本发明利用固废制备富含硅酸钙相多色景观高铁声屏障板的生产工 艺流程图。
40.图4为本发明钢渣的xrd图谱。
41.图5为本发明实施例2中s7步骤不同保温时间试样xrd图谱(a)30min,(b) 40min,(c)50min,(d)60min。
42.图6为本发明实施例2s7步骤不同保温时间试样的光学显微镜图,(a) 30min,(b)
40min,(c)50min,(d)60min。
43.图7为本发明实施例2s7步骤经1250℃煅烧保温40min试样的sem-eds图。
44.图8为本发明s10步骤中石膏的xrd图谱。
45.图9为本发明s11步骤中石英尾砂的xrd图谱。
46.图10为本发明实施例2中s14步骤中硅酸钙相制品的xrd图谱。
47.图11为本发明实施例2中s14步骤中硅酸钙相制品的sem-eds图谱。
具体实施方式
48.以下将配合实施例来详细说明本发明的实施方式,藉此对本发明如何应用技 术手段来解决技术问题,达成技术功效的实现并据以实施。
49.实施例1
50.一种利用固废制备硅酸钙相多色景观高铁声屏障的方法,包括粉料1、粉料 2、粉料3、料浆的制备、钢筋的预处理、浇注成型、高温蒸压、防水防碳化处 理工序。
51.上述硅酸钙相景观高铁声屏障方法,包括以下步骤:
52.s1、双氰胺废渣的预处理:首先将双氰胺废渣置于电热干燥箱烘干12h(烘 干条件105℃),以脱除将双氰胺废渣中的游离水,取出后在干燥空气中冷却, 而后采用水泥球磨机进行粉磨(转速48r/min),使物料的比表面积达到300 m2/kg;
53.s2、废光伏板预处理:首先将废光伏板进行分拆、分拣,挑选出铝质边框、 废塑料、缆线和接头,将废光伏板的玻璃采用颚式破碎机破碎至2~5mm颗粒,破 碎后的颗粒置于水泥球磨机中(转速48r/min),粉磨至比表面积200m2/kg;
54.s3、精炼渣预处理:首先将精炼渣置于105℃烘箱内烘干12h至恒重,保 证含水率不大于0.2%,而后采用行星式球磨机进行分散,使物料的比表面积达 到200m2/kg;
55.s4、高炉瓦斯灰预处理:将高炉瓦斯灰堆放阴凉通风处晾干,使其含水量小 于10%,然后将钢铁尘泥置于电热干燥箱12h烘干处理(烘干条件105℃),以 脱除将高炉瓦斯灰中的游离水,取出后在干燥空气中冷却,而后采用行星式球磨 机进行分散,使物料的比表面积达到300m2/kg;
56.s5、钢渣的预处理:钢渣经颚式破碎机破碎2~5mm颗粒后,而后将钢渣置于 电热干燥箱烘干12h(烘干条件105℃),烘干后放入球磨机中(转速48r/min), 粉磨至比表面积200m2/kg;
57.s6、压制成型:将预处理后的双氰胺废渣粉、废光伏板粉、精炼渣、高炉瓦 斯灰和钢渣按重量百分比:76%:11%:8%:4%:1%的比例混合,采用行星式球磨 机进行混匀。将搅拌均匀干料混合物加入其质量8%的水,然后将混合料放入模 具,经液压压力机压制成球(球团尺寸φ30mm
×
20mm);将球团置于电热烘干 箱中恒温烘干40min(烘干条件100℃);
58.s7、高温煅烧:干燥后的球团置于马弗炉内煅烧,煅烧制度为:由室温升至 800℃,升温速率为0.5℃/min,而后保温20min;再由800℃升至所需温度1150℃, 升温速率为3.5℃/min,而后保温30min;煅烧完成后降温至1000℃时取出试样, 取出的试样经鼓风急冷至室温;
59.s8、球磨处理:将磷石膏置于电热干燥箱中烘干12h(烘干条件105℃), 而后在与烧制成型的试样混合(磷石膏用量为烧至成型试样质量的6%),再置 于水泥球磨机中(转
速48r/min),粉磨至比表面积350m2/kg,得到粉料1备用;
60.s9、废贝壳的预处理:首先将废贝壳进行筛选,筛除废贝壳中杂质,而后将 废贝壳放入转筒洗石机中进行清洗,清洗后的废贝壳晾干后置于电热干燥箱烘干 12h(烘干条件105℃),烘干后的贝壳颚式破碎机中破碎至1~3cm,而后置于马 弗炉内煅烧,煅烧制度为:由室温升至300℃,升温速率为1℃/min,而后保温 30min;再由300℃升至所需温度800℃,升温速率为3℃/min,而后保温60min; 煅烧完成后鼓风冷却至100℃时取出试样;再将冷却至室温的废贝壳放入水泥球 磨机中(转速48r/min),粉磨至比表面积350m2/kg,得到粉料2;
61.s10、电解锰渣+柠檬酸石膏的预处理:将电解锰渣和氟石膏分别置于电热干 燥箱中烘干12h(烘干条件105℃),烘干后的电解锰渣和柠檬酸石膏按照质量 比1:1放入水泥球磨机中(转速48r/min),粉磨至比表面积300m2/kg,得到粉 料3;
62.s11、锰矿尾砂+石英尾砂的预处理:首先将锰矿尾砂使用水力旋流器进行筛 分(料浆浓度30%),而后将筛分后颗粒尺寸大于0.074mm锰矿尾砂和石英尾砂 按比例70%:30%一起湿进行湿法混磨(料浆浓度65%),湿磨后至比表面积 350m2/kg,得到湿磨料浆,磨细后得到的料浆在料浆罐中存放;
63.s12、钢筋的预处理:将φ4钢筋经过冷拉、除锈、调直、切断后,点焊5cm
ꢀ×
5cm钢筋网,而后将钢筋网放入防腐涂料池中浸泡15min,取出后晾干;将经 过防腐处理的钢筋网,按相对位置和工艺尺寸放入磨具中,并将其固定;
64.s13、浇注成型:将粉料1、粉料2、粉料3和尾矿料浆分别按质量比12:20: 8:78加入搅拌缸中,混合均匀,加入干料总量50%的温水,再加入总用水量4.5
‰ꢀ
的稳泡剂,搅拌90s,之后加入干料总重量0.6
‰
的铝粉膏再搅拌30s,得到混 合均匀的料浆,搅拌过程中设置保温措施,保证料浆浇注时的入模温度在45℃, 浇注入模具中;
65.s14、制品养护:将s13中浇注入模的料浆,进行静停发气、预养护、坯体 切割,高温蒸压养护,得到富含硅酸钙相的板材制品;其中,静停发气和预养护 时间为3小时,预养护温度为50℃;高温蒸压养护的流程为:密闭、抽真空、 升温至170℃,蒸压压力1.2mpa,保持9h,再降至常温常压;
66.s15、防水防碳化处理:首先将富含硅酸钙相制品风干,再采用毛刷进行2 遍表面清理,(一次毛刷清理、一次吸尘器清理),将清理后的富含硅酸钙相制 品进行防水防碳化处理,防水防碳化处理的制品采用彩色渗透型有机加固溶剂进 行雾化喷涂2遍,喷涂后晾干的制品可作为多色景观高铁声屏障板材。
67.所述步骤s1中双氰胺废渣干基粒度0.01~0.1mm,主要矿物组成为方解石, 其主要化学成分和含量为:sio25~15%,al2o31~10%,cao 45~70%,fe2o31~5%, mgo 0.01~3%,k2o+na2o 0.01~2%,c 5~20%,烧失量20~40%。
68.所述步骤s2中废光伏板主要化学成分和含量为:cao 65~85%,sio21~10%, al2o32~6%,feo 0.01~3%,fe2o30.01~5%,mgo 0.01~1%,k2o+na2o 0.01~2%, 烧失量15~30%。
69.所述步骤s3中精炼渣矿物组成为钙铝石(c
12
a7)和水钙铝榴石(c3ah6), 主要化学成分和含量为:主要成分和含量为:cao 35~50%,al2o330~45%,sio
2 1~5%,mgo 2~8%,fe2o31~5%,so31~4%。
70.所述步骤s4中高炉瓦斯灰的主要化学成分和含量为:sio210~30%,al2o
3 10~30%,fe2o315~45%,mgo 0.1~2%,cao 10~20%,k2o 0.01~1%,na2o 0.1~5%, tio21~8%,烧失量9~15%。
71.所述步骤s5中钢渣的主要化学成分和含量为:sio210~20%,al2o31~7%, fe2o32~33%,mgo 3~12%,cao 30~50%,feo 3~15%,na2o 0.01~3%,k2o 0.01~3%, so30.26%,p2o5 1~6%,烧失量2~10%。
72.所述步骤s3、s4和s7行星式球磨机分散时间为20min,磨机速率为 200r/min。
73.可选地,所述步骤s6中,压制成型的压力为20mpa。
74.所述步骤s8中磷石膏的主要化学成分和含量为:cao 35~50%,sio21~4%, al2o30~1.5%,mgo 1~4%,so330~45%,p2o51~6%。
75.所述步骤s9中废贝壳的主要矿物相为方解石和文石,其主要组成为:caco
3 80~92%,mgco31~10%,ca3(po4)20.01~2%,sio20.01~2%,al2o3+cao+fe2o
3 0.01~2%,烧失量1~12%。
76.所述步骤s10中电解锰渣的主要化学成分和含量为:sio225~40%,cao 5~15%,al2o35~15%,fe2o30.1~7%,mgo 0.1~3%,mno 0.1~5%,so320~40%,k2o 0.1~3%,na2o 0.01~1%,p2o50.01~1%,tio20.01~1%。
77.所述步骤s10中磷石膏的主要化学成分和含量为:cao35~50%,sio21~4%, al2o30~1.5%,mgo1~4%,so330~45%,p2o51~6%。
78.所述步骤s10中柠檬酸石膏的主要化学成分和含量为:cao 32~40%,sio
2 0.1~5%,al2o30.1~3%,mgo 0.1~1%,so335~55%,caf22~7%。k2o 0.01~1%,p2o
5 0.01~1%。
79.所述步骤s11中锰矿尾砂的主要化学成分和含量为:cao 1~10%,sio
2 35~60%,al2o31~7%,mgo 0.1~4%,mno 10~25%,fe2o35~12%,k2o+na2o 0.01~2%, 烧失量5~10%。
80.所述步骤s11中石英尾砂主要矿物组成为石英,杂质矿物组成为钠长石、钙 长石、黑云母和赤铁矿。主要化学成分和含量为:cao 0.01~3%,sio270~95%, al2o30.1~5%,mgo 0.01~3%,fe2o30.01~2%,so30.01~1%,k2o+na2o 0.01~1%, 烧失量0.1~3%。
81.所述步骤s12中防腐剂由钒钛矿渣、钼尾矿、镍渣、磷酸锌、环氧锌黄、复 合乳液、六偏硅酸钠、助剂、去离子水组成,其对应比例为11.7:4.1:13.9: 0.9:0.6:32.9:1.5:6.1:28.3,ph值9.0~9.5。复合乳液由中苯丙三元共聚物、 聚醋酸乙烯和环氧树脂组成,其重量百分比分别对应为55:35:10,钒钛矿渣、 镍渣、钼尾矿的比表面积控制在350m2/kg。
82.所述步骤s13中稳泡剂由三乙醇胺、油酸、去离子水配制而成,其对应比例 为3.1:1.2:38。
83.所述步骤s15中防水防碳化处理后的富含硅酸钙相制品采用彩色渗透型有 机加固溶剂进行雾化喷涂,所用的喷涂液为高渗透性界面处理剂,ph值6~10, 由环保型乳液和改性助剂组成,不挥发物为5%,其表干时间2h,拉伸粘结强度 0.5mpa,浸水处理的拉伸粘结强度0.5mpa,喷涂时气温应在5~35℃之间,贮藏 期间如出现分层、沉淀,使用中搅拌均匀即可。
84.按步骤s8制备的粉料1性能指标(见表1),其性能符合gb175-2007《通 用硅酸盐水
泥》的标准。
85.表1粉料1的性能
[0086][0087][0088]
按步骤s9制备的粉料2其有效cao含量为65%,mgo含量为4.67%,消解温 度63℃,消解时间12min,0.08mm方孔筛筛余12%,符合jc/t621-1996《硅酸 盐建筑制品用石灰》标准要求。
[0089]
按步骤s10制备的粉料3,1:1混合的电解锰渣和柠檬酸石膏符合gb/t 21371-2019《用于水泥中的工业副产石膏》中规定的工业副产品石膏要求。柠檬 酸石膏为湿法石膏。混合的石膏中caso4·
2h2o和caso4总和≥90%,氯离子≤0.4%, ph值≥5。
[0090]
按上述步骤制备的富含硅酸钙相景观高铁声屏障板性能指标如表2所示。
[0091]
表2实施例1制备的富含硅酸钙相景观高铁声屏障板性能指标
[0092][0093]
实施例2
[0094]
一种利用固废制备富含硅酸钙相多色景观高铁声屏障的方法,包括粉料1、 粉料2、粉料3、料浆的制备、钢筋的预处理、浇注成型、高温蒸压、防水防碳 化处理工序。
[0095]
上述硅酸钙相景观高铁声屏障方法,包括以下步骤:
[0096]
s1、双氰胺废渣的预处理:首先将双氰胺废渣置于电热干燥箱烘干12h(烘 干条件105℃),以脱除将双氰胺废渣中的游离水,取出后在干燥空气中冷却, 而后采用水泥球磨机进行粉磨(转速48r/min),使物料的比表面积达到350 m2/kg;
[0097]
s2、废光伏板预处理:首先将废光伏板进行分拆、分拣,挑选出铝质边框、 废塑料、缆线和接头,将废光伏板的玻璃采用颚式破碎机破碎至2~5mm颗粒,破 碎后的颗粒置于水泥球磨机中(转速48r/min),粉磨至比表面积300m2/kg;
[0098]
s3、精炼渣预处理:首先将精炼渣置于105℃烘箱内烘干12h至恒重,保 证含水率不大于0.2%,而后采用行星式球磨机进行分散,使物料的比表面积达 到300m2/kg;
[0099]
s4、高炉瓦斯灰预处理:将高炉瓦斯灰堆放阴凉通风处晾干,使其含水量小 于10%,然后将钢铁尘泥置于电热干燥箱12h烘干处理(烘干条件105℃),以 脱除将高炉瓦斯灰中的游离水,取出后在干燥空气中冷却,而后采用行星式球磨 机进行分散,使物料的比表面积达到400m2/kg;
[0100]
s5、钢渣的预处理:钢渣经颚式破碎机破碎2~5mm颗粒后,而后将钢渣置于 电热干燥箱烘干12h(烘干条件105℃),烘干后放入球磨机中(转速48r/min), 粉磨至比表面积
250m2/kg;
[0101]
s6、压制成型:将预处理后的双氰胺废渣粉、废光伏板粉、精炼渣、高炉瓦 斯灰和钢渣按重量百分比:80%:10%:6%:3%:1%的比例混合,采用行星式球磨机 进行混匀。将搅拌均匀干料混合物加入其质量9%的水,然后将混合料放入模具, 经液压压力机压制成球(球团尺寸φ30mm
×
20mm);将球团置于电热烘干箱中 恒温烘干40min(烘干条件100℃);
[0102]
s7、高温煅烧:干燥后的球团置于马弗炉内煅烧,煅烧制度为:由室温升至 800℃,升温速率为0.5℃/min,而后保温20min;再由800℃升至所需温度1250℃, 升温速率为3.5℃/min,而后保温40min;煅烧完成后降温至1050℃时取出试样, 取出的试样经鼓风急冷至室温;
[0103]
s8、球磨处理:将磷石膏置于电热干燥箱中烘干12h(烘干条件105℃), 而后在与烧制成型的试样混合(磷石膏用量为烧至成型试样质量的7%),再置 于水泥球磨机中(转速48r/min),粉磨至比表面积380m2/kg,得到粉料1备用;
[0104]
s9、废贝壳的预处理:首先将废贝壳进行筛选,筛除废贝壳中杂质,而后将 废贝壳放入转筒洗石机中进行清洗,清洗后的废贝壳晾干后置于电热干燥箱烘干 12h(烘干条件105℃),烘干后的贝壳颚式破碎机中破碎至1~3cm,而后置于马 弗炉内煅烧,煅烧制度为:由室温升至300℃,升温速率为1℃/min,而后保温 30min;再由300℃升至所需温度850℃,升温速率为3℃/min,而后保温100min; 煅烧完成后鼓风冷却至100℃时取出试样;再将冷却至室温的废贝壳放入水泥球 磨机中(转速48r/min),粉磨至比表面积400m2/kg,得到粉料2;
[0105]
s10、电解锰渣+柠檬酸石膏的预处理:将电解锰渣和氟石膏分别置于电热干 燥箱中烘干12h(烘干条件105℃),烘干后的电解锰渣和柠檬酸石膏按照质量 比1:1放入水泥球磨机中(转速48r/min),粉磨至比表面积350m2/kg,得到粉 料3;
[0106]
s11、锰矿尾砂+石英尾砂的预处理:首先将锰矿尾砂使用水力旋流器进行筛 分(料浆浓度35%),而后将筛分后颗粒尺寸大于0.074mm锰矿尾砂和石英尾砂 按比例60%:40%一起湿进行湿法混磨(料浆浓度70%),湿磨后至比表面积 400m2/kg,得到湿磨料浆,磨细后得到的料浆在料浆罐中存放;
[0107]
s12、钢筋的预处理:将φ4钢筋经过冷拉、除锈、调直、切断后,点焊5cm
ꢀ×
5cm钢筋网,而后将钢筋网放入防腐涂料池中浸泡25min,取出后晾干;将经 过防腐处理的钢筋网,按相对位置和工艺尺寸放入磨具中,并将其固定;
[0108]
s13、浇注成型:将粉料1、粉料2、粉料3和尾矿料浆分别按质量比9:23: 6:88加入搅拌缸中,混合均匀,加入干料总量60%的温水,再加入总用水量7
‰ꢀ
的稳泡剂,搅拌120s,之后加入干料总重量0.65
‰
的铝粉膏再搅拌50s,得到 混合均匀的料浆,搅拌过程中设置保温措施,保证料浆浇注时的入模温度在 48℃,浇注入模具中;
[0109]
s14、制品养护:将s13中浇注入模的料浆,进行静停发气、预养护、坯体 切割,高温蒸压养护,得到富含硅酸钙相的板材制品;其中,静停发气和预养护 时间为4小时,预养护温度为55℃;高温蒸压养护的流程为:密闭、抽真空、 升温至185℃,蒸压压力1.3mpa,保持8h,再降至常温常压;
[0110]
s15、防水防碳化处理:首先将富含硅酸钙相制品风干,再采用毛刷进行2 遍表面清理,(一次毛刷清理、一次吸尘器清理),将清理后的富含硅酸钙相制 品进行防水防碳化
处理,防水防碳化处理的制品采用彩色渗透型有机加固溶剂进 行雾化喷涂2遍,喷涂后晾干的制品可作为多色景观高铁声屏障板材。
[0111]
所述步骤s1中双氰胺废渣干基粒度0.01~0.1mm,主要矿物组成为方解石, 其主要化学成分和含量为:sio25~15%,al2o31~10%,cao 45~70%,fe2o31~5%, mgo 0.01~3%,k2o+na2o 0.01~2%,c 5~20%,烧失量20~40%。
[0112]
所述步骤s2中废光伏板主要化学成分和含量为:cao 65~85%,sio21~10%, al2o32~6%,feo 0.01~3%,fe2o30.01~5%,mgo 0.01~1%,k2o+na2o 0.01~2%, 烧失量15~30%。
[0113]
所述步骤s3中精炼渣矿物组成为钙铝石(c
12
a7)和水钙铝榴石(c3ah6), 主要化学成分和含量为:主要成分和含量为:cao 35~50%,al2o330~45%,sio
2 1~5%,mgo 2~8%,fe2o31~5%,so31~4%。
[0114]
所述步骤s4中高炉瓦斯灰的主要化学成分和含量为:sio210~30%,al2o
3 10~30%,fe2o315~45%,mgo 0.1~2%,cao 10~20%,k2o 0.01~1%,na2o 0.1~5%, tio21~8%,烧失量9~15%。
[0115]
所述步骤s5中钢渣的主要化学成分和含量为:sio210~20%,al2o31~7%, fe2o32~33%,mgo 3~12%,cao 30~50%,feo 3~15%,na2o 0.01~3%,k2o 0.01~3%, so30.26%,p2o5 1~6%,烧失量2~10%。
[0116]
所述步骤s3、s4和s7行星式球磨机分散时间为25min,磨机速率为 200r/min。
[0117]
可选地,所述步骤s6中,压制成型的压力为25mpa。
[0118]
所述步骤s8中磷石膏的主要化学成分和含量为:cao 35~50%,sio21~4%, al2o30~1.5%,mgo 1~4%,so330~45%,p2o51~6%。
[0119]
所述步骤s9中废贝壳的主要矿物相为方解石和文石,其主要组成为:caco
3 80~92%,mgco31~10%,ca3(po4)20.01~2%,sio20.01~2%,al2o3+cao+fe2o
3 0.01~2%,烧失量1~12%。
[0120]
所述步骤s10中电解锰渣的主要化学成分和含量为:sio225~40%,cao5~15%,al2o35~15%,fe2o30.1~7%,mgo 0.1~3%,mno 0.1~5%,so320~40%,k2o0.1~3%,na2o 0.01~1%,p2o50.01~1%,tio20.01~1%。
[0121]
所述步骤s10中磷石膏的主要化学成分和含量为:cao 35~50%,sio21~4%, al2o30~1.5%,mgo 1~4%,so330~45%,p2o51~6%。
[0122]
所述步骤s10中柠檬酸石膏的主要化学成分和含量为:cao 32~40%,sio
2 0.1~5%,al2o30.1~3%,mgo 0.1~1%,so335~55%,caf22~7%。k2o 0.01~1%,p2o
5 0.01~1%。
[0123]
所述步骤s11中锰矿尾砂的主要化学成分和含量为:cao 1~10%,sio
2 35~60%,al2o31~7%,mgo 0.1~4%,mno 10~25%,fe2o35~12%,k2o+na2o 0.01~2%, 烧失量5~10%。
[0124]
所述步骤s11中石英尾砂主要矿物组成为石英,杂质矿物组成为钠长石、钙 长石、黑云母和赤铁矿。主要化学成分和含量为:cao 0.01~3%,sio270~95%, al2o30.1~5%,mgo 0.01~3%,fe2o30.01~2%,so30.01~1%,k2o+na2o0.01~1%, 烧失量0.1~3%。
[0125]
所述步骤s12中防腐剂由钒钛矿渣、钼尾矿、镍渣、磷酸锌、环氧锌黄、复 合乳液、
六偏硅酸钠、助剂、去离子水组成,其对应比例为11.7:4.1:13.9: 0.9:0.6:32.9:1.5:6.1:28.3,ph值9.0~9.5。复合乳液由中苯丙三元共聚物、 聚醋酸乙烯和环氧树脂组成,其重量百分比分别对应为60:31:9,钒钛矿渣、镍 渣、钼尾矿的比表面积控制在400m2/kg。
[0126]
所述步骤s13中稳泡剂由三乙醇胺、油酸、去离子水配制而成,其对应比例 为3.1:1.2:38。
[0127]
所述步骤s15中防水防碳化处理后的富含硅酸钙相制品采用彩色渗透型有 机加固溶剂进行雾化喷涂,所用的喷涂液为高渗透性界面处理剂,ph值6~10, 由环保型乳液和改性助剂组成,不挥发物为4.5%,其表干时间1.5h,拉伸粘结 强度1mpa,浸水处理的拉伸粘结强度1mpa,喷涂时气温应在5~35℃之间,贮藏 期间如出现分层、沉淀,使用中搅拌均匀即可。
[0128]
按步骤s8制备的粉料1性能指标(见表3),其性能符合gb175-2007《通 用硅酸盐水泥》的标准。
[0129]
表3粉料1的性能
[0130][0131]
按步骤s9制备的粉料2其有效cao含量为67%,mgo含量为4.31%,消解温 度68℃,消解时间13min,0.08mm方孔筛筛余11%,符合jc/t621-1996《硅酸 盐建筑制品用石灰》标准要求。
[0132]
按步骤s10制备的粉料3,1:1混合的电解锰渣和柠檬酸石膏符合gb/t 21371-2019《用于水泥中的工业副产石膏》中规定的工业副产品石膏要求。柠檬 酸石膏为湿法石膏。混合的石膏中caso4·
2h2o和caso4总和≥90%,氯离子≤0.4%, ph值≥5。
[0133]
按上述步骤制备的富含硅酸钙相景观高铁声屏障板性能指标如表4所示。
[0134]
表4实施例2制备的富含硅酸钙相景观高铁声屏障板性能指标
[0135][0136]
实施例3
[0137]
一种利用固废制备富含硅酸钙相多色景观高铁声屏障的方法,包括粉料1、 粉料2、粉料3、料浆的制备、钢筋的预处理、浇注成型、高温蒸压、防水防碳 化处理工序。
[0138]
上述硅酸钙相景观高铁声屏障方法,包括以下步骤:
[0139]
s1、双氰胺废渣的预处理:首先将双氰胺废渣置于电热干燥箱烘干12h(烘 干条件105℃),以脱除将双氰胺废渣中的游离水,取出后在干燥空气中冷却, 而后采用水泥球磨机进行粉磨(转速48r/min),使物料的比表面积达到400 m2/kg;
[0140]
s2、废光伏板预处理:首先将废光伏板进行分拆、分拣,挑选出铝质边框、 废塑料、
缆线和接头,将废光伏板的玻璃采用颚式破碎机破碎至2~5mm颗粒,破 碎后的颗粒置于水泥球磨机中(转速48r/min),粉磨至比表面积350m2/kg;
[0141]
s3、精炼渣预处理:首先将精炼渣置于105℃烘箱内烘干12h至恒重,保 证含水率不大于0.2%,而后采用行星式球磨机进行分散,使物料的比表面积达 到350m2/kg;
[0142]
s4、高炉瓦斯灰预处理:将高炉瓦斯灰堆放阴凉通风处晾干,使其含水量小 于10%,然后将钢铁尘泥置于电热干燥箱12h烘干处理(烘干条件105℃),以 脱除将高炉瓦斯灰中的游离水,取出后在干燥空气中冷却,而后采用行星式球磨 机进行分散,使物料的比表面积达到450m2/kg;
[0143]
s5、钢渣的预处理:钢渣经颚式破碎机破碎2~5mm颗粒后,而后将钢渣置于 电热干燥箱烘干12h(烘干条件105℃),烘干后放入球磨机中(转速48r/min), 粉磨至比表面积350m2/kg;
[0144]
s6、压制成型:将预处理后的双氰胺废渣粉、废光伏板粉、精炼渣、高炉瓦 斯灰和钢渣按重量百分比:82%:8%:5%:2%:3%的比例混合,采用行星式球磨机 进行混匀。将搅拌均匀干料混合物加入其质量11%的水,然后将混合料放入模具, 经液压压力机压制成球(球团尺寸φ30mm
×
20mm);将球团置于电热烘干箱中 恒温烘干40min(烘干条件100℃);
[0145]
s7、高温煅烧:干燥后的球团置于马弗炉内煅烧,煅烧制度为:由室温升至 800℃,升温速率为0.5℃/min,而后保温20min;再由800℃升至所需温度1300℃, 升温速率为3.5℃/min,而后保温60min;煅烧完成后降温至1100℃时取出试样, 取出的试样经鼓风急冷至室温;
[0146]
s8、球磨处理:将磷石膏置于电热干燥箱中烘干12h(烘干条件105℃), 而后在与烧制成型的试样混合(磷石膏用量为烧至成型试样质量的10%),再置 于水泥球磨机中(转速48r/min),粉磨至比表面积400m2/kg,得到粉料1备用;
[0147]
s9、废贝壳的预处理:首先将废贝壳进行筛选,筛除废贝壳中杂质,而后将 废贝壳放入转筒洗石机中进行清洗,清洗后的废贝壳晾干后置于电热干燥箱烘干 12h(烘干条件105℃),烘干后的贝壳颚式破碎机中破碎至1~3cm,而后置于马 弗炉内煅烧,煅烧制度为:由室温升至300℃,升温速率为1℃/min,而后保温 30min;再由300℃升至所需温度900℃,升温速率为3℃/min,而后保温120min; 煅烧完成后鼓风冷却至100℃时取出试样;再将冷却至室温的废贝壳放入水泥球 磨机中(转速48r/min),粉磨至比表面积500m2/kg,得到粉料2;
[0148]
s10、电解锰渣+柠檬酸石膏的预处理:将电解锰渣和氟石膏分别置于电热干 燥箱中烘干12h(烘干条件105℃),烘干后的电解锰渣和柠檬酸石膏按照质量 比1:1放入水泥球磨机中(转速48r/min),粉磨至比表面积400m2/kg,得到粉 料3;
[0149]
s11、锰矿尾砂+石英尾砂的预处理:首先将锰矿尾砂使用水力旋流器进行筛 分(料浆浓度40%),而后将筛分后颗粒尺寸大于0.074mm锰矿尾砂和石英尾砂 按比例50%:50%一起湿进行湿法混磨(料浆浓度75%),湿磨后至比表面积 500m2/kg,得到湿磨料浆,磨细后得到的料浆在料浆罐中存放;
[0150]
s12、钢筋的预处理:将φ4钢筋经过冷拉、除锈、调直、切断后,点焊5cm
ꢀ×
5cm钢筋网,而后将钢筋网放入防腐涂料池中浸泡30min,取出后晾干;将经 过防腐处理的钢筋网,按相对位置和工艺尺寸放入磨具中,并将其固定;
[0151]
s13、浇注成型:将粉料1、粉料2、粉料3和尾矿料浆分别按质量比7:26: 4:100加入搅拌缸中,混合均匀,加入干料总量65%的温水,再加入总用水量 11.5
‰
的稳泡剂,搅拌160s,之后加入干料总重量0.5
‰
的铝粉膏再搅拌60s, 得到混合均匀的料浆,搅拌过程中设置保温措施,保证料浆浇注时的入模温度在 50℃,浇注入模具中;
[0152]
s14、制品养护:将s13中浇注入模的料浆,进行静停发气、预养护、坯体 切割,高温蒸压养护,得到富含硅酸钙相的板材制品;其中,静停发气和预养护 时间为5小时,预养护温度为70℃;高温蒸压养护的流程为:密闭、抽真空、 升温至195℃,蒸压压力1.4mpa,保持5h,再降至常温常压;
[0153]
s15、防水防碳化处理:首先将富含硅酸钙相制品风干,再采用毛刷进行2 遍表面清理,(一次毛刷清理、一次吸尘器清理),将清理后的富含硅酸钙相制 品进行防水防碳化处理,防水防碳化处理的制品采用彩色渗透型有机加固溶剂进 行雾化喷涂2遍,喷涂后晾干的制品可作为多色景观高铁声屏障板材。
[0154]
所述步骤s1中双氰胺废渣干基粒度0.01~0.1mm,主要矿物组成为方解石, 其主要化学成分和含量为:sio25~15%,al2o31~10%,cao 45~70%,fe2o31~5%, mgo 0.01~3%,k2o+na2o 0.01~2%,c 5~20%,烧失量20~40%。
[0155]
所述步骤s2中废光伏板主要化学成分和含量为:cao 65~85%,sio21~10%, al2o32~6%,feo 0.01~3%,fe2o30.01~5%,mgo 0.01~1%,k2o+na2o 0.01~2%, 烧失量15~30%。
[0156]
所述步骤s3中精炼渣矿物组成为钙铝石(c
12
a7)和水钙铝榴石(c3ah6), 主要化学成分和含量为:主要成分和含量为:cao 35~50%,al2o330~45%,sio
2 1~5%,mgo 2~8%,fe2o31~5%,so31~4%。
[0157]
所述步骤s4中高炉瓦斯灰的主要化学成分和含量为:sio210~30%,al2o
3 10~30%,fe2o315~45%,mgo 0.1~2%,cao 10~20%,k2o 0.01~1%,na2o 0.1~5%, tio21~8%,烧失量9~15%。
[0158]
所述步骤s5中钢渣的主要化学成分和含量为:sio210~20%,al2o31~7%, fe2o32~33%,mgo 3~12%,cao 30~50%,feo 3~15%,na2o 0.01~3%,k2o 0.01~3%, so30.26%,p2o5 1~6%,烧失量2~10%。
[0159]
所述步骤s3、s4和s7行星式球磨机分散时间为30min,磨机速率为 200r/min。
[0160]
可选地,所述步骤s6中,压制成型的压力为30mpa。
[0161]
所述步骤s8中磷石膏的主要化学成分和含量为:cao 35~50%,sio21~4%, al2o30~1.5%,mgo 1~4%,so330~45%,p2o51~6%。
[0162]
所述步骤s9中废贝壳的主要矿物相为方解石和文石,其主要组成为:caco
3 80~92%,mgco31~10%,ca3(po4)20.01~2%,sio20.01~2%,al2o3+cao+fe2o
3 0.01~2%,烧失量1~12%。
[0163]
所述步骤s10中电解锰渣的主要化学成分和含量为:sio225~40%,cao5~15%,al2o35~15%,fe2o30.1~7%,mgo 0.1~3%,mno 0.1~5%,so320~40%,k2o0.1~3%,na2o 0.01~1%,p2o50.01~1%,tio20.01~1%。
[0164]
所述步骤s10中磷石膏的主要化学成分和含量为:cao 35~50%,sio21~4%, al2o30~1.5%,mgo 1~4%,so330~45%,p2o51~6%。
[0165]
所述步骤s10中柠檬酸石膏的主要化学成分和含量为:cao 32~40%,sio
2 0.1~5%,al2o30.1~3%,mgo 0.1~1%,so335~55%,caf22~7%。k2o 0.01~1%,p2o
5 0.01~1%。
[0166]
所述步骤s11中锰矿尾砂的主要化学成分和含量为:cao 1~10%,sio
2 35~60%,al2o31~7%,mgo 0.1~4%,mno 10~25%,fe2o35~12%,k2o+na2o0.01~2%, 烧失量5~10%。
[0167]
所述步骤s11中石英尾砂主要矿物组成为石英,杂质矿物组成为钠长石、钙 长石、黑云母和赤铁矿。主要化学成分和含量为:cao 0.01~3%,sio270~95%, al2o30.1~5%,mgo 0.01~3%,fe2o30.01~2%,so30.01~1%,k2o+na2o 0.01~1%, 烧失量0.1~3%。
[0168]
所述步骤s12中防腐剂由钒钛矿渣、钼尾矿、镍渣、磷酸锌、环氧锌黄、复 合乳液、六偏硅酸钠、助剂、去离子水组成,其对应比例为11.7:4.1:13.9: 0.9:0.6:32.9:1.5:6.1:28.3,ph值9.0~9.5。复合乳液由中苯丙三元共聚物、 聚醋酸乙烯和环氧树脂组成,其重量百分比分别对应为63:29:8,钒钛矿渣、镍 渣、钼尾矿的比表面积控制在450m2/kg。
[0169]
所述步骤s13中稳泡剂由三乙醇胺、油酸、去离子水配制而成,其对应比例 为3.1:1.2:38。
[0170]
所述步骤s15中防水防碳化处理后的富含硅酸钙相制品采用彩色渗透型有 机加固溶剂进行雾化喷涂,所用的喷涂液为高渗透性界面处理剂,ph值6~10, 由环保型乳液和改性助剂组成,不挥发物为4%,其表干时间1.3h,拉伸粘结强 度1.5mpa,浸水处理的拉伸粘结强度1.5mpa,喷涂时气温应在5~35℃之间,贮 藏期间如出现分层、沉淀,使用中搅拌均匀即可。
[0171]
按步骤s8制备的粉料1性能指标(见表5),其性能符合gb175-2007《通 用硅酸盐水泥》的标准。
[0172]
表5粉料1的性能
[0173][0174]
按步骤s9制备的粉料2其有效cao含量为69%,mgo含量为4.24%,消解温 度70℃,消解时间11min,0.08mm方孔筛筛余9%,符合jc/t621-1996《硅酸盐 建筑制品用石灰》标准要求。
[0175]
按步骤s10制备的粉料3,1:1混合的电解锰渣和柠檬酸石膏符合gb/t 21371-2019《用于水泥中的工业副产石膏》中规定的工业副产品石膏要求。柠檬 酸石膏为湿法石膏。混合的石膏中caso4·
2h2o和caso4总和≥90%,氯离子≤0.4%, ph值≥5。
[0176]
按上述步骤制备的富含硅酸钙相景观高铁声屏障板性能指标如表6所示。
[0177]
表6实施例3制备的富含硅酸钙相景观高铁声屏障板性能指标
[0178][0179]
下面结合附图对本发明做进一步说明:
[0180]
实施例2中s7步骤煅烧后试样的物相组成及结构
[0181]
表7水泥生料化学成分组成(wt%)
[0182][0183]
根据煅烧制度将s7步骤中煅烧试样编号设为cs-1~cs-4,4个样品与组成 比例相同(见表7),在1250℃的温度条件下分别保温30min、40min、50min、 60min。试样的矿物组成和相对比例通过x射线衍射定量分析方法确定,图6(a)
ꢀ‑
(d)给出了4个试样的x射线衍射图谱,试样矿物定量分析结果见表8。从表 8可以看出:随着恒温时间延长,试样中硅酸三钙的含量先增加而后降低,硅酸 二钙的含量逐渐先降低而后增加,游离钙的含量低于2%。然而,试样中铁铝酸 四钙的含量较少,铝酸三钙的含量较高。
[0184]
表8cs1-4试样矿物成分定量分析(wt%)
[0185][0186]
图6为本发明实施例2中s7步骤在1250℃的温度条件下分别保温30min、 40min、50min、60min的光学显微镜图片。从图6可以看出,(a)图矿晶体大 小不均匀,晶体多呈板柱状,不规则状分布。而(b)图中尺寸较大,形态主要 呈规则的长柱状、板状,晶体边界棱角完整,表面平滑。(c)和(d)图中有大 量矿巢出现,晶体表面呈麻面状或有粗交叉双晶纹出现分布不均匀,含量偏少, 部分黑色中间相呈片状分布。游离钙多呈中堆或分散分布,游离钙含量合格,液 相分布不均匀。从形状推断试样烧成有还原气氛出现。由黑色中间相形态推断该 试样冷却稍慢。
[0187]
图7为本发明实施例2中s7步骤1250℃煅烧后试样保温40min的sem-eds 图,由eds图谱及统计结果分析(见表9),可知a、b两点矿物均为c2s。该熟 料中以类似b点成分的c2s较为普遍。a点ca/si为2.3,a点固熔的杂质离子较 多,主要为k
+
和na
+
碱金属离子。而且,结晶不完整、晶格畸变较大。杂质离子 的掺杂可能改变了c2s晶体硅氧四面体(sio
44-)的取向。b
点硅酸二钙(c2s)的 ca/si为2.1,同时固熔了铝、铁、镁以及少量的钾和钠。c点出现部分空心管 状结构,eds分析表明:其主要是铁铝酸钙的固溶体,同时掺杂部分硅、镁以及 碱金属离子。
[0188]
同时,从图7可以看出:硅酸二钙(c2s)颗粒一般在15μm以下,而且表 面形成较多的微裂纹,可能是由于降温过程中高温晶型向低温晶型转变时晶体对 称性降低引起的,也可能为掺杂离子在降温过程中的溶出通道(exsolved),因 为和高温晶型相比,低温晶型不容易固熔杂质离子。样品熟料表面的微裂纹也很 可能是硅酸二钙晶体中掺杂物质使结晶拉力增加,从而导致开裂缺陷。较小的硅 酸二钙(c2s)结晶尺寸、显著晶体开裂缺陷可能是增加熟料水化反应活性的原 因。
[0189]
表9a、b、c三点eds分析统计结果(mol)
[0190][0191]
富含硅酸钙相制品的物相组成及结构
[0192]
图10为本发明实施例2中s14步骤中硅酸钙相制品的xrd图谱;图11为 本发明实施例2中s14步骤中硅酸钙相制品的sem-eds图谱。从图10可以看出, 托贝莫来石和方解石是制品中的新生成物相,水化产物托贝莫来石和c-s-h的形 成合理解释了并保证了制品较好的强度。尾矿体系中的钠长石、微斜长石矿物经 高温蒸压反应之后依旧存在(石英尾砂的物相组成见图9),可以确定这些矿物 本研究体系所采用的蒸压条件下活性较低,未能全部参与反应。此外图11中, xrd图谱存在一定弥散的背景,证明有无定形(无衍射性)的物质存在于制品之 中,制品中存在一些小的颗粒尺寸,导致衍射峰宽化,并入xrd衍射背景当中。
[0193]
图11(a)为制品气孔内壁的sem照片,从中可以明显水化产物密集丛生, 生成结晶比较差无定形的凝胶状c-s-h(见图中a处)和大量结晶度比较好柳叶 状或叶片状1.4nm的托贝莫来石(见图中b处)。同时凝胶作为“粘结剂”将密 集的水化产物相互胶结在一起,形成良好的网络状框架结构,对制品的强度提高 起到了一定作用。从图11(b)对(a)中b处放大50000倍的图中可看出,片 状的托贝莫来石结晶良好,宽度1~2μm,厚度为60~80nm,片状托贝莫来石 相互穿插搭接,同时各片之间形成空腔,使制品具备了隔热保温性能。
[0194]
从eds图对图11(b)中的标注区域的分析图谱及定量结果可见,谱图中含 有o、al、si、ca元素的原子数与托贝莫来石成分基本相同。
[0195]
综上所述,本发明利用固废制备富含硅酸钙相多色景观高铁声屏障,在物理 力学性能(强度和密度)上,耐久性能(防渗、抗冻性、抗碳化)都有所提高, 同时在隔音、吸声效果上优于市场现有产品。值得大力推广。
[0196]
以上所述仅为本发明的优选实施例而已,并不用于限制本发明,对于本领域 的技术人员来说,凡在本发明的精神和原则之内,所作的任何修改、等同替换、 改进等,均应包含在本发明的保护范围之内。