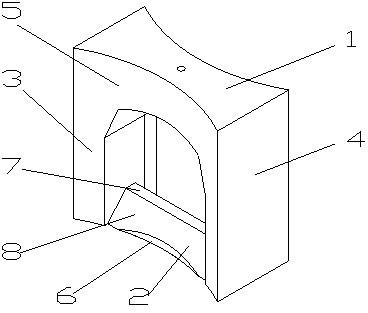
1.本实用新型涉及一种双膛石灰竖窑两膛之间的连接通道,属于双膛石灰竖窑砌筑结构技术领域。
背景技术:2.在双膛石灰竖窑的砌筑中有两个通道,一个环形通道,一个连接两个窑膛的连接通道。由于要形成完整的环形通道,以及窑膛耐火材料有一个稳定的支撑,两个窑膛的间距不能太小,中间由连接通道相连接。连接通道由上横梁、下横梁和两侧立柱组成,中间是气体通道,一般的连接通道的上横梁和下横梁的截面均为矩形,上横梁的下表面和下横梁的上表面为平面。在生产过程中发现,当夹带有大量高温粉尘的气流通过连接通道时,在上横梁和下横梁的阻挡作用下,会有部分灰尘发生沉降,由于下横梁的上表面为平面,沉降粉尘灰堆积于下横梁的上表面,因粉尘有一定的粘性,沉降的粉尘之间发生粘结,过往的气流不能将沉积在下横梁上表面的粉尘带走,导致粉尘会越集越多,最后堵塞连接通道。连接通道发生堵塞现象时,操作人员要进行清灰作业,目前清灰一般采用两种方法,一是通过连接通道顶部的预留孔,用钢钎清除积灰块,二是用空气炮清除。不论哪种方法,由于连接通道的的下横梁的宽度较大,彻底清除积灰较为困难。再有,每次清灰前,石灰窑都要降温,不但影响窑的产量,石灰的质量也受到影响,同时降温清灰也导致连接通道的拱顶砖容易脱落,影响连接通道的使用寿命。
3.综上所述,目前双膛石灰竖窑的连接通道有一定的缺点,十分有必要进行改进。
技术实现要素:4.本实用新型所要解决的技术问题是提供一种可以避免积灰的双膛石灰竖窑连接通道,这种连接通道可以显著减少粉尘在下横梁上表面的堆积,并且对沉降在下横梁上表面的粉尘清理容易,可以杜绝发生连接通道堵塞的现象,以减少石灰窑通道清灰次数和石灰窑的停窑时间,提高石灰窑的产量和质量。
5.解决上述技术问题的技术方案是:
6.一种可以避免积灰的双膛石灰竖窑连接通道,它包括上横梁、下横梁、左立柱、右立柱,上横梁和下横梁的两侧面分别为向内的上横梁圆弧侧面和下横梁圆弧侧面,上横梁和下横梁两侧的圆弧侧面分别与连接通道两端的双膛石灰窑膛的圆周外壁相连接,其改进之处是,下横梁上部两侧分别有两个斜面,两个斜面的上边缘分别与下横梁上表面的两侧相交,两个斜面中间的下横梁上表面为沿着下横梁长度方向的长条平面,或者两个斜面的上端相交为沿着下横梁长度方向的直线,两个斜面的下边缘分别与下横梁两侧的下横梁圆弧侧面相交,下横梁的截面上部为梯形或三角形,截面下部为长方形,上部梯形截面的梯形上底边的长度小于梯形下底边长度,下部长方形截面的宽度为下横梁的两个下横梁圆弧侧面之间的距离。
7.上述可以避免积灰的双膛石灰竖窑连接通道,所述下横梁的两个斜面与水平面的
倾斜角度为45
‑
60
°
,下横梁中间位置的梯形截面的上底边的长度小于下底边的长度的1/3。
8.本实用新型的有益效果是:
9.本实用新型的连接通道下横梁的截面上部两侧分别有向外侧下方倾斜的斜面,夹带有大量高温粉尘的气流通过连接通道时,沉降的粉尘落到下横梁上表面时会沿着两侧的斜面滑落,不容易堆积在下横梁的斜面表面,下横梁上表面的平面面积小,粉尘在气流带动下在下横梁上表面也不易停留,即使停留或黏在下横梁的两侧斜面和下横梁上平面的粉尘也容易清理。
10.本实用新型结构简单、设计科学合理,可以减少石灰窑通道清灰次数,清灰的时间变短,清灰更加容易,减少了石灰窑的停窑时间,延长了石灰窑的生产时间,提高了石灰窑的产量、质量,也延长了石灰窑连接通道的使用寿命。
附图说明
11.图1是本实用新型的结构示意图;
12.图2是图1的剖视图;
13.图3是本实用新型的另一种结构的剖视图。
14.图中标记如下:上横梁1、下横梁2、左立柱3、右立柱4、上横梁圆弧侧面5、下横梁圆弧侧面6、下横梁上表面7、斜面8、梯形截面9、长方形截面10、三角形截面11、连接通道12、双膛石灰竖窑膛13。
具体实施方式
15.本实用新型的连接通道12由上横梁1、下横梁2、左立柱3、右立柱4组成,上横梁1和下横梁2的两侧面分别为向内的上横梁圆弧侧面5和下横梁圆弧侧面6,上横梁1和下横梁2两侧的圆弧侧面分别与连接通道12两端的双膛石灰窑膛13的圆周外壁相连接,这些结构是现有双膛石灰窑的正常结构。
16.为了减少连接通道12积灰,使连接通道12的积灰易于清理,本实用新型对下横梁2进行了改进。
17.图1、2显示,下横梁2上部两侧分别有两个斜面8,两个斜面8的上边缘分别与下横梁上表面7的两侧相交,两个斜面8中间的下横梁上表面7为沿着下横梁2长度方向的长条平面,两个斜面8下边缘分别与下横梁2两侧的下横梁圆弧侧面6相交。这种结构的下横梁2的截面上部为梯形截面9,截面下部为长方形截面10,梯形截面9的梯形上底边的长度小于梯形下底边的长度,下部长方形截面10的宽度为下横梁2的两个下横梁圆弧侧面6之间的距离。
18.图3显示,下横梁2的另一种结构是,下横梁2上部两侧的两个斜面8的上端相交,相交处为沿着下横梁2长度方向的直线,两个斜面8的下边缘分别与下横梁2两侧的下横梁圆弧侧面6相交。这种结构的下横梁2的截面上部为三角形截面11,截面下部为长方形截面10,下部长方形截面10的宽度为下横梁2的两个下横梁圆弧侧面6之间的距离。
19.图2、3显示,两种结构的下横梁2的两个斜面8与水平面的倾斜角度为45
‑
60
°
,下横梁2中间位置的梯形截面9的梯形上底边的长度小于梯形下底边的长度的1/3。这样设计的原因是,斜面8的水平夹角不能太小,夹角太小斜面8也容易积灰。同时,两个斜面8的倾斜角
度和两个斜面8上端之间的距离是由两个窑膛的间距所决定的,是否将下横梁2上部设计为梯形截面9还是三角形截面11,要兼顾两个窑膛的间距和下横梁2的斜面8水平夹角,使之形成最合理的布局,达到最好的效果。
20.图1、2、3显示,无论采用梯形截面9还是三角形截面11,夹带有大量高温粉尘的气流通过连接通道12时,在斜面8上下滑力大于摩擦力,沉降的粉尘落到下横梁上表面7时会沿着两侧的斜面8滑落,不容易堆积在下横梁2的斜面8表面,下横梁上表面7的平面面积小,粉尘在气流带动下在下横梁上表面7也不易停留,即使停留或黏在下横梁的两侧斜面8和下横梁上平面7的粉尘也容易清理。
21.本实用新型的一个实施例如下:
22.上横梁1的长度为914(窄处),最大宽度为1444mm,高度为940mm;
23.下横梁2的长度为2600mm,最大宽度为1444mm,高度为900mm;
24.左立柱3的宽度为1444(窄处)/1770(宽处)mm,厚度为510mm,高度为2600mm;
25.右立柱4的宽度为1444(窄处)/1770(宽处)mm,厚度为510mm,高度为2600mm;
26.下横梁上表面7的宽度为260mm;
27.斜面8的水平夹角为50
°
;
28.下横梁2中间位置的梯形截面9的梯形上底边的长度为260mm,梯形下底边的长度为960mm;
29.下横梁2中间位置的长方形截面10的长度为960mm,高度为183mm。(注:梁的总高是900mm=417+183+300)。