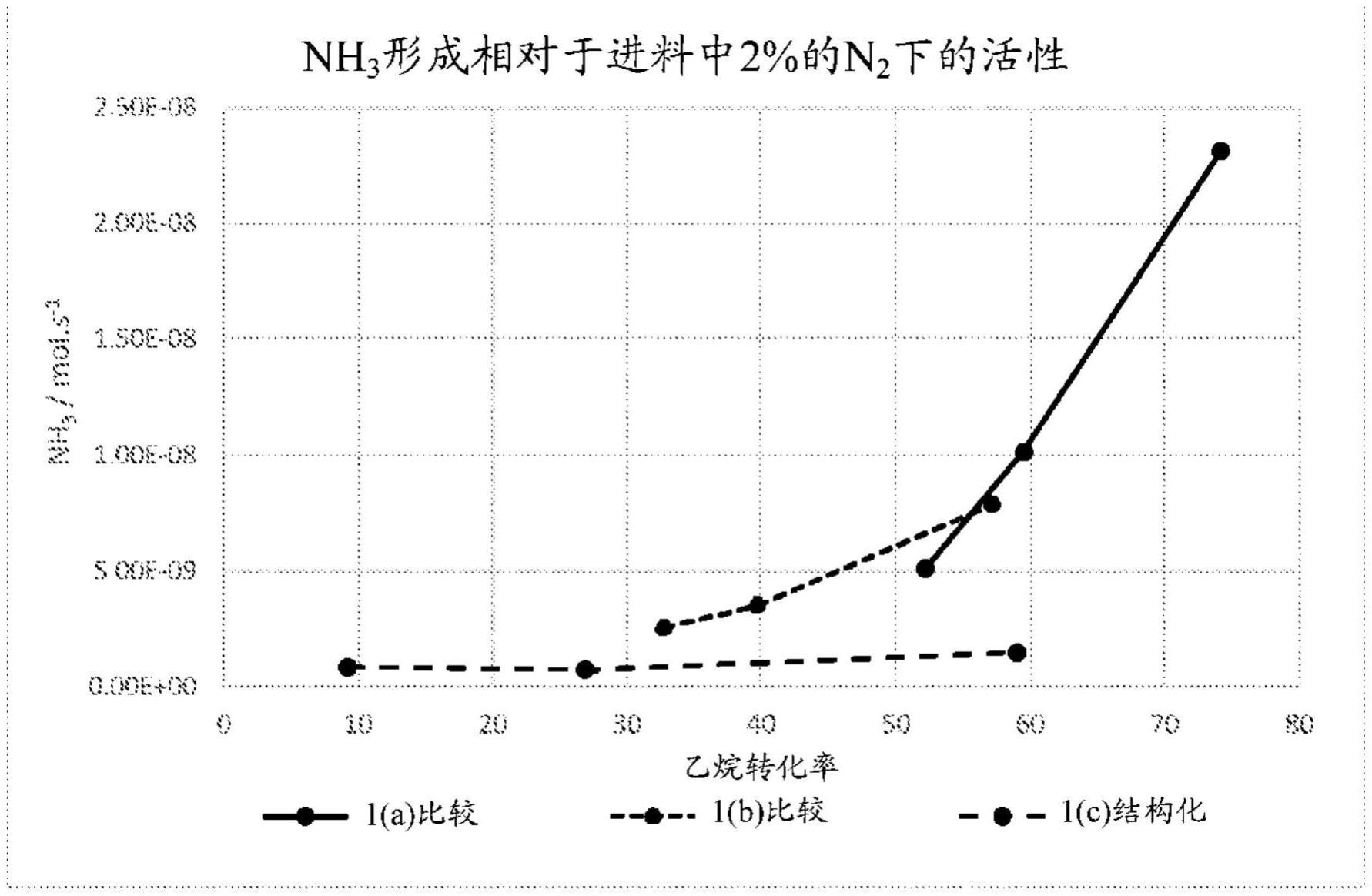
蒸汽重整
1.本发明涉及一种烃类蒸汽重整以产生合成气的方法和用于实施该方法的装置。
2.合成气包括氢气和碳氧化物(一氧化碳和二氧化碳),并且可含有氮气和其它气体,例如氩气和低含量的甲烷。合成气可含有较多或较少量的氢气和碳氧化物,以适于特定最终用途,诸如用于精炼厂或燃料电池的制氢、氨合成、甲醇合成、二甲醚合成,或液烃合成的费托方法。合成气通常通过蒸汽重整方法产生。
3.在常规蒸汽重整方法中,烃原料和蒸汽以及在一些情况下还有二氧化碳的混合物在高压下通过含有颗粒催化剂的管,该管通过合适的加热介质(通常为热气混合物)进行外部加热。颗粒催化剂通常为成型单元的形式,例如具有多个通孔的圆柱体,并且通常由耐火载体材料如α-氧化铝、铝酸钙或铝酸镁并使用合适的具有催化活性的金属如镍浸渍形成。
4.烃原料通常含有少量氮,其在蒸汽重整催化剂的作用下转化成氨。合成气中不需要氨,而氨可溶于工艺冷凝液中,工艺冷凝液理想地重回到该工艺,并且目前已提出力图使氨的形成最少化的工艺。
5.us5498404公开了一种在减少氨形成的情况下对含氮的含碳原料进行催化蒸汽重整的方法,其中,该原料与负载型镍催化剂进行接触,该负载型镍催化剂还包括基于催化剂中镍的量计算的量为0.01重量%至10重量%的铜。优选地,该含铜催化剂用作常规镍蒸汽重整催化剂的固定床中的亚层。实施例1表明,随着铜含量增加,催化剂的蒸汽重整活性越来越低。
6.wo2009/054830公开了通过使用具有约10%至约25%镍的第一阶段催化剂、具有小于10%镍的第二阶段催化剂和具有2%或更少的低浓度铑催化剂的最终阶段催化剂来重整天然气,而不产生过量的氨。通过减少催化剂中的镍含量和朝向出口的管的最热部分处的表面积来抑制氨的形成。然而,由于第二阶段中镍含量降低,转化率不理想地变得较低,于是需要铑催化剂来提供足够的合成气产物。贵金属催化剂对于在蒸汽重整器中大规模产生合成气而言过于昂贵,并且使用混合催化剂会增加催化剂装载、操作和排放的成本和复杂性。此外,混合催化剂在金属回收方面对于再处理而言更具挑战性。
7.目前已发现,在不依赖使用铑催化剂而通过使用镍蒸汽重整催化剂的情况下,可减少氨的形成,其中,镍存在于催化剂表面的薄层中。
8.相应地,本发明提供了一种对含有一种或多种氮化合物的烃原料进行蒸汽重整的方法,包括:使烃原料和蒸汽的混合物通过由一种或多种镍蒸汽重整催化剂组成的催化剂床,该镍蒸汽重整催化剂置于管式蒸汽重整器中的多个外部加热管中,其中每根管具有馈送烃和蒸汽混合物的入口及回收含有氢气、一氧化碳、二氧化碳、蒸汽、氨和甲烷的重整气体的出口,并且至少在该管的出口处,该蒸汽重整催化剂为包含镍的结构化蒸汽重整催化剂,而镍分散于作为非多孔金属或陶瓷结构上的涂层存在的多孔金属氧化物表面上,其中该金属氧化物涂层中镍含量在5重量%至50重量%的范围内,并且该涂层的厚度在5微米至150微米的范围内。
9.该方法中馈送的含烃原料可包括任何气态或低沸点烃原料,诸如天然气、伴生气、lpg、石油馏分、柴油、石脑油或它们的混合物,或来自化学工艺的废气,诸如精炼厂废气或
预重整气体。优选地,烃原料包括甲烷,并且可为预重整气体、伴生气或天然气。天然气是特别优选的原料。该原料可被压缩至在10巴至100巴绝对压力范围内的压力。该烃原料的压力可有效地控制整个工艺中的压力。优选地,操作压力在15巴至80巴的绝对压力范围内,更优选地在20巴至50巴的绝对压力范围内,因为这使该工艺的性能表现得到增强。
10.如果烃原料在压缩之前或优选地在压缩之后含有硫化合物,则可以对原料进行脱硫。脱硫可包括使用como或nimo催化剂的加氢脱硫和使用合适的硫化氢吸附剂如氧化锌吸附剂的硫化氢吸收。超纯化吸附剂可有效地用于硫化氢吸附剂的下游,以进一步保护蒸汽重整催化剂。合适的超纯化吸附剂可包括铜-氧化锌/氧化铝材料和铜-镍-氧化锌/氧化铝材料。为了有利于加氢脱硫和/或降低重整工艺中碳沉积的风险,可将氢气添加到压缩烃原料中。所得混合气体流中氢气的量可在1体积%至20体积%的范围内,但优选地在1体积%至10体积%的范围内,更优选地在1体积%至5%体积的范围内。
11.如果烃原料含有其它污染物,诸如氯化物或重金属污染物,则可在重整之前,在任何脱硫的上游或下游,使用常规吸附剂去除这些污染物。适用于氯化物去除的吸附剂是已知的并且包括碱化的氧化铝材料。类似地,用于重金属诸如汞或砷的吸附剂是已知的并且包括硫化铜材料。
12.在含烃原料为含甲烷的预重整气体的情况下,这可通过使烃/蒸汽混合物经受绝热低温蒸汽重整步骤而形成。烃可以为富烃的天然气、石脑油或其它烃含量高于甲烷含量的含烃原料。预重整方法是已知的。在这类方法中,烃/蒸汽混合物经过加热,通常加热至400℃至650℃的范围内的温度,然后绝热通过合适的颗粒蒸汽重整催化剂固定床,该催化剂通常为具有高镍含量(例如高于40重量%,表示为nio的)沉淀催化剂。在这类绝热低温预重整步骤期间,任何含量高过甲烷的烃与蒸汽进行反应,得到含有甲烷、碳氧化物和氢气混合物的预重整气体。使用这种通常被称为预重整的绝热重整步骤期望地确保进入管式蒸汽重整器的进料所含的烃不高于甲烷并且还包含大量的氢气。对于使下游管式蒸汽重整器中催化剂上碳形成的风险最小化而言,这是理想的。
13.在该方法中,烃原料可含有0.1体积%至25体积%的一种或多种氮化合物。该烃原料中的一种或多种氮化合物的含量可以为0.5体积%至25体积%、1体积%至10体积%或1体积%至5体积%。该一种或多种氮化合物可包括一种或多种胺,但通常包括氮气(n2)或由氮气组成。因此,该烃原料的氮气含量可以在0.1体积%至25体积%或0.5体积%至25体积%,优选地在1体积%至10体积%,更优选地在1体积%至5体积%的范围内。
14.可将该原料进行预热。其可方便地在压缩后和脱硫前使用合适的热源诸如火焰加热器进行预热。
15.将该烃原料与蒸汽进行混合以形成重整进料气体。蒸汽引入可通过直接注入蒸汽和/或通过使原料与加热水流进行接触使原料饱和来进行。在一些实施方案中,该烃原料在馈送了热水的饱和器中进行饱和以形成饱和气体混合物。如果需要,可通过直接添加蒸汽来增加饱和气体混合物的蒸汽含量。优选地,水包括从重整气体回收的冷凝液流、从饱和器底部回收的水和在该过程中产生的其它冷凝液中的一者或多者。理想地,引入的蒸汽量足以使原料中的蒸汽与碳的比率至少为1.8:1,即每克烃碳原子含有至少1.8摩尔的蒸汽。优选地,蒸汽与碳的比率在1.8:1至5:1的范围内,更优选地在2.5:1至3.5:1的范围内,尤其是2.8:1至3.2:1的范围内,因为这会使氢气产量和效率达到最佳平衡。
16.取决于蒸汽和氮化合物的含量,包括烃原料和蒸汽的重整进料气体可包含0.02体积%至14.0体积%,可选地0.1体积%至10.0体积%,或可选地0.2体积%至6.0体积%的一种或多种氮化合物。
17.然后,理想地,在重整之前对重整进料气体混合物进行预热。在优选的实施方案中,通过使其通过火焰加热器来加热烃/蒸汽混合物。理想地,将混合流加热至在300℃至650℃或450℃至650℃,优选地在450℃至600℃,更优选地在450℃至550℃范围内的入口温度。在没有预重整器的情况下,300℃至550℃范围内的入口温度尤为合适,在有预重整器的情况下,550℃至650℃范围内的更高入口温度尤为合适。
18.在重整方法中,甲烷与蒸汽进行反应,产生氢气、一氧化碳和二氧化碳。存在的任何含有两个或更多个碳原子的烃被转化为甲烷,从而经过蒸汽重整。此外发生可逆的水煤气转化反应。总之,这是一个吸热过程,需要加热管和催化剂,以维持反应并达到期望的转化率。通常,蒸汽重整器的热量输入可使得管出口处的气体流产物的温度高于入口温度,通常比入口温度高100至350或400摄氏度。
19.管式蒸汽重整器包含通常为垂直排列的多个管,气体混合物可通过这些管,并且通过在这些管的外表面周围使热气流动将热量传递给管。热气体可包括燃烧气体或合成气。管入口通常位于顶端,从而使得进料气体混合物通常被馈送至蒸汽重整器的顶部并向下流过管。
20.因此,管式蒸汽重整器可具有用于重整进料气体的入口、用于重整气体混合物的出口和与入口连通的多个垂直管,气体混合物可通过垂直管,并且通过在热交换区中使热气围绕管流动将热量传递给垂直管,其中每根管含有作为管内层提供的一种或多种蒸汽重整催化剂,其中至少邻近出口的蒸汽重整催化剂层是结构化的镍蒸汽重整催化剂。
21.在该方法中,邻近管出口的催化剂是结构化蒸汽重整催化剂。所谓“结构化蒸汽重整催化剂”指涂覆在非多孔结构(通常为金属或陶瓷结构)上的蒸汽重整催化剂。该结构化催化剂中的镍分散于多孔金属氧化物的表面上,该多孔金属氧化物作为表面涂层负载在非多孔结构上。
22.金属或陶瓷结构基本上是非多孔的,因此具有基本上由其形状限定的较小表面积。为了提供足够的活性,结构化催化剂中的镍分散在涂覆在非多孔金属或陶瓷载体上的多孔金属氧化物上。在非多孔结构上的含有镍的多孔金属氧化物涂层的厚度在5微米至150微米,优选地在10微米至100微米的范围内,更优选地在10微米至80微米的范围内,最优选地在10微米至50微米的范围内。上述优选的范围使得催化剂具有最佳活性、粘附性和内聚性。
23.通过已知的载体涂覆(wash-coating)工艺可将镍施加到结构上,由此金属氧化物的浆料(其可包括作为成分的镍氧化物)通过浸渍或喷涂施加到金属或陶瓷结构上,然后,对其进行干燥和热处理以将金属氧化物结合到载体上。还可以通过使用可溶镍化合物的浸渍技术将镍施加到金属氧化物涂覆的载体上,然后对其进行干燥和煅烧以将镍化合物转化成镍氧化物。可以使用这些技术的组合,包括将溶液中的镍与金属氧化物载体浆料组合施用。
24.结构上的蒸汽重整催化剂包含镍。金属氧化物涂层的镍含量在5重量%至50重量%,优选地在10重量%至30重量%,更优选地在10重量%至20重量%范围内。可选地,选
自铂、铑、钌或钯或它们的混合物的铂族金属可包含在上述涂层中。如果包含,铂族金属促进剂能够以0.05重量%至1重量%范围内的量存在于涂层中。涂层可以10g/m2至150g/m2,优选地10g/m2至80g/m2、更优选地30g/m2至60g/m2范围内的量施加到非多孔载体结构上。
25.碱金属氧化物诸如钾氧化物也可存在于该结构上的多孔金属氧化物涂层中,但通常并非必需。如果存在,碱金属氧化物的量可在0.5重量%至7.0重量%的范围内。
26.镍分散于其上的多孔金属氧化物可以为任何合适的耐火氧化物,其包括氧化铝、二氧化钛、氧化锆、锌氧化物、氧化镁、二氧化铈、镨氧化物、氧化钇和氧化镧。优选的多孔金属氧化物包括氧化铝、氧化锆、二氧化铈、氧化镧以及它们中的两种或更多种的混合物。
27.在一些实施方案中,该金属或陶瓷结构可以为实心体,诸如球体或圆柱体,其可具有一个或多个通孔。此类结构化催化剂可以与常规粒状蒸汽重整催化剂相当的方式使用。
28.在一些实施方案中,该结构化催化剂可包括具有多个通道的金属或陶瓷结构,工艺流体能够以有序而非随机的方向通过该通道。当需要减小压降和改善的传热时,此类结构化催化剂是优选的。因此,该结构化催化剂可包括具有与该管互补的直径的圆柱形单元,该圆柱形单元放置在管内,该圆柱形单元包括多个通道,工艺流体能够以有序而非随机的方向通过该通道。所谓术语“互补”指该圆柱形单元的直径可比放置该单元的管的内径小1mm至20mm,从而使其整齐地放置于管内。该圆柱形单元可包括穿孔和/或内部结构,该穿孔和/或内部结构使工艺流体通过单元时轴向和径向流动。优选地,该圆柱形单元可堆叠,从而使得其可轻松装载于彼此之上,并在管内形成自支撑。使用具有工艺流体能够以有序而非随机的方向通过的多个通道的圆柱形单元而非涂层粒料的优点在于可减少催化剂涂层的量。例如,对于涂层金属或陶瓷粒料,涂层可以每立方米管约100kg至150kg的ni(以nio计)进行施加。对于具有工艺流体能够以有序而非随机的方向通过的多个通道的涂层圆柱形结构,涂层的量能够为每立方米管约4kg至7kg的ni(以nio计)。
29.优选地,使用可商购获得的不锈钢金属箔制备的结构化催化剂。
30.us2012/0195801a1中描述了优选的结构化催化剂。这些结构化催化剂包括布置于中心杆上的波浪形金属盘形式的扇形装置。该扇形装置具有由折叠的金属箔形成的径向流体管道,其沿径向引导流体与管内壁流动接触;该扇形装置具有上表面、下表面和外径面,使得径向流体管道沿着该扇形装置的外径面终止,以形成面向管的内壁的流体管道开口。该扇形装置还具有与该扇形装置的上表面或下表面接触的平面或波浪形金属垫圈,其中该垫圈可以为具有内径和外径的环形,该垫圈与该扇形装置的上表面或下表面接触,使得该垫圈的外径从该扇形装置的外径面沿径向向外延伸。该垫圈还可具有从该垫圈的外径向外延伸的分隔突出片,该分隔突出片将该垫圈与管内壁分隔开,使得该垫圈在该扇形装置的外径面与反应器管之间产生间隔。另选的蒸汽重整催化剂可负载于其上的结构化催化剂布置包括us2012/0294779、us2012/0288420、us8257658、us8235361、us7976783、us7566487、us7761994、us8178075和us7871579中描述的催化剂。
31.在每根管中可有单一类型的结构化催化剂,在这种情况下,管中的催化剂床仅由结构化催化剂组成。或者,在管中可有两层、三层或更多层的蒸汽重整催化剂,其中在每种情况下,至少邻近管出口的层为结构化催化剂。
32.因此,管可在结构化催化剂的上游包括非结构化蒸汽重整催化剂。蒸汽重整催化剂的相对量的厚度可发生变化,以达到期望的转化率。在一些实施方案中,邻近管出口处包
括非结构化催化剂层和结构化催化剂层,则结构化催化剂层可占床体积的95%至5%,或可占床体积的80%至20%,或可占床体积的75%至25%。在管的剩余部分中催化剂床中的其它蒸汽重整催化剂层可以为常规的粒状催化剂,其中镍分布在粒料或者蛋壳型镍基催化剂中,其中镍层仅存在于耐火金属氧化物颗粒的表面上。合适的非结构化催化剂由镍和可选的钾氧化物的粒料组成,该粒料负载在包含氧化铝或碱土金属铝酸盐诸如铝酸钙和/或铝酸镁的耐火氧化物载体上。
33.在催化剂床由两层或三层镍蒸汽重整催化剂组成的情况下,优选地,管入口处的催化剂层为非结构化的粒状镍蒸汽重整催化剂。在结构化蒸汽重整催化剂的上游使用非结构化粒状催化剂的情况下,优选地,非结构化的粒状催化剂的镍含量(以nio表示)在10重量%至30重量%的范围内。因此,在一些实施方案中,催化剂管可包括两层镍蒸汽重整催化剂或由两层镍蒸汽重整催化剂组成,其中邻近管出口的催化剂层为结构化镍蒸汽重整催化剂,并且邻近管入口的催化剂层为含有10%至30%镍(以nio表示)的非结构化的粒状镍蒸汽重整催化剂。
34.通常,催化剂以氧化形式提供到管式蒸汽重整器的管中,并通过镍氧化物还原进行活化,以原位形成元素镍。例如,氧化形式的催化剂可置于管中,并且用还原剂诸如含氢气体还原镍氧化物。已知的还原技术可用于产生用于蒸汽重整的活性催化剂。
35.另选地,可将催化剂中的镍氧化物非原位还原,然后使用含氧气体诸如空气或氮气稀释的空气使得元素金属涂覆有薄的氧化物钝化层。也可使用氧气和二氧化碳(可选地,与氮气)的混合物。以这种方式,还原的催化剂可被安全地运输给使用者,并且生成活性催化剂的时间和在后续活化期间使用的氢气的量减少。
36.可使用各种管式蒸汽重整器布置。管式蒸汽重整器可以为常规的顶烧蒸汽重整器或侧烧蒸汽重整器。在此类重整器中,通过使用置于管顶端或沿着管长度方向的多个燃烧器燃烧燃料气体来提供热气。或者,该蒸汽重整器可以为气体加热重整器(ghr),其中热气可由来自燃烧过程的烟道气提供,或者可以为通过烃的催化或非催化部分氧化或通过烃和/或重整气体混合物的自热重整产生的合成气。此外,热气可与已经通过上述多个管的重整气体进行混合。这些管可具有圆形横截面,并且可具有5m至15m的长度,并且优选地,具有在5cm至30cm或10cm至15cm范围内的内径。在使用中,管沿自身长度方向以温度梯度进行操作,管入口端通过吸热蒸汽重整反应进行冷却。管和入口处反应气体的温度可在300℃至650℃或450℃至650℃,优选地在450℃至600℃,更优选地在450℃至550℃的范围内。在用以形成合成气的转化基本完成的管出口端处,管的温度更高。管和出口处反应气体的温度可在600℃至950℃的范围内。可以将管中催化剂的温度表示为床的温度,这一温度为一个或多个管中催化剂床的入口和出口之间催化剂的平均温度。理想地,床的温度可在625℃至775℃或640℃至760℃的范围内。
37.从管出口回收重整气体或粗制合成气。该重整气体含有氢气、一氧化碳、二氧化碳、水蒸气、氨和甲烷。由于该方法具有平衡缺陷,该重整气体含有一些甲烷。来自管式重整器的甲烷含量或“甲烷泄漏”指示该工艺的效率。此外,甲烷可在使用重整气体的下游工艺中累积,这是不理想的。相应地,低量甲烷泄漏更为理想。使用结构化蒸汽重整催化剂和上述反应条件,该方法能够提供低量甲烷泄漏,例如基于干气体低于15体积%。在随后粗制合成气不进行二次或自热重整的情况下,优选地,甲烷泄漏基于干气体低于10体积%,并且尤
其是基于干气体小于5体积%。术语“基于干气体”指不考虑重整气体的蒸汽含量,并且用于允许与具有不同蒸汽量的其它重整气体进行比较。
38.此外,重整气体的氨含量出人意料的低。不受理论的束缚,申请人认为,镍仅作为薄层存在于结构的表面意味着有氨形成的副反应受到抑制。因此,在该方法中,重整气体的氨含量基于干气体可低于200ppmv。在一些实施方案中,重整气体的氨含量基于干气体可低于100ppmv,优选地低于50ppmv,更优选地低于10ppmv。
39.相应地,本发明进一步提供了如本文所述的一种结构化蒸汽重整催化剂的用途,该催化剂包含:分散在多孔金属氧化物表面上的镍,该多孔金属氧化物作为涂层存在于非多孔金属或陶瓷结构上,其中该金属氧化物涂层的镍含量在5重量%至50重量%的范围内,并且该涂层的厚度在5微米至150微米的范围内,以在对含氮烃原料进行催化蒸汽重整期间抑制氨的形成。
40.该方法还可包括:将该重整气体冷却至露点以下,以使蒸汽冷凝,以及然后将该冷凝液分离,以从该重整气体中形成合成气。该冷凝液捕获大部分(如非全部)在蒸汽重整方法中形成的氨。该冷凝液的氨含量可低于400mg/l,优选地低于200mg/l,更优选地低于100mg/l,最优选地低于50mg/l或甚至20mg/l。在一个优选的实施方案中,至少一部分该冷凝液经过再循环并且用于产生用于该蒸汽重整方法的蒸汽。
41.本发明所述的方法可用作制造氢、甲醇、二甲基醚、烯烃、氨、尿素或通过费托合成法获得的液烃诸如柴油燃料的方法的一部分。因此,重整气体可经过进一步处理,包括:将其冷却至低于蒸汽露点、冷凝液分离、氢分离、二氧化碳分离、甲醇合成、二甲基醚合成、烯烃合成、氨合成或烃液体合成的一个或多个步骤。已知的方法可用于完成这些步骤。
42.结合以下图1至图6所示实施例进一步描述本发明,其中:
43.图1是描绘了在使用含有2体积%的n2的重整器进料的试验中每秒产生的氨相对于每mol%乙烷的转化率的图;
44.图2是描绘了在使用含有5体积%的n2的重整器进料的试验中每秒产生的氨相对于每mol%乙烷的转化率的图;
45.图3是描绘了在使用含有8体积%的n2的重整器进料的试验中每秒产生的氨相对于每mol%乙烷的转化率的图;
46.图4是描绘了在使用含有2体积%的n2的重整器进料的试验中,催化剂中每mol%乙烷转化率相对于催化剂中每m2的ni中每秒产生的氨的图;
47.图5是描绘了在使用含有5体积%的n2的重整器进料的试验中,催化剂中每mol%乙烷转化率相对于催化剂中每m2的ni中每秒产生的氨的图;以及
48.图6是描绘了在使用含有8体积%的n2的重整器进料的试验中,催化剂中每mol%乙烷转化率相对于催化剂中每m2的ni中每秒产生的氨的图。
49.实施例1
50.在常规圆柱形粒状蒸汽重整催化剂上和结构化催化剂上进行测试,该常规圆柱形粒状蒸汽重整催化剂含有17.6重量%的镍或7.2重量%的镍,而该结构化催化剂包括在稳定化铝氧化物上含有13重量%的镍和0.25重量%的铑的催化剂涂层,其作为载体涂层施加到不锈钢颗粒(3.3mm
×
3.3mm的圆柱)上。该催化剂涂层负载为23mg/in2。该催化剂涂层的厚度为约30微米。
[0051][0052]
在具有内径为约25mm及长度为约2100mm的单个电加热重整器管的实验室用蒸汽重整器中测试上述催化剂。反应器基于向上流动的方式进行操作。通过可变冲程泵将用于产生蒸汽的水供应到该装置中,并馈送到该反应器的底部,水在此处进行气化。将天然气通过单独的脱硫容器馈送,然后经由热式质量流量控制器递送至反应器。如果需要,氮气和氢气也通过独立的质量流量控制器供应到反应器中。水和气体全部通过相同的入口管进入反应器。气体产物经由管出口离开反应器并冷却至环境温度以冷凝蒸汽,然后将蒸汽收集在捕气罐中。将少量干燥排出气体馈送到瓦里安cp490四通道微气相色谱(gc)分析仪中。然后,该气体返回到出口气量计处,以允许计算来自重整器的完全质量平衡。
[0053]
对于每种催化剂,测量粒料尺寸以确定需要多少粒料才能产生21080mm2的几何表面积(gsa)。对于结构化催化剂,装入363个涂层粒料,而对于比较催化剂,装入389个粒料。装入反应管中的镍的量对于结构化催化剂和对于比较催化剂1(a)和1(b)分别为0.07g、3.45g和1.30g。用3.35mm至4.00mm的氧化铝碎片和在靠近出口处装入重整器管中的混合物将粒料稀释至100ml。重整器管的剩余部分装入有3.35mm至4.75mm的氧化铝碎片。
[0054]
在n2中,使用50体积%的h2在600℃下还原催化剂2小时。
[0055]
然后,在27巴的压力下使用510℃至800℃范围内的床入口温度进行重整,蒸汽与碳的比率为3:1。首先,通过在610℃、685℃、735℃、800℃和735℃的入口温度下操作重整器,每种情况以至少8小时来进行比较催化剂的催化剂调节。通过在510℃、580℃、610℃、685℃、735℃、800℃、735℃、685℃、610℃、580℃和510℃的入口温度下操作重整器,每种情况以至少8小时来进行,随后再次在800℃下用h2处理16.5小时,以确保所有的镍为活性还原形式,从而进行结构化催化剂的催化剂调节。这种额外的调节是为了确保催化剂被完全还原并且不被认为在随后的测试中影响氨的形成。
[0056]
经过调节后,在685℃、735℃和800℃的入口温度下对每种催化剂进行测试。
[0057]
进料的氮含量经过调节以在催化剂入口处的进料气体混合物中提供基于湿气体为2体积%、5体积%和8体积%的n2。
[0058]
从重整器收集重整气体并冷却至露点以下,以冷凝蒸汽并形成含氨的冷凝液。冷凝液中的氨含量与蒸汽重整器中催化剂所形成的氨成比例。在8小时测试期的末尾,在5分钟内收集冷凝液样本(250ml)并分析其中的氨含量。
[0059]
使用校准的离子选择性电极(ise)测量从重整气体回收的冷凝液中的氨浓度。制备含有0.1ppm(w/v)、1ppm(w/v)和10ppm(w/v)的氨的标准溶液。将氢氧化钠缓冲液加入到上述样本中以释放氨。当ise电压测量值稳定时,使用读数产生ise电压读数对log10氨浓度的线性校准曲线。使用ise测量的电压读数通过从校准曲线推导来确定氨浓度,从而以相同的方式分析上述冷凝液中的氨浓度。
[0060]
使用含有不同氮量的进料气体对每种催化剂进行重复测试。这通过经由氮气供应
管线以各种流量引入氮气以提供馈送到重整器管的进料气体中的所需水平来进行。
[0061]
下表列出了对于具有不同氮含量的进料气体用于不同催化剂的冷凝液中产生的氨的结果。
[0062]
比较催化剂1(a)床入口温度℃[n2],vol.%[nh3],mg/l 68520.102 68550.226 68580.451 73520.209 73550.515 73580.901 80020.501 80051.100 80081.800
[0063]
比较催化剂1(b)床入口温度℃[n2],vol.%[nh3],mg/l 68520.050 68550.081 68580.144 73520.071 73550.210 73580.420 80020.166 80050.435 80080.807
[0064]
结构化催化剂1(c)床入口温度℃[n2],vol.%[nh3],mg/l 68520.015 68550.018 68580.019 73520.014 73550.020 73580.026 80020.031 80050.060 80080.081
[0065]
在入口温度的范围内,相较于比较实施例,结构化催化剂产生的氨的量更低。然而,催化剂含有不同的量镍,具有不同的镍表面积,并具有不同的活性。如果一种催化剂更具活性,则消耗的蒸汽量将大于活性较低的催化剂所消耗的量。当这一未反应的蒸汽进行冷凝时,氨浓度会受到影响。为此,基于氧平衡计算水的摩尔流量,该平衡根据从进料气体的组成和速率的知识以及使用与蒸汽重整器耦接的gc系统获得的有关重整气体的气相色
谱数据导出。进入和离开该系统的氧气量的差异可用于确定每秒产生的氨的量。
[0066]
此外,该结构化催化剂能够以天然气中烃的高转化率产生重整气体。
[0067]
通过气相色谱法分析除去冷凝液后的重整气体,以确定烃向氢气和碳氧化物的转化率。与可逆的甲烷转化相比,天然气中乙烷的转化率更有助于测量总的催化剂活性。
[0068]
将氨浓度/秒相对于乙烷的转化率作图说明催化剂在活性和氨产生方面的有效性。图1至图3示出了产生的氨/秒相对于乙烷转化率的百分比。结果在以下列出:
[0069][0070][0071][0072]
相较于比较催化剂,该结构化催化剂在测试温度下的乙烷转化率以更低水平开始,但可以看出,在800℃下,相较于比较催化剂1(b),该结构化催化剂提供了更高的乙烷转化率,不过产生了一小部分氨,在进料气体的n2含量为2体积%、5体积%和8体积%的情况下均是如此。而在735℃下的比较催化剂1(a)达到了与800℃下的结构化催化剂相当的乙烷转化率,但后者含有一小部分镍含量。在更高的入口温度下对结构化催化剂进行测试可进一步提升乙烷转化率并保持较低氨浓度。
[0073]
尽管对于给定的入口温度,该结构化催化剂的活性低于标准粒状催化剂的活性,但将催化剂在相同的烃转化率下进行操作时产生的氨考虑在内是有意义的,能够更好地反映在使用中预期的操作。此外,在该结构化催化剂中的镍晶粒比粒状催化剂中的镍晶粒小一个数量级,从而具有不同的镍表面积(比较催化剂1(a)为0.5m2/g,而结构化催化剂为8m2/g)。考虑到这一点,结构化催化剂和粒状催化剂之间的性能差异得到了更清晰的描述。图4、图5和图6示出了根据镍表面积产生的氨相对于乙烷转化率的百分比。这些图说明使用结构
化催化剂产生的氨的量显著低于使用常规粒状催化剂产生的氨的量。此外,可以使用明显更少的镍获得与粒状催化剂相当的活性,同时产生明显更少的氨。这已通过将镍分散在非多孔载体上的薄涂层中实现。这些结果说明,通过在重整器出口附近使用结构化催化剂,可以减少氨的形成,而不影响整体重整性能。