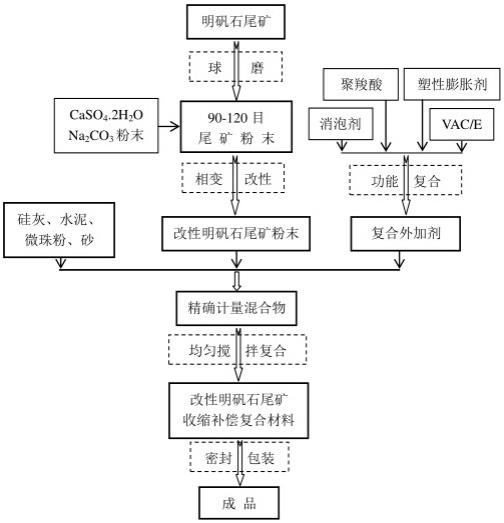
1.本发明属于无机固体废弃物资源化利用领域,适用于明矾石尾矿综合性资源化利用,是一种利用活性二氧化硅含量低的明矾石制备收缩补偿水泥基复合材料的方法。
背景技术:2.我国矿产资源丰富,特别是非金属矿产资源,在矿物浮选过程中会产生大量的废弃尾矿。如,福建紫金山铜矿是大型低品位铜矿,主要金属矿物为黄铁矿、硫砷铜矿等,非金属矿物以石英、明矾石、高岭石为主。当前,紫金山铜矿资源中铜品位0.4%以上通过浮选处理的矿石量约为1.25亿吨,尾矿产率为90%,因此紫金山铜尾矿量将达到1亿吨以上,这些尾矿中含有大量有利用价值的非金属矿物。目前,己成功从铜尾矿中浮选富集硫铁矿产品,然后浮选明矾石精矿产品,浮选得到的明矾石精矿中明矾石品位可达60%~70%。尾矿的堆积会占用大量土地,也会引起环境生态污染甚至地质灾害。因而,明矾石尾矿的资源化利用具有重要的资源和环境意义。
3.目前,有关明矾石尾矿高值化应用的综合利用研究还不成熟,不少国家和地区都在探索适合自己条件的明矾石加工工业技术,而且倾向于酸法工艺路线的研究,但能够顺利实现工业化连续生产的技术路线却非常稀少,主要是因为成本过高等各种原因阻碍了其工业化应用。此外,明矾石尾矿中含有较丰富的二氧化硅晶体、硫酸铝盐,为制备具有收缩补偿功能的水泥基复合材料提供了潜在可能。
4.水泥基材料作为常用的建筑材料,被广泛应用于各类工程结构。但其存在较为严重的养护收缩和长期徐变收缩现象,容易导致水泥基材料制品尺寸改变甚至收缩开裂。开发基于明矾石尾矿的收缩补偿材料,既可以实现尾矿的资源化利用,又可针对水泥基材料的固有缺陷进行改善。
技术实现要素:5.本发明针对煅烧后的明矾石尾矿制备风电基座灌浆料的方法,该方法是一种工艺简单、成本低廉的明矾石尾矿处理方法。
6.本发明针对明矾石尾矿中含有的二氧化硅和硅酸盐矿物,提供一种制备新型公路护轮带修复工程复合材料及其制备方法,该方法是一种工艺简单、成本低廉的明矾石尾矿的高效资源化处理方法。
7.本发明的技术方案包含以下几个主要部分:1)明矾石高温改性明矾石尾矿中含有较丰富的二氧化硅,但这些二氧化硅多处于晶体状态,缺乏必要的活性,难以产生火山灰反应和效应。该专利采用的技术手段是相变改性,即通过在明矾石尾矿中掺入一定质量比例的na2co3和caso4.2h2o粉末进行高温相变改性,使明矾石尾矿中的非活性二氧化硅晶体由晶态变成具有活性的无定型态,同时将明矾石尾矿中非活性的高岭石相变成具有良好火山灰活性的偏高岭土。从而利用相变改性后明矾石尾矿中的活性
无定型二氧化硅与水泥水化,明矾石尾矿中的部分超细铝酸盐矿物作为微骨料与水化硅酸钙具有更好的结合能力,更进一步增加水泥基复合材料的力学强度和耐久性能。同时,激活明矾石中的硫铝酸盐。
8.高温相变改性的温度是一个重要的工艺参数。将明矾石尾矿球磨至粒径为90-120目的颗粒,可以提高明矾石改性的均匀性,同时可以一定程度降低高温改性的温度。同时,加入粒径为100-180目的na2co3粉末可以有效降低明矾石尾矿的熔点和改性温度,从而大幅简化明矾石尾矿的改性工艺,有效降低能源的消耗。所开展的大量实验表明,加入na2co3粉末后可将明矾石尾矿的改性温度调到800~1100℃,因而选该温度范围作为煅烧改性温度;na2co3粉末加入量通常根据明矾石尾矿的矿相以及各化学元素的相对含量而定,通常在0.5wt%-2.5wt%范围之内。
9.对caso4.2h2o进行高温相变改性,将其由结晶水态转化为非结晶水态caso4,改性明矾石尾矿的活性硫铝酸盐、caso4和水泥中的ca(oh)2反应生成具有微膨胀功能的钙矾石,补偿水泥基材料在养护和长期收缩变形,可防止材料因为收缩而出现开裂。
10.高温改性工艺的时间长短也是一个重要的参数,实验表明:如果时间小于2小时则相变改性的程度较低,活性无定型二氧化硅的含量偏低,影响火山灰效应的效果;当时间大于4小时,则可能会出现一定的烧结现象,也会影响晶态二氧化硅的非定型相变活化效果。因而,基于大量实验结果,最终确定相变改性工艺的时间为2-4小时。相变改性结束并冷却至室温后,将混合料球磨至160-200目。
11.2)高效多功能复合外加剂外加剂是制备高性能改性明矾石尾矿复合材料的重要组成部分,不仅可以调整其施工和易性,还可大幅改善其力学性能和物化性能。本发明专利制备了高效多功能复合外加剂,具备减水、控制和易性、提升粘结性、强度和耐久性等综合性功能。其中,减水剂选用了高效聚羧酸或改性聚羧酸,通过减少拌合水用量来提高护轮带材料的力学强度。采用具有良好分散功能的乙烯醋酸乙烯共聚物(vac/e)作为分散剂,提高各组分的分散性和护轮带修复材料的均匀性。同时,加入一定量的塑性膨胀剂,以补充可能存在的收缩补偿不足不放呢;加入一定量的消泡剂,以改善气孔结构,提修复材料的力学性能。经过多次实验,确定了高效多功能复合外加剂的组成,由80-100份聚羧酸或改性聚羧酸减水剂、15-25份乙烯醋酸乙烯共聚物(vac/e)、3-5份消泡剂和1-6份塑性膨胀剂组成。
12.3)后期强度通过掺加3-6份粒径范围0.1-0.3μm纯度大于90%的硅灰,弥补改性明矾石尾矿中无定型二氧化硅含量不足的缺陷,可以提高水泥水化硅酸钙的含量,进一步提高修复材料的后期力学性能和物化性能。同时,加入粉煤灰微珠粉,不仅可改善施工操作的和易性,而且还可以一定程度的提高材料的后期强度。
13.针对本发明专利所述的改性明矾石尾矿进行了火山灰活性实验,采用抗压强度比法以掺入30%改性明矾石尾矿的水泥胶砂28 d抗压强度与硅酸盐水泥胶砂28 d抗压强度之比来表征改性明矾石尾矿的活性指数。如果该比值大于0.62,则认为改性明矾石尾矿具有火山灰胶凝活性,因为非活性磨细石英粉的抗压强度比为 0.62。
14.表1
ꢀꢀ
8天强度比
由表1可以看出改性明矾石尾矿的水泥胶砂28 d抗压强度与硅酸盐水泥胶砂28 d抗压强度之比为0.95,远大于0.62,具有良好的火山灰胶凝活性。
15.针对技术路线中,对改性明矾石中活性硫酸盐及caso4.2h2o无水化改性进行限制膨胀率和抗压强度实验。
16.表2
ꢀꢀ
压强度材料配合比(单位g)表3
ꢀꢀ
限制膨胀率材料配合比(单位g)表4
ꢀꢀ
实验数据由表4可以看出煅烧后的明矾石尾矿通过掺入caso4具有了良好的收缩补偿作用。
17.实现本发明目的的技术方案具体步骤为:第一步将明矾石尾矿球磨至粒度范围为90-120目;第二步在球磨后的明矾石尾矿粉末中加入一定质量份数的caso4.2h2o和na2co3粉末和,并进行充分搅拌,形成均匀的混合物;第三步将混合物粉末加入高温炉进行2-4小时的改性,然后缓慢冷却至室温后进行球磨,形成改性明矾石尾矿粉末;第四步将原材料按质量份比例称取,水泥80-90份,相变改性明矾石尾矿粉2-10份,硅灰0-3份,微珠粉1-5份,砂90-100份,活性矿粉0-5份,多功能复合外加剂0.10-0.68份;第五步:将改性明矾石尾矿粉、硅灰、水泥、微珠粉、砂、活性矿粉和高效多功能复合外加剂按顺序先加入搅拌锅中搅拌4-8分钟,形成收缩补偿水泥基复合材料;第六步:将上述收缩补偿水泥基复合材料进行防潮密封包装。
附图说明
18.图1是本发明的本发明制备煅烧后的明矾石尾矿制备风电基座灌浆料的工艺流程图。
具体实施方式
19.下面具体说明本发明的实施方式。
20.如图1所示,第一步将明矾石尾矿球磨至粒度范围为90-120目;第二步在球磨后的明矾石尾矿粉末中加入一定质量份数的caso4.2h2o和na2co3粉末和,并进行充分搅拌,形成均匀的混合物;第三步将混合物粉末加入高温炉进行2-4小时的改性,然后缓慢冷却至室温后进行球磨,形成改性明矾石尾矿粉末;第四步将原材料按质量份比例称取,水泥80-90份,改性明矾石尾矿粉2-10份,硅灰0-3份,微珠粉1-5份,砂90-100份,活性矿粉0-5份,多功能复合外加剂0.10-0.68份;第五步:将改性明矾石尾矿粉、硅灰、水泥、微珠粉、砂、活性矿粉和高效多功能复合外加剂按顺序先加入搅拌锅中搅拌4-8分钟,形成收缩补偿水泥基复合材料;第六步:将上述收缩补偿水泥基复合材料进行防潮密封包装。
21.上述各步骤中所述的水泥为425或525硅酸盐水泥;所述的石英砂的细度模数为2.6-3.2,所述的硅灰为二氧化硅(sio2)含量大于90%,粒径为0.1-0.3μm;所述的矿粉为s95及以上等级矿粉;所述的高效多功能复合外加剂聚羧酸或改性聚羧酸、乙烯醋酸乙烯共聚物(vac/e)、消泡剂和塑性膨胀剂组成;所述的改性明矾石尾矿粉是将明矾石尾矿放入煅烧炉中,温度800~1100℃进行高温煅烧2~4小时取出冷却至室温后放入球磨机中磨细获得,细度为160-200目,筛余小于5%。
22.下述实施例中,采用的明矾石尾矿来自福建,其化学成分分析见表5,主要矿物组成见表6。
23.表5
ꢀꢀ
明矾石尾矿化学成分分析表6
ꢀꢀ
明矾石尾矿的主要矿物组成实施例1:结合图1,混合料配合比见表7表7
ꢀꢀ
实施例1混合料配合比第一步:将硅灰0.5kg、矿粉0.5kg、水泥4kg、改性明矾石尾矿粉1kg、多功能复合外
加剂0.06kg、石英砂8kg按顺序先加入搅拌锅中搅拌1~2分钟;第二步:加入拌合水2公斤搅拌2~3分钟,制备样品。
24.实施例2:结合图1混合料配合比见表8。
25.表8
ꢀꢀ
实施例2混合料配合比第一步:将硅灰0.5kg、矿粉0.5kg、水泥5kg、改性明矾石尾矿粉1kg、多功能复合外加剂0.06kg、石英砂8kg按顺序先加入搅拌锅中搅拌1~2分钟第二步:加入拌合水2公斤搅拌2~3分钟,制备样品。
26.实施例3:结合图1混合料配合比见表9。
27.表9
ꢀꢀ
实施例3混合料配合比第一步:将硅灰0.5kg、矿粉0.5kg、水泥6kg、改性明矾石尾矿粉1kg、多功能复合外加剂0.06kg、石英砂8kg按顺序先加入搅拌锅中搅拌1~2分钟;第二步:加入拌合水2公斤搅拌2~3分钟,制备样品。
28.上述实施例制得的风电基座灌浆料的抗压强度和流动度见表10。
29.表10
ꢀꢀ
利用改性明矾石尾矿制得的风电基座灌浆料的抗压强度和流动度