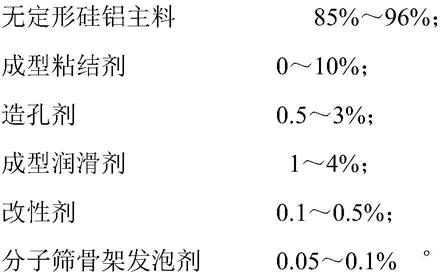
4a分子筛配料及4a分子筛制作方法
技术领域
1.本发明涉及的是一种4a分子筛配料,具体是用于环境voc吸附的分子筛,可用于吸附水,甲醇、乙醇、硫化氢、氟化氢、二氧化硫、二氧化碳、乙烯、丙烯、甲烷、乙醚、乙炔等voc气体吸附治理的环保领域。本发明还涉及了该种分子筛的制作方法。
背景技术:2.分子筛吸附是一种应用价值巨大的污染气体分离技术,在很多voc排放领域有广泛的应用。分子筛材料作为一种优势的吸附材料,具有耐介质腐蚀、机械性能好、运行寿命长等特点。与传统燃烧工艺相比,使用分子筛寿命长,能耗低,处理效果好,且能解决无组织废气治理问题。同时,采用自动化控制吸附、脱附工艺,能方便地通过自动收集、富集废气,实现工业生产voc治理自动化高效进行。
3.4a分子筛以高装填密度,在同体积下具有更高的吸附比表面积。但是4a分子筛的生产与加工面临以下问题:
4.一、分子筛骨架孔隙分布不均匀,吸附效率低;
5.二、分子筛内部孔隙结构,封闭孔隙占比过高;
6.三、普通分子筛再生温度过高,再生过程超过650摄氏度,就会造成纳米结构坍塌,分子筛的结构稳定性差;
7.四、有机物添加量大,烧制过程,有机物产生的废气需要深度处理,分子筛生产过程不利于环保。
技术实现要素:8.本发明需要解决的技术问题是提供一种4a分子筛配料,该种4a分子筛配料制作出的4a分子筛均匀孔隙分布、开放孔隙占比高,制作过程比较环保。
9.本发明还提供了使用上述4a分子筛配料的一种4a分子筛制作方法。
10.本发明还提供了一种上述4a分子筛的制作方法。
11.本发明4a分子筛配料采取如下技术方案:
12.一种4a分子筛配料,包括以下质量百分含量的各组分:
[0013][0014]
本发明解决问题还可以进一步采取以下改进措施:
[0015]
优选地,所述无定形硅铝主料包括无定形氧化硅、氢氧化铝中的至少一种。
[0016]
优选地,所述无定形硅铝主料中,无定形氧化硅和氢氧化铝的质量比为9:1~6:4。通过无定形氧化硅和氢氧化铝的协调配比,可获得较好的成型性能和烧结特性。
[0017]
优选地,所述无定形硅铝主料的粒度不大于10微米,并依据设计分子筛的气流通道孔径要求,选择合适的粒度范围。更优选地,设计的分子筛气流通道孔径为0.1微米时,选用粒度为2~4微米的无定形硅铝主料;设计的分子筛气流通道孔径为1微米时,选用粒度为5~8微米的无定形硅铝主料。
[0018]
优选地,所述成型粘结剂包括聚乙烯醇(pva)、改性淀粉醚、羧甲基淀粉(cms)中的至少一种;所述造孔剂包括炭黑粉、石墨粉、膨胀石墨粉、纤维素中的至少一种。
[0019]
优选地,所述成型润滑剂为植物油。更优选成型润滑剂为菜籽油。
[0020]
优选地,改性剂包括氧化镁、氢氧化镁、氧化钙、高岭土、氧化锌、五氧化二钒、氧化锆中的一种或几种;
[0021]
分子筛骨架发泡剂包括碳化硅、氮化硅、氮化铝、氮化硼中的一种或几种。
[0022]
为获得更好的大孔隙率分子筛骨架,选用微量的中高温发泡剂,配合造孔剂使用,可获得大于55%的开口孔隙率。
[0023]
使用上述4a分子筛配料的4a分子筛制作方法技术方案为:
[0024]
包括以下步骤:
[0025]
a、将所述的各组分按比例混合均匀,得混料;
[0026]
b、将混料进行挤出成型,具体包括将混料进行球磨、练泥、陈化、挤出、干燥、烧制和修整的步骤,即得所述4a分子筛;或
[0027]
c、将混料进行干压成型,具体包括将混料进行干压、烧制和修整的步骤,即得所述4a分子筛。
[0028]
优选地,步骤b中,所述陈化的时间为12~36小时。
[0029]
优选地,步骤b中,所述烧成前还包括排胶的步骤,所述排胶温度为260~400℃,排胶时间为2~8小时;所述烧成温度为770~1050℃,烧成时间为0.5~2小时;
[0030]
步骤c中,所述烧成前还包括排胶的步骤,所述排胶温度为260~400℃,排胶时间为1~2小时;所述烧成温度为770~1050℃,烧成时间为0.5~2小时;
[0031]
优选地,步骤b和c中,所述喷膜的厚度为5~25微米;烧成温度为880~980℃,烧成时间为0.5~1.5小时。
[0032]
上述技术方案具有这样的技术效果:
[0033]
1)本发明通过造孔剂和发泡剂的匹配使用,获得分子筛骨架的均匀孔隙分布和全开孔结构,并添加合适的改性剂提高了分子筛的吸附性能。采用无定形氧化硅和氢氧化铝的混合配方,减少粘结剂的加入量。
[0034]
2)本发明的干压成型采用塑料成型支架,获得4a分子筛的孔隙之间的相互联通。提高了孔隙占比。
[0035]
3)本发明制作过程比较环保。
[0036]
4)本发明通过造孔剂和发泡剂的匹配使用,获得分子筛骨架的均匀孔隙分布和全开孔结构,并添加合适的改性剂将烧成温度降低150~250℃。
[0037]
5)本发明4a分子筛制作方法可分别采用(1)挤出成型制作蜂窝结构;(2)干压成型制作平板或异性结构;(3)滚球机制作球状结构。
具体实施方式
[0038]
下面结合具体实施例对本发明进行具体描述。
[0039]
实施例1:
[0040]
一种4a分子筛配料,包括无定形硅铝主料、改性剂、造孔剂、成型润滑剂和分子筛骨架发泡剂、成形粘结剂。所述各组分的质量百分含量如下:无定形硅铝主料为无定形氧化硅和氢氧化铝的混合物,无定形氧化硅和氢氧化铝的混合物(混合比例为:8:2)85%;成型粘结剂,即聚乙烯醇(pva)10%;造孔剂,即炭黑粉0.5%;成型润滑剂,即菜籽油4%;改性剂,即氧化镁0.45%;分子筛骨架发泡剂,即碳化硅0.05%。
[0041]
本实施例提供了一种4a分子筛的制作方法,包括以下步骤:
[0042]
a、将改性剂、造孔剂、成型润滑剂和分子筛骨架发泡剂先与成形粘结剂混合均匀,再加入无定形硅铝主料混合得混料;所述各组分的质量百分含量如下:无定形氧化硅和氢氧化铝的混合物(混合比例为:8:2)85%;聚乙烯醇(pva)10%;炭黑粉0.5%;菜籽油4%;氧化镁0.45%;碳化硅0.05%。
[0043]
优选地,所述无定形硅铝主料的粒度不大于10微米,并依据设计分子筛的气流通道孔径要求,选择合适的粒度范围。更优选地,设计的分子筛气流通道孔径为0.1微米时,选用粒度为2~4微米的无定形硅铝主料;设计的分子筛气流通道孔径为1微米时,选用粒度为5~8微米的无定形硅铝主料。
[0044]
b、将混料进行挤出成型,具体包括将混料进行球磨、练泥、陈化、挤出、干燥、烧制和修整的步骤,即得所述4a分子筛;
[0045]
步骤b中,所述混料球磨时间为5~10小时,混好原料以九份加一份水进行捏合制泥,练好的泥料经过12~36小时陈化后待成型;烧制包括依次排胶、喷膜、烧成步骤,排胶温度为260~400℃,排胶时间为2~8小时;烧成温度为770~1050℃,烧成时间为0.5~2小时;喷膜的厚度为5~25微米,喷膜是用常规操作,喷膜温度为770~1050℃,相当在分子筛产品表面做一层稳定剂,膜料的主配方是粒度更小的上述配方原料粉体颗粒。
[0046]
本实施例制得的4a分子筛的孔隙分布均匀,采用饱和吸水法测量其多孔结构孔隙占比为32~34%,即全部孔隙占分子筛的体积的32~34%。
[0047]
本例中,也可以去除烧制中的排胶、喷膜工序,或去除排胶、喷膜工序中一个工序。
[0048]
实施例2:
[0049]
一种4a分子筛配料,包括无定形硅铝主料、改性剂、造孔剂、成型润滑剂和分子筛骨架发泡剂、成形粘结剂。所述各组分的质量百分含量如下:无定形硅铝主料为无定形氧化硅和氢氧化铝的混合物,无定形氧化硅和氢氧化铝的混合物(混合比例为:6:4)90%;成型粘结剂,即改性淀粉醚4.4%;造孔剂,即石墨粉3%;成型润滑剂,即大豆油2%;改性剂,即氢氧化镁0.5%;分子筛骨架发泡剂,即氮化硅0.1%。
[0050]
本实施例提供了一种4a分子筛的制作方法,包括以下步骤:
[0051]
a、将改性剂、造孔剂、成型润滑剂和分子筛骨架发泡剂先与成形粘结剂混合均匀,再加入无定形硅铝主料混合得混料;所述各组分的质量百分含量如下:无定形氧化硅和氢氧化铝的混合物(混合比例为:6:4)90%;改性淀粉醚4.4%;石墨粉3%;大豆油2%;氢氧化镁0.5%;氮化硅0.1%。
[0052]
无定形硅铝主料的粒度大小选择方法与实施例1一样。
[0053]
b、将混料进行挤出成型,具体包括将混料进行球磨、练泥、陈化、挤出、干燥、烧制和修整的步骤,即得所述4a分子筛;
[0054]
步骤b中,所述混料球磨时间为5~10小时,混好原料以九份加一份水进行捏合制泥,练好的泥料经过12~36小时陈化后待成型;烧制包括排胶、喷膜、烧成步骤,所述排胶温度为260~400℃,排胶时间为2~8小时;所述烧成温度为770~1050℃,烧成时间为0.5~2小时;所述喷膜的厚度为5~25微米,喷膜是用常规操作,喷膜温度为770~1050℃,膜料的主配方是粒度更小的上述配方原料粉体颗粒。烧成时间也可以选择为0.5~1.5小时。
[0055]
本实施例采用饱和吸水法测量制得的4a分子筛的孔隙分布均匀,多孔结构孔隙占比(即全部孔隙占分子筛的体积的比例)为30~33%。
[0056]
本例中,也可以去除烧制中的排胶、喷膜工序,或去除排胶、喷膜工序中一个工序。
[0057]
实施例3:
[0058]
一种4a分子筛配料,包括无定形硅铝主料、改性剂、造孔剂、成型润滑剂和分子筛骨架发泡剂、成形粘结剂。所述各组分的质量百分含量如下:无定形硅铝主料为无定形氧化硅和氢氧化铝的混合物,无定形氧化硅和氢氧化铝的混合物(混合比例为:5:5)95%;成型粘结剂,即聚乙烯醇(pva)3%;造孔剂,即纤维素1.8%;成型润滑剂,即菜籽油1%;改性剂,即五氧化二钒0.1%;分子筛骨架发泡剂,即氮化铝0.1%。
[0059]
本实施例提供了一种4a分子筛的制作方法,包括以下步骤:
[0060]
a、将改性剂、造孔剂、成型润滑剂和分子筛骨架发泡剂先与成形粘结剂混合均匀,再加入无定形硅铝主料混合得混料;所述各组分的质量百分含量如下:无定形氧化硅和氢氧化铝的混合物(混合比例为:5:5)95%;聚乙烯醇(pva)3%;纤维素1.8%;菜籽油1%;五氧化二钒0.1%;氮化铝0.1%。
[0061]
无定形硅铝主料的粒度大小选择方法与实施例1一样。
[0062]
b、将混料进行挤出成型,具体包括将混料进行球磨、练泥、陈化、挤出、干燥、烧制和修整的步骤,即得所述4a分子筛;
[0063]
步骤b中,所述混料球磨时间为5~10小时,混好原料以九份加一份水进行捏合制泥,练好的泥料经过12~36小时陈化后待成型;烧制包括排胶、喷膜、烧成步骤,所述排胶温度为260~400℃,排胶时间为2~8小时;所述烧成温度为770~1050℃,烧成时间为0.5~2小时;所述喷膜的厚度为5~25微米,喷膜是用常规操作,喷膜温度为770~1050℃,相当在分子筛产品表面做一层稳定剂,膜料的主配方是粒度更小的上述配方原料粉体颗粒。
[0064]
本实施例制得的4a分子筛的孔隙分布均匀,采用饱和吸水法测量其多孔结构孔隙占比(即全部孔隙占分子筛的体积的比例)为30~32%。
[0065]
本例中,也可以去除烧制中的排胶、喷膜工序,或去除排胶、喷膜工序中一个工序。
[0066]
实施例4:
[0067]
一种4a分子筛配料,包括无定形硅铝主料、改性剂、造孔剂、成型润滑剂和分子筛骨架发泡剂、成形粘结剂。所述各组分的质量百分含量如下:无定形硅铝主料为无定形氧化硅和氢氧化铝的混合物,无定形氧化硅和氢氧化铝的混合物(混合比例为:5:5)96%;成型粘结剂,为0%;造孔剂,即纤维素1.8%;成型润滑剂,即菜籽油1%;改性剂,即五氧化二钒0.1%;分子筛骨架发泡剂,即氮化铝0.1%。
[0068]
本实施例提供了一种4a分子筛的制作方法,包括以下步骤:
[0069]
a、将改性剂、造孔剂、成型润滑剂和分子筛骨架发泡剂与无定形硅铝主料干燥后混合5~10小时得混料;所述各组分的质量百分含量如下:无定形氧化硅和氢氧化铝的混合物(混合比例为:5:5)96%;纤维素2.8%;菜籽油1%;五氧化二钒0.1%;氮化铝0.1%。
[0070]
无定形硅铝主料的粒度大小选择方法与实施例1一样。
[0071]
c、将混料进行干压成型,具体包括将混料进行干压、烧制和修整的步骤,即得所述4a分子筛;
[0072]
步骤c中,烧制包括排胶、喷膜、烧成步骤,排胶的步骤在烧成前,排胶温度为260~400℃,排胶时间为1~2小时;所述烧成温度为770~1050℃,烧成时间为0.5~2小时;喷膜的厚度为5~25微米,喷膜是用常规操作,喷膜温度为770~1050℃,相当在分子筛产品表面做一层稳定剂,膜料的主配方是粒度更小的上述配方原料粉体颗粒。也可以烧成温度为880~980℃,烧成时间为0.5~1.5小时。
[0073]
所述干压成型采用塑料成型支架,获得4a分子筛的孔隙之间的相互联通。
[0074]
本实施例制得的4a分子筛的孔隙分布均匀,采用饱和吸水法测量其多孔结构孔隙占比(即全部孔隙占分子筛的体积的比例)为30~33%。
[0075]
本例中,也可以去除烧制中的排胶、喷膜工序,或去除排胶、喷膜工序中一个工序。
[0076]
实施例5:
[0077]
一种4a分子筛配料,包括无定形硅铝主料、改性剂、造孔剂、成型润滑剂和分子筛骨架发泡剂、成形粘结剂。所述各组分的质量百分含量如下:无定形硅铝主料为无定形氧化硅和氢氧化铝的混合物,无定形氧化硅和氢氧化铝的混合物(混合比例为6:4)93%;成型粘结剂,为0%;造孔剂,即炭黑粉2.5%;成型润滑剂,即大豆油4%;改性剂,即氢氧化镁0.45%;分子筛骨架发泡剂,即碳化硅0.05%。
[0078]
本实施例提供了一种4a分子筛的制作方法,包括以下步骤:
[0079]
a、将改性剂、造孔剂、成型润滑剂和分子筛骨架发泡剂与无定形硅铝主料干燥后混合5~10小时得混料;所述各组分的质量百分含量如下:无定形氧化硅和氢氧化铝的混合物(混合比例为6:4)93%;炭黑粉2.5%;大豆油4%;氢氧化镁0.45%;碳化硅0.05%。
[0080]
无定形硅铝主料的粒度大小选择方法与实施例1一样。
[0081]
c、将混料进行干压成型,具体包括将混料进行干压、烧制和修整的步骤,即得所述4a分子筛;
[0082]
步骤c中,烧制包括排胶、喷膜、烧成步骤,排胶的步骤在烧成前,所述排胶温度为260~400℃,排胶时间为1~2小时;所述烧成温度为770~1050℃,烧成时间为0.5~2小时;所述喷膜的厚度为5~25微米。喷膜是用常规操作,喷膜温度为770~1050℃,相当在分子筛产品表面做一层稳定剂,膜料的主配方是粒度更小的上述配方原料粉体颗粒。也可以烧成温度为880~980℃。
[0083]
所述干压成型采用塑料成型支架,获得4a分子筛的孔隙之间的相互联通。
[0084]
本实施例制得的4a分子筛的孔隙分布均匀,采用饱和吸水法测量其多孔结构孔隙占比(即全部孔隙占分子筛的体积的比例)为31~35%。
[0085]
本例中,也可以去除烧制中的排胶、喷膜工序,或去除排胶、喷膜工序中一个工序。
[0086]
实施例6:
[0087]
一种4a分子筛配料,包括无定形硅铝主料、改性剂、造孔剂、成型润滑剂和分子筛
骨架发泡剂、成形粘结剂。所述各组分的质量百分含量如下:无定形硅铝主料为无定形氧化硅和氢氧化铝的混合物,无定形氧化硅和氢氧化铝的混合物(混合比例为8:2)95%;成型粘结剂,为0%;造孔剂,即石墨粉0.5%;成型润滑剂,即棕榈油4%;改性剂,即氧化钙0.4%;分子筛骨架发泡剂,即氮化硅0.1%。
[0088]
本实施例提供了一种4a分子筛的制作方法,包括以下步骤:
[0089]
a、将改性剂、造孔剂、成型润滑剂和分子筛骨架发泡剂与无定形硅铝主料干燥后混合5~10小时得混料;所述各组分的质量百分含量如下:无定形氧化硅和氢氧化铝的混合物(混合比例为8:2)95%;石墨粉0.5%;棕榈油4%;氧化钙0.4%;氮化硅0.1%。
[0090]
无定形硅铝主料的粒度大小选择方法与实施例1一样。
[0091]
c、将混料进行干压成型,具体包括将混料进行干压、烧制和修整的步骤,即得所述4a分子筛;
[0092]
步骤c中,烧制包括排胶、喷膜、烧成步骤,排胶的步骤在烧成前,排胶温度为260~400℃,排胶时间为1~2小时;所述烧成温度为770~1050℃,烧成时间为0.5~2小时;所述喷膜的厚度为5~25微米。喷膜是用常规操作,喷膜温度为770~1050℃,相当在分子筛产品表面做一层稳定剂,膜料的主配方是粒度更小的上述配方原料粉体颗粒。也可以烧成温度为880~980℃。所述干压成型采用塑料成型支架,获得4a分子筛的孔隙之间的相互联通。
[0093]
本实施例制得的4a分子筛的孔隙分布均匀,采用饱和吸水法测量其多孔结构孔隙占比(即全部孔隙占分子筛的体积的比例)为30~33%。
[0094]
本例中,也可以去除烧制中的排胶、喷膜工序,或去除排胶、喷膜工序中一个工序。
[0095]
对比例1:
[0096]
一种4a分子筛配料,各组分与实施例1相同。分子筛骨架发泡剂为氮化硅。
[0097]
本对比例提供了一种4a分子筛的制作方法,所述具体步骤与实施例1基本相同,不同之处仅在于:步骤a中,所采用的分子筛骨架发泡剂为氮化硅。
[0098]
本对比例由于采用的分子筛骨架发泡剂为氮化硅,在所述较低的烧成温度下烧制,采用饱和吸水法测量制得的4a分子筛的多孔结构孔隙占比为40~45%。
[0099]
本发明4a分子筛制作方法可分别采用(1)挤出成型制作蜂窝结构;(2)干压成型制作平板或异性结构;(3)滚球机制作球状结构。
[0100]
采用本发明的配料的组分配比时,可以采用干压成型和滚球机成型工艺制备。
[0101]
本发明通过造孔剂和发泡剂的匹配使用,获得分子筛骨架的均匀孔隙分布和全开孔结构,并添加合适的改性剂将烧成温度降低150~250℃。
[0102]
以上所述仅为本发明的较佳实施例而已,并不用以限制本发明,凡在本发明的精神和原则之内所作的任何修改、等同替换和改进等,均应包含在本发明的保护范围之内。