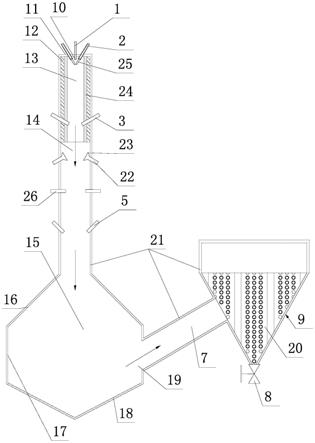
1.本发明涉及锂电池负极材料制备技术领域,具体讲是一种纳米氧化亚硅粉体的制备方法。
背景技术:2.锂电池或称锂离子电池是一种二次电池,即可充放电池,通常包含正极、负极、隔膜、电解液和壳体等部分。正极为高脱锂电位材料,负极为低嵌锂电位材料。与传统电池相比,锂离子电池具有很多优点,如能量密度高、电压高、自放电率低、无记忆效应、循环寿命长、工作温度范围广、工作安全可靠、绿色环保等。锂离子电池已经广泛地应用于移动电话、笔记本电脑等便携式电子设备中,与此同时,电动玩具、电动工具也广泛地使用锂电池。近几年高功率锂电池组被广泛地应用于新能源电动汽车,以蔚来、特斯拉为主的国内外纯电动汽车品牌正逐步地占领市场,取代传统的燃油汽车。
3.目前已经商业化的锂电池的负极材料主要有石墨、硬炭和软炭等碳材料,以及硅基、锡基、锑基、镁基等合金材料。虽然石墨类碳材料是目前商业化的负极材料,但是随着科技的进步,人们对锂电池续航的要求越来越高,石墨类负极材料很难满足未来市场要求,而硅基类负极材料的高比能量密度正好满足需求,是未来负极市场重要的可替代材料。
4.目前商业用的石墨负极材料已经接近理论值372mah/g,要提高比容量必须寻找新的材料。虽然硅的理论容量值有4200mah/g,远大于石墨负极,但纯硅在锂电池充放电时膨胀率达到300%,给电池带来了巨大隐患。而氧化亚硅的理论容量值接近2400mah/g,通过表面改性体积膨胀率可以降到30%以下,大大提高了锂电池的安全性。为了锂电池的安全性能,同时考虑到锂电池的续航性,很多企业采用氧化亚硅代替石墨作锂电池的负极材料。氧化亚硅一般用sio
x
表示。
5.锂电池充放电过程中氧化亚硅由于体积膨胀效应的影响,电极在充放电过程中会发生结构破坏,导致活性物质从集流体上剥落,造成负极的可逆容量降低、循环性能变差。研究者做了大量的研究和探索,发现当金属硅的粒径降低到150nm及以下时,硅的体积效应将变得很小,达到了锂电池可以耐受的范围。因此,通过控制氧化亚硅粉体的粒径为纳米级如150nm及以下时,从而降低负极充放电过程的体积膨胀,可以很好地提高锂电池的安全性能。
6.目前生产氧化亚硅主要的方法有化学气相沉积法,简称cvd法,发生的化学反应如si+sio2
→
sio
x
,该方法通过在真空密闭容器内高温加热,一般温度1300-1700℃,发生化学反应,使生成的氧化硅粉体沉积,然后收集。该方法由于须等反应完成且粉体完全沉积后才能收集,无法做到连续化生产,产能低。且收集的氧化亚硅粉体由于沉积时聚集在一起,取出来的成品存在大量的连体和枝状结构,粉体的粒度分布很宽,大颗粒多,形状各异。即使对以上现有技术制备出的氧化亚硅再进行球磨处理,仍然不能满足质量要求,因为工业生产普遍采用的球磨机无法做到平均粒径为纳米级,一般只能在微米级,最多为亚微米级,无法达到150nm及以下的粒径,若采用高能球磨机球磨,在一定程度上可达到纳米级粒径,但
生产成本太高。
技术实现要素:7.本发明要解决的技术问题是,提供生产效率高且制备出的氧化亚硅粉体粒径分布合理、不需球磨、粉体球形度高、分散性好的一种纳米氧化亚硅粉体的制备方法。
8.本发明的技术解决方案是,提供一种纳米氧化亚硅粉体的制备方法,包括以下步骤,
9.硅粉的进料、二氧化硅粉的喷入、工质气体的进入及纳米氧化亚硅粉体的制备在封闭腔室内连续进行:
10.从上部的圆筒形的蒸发腔室的圆形顶板中心的垂直且连通工质气体循环系统和硅粉加料装置的硅粉进料管进料,圆形顶板上的多支与水电气连通的等离子枪产生的交叉的等离子弧矩将硅粉进料管出口处的硅粉在蒸发腔室内蒸发得到硅蒸气;
11.蒸发腔室下部的多根从外上向内下倾斜且连通工质气体循环系统的第一工质气体进气管中的工质气体将硅蒸气送至中部的反应腔室;
12.内径大于蒸发腔室内径的圆筒形的反应腔室的上部的多根从外下向内上倾斜且连通工质气体循环系统和二氧化硅加料装置的二氧化硅粉喷入管将二氧化硅粉喷至向下运行的硅蒸气上;
13.反应腔室的中部的多根水平向的第二工质气体进气管的工质气体呈切线角度进入反应腔室,并带动粉体在反应腔室内旋转,反应腔室下部的多根从外上向内下倾斜且连通工质气体循环系统的第三工质气体进气管中的工质气体进入反应腔室,二氧化硅粉和硅蒸气在反应腔室内发生氧化还原反应,生成了氧化亚硅蒸气,下行过程碰到冷却工质气体,瞬间完成液固转变过程,变成球形纳米固态粉末;
14.球形纳米固态粉末继续下行,在内径大于反应腔室内径的中空圆形的纳米氧化亚硅粉体生成腔室中进一步生成纳米氧化亚硅粉体;
15.纳米氧化亚硅粉体经连接管进入收集器中,并间歇收集纳米氧化亚硅粉体成品。
16.采用以上步骤后,本发明一种纳米氧化亚硅粉体的制备方法具有以下优点:
17.由于本发明硅粉的进料、二氧化硅粉的喷入、工质气体的进入及纳米氧化亚硅粉体的制备在封闭腔室内连续进行,一旦开机后,能保证连续化生产,并且收集器间歇收集纳米氧化亚硅粉体成品时仍不影响设备的连续化生产,其生产效率高,产能高即产量高。本发明的蒸发腔室、反应腔室和纳米氧化亚硅粉体生成腔室从上至下的排布结构简单、紧凑,顶部多支等离子枪与硅粉进料管交叉合理布局,将硅粉瞬间蒸发成硅蒸气,外上向内下倾斜的多根第一工质气体进气管的工质气体将硅蒸气快速送入反应腔室,外下向内上倾斜的多根二氧化硅粉喷入管将二氧化硅粉喷至硅蒸气,反应腔室的中部的多根水平向的第二工质气体进气管的工质气体呈切线角度进入反应腔室,并带动粉体在反应腔室内旋转,增加了硅蒸气与二氧化硅的接触面,两者的反应更充分彻底。二氧化硅粉和硅蒸气在反应腔室内发生氧化还原反应,生成了氧化亚硅蒸气,下行过程碰到冷却工质气体,瞬间完成液固转变过程,变成球形纳米固态粉末,球形纳米固态粉末继续下行,在内径大于反应腔室内径的中空圆形的纳米氧化亚硅粉体生成腔室中进一步生成纳米氧化亚硅粉体。整个反应生成过程中,粉体间没有相互团聚、粘连的时间和条件,纳米氧化亚硅粉体形成过程快速、分散、均
匀,纳米氧化亚硅粉体成品分散、颗粒粒径均匀,不需球磨,制备出的氧化亚硅粉体的平均粒径为20-150nm,能完全满足质量要求,并大幅度降低了生产成本,且下行过程中,生成的氧化亚硅蒸气经过冷却气体时由于表面张力而形成球形,得到球形粉末颗粒,即本发明方法制备出的氧化亚硅粉体球形度高。
18.进一步地,所述的封闭腔室即蒸发腔室、反应腔室、纳米氧化亚硅粉体生成腔室、连接管和纳米氧化亚硅粉体成品的收集器的外壳均设有供冷却剂循环的冷却剂夹层;蒸发腔室的冷却剂夹层内有保温层,保温层内有耐高温层。采用以上结构后,供冷却剂循环的冷却剂夹层如供冷却水循环的冷却水夹层,能降低封闭腔室即设备的整体温度,使设备的工作条件更好,从而保证设备始终处于良好的工作状态。保温层的设置能减少高温层内的能量损失,充分保证硅粉的蒸发效果,保温层还对蒸发腔室内的耐高温层起固连作用,使设备始终处于良好的工作状态。
19.进一步地,所述的中空圆形的纳米氧化亚硅粉体生成腔室的中空形状为:上部为连通反应腔室且上小下大的圆锥形、中部为大径圆筒形、下部为上大下小的圆锥形,中部的大径圆筒形的内径大于反应腔室的内径,中部的大径圆筒形的侧边上有连接管的纳米氧化亚硅粉体的进口。纳米氧化亚硅粉体生成腔室采用以上具体结构后,氧化还原反应生成的纳米氧化亚硅粉体从反应腔室一下进入直径大数倍的纳米氧化亚硅粉体生成腔室进一步冷却生成成品纳米氧化亚硅粉体,数倍增大的空间有效地减少了纳米氧化亚硅粉体颗粒之间的相互碰撞和团聚,使制备出的纳米氧化亚硅粉体成品分散性更好、颗粒粒径均匀性更好、球形度更高。
20.进一步地,所述的与水电气连通的等离子枪采用非转移弧的等离子枪;所述的多支指沿圆周均匀分布的2-6支;每支等离子枪的轴线的延长线与硅粉进料管的轴线的延长线的夹角为30
°
—60
°
;所述的工质气体为氩气、氢气、氮气、氨气、氦气中的一种或多种混合气体。采用以上步骤后,顶部多支等离子枪与硅粉进料管交叉布局更合理,将硅粉瞬间蒸发成硅蒸气的技术效果能得到进一步的保证。
21.进一步地,位于反应腔室内的二氧化硅粉喷入管的出口端为喇叭口,喇叭口的直径大于二氧化硅粉喷入管的管体的直径;所述的多根指沿圆周均匀分布的4-16根;每根二氧化硅粉喷入管的轴线与反应腔室内壁的夹角为15
°
—75
°
;在同一水平面上的多根二氧化硅粉喷入管的最高点与在同一水平面上的多支等离子枪的最低点的垂直距离为200—800mm;多根二氧化硅粉体喷入管的轴线延长线的交叉点与多支等离子枪的轴线延长线的交叉点在同一铅垂线上。采用以上步骤后,二氧化硅粉喷入的角度更合理,更均匀和更分散,使二氧化硅与硅的反应更充分,使纳米氧化亚硅粉体形成过程更快速、更分散、更均匀,制备出的纳米氧化亚硅粉体成品更分散、颗粒粒径更均匀。
22.进一步地,所述的第一工质气体进气管的多根指沿圆周均匀分布的3-8根;每根第一工质气体进气管的轴线与蒸发腔室内壁的夹角为15
°
—60
°
;所述的第二工质气体进气管的多根指沿圆周均匀分布的3-8根;所述的第三工质气体进气管的多根指沿圆周均匀分布的3-8根;每根第三工质气体进气管的轴线与反应腔室内壁的夹角为15
°
—60
°
。采用以上步骤后,工质气体的冷却和输送效果更好,进一步保证了反应过程和纳米氧化亚硅粉体制备过程的分散性和均匀性。
23.进一步地,每支等离子枪的进气压力为0.1-0.0.6mpa,每支等离子枪的气体流量
为1-15m3/h;多支等离子枪交叉构成的主弧炬弧长为300-800mm,弧宽为100-350mm;硅粉进料管的输送气压为0.1-0.3mpa,气体流量为1-10m3/h;二氧化硅粉体喷入管的喷气压力为0.1-0.3mpa,气体流量为在1-10m3/h;第一工质气体进气管的气体压力为0.1-0.3mpa,第一工质气体进气管的气体流量为5-30m3/h;第二工质气体进气管的气体压力为0.1-0.3mpa,第二工质气体进气管的气体流量为5-30m3/h;第三工质气体进气管的气体压力为0.1-0.3mpa,气体流量为10-80m3/h。采用以上步骤后,硅粉的蒸发效果更好,硅粉的蒸发量能得到进一步保证,工质气体的冷却和输送效果更好,且粒径分布可调控,进一步保证了反应过程和纳米氧化亚硅粉体制备过程的分散性和均匀性,以及连续化生产过程,进一步提高了生产效率,进一步保证了高产能,且进一步保证了制备出的纳米氧化亚硅粉体的分散性和均匀性。
24.进一步地,反应腔室的温度为1350-1900℃;反应腔室的压力为0.001-0.04mpa。采用以上步骤后,使二氧化硅与硅的反应更充分,使纳米氧化亚硅粉体形成过程更快速、更分散、更均匀,制备出的纳米氧化亚硅粉体成品更分散、颗粒粒径更均匀。
25.进一步地,硅粉与二氧化硅粉的比例在1:0.8-1.5之间,硅粉的进料量为0.2-5kg/h,二氧化硅粉的进料量为0.16-7.5kg/h。采用以上步骤后,实现了硅粉和二氧化硅粉进料的较高覆盖率,进一步保证了连续生产所需的足够的硅粉和二氧化硅粉,进一步保证了高的产能,且进一步保证了制备出的纳米氧化亚硅粉体的分散性和均匀性。
26.进一步地,制备出的氧化亚硅粉体的平均粒径为20-150nm,氧化亚硅粉体的形状为球形。采用以上步骤后,进一步保证了粒径分布可调控,纳米氧化亚硅粉体成品分散、颗粒粒径均匀,不需球磨,进一步满足质量要求,并进一步降低生产成本。
附图说明
27.图1是本发明方法采用的设备的外形结构示意图。
28.图2是本发明方法采用的设备的竖向剖视结构示意图。
29.图3是本发明方法中多根第二工质气体进气管中的一根向反应腔室呈切线角度进气以并带动粉体在反应腔室内旋转的示意图。
30.图中所示:1、硅粉进料管,2、等离子枪,3、第一工质气体进气管,4、二氧化硅粉喷入管,5、第三工质气体进气管,6、封闭腔室,7、连接管,8、收集阀门,9、收集器,10、硅粉进料管出口处,11、圆形顶板,12、保温层,13、蒸发腔室,14、反应腔室,15、纳米氧化亚硅粉体生成腔室,16、上小下大的圆锥形,17、大径圆筒形,18、上大下小的圆锥形,19、纳米氧化亚硅粉体的进口,20、多孔管壁,21、冷却水夹层,22、管体,23、喇叭口,24、耐高温层,25、等离子弧炬,26、第二工质气体进气管。
具体实施方式
31.下面结合附图对本发明的具体实施方式作进一步说明。在此需要声明的是,对于这些具体实施方式的说明用于帮助理解本发明,但并不构成对本发明的限定。此外,下面所描述的本发明的各个具体实施方式中所涉及的技术特征只要彼此之间未构成冲突就可以相互组合。
32.如图1、图2所示。
33.本发明一种纳米氧化亚硅粉体的制备方法,包括以下步骤,
34.硅粉的进料、二氧化硅粉的喷入、工质气体的进入及纳米氧化亚硅粉体的制备在封闭腔室6内连续进行:
35.从上部的圆筒形的蒸发腔室13的圆形顶板11中心的垂直且连通工质气体循环系统(图中未示出,以下亦同)和硅粉加料装置如加料桶或称加料罐、加料管等(图中未示出,以下亦同)的硅粉进料管1进料,圆形顶板11上的多支与水电气连通的等离子枪2产生的交叉的等离子弧炬25将硅粉进料管出口处10的硅粉在蒸发腔室13内蒸发得到硅蒸气。
36.蒸发腔室13下部的多根从外上向内下倾斜且连通工质气体循环系统的第一工质气体进气管3中的工质气体将硅蒸气送至中部的反应腔室14。
37.内径大于蒸发腔室13内径的圆筒形的反应腔室14的上部的多根从外下向内上倾斜且连通工质气体循环系统和二氧化硅加料装置如加料桶或称加料罐、加料管等(图中未示出,以下亦同)的二氧化硅粉喷入管4将二氧化硅粉喷至向下运行的硅蒸气上。
38.反应腔室14的中部的多根水平向的第二工质气体进气管26的工质气体呈切线角度进入反应腔室14,并带动粉体在反应腔室14内旋转,反应腔室14下部的多根从外上向内下倾斜且连通工质气体循环系统的第三工质气体进气管5中的工质气体进入反应腔室14,二氧化硅粉和硅蒸气在反应腔室14内发生氧化还原反应,生成了氧化亚硅蒸气,下行过程碰到冷却工质气体,瞬间完成液固转变过程,变成球形纳米固态粉末;
39.球形纳米固态粉末继续下行,在内径大于反应腔室内径的中空圆形的纳米氧化亚硅粉体生成腔室中进一步生成纳米氧化亚硅粉体。
40.纳米氧化亚硅粉体经连接管7进入收集器9中,并间歇收集纳米氧化亚硅粉体成品。
41.所述的封闭腔室6即蒸发腔室13、反应腔室14、纳米氧化亚硅粉体生成腔室15、连接管7和纳米氧化亚硅粉体成品的收集器9的外壳均设有供冷却剂循环的冷却剂夹层,如供冷却水循环的冷却水夹层21。换句话说,所述的封闭腔室6指蒸发腔室13、反应腔室14、纳米氧化亚硅粉体生成腔室15、连接管7和纳米氧化亚硅粉体成品的收集器9,所述的封闭腔室6的外壳设有供冷却剂循环的冷却剂夹层,如供冷却水循环的冷却水夹层21,蒸发腔室13、反应腔室14、纳米氧化亚硅粉体生成腔室15、连接管7和收纳米氧化亚硅粉体成品的集器9的冷却水夹层21相互之间连通。当然,冷却水夹层21各自独立即各自独立进出水也是可以的,但优选相互之间连通。蒸发腔室13的冷却剂夹层如冷却水夹层21内有保温层12,保温层12内有耐高温层24。保温层12的保温材料如采用石墨碳毡构成的保温层。耐高温层24如采用耐高温材料如石墨构成的耐高温层。其具体连接结构可为,石墨碳毡卷在石墨管上构成石墨碳毡筒,可在石墨碳毡筒外用碳纤维绳将石墨碳毡筒捆绑,再将直径大于冷却水夹层21构成的管壁直径并包有石墨管的石墨碳毡筒过盈配合或称扎紧在冷却水夹层21构成的管壁内,使保温层12和耐高温层24和冷却水夹层21构成的管壁相互之间牢固固定。
42.所述的中空圆形的纳米氧化亚硅粉体生成腔室15的中空形状优选为:上部为连通反应腔室14且上小下大的圆锥形16、中部为大径圆筒形17、下部为上大下小的圆锥形18,中部的大径圆筒形17的内径大于反应腔室14的内径,如大2-3倍,中部的大径圆筒形17的侧边上有连接管7的纳米氧化亚硅粉体的进口19。
43.所述的与水电气连通的等离子枪2采用非转移弧的等离子枪。所述的多支可为沿
圆周均匀分布的2-6支。每支等离子枪2的轴线的延长线与硅粉进料管1的轴线的延长线的夹角为30
°
—60
°
。所述的工质气体为氩气、氢气、氮气、氨气、氦气中的一种或多种混合气体,如氮气,又如氮气与氩气的混合气体,再如氩气与氢气两者的混合气体,或如氩气、氮气和氢气三者的混合气体。
44.位于反应腔室14内的二氧化硅粉喷入管4的出口端为喇叭口23,喇叭口23的直径大于二氧化硅粉喷入管4的管体22的直径。所述的多根可为沿圆周均匀分布的4-16根。每根二氧化硅粉喷入管4的轴线与反应腔室14内壁的夹角为15
°
—75
°
。每根二氧化硅粉喷入管4的直径可为8-30mm。在同一水平面上的多根二氧化硅粉喷入管4的最高点与在同一水平面上的多支等离子枪2的最低点的垂直距离为200—800mm。多根二氧化硅粉体喷入管4的轴线延长线的交叉点与多支等离子枪2的轴线延长线的交叉点在同一铅垂线上。二氧化硅粉喷入管4也可称二氧化硅喷料管。
45.所述的第一工质气体进气管3的多根指沿圆周均匀分布的3-8根,优选6根;每根第一工质气体进气管3的轴线与蒸发腔室内壁的夹角为15
°
—60
°
。所述的第二工质气体进气管26的多根指沿圆周均匀分布的3-8根,优选6根。所述的第三工质气体进气管5的多根指沿圆周均匀分布的3-8根,优选6根;每根第三工质气体进气管的轴线与反应腔室内壁的夹角为15
°
—60
°
。
46.每支等离子枪2的进气压力为0.1-0.6mpa,每支等离子枪2的气体流量为1-15m3/h;多支等离子枪交叉构成的主弧炬弧长为300-800mm,弧宽为100-350mm;硅粉进料管1的输送气压为0.1-0.3mpa,气体流量为1-10m3/h;二氧化硅粉体喷入管4的喷气压力为0.1-0.3mpa,气体流量为在1-10m3/h;第一工质气体进气管3的气体压力为0.1-0.3mpa,第一工质气体进气管3的气体流量为5-30m3/h;第二工质气体进气管26的气体压力为0.1-0.3mpa,第二工质气体进气管26的气体流量为5-30m3/h;第三工质气体进气管5的气体压力为0.1-0.3mpa,第三工质气体进气管5的气体流量为10-80m3/h。
47.反应腔室的温度为1350-1900℃;反应腔室的压力为0.001-0.04mpa。不难理解,温度可经安装在设备上温度表或温度传感器显示或控制,压力可经安装在设备上压力表或压力传感器显示或控制。
48.硅粉与二氧化硅粉的比例在1:0.8-1.5之间,硅粉的进料量为0.2-5kg/h,二氧化硅粉的进料量为0.16-7.5kg/h。
49.制备出的氧化亚硅粉体的平均粒径为20-150nm,氧化亚硅粉体的形状为球形。
50.不难理解,本发明方法所采用的设备还包括现有技术的设备,如与封闭腔室6连通的引风机,吹落收集器9内的氧化亚硅粉体以收集氧化亚硅粉体用的反吹装置,控制引风机频率的变频器,控制柜和引弧箱等(以上现有技术的设备图中均未示出,以下亦同)。
51.下面结合具体制备步骤对本发明一种纳米氧化亚硅粉体的制备方法再做较详细的展开说明。
52.本技术一种纳米氧化亚硅粉体的制备方法,采用以下具体步骤:
53.s1、将购买的硅粉原料和二氧化硅粉原料预球磨,使粉体的尺寸平均粒径控制在d50:1-15μm,然后100-150℃烘干,密封干燥储藏备用。硅粉和二氧化硅粉也可以直接从市场上购买同规格的产品。也就是说,预球磨步骤不属必备步骤,能直接购买符合要求的硅粉和二氧化硅粉,就直接应用于本发明制备过程。在本发明中,硅粉的尺寸要求仅是为了实现
最佳的生产效果,在其它实施例中,使用上述尺寸之外的硅粉也同样能够实现本技术的技术方案,但在通常情况下,优选使用上述粒径的亚微米粒径的硅粉和二氧化硅粉。当然,若是硅粉和二氧化硅的粒径在纳米级,也同样适用。
54.s2、设备安装调试好后,先进行气密性检测,采取充氮气高压检测和抽真空低压检测密封性:高压1.2mpa、30分钟内气体压力不变;低压0.05mpa、30分钟内气体压力不变。如果有漏气现象需要排查解决,只有确认整个封闭系统不漏气才能开机生产。
55.所述蒸发腔室13及上部腔体的内径可为140-800mm,高度可为200-800mm,蒸发腔室13的内径优选200mm,高度优选500mm。
56.等离子枪2优选为非转移弧的等离子枪,为2-6支,优选4支。单支等离子枪2的等离子弧炬25的弧长200-700mm,弧宽50-30mm。单支等离子枪2的输入电流为60-500a,电压为100-400v。4支等离子枪2沿圆周均匀分布于蒸发腔室13的圆形顶板11上,4支等离子枪2聚集成一个主弧炬,主弧炬弧长为300-800mm,弧宽为100-350mm,主弧炬的中心温度为10000-20000℃。优选的,主弧炬弧长800mm,弧宽150mm,主弧炬中心温度为20000℃。
57.等离子体枪2使用的工作气体为氩气、氢气、氮气、氨气、氦气中的一种或多种混合气体。优选的,等离子枪的工作气体为氩气、氢气混合气体,氢气体积比例占25%,每支等离子枪2的进气量可为1-15m3/h,优选为5m3/h。进气压力可0.1-0.6mpa,优选为0.15mpa。
58.所述第一工质气体进气管3的轴线与蒸发腔室13内壁成30-60
°
夹角,第一工质气体进气管3的轴线与蒸发腔室13内壁优选为60
°
夹角;孔径4-25mm,优选10mm。可连接冷却氩气,气流量控制在20-30m3/h。第二工质气体进气管26的孔径10-40mm,优选25mm。在本发明的其它实施例中,冷却气体还可为氮气、氩气或其它不活泼性气体等。所述第三工质气体进气管5的有关参数也与第一工质气体进气管3的以上参数相同,在此不赘述。
59.所述的反应腔室14的内径可为140-800mm,高度可为200-800mm,所述的反应腔室14的内径优选200mm,高度优选800mm。
60.所述的二氧化硅喷入管4的轴线与反应腔室14内壁的夹角可为15-75
°
,优选60
°
。二氧化硅喷料管的内径可为8-30mm,优选为15mm,且出口成喇叭形状。在同一水平面上的多根二氧化硅粉喷入管4的最高点与在同一水平面上的多支等离子枪2的最低点的垂直距离为200—800mm,优选为500mm。多根二氧化硅粉体喷入管4的轴线延长线的交叉点与多支等离子枪2的轴线延长线的交叉点在同一铅垂线上。
61.所述的纳米氧化亚硅粉体生成腔室15顶部与反应腔室14的接口的内径与反应腔室14一致,可为140-800mm,优选为200mm,中部大径圆筒形17的内径可为800-1500mm,优选为800mm,纳米氧化亚硅粉体生成腔室15高度为600-1000mm,优选800mm。连接管7的内径优选为径200mm。收集器9可安装有现有技术的反吹装置,反吹装置与引风机连接,引风机的功率可25-45kw。
62.s3、将硅粉如纯硅粉原料装入位于硅粉进料管1顶部的硅粉加料桶或称硅粉加料罐中,将二氧化硅粉装入二氧化硅粉加料桶或称二氧化硅粉加料罐中,加料方式可优先采用现有技术的气体脉冲式。
63.s4、打开冷却水系统的进出水阀门,向冷却水夹层21内通入冷却水,水压可控制在0.4-0.8mpa,冷却水流量可控制在1.0-5.0m3/h范围,进水温可为10-25℃。
64.s5、开启工质气体循环系统的气瓶、气泵和阀门,各路气体压力通过调压阀调节。
等离子枪2的进气压力控制在0.1-0.6mpa,每支等离子枪2的气体流量控制在1-15m3/h。硅粉加料管1的输送气压控制在0.1-0.3mpa,气体流量控制在1-10m3/h。二氧化硅喷入管4的气压控制在0.1-0.3mpa,气体流量控制在1-10m3/h。第一工质气体进气管3的气体压力为0.1-0.3mpa,第一工质气体进气管3的气体流量为5-30m3/h。第二工质气体进气管26的气体压力为0.1-0.3mpa,第二工质气体进气管26的气体流量为5-30m3/h。第三工质气体进气管5的气体压力为0.1-0.3mpa,气体流量为10-80m3/h。
65.s6、打开控制柜的电源,开启引弧箱,观察等离子弧炬25的火焰外形,通过调节单种气体的进气流量或混合气体的比例和进气流量,调节等离子弧炬25的长度,控制主弧炬弧长300-800mm,弧宽100-350mm,功率发生器的电流为100-500a,电压为50-400v。
66.s7、待电流电压稳定后开始加料。首先开启硅粉进料管1前的阀门,加入硅粉,接着开启二氧化硅粉喷入管4前的阀门,加或称喷入入二氧化硅粉,加入硅粉即si与二氧化硅粉即sio2的比例为1:0.8-1.5,硅粉的进料量为0.2-5kg/h,二氧化硅粉的进料量为0.16-7.5kg/h。
67.粉体制备过程中,反应腔室的温度控制在1350-1900℃,优选为1400℃;反应腔室的压力控制在0.001-0.04mpa,优选为0.003mpa。
68.s8、随着生产的持续运行,制备出的氧化亚硅粉体即sio
x
粉体越来越多,可在连续生产5-6小时后每隔一个小时开启一次反吹装置和收集阀门8,将吸附在收集器9中多孔管壁20上的粉体吹落下来,经收集阀门8收集。
69.制备出成品纳米氧化亚硅每小时可为0.5-5kg,粉体的平均粒径为20-150nm。制备的纳米氧化亚硅粉体为球形状。制备出成品纳米氧化亚硅粉体的氮含量《5%,碳含量《5%,符合质量要求。
70.不难理解,以上的
“°”
可用“度”表示。以上压力可采用压力表或压力传感器控制。以上进气量可采用流量表或流量传感器控制。以上所述的向下运行与下行意思相同。控制柜中有控制整个设备的主控制器如cpu或cpu或plc或mcu,主控制器与各种传感器等电连接。
71.以上所述的与水电气系统连通的等离子枪2为现有技术,如可采用本技术人申请号为202110556623.7、发明名称为纳米金属包覆粉末的制备方法的在先申请中的等离子枪,即与水电气系统连通的第一等离子枪或第二等离子枪的结构,也即非转移弧的与水电气系统连通的等离子枪。
72.与水电气系统连通的等离子枪2有多种叫法,有的称等离子枪及其对应的供水供电供气设备,有的称等离子雾化喷枪系统,有的称等离子弧发生装置,有的称等离子体电极,有的用等离子体焰矩和雾化喷嘴来代替总的名称,有的称为非转移弧或转移弧,也有的称为非转移弧系统或转移弧系统。等离子弧炬25也有多种叫法,有的称等离子射流,有的称等离子弧,有的称等离子电弧,有的称等离子体弧,有的称等离子电弧射流。
73.以上所述仅为本发明的优选实施方式,并不用于限制本发明,对于本领域的技术人员来说,本发明可以有各种更改和变化。凡在本发明精神和原则之内,所作的任何修改、等同替换、改进等,均应包含在本发明的保护范围之内。