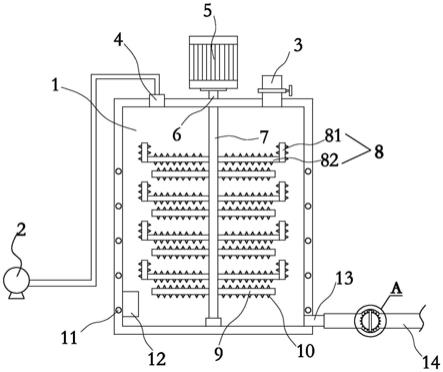
1.本发明涉及陶瓷基板技术领域,尤其涉及一种996氧化铝陶瓷基板的制备方法。
背景技术:2.随着电子行业封装技术的不断发展,逐步朝集成度高、功能齐备、性能优异和可靠性强的方向研发进步。基板材料在电子封装工艺过程中主要起绝缘、散热、保护和承载芯片与金属电子线路等作用。相较于其他电子基板材料,氧化铝陶瓷材料具有硬度高、耐化学腐蚀性好、抗弯强度大、膨胀系数匹配性好等特点,同时原料丰富,价格较低,已成为应用量最大、应用领域最广的陶瓷基板材料。其应用领域主要有电子陶瓷元件、片式电阻、陶瓷覆铜板、led散热片、聚焦电位器、臭氧发生器及传感器绝缘衬板等电子和微电子产品。
3.在实际应用时,陶瓷中氧化铝含量高于75%的均被称作氧化铝陶瓷。氧化铝陶瓷通常根据氧化铝的含量进行分类,比如含量为75%、90%、95%、99%左右的氧化铝陶瓷分别称为75瓷、90瓷、95瓷和99瓷。99瓷具有机械性能良好,介电常数低,介电损耗小,电学性能稳定等优点,因此常应用高科技领域以及工作环境苛刻的军事领域。但现有技术生产出的99瓷产品质量稳定性差,生产时的烧结成瓷温度过高,严重阻碍了其进一步发展。
4.2021年1月5号公布的发明专利cn112174648a公开了一种高纯氧化铝陶瓷基板的制备方法,包括:s1、将重量份数为99-99.5份的高纯氧化铝粉、0.5-1份的烧结助剂放入球磨机,以水为溶剂,加水溶性分散剂,研磨混合得料浆;s2、料浆真空除泡后装入料浆桶,加催化剂和引发剂,搅拌均匀,接气源,开启气源对料浆施加压力控制料浆通过连通管自模具底部注浆口注入模具,使料浆在模具内自下而上流动至注满模具,固化脱模得坯体;s3、烘干坯体后软化,切坯片,干燥;s4、烧结坯片,抚平得基板。该发明所述的基板烧结温度低、烧结范围宽、烧结收缩性可控。利用气源对料浆施加压力,使料浆由模具底部自下而上注入模具,避免了料浆中比重高的物料沉积到模具底部引起坯体密度差大、成型缺陷大的问题。
5.本发明针对氧化铝陶瓷的配方和工艺进行了优化,将氧化铝的含量增加至99.6%,在提升氧化铝陶瓷电学性能和机械性能的同时,降低生产成本。
技术实现要素:6.因此,针对以上内容,本发明提供一种996氧化铝陶瓷基板的制备方法,解决现有技术生产出的99瓷产品质量稳定性差,烧结成瓷温度过高的问题。
7.为达到上述目的,本发明是通过以下技术方案实现的:
8.一种996氧化铝陶瓷基板的制备方法,包括以下步骤:
9.(1)烧结助剂的制备:将硝酸铜、丙三醇钛、四乙氧基硅烷、丙烯酸、聚氮丙啶交联剂、三聚磷酸钠、乙醇按比例加入装有水的反应器内,在60~70℃下搅拌30~60min,然后加入自由基引发剂,搅拌反应至形成凝胶,室温下静置20~30h,然后进行脱水干燥,研磨得到粉末,然后将粉末放入煅烧炉内进行煅烧,得到cuo-tio
2-sio2三元烧结助剂;
10.(2)浆料的制备:将氧化铝粉末、烧结助剂按照质量比99.6:0.4加入球磨机中,同
时加入溶剂、分散剂、粘合剂、脱泡剂加入球磨机中球磨15~20h,然后送入脱泡装置内进行脱泡处理,得到流动性良好且稳定的浆料;
11.所述脱泡装置包括脱泡罐和真空泵,所述脱泡罐的顶部两侧分别设有进料口和抽气口,所述抽气口通过真空管与真空泵相连通,所述脱泡罐的顶部安装有驱动电机,所述驱动电机输出端固定连接有转轴,所述转轴的底端贯穿脱泡罐的顶部并与搅拌轴的顶端相铰接,所述搅拌轴通过轴承与脱泡罐底部内壁固定连接,所述搅拌轴固定连接有若干个第一搅拌单元和第二搅拌单元,所述第一搅拌单元和第二搅拌单元沿搅拌轴长度方向交替设置,所述第一搅拌单元由3~6个搅拌杆组成,所述第二搅拌单元由2~4个搅拌叶片组成,所述搅拌杆和搅拌叶片外壁固定连接有破泡刺,所述搅拌杆包括纵向搅拌杆和横向搅拌杆,所述纵向搅拌杆和横向搅拌杆固定连接,所述脱泡罐的侧壁底部设有出料口,所述出料口连接有出料管;
12.(3)流延成型、冲压:浆料经过流延机、冲片机处理后,得到所需形状及尺寸的生坯片;
13.(4)排胶:将生坯片放入排胶炉中进行排胶;
14.(5)烧结:将排胶后的生坯片置于烧结炉中,以1.5~2.5℃/min的速率升温至1500℃,保温10~20min后降温至1450℃,保温12~20h,冷却后取出即得996氧化铝陶瓷基板。
15.进一步的改进是:步骤(1)中水的质量按100%计,各原料组分的添加量为:硝酸铜7~9%、丙三醇钛16~20%、四乙氧基硅烷36~42%、丙烯酸8~12%、聚氮丙啶交联剂1~3%、三聚磷酸钠0.2~0.4%、乙醇8~15%、自由基引发剂0.4~0.8%。
16.进一步的改进是:所述自由基引发剂为过硫酸盐类引发剂。
17.进一步的改进是:步骤(1)中煅烧温度为620~660℃。
18.进一步的改进是:所述氧化铝粉末由平均粒径为3~5μm的α相氧化铝和平均粒径为50nm的α相氧化铝按质量比20:80~40:60混合而成。
19.进一步的改进是:所述分散剂由聚乙烯亚胺和烷基苯磺酸钠按质量比1:1~4:1复配而成。
20.进一步的改进是:所述出料管之间设有脱泡部,所述脱泡部包括球形壳体和设置在球形壳体内的转动杆,所述转动杆竖直方向设置,所述转动杆外壁套接有脱泡球,所述脱泡球上设有破泡刺,当转动杆在驱动装置作用下转动时,带动脱泡球进行旋转,消除浆料中残留的气泡。
21.进一步的改进是:所述脱泡罐的侧壁上安装有加热管,所述加热管环绕在脱泡罐上,所述脱泡罐内壁上设有温度传感器。
22.进一步的改进是:以氧化铝粉末质量100%计,所述溶剂、分散剂、粘合剂、脱泡剂的添加量依次为180~220%、3.5~5.5%、10~15%、0.9~1.6%。
23.进一步的改进是:步骤(4)排胶的具体工艺参数为:在氮气气氛下进行第一次排胶,以1~2℃/min升温速率升温至500~580℃,保温30~50min,然后在空气气氛下进行第二次排胶,以2~4℃/min升温速率升温至210~240℃,保温100~150min。
24.通过采用前述技术方案,本发明的有益效果是:
25.氧化铜在烧结过程中形成液相,促进氧化铝陶瓷致密化;二氧化钛与氧化铝形成al2ti7o
15
相,同时形成大量的正离子空位,进而促进晶粒生长和氧化铝陶瓷致密化进程;二
氧化硅在烧结过程既能生成玻璃相,又能够与氧化铝形成低温共熔体,起到促进烧结的作用。将氧化铜、二氧化钛、二氧化硅进行复配,形成三元烧结助剂体系,能够更好地促进烧结,降低烧结温度,同时还能改善氧化铝陶瓷的综合性能。现有的多元烧结助剂是将各种烧结助剂放入球磨罐中进行球磨,再经过研磨、过筛后制得的,理论上在烧结过程能够形成足够多的液相,使氧化铝颗粒之间产生润滑作用,有助于颗粒迁移和重排,使坯体内的组织更加均匀;同时液相也能填充到氧化铝颗粒之间的间隙内,消除气孔,从而提高坯体的致密度。本技术人发现传统方法制得的多元烧结助剂各组分分散不均匀,易发生团聚,在高温下形成的液相较少,难以对颗粒起到润滑作用,也难以填充到颗粒间的孔隙中,使气孔难以消除而残留下来,最终影响氧化铝陶瓷的致密度。本技术人采用新的制备方法得到的cuo-tio
2-sio2三元烧结助剂分散均匀,改善了粉体之间的聚集、团聚,具体原理是:首先,丙烯酸进行自由基聚合反应形成聚合物,再与聚氮丙啶交联剂发生交联反应,形成三维网状骨架结构,该结构能够产生空间阻隔屏蔽作用,有效地抑制团聚现象的发生,提高分散性。其次,三聚磷酸钠在水中电离出大量的离子基团,吸附在凝胶颗粒表面,使颗粒表面的电荷量增加,利用同性相斥原理,增加颗粒间的距离;另外三聚磷酸钠还能在颗粒表面形成分子链,起到空间位阻作用,从而进一步防止产生团聚。最后,经过煅烧除去凝胶中的有机物,得到cuo-tio
2-sio2三元烧结助剂。在烧结过程中产生较多的液相,使生产出的氧化铝陶瓷的致密度和力学性能均高于添加传统工艺的三元烧结助剂后制备得到的氧化铝陶瓷。
26.高纯的氧化铝陶瓷的烧结温度通常高于1700℃,添加烧结助剂能够降低降低烧结温度,目前国内常使用mgo-sio
2-al2o3和cao-mgo-sio
2-al2o3烧结助剂体系,制备的氧化铝陶瓷具有良好的机械性能和电学性能,但烧结温度仍高于1580℃,生产成本高。对此,本技术人从以下几个方面改进:第一方面,通过新的制备工艺,生产的cuo-tio
2-sio2三元烧结助剂能够更好地促进烧结,降低烧结温度。第二方面,将微米级和纳米级的氧化铝颗粒进行复配,纳米氧化铝颗粒的表面活性高,显著降低烧结温度;同时纳米级颗粒也能填充到微米级颗粒的缝隙内,紧密堆积,得到致密度高的氧化铝厂陶瓷制品。纳米氧化铝颗粒之间易产生团聚现象,使烧结后的陶瓷晶粒不均匀,影响产品的综合性能。本技术利用聚乙烯亚胺和烷基苯磺酸钠复配体系,有效吸附在纳米氧化铝颗粒的表面,减少团聚大分子的形成。第三方面,不同于现有工艺直接将升温至最高温度,并在该温度下长时间保温烧结,本技术采用分段烧结方式,首先升温至1500℃,使生坯达到一定致密化,再将温度降至1450℃,通过低温晶界扩散使坯体完成接近完全致密化,避免了能源的大量浪费,降低了成本。同时晶界迁移受到抑制,抑制了坯体晶粒长大,从而提高了氧化铝陶瓷的力学性能。
27.现有的脱泡装置结构设计不合理,脱泡效率不佳,难以完全消除浆料中的起泡,影响后续工序的顺序进行,导致生产出的氧化铝陶瓷基板存在缺陷。本技术采用改性的脱泡装置,通过真空泵、驱动电机、第一搅拌单元、第二搅拌单元和破泡刺的相互配合,达到了良好的脱泡效果。搅拌叶片又分为纵向搅拌杆和横向搅拌杆,该设置提高了搅拌覆盖范围,避免出现死角,充分脱除浆料内的气泡。通过加热管对脱泡罐内的浆料进行适当加热,增加浆料的流动速度,使气泡更快地从浆料中逸出,提高脱泡效率。脱泡部的设置,能够进一步保证脱泡效果,若浆料中残留未完全消除的气泡,脱泡球上的破泡刺与浆料接触过程中刺破残留气泡,保证后续加工过程的顺利进行。
附图说明
28.图1是本发明实施例中脱泡装置的结构示意图;
29.图2是图1中a处放大示意图。
具体实施方式
30.以下将结合具体实施例来详细说明本发明的实施方式,借此对本发明如何应用技术手段来解决技术问题,并达成技术效果的实现过程能充分理解并据以实施。
31.若未特别指明,实施例中所采用的技术手段为本领域技术人员所熟知的常规手段,所采用的试剂和产品也均为可商业获得的。所用试剂的来源、商品名以及有必要列出其组成成分者,均在首次出现时标明。
32.实施例1
33.一种996氧化铝陶瓷基板的制备方法,包括以下步骤:
34.(1)烧结助剂的制备:将硝酸铜、丙三醇钛、四乙氧基硅烷、丙烯酸、聚氮丙啶交联剂、三聚磷酸钠、乙醇按比例加入装有水的反应器内,在60℃下搅拌30min,然后加入过硫酸铵,搅拌反应至形成凝胶,室温下静置20h,然后进行脱水干燥,研磨得到粉末,然后将粉末放入煅烧炉内进行煅烧,煅烧温度为620℃,得到cuo-tio
2-sio2三元烧结助剂;
35.按水的质量100%计,各原料组分的添加量为:硝酸铜7%、丙三醇钛16%、四乙氧基硅烷36%、丙烯酸8%、聚氮丙啶交联剂1%、三聚磷酸钠0.2%、乙醇8%、过硫酸铵0.4%;
36.(2)浆料的制备:将氧化铝粉末、烧结助剂按照质量比99.6:0.4加入球磨机中,同时加入异丙醇、分散剂、粘合剂、脱泡剂加入球磨机中球磨15h,然后送入脱泡装置内进行脱泡处理,得到流动性良好且稳定的浆料;
37.所述氧化铝粉末由平均粒径为3~5μm的α相氧化铝(淄博宏豪晶体材料有限公司生产)和平均粒径为50nm的α相氧化铝(杭州柘铭新材料有限公司生产,型号为zm-al50)按质量比20:80混合而成,所述分散剂由聚乙烯亚胺和烷基苯磺酸钠按质量比1:1复配而成,所述粘合剂为聚乙烯醇缩丁醛,以氧化铝粉末质量100%计,所述异丙醇、分散剂、粘合剂、脱泡剂的添加量依次为180%、3.5%、10%、0.9%;
38.参考图1及图2,所述脱泡装置包括脱泡罐1和真空泵2,所述脱泡罐的顶部两侧分别设有进料口3和抽气口4,所述抽气口4通过真空管与真空泵2相连通,所述脱泡罐1的顶部安装有驱动电机5,所述驱动电机5输出端通过联轴器固定连接有转轴6,所述转轴6的底端贯穿脱泡罐1的顶部并与搅拌轴7的顶端相铰接,所述搅拌轴7通过轴承与脱泡罐1底部内壁固定连接,所述搅拌轴7固定连接有若干个第一搅拌单元和第二搅拌单元,所述第一搅拌单元和第二搅拌单元沿搅拌轴7长度方向交替设置,所述第一搅拌单元由5个等间隔分布的搅拌杆8组成,所述第二搅拌单元由3个等间隔分布的搅拌叶片9组成,所述搅拌杆8和搅拌叶片9外壁固定连接有破泡刺10,所述搅拌杆8包括纵向搅拌杆81和横向搅拌杆82,所述纵向搅拌杆91和横向搅拌杆92固定连接,所述脱泡罐1的侧壁上安装有加热管11,所述加热管11环绕在脱泡罐1上,所述脱泡罐1内壁上设有探测浆料实时温度的温度传感器12,所述脱泡罐1的侧壁底部设有出料口13,所述出料口13连接有出料管14,所述出料管14之间设有脱泡部,所述脱泡部包括球形壳体15和设置在球形壳体内的转动杆16,所述转动杆竖直方向设置,所述转动杆16外壁套接有脱泡球17,所述脱泡球17上设有破泡刺;
39.工作时,通过进料口将浆料导入脱泡罐内,然后将脱泡罐闭合密封,开启驱动电机,转轴开始转动,带动搅拌轴转动,与搅拌轴相连接的第一搅拌单元和第二搅拌单元对浆料进行搅拌,同时开启真空泵,抽除脱泡罐内的气体,使真空罐内形成负压,搅拌后浆料气泡在负压作用下不断逸出。加热管和温度传感器相互配合,使浆料处于合适的温度,气泡更易从浆料中逸出。当浆料从出料口流出时,转动杆在驱动装置作用下转动时,带动脱泡球进行旋转,消除浆料中残留的气泡;
40.(3)流延成型、冲压:浆料经过流延机、冲片机处理后,得到所需形状及尺寸的生坯片;
41.(4)排胶:将生坯片放入排胶炉中进行排胶,具体工艺参数为:在氮气气氛下进行第一次排胶,以1℃/min升温速率升温至500℃,保温50min,然后在空气气氛下进行第二次排胶,以2℃/min升温速率升温至210℃,保温150min;
42.(5)烧结:将排胶后的生坯片置于烧结炉中,以1.5℃/min的速率升温至1500℃,保温10min后降温至1450℃,保温12h,冷却后取出即得996氧化铝陶瓷基板。
43.对本实施例制备的氧化铝陶瓷基板进行检测,性能为:相对密度98.0%,体积密度3.90g/cm3,抗弯强度为485mpa。
44.实施例2
45.一种996氧化铝陶瓷基板的制备方法,包括以下步骤:
46.(1)烧结助剂的制备:将硝酸铜、丙三醇钛、四乙氧基硅烷、丙烯酸、聚氮丙啶交联剂、三聚磷酸钠、乙醇按比例加入装有水的反应器内,在65℃下搅拌45min,然后加入过硫酸钾,搅拌反应至形成凝胶,室温下静置25h,然后进行脱水干燥,研磨得到粉末,然后将粉末放入煅烧炉内进行煅烧,煅烧温度为640℃,得到cuo-tio
2-sio2三元烧结助剂;
47.按水的质量100%计,各原料组分的添加量为:硝酸铜8%、丙三醇钛18%、四乙氧基硅烷40%、丙烯酸10%、聚氮丙啶交联剂2%、三聚磷酸钠0.3%、乙醇12%、过硫酸钾0.6%;
48.(2)浆料的制备:将氧化铝粉末、烧结助剂按照质量比99.6:0.4加入球磨机中,同时加入异丙醇、分散剂、粘合剂、脱泡剂加入球磨机中球磨18h,然后送入脱泡装置内进行脱泡处理,得到流动性良好且稳定的浆料;
49.所述氧化铝粉末由平均粒径为3~5μm的α相氧化铝和平均粒径为50nm的α相氧化铝按质量比30:70混合而成,所述分散剂由聚乙烯亚胺和烷基苯磺酸钠按质量比2:1复配而成,
50.以氧化铝粉末质量100%计,所述异丙醇、分散剂、粘合剂、脱泡剂的添加量依次为200%、4.5%、12%、1.2%;
51.(3)流延成型、冲压:浆料经过流延机、冲片机处理后,得到所需形状及尺寸的生坯片;
52.(4)排胶:将生坯片放入排胶炉中进行排胶,具体工艺参数为:在氮气气氛下进行第一次排胶,以1.5℃/min升温速率升温至550℃,保温40min,然后在空气气氛下进行第二次排胶,以3℃/min升温速率升温至230℃,保温120min;
53.(5)烧结:将排胶后的生坯片置于烧结炉中,以2℃/min的速率升温至1500℃,保温15min后降温至1450℃,保温16h,冷却后取出即得996氧化铝陶瓷基板。
54.对本实施例制备的氧化铝陶瓷基板进行检测,性能为:相对密度99.2%,体积密度3.99g/cm3,抗弯强度为522mpa。
55.实施例3
56.一种996氧化铝陶瓷基板的制备方法,包括以下步骤:
57.(1)烧结助剂的制备:将硝酸铜、丙三醇钛、四乙氧基硅烷、丙烯酸、聚氮丙啶交联剂、三聚磷酸钠、乙醇按比例加入装有水的反应器内,在70℃下搅拌60min,然后加入过硫酸铵,搅拌反应至形成凝胶,室温下静置30h,然后进行脱水干燥,研磨得到粉末,然后将粉末放入煅烧炉内进行煅烧,煅烧温度为660℃,得到cuo-tio
2-sio2三元烧结助剂;
58.按水的质量100%计,各原料组分的添加量为:硝酸铜9%、丙三醇钛20%、四乙氧基硅烷42%、丙烯酸12%、聚氮丙啶交联剂3%、三聚磷酸钠0.4%、乙醇15%、过硫酸铵0.8%;
59.(2)浆料的制备:将氧化铝粉末、烧结助剂按照质量比99.6:0.4加入球磨机中,同时加入溶剂、分散剂、粘合剂、脱泡剂加入球磨机中球磨20h,然后送入脱泡装置内进行脱泡处理,得到流动性良好且稳定的浆料;
60.所述氧化铝粉末由平均粒径为3~5μm的α相氧化铝和平均粒径为50nm的α相氧化铝按质量比40:60混合而成,所述分散剂由聚乙烯亚胺和烷基苯磺酸钠按质量比1:1~4:1复配而成,以氧化铝粉末质量100%计,所述溶剂、分散剂、粘合剂、脱泡剂的添加量依次为220%、5.5%、15%、1.6%;
61.(3)流延成型、冲压:浆料经过流延机、冲片机处理后,得到所需形状及尺寸的生坯片;
62.(4)排胶:将生坯片放入排胶炉中进行排胶,具体工艺参数为:在氮气气氛下进行第一次排胶,以2℃/min升温速率升温至580℃,保温30min,然后在空气气氛下进行第二次排胶,以4℃/min升温速率升温至240℃,保温100min;
63.(5)烧结:将排胶后的生坯片置于烧结炉中,以2.5℃/min的速率升温至1500℃,保温20min后降温至1450℃,保温20h,冷却后取出即得996氧化铝陶瓷基板。
64.对本实施例制备的氧化铝陶瓷基板进行检测,性能为:相对密度98.4%,体积密度3.93g/cm3,抗弯强度为509mpa。
65.对比例
66.与实施例1的区别在于:cuo-tio
2-sio2三元烧结助剂制备方法,称取与实施例1相同比例的氧化铜、二氧化钛和二氧化硅,放入球磨罐中球磨24h,再经过研磨、过筛,得到cuo-tio
2-sio2三元烧结助剂。
67.对本对比例制备的氧化铝陶瓷基板进行检测,性能为:相对密度95.8%,体积密度3.71g/cm3,抗弯强度为420mpa。
68.以上所记载,仅为利用本创作技术内容的实施例,任何熟悉本项技艺者运用本创作所做的修饰、变化,皆属本创作主张的专利范围,而不限于实施例所揭示者。