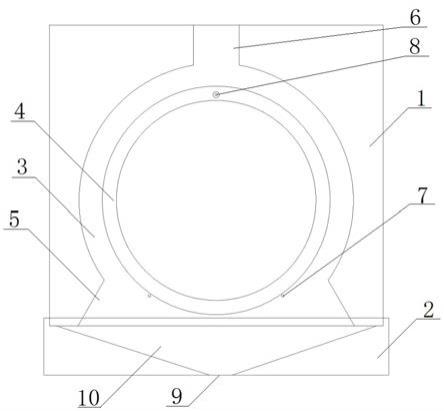
1.本发明属于半导体外延生长设备技术领域,尤其涉及一种碳化硅涂层石墨基座及其制备方法。
背景技术:2.mocvd设备是led产业生产过程中最重要的设备,由于其技术含量高,其价值占整个产业链(外延片—芯片—封装—应用)的70%。cvd-sic涂层石墨基座是衬底材料的承载体和发热体,是mocvd设备最关键的零部件,直接决定薄膜材料均匀性和纯度。碳化硅涂层与基体的结合力、表面粗糙度、致密性、纯度等指标直接影响了外延片的质量及石墨基座的寿命。
3.碳化硅涂层石墨基座的制备方法目前广泛应用的是化学气相沉积法和化学气相反应法。化学气相沉积法主要是在一定的沉积温度下,采用三氯甲基硅烷作为前驱体,氢气作为稀释气体和载气气体,氩气为稀释气体,三氯甲基硅烷通过油温加热呈现气体形式,然后通过鼓泡的方式利用载气氢气带入到沉积炉内,经过一系列的化学反应变化形成碳化硅外层,沉积到石墨基座表面,沉积温度为1050-1200℃,石墨表面活性位置跟反应气体原子或分子结合形成络合物,随后生成固态碳化硅粒子,粒子不断的堆积长大,形成碳化硅涂层。碳化硅涂层的形核点越多、大颗粒越少涂层晶粒越细,得到的涂层也更加致密,抗腐蚀性越强。
4.专利公开号cn112374912 a公开了一种石墨基座表面制备碳化硅涂层的方法,该方法使用硅粉和二氧化硅粉末在高温下反应生成sio气体,sio气体在石墨基座表面先生成碳化硅涂层,然后再用化学气相沉积的方法制备外层碳化硅涂层。该方法同时采用硅粉与二氧化硅粉末,在高温时硅粉和sio气体会同时与石墨基座反应,不易控制,且硅粉易附着在基体表面造成石墨基座表面粗糙。
技术实现要素:5.有鉴于此,本发明的目的在于提供一种碳化硅涂层石墨基座,以解决现有技术中碳化硅涂层颗粒大小不均匀,在mocvd使用环境中抗热震性能及耐腐蚀性能不佳;另外,本技术还提供了一种碳化硅涂层石墨基座的制作方法。
6.为实现上述目的,本发明的一种碳化硅涂层石墨基座所采用的技术方案是:一种碳化硅涂层石墨基座,包括:石墨基座:呈圆盘片状;石墨基座表面沉积碳化硅薄膜,在碳化硅薄膜外沉积石墨烯薄膜或难熔金属碳化物层;或者石墨基座表面沉积难熔金属碳化物层;碳化硅涂层:沉积在难熔金属碳化物层表面或者沉积在石墨烯薄膜表面。
7.有益效果:通过在石墨基座表面沉积石墨烯薄膜或者难熔金属碳化物层,从而在
沉积碳化硅涂层时,大大提高基体表面的比表面积,从而在基体表面形成了更多的形核位点,减轻了碳化硅晶粒聚集程度,使碳化硅涂层的晶粒分布更加均匀致密,增强石墨基座与碳化硅涂层之间的结合力,提高了碳化硅涂层石墨基座的抗热震性能及耐腐蚀性能。
8.一种碳化硅涂层石墨基座制备方法,包括:步骤1:对石墨基座进行预处理,放置于化学气相沉积室内;步骤2:对化学气相沉积室抽真空,然后用惰性气体清洗沉积室;步骤3:采用化学气相沉积工艺在石墨基座表面沉积一层碳化硅薄膜,然后沉积难熔金属碳化物层或者石墨烯薄膜;或者直接在石墨基座表面沉积难熔金属碳化物层;步骤4:采用化学气相沉积工艺在步骤3中形成的难熔金属碳化物层或者石墨烯薄膜外沉积碳化硅涂层。
9.有益效果:本发明在制备碳化硅涂层石墨基座时,方法步骤简单,形成的碳化硅涂层石墨基座的碳化硅涂层的晶粒分布更加均匀致密,增强了碳化硅涂层与石墨基座的之间的结合力,提高了碳化硅涂层石墨基座的抗热震性能及耐腐蚀性能。
10.进一步的,步骤3中,在石墨基座表面沉积一层碳化硅薄膜时,先将化学气相沉积室升温至1100-1500℃,往化学气相沉积室内通入四氯化硅和氢气,四氯化硅和氢气的摩尔比为1:1-1:20,氢气流量为0.1-1slm,沉积压力为1-20kpa,沉积时间为10-30min,在石墨基体表面原位生成一层碳化硅薄膜。
11.有益效果:方便在石墨基座表面沉积形成碳化硅薄膜,使碳化硅薄膜成为石墨烯薄膜或者难熔金属碳化物层外延生长的衬底,使石墨烯或难熔金属碳化物能够沉积外延生长。
12.进一步的,步骤3中,在碳化硅薄膜外沉积石墨烯薄膜时,关闭四氯化硅和氢气,将化学气相沉积室抽真空,将化学气相沉积室降温至1000-1200℃,然后往化学气相沉积室通入甲醇,压力为5-20kpa,甲醇流量为10-20g/h,沉积时间0.5-2h,在碳化硅薄膜表面沉积一层石墨烯薄膜。
13.有益效果:方便在碳化硅薄膜表面沉积石墨烯薄膜,从而增加石墨基座的比表面积,在基体表面形成了更多的形核位点,方便形成一层均匀、致密的碳化硅涂层。
14.步骤3中,在碳化硅薄膜外沉积难熔金属碳化物层时,关闭四氯化硅和氢气,将化学气相沉积室抽真空,将化学气相沉积室温度调至1400-2300℃,使用难熔金属的气态化合物作为难熔金属来源,通入碳源、还原气体、稀释气体,在碳化硅薄膜表面沉积一层难熔金属碳化物层。
15.有益效果:方便在碳化硅薄膜表面沉积难熔金属碳化物层,从而增加石墨基座的比表面积,在基体表面形成了更多的形核位点,方便形成一层均匀、致密的碳化硅涂层。
16.进一步的,所述难熔金属碳化物层为碳化钽涂层;在形成碳化钽涂层时,使用tacl5作为钽源,丙烯作为碳源,氢气作为还原气体,氩气作为稀释气体,tacl5和h2的摩尔比为1:3-1:5,tacl5与丙烯的摩尔比1:1-3:1,氢气流量为0.1-2 slm,氩气为20-50slm,沉积时间为0.5-2h,在碳化硅薄膜表面沉积一层碳化钽。
17.有益效果:方便在碳化硅薄膜表面沉积形成碳化钽涂层,从而通过碳化钽涂层增加石墨基座的比表面积,方便基体表面形成了更多的形核位置,方便形成一层均匀、致密的碳化硅涂层。
18.步骤3中,直接在石墨基座表面沉积难熔金属碳化物层时,使用难熔金属的气态化合物作为难熔金属来源,通入还原气体、稀释气体,在石墨基座表面沉积一层难熔金属碳化物层。
19.有益效果:直接在石墨基座表面沉积一层难熔金属碳化物层,不仅能够满足增加石墨基座的比表面积,方便基体表面形成了更多的形核位置的要求,而且,还比较简单方便。
20.进一步的,所述难熔金属碳化物层为碳化钽涂层;在形成碳化钽涂层时,使用tacl5作为钽源,氢气作为还原气体,氩气作为稀释气体,沉积温度为1400-2300℃,tacl5和h2的摩尔比1:3-1:5,氢气流量为0.1-2slm,氩气流量为20-50slm,沉积时间为0.5-2h,在石墨基座表面沉积一层碳化钽涂层。
21.有益效果:方便在石墨基座表面直接沉积一层碳化钽涂层。
22.在步骤4中,在难熔金属碳化物层或者石墨烯薄膜外沉积碳化硅涂层时,关闭步骤3通入的气体,向化学气相沉积室通入甲基三氯硅烷、氢气和氮气,氢气与甲基三氯硅烷的摩尔比为:6:1-20:1,氢气流量为0.1-2slm,氮气流量为20-30slm,先同时通入氢气和甲基三氯硅烷5-10min后关闭,然后通入氮气对沉积室进行吹扫,吹扫时间为5-20s,再通入氢气与甲基三氯硅烷如此反复进行,总沉积时间为5-10h。
23.有益效果:一方面,方便在难熔金属碳化物层或者石墨烯薄膜外形成在碳化硅涂层;另一方面,通入氮气对沉积室进行吹扫,能够将沉积的较大的碳化硅涂层颗粒吹扫掉,保留小的颗粒,从而达到晶粒细化的目的。
附图说明
24.图1是本发明的化学气相沉积室的结构示意图;图2是图1中的化学气相沉积室的侧视图;图3是图1中的化学气相沉积室的沉积室的结构示意图;图4是图1中的化学气相沉积室的底座的结构示意图;图5是图4的化学气相沉积室的底座的俯视图。
25.附图标记:1-沉积室;2-底座;3-放置腔;4-石墨基座;5-下接口;6-出气口;7-钨针;8-钨柱;9-进气口;10-气体扩散腔室;11-上接口;12-支撑台阶。
具体实施方式
26.下面结合附图及具体实施方式对本发明的一种碳化硅涂层石墨基座作进一步详细描述:本发明的一种碳化硅涂层石墨基座的结构具体实施例一:包括石墨基座,石墨基座呈圆盘片状,在石墨基座表面沉积有碳化硅薄膜,碳化硅薄膜的厚度为50-200nm;在碳化硅薄膜外沉积石墨烯薄膜,碳化硅薄膜作为石墨烯外延生长的衬底,石墨烯薄膜的厚度为100-300nm;在石墨烯薄膜表面沉积有碳化硅涂层。
27.沉积的石墨烯具有较大的比表面积(石墨烯比表面积约为2600m2/g,约为石墨的1000倍),能够增加化学气相沉积碳化硅形核位点。从而在石墨烯薄膜外沉积碳化硅时,能够减轻碳化硅晶粒在石墨烯薄膜上的聚集程度,使碳化硅晶粒在石墨烯薄膜表面分布更加
均匀,而且沉积在石墨烯薄膜上的碳化硅晶粒的粒径均匀,从而使形成的碳化硅涂层更加均匀、致密,且石墨烯表面形核位点较多与碳化硅涂层之间的结合力较强,增强了石墨基座与碳化硅涂层之间的结合力,从而使碳化硅涂层石墨基座具有较佳的抗热震性能和耐腐蚀性能。
28.碳化硅薄膜与石墨烯薄膜过厚会导致层间应力变大,进而导致碳化硅涂层易脱落,影响碳化硅涂层使用寿命。
29.制备本实施例中的碳化硅涂层石墨基座的方法包括如下步骤:步骤1:对石墨基座进行预处理,也即对石墨基座清理干净,然后将石墨基座放置于化学气相沉积室内。
30.步骤2:对化学气相沉积室抽真空,然后用惰性气体清洗沉积室。
31.步骤3:采用化学气相沉积工艺在石墨基座表面沉积一层碳化硅薄膜,然后在碳化硅薄膜外沉积石墨烯薄膜。
32.在石墨基座表面沉积一层碳化硅薄膜时,先将化学气相沉积室升温至1100-1500℃,往化学气相沉积室内通入四氯化硅和氢气,四氯化硅和氢气的摩尔比为1:1-1:20,氢气流量为0.1-1slm,沉积压力为1-20kpa,沉积时间为10-30min,在石墨基体表面原位生成一层碳化硅薄膜,碳化硅薄膜的厚度为50-200nm。用碳化硅薄膜作为石墨烯外延生长的衬底,从而方便石墨烯相对于石墨基座沉积固定。
33.在碳化硅薄膜外沉积石墨烯薄膜时,关闭四氯化硅和氢气,将化学气相沉积室抽真空,将化学气相沉积室降温至1000-1200℃,然后往化学气相沉积室通入甲醇,压力为5-20kpa,甲醇流量为10-20g/h,沉积时间0.5-2h,在碳化硅薄膜表面沉积一层石墨烯薄膜,石墨烯薄膜的厚度为100-300nm。
34.步骤4:采用化学气相沉积工艺在形成的石墨烯薄膜外沉积碳化硅涂层。
35.在石墨烯薄膜外沉积碳化硅涂层时,关闭步骤3通入的甲醇,向化学气相沉积室轮换地通入甲基三氯硅烷、氢气和氮气,氢气与甲基三氯硅烷的摩尔比为:6:1-20:1,氢气流量为0.1-2slm,氮气流量为20-30slm,先同时向化学气相沉积室通入氢气和甲基三氯硅烷,通入5-10min后关闭,然后通入氮气对沉积室进行吹扫,吹扫时间为5-20s,如此反复进行,总沉积时间为5-10h。
36.吹扫能够把大的碳化硅颗粒吹扫掉,保留小的颗粒,实现了小晶粒的密集,从而达到细化碳化硅晶粒的目的,使形成的碳化硅涂层更加均匀、致密,从而提高了碳化硅涂层的抗腐蚀性能。
37.本发明的一种碳化硅涂层石墨基座的结构具体实施例二:包括石墨基座,石墨基座呈圆盘片状,在石墨基座表面沉积有碳化硅薄膜,碳化硅薄膜的厚度为50-200nm;在碳化硅薄膜外沉积难熔金属碳化物层,碳化硅薄膜作为难熔金属碳化物外延生长的衬底,在难熔金属碳化物层表面沉积有碳化硅涂层;难熔金属碳化物的表面能大,有利于细小硅晶粒生长。本实施例中,难熔金属碳化物层为碳化钽层;其他实施例中,难熔金属碳化物层还可以为碳化钨层、碳化钛层或者碳化钼层。
38.制备本实施例中的碳化硅涂层石墨基座的方法包括如下步骤:步骤1:对石墨基座进行预处理,也即对石墨基座清理干净,放置于化学气相沉积室内;
步骤2:对化学气相沉积室抽真空,然后用惰性气体清洗沉积室;步骤3:采用化学气相沉积工艺在石墨基座表面沉积一层碳化硅薄膜,然后沉积难熔金属碳化物层。
39.在石墨基座表面沉积一层碳化硅薄膜时,先将化学气相沉积室升温至1100-1500℃,往化学气相沉积室内通入四氯化硅和氢气,四氯化硅和氢气的摩尔比为1:1-1:20,氢气流量为0.1-1slm,沉积压力为1-20kpa,沉积时间为10-30min,在石墨基体表面原位生成一层碳化硅薄膜。碳化硅薄膜的厚度为50-200nm。用碳化硅薄膜作为难熔金属碳化物外延生长的衬底,从而方便难熔金属碳化物相对于石墨基座沉积固定。
40.在碳化硅薄膜外沉积难熔金属碳化物层时,关闭四氯化硅和氢气,将化学气相沉积室抽真空,将化学气相沉积室温度调至1400-2300℃,使用难熔金属的气态化合物作为难熔金属来源,通入碳源、还原气体、稀释气体,在碳化硅薄膜表面沉积一层难熔金属碳化物层,难熔金属碳化物层的厚度为100-300nm,碳化硅薄膜与难熔金属碳化物层过厚会导致层间应力变大,进而导致碳化硅涂层易脱落,影响碳化硅涂层使用寿命。
41.本实施例中,难熔金属碳化物层为碳化钽涂层;在形成碳化钽涂层时,使用钽的气态化合物tacl5作为钽源,丙烯作为碳源,氢气作为还原气体,氩气作为稀释气体和携带气体,将碳源置于高温化学气相沉积炉内,抽真空,并向高温化学气相沉积炉内通入tacl5、h2、氩气,tacl5和h2的摩尔比为1:3-1:5,tacl5与丙烯的摩尔比1:1-3:1,氢气流量为0.1-2 slm,氩气为20-50slm,沉积时间为0.5-2h,在碳化硅薄膜表面沉积一层碳化钽涂层。其他实施例中,钽源还可以为tacl4;碳源还可以为甲烷或丙烷。
42.在难熔金属碳化物层外沉积碳化硅涂层时,关闭步骤3通入的tacl5、h2、氩气,向化学气相沉积室轮换地通入甲基三氯硅烷、氢气和氮气,氢气与甲基三氯硅烷的摩尔比为:6:1-20:1,氢气流量为0.1-2slm,氮气流量为20-30slm,先同时通入氢气和甲基三氯硅烷,通入5-10min后关闭,然后通入氮气对沉积室进行吹扫,吹扫时间为5-20s,如此反复进行,总沉积时间为5-10h。
43.吹扫能够把大的碳化硅颗粒吹扫掉,保留小的颗粒,实现了小晶粒的密集,从而达到细化碳化硅晶粒的目的,使形成的碳化硅涂层更加均匀、致密,从而提高了碳化硅涂层的抗腐蚀性能。
44.本发明的一种碳化硅涂层石墨基座的结构具体实施例三:包括石墨基座,石墨基座呈圆盘片状;石墨基座表面沉积难熔金属碳化物层,在难熔金属碳化物层表面沉积有碳化硅涂层;难熔金属碳化物的表面能大,有利于细小硅晶粒生长。本实施例中,难熔金属碳化物层为碳化钽层;其他实施例中,难熔金属碳化物层还可以为碳化钨层、碳化钛层或者碳化钼层。
45.制备本实施例中的碳化硅涂层石墨基座的方法包括如下步骤:步骤1:对石墨基座进行预处理,放置于化学气相沉积室内;步骤2:对化学气相沉积室抽真空,然后用惰性气体清洗沉积室;步骤3:直接在石墨基座表面沉积难熔金属碳化物层;直接在石墨基座表面沉积难熔金属碳化物层时,石墨基座表面经抛光处理,使用难熔金属的气态化合物作为难熔金属来源,通入还原气体、稀释气体,在石墨基座表面沉积一层难熔金属碳化物层,难熔金属碳化物层的厚度为100-300nm,难熔金属碳化物层过厚会
导致层间应力变大,进而导致碳化硅涂层易脱落,影响碳化硅涂层使用寿命。
46.本实施例中,难熔金属碳化物层为碳化钽涂层;在形成碳化钽涂层时,使用tacl5作为钽源,氢气作为还原气体,氩气作为稀释气体,沉积温度为1400-2300℃,tacl5和h2的摩尔比1:3-1:5,氢气流量为0.1-2slm,氩气流量为20-50slm,沉积时间为0.5-2h,在石墨基座表面沉积一层碳化钽涂层。
47.在难熔金属碳化物层外沉积碳化硅涂层时,关闭步骤3通入的tacl5、h2、氩气,向化学气相沉积室轮换地通入甲基三氯硅烷、氢气和氮气,氢气与甲基三氯硅烷的摩尔比为:6:1-20:1,氢气流量为0.1-2slm,氮气流量为20-30slm,先同时通入氢气和甲基三氯硅烷5-10min后关闭,然后通入氮气对沉积室进行吹扫,吹扫时间为5-20s,如此反复进行,总沉积时间为5-10h。
48.吹扫能够把大的碳化硅颗粒吹扫掉,保留小的颗粒,实现了小晶粒的密集,从而达到细化碳化硅晶粒的目的,使形成的碳化硅涂层更加均匀、致密,从而提高了碳化硅涂层的抗腐蚀性能。
49.本发明的一种碳化硅涂层石墨基座的结构具体实施例四:包括石墨基座,石墨基座呈圆盘片状,在石墨基座表面沉积有碳化硅薄膜,碳化硅薄膜的厚度为100nm;在碳化硅薄膜外沉积石墨烯涂层,碳化硅薄膜作为石墨烯外延生长的衬底,石墨烯涂层的厚度为100nm;在石墨烯涂层表面沉积有碳化硅涂层。
50.制备本实施例中的碳化硅涂层石墨基座的方法包括如下步骤:步骤1:对石墨基座进行预处理,也即对石墨基座清理干净,然后将石墨基座放置于化学气相沉积室内。
51.步骤2:对化学气相沉积室抽真空,然后用惰性气体清洗沉积室。
52.步骤3:采用化学气相沉积工艺在石墨基座表面沉积一层碳化硅薄膜,然后在碳化硅薄膜外沉积石墨烯涂层。
53.在石墨基座表面沉积一层碳化硅薄膜时,先将化学气相沉积室升温至1300℃,往化学气相沉积室内通入四氯化硅和氢气,四氯化硅和氢气的摩尔比为1:10,氢气流量为1slm,沉积压力为5kpa,沉积时间为20min,在石墨基体表面原位生成一层碳化硅薄膜,碳化硅薄膜的厚度为50-200nm。用碳化硅薄膜作为石墨烯外延生长的衬底,从而方便石墨烯相对于石墨基座沉积固定。
54.在碳化硅薄膜外沉积石墨烯涂层时,关闭四氯化硅和氢气,将化学气相沉积室抽真空,将化学气相沉积室降温至1100℃,然后往化学气相沉积室通入甲醇,压力为10kpa,甲醇流量为20g/h,沉积时间0.5h,在碳化硅薄膜表面沉积一层石墨烯涂层,石墨烯涂层的厚度为100nm。
55.步骤4:采用化学气相沉积工艺在形成的石墨烯涂层外沉积碳化硅涂层。
56.在石墨烯涂层外沉积碳化硅涂层时,关闭步骤3通入的甲醇,向化学气相沉积室轮换地通入甲基三氯硅烷、氢气和氮气,氢气与甲基三氯硅烷的摩尔比为:10:1,氢气流量为2slm,氮气流量为30slm,先同时向化学气相沉积室通入氢气和甲基三氯硅烷,通入10min后关闭,然后通入氮气对沉积室进行吹扫,吹扫时间为10s,如此反复进行,总沉积时间为5h。
57.本发明的一种碳化硅涂层石墨基座的结构具体实施例五:包括石墨基座,石墨基座呈圆盘片状,在石墨基座表面沉积有碳化硅薄膜,碳化硅薄膜的厚度为90nm;在碳化硅薄
膜外沉积难熔金属碳化物层,碳化硅薄膜作为难熔金属碳化物外延生长的衬底,在难熔金属碳化物层表面沉积有碳化硅涂层;难熔金属碳化物的表面能大,有利于细小硅晶粒生长。本实施例中,难熔金属碳化物层为碳化钽层;其他实施例中,难熔金属碳化物层还可以为碳化钨层、碳化钛层或者碳化钼层。
58.制备本实施例中的碳化硅涂层石墨基座的方法包括如下步骤:步骤1:对石墨基座进行预处理,也即对石墨基座清理干净,放置于化学气相沉积室内;步骤2:对化学气相沉积室抽真空,然后用惰性气体清洗沉积室;步骤3:采用化学气相沉积工艺在石墨基座表面沉积一层碳化硅薄膜,然后沉积难熔金属碳化物层。
59.在石墨基座表面沉积一层碳化硅薄膜时,先将化学气相沉积室升温至1500℃,往化学气相沉积室内通入四氯化硅和氢气,四氯化硅和氢气的摩尔比为1:8,氢气流量为0.8slm,沉积压力为8kpa,沉积时间为20min,在石墨基体表面原位生成一层碳化硅薄膜。碳化硅薄膜的厚度为90nm。用碳化硅薄膜作为难熔金属碳化物外延生长的衬底,从而方便难熔金属碳化物相对于石墨基座沉积固定。
60.在碳化硅薄膜外沉积难熔金属碳化物层时,关闭四氯化硅和氢气,将化学气相沉积室抽真空,将化学气相沉积室温度调至1600℃,使用难熔金属的气态化合物作为难熔金属来源,通入碳源、还原气体、稀释气体,在碳化硅薄膜表面沉积一层难熔金属碳化物层。
61.本实施例中,难熔金属碳化物层为碳化钽涂层;在形成碳化钽涂层时,使用钽的气态化合物tacl5作为钽源,丙烯作为碳源,氢气作为还原气体,氩气作为稀释气体和携带气体,将碳源置于高温化学气相沉积炉内,抽真空,并向高温化学气相沉积炉内通入tacl5、h2、氩气,tacl5和h2的摩尔比为1:4,tacl5与丙烯的摩尔比2:1,氢气流量为1.5slm,氩气为30slm,沉积时间为1.5h,在碳化硅薄膜表面沉积一层碳化钽涂层。其他实施例中,钽源还可以为tacl4;碳源还可以为甲烷或丙烷。
62.在难熔金属碳化物层外沉积碳化硅涂层时,关闭步骤3通入的tacl5、h2、氩气,向化学气相沉积室轮换地通入甲基三氯硅烷、氢气和氮气,氢气与甲基三氯硅烷的摩尔比为:15:1,氢气流量为1.5slm,氮气流量为20slm,先同时通入氢气和甲基三氯硅烷,通入8min后关闭,然后通入氮气对沉积室进行吹扫,吹扫时间为15s,如此反复进行,总沉积时间为4.5h。
63.本发明的一种碳化硅涂层石墨基座的结构具体实施例六:包括石墨基座,石墨基座呈圆盘片状;石墨基座表面沉积难熔金属碳化物层,在难熔金属碳化物层表面沉积有碳化硅涂层;难熔金属碳化物的表面能大,有利于细小硅晶粒生长。本实施例中,难熔金属碳化物层为碳化钽层;其他实施例中,难熔金属碳化物层还可以为碳化钨层、碳化钛层或者碳化钼层。
64.制备本实施例中的碳化硅涂层石墨基座的方法包括如下步骤:步骤1:对石墨基座进行预处理,放置于化学气相沉积室内;步骤2:对化学气相沉积室抽真空,然后用惰性气体清洗沉积室;步骤3:直接在石墨基座表面沉积难熔金属碳化物层;直接在石墨基座表面沉积难熔金属碳化物层时,石墨基座表面经抛光处理,使用
难熔金属的气态化合物作为难熔金属来源,通入还原气体、稀释气体,在石墨基座表面沉积一层难熔金属碳化物层。
65.本实施例中,难熔金属碳化物层为碳化钽涂层;在形成碳化钽涂层时,使用tacl5作为钽源,氢气作为还原气体,氩气作为稀释气体,沉积温度为1650℃,tacl5和h2的摩尔比1:3,氢气流量为0.1-2slm,氩气流量为20-50slm,沉积时间为0.5-2h,在石墨基座表面沉积一层碳化钽涂层。
66.在难熔金属碳化物层外沉积碳化硅涂层时,关闭步骤3通入的tacl5、h2、氩气,向化学气相沉积室轮换地通入甲基三氯硅烷、氢气和氮气,氢气与甲基三氯硅烷的摩尔比为:6:1,氢气流量为1.6slm,氮气流量为25slm,先同时通入氢气和甲基三氯硅烷6min后关闭,然后通入氮气对沉积室进行吹扫,吹扫时间为12s,如此反复进行,总沉积时间为8h。化学气相沉积室如图1和图2所示,包括底座2、支撑在底座2上的沉积室1;具体的,底座2呈长方体状,在底座2中设置有气体扩散腔室10,底座2的下表面中部开设有进气口9,进气口9与气体扩散腔室10连通,底座2的上表面开设有上接口11,上接口11与气体扩散腔室10连通。本实施例中,气体扩散腔室10为从下向上逐渐扩大的扩口结构,以方便气流经过气体扩散腔室10时在左右方向上扩散。
67.如图4和图5所示,底座2上接口11与气体扩散腔室10连通处设置有支撑台阶12,以供沉积室1底部插入底座2上接口11后支撑在底座2中。
68.如图3所示,沉积室1设置有放置腔3,放置腔3用于放置石墨基座4,石墨基座4与放置腔3前后腔壁之间的距离为5-10nm,从而有利于保证气体沉积速率同时也便于吹扫。
69.沉积室1下表面开设有下接口5,下接口5与放置腔3连通设置,下接口5为从下向上逐渐缩小的缩口结构,沉积室1的下接口5能够供石墨基座4放置于放置腔3中。沉积室1上表面开设有出气口6,出气口6与沉积室1的放置腔3连通设置。
70.沉积室1的前侧面下部开设有两个穿孔,穿孔将沉积室1放置腔3与外界连通,以在石墨基座4竖直放置在放置腔3中后,钨针7从穿孔穿过后对石墨基座4形成支撑。
71.在沉积室1前侧壁上部与后侧壁上部前后对应设置有两个钨柱8,石墨基座4在前后方向插设在两个钨柱8之间,以防止石墨基座4在前后方向发生晃动。
72.底座2中的气体扩散腔室10、沉积室1的放置腔3均在前后方向设计狭窄,使底座2的气体扩散腔室10、沉积室1的放置腔3形成连通的、供气体流通的狭缝。气体从进气口9进入底座2后,经过气体扩散腔室10,气体扩散腔室10能够将气体在左右方向进行扩散,扩散的气体到达沉积室1的放置腔3,流经放置腔3中的石墨基座4,并在石墨基座4的表面气相沉积,然后多余的气体从沉积室1的出气口6排出。
73.以上仅为本发明的较佳实施例而已,并不用以限制本发明,凡在本发明的精神和原则之内,所作的任何修改、等同替换、改进等,均应包含在本发明的保护范围之内。