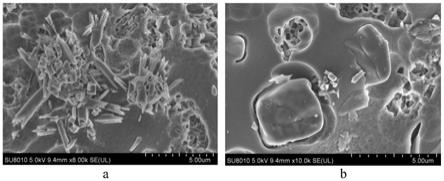
1.本发明涉及建筑陶瓷材料技术领域,尤其涉及一种建筑陶瓷坯体的制备方法及其产品。
背景技术:2.我国是全球最大的陶瓷生产国和出口国,建筑陶瓷行业产量近十年稳居世界第一,在全球市场中占据着无可替代的重要地位。近年来建筑陶瓷以其优异的性能和优雅别致的美学效果越来越被市场和消费者青睐,但目前建筑陶瓷的生产仍存在着“高污染、高能耗、高排放”的问题,如何使建筑陶瓷行业节能低碳、绿色发展,是全行业亟待解决的难题。目前我国的建筑陶瓷(尤其是岩板)大部分采用高铝配方体系,其铝含量在15~25wt%之间,烧成温度较高,大多在1150~1180℃之间,且产品普遍偏厚,厚度为8~12mm,其抗折强度大多为40~70mpa,普遍偏低。若能采用成本低廉的低铝原料,制备可在超低温烧成的高强度建筑陶瓷,对研发推广薄型瓷砖极其有利,不仅能够降低产品生产和运输成本,而且可以减少日益匮乏的高铝原料的使用,对于保护资源、节能低碳、减少环境污染具有重要意义。
技术实现要素:3.本发明的目的在于克服现有技术的不足,提供一种采用低铝原料低温制备建筑陶瓷坯体的方法,以解决高铝制品烧成温度高和原料成本高、低铝制品抗折强度低的问题,在保护资源、节能低碳、减少环境污染的同时,有利于轻量、薄型产品的开发,从而降低产品生产和运输成本。本发明的另一目的在于提供利用上述采用低铝原料低温制备建筑陶瓷坯体的方法制得的产品。
4.本发明的目的通过以下技术方案予以实现:
5.本发明提供的一种采用低铝原料低温制备建筑陶瓷坯体的方法,包括以下步骤:
6.(1)所述坯体的原料组成为钼矿尾砂40~50wt%、钢渣10~25wt%、页岩30~45wt%,其中钼矿尾砂、钢渣、页岩中al2o3的含量分别<12wt%、<2wt%、<8wt%;将所述各原料组成混合后进行湿法球磨,经干燥、过筛、造粒,得到中位粒径为20~60目的物料;
7.(2)将所述物料压制成型后,以10~25℃/min的升温速率从室温升温至1100~1140℃,保温10~20min,随炉自然冷却至室温,即得到低温低铝建筑陶瓷坯体。
8.进一步地,本发明所述各原料组成混合后的物料,其化学组成为:sio257.05~65.46wt%、al2o37.78~9.07wt%、fe2o34.74~8.17wt%、cao 8.66~14.37wt%、mgo 1.78~2.68wt%、k2o 2.51~3.08wt%、na2o 0.79~0.99wt%、tio20.17~0.22wt%、il5.86~6.63wt%。
9.进一步地,本发明所述钼矿尾砂的粒度为20~60目,钢渣的粒度为30~80目,页岩的粒度为30~80目。所述步骤(2)中压制成型的压力为6~10mpa。
10.本发明的另一目的通过以下技术方案予以实现:
11.本发明利用上述采用低铝原料低温制备建筑陶瓷坯体的方法制得的产品,所制得陶瓷坯体的主晶相为石英和透辉石,陶瓷坯体的抗折强度为84.26~101.45mpa、吸水率为0.16~0.45%。
12.本发明具有以下有益效果:
13.本发明采用的钼矿尾砂、钢渣及粉砂质页岩为低铝原料,其中钢渣是炼钢过程产生的固体废弃物,对环境有一定的污染;钼矿尾砂和粉砂质页岩目前大多用来制备免烧砖和道路填埋,附加值较低。本发明利用钼矿尾砂和页岩含有一定量的钾钠化合物,而钢渣富含钙铁镁,三者可在950℃以下形成k-na-ca-mg-fe多元低共熔物,从而在坯体中原位生成了透辉石和石英晶相,通过石英晶相的弥散增韧和棒状透辉石晶相的钉扎效应,克服了低铝制品抗折强度较低的缺陷,有利于制备轻量、薄型产品;而且有效解决了高铝制品烧成温度高和原料成本高的难题,节能环保,经济效益显著,市场前景广阔。
附图说明
14.下面将结合实施例和附图对本发明作进一步的详细描述:
15.图1是本发明实施例所制得的陶瓷坯体的显微结构图(a:8000倍;b:10000倍);
16.图2是本发明实施例所制得的陶瓷坯体的xrd图谱。
具体实施方式
17.实施例一:
18.本实施例一种采用低铝原料低温制备建筑陶瓷坯体的方法,其步骤如下:
19.(1)坯体的原料组成为钼矿尾砂43wt%、钢渣12wt%、页岩45wt%,粒度均为50目;将上述各原料组成混合后进行湿法球磨(料∶球∶水=1∶2∶1)30min,所得浆料放入烘箱中在100℃温度下干燥4h,过100目筛后进行粉末造粒,得到中位粒径为30目的物料;
20.(2)将上述物料在压力10mpa下压制成型,压制时间为30s;然后放入箱式电阻烧结炉中,以22℃/min的升温速率从室温升温至1100℃,保温10min,随炉自然冷却至室温,即得到低温低铝建筑陶瓷坯体。
21.实施例二:
22.本实施例一种采用低铝原料低温制备建筑陶瓷坯体的方法,其步骤如下:
23.(1)坯体的原料组成为钼矿尾砂45wt%、钢渣20wt%、页岩35wt%,粒度均为50目;将上述各原料组成混合后进行湿法球磨(料∶球∶水=1∶2∶1)30min,所得浆料放入烘箱中在100℃温度下干燥4h,过100目筛后进行粉末造粒,得到中位粒径为40目的物料;
24.(2)将上述物料在压力6mpa下压制成型,压制时间为30s;然后放入箱式电阻烧结炉中,以15℃/min的升温速率从室温升温至1120℃,保温10min,随炉自然冷却至室温,即得到低温低铝建筑陶瓷坯体。
25.实施例三:
26.本实施例一种采用低铝原料低温制备建筑陶瓷坯体的方法,其步骤如下:
27.(1)坯体的原料组成为钼矿尾砂50wt%、钢渣10wt%、页岩40wt%,粒度均为50目;将上述各原料组成混合后进行湿法球磨(料∶球∶水=1∶2∶1)30min,所得浆料放入烘箱中在100℃温度下干燥4h,过100目筛后进行粉末造粒,得到中位粒径为50目的物料;
28.(2)将上述物料在压力6mpa下压制成型,压制时间为30s;然后放入箱式电阻烧结炉中,以12℃/min的升温速率从室温升温至1140℃,保温10min,随炉自然冷却至室温,即得到低温低铝建筑陶瓷坯体。
29.实施例四:
30.本实施例一种采用低铝原料低温制备建筑陶瓷坯体的方法,其步骤如下:
31.(1)坯体的原料组成为钼矿尾砂40wt%、钢渣15wt%、页岩45wt%,粒度均为50目;将上述各原料组成混合后进行湿法球磨(料∶球∶水=1∶2∶1)30min,所得浆料放入烘箱中在100℃温度下干燥4h,过100目筛后进行粉末造粒,得到中位粒径为60目的物料;
32.(2)将上述物料在压力8mpa下压制成型,压制时间为30s;然后放入箱式电阻烧结炉中,以15℃/min的升温速率从室温升温至1130℃,保温10min,随炉自然冷却至室温,即得到低温低铝建筑陶瓷坯体。
33.以某建筑陶瓷厂陶瓷坯体作为对比例,其原料组成为:瓷石32wt%、钾长石10wt%、钠长石12wt%、高岭土21wt%、黑泥10wt%、白泥14wt%、滑石1wt%;其制备方法同实施例一。
34.本发明实施例所用原料及对比例原料的化学组成如表1所示。
35.表1本发明实施例所用原料及对比例原料的化学组成(wt%)
36.化学组成sio2al2o3fe2o3caomgok2ona2otio2il钼矿尾砂73.5511.651.842.050.845.051.880.432.71钢渣15.601.8025.1442.257.070.03008.11页岩67.797.643.288.541.661.370.1109.61对比例坯体67.8919.091.560.400.893.621.850.284.42
37.如图1、图2所示,本发明实施例所制得的陶瓷坯体主晶相为石英和透辉石,石英晶相具有弥散增韧的作用,棒状透辉石晶相具有钉扎效应,从而有效提高了产品的抗折强度。
38.本发明实施例所制得的陶瓷坯体、以及对比例陶瓷坯体的性能测试如下:
39.抗折强度的测定:依据gb/t17657-2013(三点弯曲法测静曲强度)标准进行测定,公式如式(1)所示:
[0040][0041]
式中:b‑‑
试件的静曲强度单位为兆帕(mpa);
[0042]fmax
‑‑
试件破坏时最大载荷,单位为牛顿(n);
[0043]
l
‑‑
两支座间距离,单位为毫米(mm);
[0044]b‑‑
试件宽度,单位为毫米(mm);
[0045]
t
‑‑
试件厚度,单位为毫米(mm)。
[0046]
吸水率的测定:依据gb/t 3299-2011(真空法),公式如式(2)所示:
[0047][0048]
式中:ω
‑‑
试样的吸水率,%;
[0049]
m0‑‑
干燥试样的质量,单位为克(g);
[0050]
m1‑‑
吸水饱和试样的质量,单位为克(g)。
[0051]
测试结果如表2所示。
[0052]
表2本发明实施例以及对比例陶瓷坯体的性能指标
[0053]