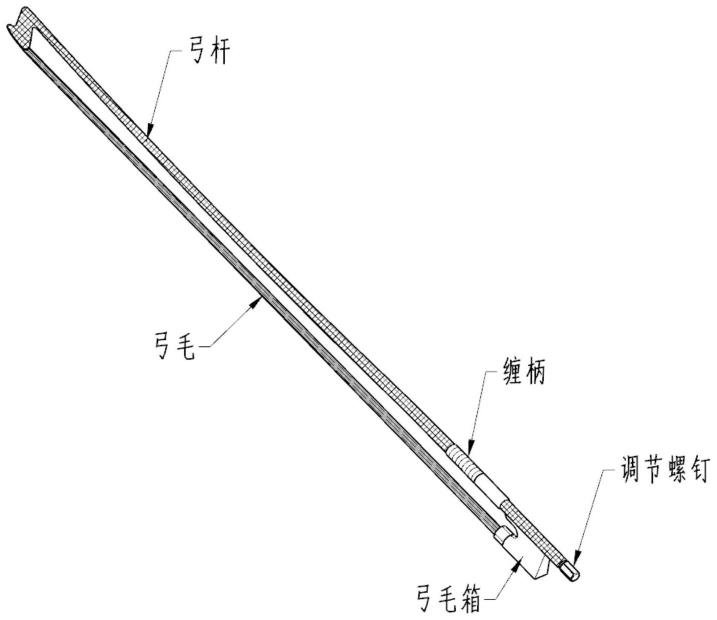
1.本发明属于弦乐器材领域,具体涉及一种陶瓷复合材料琴弓弓杆、制备方法及应用。
背景技术:2.小提琴、中提琴、大提琴、贝斯和二胡等拉弦式弦乐器在各种交响乐演奏、独奏和伴奏等表演场合具有举足轻重的地位,乐器的音质直接影响其艺术表达效果。对于上述拉弦式弦乐器来说,决定乐器音质的因素主要有琴体和琴弓。而琴弓是演奏者与琴建立联系的唯一桥梁,因此,演奏效果与弓的性能息息相关。
3.琴弓的结构可分为弓杆、弓毛、弓毛箱、调节螺钉和缠柄等附件。弓杆是琴弓的主体,其材质决定了琴弓的整体性能。衡量弓杆优劣的主要指标是它的张力性能。一方面,为了获得更大、更稳定的张力,弓杆材料选用巴西产的伯尔南布克木等木材以及碳纤维材料;另一方面,为了使得琴弓在长期演奏和复杂温度、湿度环境下保持均一的张力性能,需要对弓杆表面进行上漆等表面处理。
4.然而,由于过度开采导致的伯尔南布克木数量骤减,巴西政府早已限制其砍伐和交易,用于制作琴弓的主要木材已逐年短缺。另一方面,普通木材和碳纤维材料的琴弓在性能上存在振动传递速度低、弹性差、热膨胀系数大、吸湿变形量大和变形后难以恢复等短板。
5.现有技术中公开了一种碳纤复合琴弓,申请号为200420027215.4,琴弓是由玻璃纤维内芯体和包裹在玻璃纤维内芯体表面的碳纤维层组成,玻璃纤维内芯体和碳纤维层通过粘接剂粘结相连。该结构的琴弓以塑代木,节省大量的木材资源;但其无法控制琴弓的弹性模量,存在振动传递速度低、弹性差、热膨胀系数大的问题。
6.现有技术中公开了一种胡琴,申请号为201520085200.1,琴杆包括下端插装在琴筒中的空心碳纤维主支撑杆;该琴杆采用碳纤维空心管制作琴杆,杆体强度高,不会弯曲、变形,但只能通过碳纤维振动板进行振动传递速度低的调节,琴杆的弹性模量仍无法实现控制。
7.连续纤维增强的陶瓷基复合材料具有轻质、高强、耐高温等优势,被广泛应用于航空、航天防热构件,主要解决的是其耐高温、高强度、高刚度和断裂韧性问题。采用这种材料作为琴弓的主体材料,有望克服普通木材和碳纤维材料琴弓的上述不足,但仍需要解决其作为演奏乐器时的弹性模量问题。弹性模量越高,振动传递速度越快、但演奏时的手感较为生硬;弹性模量越低,振动传递速度越慢、手感较为柔和。因此需要在材料、结构和工艺等方面进行设计,实现振动传递效果和演奏手感的有效协调。
技术实现要素:8.要解决的技术问题:
9.为了避免现有技术的不足之处,本发明提出一种陶瓷复合材料琴弓弓杆、制备方
法及应用,采用碳纤维或陶瓷纤维作为基体,在其表面依次沉积界面层和陶瓷基体,得到陶瓷复合材料琴弓弓杆;通过设置界面层和陶瓷基体,以及对其沉积工艺的参数条件限定,解决了琴弓弓杆弹性不足、复杂温湿度环境下张力不稳定、长时间使用后性能和尺寸变化等问题。
10.本发明的技术方案是:一种陶瓷复合材料琴弓弓杆,其特征在于:包括碳纤维或陶瓷纤维空杆,及依次沉积于其表面的界面层和陶瓷基体。
11.本发明的技术方案是:所述界面层为热解碳或氮化硼,厚度为100-600nm。
12.本发明的进一步技术方案是:所述陶瓷基体为碳化硅或氮化硅。
13.一种陶瓷复合材料琴弓弓杆的制备方法,其特征在于具体步骤如下:
14.步骤1:弓杆内型模型建立;
15.步骤2:内型模具加工;采用石墨纸、芳纶纸、硫酸纸或天然木材作为模具材料,按照弓杆内型几何型面加工出弓杆内型模具;
16.步骤3:编织体制备;以碳纤维或陶瓷纤维中的一种或几种作为原材料,在弓杆内型模具周面上编织出弓杆编织体;
17.步骤4:界面层制备;将带有弓杆内型模具的弓杆编织体放置在化学气相沉积炉内,在弓杆编织体表面制备界面层;
18.所述界面层为热解碳时,制备工艺为:沉积压力为50-1000pa,沉积温度为900-1050℃,沉积时间为5-9h,沉积气体为丙烯和氢气的混合气体,沉积完成后,再在真空条件下,于1750-2250℃热处理5-20h;其中,丙烯和氢气的流量比为1:1-5;循环执行3-6次;
19.所述界面层为氮化硼时,制备工艺为:沉积压力为100-8000pa,沉积温度为850-1050℃,沉积时间为10-20h,沉积气体为氩气、氢气、氨气和三氯化硼的混合气体;其中,氩气、氢气、氨气和三氯化硼的流量比为1:1-3:2-8:2-8;循环执行2-4次;
20.步骤5:陶瓷基体制备;将完成界面层制备的弓杆编织体放置在化学气相沉积炉内,在弓杆编织体表面制备陶瓷基体;
21.陶瓷基体为碳化硅时,制备工艺为:于压力为200-5000pa条件下,升温至900-1200℃,保温1-2h后,通入三氯甲基硅烷、氢气和氩气的混合气体,三氯甲基硅烷、氢气和氩气的流量比为1:5-15:15-25,沉积15-28h后,继续保温1-2h,降温至室温;循环执行12-18次。
22.陶瓷基体为氮化硅时,制备工艺为:于压力为200-5000pa条件下,升温至700-1200℃,保温1-2h后,氢气、氩气、三氯甲基硅烷和氨气的混合气体,氢气、氩气、三氯甲基硅烷和氨气的流量比为1:1:5-50:5-50,沉积10-25h后,继续保温1-2h,降温至室温;循环执行4-8次;
23.步骤6:加工;采用机械加工和打磨的方式,将制备完陶瓷基体的弓杆内部剩余的模具残渣去除,并将外型面和与弓毛箱连接处的长槽加工至设计尺寸。
24.本发明的进一步技术方案是:所述步骤1中,以选定琴弓弓杆型面为参考,将其型面向内偏置0.5-2.0mm,获得弓杆内型几何型面。
25.本发明的进一步技术方案是:所述步骤2中,在内型模具加工前,采用树脂胶对模具材料进行固化加强。
26.本发明的进一步技术方案是:所述步骤3中,采用二维编织的方式进行编织体编织,厚度为步骤1所述偏置尺寸;所述二维编织为二维平纹编织、二维缎纹编织、二维斜纹编
织或2.5维编织。
27.本发明的进一步技术方案是:所述编织体原材料为碳纤维时,编织布的经向与琴弓中轴线的夹角为0~20
°
;所述编织体原材料为陶瓷纤维时,编织布的经向与琴弓中轴线的夹角为30~45
°
。
28.本发明的进一步技术方案是:所述步骤3中,编织体原材料选用碳化硅纤维或莫来石纤维。
29.一种陶瓷复合材料琴弓弓杆的应用,其特征在于:所述陶瓷复合材料琴弓弓杆应用于拉弦式弦乐器,包括提琴、中提琴、大提琴、贝斯和二胡。
30.有益效果
31.本发明的有益效果在于:
32.一、采用《gb/t 15777-1995木材顺纹抗压弹性模量测定方法》测得,陶瓷复合材料的弹性模量为45-150gpa,显著高于天然木材的15-25gpa。因此将陶瓷复合材料作为弓杆的主体材料,可显著提升琴弓的弹性和振动传递速度,使琴弓对振动的反馈更迅速、更清晰。
33.现有技术中该材料被应用在航空航天领域中,主要关注的是材料的耐温性、高强度、高刚度和断裂韧性。在纤维预制体方面,一般仅考虑0
°
编织方向的性能(即性能最高的方向);界面层制备方面,一般均选择能够使强度、断裂韧性最高的工艺参数;陶瓷基体制备方面,一般均选择能够使强度、耐温性最高的工艺参数。而本发明关注的是影响振动传递速度和演奏手感的性能,即材料的弹性模量必须通过纤维预制体、界面层和陶瓷基体的联合设计,将弹性模量控制在合适的范围内。
34.其中,作为基体的纤维类型及其编织角会直接影响琴弓轴线的弹性模量,如不进行调整,陶瓷纤维会造成弹性模量过高、碳纤维会造成弹性模量不足的问题;本发明对界面层和陶瓷基体的沉积工艺的参数条件进行了限定,所取的沉积时间均在曲线变缓和部分,因此所制备材料性能较为稳定。如图4所示,对于碳纤维编织体,编织角应介于0~20
°
,否则无法达到提升模量的效果;对于碳化硅陶瓷纤维编织体,编织角应介于30~45
°
,否则模量太高,演奏手感生硬。如图5、6所示,分别表示界面层和陶瓷基体制备工艺参数(时间)应处于一定范围内,偏离此范围将导致材料的模量不稳定,无法形成性能均匀的弓杆产品。
35.二、采用《gb/t 1932-2009木材干缩性测定方法》测得,陶瓷复合材料的轴向干缩率为0,径向干缩率为0,体积干缩率为0,显著低于木材的0.1-0.5%的轴向干缩率、2-6%的径向干缩率和5-15%的体积干缩率。因此,将陶瓷复合材料作为弓杆的主体材料,可有效解决琴弓在复杂温湿度环境下张力不稳定、长时间使用后性能和尺寸变化等问题,且无需进行任何上漆等表面处理。
36.三、本发明所述弓杆具有空心结构特征,能够将充分发挥弓杆的振动传递效果,相比传统实心纯木材质弓杆和实心碳纤维材质弓杆,其重量较轻,且可根据演奏者喜好增加配重以调节琴弓重量和重心;此外,振动传递仅集中于空心弓杆的表面,进一步改善了琴弓对振动的清晰反馈。
37.四、本发明制备过程中所采用的模具材料会在步骤4和步骤5的实施过程中受高温影响不断地碳化,并在步骤4和步骤5的工艺废气环境中腐蚀、粉化,同时在化学气相沉积炉内随工艺废气排出。即,步骤2中所述模具材料会在后续制备工艺中逐渐原位消失,而这种模具的材料选择是与纤维编织形式和其他步骤中的工艺参数(温度、流量和时间)密切相关
的。如超出此模具材料选择范围或工艺参数范围,会出现模具无法达到弓杆定型效果、消失后残余量太大等问题。
38.五、相比天然木材,陶瓷复合材料具有耐酸、耐碱、阻燃、耐(霉)菌、耐虫害等天然优势,可显著提升琴弓的环境适应性和使用寿命。
39.六、陶瓷复合材料弓杆的应用,可节省日趋短缺的木制原材料,符合环保主题。
附图说明
40.图1为具有本发明所述陶瓷复合材料弓杆的琴弓示意图;
41.图2为本发明所述陶瓷复合材料弓杆的外观照片;
42.图3为本发明所述陶瓷复合材料弓杆的截面照片;
43.图4为纤维类型及其编织经向与琴弓轴线的夹角对弹性模量的影响曲线图;
44.图5为本发明纤维类型及界面层沉积时间对弹性模量的影响曲线图;
45.图6为本发明纤维类型及陶瓷基体沉积时间对弹性模量的影响曲线图。
具体实施方式
46.下面通过参考附图描述的实施例是示例性的,旨在用于解释本发明,而不能理解为对本发明的限制。
47.参照图1-3所示,本发明一种陶瓷复合材料琴弓弓杆,包括碳纤维或陶瓷纤维空杆,及依次沉积于其表面的界面层和陶瓷基体;所述界面层为热解碳或氮化硼,厚度为100-600nm;所述陶瓷基体为碳化硅或氮化硅。
48.所示陶瓷复合材料琴弓弓杆的制备方法,具体步骤如下:
49.步骤1:弓杆内型模型建立;以选定琴弓弓杆型面为参考,将其型面向内偏置0.5-2.0mm,获得弓杆内型几何型面;
50.步骤2:内型模具加工;采用石墨纸、芳纶纸、硫酸纸或天然木材作为模具材料,按照弓杆内型几何型面加工出弓杆内型模具;在内型模具加工前,可以采用树脂胶对模具材料进行固化加强;
51.步骤3:编织体制备;以碳纤维或陶瓷纤维(如碳化硅纤维或莫来石纤维等)中的一种或几种作为原材料,在弓杆内型模具周面上编织出弓杆编织体;采用二维编织的方式进行编织体编织,厚度为步骤1所述偏置尺寸;所述二维编织为二维平纹编织、二维缎纹编织、二维斜纹编织或2.5维编织;
52.所述编织体原材料为碳纤维时,编织布的经向与琴弓中轴线的夹角为0~20
°
;所述编织体原材料为陶瓷纤维时,编织布的经向与琴弓中轴线的夹角为30~45
°
;
53.步骤4:界面层制备;将带有弓杆内型模具的弓杆编织体放置在化学气相沉积炉内,在弓杆编织体表面制备界面层;
54.所述界面层为热解碳时,制备工艺为:沉积压力为50-1000pa,沉积温度为900-1050℃,沉积时间为5-9h,沉积气体为丙烯和氢气的混合气体,沉积完成后,再在真空条件下,于1750-2250℃热处理5-20h;其中,丙烯和氢气的流量比为1:1-5;循环执行3-6次;
55.所述界面层为氮化硼时,制备工艺为:沉积压力为100-8000pa,沉积温度为850-1050℃,沉积时间为10-20h,沉积气体为氩气、氢气、氨气和三氯化硼的混合气体;其中,氩
气、氢气、氨气和三氯化硼的流量比为1:1-3:2-8:2-8;循环执行2-4次;
56.步骤5:陶瓷基体制备;将完成界面层制备的弓杆编织体放置在化学气相沉积炉内,在弓杆编织体表面制备陶瓷基体;
57.陶瓷基体为碳化硅时,制备工艺为:于压力为200-5000pa条件下,升温至900-1200℃,保温1-2h后,通入三氯甲基硅烷、氢气和氩气的混合气体,三氯甲基硅烷、氢气和氩气的流量比为1:5-15:15-25,沉积15-28h后,继续保温1-2h,降温至室温;循环执行12-18次。
58.陶瓷基体为氮化硅时,制备工艺为:于压力为200-5000pa条件下,升温至700-1200℃,保温1-2h后,氢气、氩气、三氯甲基硅烷和氨气的混合气体,氢气、氩气、三氯甲基硅烷和氨气的流量比为1:1:5-50:5-50,沉积10-25h后,继续保温1-2h,降温至室温;循环执行4-8次;
59.其中,步骤2中所述模具材料会在步骤4和步骤5的实施过程中受高温影响不断地碳化,并在步骤4和步骤5的工艺废气环境中腐蚀、粉化,同时在化学气相沉积炉内随工艺废气排出。即,步骤2中所述模具材料会在后续制备工艺中逐渐原位消失,而这种模具的材料选择是与纤维编织形式和其他步骤中的工艺参数(温度、流量和时间)密切相关的。如超出此模具材料选择范围或工艺参数范围,会出现模具无法达到弓杆定型效果、消失后残余量太大等问题。
60.步骤6:加工;采用机械加工和打磨的方式,将制备完陶瓷基体的弓杆内部剩余的模具残渣去除,并将外型面和与弓毛箱连接处的长槽加工至设计尺寸。
61.实施例1:
62.一种陶瓷复合材料琴弓弓杆,其制备方法包括以下步骤:
63.步骤1:内型模型建立。以典型琴弓弓杆型面为参考,将其型面向内偏置0.8mm,获得弓杆内型几何型面。
64.步骤2:内型模具加工。采用天然木材作为模具材料,按照弓杆内型几何型面加工出弓杆内型模具。
65.步骤3:编织体制备。以碳纤维作为原材料,采用二维平纹编织的方式,在弓杆内型模具上编织出厚度为0.8mm的编织体。
66.步骤4:界面层制备。将带有弓杆内型模具的弓杆编织体放置在化学气相沉积炉内,在弓杆编织体表面制备厚度为250nm的热解碳界面层。其制备过程为:沉积压力为800pa,沉积温度为1050℃,沉积时间为56h,沉积气体为丙烯和氢气的混合气体,沉积完成后,再在真空条件下,于1950℃热处理30h;其中,丙烯和氢气的流量比为1:5;循环执行3次。
67.步骤5:陶瓷基体制备。将完成界面层制备的弓杆编织体放置在化学气相沉积炉内,在弓杆编织体表面制备碳化硅陶瓷基体。其制备过程为:于压力为2000pa条件下,升温至1000℃,保温2h后,通入三氯甲基硅烷、氢气和氩气的混合气体,三氯甲基硅烷、氢气和氩气的流量比为1:12:18,沉积55h后,继续保温2h,降温至室温;循环执行5次。
68.步骤6:加工。采用机械加工和打磨的方式,将制备完陶瓷基体的弓杆内部残余模具材料去除,并将外型面和与弓毛箱连接处的长槽加工至设计尺寸。
69.实施例2:
70.一种陶瓷复合材料琴弓弓杆,其制备方法包括以下步骤:
71.步骤1:内型模型建立。以典型琴弓弓杆型面为参考,将其型面向内偏置1.0mm,获
得弓杆内型几何型面。
72.步骤2:内型模具加工。采用硫酸纸木材作为模具材料,按照弓杆内型几何型面卷绕出弓杆内型模具,并采用树脂胶对卷绕的硫酸纸进行固化加强。
73.步骤3:编织体制备。以碳化硅纤维作为原材料,采用二维斜纹编织的方式,在弓杆内型模具上编织出厚度为1.0mm的编织体。
74.步骤4:界面层制备。将带有弓杆内型模具的弓杆编织体放置在化学气相沉积炉内,在弓杆编织体表面制备厚度为480nm的热解碳界面层。其制备过程为::沉积压力为900pa,沉积温度为700℃,沉积时间为32h,沉积气体为氩气、氢气、氨气和三氯化硼的混合气体;其中,氩气、氢气、氨气和三氯化硼的流量比为1:1.5:6:6;循环执行2次。
75.步骤5:陶瓷基体制备。将完成界面层制备的弓杆编织体放置在化学气相沉积炉内,在弓杆编织体表面制备碳化硅陶瓷基体。其制备过程为:于压力为1200pa条件下,升温至1050℃,保温2h后,通入三氯甲基硅烷、氢气和氩气的混合气体,三氯甲基硅烷、氢气和氩气的流量比为1:10:15,沉积48h后,继续保温2h,降温至室温;循环执行4次。
76.步骤6:加工。采用机械加工和打磨的方式,将制备完陶瓷基体的弓杆内部残余模具材料去除,并将外型面和与弓毛箱连接处的长槽加工至设计尺寸。
77.效果验证
78.对实施例1-2制备的弓杆采用《gb/t 15777-1995木材顺纹抗压弹性模量测定方法》测得,弓杆材料的弹性模量分别为75gpa和228gpa,显著高于天然木材的15-25gpa。因此采用实施例1-2制备的弓杆,可显著提升琴弓的弹性和振动传递速度,使琴弓对振动的反馈更迅速、更清晰。
79.对实施例1-2制备的弓杆采用《gb/t 1932-2009木材干缩性测定方法》测得,两种弓杆材料的轴向干缩率为0,径向干缩率为0,体积干缩率为0,显著低于木材的0.1-0.5%的轴向干缩率、2-6%的径向干缩率和5-15%的体积干缩率。因此采用实施例1-2制备的弓杆,可在不进行任何表面处理的条件下有效解决琴弓在复杂温湿度环境下张力不稳定、长时间使用后性能和尺寸变化等问题。
80.尽管上面已经示出和描述了本发明的实施例,可以理解的是,上述实施例是示例性的,不能理解为对本发明的限制,本领域的普通技术人员在不脱离本发明的原理和宗旨的情况下在本发明的范围内可以对上述实施例进行变化、修改、替换和变型。