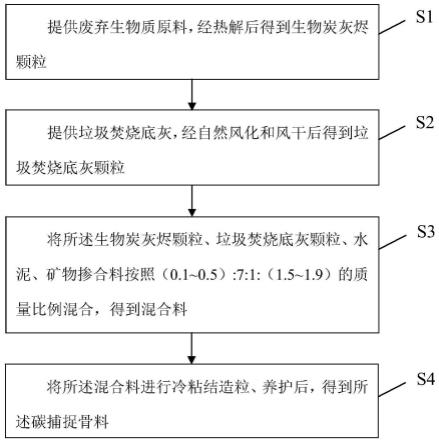
1.本发明涉及混凝土技术领域,尤其涉及一种以生物炭和底灰为原料的碳捕捉骨料及其制备方法。
背景技术:2.骨料是制备混凝土的基本原料,大约占混凝土总质量的三分之二左右,随着混凝土每年的使用量急剧上升,骨料的需求量也逐渐扩大。现有的骨料一般是天然骨料,如卵石、碎石和河砂等等,但是随着矿山河流等过度开采,骨料的自然资源越来越匮乏,导致天然骨料的使用成本升高。因此,找到代替天然砂石的人造骨料具有重要意义。
3.目前,由于二氧化碳的排放量的增加,使得全球变暖日益严重,出现了严重干旱、降雨模式变化、极端热浪、冰川融化和海平面上升等问题。建筑业是二氧化碳排放严重的行业之一,水泥行业的总排放量预计将占全球二氧化碳排放量的近8%。
4.城市垃圾随着城市化进程的不断推进而日益增多,垃圾焚烧过后剩余的灰渣中约80%为底灰,20%为飞灰。目前垃圾焚烧底灰的主要处理方式是填埋,但填埋需要占用大量的土地资源;且由于焚烧垃圾组成复杂,底灰中可能含有多种重金属、无机盐类物质,在垃圾焚烧底灰填埋或利用过程中,有害成分可能会在酸雨等因素作用下浸出从而导致土地环境污染。
5.所以,亟需提出一种二氧化碳捕捉和封存技术来减少大气中二氧化碳的浓度,并且寻找一种合理的垃圾焚烧底灰处理方式来减少土地污染和全球变暖等环境问题,并使得废物资源能够得到有效的重复利用。
技术实现要素:6.鉴于上述现有技术的不足,本发明的目的在于提供一种以生物炭和底灰为原料的碳捕捉骨料及其制备方法,旨在将生物炭和垃圾焚烧底灰作为制备成可用于混凝土原料的高强轻粗碳捕捉骨料来代替天然骨料,同时实现骨料力学性能的提升、二氧化碳的捕捉和封存及垃圾焚烧底灰的有效处理,保护环境且节约资源。
7.本发明的技术方案如下:
8.本发明的第一方面,提供一种以生物炭和底灰为原料的碳捕捉骨料的制备方法,其中,包括步骤:
9.提供废弃生物质原料,经热解后得到生物炭灰烬颗粒;
10.提供垃圾焚烧底灰,经自然风化和风干后得到垃圾焚烧底灰颗粒;
11.将所述生物炭灰烬颗粒、垃圾焚烧底灰颗粒、水泥、矿物掺合料按照(0.1~0.5):7:1:(1.5~1.9)的质量比例混合,得到混合料;
12.将所述混合料进行冷粘结造粒、养护后,得到所述碳捕捉骨料。
13.可选地,所述废弃生物质原料包括废木屑、作物残渣、生物粪便中的至少一种。
14.可选地,所述提供废弃生物质原料,经热解后得到生物炭灰烬颗粒的步骤具体包
括:提供废弃生物质原料,进行磨碎和筛分处理,使得所述废弃生物质原料的粒径为0.063~2mm,经热解后得到生物炭灰烬颗粒。
15.可选地,所述热解的温度为500~700℃,时间为2h。
16.可选地,所述生物炭灰烬颗粒的粒径小于2.36mm,所述垃圾焚烧底灰颗粒的粒径小于2.36mm。
17.可选地,所述提供垃圾焚烧底灰,经自然风化和风干后得到垃圾焚烧底灰颗粒的具体步骤包括:
18.提供垃圾焚烧底灰,进行磁选,然后经自然风化和风干28~35天、破碎、筛选后得到垃圾焚烧底灰颗粒。
19.可选地,所述水泥为硅酸盐水泥。
20.可选地,所述混合料经冷粘结造粒、养护后,得到所述碳捕捉骨料的步骤具体包括:
21.将所述混合料投入圆盘造粒机中进行冷粘结造粒后,得到粗骨料坯体,所述粗骨料坯体的粒径范围为4.75~16mm;
22.将所述粗骨料坯体在温度20
±
2℃,相对湿度大于95%的条件下养护至少28天后,得到所述碳捕捉骨料。
23.可选地,所述圆盘造粒机的圆盘倾角为45
°
~60
°
,圆盘直径为1m,边缘高为1.5cm,转速为35~55rpm。
24.本发明的第二方面,提供一种以生物炭和底灰为原料的碳捕捉骨料,其中,所述碳捕捉骨料采用本发明如上所述的制备方法制备而成。
25.有益效果:本发明提供了一种以生物炭和底灰为原料的碳捕捉骨料的制备方法,本发明将生物炭替代部分胶凝材料加入到骨料中,可以增强骨料的碳捕捉能力,并且减少骨料水化过程中的二氧化碳排放量,增强骨料的固碳能力;通过生物炭对垃圾焚烧底灰中有机和无机污染物的高吸附能力,能够大量的处理和稳定垃圾焚烧底灰,减少环境污染和土地资源使用压力;同时,生物炭能通过内养护作用促进水泥水化和水化产物的形成,并通过外部的碳化养护产生内外协同作用,加强碳化程度,从而增强骨料的力学性能和机械强度。利用生物炭和垃圾焚烧底灰颗粒多孔轻质的特点,使得制备得到的骨料的质量较轻,可以作为轻粗骨料使用。通过矿物掺合料与水泥水化形成的c-s-h凝胶、钙矾石等水化产物,能够很好的固定底灰中的cu、pb、cr等重金属和无机盐,绿色环保。利用矿物掺合料火山灰活性强的特点,与生物炭和垃圾焚烧底灰结合,并通过水泥作为粘接剂,使得制备得到的骨料具有较高的强度与较低的吸水率。通过本发明的制备方法制备得到的骨料,完全符合高强轻粗骨料的各项性能要求,能够替代天然轻骨料(浮石、页岩等)和烧结轻骨料(钢渣粉烧结骨料、陶粒等)作为轻骨料混凝土的原料,一方面减少了天然轻骨料的开采,能够有效的节约资源;另一方面,相较于需要上千摄氏度的烧结陶粒所消耗的能量,本发明通过冷粘结法制作骨料,耗能极低,污染少,在节约能源、环境保护等方面有着巨大的优势。本发明提供了一种新型的具有高经济效益和环保效益的碳捕捉骨料的生产方法、同时实现骨料力学性能的提升、二氧化碳的捕捉和封存及垃圾焚烧底灰的有效处理,保护环境且节约资源。
附图说明
26.图1为本发明实施例中以生物炭和底灰为原料的碳捕捉骨料的制备方法的流程示意图。
具体实施方式
27.本发明提供一种以生物炭和底灰为原料的碳捕捉骨料及其制备方法,为使本发明的目的、技术方案及效果更加清楚、明确,以下对本发明进一步详细说明。应当理解,此处所描述的具体实施例仅仅用以解释本发明,并不用于限定本发明。
28.除非另有定义,本文所使用的所有的技术术语和科学术语与属于本发明的技术领域的技术人员通常理解的含义相同。本文中在本发明的说明书中所使用的术语只是为了描述具体的实施方式的目的,不是旨在于限制本发明。
29.本发明实施例提供一种以生物炭和底灰为原料的碳捕捉骨料的制备方法,如图1所示,包括步骤:
30.s1、提供废弃生物质原料,经热解后得到生物炭灰烬颗粒;
31.s2、提供垃圾焚烧底灰,经自然风化和风干后得到垃圾焚烧底灰颗粒;
32.s3、将所述生物炭灰烬颗粒、垃圾焚烧底灰颗粒、水泥、矿物掺合料按照(0.1~0.5):7:1:(1.5~1.9)的质量比例混合,得到混合料;
33.s4、将所述混合料进行冷粘结造粒、养护后,得到所述碳捕捉骨料。
34.本发明将生物炭替代部分胶凝材料加入到骨料中,可以增强骨料的碳捕捉能力,并且减少骨料水化过程中的二氧化碳排放量,增强骨料的固碳能力;由于生物炭具有介孔结构、相对较高的表面积和丰富的官能团,能够吸附并固定住垃圾焚烧底灰中有机和无机污染物,能够大量的处理和稳定垃圾焚烧底灰,使得骨料的质量更轻,减少垃圾焚烧底灰带来的环境污染和填埋垃圾焚烧底灰所带来的土地资源使用压力;同时,生物炭能通过内养护作用促进水泥水化和水化产物的形成(具体地,生物炭的多孔结构可以将水吸附在孔隙内部,随后在熟化过程中通过释放水分和增加内部相对湿度来促进固化和改善水化,从而提高水泥水化的速度,使得水化程度提高),并通过外部的碳化养护产生内外协同作用,加强碳化程度,从而增强骨料的力学性能和机械强度。利用生物炭和垃圾焚烧底灰颗粒多孔轻质的特点,使得制备得到的骨料的质量较轻,可以作为轻粗骨料使用。通过矿物掺合料与水泥水化形成的c-s-h凝胶、钙矾石等水化产物,能够很好的固定底灰中的cu、pb、cr等重金属和无机盐,绿色环保。利用矿物掺合料火山灰活性强的特点,与生物炭和垃圾焚烧底灰结合,并通过水泥作为粘接剂,采用冷粘结造粒技术使得制备得到的骨料具有较高的强度与较低的吸水率。通过本发明的制备方法制备得到的骨料,完全符合高强轻粗骨料的各项性能要求,能够替代天然轻骨料(浮石、页岩等)和烧结轻骨料(钢渣粉烧结骨料、陶粒等)作为轻骨料混凝土的原料。
35.步骤s1中,在一种实施方式中,所述废弃生物质原料包括废木屑、作物残渣、生物粪便中的至少一种,但不限于此。由上述废弃生物质原料制备得到的生物炭具有介孔结构、相对较大的表面积和丰富的官能团,能够吸附并固定住垃圾焚烧底灰中有机和无机污染物,能够大量的处理和稳定垃圾焚烧底灰,使得骨料的质量更轻,可以将水吸附在孔隙内部,随后在熟化过程中通过释放水分和增加内部相对湿度来促进固化和改善水化,从而提
高水泥水化的速度,使得水化程度提高。
36.在一种实施方式中,所述提供废弃生物质原料,经热解后得到生物炭灰烬颗粒的步骤具体包括:提供废弃生物质原料,进行磨碎和筛分处理,使得所述废弃生物质原料的粒径为0.063~2mm,经热解后得到生物炭灰烬颗粒。使用较细的生物质原料可以提高生物炭灰烬颗粒的生产率。
37.在一种实施方式中,所述热解的温度为500~700℃,时间为2h。热解温度不宜过高或者过低,温度过高会使得生物炭灰烬颗粒孔隙过大,影响骨料的强度;温度过低则会导致生物炭灰烬颗粒的二氧化碳吸附能力减弱。500℃至700℃的温度范围内热解是生物炭灰烬颗粒作为骨料掺合料最合适的温度。具体实施时,将所述废弃生物质原料放置在马弗炉中,以10℃/min的升温速率,升温到500℃至700℃保持2h。优选地,所述热解的温度为600℃。
38.具体实施时,将制备得到的生物炭灰烬颗粒在100℃的水中浸泡0.5h至完全饱和,然后通过真空干燥过滤,获得饱和表面干燥条件,然后装入透明塑料袋中进行密封保存备用。
39.在一种实施方式中,所述生物炭灰烬颗粒的粒径小于2.36mm以使其适用于冷粘结造粒。
40.步骤s2中,在一种实施方式中,所述提供垃圾焚烧底灰,经自然风化和风干后得到垃圾焚烧底灰颗粒的具体步骤包括:
41.提供垃圾焚烧底灰,进行磁选,然后经自然风化和风干28~35天、破碎、筛选后得到垃圾焚烧底灰颗粒。垃圾焚烧底灰由于原料来源复杂,可能含有许多重金属元素,所以通过磁选可以将底灰中的金属回收利用,并有利于下一步的破碎。该过程具体可以将垃圾焚烧底灰放置在磁选机的传送带上,然后开启机器进行自动磁选。所述自然风化和风干同时进行,其目的是降低垃圾焚烧底灰里的重金属,自然风化和风干可在室外、防雨的环境中进行。优选地,所述自然风化和风干的时间为30天。
42.在一种实施方式中,所述垃圾焚烧底灰颗粒的粒径小于2.36mm。底灰中粒径较大的可以直接作为粗骨料应用于工程中,而小于2.36mm的颗粒较难处理,并且这一部分占底灰总量的50%以上。此外,冷粘结技术只适用于细颗粒物质的处理,因此选用粒径小于2.36mm的底灰颗粒。
43.步骤s3中,将所述生物炭灰烬颗粒、垃圾焚烧底灰颗粒、水泥、矿物掺合料按照(0.1~0.5):7:1:(1.5~1.9)的质量比例混合,得到混合料。生物炭灰烬颗粒掺量过高会导致孔隙率过大,骨料机械强度降低。在该比例下,制备得到的骨料生产效率较高,粒径分布均匀,强度较高;并且生物炭的二氧化碳吸附能力能够得到稳定发挥,同时还能大量的处理垃圾焚烧底灰,既降低了经济成本又减少处理垃圾焚烧底灰对环境带来的污染。优选地,将所述生物炭灰烬颗粒、垃圾焚烧底灰颗粒、水泥、矿物掺合料按照0.3:7:1:1.7的质量比例混合,得到混合料。
44.在一种实施方式中,所述矿物掺合料优选为矿粉。这是因为矿粉活性更高,能够很好的增强骨料的强度,降低骨料的吸水率。
45.在一种实施方式中,所述水泥为硅酸盐水泥,但不限于此。硅酸盐水泥的主要矿物组成是:硅酸三钙、硅酸二钙、铝酸三钙、铁铝酸四钙。硅酸三钙决定着硅酸盐水泥四个星期内的强度;硅酸二钙四星期后才发挥强度作用,约一年左右达到硅酸三钙四个星期的发挥
强度;铝酸三钙强度发挥较快,但强度低,其对硅酸盐水泥在1至3天或稍长时间内的强度起到一定的作用;铁铝酸四钙的强度发挥也较快,但强度低,对硅酸盐水泥的强度贡献小。
46.步骤s4中,采取冷粘结造粒技术进行造粒。冷粘结造粒技术具有能耗低,污染物排放少的优点,其相较于需要上千摄氏度的烧结陶粒等有着巨大的优势。利用冷粘结造粒技术可以循环利用固体废物,减少骨料制备过程二氧化碳排放量和固体废物填埋带来的环境负担,其产物可替代天然骨料,进而有效节约自然资源。因此,将冷粘结技术应用于生物炭和城市垃圾焚烧底灰的处理,能将生物炭和垃圾焚烧底灰制成骨料应用于混凝土中,可以实现废物利用,并且减少环境污染和土地资源的占用。
47.在一种实施方式中,所述混合料经冷粘结造粒、养护后,得到所述碳捕捉骨料的步骤具体包括:
48.s41、将所述混合料投入圆盘造粒机中进行冷粘结造粒后,得到粗骨料坯体,所述粗骨料坯体的粒径范围为4.75~16mm;
49.s42、将所述粗骨料坯体在温度20
±
2℃,相对湿度大于95%的条件下养护至少28天后,得到所述碳捕捉骨料。
50.步骤s41,4.75mm是粗骨料的界定粒径,一般认为大于4.75mm的骨料为粗骨料。而且,由于骨料是人造的,因此粒径越大骨料的强度反而呈下降趋势,且大于16mm的骨料强度下降较为明显。故而,选择粗骨料坯体粒径范围为4.75-16mm。
51.具体实施时,将混合料投入到圆盘造粒机中进行搅拌,在搅拌过程中对混合料均匀地喷洒水,总用水量与所述混合料的质量比为20%~22%(水与混合料的比例过高或过低都会很大程度的影响骨料的成型,导致无法造出合适的骨料或造粒的效率很低),并且保持合适的旋转速度,使得混合料在水分和离心作用下充分地聚合,最后得到粗骨料坯体。为了使得原料能更充分地混合,应先将生物炭和垃圾焚烧底灰等粉状材料放在圆盘上搅拌5-10分钟左右,待颜色均匀无明显颗粒时即可。具体实施时,将所述混合料投入圆盘造粒机前需要预留一部分混合料,并且在之后加水混合过程中,根据混合物的干湿度情况分量投入。通过分批投料可以有效地提高最终的骨料生产率和颗粒均匀度。
52.在一种实施方式中,所述圆盘造粒机的圆盘倾角为45
°
~60
°
,圆盘直径为1m,边缘高为1.5cm,转速为35~55rpm。
53.步骤s42中,还可以在不同温度下(20-80℃)水浴养护。水浴养护能够提供充足的水分,使得骨料内部水化充分,能明显增强骨料性能。其中,温度不宜过高或者过低;高温会导致骨料的水分蒸发,降低骨料性能;低温会抑制水化,进而影响骨料性能。
54.本发明实施例还提供一种以生物炭和底灰为原料的碳捕捉骨料,其中,所述碳捕捉骨料采用本发明实施例如上所述的制备方法制备而成。所述碳捕捉骨料的单颗粒抗压强度为2.44~2.70mpa,二氧化碳吸附性能6.4~7.6mmol/g,吸水率为14.25~16.32%。按照gb t 17431.1-轻集料及其试验方法第1部分中规定,可以认为所述碳捕捉骨料为轻集料,按照该规范,骨料的筒压强度达到高强轻粗集料的要求。相比市面上大多商品轻粗骨料,本发明所制作骨料强度更高,性能更好;吸水率较低,可以满足后续产品需求;并且具有极高经济效益和环保效益,将生物质废弃物和垃圾焚烧底灰重复利用,既降低了材料成本又减少了环境污染;同时,通过冷粘结法制作骨料,耗能极低,污染少,相较于需要上千摄氏度的烧结陶粒等有着巨大的优势。
55.下面通过具体的实施例对本发明作进一步地说明。
56.下述各实施例中,原材料中所用的生物炭灰烬颗粒,以粒径为0.063mm~2mm范围的废木屑为原料经高温热解制备;垃圾焚烧底灰为垃圾焚烧发电厂产出的底灰,经过磁选、自然风化和风干后,选取尺寸小于2.36mm的底灰颗粒;其他原料,如矿物掺合料(选用矿粉或钢渣粉)、硅酸盐水泥都来源于市售。原材料化合物组成如表1所示:
57.表1:原材料化合物组成
[0058][0059]
实施例1:
[0060]
将废木屑末过筛,得到粒径为0.063mm~2mm的废木屑末,然后将其放入马费炉中进行高温热解,升温速率为10℃/min,在升到600℃后保持该温度两小时,得到生物炭灰烬颗粒,冷却后将生物炭灰烬颗粒在100℃的水中浸泡0.5h后完全饱和,然后通过真空过滤干燥,获得饱和表面干燥条件;
[0061]
从垃圾焚烧发电厂收集的焚烧发电后残留的底灰,通过磁选机进行磁选后,进行湿润冷却处理,再将其放在自然条件下风化1个自然月并风干,然后进行筛分处理:在实验环境20℃
±
2℃的条件下,将底灰通过37.5mm、31.5mm、26.5mm、19mm、16mm、9.5mm、4.75mm与2.36mm的标准筛,选取2.36mm以下的底灰(含量占总体积50%以上),其余底灰磁选后破碎至2.36mm。将生物炭灰烬颗粒、矿粉、硅酸盐水泥与垃圾焚烧底灰以0.1:1.9:1:7的质量比例充分混合;
[0062]
将上述混合好的原料投入圆盘造粒机中造粒,获得4.75-16mm的轻粗骨料坯体;
[0063]
将上述造粒完成后的轻粗骨料坯体放置在温度20
±
2℃,相对湿度为95%的环境中养护28天,得到高强度碳捕捉骨料。
[0064]
经测试,得到的碳捕捉骨料的单颗粒抗压强度为2.47mpa,吸水率为15.43%,二氧化碳吸附性能6.4mmol/g。
[0065]
实施例2:
[0066]
将废木屑末过筛,得到粒径为0.063mm~2mm的废木屑末,然后将其放入马费炉中进行高温热解,升温速率为10℃/min,在升到600℃后保持该温度两小时,得到生物炭灰烬颗粒,冷却后将生物炭灰烬颗粒在100℃的水中浸泡0.5h后完全饱和,然后通过真空过滤干燥,获得饱和表面干燥条件。
[0067]
从垃圾焚烧发电厂收集的焚烧发电后残留的底灰,通过磁选机进行磁选后,进行湿润冷却处理,再将其放在自然条件下风化1个自然月并风干,然后进行筛分处理:在实验环境20℃
±
2℃的条件下,将底灰通过37.5mm、31.5mm、26.5mm、19mm、16mm、9.5mm、4.75mm与
2.36mm的标准筛,选取2.36mm以下的底灰(含量占总体积50%以上),其余底灰磁选后破碎至2.36mm。将生物炭灰烬颗粒、钢渣粉、硅酸盐水泥与垃圾焚烧底灰以0.3:1.7:1:7的质量比例充分混合;
[0068]
将上述混合好的原料投入圆盘造粒机中造粒,获得4.75-16mm的轻粗骨料坯体;
[0069]
将上述造粒完成后的轻粗骨料坯体放置在温度20
±
2℃,相对湿度为95%的环境中养护28天,得到高强度碳捕捉骨料。
[0070]
经测试,得到的碳捕捉骨料的单颗粒抗压强度为2.70mpa,吸水率为16.32%,二氧化碳吸附性能7.3mmol/g。
[0071]
实施例3:
[0072]
将废木屑末过筛,得到粒径为0.063mm~2mm的废木屑末,然后将其放入马费炉中进行高温热解,升温速率为10℃/min,在升到600℃后保持该温度两小时,得到生物炭灰烬颗粒,冷却后将生物炭灰烬颗粒在100℃的水中浸泡0.5h后完全饱和,然后通过真空过滤干燥,获得饱和表面干燥条件;
[0073]
从垃圾焚烧发电厂收集的焚烧发电后残留的底灰,通过磁选机进行磁选后,进行湿润冷却处理,再将其放在自然条件下风化1个自然月并风干,然后进行筛分处理:在实验环境20℃
±
2℃的条件下,将底灰通过37.5mm、31.5mm、26.5mm、19mm、16mm、9.5mm、4.75mm与2.36mm的标准筛,选取2.36mm以下的底灰(含量占总体积50%以上),其余底灰磁选后破碎至2.36mm。将生物炭灰烬颗粒、矿粉、硅酸盐水泥与垃圾焚烧底灰以0.5:1.5:1:7的质量比例充分混合;
[0074]
将上述混合好的原料投入圆盘造粒机中造粒,获得4.75-16mm的轻粗骨料坯体;
[0075]
将上述造粒完成后的轻粗骨料坯体放置在温度20
±
2℃,相对湿度为95%的环境中养护28天,得到高强度碳捕捉骨料。
[0076]
经测试,得到的碳捕捉骨料的单颗粒抗压强度为2.44mpa,吸水率为14.25%,二氧化碳吸附性能7.6mmol/g。
[0077]
综上所述,本发明提供了一种以生物炭和底灰为原料的碳捕捉骨料的制备方法,本发明将生物炭替代部分胶凝材料加入到骨料中,可以增强骨料的碳捕捉能力,并且减少骨料水化过程中的二氧化碳排放量,增强骨料的固碳能力;通过生物炭对垃圾焚烧底灰中有机和无机污染物的高吸附能力,能够大量的处理和稳定垃圾焚烧底灰,减少环境污染和土地资源使用压力;同时,生物炭能通过内养护作用促进水泥水化、提高水化产物的形成,并通过外部的碳化养护产生内外协同作用,加强碳化程度,从而增强骨料的力学性能和机械强度。利用生物炭和垃圾焚烧底灰颗粒多孔轻质的特点,使得制备得到的骨料的质量较轻,可以作为轻粗骨料使用。通过矿物掺合料与水泥水化形成的c-s-h凝胶、钙矾石等水化产物,能够很好的固定底灰中的cu、pb、cr等重金属和无机盐,绿色环保。利用矿物掺合料火山灰活性强的特点,与生物炭和垃圾焚烧底灰结合,并通过水泥作为粘接剂,使得制备得到的骨料具有较高的强度与较低的吸水率。通过本发明的制备方法制备得到的骨料,完全符合高强轻粗骨料的各项性能要求,能够替代天然轻骨料(浮石、页岩等)和烧结轻骨料(钢渣粉烧结骨料、陶粒等)作为轻骨料混凝土的原料,一方面减少了天然轻骨料的开采,能够有效的节约资源;另一方面,相较于需要上千摄氏度的烧结陶粒所消耗的能量,本发明通过冷粘结法制作骨料,耗能极低,污染少,在节约能源、环境保护等方面有着巨大的优势。本发明
提供了一种新型的具有高经济效益和环保效益的碳捕捉骨料的生产方法、同时实现骨料力学性能的提升、二氧化碳的捕捉和封存及垃圾焚烧底灰的有效处理,保护环境且节约资源。
[0078]
应当理解的是,本发明的应用不限于上述的举例,对本领域普通技术人员来说,可以根据上述说明加以改进或变换,所有这些改进和变换都应属于本发明所附权利要求的保护范围。