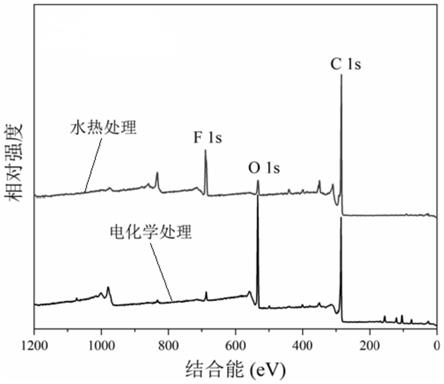
1.本发明涉及新材料技术领域,具体地说,涉及一种煤系石墨纯化同时制备氟化石墨烯的方法。
背景技术:2.我国煤系石墨矿产资源稀缺,查明资源储量仅约为5280万吨。然而,长期以来,石墨资源特别是煤系石墨资源并没有得到很好的重视,研究和开发程度比较低,普遍被当作煤来销售,或者被应用于低附加值产品,这就造成了煤系石墨矿资源的极大浪费。因此,对煤系石墨资源的高附加值应用研究迫在眉睫。
3.煤系石墨的提纯是制备所有石墨材料的基础,是制约煤系石墨材料发展的共性问题。煤系石墨只有经过纯化后才可以被广泛应用于各种领域,特别是在航空航天工业和核工业等都对所用石墨的纯度有很高的要求,甚至高达99.99%,石墨的纯度决定了其应用价值。然而,我国煤系石墨纯化技术相对落后,这和煤系石墨的原矿性质有很大的关系。煤系石墨中的杂质矿物部分以浸染状与石墨紧密结合在一起,或被包裹于集合体内部,增加了提纯难度,因此目前工业化的纯化技术,如浮选法普遍存在纯化效率低的问题,如高温法、碱酸法、氢氟酸法、氯化焙烧法等存在高能耗、高污染问题。
4.在煤系石墨提纯的基础上,对煤系石墨进行改性才能使煤系石墨具有更高端的市场前景以及更高的经济价值。相比于石墨烯、氧化石墨烯,石墨烷等材料,氟化石墨烯中由于氟原子的存在,使氟化石墨烯具有高的热稳定性(大于400℃)、高的介电强度(约10mv/cm)、高的c-f键结合能(530kj/mol)、大的带隙宽度(约3ev)、强的疏水性、低表面能等优异的物理化学性质。目前,氟化石墨烯的制备技术手段有很多,通常可以分为两大类,即“自下而上”法以及“自上而下”法。“自下而上”法是以石墨烯或者氧化石墨烯为原料制备得到氟化石墨烯,这种方法所用的原料石墨烯或者氧化石墨烯成本高,氟化试剂成本高,不易获得,毒性大。此外,若使用气相直接氟化制备石墨烯,该过程对反应设备要求很高,并存在一定危险性。“自上而下”法是以氟化石墨或石墨为原料,通过机械剥离或者液相剥离等制备得到氟化石墨烯,更适合批量化生产路线。相比于氟化石墨,选用石墨为原料直接制备氟化石墨烯,成本更低。以石墨为原料直接制备氟化石墨烯的相关研究报道较少,并且目前也存在一定的问题。2011年,bruna等人(文献:synthesis and properties of monolayer graphene oxyfluoride,j.mater.chem.,2011,21,18730)以石墨片为原料,采用50%的氢氟酸为电解液,通过电化学法制备得到了氟化氧化石墨烯,其产物f/o比在1左右。然而,该方法所用的氢氟酸质量分数较高,不是市面所售的40%的氢氟酸,此外,氢氟酸的使用对环境和人体都有害。2015年jeon等人(文献:fluorine:edge-fluorinated graphene nanoplatelets as high performance electrodes for dye-sensitized solar cells and lithium ion batteries.adv.funct.mater.2015,25,1170)选用石墨为原料,在机械球磨的过程中通入氩气/氟气的混合气体制备得到氟化石墨烯。然而在高速球磨的条件下引入氟气存在严重的安全问题,并且此方法得到的氟化石墨烯的氟含量仅为3%。2018年,
zhou等人(文献:electrochemically scalable production of fluorine-modified graphene for flexible and high-energy ionogel-based microsupercapacitors.j am chem soc,2018,140(26),8198-8205.)选用石墨作为阳极,以中性含氟无机盐nabf4、nh4bf4或kpf6做电解液,制备得到氟化石墨烯。然而,该方法制备得到的氟含量较低,仅为3%左右。
5.综上所述,现有的各种技术手段严重制约了煤系石墨的纯化和氟化石墨烯的制备,因此发展一种环境友好型的纯化煤系石墨技术以及安全、低成本、氟掺杂量可调的氟化石墨烯制备技术迫在眉睫。
技术实现要素:6.为解决上述技术问题,本发明的目的在于提供一种煤系石墨纯化同时制备氟化石墨烯的方法。该方法避免了使用强酸强碱等造成的环境污染问题,并且可以降低能耗;煤系石墨纯化的脱灰率可达到92.91%,在煤系石墨纯化的同时制备得到氟掺杂的氟化石墨烯,氟含量可达16.86%,并且氟化度可调。
7.为实现本发明的目的,本发明采用如下技术方案:
8.一种煤系石墨纯化同时制备氟化石墨烯的方法,其中,所述的方法包括如下步骤:
9.1)选用块状天然煤系石墨和惰性电极分别作为阳极和阴极,选用含氟无机盐溶液作为电解液,将两电极与工作电源相连,进行电化学剥离处理,得到剥离产物;
10.2)将步骤1)所得的剥离产物进行超声处理,取其悬浮液进行固液分离和烘干处理,得到部分纯化的氟化氧化石墨烯粉末;
11.3)将步骤2)所得的氟化氧化石墨烯粉末和nh4f溶液混合,进行水热处理,得到水热处理后的产物;
12.4)将步骤3)所得的水热处理后的产物自然降温后进行固液分离、水洗和烘干处理,得到纯化的氟化石墨烯。
13.本发明提供一种煤系石墨纯化同时制备氟化石墨烯的方法,该方法以块状天然煤系石墨原矿为原料,经过电化学剥离处理和水热处理后,即可得到纯化并且氟含量可调的氟化石墨烯。本发明中,块状天然煤系石墨原矿经过电化学剥离处理后,即可得到部分提纯和少量氟惨杂的氟化氧化石墨烯中间产物,该产物脱灰率可达50%以上,氟含量可达5%以上。中间产物进一步进行水热处理后,提纯效果和氟掺杂量可进一步提高,脱灰率可达92.91%,氟含量可达16.86%,并且氧含量显著降低至7.70%以下,即得到氟化石墨烯。此外,该方案可以实现对氟化石墨烯样品中氟含量的调控。
14.进一步地,步骤1)中,所述的含氟无机盐溶液的浓度为0.5~1.5m。
15.本发明中,含氟无机盐溶液的浓度对剥离速度具有一定的影响;当浓度低于0.5m时,剥离速率非常慢;而当浓度高于1.5m时,一方面,剥离速率较快,因此剥离产物层数较大,以纳米石墨片为主,少层石墨烯含量较少,另一方面,剥离后的石墨片中含氧官能团含量较低,氟含量虽有所升高,但主要是吸附上去的氟,不是c-f共价键。因此,本发明中含氟无机盐溶液的浓度选择0.5~1.5m。
16.本发明首先考察了电化学剥离处理过程中,不同浓度的电解液——含氟无机盐溶液对中间产物氟化氧化石墨烯的氟含量和含氧官能团含量的影响。然后考察了水热处理对
最终产物氟化石墨烯的氟含量和氧含量的影响。如图1和图2所示。一般来说,在电化学剥离处理过程中,当电解液的浓度降低时,中间产物氟化氧化石墨烯中的氟含量逐渐降低,含氧官能团含量逐渐增加。
17.进一步地,步骤1)中,所述的电化学剥离处理在10v电压条件下进行,处理时间为10~60min。
18.进一步地,所述的含氟无机盐溶液为nh4f、naf、kf、nabf4、nh4bf4溶液中的一种或几种,优选nh4f溶液。
19.本发明中,以含氟无机盐溶液如nh4f、naf、kf、nabf4、nh4bf4溶液中的一种或几种为电解液,优选以nh4f溶液为电解液。以nh4f溶液作为电解液,在10v电压条件下,对块状煤系石墨进行电化学剥离处理。在电场力的作用下,电解液中的氟离子会发生定向迁移,插入煤系石墨层间,形成以半离子键为主的c-f键。电解液中的水会失去电子形成羟基和氧自由基,这些活泼的自由基会使煤系石墨边缘发生氧化,生成羟基、环氧基、羧基等官能团。同时,伴随着氧气等气体的产生,煤系石墨会进一步发生膨胀,最终剥离制备得到氟化氧化石墨烯。另外,在电场力的作用下,由于石墨晶粒会发生膨胀,包裹于石墨集合体中的杂质矿物会暴露出来并与石墨晶粒分离,从而提高煤系石墨的纯度。随着电解液的浓度降低,产物氟化氧化石墨烯中的氟含量有所降低,这主要是由于随着电解液中氟离子浓度降低,插入煤系石墨层间的氟离子减少,形成的c-f键减少。另外,中间产物氟化氧化石墨烯中的含氧官能团含量显著增加,这主要是由于随着电解液浓度减少,电解液中水含量增加,水分解产生羟基和氧自由基增加,加强了对煤系石墨边缘的氧化作用。在10v工作电压下,随着电解液的浓度降低,产物的脱灰率增加,这主要是由于电解液浓度降低后,电化学剥离速率降低。相比于在高电解液浓度下,部分煤系石墨来不及充分膨胀就被剥落,在低电解液浓度条件下,电化学剥离可以使被包裹于石墨集合体中的杂质矿物充分暴露,并同石墨晶粒分离。
20.进一步地,步骤3)中,氟化氧化石墨烯粉末与nh4f溶液的固液比为0.2~2%。
21.进一步地,所述的nh4f溶液的浓度为0.2~2m,优选1~2m。
22.本发明中,水热处理过程中,nh4f溶液的浓度对产物中灰分的含量具有一定的影响,这是因为氟化铵在水热处理过程中可以生成氢氟酸,氢氟酸可以溶解杂质矿物。若nh4f溶液的浓度过低,会降低产物脱灰率。
23.进一步地,步骤3)中,所述的水热处理为在温度120~180℃下进行,反应时间为8~36h。优选地,所述的水热处理为在温度140~160℃下进行,反应时间为20~24h。
24.本发明中,选用块状天然煤系石墨为原料,经电化学剥离处理后,经超声处理、固液分离和烘干处理后再进行水热处理,水热处理过程中以nh4f溶液为介质,溶液浓度为0.2~2m,优选浓度为1~2m,反应温度为120~180℃,优选反应温度为140~160℃,反应时间为8~36h,优选为20~24h。经过水热处理后,产物中的氟含量和脱灰率显著提升,氧含量显著降低。这是由于在水热条件下,氟化氧化石墨烯中的一部分含氧官能团会发生还原,一部分含氧官能团会被氟原子取代形成c-f共价键。另外,在水热处理过程中,以sio2、al2o3、cao、mgo为主的杂质矿物会进一步除去,因此,产物中的氧含量会显著降低,氟含量增加。
25.进一步地,步骤2)中,所述的超声处理的功率为300~600w,处理时间为10~60min。
26.进一步地,步骤4)中,所述的自然降温为自然降温至25~30℃;步骤2)和步骤4)
中,所述的烘干处理的温度为50~80℃。
27.与现有技术相比,本发明具有如下优点:
28.本发明提供了一种块状煤系石墨原矿提纯同时制备氟化石墨烯的方法,脱灰率可达到92.91%,氟含量可达16.86%,并且氟化度可调。本发明选用块体状煤系石墨原矿为原料,首先避免了对石墨块体的破碎和磨矿处理,相比于其它纯化工艺,大大降低了能耗。通过调节电化学处理过程中电解液的浓度,可以实现对最终氟化石墨烯产物中氟含量的可控调节。另外,该方法不需要特殊的仪器或者气体,操作安全简单,成本低廉,有望实现大规模生产。
附图说明
29.附图用来提供对本发明的进一步理解,并且构成说明书的一部分,与本发明的实施例一起用于解释本发明,并不构成对本发明的限制。在附图中:
30.图1为随电解液浓度的变化,中间产物氟化氧化石墨烯中氟含量和含氧官能团含量的变化规律;
31.图2为对不同中间产物进行水热处理后,最终产物氟化石墨烯中氟含量和氧含量的变化规律;
32.图3为实施例1中电化学处理后和水热处理后的样品的xps图谱;
33.图4为实施例2中电化学处理后和水热处理后的样品的灰分含量;
34.图5为实施例3中氟化石墨烯产物的sem图;
35.图6为实施例4中电化学处理后和水热处理后的样品的raman图谱。
具体实施方式
36.下面将结合本发明实施例中的附图,对本发明实施例中的技术方案进行清楚、完整地描述,显然,所描述的实施例仅仅是本发明的一部分实施例,而不是全部的实施例。基于本发明中的实施例,本领域普通技术人员在没有做出创造性劳动的前提下所获得的所有其他实施例,都属于本发明保护的范围。
37.实施例1
38.本实施例提供了一种煤系石墨纯化同时制备氟化石墨烯的方法,制备方法如下:
39.(1)选用块状天然煤系石墨和箔电极分别作为阳极和阴极,选用0.5m nh4f溶液作为电解液,使用铜丝将两电极与工作电源相连,在10v电压条件下进行电化学剥离处理,处理时间为45min,得到剥离产物;
40.(2)将步骤(1)所得的剥离产物在300w功率下超声处理30min,静置10min取悬浮液通过抽滤方式进行固液分离,并在50℃条件下烘干得到氟化氧化石墨烯粉末;
41.(3)取0.1g氟化氧化石墨烯粉末与50ml的1mnh4f溶液共混,加入反应釜中进行水热处理,所述的水热处理为在温度140℃下进行,反应时间为24h,得到水热处理后的产物;
42.(4)将水热处理后的产物自然降温至25℃,之后,通过抽滤、水洗并在50℃条件下烘干得到氟化石墨烯粉末。
43.电化学处理后和水热处理后的样品的xps图谱如图3所示。
44.实施例2
45.本实施例提供了一种煤系石墨纯化同时制备氟化石墨烯的方法,制备方法如下:
46.(1)选用块状天然煤系石墨和钛合金电极分别作为阳极和阴极,选用1m nh4f溶液作为电解液,使用铜丝将两电极与工作电源相连,在10v电压条件下进行电化学剥离处理,处理时间为10min,得到剥离产物。
47.(2)将步骤(1)所得的剥离产物在600w功率下超声处理10min,静置30min取悬浮液通过抽滤方式进行固液分离,并在80℃条件下烘干得到氟化氧化石墨烯粉末;
48.(3)取1g氟化氧化石墨烯粉末与50ml的1mnh4f溶液共混,加入反应釜中进行水热处理,所述的水热处理为在温度140℃下进行,反应时间为24h,得到水热处理后的产物;
49.(4)将水热处理后的产物自然降温至30℃,之后,通过抽滤、水洗并在80℃条件下烘干得到氟化石墨烯粉末。
50.电化学处理后和水热处理后的样品的灰分含量如图4所示。
51.实施例3
52.本实施例提供了一种煤系石墨纯化同时制备氟化石墨烯的方法,制备方法如下:
53.(1)选用块状天然煤系石墨和钛合金电极分别作为阳极和阴极,选用1.5m nh4f溶液作为电解液,使用铜丝将两电极与工作电源相连,在10v电压条件下进行电化学剥离处理,处理时间为60min,得到剥离产物;
54.(2)将步骤(1)所得的剥离产物在400w功率下超声处理20min,之后在1000rpm/min条件下离心5min,得到悬浮液,并通过抽滤方式进行固液分离,并在60℃条件下烘干得到氟化氧化石墨烯粉末;
55.(3)取0.5g氟化氧化石墨烯粉末与50ml的2mnh4f溶液共混,加入反应釜中进行水热处理,所述的水热处理为在温度140℃下进行,反应时间为20h,得到水热处理后的产物;
56.(4)将水热处理后的产物自然降温至30℃后,通过抽滤、水洗并在50℃条件下烘干得到氟化石墨烯粉末。
57.氟化石墨烯产物的sem图如图5所示。
58.实施例4
59.本实施例提供了一种煤系石墨纯化同时制备氟化石墨烯的方法,制备方法中除步骤(3)中水热处理为在温度160℃下进行,反应时间为8h外,其余与实施例1一致。电化学处理后和水热处理后的样品的raman图谱如图6所示,表明经过水热处理,产物结构缺陷显著降低,含氧官能团发生了部分脱除。
60.实施例5
61.本实施例提供了一种煤系石墨纯化同时制备氟化石墨烯的方法,制备方法中除步骤(3)中水热处理为在温度120℃下进行,反应时间为36h外,其余与实施例1一致。
62.实施例6
63.本实施例提供了一种煤系石墨纯化同时制备氟化石墨烯的方法,制备方法如下:
64.(1)选用块状天然煤系石墨和箔电极分别作为阳极和阴极,选用0.8m naf溶液作为电解液,使用铜丝将两电极与工作电源相连,在10v电压条件下进行电化学剥离处理,处理时间为30min,得到剥离产物;
65.(2)将步骤(1)所得的剥离产物在450w功率下超声处理60min,静置10min取悬浮液通过抽滤方式进行固液分离,并在60℃条件下烘干得到氟化氧化石墨烯粉末;
66.(3)取0.1g氟化氧化石墨烯粉末与50ml的2mnh4f溶液共混,加入反应釜中进行水热处理,所述的水热处理为在温度180℃下进行,反应时间为30h,得到水热处理后的产物;
67.(4)将水热处理后的产物自然降温至28℃后,通过抽滤、水洗并在60℃条件下烘干得到氟化石墨烯粉末。
68.实施例7
69.本实施例提供了一种煤系石墨纯化同时制备氟化石墨烯的方法,制备方法如下:
70.(1)选用块状天然煤系石墨和箔电极分别作为阳极和阴极,选用1.2m kf溶液作为电解液,使用铜丝将两电极与工作电源相连,在10v电压条件下进行电化学剥离处理,处理时间为30min,得到剥离产物;
71.(2)将步骤(1)所得的剥离产物在500w功率下超声处理20min,静置10min取悬浮液通过抽滤方式进行固液分离,并在58℃条件下烘干得到氟化氧化石墨烯粉末;
72.(3)取0.1g氟化氧化石墨烯粉末与50ml的0.2mnh4f溶液共混,加入反应釜中进行水热处理,所述的水热处理为在温度150℃下进行,反应时间为22h,得到水热处理后的产物;
73.(4)将水热处理后的产物自然降温至26℃后,通过抽滤、水洗并在58℃条件下烘干得到氟化石墨烯粉末。
74.实施例8
75.本实施例提供了一种煤系石墨纯化同时制备氟化石墨烯的方法,制备方法如下:
76.(1)选用块状天然煤系石墨和箔电极分别作为阳极和阴极,选用0.8m nabf4溶液作为电解液,使用铜丝将两电极与工作电源相连,在10v电压条件下进行电化学剥离处理,处理时间为30min,得到剥离产物;
77.(2)将步骤(1)所得的剥离产物在450w功率下超声处理60min,静置10min取悬浮液通过抽滤方式进行固液分离,并在60℃条件下烘干得到氟化氧化石墨烯粉末;
78.(3)取0.1g氟化氧化石墨烯粉末与50ml的1mnh4f溶液共混,加入反应釜中进行水热处理,所述的水热处理为在温度180℃下进行,反应时间为30h,得到水热处理后的产物;
79.(4)将水热处理后的产物自然降温至28℃后,通过抽滤、水洗并在60℃条件下烘干得到氟化石墨烯粉末。
80.实施例9
81.本实施例提供了一种煤系石墨纯化同时制备氟化石墨烯的方法,制备方法如下:
82.(1)选用块状天然煤系石墨和箔电极分别作为阳极和阴极,选用0.8m nh4bf4溶液作为电解液,使用铜丝将两电极与工作电源相连,在10v电压条件下进行电化学剥离处理,处理时间为30min,得到剥离产物;
83.(2)将步骤(1)所得的剥离产物在480w功率下超声处理25min,静置10min取悬浮液通过抽滤方式进行固液分离,并在60℃条件下烘干得到氟化氧化石墨烯粉末;
84.(3)取0.1g氟化氧化石墨烯粉末与50ml的1mnh4f溶液共混,加入反应釜中进行水热处理,所述的水热处理为在温度180℃下进行,反应时间为30h,得到水热处理后的产物;
85.(4)将水热处理后的产物自然降温至28℃后,通过抽滤、水洗并在60℃条件下烘干得到氟化石墨烯粉末。
86.对比例1
87.本对比例选用天然煤系石墨粉末为原料,对其直接进行水热处理,具体如下:
88.(1)取0.1g煤系石墨粉末与50ml的1mnh4f溶液共混,并加入反应釜中进行水热处理,水热处理条件同实施例1,具体为:水热处理在温度140℃下进行,反应时间为24h,得到水热处理后的产物;
89.(2)将水热处理后的产物自然降温至25℃,之后,通过抽滤、水洗并在50℃条件下烘干得到氟化石墨烯粉末。
90.对比例2
91.本对比例选用天然煤系石墨粉末为原料,对其直接进行水热处理,具体为:
92.(1)取1g煤系石墨粉末与50ml的1.5mnh4f溶液共混,并加入反应釜中进行水热处理,水热处理条件同实施例2,具体为:水热处理在温度140℃下进行,反应时间为24h,得到水热处理后的产物;
93.(2)将水热处理后的产物自然降温至30℃,之后,通过抽滤、水洗并在80℃条件下烘干得到氟化石墨烯粉末。
94.对比例3
95.本对比例选用块状天然煤系石墨为原料,仅进行电化学处理,电化学处理条件同实施例1,具体为:
96.(1)选用块状天然煤系石墨和箔电极分别作为阳极和阴极,选用0.5m nh4f溶液作为电解液,使用铜丝将两电极与工作电源相连,在10v电压条件下进行电化学剥离处理,处理时间为45min,得到剥离产物;
97.(2)将步骤(1)所得的剥离产物在300w功率下超声处理30min,静置10min取悬浮液通过抽滤方式进行固液分离,并在50℃条件下烘干得到氟化石墨烯粉末。
98.对比例4
99.本对比例选用块状天然煤系石墨为原料,仅进行电化学处理,电化学处理条件同实施例3,具体为:
100.(1)选用块状天然煤系石墨和钛合金电极分别作为阳极和阴极,选用1.5m nh4f溶液作为电解液,使用铜丝将两电极与工作电源相连,在10v电压条件下进行电化学剥离处理,处理时间为60min,得到剥离产物;
101.(2)将步骤(1)所得的剥离产物在400w功率下超声处理20min,之后在1000rpm/min条件下离心5min,得到悬浮液,并通过抽滤方式进行固液分离,并在60℃条件下烘干得到氟化石墨烯粉末。
102.试验例1
103.本试验例考察了本发明实施例和对比例得到的最终产物的脱灰率、氟含量和氧含量。其中脱灰率通过热重法确定,氟含量和氧含量通过x射线光电子能谱测定。
104.结果见表1所示:
105.表1
106.产物脱灰率(%)氟含量(%)氧含量(%)实施例192.9116.865.40实施例283.5012.106.80实施例389.918.897.70
实施例486.1914.775.80实施例586.8315.775.60实施例687.2215.915.23实施例780.1712.897.49实施例887.2016.335.17实施例984.4315.326.91对比例160.211.719.72对比例273.531.6310.11对比例333.912.0232.30对比例439.803.5223.70
107.从上述试验结果可以看出,产物的脱灰率较高,采用本发明方法可以实现对煤系石墨的提纯。产物中氟含量高,氧含量低,采用本方法可以制备得到氟化石墨烯。
108.试验例2
109.本试验例考察了电化学剥离处理过程中,电解液的浓度对中间产物氟化氧化石墨烯中氟含量和含氧官能团含量的影响以及对最终产物氟化石墨烯中氟含量和氧含量的影响。
110.试验方法:参照实施例1,所不同的改变电解液nh4f溶液的浓度,其他同实施例1。考察不同浓度的电解液对中间产物氟化氧化石墨烯中的氟含量和含氧官能团含量的影响以及最终产物氟化石墨烯中的氟含量和氧含量的影响,其中氟含量、含氧官能团含量和氧含量通过x射线光电子能谱测定。
111.试验结果如图1和图2所示。
112.结果表明:通过改变电化学剥离处理过程中电解液的浓度,可以调控水热处理后的最终产物氟化石墨烯的氟含量。一般来说,在电化学剥离处理过程中,随着电解液的浓度的降低,中间产物氟化氧化石墨烯中的含氧官能团含量会增加,因此,经过水热处理后的最终产物氟化石墨烯的碳氟键也会增加,产物氟含量逐渐增加。
113.最后应说明的是:以上所述仅为本发明的优选实施例而已,并不用于限制本发明,尽管参照前述实施例对本发明进行了详细的说明,对于本领域的技术人员来说,其依然可以对前述各实施例所记载的技术方案进行修改,或者对其中部分技术特征进行等同替换。凡在本发明的精神和原则之内,所作的任何修改、等同替换、改进等,均应包含在本发明的保护范围之内。