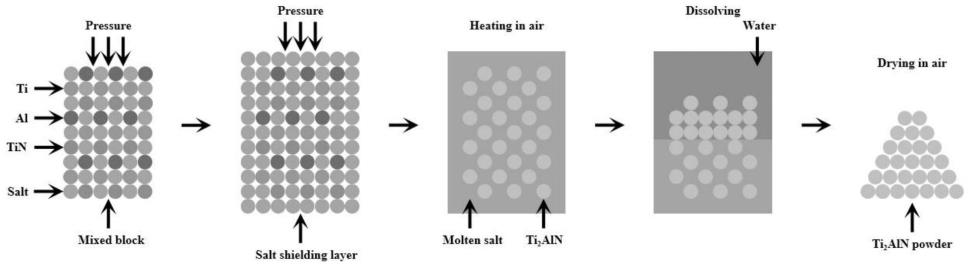
一种max相粉体的低温无保护气氛合成方法
技术领域
1.本发明涉及一种max相粉体的低温无保护气氛合成方法,属于材料合成与制备领域。
背景技术:2.max相材料为一类新型三元层状化合物,由m、a、x三种元素组成,分子通式为m
n+1
axn,(m:过渡金属元素,a:主族元素,x:碳或氮,n=1,2,3,...),max相兼具金属材料(优异的导电、导热性,机械加工性能,抗热震性能等)与陶瓷材料(高模量、耐高温、抗氧化性、耐腐蚀性等)的优良性能。近二十年来,该领域在国际上研究活跃,进展显著,其在能源与环境领域的潜在应用已得到广泛认可。
3.目前,max相材料的合成方法主要有无压烧结(ps)、热压烧结(hp)、热等静压烧结(hip)、放电等离子体烧结(sps)等,其中ps方法主要用于合成max相粉体,而hp、hip、sps等方法主要用于制备max相块体材料。采用ps、hp、hip方法时,需在高于1400℃的条件下才能合成高纯度max相,且加热时需通入ar等惰性气氛以防止氧化;对于hp、hip方法而言还需要使用模具并施加机械或气体压力,进一步提高生产成本;sps方法虽可在相对较低的温度下合成高纯度max相材料,但设备昂贵、合成产量低。max相材料的应用除少量使用块体材料制备零件外,更多的是以粉体的形式作为原料制备各种复合材料以及二维mx烯材料等,而除ps方法以外,上述合成路线如果要得到max相粉体,需要将合成的块体材料破碎、研磨,导致产量不足,粒径不均,成本居高不下。综上,已有方法的这些缺点限制高纯度max相粉体的低成本、大批量生产以及工业化应用。
技术实现要素:4.本发明的目的在于提供一种max相粉体的低温无保护气氛合成方法,包含以下步骤:(1)原料称重、混合;(2)加入低熔点盐并混合均匀;(3)混合物压制成坯体;(4)混合物坯体包覆盐壳;(5)空气中加热、保温、冷却;(6)盐溶于水;(7)固液分离;(8)粉体清洗、干燥。
5.进一步地,所选max相包括但不限于ti2alc、ti2aln、ti3sic2、cr2alc、v2alc。
6.进一步地,步骤(1)中,所选原料包括但不限于m、a、mx(m代表过渡金属元素,例如ti;a代表主族元素,例如al、si、sn;x代表c或n元素),其摩尔比遵循max相分子通式m
n+1
axn,即质量比约为am:aa:n
·amx
,其中,a
x
表示元素或化合物x的相对原子质量。
7.进一步地,步骤(2)中,所选低熔点盐包括但不限于(na,k)cl、kbr、licl,其熔点低于原料m、a、mx的最低氧化温度与熔点,原料与盐的质量比范围为1:0.5~1:5,高温下盐熔体为原料成分扩散提供介质,并基于旋节分解原理控制合成粉末粒径;所述原料与盐的混合方式为球磨。
8.进一步地,步骤(4)中,盐壳厚度为2~8mm,坯体四周均匀包覆,以保证盐壳在原料氧化或熔化前及时熔融,在坯体表面形成致密包覆层以隔绝空气中的氧。
9.进一步地,步骤(5)中,所用加热设备包括但不限于马弗炉、管式炉,升温速率为2
~10℃/min,加热温度为650~1250℃,保温时间为0.5~5h,降温方式包括但不限于随炉冷却。
10.本发明的有益效果:
11.本发明提供一种max相粉体的低温无保护气氛合成方法,不仅能显著降低max相粉体的合成温度,而且无需使用保护性气体或真空,在空气环境中即可合成高纯度max相粉体,从而显著降低max相粉体的生产成本。此外,本发明还可通过调整熔盐比例、加热温度和保温时间,改变所合成max相粉体的粒度,达到粉体形貌控制的目的。
附图说明
12.图1:max相粉体低温无保护气氛合成工艺流程图;
13.图2:实施例1所合成的ti2aln粉体照片;
14.图3:实施例1所合成的ti2aln粉体xrd图;
15.图4:实施例1所合成的ti2aln粉体sem图。
具体实施方式
16.下面结合附图与具体实施例,对本发明做进一步说明,但本发明的保护范围并且不限于所述内容。
17.实施例1
18.不同烧结温度条件下合成ti2aln粉体:
19.(1)选取原料ti、al、tin,质量比为1.8:1.0:2.3,低能球磨2~6h混合均匀;
20.(2)选取低熔点共晶盐(na,k)cl(质量比为nacl:kcl=1:1,熔点为650℃),与原料混合物(ti-al-tin)以质量比为1:1的比例混合,低能球磨2~6h混合均匀;
21.(3)将ti-al-tin与(na,k)cl的混合物装填到模具中,用压力机以40~80kg/cm2的载荷压制成坯体,保持载荷5~15min,脱模后放入干燥箱中,在45~60℃的温度下干燥2~6h;
22.(4)选取尺寸略大的模具,用适量(na,k)cl铺满模具底部,再放入干燥后的坯体,用适量(na,k)cl填满模具内剩余空间,同时,用压力机以40~80kg/cm2的载荷压制成包覆盐壳的坯体,盐壳厚度为2~8mm,保持载荷5~15min,脱模后放入干燥箱中,在45~60℃的温度下干燥2~6h;
23.(5)将包覆盐壳的坯体放入坩埚,在马弗炉中以5~10℃/min的升温速率加热至700~1000℃,并保温2h,再随炉冷却至室温;
24.(6)将烧结后的粉料块放入沸水中反复搅拌,直至料块表面和内部的盐完全溶解,通过静置或离心沉淀,使合成的粉体与盐溶液分离,滤去溶液,并反复用水清洗粉体,直至用agno3检测清洗液中的cl-时完全无法检出;
25.(7)将清洗后的粉体放入干燥箱中,在45~60℃的温度下干燥6~12h,待完全干燥后,放入研钵中充分研磨;
26.(8)在上述合成条件下,所合成的ti2aln粉的纯度为96.8~97.5%,原子比为ti:al:n=2.1:1.0:1.1,粉体呈现均匀的层状结构特征,平均粒径为20~28μm。
27.本实施例所用ti2aln粉体低温无保护气氛合成工艺流程图如图1所示;所合成
ti2aln粉体的实物照片如图2所示;ti2aln粉体的xrd图如图3所示;sem形貌图如图4所示。
28.实施例2
29.不同保温时间条件下合成ti2aln粉体:
30.(1)选取原料ti、al、tin,质量比为1.8:1.0:2.3,低能球磨2~6h混合均匀;
31.(2)选取低熔点共晶盐(na,k)cl(质量比为nacl:kcl=1:1,熔点为650℃),与原料混合物(ti-al-tin)以质量比为1:1的比例混合,低能球磨2~6h混合均匀;
32.(3)将ti-al-tin与(na,k)cl的混合物装填到模具中,用压力机以40~80kg/cm2的载荷压制成坯体,保持载荷5~15min,脱模后放入干燥箱中,在45~60℃的温度下干燥2~6h;
33.(4)选取尺寸略大的模具,用适量(na,k)cl铺满模具底部,再放入干燥后的坯体,用适量(na,k)cl填满模具内剩余空间,同时,用压力机以40~80kg/cm2的载荷压制成包覆盐壳的坯体,盐壳厚度为2~8mm,保持载荷5~15min,脱模后放入干燥箱中,在45~60℃的温度下干燥2~6h;
34.(5)将包覆盐壳的坯体放入坩埚,在马弗炉中以5~10℃/min的升温速率加热至700℃,并保温0.5~5h,再随炉冷却至室温;
35.(6)将烧结后的粉料块放入沸水中反复搅拌,直至料块表面和内部的盐完全溶解,通过静置或离心沉淀,使合成的粉体与盐溶液分离,滤去溶液,并反复用水清洗粉体,直至用agno3检测清洗液中的cl-时完全无法检出;
36.(7)将清洗后的粉体放入干燥箱中,在45~60℃的温度下干燥6~12h,待完全干燥后,放入研钵中充分研磨;
37.(8)在上述合成条件下,所合成的ti2aln粉的纯度为97.0~97.9%,原子比为ti:al:n=2.0:1.0:1.0,粉体呈现均匀的层状结构特征,平均粒径为18~25μm。
38.实施例3
39.不同盐含量条件下合成ti2aln粉体:
40.(1)选取原料ti、al、tin,质量比为1.8:1.0:2.3,低能球磨2~6h混合均匀;
41.(2)选取低熔点共晶盐(na,k)cl(质量比为nacl:kcl=1:1,熔点为650℃),与原料混合物(ti-al-tin)以质量比为1:0.5~1:5的比例混合,低能球磨2~6h混合均匀;
42.(3)将ti-al-tin与(na,k)cl的混合物装填到模具中,用压力机以40~80kg/cm2的载荷压制成坯体,保持载荷5~15min,脱模后放入干燥箱中,在45~60℃的温度下干燥2~6h;
43.(4)选取尺寸略大的模具,用适量(na,k)cl铺满模具底部,再放入干燥后的坯体,用适量(na,k)cl填满模具内剩余空间,同时,用压力机以40~80kg/cm2的载荷压制成包覆盐壳的坯体,盐壳厚度为2~8mm,保持载荷5~15min,脱模后放入干燥箱中,在45~60℃的温度下干燥2~6h;
44.(5)将包覆盐壳的坯体放入坩埚,在管式炉中以2~10℃/min的升温速率加热至700℃,并保温2h,再随炉冷却至室温;
45.(6)将烧结后的粉料块放入沸水中反复搅拌,直至料块表面和内部的盐完全溶解,通过静置或离心沉淀,使合成的粉体与盐溶液分离,滤去溶液,并反复用水清洗粉体,直至用agno3检测清洗液中的cl-时完全无法检出;
46.(7)将清洗后的粉体放入干燥箱中,在45~60℃的温度下干燥6~12h,待完全干燥后,放入研钵中充分研磨;
47.(8)在上述合成条件下,所合成的ti2aln粉的纯度为97.0~97.5%,原子比为ti:al:n=2.1:1.2:1.0,粉体呈现均匀的层状结构特征,平均粒径为12~21μm。
48.实施例4
49.合成ti2alc粉体:
50.(1)选取原料ti、al、tic,质量比为1.8:1.0:2.2,低能球磨2~6h混合均匀;
51.(2)选取低熔点共晶盐(na,k)cl(质量比为nacl:kcl=1:1,熔点为650℃),与原料混合物(ti-al-tic)以质量比为1:1的比例混合,滚筒球磨2~6h混合均匀;
52.(3)将ti-al-tic与(na,k)cl的混合物装填到模具中,用压力机以40~80kg/cm2的载荷压制成坯体,保持载荷5~15min,脱模后放入干燥箱中,在45~60℃的温度下干燥2~6h;
53.(4)选取尺寸略大的模具,用适量(na,k)cl铺满模具底部,再放入干燥后的坯体,用适量(na,k)cl填满模具内剩余空间,同时,用压力机以40~80kg/cm2的载荷压制成包覆盐壳的坯体,盐壳厚度为2~8mm,保持载荷5~15min,脱模后放入干燥箱中,在45~60℃的温度下干燥2~6h;
54.(5)将包覆盐壳的坯体放入坩埚,在马弗炉中以5~10℃/min的升温速率加热至700℃,并保温2h,再随炉冷却至室温;
55.(6)将烧结后的粉料块放入沸水中反复搅拌,直至料块表面和内部的盐完全溶解,通过静置或离心沉淀,使合成的粉体与盐溶液分离,滤去溶液,并反复用水清洗粉体,直至用agno3检测清洗液中的cl-时完全无法检出;
56.(7)将清洗后的粉体放入干燥箱中,在45~60℃的温度下干燥6~12h,待完全干燥后,放入研钵中充分研磨;
57.(8)在上述合成条件下,所合成的ti2alc粉的纯度为97.2~97.4%,原子比为ti:al:c=2.0:1.0:1.1,粉体呈现均匀的层状结构特征,平均粒径为20~25μm。