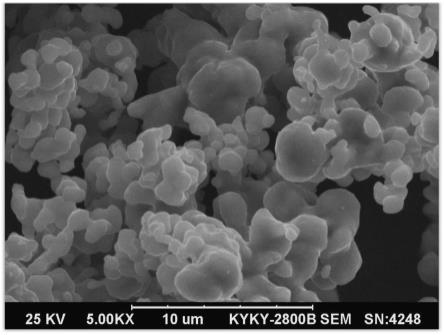
1.本发明涉及电池领域,具体而言,涉及一种磷酸铁的制备方法、磷酸铁锂的制备方法。
背景技术:2.硫酸渣作为炼铁等原料已有100多年的历史,每年排放硫酸渣的量可达300多万吨,其中只有100多万吨得到了合理的利用,其余都排入环境中。堆积则侵占农田,污染土地;排入江河则污染水体。
3.当前硫酸渣综合利用的方法有很多,绝大部分硫酸渣采用“分选铁精矿余渣制砖”。作为炼铁原料,铁品位不低于25%的硫酸渣,从中分选铁精矿都有一定的经济价值,分选工艺与一般铁矿分选工艺差别不大,可根据渣中铁矿物比磁化系数的高低分别采用重力分选或磁选方法来进行。经济分析如下:若每年硫酸渣入选量为2万吨,设从铁品位30的渣中分选出品位60的精矿(品位≥60%的铁精矿可直接用于炼铁),按产率40%计算,可年产铁精矿8000吨,品位60的精矿(硫含量≤0.5)每吨售价110元,每吨生产成本70元,吨利润40元,年利润32万元。建一座选铁车间的总投资50万元左右,生产不到两年,可全部收回投资。分选铁精矿后尚剩有12000吨余渣,可用于制砖,硫酸渣本身没有胶结能力,但其中含有sio2与ai2o3等活性物质。
4.硫酸渣可作为烧结矿的原料,主要利用其中的含铁成分,降低烧结原料的生产成本。但它的成球性差,吸水率高,影响烧结生产率。此外含硫较高并含有cu、pb和zn等有害元素,影响烧结矿质量。烧结料中硫酸渣的配加量一般在10%以下。将硫酸渣进行处理,增加细度,提高其含铁量,降低含硫量,可作为球团矿的原料。某些现有技术采用高温氯化法工艺,将渣中所含金属进行氯化,然后用湿法冶金浸取金、银等贵金属,并脱除渣中的有害金属。
5.随着磷酸铁锂的发展,廉价的铁源成为关注的焦点,钛白粉副产物的硫酸亚铁晶体,价格一路上涨,目前价格已经涨到350元/吨,且运费大约70-90元/吨,并且随着铁锂产能的扩大,硫酸亚铁晶体价格上涨越来越高,且难以买到。所以开发新的价格低廉,廉价易得的铁源迫在眉睫。硫酸渣每年的产生量很大,达到几百万吨,且循环利用率低。
6.有鉴于此,特提出本发明。
技术实现要素:7.本发明的一个方面,涉及一种磷酸铁的制备方法,包括以下步骤:
8.将硫酸渣和亚硫酸盐在水中混匀,得到第一混合体系;向所述第一混合体系中加入磷酸和缓冲剂后进行浸出反应;对所述浸出反应后得到的浆料进行第一固液分离,得到第一滤液和第一滤渣;向所述第一滤液中通入空气后进行第一搅拌反应;对所述第一搅拌反应后得到的浆料进行第二固液分离,得到第二滤液和第二滤渣;所述第二滤渣进行煅烧;
9.其中,所述浸出反应的压力为0.25~0.5mpa;
10.所述浸出反应的反应体系的ph为1.5~3;
11.所述缓冲剂包括磷酸二氢钠和/或磷酸氢二钠。
12.所述的磷酸铁的制备方法,能够利用硫酸渣中的铁源,从而降低磷酸铁的制备成本,方法简单,易操作。
13.本发明的另一个方面,还涉及一种磷酸铁锂的制备方法,包括所述的磷酸铁的制备方法。
14.所述的磷酸铁锂的制备方法,方法简单,成本低。
15.与现有技术相比,本发明的有益效果为:
16.(1)本发明所提供的磷酸铁的制备方法,巧妙的采用高压还原浸出,将难以被酸溶解的四氧化三铁和氧化铁红溶解出来,同时采用磷酸和磷酸二氢钠的混合溶液来浸出被还原后的铁盐,得到磷酸二氢亚铁溶液,同时在较高的ph下,可以避免部分的铝、钙、镁等被溶解掉,从而大大的提高铁的浸出率,将浸出的铁用于磷酸铁的制备。
17.(2)本发明所提供的磷酸铁的制备方法,还可以回收硫酸渣中的钴、铜、金、银以及硫酸钠等,大大提高了硫酸渣的附加值,提高硫酸渣的资源化利用率。
18.(3)本发明所提供的磷酸铁锂的制备方法,方法简单,成本低。
附图说明
19.为了更清楚地说明本发明具体实施方式或现有技术中的技术方案,下面将对具体实施方式或现有技术描述中所需要使用的附图作简单地介绍,显而易见地,下面描述中的附图是本发明的一些实施方式,对于本领域普通技术人员来讲,在不付出创造性劳动的前提下,还可以根据这些附图获得其他的附图。
20.图1为本发明实施例提供的扫描电子显微镜观察磷酸铁的结果图;
21.图2为本发明又一实施例提供的扫描电子显微镜观察磷酸铁的结果图;
22.图3为本发明又一实施例提供的磷酸铁的粒度分布结果图。
具体实施方式
23.下面将结合附图和具体实施方式对本发明的技术方案进行清楚、完整地描述,但是本领域技术人员将会理解,下列所描述的实施例是本发明一部分实施例,而不是全部的实施例,仅用于说明本发明,而不应视为限制本发明的范围。基于本发明中的实施例,本领域普通技术人员在没有做出创造性劳动前提下所获得的所有其他实施例,都属于本发明保护的范围。实施例中未注明具体条件者,按照常规条件或制造商建议的条件进行。所用试剂或仪器未注明生产厂商者,均为可以通过市售购买获得的常规产品。
24.本发明的一个方面,涉及一种磷酸铁的制备方法,包括以下步骤:
25.将硫酸渣和亚硫酸盐在水中混匀,得到第一混合体系;向所述第一混合体系中加入磷酸和缓冲剂后进行浸出反应;对所述浸出反应后得到的浆料进行第一固液分离,得到第一滤液和第一滤渣;向所述第一滤液中通入空气后进行第一搅拌反应;对所述第一搅拌反应后得到的浆料进行第二固液分离,得到第二滤液和第二滤渣;所述第二滤渣进行煅烧;
26.其中,所述浸出反应的压力为0.25~0.5mpa;
27.所述浸出反应的反应体系的ph为1.5~3;
28.所述缓冲剂包括磷酸二氢钠和/或磷酸氢二钠。
29.在一些具体的实施方式中,所述浸出反应的压力例如可以为,但不限于0.25mpa、0.3mpa、0.35mpa、0.4mpa、0.45mpa或0.5mpa。
30.在一些具体的实施方式中,所述浸出反应的反应体系的ph例如可以为,但不限于1.5、2、2.5或3。
31.硫酸渣是指黄铁矿制硫酸工艺的残渣,又称黄铁矿烘渣或烧渣。化工废渣的一种。由于渣中含铁,可以作为钢铁冶金原料使用。硫酸渣含铁的氧化物(fe2o3、fe3o4、feo)的含量约为20~50%,二氧化硅的含量约为15~65%,三氧化二铝的含量约为10%,氧化钙的含量约为5%,氧化镁的含量在5%以下,硫的含量约为1~2%,一般还含有铜、钴、铅、锌、金和银。其中,四氧化三铁在硫酸的钝化作用下形成致密的四氧化三铁。
32.本发明提供的磷酸铁的制备方法,巧妙的采用高压还原浸出,将难以被酸溶解的四氧化三铁和氧化铁红溶解出来,同时采用磷酸和磷酸二氢钠的混合溶液来浸出被还原后的铁盐,得到磷酸二氢亚铁溶液,同时浸出反应的反应体系的ph控制在1.5~3,可以避免部分的铝、钙、镁等被溶解掉,从而提高铁的浸出率。
33.磷酸能够提供氢离子,同时磷酸二氢钠和磷酸氢二钠为缓冲溶液,可以在磷酸根的氢离子消耗后,补充氢离子,同时避免溶液的ph太低,造成其他杂质被浸出。
34.本发明的浸出反应在特定的浸出条件下进行,使得浸出率大幅度提高,同时加入了亚硫酸盐,可以在酸性环境下,产生还原性,使得三价铁离子被还原为二价铁,进一步提高了浸出率,最终得到磷酸二氢亚铁溶液。同时在弱酸性环境下以及存在大量磷酸二氢根的环境里面,生成得到磷酸二氢亚铁溶液。
35.优选地,所述亚硫酸盐包括亚硫酸钠和/或亚硫酸钾。
36.优选地,所述硫酸渣的粒径为80~120目。
37.在一些具体的实施方式中,所述硫酸渣的粒径例如可以为,但不限于80目、90目、100目、110目或120目。
38.优选地,所述硫酸渣中的铁元素与所述亚硫酸盐、所述磷酸、所述缓冲剂的摩尔比为1:(0.35~0.4):(0.25~0.3):(1.7~1.75)。
39.在一些具体的实施方式中,所述硫酸渣中的铁元素与所述亚硫酸盐、所述磷酸、所述缓冲剂的摩尔比例如可以为,但不限于1:0.35:0.25:1.7、1:0.37:0.28:1.173或1:0.4:0.3:1.75。
40.优选地,所述磷酸和所述缓冲剂在15~30min(例如15min、20min、25min或30min)内加入到所述第一混合体系中。
41.优选地,每小时向所述第一滤液中通入空气的量与所述第一滤液中亚铁离子的比例为(8~12)m3:(28~32)mol。
42.在一些具体的实施方式中,每小时向所述第一滤液中通入空气的量与所述第一滤液中亚铁离子的比例例如可以为,但不限于8:28、10:30或12:32。
43.优选地,所述浸出反应的温度为130~170℃。
44.在一些具体的实施方式中,所述浸出反应的温度例如可以为,但不限于130℃、140℃、150℃、160℃或170℃。
45.优选地,所述浸出反应的时间为1~2h。
46.在一些具体的实施方式中,所述浸出反应的时间例如可以为,但不限于1h、1.2、1.4h、1.6h、1.8h或2h。
47.优选地,所述浸出反应在搅拌条件下进行。
48.优选地,向所述第一滤液中通入空气前,在搅拌的条件下,加热所述第一滤液至40~60℃(例如40℃、45℃、50℃、55℃或60℃)。
49.优选地,所述第一搅拌反应具体包括:
50.搅拌通入空气后的所述第一滤液至上清液中铁元素的含量≤0.5g/l,加热所述第一滤液至90~95℃(例如90℃、91℃、92℃、93℃、94℃或95℃)后继续搅拌30~60min(例如30min、35min、40min、45min、50min、55min或60min)。
51.优选地,所述第二滤渣煅烧前还包括洗涤和干燥。
52.优选地,所述洗涤的温度为40~50℃(例如40℃、42℃、44℃、46℃、48℃或50℃)。
53.优选地,所述洗涤至洗涤液的ph>4.5(例如4.5、4.8、5、5.5、6或6.5)。
54.优选地,干燥后的所述第二滤渣的含水量<0.5%(例如0.1%、0.2%、0.3%、0.4%或0.5%)。
55.优选地,所述第二滤渣进行煅烧的温度为650~680℃(例如650℃、655℃、660℃、665℃、670℃、675℃或680℃)。
56.优选地,所述第二滤渣进行煅烧的时间为60~90min(例如60min、65min、70min、75min、80min、85min或90min)。
57.优选地,所述第二滤渣进行煅烧后经过冷却、粉碎、筛分、除铁和包装真空,得到无水磷酸铁。
58.优选地,所述的磷酸铁的制备方法还包括:
59.所述浸出反应结束后,将所述浸出反应产生的气体导入到氢氧化钠溶液中,得到亚硫酸钠,回收备用。
60.优选地,所述的磷酸铁的制备方法还包括:
61.对所述第二滤液进行冷却和第三固液分离,得到硫酸钠晶体和母液;向所述母液中加入硫化钠,得到第三滤液和第三滤渣;调节所述第三滤液的ph为9~10,进行第四固液分离,得到第四滤液和第四滤渣;所述第三滤渣进行煅烧,采用硫酸溶解煅烧后的所述第三滤渣,得到第二混合体系;所述第二混合体系经过萃取和浓缩结晶,得到粗制硫酸铜和粗制硫酸钴。
62.优选地,所述第二滤液进行冷却后的温度为5~10℃(例如5℃、7℃、8℃、9℃或10℃)。
63.将第二滤液混合亚硫酸盐后,再混合磷酸二氢钠,返回浸出硫酸渣。循环利用三次后的第二滤液,浓缩至波美度为45~50,然后冷却至第二滤液的温度为5~10℃,离心甩干,得到的晶体为硫酸钠晶体。
64.向第四滤液中加入磷酸和磷酸二氢钠,然后返回浸出硫酸烧渣。
65.优选地,所述第三滤渣进行煅烧的温度为500~700℃(例如530℃、560℃、590℃、620℃、650℃、680℃或700℃)。
66.优选地,所述第三滤渣进行煅烧的时间为2~4h(例如2h、2.5h、3h、3.5h或4h)。
67.第三滤渣进行煅烧产生的废气采用氢氧化钠溶液吸收,返回浸出硫酸渣。
68.优选地,所述的磷酸铁的制备方法还包括:
69.向经过浮选和富集后的所述第一滤渣中加入王水,得到第三混合体系;所述第三混合体系进行第五固液分离,得到第五滤液;向所述第五滤液中加入氯化钠后进行第六固液分离,得到氯化银和第六滤液;向所述第六滤液中加入铁粉,得到粗金粉。
70.本发明在利用硫酸渣中的铁源制备磷酸铁的同时,还将硫酸渣中的铜、钴富集为粗制硫酸铜和粗制硫酸钴;还能够富集硫酸渣中的银和金。
71.本发明的另一个方面,还涉及一种磷酸铁锂的制备方法,包括所述的磷酸铁的制备方法。
72.所述的磷酸铁锂的制备方法,方法简单且成本低。
73.下面将结合具体的实施例和对比例对本发明作进一步的解释和说明。
74.实施例1
75.本实施例提供的磷酸铁的制备方法,包括以下步骤:
76.(1)将硫酸渣在球磨机内研磨后过100目筛,硫酸渣取样的检测数据见表1;
77.表1硫酸渣的具体信息
78.指标fe2o3fe3o4feosial数据16.2%52.5%1.9%10.5%3.7%camgscucozn2.7%3.1%1.2%0.21%0.11%0.0078%auagpbnicrcd2.1g/吨21.7g/吨0.0112%0.0039%0.0078%0.0002%
79.(2)将硫酸渣加入到高压釜内,加入亚硫酸钠溶液,混合搅拌;通过高压泵,将磷酸和磷酸二氢钠的混合溶液加入到高压反应釜内,边加边升温至150℃,使得反应釜内的压力为0.42mpa,加入磷酸和磷酸二氢钠混合溶液的时间为20min,在此温度和压力下搅拌反应1.5h;将反应后的浆料过滤,得到第一滤液和第一滤渣;取样第一滤渣,得到检测数据如表2;
80.表2第一滤渣的具体信息
81.指标feauagsial数据1.2%6.8g/吨67.4g/吨31.3%2.1%camgscucozn1.3%1.1%1.8%0.003%0.002%0.001%pbnicrcd
ꢀꢀ
0.008%0.002%0.003%0.0002%
ꢀꢀ
82.铁的浸出率高于95%,且富集了金银等元素;
83.(3)将第一滤液在搅拌状态升温至温度为50℃,然后通入空气,在此条件下搅拌反应至上清液中铁元素的浓度为0.35g/l,升温至95℃;在此温度下搅拌反应40min,过滤,得到第二滤液和第二滤渣;将第二滤渣洗涤后,烘干、煅烧,煅烧采用回转窑煅烧,煅烧温度为670℃,煅烧时间为80min,煅烧出料经过冷却、粉碎、筛分、除铁和包装真空,得到无水磷酸铁;无水磷酸铁的检测数据见表3;扫描电子显微镜观察磷酸铁的结果见图1和图2;磷酸铁的粒度分布见图3;
84.表3无水磷酸铁的详细信息
85.指标fep铁磷摩尔比sial数据36.09%20.66%0.96887.9ppm21.5ppmcamgscucozn29.5ppm25.9ppm21.5ppm0.3ppm10.4ppm19.4ppmbetd50pbnicrcd4.5m2/g12.831μm1.6ppm1.9ppm2.9ppm5.9ppm
86.(4)将第二滤液返回混合磷酸二氢钠,继续返回浸出硫酸渣;循环利用了三次后的第二滤液,浓缩至波美度为48,然后冷却至溶液的温度为8℃,离心甩干,得到的晶体为硫酸钠晶体,结晶后的母液,加入硫化钠溶液,过滤,得到第三滤液和第三滤渣;第三滤液中加入氢氧化钠调节溶液的ph为9.5,过滤,得到第四滤液和第四滤渣,第四滤液返回搭配新的磷酸溶液和磷酸二氢钠使用;得到硫酸钠晶体的纯度≥98.5%;
87.硫酸渣中的铁元素与亚硫酸钠、磷酸、磷酸二氢钠的摩尔数之比为1:0.37:0.3:1.7,亚硫酸钠溶液的浓度为2.5mol/l,磷酸和磷酸二氢钠混合溶液的摩尔浓度之和为2mol/l;
88.(5)第三滤渣在回转窑煅烧,煅烧温度为600℃,煅烧时间为3h,煅烧产生的废气采用氢氧化钠溶液吸收,返回浸出硫酸渣;第三滤渣经过煅烧后,加入硫酸溶解,经过p204萃取剂萃取分离钴、铜;得到的钴铜溶液,经过浓缩结晶,得到纯度为95.6%粗制硫酸铜和纯度为91.5%的粗制硫酸钴;
89.(6)第一滤渣经过浮选后,将金和银进一步富集,加入王水溶解,过滤,得到的滤液加入氯化钠,沉淀其中的银,得到氯化银,剩余的滤液中加入铁粉置换其中的金,得到粗金粉;
90.(7)将高压釜内的气体导入到2mol/l的氢氧化钠溶液中,同时往高压釜内通入氮气,使得二氧化硫气体均被排出且被氢氧化钠溶液吸收,最终使得吸收液的氢氧化钠浓度低于0.2mol/l,得到的吸收液为亚硫酸钠,返回使用;每小时通入的空气的流量(m3)与溶液中亚铁离子的总摩尔数(mol)之比为20。
91.实施例2
92.本实施例提供的磷酸铁的制备方法,包括以下步骤:
93.(1)同实施例1;
94.(2)将硫酸渣加入到高压釜内,加入亚硫酸钾溶液,混合搅拌;通过高压泵,将磷酸和磷酸二氢钠的混合溶液加入到高压反应釜内,边加边升温至130℃,使得反应釜内的压力为0.5mpa,加入磷酸和磷酸二氢钠混合溶液的时间为15min,在此温度和压力下搅拌反应2h;将反应后的浆料过滤,得到第一滤液和第一滤渣;
95.(3)将第一滤液在搅拌状态升温至温度为40℃,然后通入空气,在此条件下搅拌反应至上清液中铁元素的浓度为0.1g/l,升温至95℃;在此温度下搅拌反应30min,过滤,得到第二滤液和第二滤渣;将第二滤渣洗涤后,烘干、煅烧,煅烧采用回转窑煅烧,煅烧温度为680℃,煅烧时间为60min,煅烧出料经过冷却、粉碎、筛分、除铁和包装真空,得到无水磷酸铁;
96.(4)将第二滤液返回混合磷酸二氢钠,继续返回浸出硫酸渣;循环利用了三次后的
第二滤液,浓缩至波美度为48,然后冷却至溶液的温度为8℃,离心甩干,得到的晶体为硫酸钠晶体,结晶后的母液,加入硫化钠溶液,过滤,得到第三滤液和第三滤渣;第三滤液中加入氢氧化钠调节溶液的ph为9,过滤,得到第四滤液和第四滤渣,第四滤液返回搭配新的磷酸溶液和磷酸二氢钠使用;
97.硫酸渣中的铁元素与亚硫酸钾、磷酸、磷酸二氢钠的摩尔数之比为1:0.35:0.25:1.7,亚硫酸钾溶液的浓度为2.5mol/l,磷酸和磷酸二氢钠混合溶液的摩尔浓度之和为2mol/l;
98.(5)第三滤渣在回转窑煅烧,煅烧温度为500℃,煅烧时间为4h,煅烧产生的废气采用氢氧化钠溶液吸收,返回浸出硫酸渣;第三滤渣经过煅烧后,加入硫酸溶解,经过p204萃取剂萃取分离钴、铜;得到钴铜溶液,经过浓缩结晶,得到粗制硫酸铜和粗制硫酸钴;
99.(6)~(7)同实施例1。
100.实施例3
101.本实施例提供的磷酸铁的制备方法,包括以下步骤:
102.(1)同实施例1;
103.(2)将硫酸渣加入到高压釜内,加入亚硫酸钠溶液,混合搅拌;通过高压泵,将磷酸和磷酸二氢钠的混合溶液加入到高压反应釜内,边加边升温至170℃,使得反应釜内的压力为0.25mpa,加入磷酸和磷酸二氢钠混合溶液的时间为30min,在此温度和压力下搅拌反应1h;将反应后的浆料过滤,得到第一滤液和第一滤渣;
104.(3)将第一滤液在搅拌状态升温至温度为60℃,然后通入空气,在此条件下搅拌反应至上清液中铁元素的浓度为0.5g/l,升温至90℃;在此温度下搅拌反应60min,过滤,得到第二滤液和第二滤渣;将第二滤渣洗涤后,烘干、煅烧,煅烧采用回转窑煅烧,煅烧温度为650℃,煅烧时间为90min,煅烧出料经过冷却、粉碎、筛分、除铁和包装真空,得到无水磷酸铁;
105.(4)将第二滤液返回混合磷酸二氢钠,继续返回浸出硫酸渣;循环利用了三次后的第二滤液,浓缩至波美度为48,然后冷却至溶液的温度为8℃,离心甩干,得到的晶体为硫酸钠晶体,结晶后的母液,加入硫化钠溶液,过滤,得到第三滤液和第三滤渣;第三滤液中加入氢氧化钠调节溶液的ph为10,过滤,得到第四滤液和第四滤渣,第四滤液返回搭配新的磷酸溶液和磷酸二氢钠使用;
106.硫酸渣中的铁元素与亚硫酸钠、磷酸、磷酸二氢钠的摩尔数之比为1:0.4:0.3:1.75,亚硫酸钠溶液的浓度为2.5mol/l,磷酸和磷酸二氢钠混合溶液的摩尔浓度之和为2mol/l;
107.(5)第三滤渣在回转窑煅烧,煅烧温度为700℃,煅烧时间为2h,煅烧产生的废气采用氢氧化钠溶液吸收,返回浸出硫酸渣;第三滤渣经过煅烧后,加入硫酸溶解,经过p204萃取剂萃取分离钴、铜;得到钴铜溶液,经过浓缩结晶,得到粗制硫酸铜和粗制硫酸钴;
108.(6)~(7)同实施例1。
109.对比例1
110.本对比例提供的磷酸铁的制备方法,与实施例1相比,区别仅在于浸出反应的压力为0.1mpa,铁的浸出率为83%。
111.对比例2
112.本对比例提供的磷酸铁的制备方法,与实施例1相比,区别仅在于浸出反应的反应体系的ph为1,得到第一滤渣的详细信息分别见表4。
113.表4第一滤渣的具体信息
114.指标feauagsial数据1.12%6.8g/吨67.3g/吨30.1%1.8%camgscucozn0.8%0.9%1.6%0.002%0.001%0.001%pbnicrcd
ꢀꢀ
0.005%0.001%0.001%0.0001%
ꢀꢀ
115.对比例3
116.本对比例提供的磷酸铁的制备方法,与实施例1相比,区别仅在于浸出反应的时间为0.5h,铁的浸出率为81%。
117.通过比较实施例1、对比例1和对比例3可知,浸出反应的压力和时间需要在一定范围内,才能保证铁的浸出效果。
118.通过比较实施例1和对比例2可知,在低ph下,其他杂质的浸出率大大提高,从而使得铁溶液中引入了很多杂质,影响了铁的浸出效果,说明ph需要在一定范围内才能保证铁的浸出纯度。
119.尽管已用具体实施例来说明和描述了本发明,然而应意识到,以上各实施例仅用以说明本发明的技术方案,而非对其限制;本领域的普通技术人员应当理解:在不背离本发明的精神和范围的情况下,可以对前述各实施例所记载的技术方案进行修改,或者对其中部分或者全部技术特征进行等同替换;而这些修改或者替换,并不使相应技术方案的本质脱离本发明各实施例技术方案的范围;因此,这意味着在所附权利要求中包括属于本发明范围内的所有这些替换和修改。