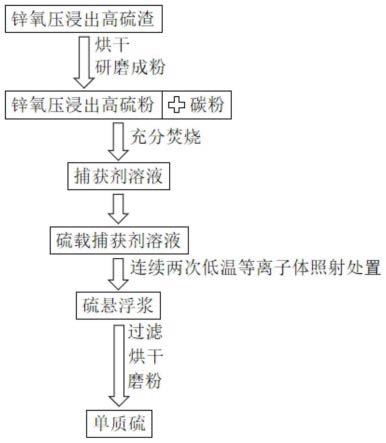
1.本发明涉及一种利用锌氧压浸出高硫渣回收单质硫的方法,属于危险废弃物无害化处置及资源化利用领域。
背景技术:2.锌冶炼企业生产单吨金属锌就要产出0.7~0.9吨锌浸出渣,而我国每年产生约60万吨锌氧压浸出渣。锌氧压浸出工艺是通过加压、通氧、添加表面活性剂(木质磺酸盐)方式实现硫化锌精矿粉中锌元素高效浸出的技术。利用锌氧压浸出工艺浸锌产生的浸出渣中含有大量的硫元素,硫品位高于40%,部分浸出渣中硫氧化物含量可达80%以上。在锌氧压高硫渣中硫主要以单质硫、硫化物、硫酸盐(复盐)等形式存在。除了富含硫,锌氧压高硫渣中硫中还含有贵金属元素及多种重金属元素。考虑到锌氧压高硫渣的环境危害性,锌氧压高硫渣被列入在《国家危险废弃物名录》(代码:321-006-48)中,危险特性为毒性。因此,对比目前锌冶炼企业大量堆存的锌氧压高硫渣必须研发高效的无害化及资源化技术加以应对及处置。否者,巨量堆存的锌氧压高硫渣不仅会对环境产生巨大威胁,未来可预期的时间内必然会对锌冶炼企业生产活动的健康、有序、长久发展造成不可逆的影响。
技术实现要素:3.发明目的:本发明的目的是提供一种利用锌氧压浸出高硫渣高效回收单质硫的方法,该方法的处置效率快,无次生污染物生成,单质硫回收效率高、纯度高。
4.技术方案:本发明所述一种利用锌氧压浸出高硫渣回收单质硫的方法包括以下步骤:
5.((1)将锌氧压浸出的高硫渣烘干,研磨,得到锌氧压浸出的高硫粉;
6.(2)将锌氧压浸出的高硫粉和碳粉混合,搅拌,得到碳掺高硫粉;
7.(3)将碳掺高硫粉焚烧,焚烧过程产生的气体通入捕获剂溶液中,得到硫载捕获剂溶液;
8.(4)对硫载捕获剂溶液连续两次进行低温等离子照射处置,得到的硫悬浮浆;
9.(5)将硫悬浮浆过滤,得到的固体烘干,研磨,得到单质硫。
10.其中,步骤(2)中,所述碳粉和锌氧压浸出的高硫粉的质量比为0.5~1.5:1。
11.其中,步骤(3)中,所述捕获剂溶液为甲酸钠溶液、乳酸钠溶液、草酸钠溶液中的任意一种。
12.其中,步骤(3)中,所述捕获剂溶液的浓度为1~10m。
13.其中,步骤(4)中,所述连续两次进行低温等离子照射处置中的第一次低温等离子照射处置时,电压为5~75kv,气氛为空气。
14.其中,步骤(4)中,所述连续两次进行低温等离子照射处置中的第二次低温等离子照射处置时,电压为5~75kv,气氛为氢气和二氧化碳气体的混合气体。
15.其中,所述氢气和二氧化碳气体的摩尔比为1~4:10。
2449.1-2014)进行测定。
28.上述实验结果如表1所示。
29.表1碳粉和锌氧压浸出高硫粉质量比对硫回收效率及回收硫纯度影响
[0030][0031]
由表1可看出,在碳粉和锌氧压浸出高硫粉质量比变化条件下回收硫纯度均高于98%。而当碳粉和锌氧压浸出高硫粉质量比小于0.5:1,碳粉掺入量较少,高硫粉引燃效率降低,二氧化硫气体燃烧释放量减少,导致硫回收效率随着碳粉和锌氧压浸出高硫粉质量比减小显著降低。当碳粉和锌氧压浸出高硫粉质量比等于0.5~1.5:1,将碳掺高硫粉吹入到燃烧炉充分焚烧,焚烧过程中碳粉点燃后进一步引燃高硫粉,碳粉充分燃烧释放二氧化碳,高硫粉充分燃烧释放二氧化硫气体。最终,硫回收效率均高于62%。而当碳粉和锌氧压浸出高硫粉质量比大于1.5:1,硫回收效率随着碳粉和锌氧压浸出高硫粉质量比进一步增加变化不显著。因此,综合而言,结合效益与成本,当碳粉和锌氧压浸出高硫粉质量比等于0.5~1.5:1时,最有利于提高硫回收效率和所回收硫的纯度。
[0032]
实施例2捕获剂溶液浓度对硫回收效率及回收硫纯度影响
[0033]
将锌氧压浸出高硫渣烘干,研磨成粉,得到锌氧压浸出高硫粉。按照质量比1.5:1分别称取碳粉和锌氧压浸出高硫粉,混合,搅拌均匀,得到碳掺高硫粉。将碳掺高硫粉吹入到燃烧炉充分焚烧,将燃烧过程产生的气体通入捕获剂溶液,其中捕获剂溶液的浓度分别为0.5m、0.7m、0.9m、1m、5.5m、10m、10.5m、11.5m、12.5m的甲酸钠溶液,得到九组硫载捕获剂溶液。对九组硫载捕获剂溶液进行连续两次低温等离子照射处置,其中对硫载捕获剂溶液进行第一次低温等离子照射处置时,低温等离子体作用电压为40kv,低温等离子作用气氛为空气;对硫载捕获剂溶液进行第二次低温等离子照射处置时,低温等离子体作用电压为40kv,低温等离子作用气氛为氢气和二氧化碳混合气体,氢气和二氧化碳气体摩尔比为2.5:10,得到九组硫悬浮浆。将九组硫悬浮浆分别过滤,得到九组的固体部分在100℃温度
条件下烘干15h,磨粉,得到九组单质硫。
[0034]
硫回收效率计算及回收硫纯度测定均同实施例1,结果如表2所示。
[0035]
表2捕获剂溶液浓度对硫回收效率及回收硫纯度影响
[0036][0037]
由表2可看出,在捕获剂溶液浓度变化条件下回收硫纯度均高于99%。而当捕获剂溶液浓度小于1m,被捕获剂溶液吸收二氧化碳和二氧化硫气体量减少,导致硫回收效率随着捕获剂溶液浓度减小显著降低。当捕获剂溶液浓度等于1~10m,二氧化碳和二氧化硫气体被捕获剂溶液吸收,生成碳酸根和亚硫酸根。一次低温等离子体照射过程中,空气中的氧气和水蒸气在放电通道中发生电离和解离,生成氧自由基和氢氧根自由基。氧自由基和氢氧根自由基可与甲酸钠、乳酸钠、草酸钠反应生成二氧化碳自由基和氢氧化钠,二氧化碳自由基可与亚硫酸根反应生成碳酸根和单质硫。氢氧化钠可强化单质硫水固分离过程。二次低温等离子体照射过程中,氢气在放电通道中生成氢自由基,氢自由基可与亚硫酸根反应生成单质硫和水,可进一步强化单质硫生成过程。最终,硫回收效率均高于67%。当捕获剂溶液浓度大于10m,硫回收效率随着捕获剂溶液浓度进一步增加变化不显著。因此,综合而言,结合效益与成本,当捕获剂溶液浓度等于1~10m时,最有利于提高硫回收效率和所回收硫的纯度。
[0038]
实施例3氢气和二氧化碳气体摩尔比对硫回收效率及回收硫纯度影响
[0039]
将锌氧压浸出高硫渣烘干,研磨成粉,得到锌氧压浸出高硫粉。按照质量比1.5:1分别称取碳粉和锌氧压浸出高硫粉,混合,搅拌均匀,得到碳掺高硫粉。将碳掺高硫粉吹入到燃烧炉充分焚烧,将燃烧过程产生的气体通入捕获剂溶液,得到硫载捕获剂溶液,其中捕获剂溶液为浓度为10m的甲酸钠溶液。对硫载捕获剂溶液进行连续两次低温等离子照射处置,其中对硫载捕获剂溶液进行第一次低温等离子照射处置时,低温等离子体作用电压为75kv,低温等离子作用气氛为空气;对硫载捕获剂溶液进行第二次低温等离子照射处置时,低温等离子体作用电压为75kv,低温等离子作用气氛为氢气和二氧化碳混合气体,氢气和二氧化碳气体摩尔比分别为0.5:10、0.7:10、0.9:10、1:10、2.5:10、4:10、4.5:10、5:10、
5.5:10,得到九组的硫悬浮浆。将九组硫悬浮浆分别过滤,得到九组固体部分在150℃温度条件下烘干6h,磨粉,得到九组单质硫。
[0040]
硫回收效率计算及回收硫纯度测定均同实施例1,结果如表3所示。
[0041]
表3氢气和二氧化碳气体摩尔比对硫回收效率及回收硫纯度影响
[0042][0043][0044]
由表3可看出,在氢气和二氧化碳气体摩尔比变化条件下回收硫纯度均高于99%。而当氢气和二氧化碳气体摩尔比小于1:10,氢气通入量较少,氢气在放电通道中生成的氢自由基减少,导致硫回收效率随着氢气和二氧化碳气体摩尔比减小显著降低。当氢气和二氧化碳气体摩尔比等于1~4:10,二次低温等离子体照射过程中,氢气在放电通道中生成氢自由基,氢自由基可与亚硫酸根反应生成单质硫和水,可进一步强化单质硫生成过程。最终,硫回收效率均高于72%。当氢气和二氧化碳气体摩尔比大于4:10,硫回收效率随着氢气和二氧化碳气体摩尔比进一步增加变化不显著。因此,综合而言,结合效益与成本,当氢气和二氧化碳气体摩尔比等于1~4:10时,最有利于提高硫回收效率和所回收硫的纯度。
[0045]
实施例4捕获剂溶液种类对硫回收效率及回收硫纯度影响
[0046]
将锌氧压浸出高硫渣烘干,研磨成粉,得到锌氧压浸出高硫粉。按照质量比1.5:1分别称取碳粉和锌氧压浸出高硫粉,混合,搅拌均匀,得到碳掺高硫粉。将碳掺高硫粉吹入到燃烧炉充分焚烧,将燃烧过程产生的气体通入捕获剂溶液,其中捕获剂溶液分别为浓度为10m的甲酸钠、乳酸钠或草酸钠溶液,得到三组硫载捕获剂溶液。对三组硫载捕获剂溶液进行连续两次低温等离子照射处置,其中对硫载捕获剂溶液进行第一次低温等离子照射处置时,低温等离子体作用电压为75kv,低温等离子作用气氛为空气;对硫载捕获剂溶液进行第二次低温等离子照射处置时,低温等离子体作用电压为75kv,低温等离子作用气氛为氢气和二氧化碳混合气体,氢气和二氧化碳气体摩尔比为4:10,得到三组硫悬浮浆。将三组硫悬浮浆分别过滤,得到三组固体部分在150℃温度条件下烘干6h,磨粉,得到三组单质硫。
[0047]
硫回收效率计算及回收硫纯度测定均同实施例1,结果如表4所示。
[0048]
表4捕获剂溶液种类对硫回收效率及回收硫纯度影响
[0049][0050]
由表4可看出,当捕获剂溶液选择甲酸钠、乳酸钠或草酸钠溶液时,硫回收效率均大于76%,回收硫纯度均大于99%。
[0051]
对比例1不同对比工艺对硫回收效率及回收硫纯度影响
[0052]
本发明工艺:采用实施例4中捕获剂溶液选择甲酸钠情况,即将锌氧压浸出高硫渣烘干,研磨成粉,得到锌氧压浸出高硫粉。按照质量比1.5:1分别称取碳粉和锌氧压浸出高硫粉,混合,搅拌均匀,得到碳掺高硫粉。将碳掺高硫粉吹入到燃烧炉充分焚烧,将燃烧过程产生的气体通入捕获剂溶液,得到硫载捕获剂溶液,其中捕获剂溶液分别为浓度为10m的甲酸钠溶液。对硫载捕获剂溶液进行连续两次低温等离子照射处置其中对硫载捕获剂溶液进行第一次低温等离子照射处置时,低温等离子体作用电压为75kv,低温等离子作用气氛为空气;对硫载捕获剂溶液进行第二次低温等离子照射处置时,低温等离子体作用电压为75kv,低温等离子作用气氛为氢气和二氧化碳混合气体,氢气和二氧化碳气体摩尔比为4:10,得到的硫悬浮浆。将硫悬浮浆过滤,得到的固体部分在150℃温度条件下烘干6h,磨粉,得到单质硫。
[0053]
对比工艺1:不加入碳粉的情况,将锌氧压浸出高硫渣烘干,研磨成粉,得到锌氧压浸出高硫粉。将锌氧压浸出高硫粉吹入到燃烧炉充分焚烧,将燃烧过程产生的气体通入捕获剂溶液,得到硫载捕获剂溶液,其中捕获剂溶液分别为浓度为10m的甲酸钠溶液。对硫载捕获剂溶液进行连续两次低温等离子照射处置,其中对硫载捕获剂溶液进行第一次低温等离子照射处置时,低温等离子体作用电压为75kv,低温等离子作用气氛为空气;对硫载捕获剂溶液进行第二次低温等离子照射处置时,低温等离子体作用电压为75kv,低温等离子作用气氛为氢气和二氧化碳混合气体,氢气和二氧化碳气体摩尔比为4:10,得到的硫悬浮浆。将硫悬浮浆过滤,得到的固体部分在150℃温度条件下烘干6h,磨粉,得到单质硫。
[0054]
对比工艺2:只进行第一次低温等离子体照射,将锌氧压浸出高硫渣烘干,研磨成粉,得到锌氧压浸出高硫粉。按照质量比1.5:1分别称取碳粉和锌氧压浸出高硫粉,混合,搅拌均匀,得到碳掺高硫粉。将碳掺高硫粉吹入到燃烧炉充分焚烧,将燃烧过程产生的气体通入捕获剂溶液,得到硫载捕获剂溶液,其中捕获剂溶液分别为浓度为10m的甲酸钠溶液。对硫载捕获剂溶液进行一次低温等离子照射处置,其中对硫载捕获剂溶液进行第一次低温等离子照射处置时,低温等离子体作用电压为75kv,低温等离子作用气氛为空气,得到的硫悬浮浆。将硫悬浮浆过滤,得到的固体部分在150℃温度条件下烘干6h,磨粉,得到单质硫。
[0055]
对比工艺3:只进行第二次低温等离子体照射,将锌氧压浸出高硫渣烘干,研磨成粉,得到锌氧压浸出高硫粉。按照质量比1.5:1分别称取碳粉和锌氧压浸出高硫粉,混合,搅拌均匀,得到碳掺高硫粉。将碳掺高硫粉吹入到燃烧炉充分焚烧,将燃烧过程产生的气体通
入捕获剂溶液,得到硫载捕获剂溶液,其中捕获剂溶液分别为浓度为10m的甲酸钠溶液。对硫载捕获剂溶液进行一次低温等离子照射处置,其中对硫载捕获剂溶液进行第一次低温等离子照射处置时,低温等离子体作用电压为75kv,低温等离子作用气氛为氢气和二氧化碳混合气体,氢气和二氧化碳气体摩尔比为4:10,得到的硫悬浮浆。将硫悬浮浆过滤,得到的固体部分在150℃温度条件下烘干6h,磨粉,得到单质硫。
[0056]
对比工艺4:现有技术中利用锌氧压浸出高硫渣回收单质硫的工艺,即将锌氧压浸出高硫渣烘干,然后将烘干后的锌氧压浸出高硫渣进行球磨,球磨时间为2h,球机转速为240rpm,球固比为0.45。球磨后的锌氧压浸出高硫渣与等质量水混合,搅拌均磨匀,过100目筛。过筛的乳液真空抽滤,然后在150℃温度条件下烘干6h,得到单质硫。
[0057]
本发明工艺及对比工艺1-4的硫回收效率计算及回收硫纯度测定均同实施例1,结果如表5所示。
[0058]
表5不同对比工艺对硫回收效率及回收硫纯度影响
[0059]
工艺类型硫回收效率相对误差回收硫纯度相对误差本发明工艺78.15%
±
0.1%99.58%
±
0.1%对比工艺124.27%
±
0.1%89.26%
±
0.1%对比工艺218.35%
±
0.1%45.12%
±
0.1%对比工艺321.59%
±
0.1%51.78%
±
0.1%对比工艺444.76%
±
0.1%64.59%
±
0.1%
[0060]
由表5可看出,对比工艺1、对比工艺2、对比工艺3、对比工艺4的硫回收效率均显著低于本发明工艺,且对比工艺1、对比工艺2、对比工艺3的硫回收效率之和低于本发明工艺。对比工艺1、对比工艺2、对比工艺3、对比工艺4的回收硫纯度均低于本发明工艺,且对比工艺2、对比工艺3的回收硫纯度之和低于本发明工艺回收硫纯度。