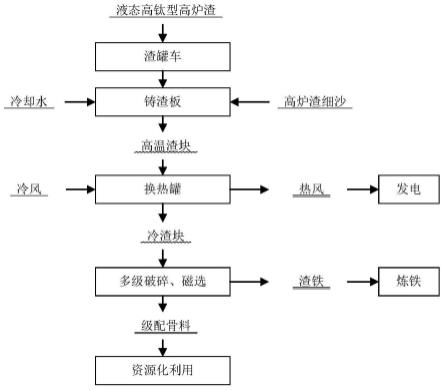
1.本发明属于冶金固废资源综合利用技术领域,具体涉及一种高钛型高炉渣的回收利用方法。
背景技术:2.以钒钛磁铁矿作为主要原料,采用传统高炉冶炼工艺冶炼得到含钒铁水和高钛型高炉渣,其中高钛型高炉渣主要成分见下表(w%):
3.caosio2mgoal2o3ttio2ti2o3tiotictintfemfefeomno25.5224.637.5913.1922.471.922.010.2790.2353.62.451.481.05
。
4.由于高钛型高炉渣不具备火山灰活性,不能像普通高炉渣一样经水淬粉磨后作为高活性矿渣微粉使用,因此高钛型高炉渣仍采用传统的热泼缓冷处理模式,破碎成级配骨料,应用于混凝土领域。
5.目前,99%的高钛型高炉渣采用传统热泼缓冷的处理方式,1%的高钛型高炉渣采用渣池水淬处理方式。缓冷处理后得到的大块渣块通过挖掘机破碎成小块,再采用多级破碎选铁工艺破碎成碎石和渣砂,作为混凝土骨料使用。
6.虽然现有的处理方式可以实现高钛型高炉渣全部资源化利用,但仍存在以下问题:
7.1)高钛型高炉渣1000℃的显热资源没有得到回收利用,通过热泼和缓冷工艺白白浪费,资源化利用率低;
8.2)处理利用效率低,方式落后,占用场地大,生产节奏紧,没有周转余地;
9.3)处理过程中形成的废气、灰尘、水蒸气等对环境有影响,现场环境差;
10.4)工人劳动强度大,效率低,作业环境差;
11.5)处理成本高,挖掘机消耗大。
技术实现要素:12.本发明提供了一种高钛型高炉渣的回收利用方法,旨在解决如何回收利用高钛型高炉渣的显热资源的问题。
13.本发明解决其技术问题所采用的技术方案是:高钛型高炉渣的回收利用方法,所述高钛型高炉渣中tio2的质量百分比含量为22%~25%,该方法包括以下步骤:利用铸渣板将温度在1200~1350℃的液态高钛型高炉渣铸造为900~1000℃的高温渣块,再将高温渣块间歇式加入换热罐中通过换热罐内由下往上流动的冷风进行换热;换热后,冷风变为热风并用于发电设备发电或物料干燥,高温渣块变为200℃以下的冷渣块并从换热罐的底部出料口连续排出用于制作级配骨料。
14.进一步的是,铸渣板包括板主体,板主体的铸渣面上设有凹坑,板主体内设有处于凹坑下侧的冷却腔,板主体上设有分别与冷却腔相通的冷却水进口和冷却水出口。
15.进一步的是,凹坑至少为两个,并在板主体的铸渣面上呈矩形阵列分布。
16.进一步的是,凹坑的横截面呈倒梯形。
17.进一步的是,凹坑的坑口的长度为80~100mm、宽度为80~100mm,凹坑的深度为100~120mm。
18.进一步的是,换热罐包括具有顶部出风口和底部进风口的竖式罐主体,竖式罐主体的上部设有进料密封装置、下部设有连续卸料装置。
19.进一步的是,发电设备包括余热锅炉和发电机。
20.进一步的是,铸造渣块的过程为:使铸渣板带凹坑的铸渣面朝上,并在凹坑表面撒一层粒度≤0.5mm的高钛型高炉渣细沙,同时开启铸渣板中间冷却水进行预冷却;通过渣罐车将温度在1200~1350℃的液态高钛型高炉渣运输到铸渣板侧部的上方,然后使渣罐车的渣罐倾翻,将液态高钛型高炉渣浇注在铸渣板的凹坑中;浇注完毕后,采用振动器振动铸渣板,使液态高钛型高炉渣的渣面摊平;之后,在液态高钛型高炉渣的渣面上洒水冷却,使其冷却为900~1000℃的高温渣块;最后,启动翻板机构使铸渣板倾翻,再采用振动器振动铸渣板,使高温渣块脱模并通过收集漏斗掉落到渣块罐中。
21.进一步的是,渣块换热的过程为:先通过渣块罐将高温渣块运输到提升机的下侧,并通过提升机将高温渣块运送到换热罐的顶部加料口,再通过加料装置间歇式加入换热罐中,同时通过风机向换热罐的底部进风口吹入冷风,冷风在换热罐内由下往上流动,加入的高温渣块在换热罐内由上往下掉落与冷风进行换热变为200℃以下的冷渣块。
22.进一步的是,从换热罐的底部出料口排出的冷渣块依次进行破碎、磁选和筛分处理后制成不同粒级的骨料。
23.本发明的有益效果是:
24.1)通过将液态高钛型高炉渣铸造为高温渣块,再将高温渣块间歇式加入换热罐中进行换热,换热出的热风用于发电设备发电或物料干燥,可使得高钛型高炉渣的显热资源得到充分回收利用,利用率达到40%以上。
25.2)整个回收处理过程中,高钛型高炉渣的资源化利用率高,占用场地较小,生产节奏紧凑。
26.3)整个回收处理过程中,工人劳动强度小,效率高,作业环境得到改善。
27.4)通过铸造渣块,省去了挖掘机的消耗,降低了处理成本。
附图说明
28.图1是本发明方法的工艺流程图;
29.图2是铸渣板的俯视结构示意图;
30.图3是铸渣板的剖视结构示意图;
31.图4是本发明中铸造渣块的设备的结构示意图;
32.图5是本发明中换热及发电设备的结构示意图;
33.图中标记为:渣罐车100、铸渣板200、凹坑210、冷却腔220、冷却水进口230、冷却水出口240、收集漏斗300、渣块罐400、提升机500、换热罐600、风机700、余热锅炉800、发电机900。
具体实施方式
34.下面结合附图和实施例对本发明作进一步的说明。
35.结合图1所示,高钛型高炉渣的回收利用方法,所述高钛型高炉渣中tio2的质量百分比含量为22%~25%,该方法包括以下步骤:利用铸渣板200将温度在1200~1350℃的液态高钛型高炉渣铸造为900~1000℃的高温渣块,再将高温渣块间歇式加入换热罐600中通过换热罐600内由下往上流动的冷风进行换热;换热后,冷风变为热风并用于发电设备发电或物料干燥,高温渣块变为200℃以下的冷渣块并从换热罐600的底部出料口连续排出用于制作级配骨料。
36.该高钛型高炉渣的回收利用方法,通过将液态高钛型高炉渣浇注在铸渣板200上铸造为高温渣块,再收集高温渣块后间歇式加入换热罐中进行换热,回收高温渣块的显热用于发电或物料干燥,冷却的冷渣块再破碎制成不同粒径的级配骨料;与传统的渣场热泼缓冷工艺相比,本发明方法处理效率高,占地面积小,流程紧凑;可以有效回收高钛型高炉渣的显热资源,且利用率达到40%以上;1000℃的高钛型高炉渣含有显热资源经折算每吨相当于25kg的标准煤,若将某钢企每年400万吨的高钛型高炉渣显热资源回收利用,按照回收率40%计算,可以回收显热资源折算约标准煤4万吨,折算价值约6千万元;另外,冷渣块制成的级配骨料能应用于建材领域,资源化利用率可以达到100%。
37.其中,液态高钛型高炉渣的比热约为1.2kj/(kg
·
℃),相当于25kg标煤/t渣(200~1000℃),堆密度为1.5t/m3,比重为3.4~3.49t/m3。
38.铸渣板200主要用于将液态高钛型高炉渣浇注为高温渣块;结合图2和图3所示,铸渣板200一般包括板主体,板主体的铸渣面上设有凹坑210,板主体内设有处于凹坑210下侧的冷却腔220,板主体上设有分别与冷却腔220相通的冷却水进口230和冷却水出口240。冷却腔220主要用于将铸造的高温渣块外部快速冷却,以快速成型,并在内部保留液芯留存大部分显热资源;铸渣板200使用时,通常还需要在凹坑210的坑口处晒水,以与冷却腔220配合,使液态高钛型高炉渣快速冷却成型。
39.在上述基础上,为了同时铸造多个高温渣块,再如图2所示,凹坑210至少为两个,并在板主体的铸渣面上呈矩形阵列分布。凹坑210的结构可以为多种,为了便于高温渣块脱模,优选将凹坑210设为横截面呈倒梯形的结构。
40.为了充分回收利用显热资源,又便于将渣块破碎,通常将液态高钛型高炉渣浇注成适当的尺寸,因此优选使凹坑210的坑口的长度为80~100mm、宽度为80~100mm,凹坑210的深度为100~120mm。该结构尺寸的凹坑210可使得铸造的高温渣块不仅能有效保留显热资源,并利于换热,而且利于冷却后的渣块进行破碎处理,降低成本。
41.结合图1、图2和图4所示,铸造渣块的过程为:使铸渣板200带凹坑210的铸渣面朝上,并在凹坑210表面撒一层粒度≤0.5mm的高钛型高炉渣细沙,同时开启铸渣板200中间冷却水进行预冷却;通过渣罐车100将温度在1200~1350℃的液态高钛型高炉渣运输到铸渣板200侧部的上方,然后使渣罐车100的渣罐倾翻,将液态高钛型高炉渣浇注在铸渣板200的凹坑210中;浇注完毕后,采用振动器振动铸渣板200,使液态高钛型高炉渣的渣面摊平;之后,在液态高钛型高炉渣的渣面上洒水冷却,使其冷却为900~1000℃的高温渣块,通常一小时左右高温渣块即可成型,具有一定的强度;最后,启动翻板机构使铸渣板200倾翻,再采用振动器振动铸渣板200,使高温渣块脱模并通过收集漏斗300掉落到渣块罐400中。通过撒
一层粒度≤0.5mm的高钛型高炉渣细沙,一方面可以防止浇注的液态高钛型高炉渣粘模,另一方面可以利于高温渣块快速成型;通过使用振动器振动铸渣板200,利于液态渣面快速摊平及高温渣块快速脱模,提供生产效率,通过铸渣板200自身的冷却和渣面上洒水强制冷却,能够提高高温渣块的冷却成型速率,进一步提高了生产效率。
42.铸渣板200一般可转动地安装在渣罐铁路旁侧采用承重钢架支撑,并设置限制其转动的部件;收集漏斗300通常设置在铸渣板200的正下方,主要用于集中收集高温渣块;渣块罐400主要用于存储高温渣块并将其运送至提升机500处,其一般处于收集漏斗300的正下方。
43.结合图4和图5所示,渣块换热的过程为:先通过渣块罐400将高温渣块运输到提升机500的下侧,并通过提升机500将高温渣块运送到换热罐600的顶部加料口,再通过加料装置间歇式加入换热罐600中,同时通过风机700向换热罐600的底部进风口吹入冷风,冷风在换热罐600内由下往上流动,加入的高温渣块在换热罐600内由上往下掉落与冷风进行换热变为200℃以下的冷渣块。通过上往下间歇式加入高温渣块,并在换热罐600内由下往上吹冷风,一方面利于高温渣块与冷风换热,有效回收显热资源,另一方面能够兼顾渣块的快速、连续外排,保证了生产效率。
44.提升机500主要用于将高温渣块提升至高处,其一般包括支架和天车。换热罐600主要用于高温渣块与介质换热;换热罐600可以为多种,优选如图5所示,换热罐600包括具有顶部出风口和底部进风口的竖式罐主体,竖式罐主体的上部设有进料密封装置、下部设有连续卸料装置。风机700主要用于为介质循环提供动力,即将冷风吹入换热罐600内。发电设备主要利用热风二次换热发电,其一般包括余热锅炉800和发电机900。
45.优选的,该高钛型高炉渣的回收利用方法还包括以下步骤:从换热罐600的底部出料口排出的冷渣块依次进行破碎、磁选和筛分处理后制成不同粒级的骨料。一般对冷渣块进行多级破碎。渣块的长度尺寸为80mm以上,通过破碎形成不同粒级的骨料,最大可以生产40mm的临界骨料,满足商品混凝土施工要求。
46.实施例1
47.某次回收利用高钛型高炉渣,过程如下:
48.使铸渣板200带凹坑210的铸渣面朝上,并在凹坑210表面撒一层粒度≤0.5mm的高钛型高炉渣细沙,同时开启铸渣板200中间冷却水进行预冷却;通过渣罐车100将温度在1200~1350℃的液态高钛型高炉渣运输到铸渣板200侧部的上方,然后使渣罐车100的渣罐倾翻,将液态高钛型高炉渣浇注在铸渣板200的凹坑210中;浇注完毕后,采用振动器轻微振动铸渣板200,使液态高钛型高炉渣的渣面摊平;之后,在液态高钛型高炉渣的渣面上洒水冷却,1小时后使其冷却为900~1000℃的高温渣块;启动翻板机构使铸渣板200倾翻,再采用振动器轻微振动铸渣板200,使高温渣块脱模并通过收集漏斗300掉落到渣块罐400中;
49.接着,先通过渣块罐400将高温渣块运输到提升机500的下侧,并通过提升机500将高温渣块运送到换热罐600的顶部加料口,再通过加料装置间歇式加入换热罐600中,同时通过风机700向换热罐600的底部进风口吹入冷风,冷风在换热罐600内由下往上流动,加入的高温渣块在换热罐600内由上往下掉落与冷风进行换热变为200℃以下的冷渣块,冷渣块并换热罐600的底部出料口连续排出,再依次进行多级破碎、磁选和筛分处理后制成不同粒级的骨料,作为建材骨料使用,过程中回收的含铁物返回炼铁工序使用;换热后,冷风变为
热风并用于发电设备发电,也可以用于物料干燥或其他用途。