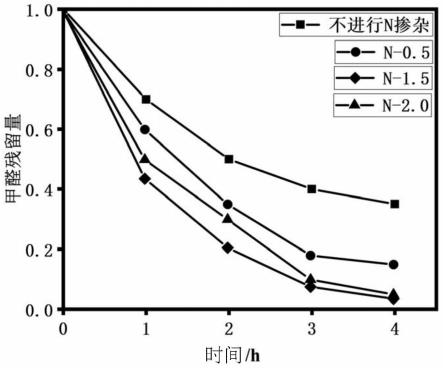
1.本发明属于陶瓷釉料领域,具体涉及一种氮掺杂的磷酸盐基光催化陶瓷产品及其制备方法。
背景技术:2.传统建筑陶瓷行业产能过剩,市场趋势逐渐狭窄,陶瓷产品的表面功能化成为提升传统陶瓷材料价值和企业创新开拓市场的重要发展方向。国内部分陶瓷企业已拓展出隔热、保温、发光、抗菌陶瓷等功能的陶瓷产品。目前建筑卫生陶瓷产品在我国工程建设、基建和家庭装修中大量使用。面对各种化工产品所释放的有毒有机物或者气体对家居环境或者人体健康造成的威胁,消费者对环保型建筑陶瓷提出了极大需求。开发出具有环保降解有毒有机污染物功能的陶瓷产品,是我国建筑陶瓷行业需要解决的问题之一。而能否将光催化剂合理运用在上述功能的陶瓷产品中,成为解决上述问题的重要课题。
3.传统的建筑卫生和日用陶瓷釉料主要分为熔块釉和生料釉。熔块釉表面缺陷少,广泛为越来越多的陶瓷企业使用。熔块釉的生产和研究主要集中以下方面:无铅无镉等无毒害元素的使用和研究,即无铅熔块釉料;高温耐磨熔块釉料;镜面装饰效果优良的透明釉料,即全抛釉;此外还有渗彩釉、乳浊釉、结晶釉等等。如何获得兼具釉面结晶效果和光催化功能的陶瓷产品是本发明所要解决的重要技术问题。
技术实现要素:4.针对上述问题,本发明提供一种氮掺杂的磷酸盐基光催化陶瓷产品及其制备方法。该产品使用磷酸盐基组分促进结晶结构取向优势生长的釉料组合物,釉料组合物在磷酸盐体系底釉的促进下,可优先形成高活性结晶结构并在釉层内取向生长,促进结晶组分在釉层表面优势分布,保证陶瓷釉表面活性位点的充分暴露。同时,釉料组合物中引入具有光催化降解性能优异的钨酸锰,对有毒气体诸如甲醛、苯基化合物等具有良好的降解性能。
5.第一方面,本发明提供一种氮掺杂的磷酸盐基光催化陶瓷产品的制备方法。所述制备方法包括以下步骤:将磷酸盐基组分促进结晶结构取向优势生长的釉料组合物施加于陶瓷本体表面;所述釉料组合物的原料组成包括:以质量百分比计,粉料a 80~90%、钨酸锰5~10%和高岭土5~10%;粉料a的原料组成包括:以质量百分比计,sio
2 15~30%、alpo
4 6~12%、mn3(po4)
2 6~10%、li3po
4 20~54%、na3po
4 16~21%、k3po
4 20~29%;将施加釉料组合物后的陶瓷本体烧成;将烧成后的陶瓷本体与含氮粉体在惰性气氛下煅烧,得到所述氮掺杂的磷酸盐基光催化陶瓷产品。一些技术方案中,所述含氮粉体是尿素。
6.传统氧化物例如氧化硅、氧化铝、氧化钙、氧化钠等组成的釉料组合物,结晶组分不易在釉层表面充分暴露,釉的活性成分不易展现良好的光催化活性。相较于氧化物体系的釉料组合物,磷酸盐体系的底釉组分在高温下具有不同的熔融液态粘度和金属离子扩散
速率,在此条件下,结晶釉组分的取向生长速度和在整体结晶釉层内的法向分布会呈现出明显变化。具体为,在磷酸盐基底釉体系下,钨酸锰基结晶釉的取向生长会在釉层表面优先分布,并形成一维取向,可为高活性结晶釉体系的充分暴露和生长提供条件。另外,通过将烧成后的陶瓷本体与含氮粉体在惰性气氛下煅烧,可以把氮元素以固溶体的形式嵌入釉面的玻璃相表面,在反复催化循环中借助氮掺杂稳定表面阳离子迁移并保持活性结构,进而提高降解效率。
7.较佳地,所述粉料a为熔块形式的粉料。
8.较佳地,所述熔块的制备过程为:按照粉料a的原料组成混合均匀后过筛于第一温度保温10~20分钟,继续于第二温度保温10~20分钟,然后于第三温度保温10~20分钟,再经淬冷、破碎得到熔块;其中,第一温度为600~900℃,第二温度为700~1000℃,第三温度为1300~1500℃;优选地,第二温度比第一温度高50~200℃。
9.较佳地,过筛的目数为30~100目。
10.较佳地,所述粉料a的粒径为100~300目。
11.较佳地,所述釉料组合物在高温烧成环境下生成呈散射取向生长的线状晶体。
12.较佳地,所述线状晶体为钨酸锰晶体。
13.较佳地,最高烧成温度为1100~1300℃,烧成周期为60~170分钟。
14.较佳地,煅烧的惰性气氛为氩气。
15.较佳地,煅烧温度为400~800℃,煅烧时间为30~90分钟。
16.较佳地,将所述釉料组合物以釉浆的形式施加于陶瓷本体表面;所述釉浆除了釉料组合物以外,还包括分散剂和水;优选地,水占釉浆的质量百分含量为40~60%,分散剂占釉浆的质量百分含量为0.1~0.5%。
17.较佳地,釉浆在陶瓷本体表面形成0.05~0.3mm的结晶釉层。
18.第二方面,本发明提供上述任一项所述的制备方法获得的氮掺杂的磷酸盐基光催化陶瓷产品。
附图说明
19.图1是实施例1釉层的xrd图;图2是实施例1-3和对比例1光催化降解甲醛的性能图;图3是实施例1-3和对比例1光催化降解苯基化合物的性能图;图4是氮掺杂的磷酸盐基光催化陶瓷产品的数码照片。
具体实施方式
20.通过下述实施方式进一步说明本发明,应理解,下述实施方式仅用于说明本发明,而非限制本发明。在没有特殊说明的情况下,各百分含量指质量百分含量。以下示例性说明本发明所述氮掺杂的磷酸盐基光催化陶瓷产品的制备方法。
21.将磷酸盐基组分促进结晶结构取向优势生长的釉料组合物施加于陶瓷本体表面。陶瓷本体的组成和规格没有特别限定,可采用本领域常用的建筑陶瓷本体。
22.所述釉料组合物的原料组成包括:以质量百分比计,粉料a 80~90%、钨酸锰5~10%和高岭土5~10%。
23.粉料a为釉料组合物的主成分,在釉料组合物中发挥底釉的作用,在高温熔融状态下提供液相环境。粉料a的原料组成包括:以质量百分比计,sio
2 15~30%、alpo
4 6~12%、mn3(po4)
2 6~10%、li3po
4 20~54%、na3po
4 16~21%、k3po
4 20~29%。粉料a在高温环境下提供活性钨酸锰结晶成核生长的液态环境,让其能以较快的速率生长。如果将粉料a替换为传统的长石、粘土,会导致结晶晶体的晶粒尺寸较小甚至无法促进晶粒生长,形成的取向生长结构少。这是因为使用传统长石或者粘土作为釉料组合物的底釉成分,钨酸锰晶核成核速度低,很难在短时间内直接成核生长。使用长石或者粘土形成的结晶釉其成长时间较长,通常仅高温条件下保温时间达到4~10小时,烧成总周期在15小时以上。本发明的釉料组合物晶花形貌易控制,节省能耗,其在高温条件下保温时间仅为5~20分钟,烧成总周期在60~170分钟。
24.如前所述,粉料a提供结晶成核生长的环境,让钨酸锰快速成核。如果粉料a在釉料组合物中的质量百分比低于80%,则结晶组分在高温熔融状态下无法有效迁移结晶生长,结晶釉成核不易,晶核生长尺寸分布不均,会导致釉装饰效果变差。如果粉料a在釉料组合物中的质量比高于90%,则晶花容易被熔融而导致晶花数量显著变少,装饰效果同样变差。
25.优选地,所述粉料a为熔块形式的粉料。将粉料a以生料形式直接使用不能实现结晶效果和催化效果同时优异。理由是熔块粉料比生料混合更均匀,成核生成晶花分布也更均匀。同时,熔块粉料也可降低烧成温度,扩大烧成范围。熔块的熔制温度较高,使得各种原料在高温下充分反应和熔融,转化成玻璃状物质,在烧成时二次再熔,降低了釉料的熔点,扩大了釉的熔融范围,为生产控制带来方便。而且,熔块形式的粉料相比生料提高了釉面质量,降低釉料收缩。制作熔块时,会使得原料中能分解的物质及某些挥发物预先排出,在釉烧时不再出现这些过程,减少了针孔缺陷。同时,经熔制后的釉料,釉烧时烧失量很小,几乎不收缩,能更好地与坯体相适应,减少滚釉、缩釉等缺陷。因此本发明所得釉料组合物呈色均匀,着色效能提高,增加釉的稳定性、悬浮性和与坯体的黏着性,减少气泡。生料虽然可实现结晶,有一定的催化效果,但是获得结晶釉的晶核生长很难控制,重复性极差,晶花大小受限,催化效果明显受限。
26.按照粉料a的原料组成称量各原料,混合、研磨、过筛得到混合物。所述混合方式可为干混。过筛的目数为30~100目。将混合物装入坩埚,放入电炉中于第一温度保温10~20分钟,继续于第二温度保温10~20分钟,然后于第三温度保温10~20分钟,再经淬冷、破碎得到熔块;其中,第一温度为600~900℃,第二温度为700~1000℃,第三温度为1300~1500℃;优选地,第二温度比第一温度高50~200℃。将熔块从水中取出,烘干后放入球磨罐中磨细,烘干备用。在该球磨过程中,例如控制熔块:磨球的质量比为1:6。可在研磨1~6小时后过筛。
27.所述粉料a的粒径为100~300目。将熔块进一步研磨是为了将其细化,使得熔块的各成分在高温条件下充分均匀分布。细化程度越高则晶花生长的均匀程度更好。
28.钨酸锰在釉料组合物中作为活性材料,起到光催化作用。将钨酸锰在釉料组合物中的质量百分比控制在5~10%。钨酸锰含量过多或过少,光催化效果均会显著减弱。钨酸锰含量低,晶花少,光催化降解组分减少,催化效果减弱;钨酸锰含量高则虽然成核晶花多,在成核时却相互重叠,导致分布不均,同样影响装饰效果和光催化效果。
29.虽然粉料a中也含有锰元素,但是粉料a中的锰是作为底釉的元素组成,而结晶釉
中引入钨酸锰可以作为结晶剂,同时起到光催化降解效果。
30.高岭土的成分为al2o3·
2sio2·
2h2o。高岭土可以提高釉料的熔融温度并改善悬浮性使釉料不易沉降。若高岭土的含量过少,则不能有效保证釉料的分散均匀性及稳定性;若高岭土含量过高,则釉料活性成分容易被高岭土包裹而无法暴露,导致釉料组合物的催化降解性能受限。
31.制备所述釉料组合物。将粉料a、钨酸锰和高岭土混合均匀并于球磨罐中磨细。球磨过程中,控制物料:磨球:水的质量比为1:1:1,研磨1-6小时后过300目筛,烘干备用。
32.将施加釉料组合物后的陶瓷本体烧成。经辊道窑氧化焰烧成,优选为快速烧成。最高烧成温度为1100~1300℃,烧成周期为60~170分钟。最高烧成温度的保温时间可为5~20分钟。
33.可以将釉料组合物制备成釉浆的形式施加于陶瓷本体表面。所述釉浆中除了釉料组合物以外,还包括水和分散剂。釉浆中水的质量百分含量为40~60%,分散剂的质量百分含量为0.1~0.5%。所述分散剂包括但不限于聚丙烯酸铵盐等。通过搅拌使得釉浆中各成分分散均匀。釉浆在陶瓷本体表面形成0.05~0.3mm的结晶釉层。此时烧成前可以先对陶瓷本体进行干燥。例如在50~100℃干燥。
34.将烧成后的陶瓷本体与含氮分体在惰性气氛下于400~800℃保温30~90min,得到所述氮掺杂的磷酸盐基光催化陶瓷产品。将氮掺杂的温度和时间控制在上述范围内的目的是控制含氮分体的分解速度和控制氮掺杂。一些技术方案中,氮源的氮质量百分含量可为20~70%。例如将尿素粉体平铺在烧成后的陶瓷本体表面。尿素的用量是每100cm2的陶瓷本体表面使用0.5~2.0g尿素粉体。尿素粉体还可以替换为三聚氰胺。
35.不可以在施釉后的陶瓷本体表面铺上尿素粉体后再进行烧成。本发明的氮掺杂需要在惰性气氛下进行。如果先在陶瓷本体表面铺上尿素粉体然后再进行烧成,则会影响釉层内的结晶取向结构生长和玻璃相结构的形成,并失去氮的特殊固溶掺杂作用。而且本发明把氮元素以固溶体的形式嵌入釉面的玻璃相结构。
36.将施釉的陶瓷本体烧成后直接在氮气气氛下进行煅烧不可以实现上述氮掺杂。因为氮气是惰性气体,会由于氮原子的活性差而难以实现上述掺杂。
37.下面进一步例举实施例以详细说明本发明。同样应理解,以下实施例只用于对本发明进行进一步说明,不能理解为对本发明保护范围的限制,本领域的技术人员根据本发明的上述内容作出的一些非本质的改进和调整均属于本发明的保护范围。下述示例具体的工艺参数等也仅是合适范围中的一个示例,即本领域技术人员可以通过本文的说明做合适的范围内选择,而并非要限定于下文示例的具体数值。
38.实施例1
39.氮掺杂的磷酸盐基光催化陶瓷产品的制备方法包括以下步骤:1)制备a料。按照如下质量配比进行配料:sio
2 20%、alpo
4 9%、mn3(po4)
2 6%、li3po
4 20%、na3po
4 16%、k3po
4 29%。将上述原料干混并研磨,过100目筛得到混合物,装入坩埚中,放入电炉中在900℃保温20分钟,在1000℃保温20分钟,在1500℃保温20分钟,取出后倒入水中淬冷制得熔块。将熔块从水中取出,烘干后放入球磨罐中,磨球取粒径5mm、15mm、20mm的球石的质量比各1/3,转速300转/分钟,控制物料:磨球的质量比为1:4,研磨4小时后过300目筛,烘干备用,记为a料。
2)制备b料。按照质量比a料80%、钨酸锰10%和高岭土10%进行配料,混合均匀并于球磨罐中,磨球取粒径5mm、15mm、20mm的球石的质量比各1/3,转速300转/分钟,控制物料:磨球的质量比为1:4,研磨6小时后过300目筛,记为b料。3)将b料加入水搅拌混匀配制成釉浆同时加入聚丙烯酸铵盐作为分散剂,釉浆中水的质量百分含量为60%,聚丙烯酸铵盐的质量百分含量为0.5%。4)将上述配制好的釉浆施釉于陶瓷表面,施釉厚度控制在0.5mm,在80℃干燥后经辊道窑氧化焰烧成,在低温500℃保温25分钟,升温至1250℃保温20分钟,烧成周期控制在60分钟。5)将尿素粉体平铺在烧成后的陶瓷本体表面,每100cm2的陶瓷本体表面使用0.5g尿素粉体,在惰性气氛下于400℃煅烧90分钟,得到所述氮掺杂的磷酸盐基光催化陶瓷产品。
40.实施例2
41.氮掺杂的磷酸盐基光催化陶瓷产品的制备方法包括以下步骤:1)制备a料。按照如下质量配比进行配料:sio
2 20%、alpo
4 9%、mn3(po4)
2 6%、li3po
4 20%、na3po
4 16%、k3po
4 29%。将上述原料干混并研磨,过100目筛得到混合物,装入坩埚中,放入电炉中在900℃保温20分钟,在1000℃保温20分钟,在1500℃保温20分钟,取出后倒入水中淬冷制得熔块。将熔块从水中取出,烘干后放入球磨罐中,磨球取粒径5mm、15mm、20mm的球石的质量比各1/3,转速300转/分钟,控制物料:磨球的质量比为1:4,研磨4小时后过300目筛,烘干备用,记为a料。2)制备b料。按照质量比a料80%、钨酸锰10%和高岭土10%进行配料,混合均匀并于球磨罐中,磨球取粒径5mm、15mm、20mm的球石的质量比各1/3,转速300转/分钟,控制物料:磨球的质量比为1:4,研磨6小时后过300目筛,记为b料。3)将b料加入水搅拌混匀配制成釉浆同时加入聚丙烯酸铵盐作为分散剂,釉浆中水的质量百分含量为60%,聚丙烯酸铵盐的质量百分含量为0.5%。4)将上述配制好的釉浆施釉于陶瓷表面,施釉厚度控制在0.5mm,在80℃干燥后经辊道窑氧化焰烧成,在低温500℃保温25分钟,升温至1250℃保温20分钟,烧成周期控制在60分钟。5)将尿素粉体平铺在烧成后的陶瓷本体表面,每100cm2的陶瓷本体表面使用1.5g尿素粉体,在惰性气氛下于600℃煅烧60分钟,得到所述氮掺杂的磷酸盐基光催化陶瓷产品。
42.实施例3
43.氮掺杂的磷酸盐基光催化陶瓷产品的制备方法包括以下步骤:1)制备a料。按照如下质量配比进行配料:sio
2 20%、alpo
4 9%、mn3(po4)
2 6%、li3po
4 20%、na3po
4 16%、k3po
4 29%。将上述原料干混并研磨,过100目筛得到混合物,装入坩埚中,放入电炉中在900℃保温20分钟,在1000℃保温20分钟,在1500℃保温20分钟,取出后倒入水中淬冷制得熔块。将熔块从水中取出,烘干后放入球磨罐中,磨球取粒径5mm、15mm、20mm的球石的质量比各1/3,转速300转/分钟,控制物料:磨球的质量比为1:4,研磨4小时后过300目筛,烘干备用,记为a料。2)制备b料。按照质量比a料80%、钨酸锰10%和高岭土10%进行配料,混合均匀并
于球磨罐中,磨球取粒径5mm、15mm、20mm的球石的质量比各1/3,转速300转/分钟,控制物料:磨球的质量比为1:4,研磨6小时后过300目筛,记为b料。3)将b料加入水搅拌混匀配制成釉浆同时加入聚丙烯酸铵盐作为分散剂,釉浆中水的质量百分含量为60%,聚丙烯酸铵盐的质量百分含量为0.5%。4)将上述配制好的釉浆施釉于陶瓷表面,施釉厚度控制在0.5mm,在80℃干燥后经辊道窑氧化焰烧成,在低温500℃保温25分钟,升温至1250℃保温20分钟,烧成周期控制在60分钟。5)将尿素分体平铺在烧成后的陶瓷本体表面,每100cm2的陶瓷本体表面使用2.0g尿素粉体,在惰性气氛下于800℃煅烧30分钟,得到所述氮掺杂的磷酸盐基光催化陶瓷产品。
44.对比例1
45.制备陶瓷产品:1)制备a料。按照如下质量配比进行配料:sio
2 20%、alpo
4 9%、mn3(po4)
2 6%、li3po
4 20%、na3po
4 16%、k3po
4 29%。将上述原料干混并研磨,过100目筛得到混合物,装入坩埚中,放入电炉中在900℃保温20分钟,在1000℃保温20分钟,在1500℃保温20分钟,取出后倒入水中淬冷制得熔块。将熔块从水中取出,烘干后放入球磨罐中,磨球取粒径5mm、15mm、20mm的球石的质量比各1/3,转速300转/分钟,控制物料:磨球的质量比为1:4,研磨4小时后过300目筛,烘干备用,记为a料。2)制备b料。按照质量比a料80%、钨酸锰10%和高岭土10%进行配料,混合均匀并于球磨罐中,磨球取粒径5mm、15mm、20mm的球石的质量比各1/3,转速300转/分钟,控制物料:磨球的质量比为1:4,研磨6小时后过300目筛,记为b料。3)将b料加入水搅拌混匀配制成釉浆同时加入聚丙烯酸铵盐作为分散剂,釉浆中水的质量百分含量为60%,聚丙烯酸铵盐的质量百分含量为0.5%。4)将上述配制好的釉浆施釉于陶瓷表面,施釉厚度控制在0.5mm,在80℃干燥后经辊道窑氧化焰烧成,在低温500℃保温25分钟,升温至1250℃保温20分钟,烧成周期控制在60分钟,得到陶瓷制品。
46.对实施例1的陶瓷产品的釉层进行xrd分析,所得结果如图1所示。对比pdf卡片在结晶釉陶瓷产品表面发现含有钨酸锰。
47.将对比例1、实施例1、实施例2、实施例3制得的含有结晶釉的陶瓷产品进行光催化测试。采用bl-ghx-v型光催化仪(比郎生物科技有限公司)对样品的光催化性能进行测试。
48.当污染物是甲醛时,将长6cm
×
宽1cm的陶瓷砖放置在有可见光辐照(氙灯,500w)的反应器中,打开灯进行光照。甲醛通过吹气的方法进入反应器,由气相色谱测得入口甲醛浓度,并计算降解率。甲醛采样时间均为20分钟每次。测量不同降解时间下甲醛的浓度得出降解曲线。当污染物是苯基化合物时,将甲醛替换为苯基化合物即可。
49.图2是每100cm2的陶瓷本体表面使用0g尿素粉体(对比例1)、每100cm2的陶瓷本体表面使用0.5g尿素粉体(实施例1)、每100cm2的陶瓷本体表面使用1.5g尿素粉体(实施例2)、每100cm2的陶瓷本体表面使用2.0g尿素粉体(实施例3)的光催化降解甲醛的性能图。
50.图3是每100cm2的陶瓷本体表面使用0g尿素粉体(对比例1)、每100cm2的陶瓷本体表面使用0.5g尿素粉体(实施例1)、每100cm2的陶瓷本体表面使用1.5g尿素粉体(实施例
2)、每100cm2的陶瓷本体表面使用2.0g尿素粉体(实施例3)的光催化降解苯基化合物的性能图。
51.可以看出不进行氮掺杂的陶瓷产品对甲醛和苯基化合物光催化降解4h的残留量大概在40%左右。进行氮掺杂后的光催化陶瓷产品降解甲醛和苯基化合物的残留量明显降低。