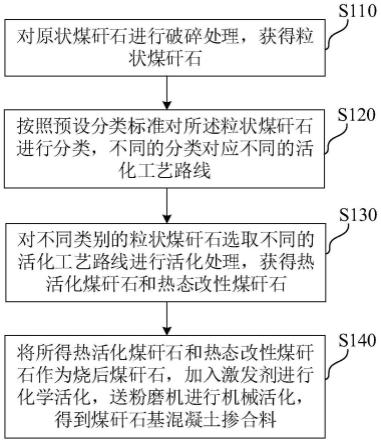
1.本发明涉及煤炭废弃物应用技术领域,更为具体地,涉及一种煤矸石基混凝土掺合料制备方法。
背景技术:2.2020年我国煤炭产量为39亿吨,煤矸石年排放量高达8亿吨。煤矸石是煤炭开采和洗选加工过程中产生的固体废弃物,其数量约占原煤产量的15%~20%,是目前我国年排放量和累计堆存量最大的工业固体废弃物之一,煤矸石现累计堆存量已超70亿吨。
3.大量煤矸石露天堆放,已形成2000余座煤矸石山,这些煤矸石山占地面积大、浪费土地资源,易发生滑坡和泥石流,且在堆放的过程中易发生自燃,产生大量黑烟和co2的同时释放出so2、no
x
等有毒有害气体,有毒有害元素随着雨水淋溶和渗滤作用进入地下水体和土壤,对生态环境造成了严重破坏,进而危害人们的生命、安全和健康。随着煤矸石堆存量的逐年增加,加大煤矸石的资源化利用是我国当前以煤为主的能源结构的必然选择,也是进一步解决其带来的社会和环境等问题的必要途径。
4.煤矸石的性质决定煤矸石资源化的途径。煤矸石是由无机质和少量有机质组成的混合物,其化学成分以sio2、al2o3为主,还含有一定量的fe2o3、cao、mgo、so3和微量的ti、v等金属元素,主要矿物组成有石英、钠长石、高岭石和伊利石等。当前,对煤矸石的利用技术主要包括:含碳量》20%的煤矸石用作燃料进行发电;利用其与黏土类似的矿物成分生产建筑材料,如制造矸石砖、矸石水泥、耐火材料和陶瓷等;对伴生矿物进行提质利用,如制取氧化铝、聚合铝、矾土及硫酸制品等;还可对透水性好、可燃成分低、易粉碎及有毒重金属含量低的煤矸石,选用机械、风力或水力等填充方式进行采空区回填利用。
5.其中,发电过程仅限于对煤矸石热值的利用,且发电过程产生的炉渣和粉尘需要做进一步的处理;煤矸石用作井下充填虽然简单易行,但其产品附加值不高,且动辄100元/吨的充填成本难以承受;提质利用的煤矸石利用量又是有限的,无法实现大宗消纳的目标。而将煤矸石用作建筑材料是实现“减量化、资源化、无害化”大宗利用的有效方式,也是实现高值化规模利用的可靠途径。
6.煤矸石“量”上的大宗性,“质”上的富含硅、铝,决定了其制备建筑材料的可能性。但是,天然煤矸石的活性较低,将未经任何方法处理的未活化煤矸石直接作为建筑胶凝材料使用,会降低产品的力学性能和耐久性,不利于其掺量的提高。若想以煤矸石为主要原材料制备建筑胶凝材料,对其活性的激发是首要任务。天然煤矸石活性低的原因主要有:煤矸石含有不同程度的碳,碳吸水性强,会降低水泥的强度和耐久性;煤矸石主要由sio2和al2o3组成,sio2由硅原子和氧原子形成规则的四面体结构晶体,属于活性很低的酸性氧化物,al2o3的晶格中,氧离子为六方紧密堆积,铝离子对称地分布在氧离子围成的八面体配位中心,晶格能很大,熔点及沸点很高,活性低;煤矸石内部相对疏松,外表面致密稳定,外壳的阻挡作用使煤矸石与其他物质反应时活性无法发挥。
7.针对以上问题,关于煤矸石做掺合料的利用,中国专利申请cn112645622a公开了“一种高活性煤矸石掺合料的制备方法”,提出将煤矸石预磨成粉后,与氧化钙和石膏进行先干混后湿混,再低温蒸养后高温煅烧,冷却后粉磨得煤矸石混凝土掺和料的工艺,该方法生产流程较为繁琐且最高仅提高12%的活性,工业化规模利用的经济性欠佳;中国专利申请cn102167532a公开了一种“混凝土掺和料及煅烧煤矸石制备混凝土掺和料的方法”,提出使用煤矸石、煤、石灰石和石膏等进行混合煅烧制备混凝土掺合料的工艺,该工艺所得掺和料用水量大、产品比表面积需磨至450~550m2/kg才能满足使用要求,增加了生产成本,同时该方法需要配备12.5%~25%的煤进行煅烧,存在可能的二次污染环境问题,不利于可持续发展;中国专利申请cn106316178a公开了一种“混凝土用矿物掺合料i级复合粉煤灰及其制作方法”,提出将5~10重量份的烧透煤矸石、20~30重量份的高炉渣、30~40重量份的转炉渣和20~45重量份的硅碎石混合破碎研磨为粉料状的复合粉煤灰的方法,该方法所制备复合粉煤灰矿物掺合料虽然需水量较低,能替代部分高强水泥,但其中煤矸石占比较小,对煤矸石资源化利用贡献较小。
技术实现要素:8.鉴于上述问题,本发明的目的是提供一种煤矸石热活化-化学+机械活化和热态改性-化学+机械活化的双工艺路线,以形成针对不同煤矸石类型的高性价比、环境友好型的混凝土活性掺合料开发工艺。
9.根据本发明的一个方面,提供了一种煤矸石基混凝土掺合料制备方法,包括:对原状煤矸石进行破碎处理,获得粒状煤矸石;
10.按照预设分类标准对所述粒状煤矸石进行分类;其中,不同的分类对应不同的活化工艺路线;
11.对不同类别的粒状煤矸石选取不同的活化工艺路线进行活化处理,获得热活化煤矸石和热态改性煤矸石;其中,对于sio2+al2o3≤50%的粒状煤矸石,直接进行高温煅烧的热活化,得到热活化煤矸石;对于sio2+al2o3>50%的粒状煤矸石,与预设比例的改性剂混合后进行烧结活化处理,得到热态改性煤矸石;
12.将所得热活化煤矸石和热态改性煤矸石作为烧后煤矸石,加入激发剂进行化学活化,送粉磨机进行机械活化,得到煤矸石基混凝土掺合料。
13.其中,可选的方案为,利用破碎设备对所述原状煤矸石进行破碎处理,所述破碎设备为颚式破碎机、反击式破碎机、冲击式破碎机、圆锥破碎机和锤式破碎机中的任意一种或两种及两种以上的组合;
14.所述破碎处理后的粒状煤矸石粒度≤30mm。
15.其中,可选的方案为,所述对于sio2+al2o3≤50%的粒状煤矸石,直接进行高温煅烧的热活化,得到热活化煤矸石的过程包括:
16.将所述sio2+al2o3≤50%的粒状煤矸石称量后送入煅烧设备中进行高温煅烧,煅烧后进行出料急冷,干燥后得热活化煤矸石。
17.其中,可选的方案为,所述煅烧设备为回转窑、流化床、回转床煅烧炉中的任意一种,煅烧温度为700~1000℃,煅烧时间为1~5h。
18.其中,可选的方案为,煅烧后的出料急冷为空气急冷和喷水急冷的其一或组合方式;
19.进行干燥处理的干燥设备为可连续进出料的圆盘干燥机、回转干燥筒、网带式干燥机、流化床中的任意一种,所述干燥处理后的物料含水率<1%。
20.其中,可选的方案为,所述对于sio2+al2o3>50%的粒状煤矸石,与预设比例的改性剂混合后进行烧结活化处理,得到热态改性煤矸石的过程包括:
21.将所述sio2+al2o3>50%的粒状煤矸石与预设比例的改性剂混合,经粉磨设备粉磨后送入造球设备造球,送入烧结机烧结,烧后出料急冷,干燥后得热态改性煤矸石。
22.其中,可选的方案为,所述改性剂为石灰石、生石灰、白云石等的其中一种或多种;其中,若所述改性剂的物料状态为块状,在与所述sio2+al2o3>50%的粒状煤矸石混合之前,还包括:将物料状态为块状的改性剂破碎成与粒状煤矸石相当粒径;并且,所述sio2+al2o3>50%的粒状煤矸石与所述改性剂的混合比例为100:10-30。
23.其中,可选的方案为,所述粉磨设备为棒磨机、球磨机、自磨机、立式辊磨机中的其中一种或任意种的组合,粉磨后的物料粒径≤0.6mm;
24.所述造球设备为圆盘或圆桶造球机、对辊压球机中的其中一种,成球直径为2~5cm;
25.所述烧结机为带式球团焙烧机,烧结温度为900~1100℃,烧结时间0.5-2h;
26.所述出料急冷为空气急冷或喷水冷却的其一或组合方式。
27.其中,可选的方案为,所述激发剂为石膏、消石灰、硫酸钠、氢氧化钠、碳酸钠、氧化钙、水泥、熟料、三乙醇胺、丙三醇和丙二醇等其中的一种或多种;其中,所述石膏为无水石膏、半水石膏、二水石膏、磷石膏、脱硫石膏中的一种或多种;
28.所述烧后煤矸石与所述激发剂比例为100:2-15。
29.其中,可选的方案为,所述粉磨设备为可连续进出料装置;并且,粉磨后得到的煤矸石基混凝土掺合料的比表面积大于350m2/kg,掺量达30%~50%。
30.上述根据本发明的煤矸石基混凝土掺合料制备方法,具有以下有益效果:
31.(1)采用煤矸石热活化-化学+机械活化和热态改性-化学+机械活化的双工艺路线,能够大大降低对原状煤矸石的理化要求,更具普适性,提高煤矸石的资源化利用率;
32.(2)采用煤矸石与改性剂粉磨造球烧结,比直接混合烧结反应更充分,反应进程更快,提高生产效率;
33.(3)无论是对煤矸石进行热活化还是热态改性处理,出料后均需进行急冷,其冷速比炉冷或堆冷更快,易形成更多的玻璃相,提高煤矸石的活性;
34.(4)采用热态处理后的煤矸石与激发剂混合后粉磨的方式,可在对物料进行机械活化的同时提升化学活化效果,比单独使用或连续使用活化效率更高效。
35.为了实现上述以及相关目的,本发明的一个或多个方面包括后面将详细说明并在权利要求中特别指出的特征。下面的说明以及附图详细说明了本发明的某些示例性方面。然而,这些方面指示的仅仅是可使用本发明的原理的各种方式中的一些方式。此外,本发明旨在包括所有这些方面以及它们的等同物。
附图说明
36.通过参考以下结合附图的说明及权利要求书的内容,并且随着对本发明的更全面理解,本发明的其它目的及结果将更加明白及易于理解。在附图中:
37.图1为根据本发明实施例的煤矸石基混凝土掺合料制备方法的流程图;
38.图2为根据本发明实施例的煤矸石基混凝土掺合料制备工艺流程。
具体实施方式
39.在下面的描述中,出于说明的目的,为了提供对一个或多个实施例的全面理解,阐述了许多具体细节。然而,很明显,也可以在没有这些具体细节的情况下实现这些实施例。在其它例子中,为了便于描述一个或多个实施例,公知的结构和设备以方框图的形式示出。
40.如前所述,现有技术中对于煤矸石做混凝土掺合料的处理方法,存在制备过程复杂、成本较高、原材料种类多、掺入量低、易产生二次污染等的显著问题,不利于大规模的工业化生产。
41.此外,煤矸石的化学组成与煤层的地质年代、地区和成矿构造等因素密切相关,我国煤矸石的多成因和广地域分布造成了其理化性能差异较大,比如可分为黏土岩类煤矸石、(粉)砂岩类煤矸石和碳酸盐类煤矸石(钙质煤矸石)等,不同地域煤矸石化学成分范围也存在很大差异,如下表所示。
42.不同地域煤矸石化学成分范围
[0043][0044]
上述现有技术往往也是针对某一地域或某一类煤矸石进行处理利用,需要有选择地使用原料,使得对于煤矸石的处理不具备普适性,限制了应用范围。
[0045]
针对以上问题,本发明提出煤矸石热活化-化学+机械活化和热态改性-化学+机械活化的双工艺路线,以形成针对不同煤矸石类型的高性价比、环境友好型的混凝土活性掺合料开发工艺,以提高其在建材领域的利用量,为实现产能化和工业规模化生产奠定基础,进而实现煤矸石的资源化无害化处置。
[0046]
以下将结合附图对本发明的具体实施例进行详细描述。
[0047]
图1示出了根据本发明实施例的煤矸石基混凝土掺合料制备方法的流程图;图2为根据本发明实施例的煤矸石基混凝土掺合料制备工艺流程。
[0048]
如图1所示,本实施例提供的煤矸石基混凝土掺合料制备方法,包括如下步骤:
[0049]
s110:对原状煤矸石进行破碎处理,获得粒状煤矸石;
[0050]
s120:按照预设分类标准对所述粒状煤矸石进行分类,不同的分类对应不同的活化工艺路线;
[0051]
s130:对不同类别的粒状煤矸石选取不同的活化工艺路线进行活化处理,获得热活化煤矸石和热态改性煤矸石;
[0052]
其中,对于sio2+al2o3≤50%的粒状煤矸石,直接进行高温煅烧的热活化,得到热活化煤矸石;对于sio2+al2o3>50%的粒状煤矸石,与预设比例的改性剂混合后进行烧结活化处理,得到热态改性煤矸石;
[0053]
s140:将所得热活化煤矸石和热态改性煤矸石作为烧后煤矸石,加入激发剂进行化学活化,送粉磨机进行机械活化,得到煤矸石基混凝土掺合料。
[0054]
下面,结合更为细化的具体实现方式对上述步骤s110-s140做更详细的说明。
[0055]
如图1和图2共同所示,在步骤s110中,需要对原状煤矸石进行破碎处理,获得粒状煤矸石。具体的,原状煤矸石首先送入破碎机破碎,降低粒度,所得粒状煤矸石可以依据其成分特征选取不同的活化工艺路线。
[0056]
由于原状煤矸石粒度较大,无法直接对其进行烧结或粉磨,因此,破碎后再活化有利于促进反应进程,提高生产效率。
[0057]
破碎设备可选择颚式破碎机、反击式破碎机、冲击式破碎机、圆锥破碎机和锤式破碎机等,根据原料状态和生产节奏的不同,可单一或组合使用。
[0058]
破碎后的粒状煤矸石粒度≤30mm。
[0059]
在步骤s120中,需要照预设分类标准对所述粒状煤矸石进行分类,不同的分类对应不同的活化工艺路线。其中的分类标准可以是粒状煤矸石中sio2和al2o3的含量,不同的含量对应不通的活化工艺路线。在本实施例中,按照sio2和al2o3的含量将粒状煤矸石进行分类成两类:sio2+al2o3≤50%的粒状煤矸石和sio2+al2o3>50%的粒状煤矸石。
[0060]
上述分类的目的时根据成分组成进行粒状煤矸石的区分,以判断是否需要改性。上述分类是基于本发明实施例的后续改性处理工艺进行的,目前还有根据煤矸石产出方式划分为煤巷矸、岩巷矸、自燃矸、洗矸、手选矸和剥离矸的分类方式,但是,根据大量的试验证明,成分组成是决定煤矸石如何处置的最主要因素,故在本发明中采用上述的分类方式。
[0061]
s130:对不同类别的粒状煤矸石选取不同的活化工艺路线进行活化处理,获得热活化煤矸石和热态改性煤矸石。其中,对于sio2+al2o3≤50%的粒状煤矸石,直接进行高温煅烧的热活化,得到热活化煤矸石;对于sio2+al2o3>50%的粒状煤矸石,与预设比例的改性剂混合后进行烧结活化处理,得到热态改性煤矸石。
[0062]
具体的,对于sio2+al2o3≤50%的粒状煤矸石,直接进行高温煅烧的热活化,得到热活化煤矸石的过程包括:
[0063]
将所述sio2+al2o3≤50%的粒状煤矸石称量后送入煅烧设备中进行高温煅烧,煅烧后进行出料急冷,干燥后得热活化煤矸石。
[0064]
高温煅烧是对煤矸石进行活性激发的重要手段,通过高温煅烧一方面可以烧除煤矸石中的碳和有机物,降低其吸水性,另一方面高温破坏了二氧化硅的硅氧四面体及氧化铝的铝氧四面体的规则结构,使其结构由有序状态转变为无定形状态,煤矸石活性由此得到提升。其中,煅烧设备可以选择回转窑、流化床、回转床煅烧炉中的任意一种,煅烧温度为700~1000℃,煅烧时间为1~5h。
[0065]
为了提高煤矸石的活性,在本发明的实施例中,煤矸石煅烧后不可随炉冷却,需通过出料急冷的方式以生成大量玻璃体提高活性,煅烧后的出料急冷可选空气急冷和喷水急冷的其一或组合方式。其中,喷水急冷会不可避免地含有一定量的水分,因此需对其进行干燥,使物料含水率<1%。进行干燥处理的干燥设备可选择圆盘干燥机、回转干燥筒、网带式干燥机、流化床等可连续进出料装置,以提升连续作业能力。
[0066]
对于sio2+al2o3>50%的粒状煤矸石,仅通过高温煅烧热活化方式无法将其活性提升至理想状态,需进行热态改性:即,将sio2+al2o3>50%的粒状煤矸石与预设比例的改性剂混合,然后经粉磨设备粉磨后送入造球设备造球,送入烧结机烧结,烧后出料急冷,干燥后得热态改性煤矸石。采用煤矸石与改性剂粉磨造球烧结,比直接混合烧结反应更充分,反应进程更快,能够有效提高生产效率。
[0067]
其中,改性剂主要是富cao原料构成,如石灰石、生石灰、白云石等的其中一种或多种;若改性剂的物料状态为块状,在与sio2+al2o3>50%的粒状煤矸石混合之前,还需要将物料状态为块状的改性剂破碎成与粒状煤矸石相当粒径,然后再进行混合送入粉磨设备;并且,sio2+al2o3>50%的粒状煤矸石与所述改性剂的混合比例为100:10-30。
[0068]
上述粉磨设备可选择棒磨机、球磨机、自磨机、立式辊磨机中的其中一种或任意种的组合,粉磨后的物料粒径≤0.6mm。
[0069]
为使各物相在高温下能够更均匀充分快速地发生反应,需将粉磨后的粉状物料造球后再进行烧结处理。本实施例中,所选用的造球设备为圆盘或圆桶造球机、对辊压球机中的其中一种,成球直径为2~5cm。对于成球性欠佳的物料,还需在造球前添加适量比例的粘结剂和水,粘结剂可选膨润土、消石灰、硅酸钠、黏土等。其中,粉状物料中添加水和粘结剂后,粉状物料、水、粘结剂三者的混合比例为100:2~8:0.5-3。
[0070]
造球设备造球完毕,送入烧结机烧结。本实施例中,烧结机可以选用带式球团焙烧机,烧结温度为900~1100℃,烧结时间0.5-2h;出料急冷可选择空气急冷或喷水冷却的其一或组合方式。
[0071]
可见,无论是对煤矸石进行热活化还是热态改性处理,出料后均需进行急冷,急冷的冷速比炉冷或堆冷更快,易形成更多的玻璃相,可以有效提高煤矸石的活性。
[0072]
此外,对于湿度较大的成型球团,其烧结和后续冷却过程可选择链篦机-回转窑-环冷机的流程,以期在烧结前进行预干燥处理。
[0073]
烧结后的物料经干燥后得热态改性煤矸石,其活性较原状煤矸石可得显著提升,首先煤矸石的一部分结晶矿物形成无定形的al2o3和sio2,比如,煅烧后的al2o3·
2sio2·
2h2o组分转变成al2o3·
2sio2相及无定形sio2和活化的al2o3,而后,富cao的改性剂在高温烧结过程中可与煤矸石反应生成具有胶凝活性的硅酸二钙、硅酸三钙和铝酸三钙。
[0074]
以添加石灰石为例:
[0075]
石灰石首先转化为氧化钙:caco3=cao+co2↑
;其次有
[0076]
2cao+sio2=2cao
·
sio2;
[0077]
3cao+sio2=3cao
·
sio2;
[0078]
3cao+al2o3=3cao
·
al2o3。
[0079]
在得到热活化煤矸石和热态改性煤矸石之后,进入步骤s140:将所得热活化煤矸石和热态改性煤矸石作为烧后煤矸石,加入激发剂进行化学活化,送粉磨机进行机械活化,得到煤矸石基混凝土掺合料。本发明这种采用热态处理后的煤矸石与激发剂混合后粉磨的方式,可在对物料进行机械活化的同时提升化学活化效果,比单独使用或连续使用活化效率更高效。
[0080]
其中,激发剂需与烧后煤矸石进行混合后再粉磨,以提高激发效率,粉磨设备选择可连续进出料装置。激发剂可选择石膏、消石灰、硫酸钠、氢氧化钠、碳酸钠、氧化钙、水泥、熟料、三乙醇胺、丙三醇和丙二醇等其中的一种或多种;其中,所述石膏为无水石膏、半水石膏、二水石膏、磷石膏、脱硫石膏中的一种或多种。所述烧后煤矸石与所述激发剂比例为100:2-15。
[0081]
粉磨设备为可连续进出料装置;并且,粉磨后得到的煤矸石基混凝土掺合料的比表面积大于350m2/kg,掺量可达30%~50%,可提升标养28d抗压强度15%~30%,并符合
gb/t 2847-2005的相关要求。
[0082]
在上述实施例中,通过加入激发剂混合粉磨的化学和机械复合活化方式,能够进一步提升煤矸石的胶凝活性,可直接用于房屋、道路、桥梁建筑等的混凝土施工中,养护制度与普通混凝土相同,显著降低工程成本;同时提高煤矸石的利用率,有利于煤矸石的规模化利用,有效减少煤矸石的堆放,具有实际的经济效益和社会环境效益。
[0083]
通过上述实施例可以看出,本发明提供的煤矸石基混凝土掺合料制备方法,采用煤矸石热活化-化学+机械活化和热态改性-化学+机械活化的双工艺路线,能够大大降低对原状煤矸石的理化要求,更具普适性,提高煤矸石的资源化利用率;并且,本发明对原料要求低,活化效果好,掺入量大,生产工艺流程简单,性价比高,易实现工业化规模生产,同时显著提高煤矸石的利用率,实现资源化消纳大宗固废、减少环境污染的目的。
[0084]
如上参照附图以示例的方式描述根据本发明的煤矸石基混凝土掺合料制备方法。但是,本领域技术人员应当理解,对于上述本发明所提出的煤矸石基混凝土掺合料制备方法,还可以在不脱离本发明内容的基础上做出各种改进。因此,本发明的保护范围应当由所附的权利要求书的内容确定。