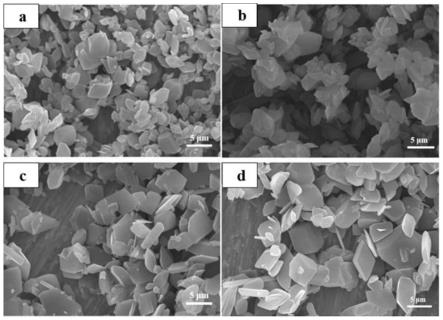
:
1.本发明涉及导热材料技术领域,具体涉及一种六方氮化硼及其制备方法与导热橡胶。
背景技术:2.六方氮化硼(h-bn)在结构上与石墨相似,被称为“白石墨”,具有耐酸碱、抗氧化等优点,此外它还具有出众的热稳定性和良好的绝缘性。h-bn在药物传递、污染物吸附、催化剂载体和水净化等方面具有潜在的应用前景。
3.目前,实验室合成h-bn的方法已有许多文献报道,但是能实现产业化的方法并不多;专利cn111606311b公开了一种表面垂直生长氮化硼纳米片的氮化硼微纳米棒;其制备方法为:在催化剂作用下,将氧化硼和镁粉的混合物进行高温固相反应,该方法需要金属镁作为催化剂,还需要借助金属网进行生长,合成方法较为复杂;同时金属镁在储存和使用过程中都具有一定的安全隐患,因此很难实现工业化生产。
4.工业上采用的合成方法主要以固体原料混合后在高温下直接氮化为主,这种方法很难实现原料在原子层面上的混合均匀,且制备得到的六方氮化硼在橡胶中的填充量达到50-55%时,表面会析出形成云雾状或粉末状的六方氮化硼,也即出现浮粉现象,也就是说,其在橡胶中的最大填充量只能达到50-55%,导致橡胶材料的导热性提升受限。
5.综上所述,目前工业法制备得到的h-bn在橡胶基体中的最大填充量只能达到50-55%,导致橡胶材料的导热性提升受限。
技术实现要素:6.本发明的目的是为了克服现有技术中六方氮化硼在橡胶基体中的填充上限不高的技术问题,提供一种六方氮化硼及其制备方法与导热橡胶。
7.本发明所要解决的技术问题采用以下的技术方案来实现:
8.本发明的目的之一在于提供一种六方氮化硼的制备方法,包括以下步骤:
9.(1)将硼源、氮源溶解于溶剂中,并进行搅拌反应,得到前驱体;
10.(2)在含氧氛围中,将所述前驱体进行第一焙烧,得到中间体;
11.(3)在氮气氛围中,将所述中间体进行第二焙烧,得到六方氮化硼。
12.本发明的目的之二在于提供一种根据前述方法制备得到的六方氮化硼。
13.本发明的目的之三在于提供一种导热橡胶,包含35-95wt%的橡胶基体和5-65wt%的导热填料;所述导热填料为前述的六方氮化硼。
14.本发明的有益效果是:
15.1、通过本发明的方法制备得到的六方氮化硼在橡胶基体中的填充量可以高达65%,能够有效的形成导热网络,改善橡胶的导热性;
16.2、本发明提供的六方氮化硼制备方法具有原料廉价、来源广的特点,并且工艺简便、能耗低,能够实现六方氮化硼的规模化生产。
附图说明:
17.图1为制备例1-4制得的前驱体的sem图;
18.图2为制备例1-4制得的六方氮化硼的sem图;
19.图3为制备例5-8制得的前驱体的sem图;
20.图4为制备例5制得的六方氮化硼的粒径分布图;
21.图5为制备例5和制备例6制得的中间体的显微镜图;
22.图6为制备例5-8制得的六方氮化硼在不同倍率下的sem图;
23.图7为制备例6制得的前驱体、中间体和六方氮化硼的红外光谱图;
24.图8为制备例3和制备例7制得的六方氮化硼的xrd图;
25.图9为制备例7、制备例9-13制得的六方氮化硼的xrd图;
26.图10为制备例17制得的六方氮化硼的xrd图。
具体实施方式:
27.为了使本发明实现的技术手段、创作特征、达成目的与功效易于明白了解,下面结合具体实施例和图示,进一步阐述本发明。
28.如前所述,本发明提供了一种六方氮化硼的制备方法,包括以下步骤:
29.(1)将硼源、氮源溶解于溶剂中,并进行搅拌反应,得到前驱体;
30.(2)在含氧氛围中,将所述前驱体进行第一焙烧,得到中间体;
31.(3)在氮气氛围中,将所述中间体进行第二焙烧,得到六方氮化硼。
32.在本发明的一个优选实施方式中,所述硼源以硼元素计,所述氮源以氮元素,所述硼源与氮源的摩尔比为(2.5-3.5):1计;例如可以是2.5:1、3:1、3.5:1或上述任意两个比值组成的范围中的任意值。
33.本发明中,所述硼源选自硼酸和/或硼砂;所述氮源选自三聚氰胺、氯化胺和尿素中的至少一种。
34.本发明中,步骤(1)中,所述氮源与硼源在溶剂中搅拌进行反应能够得到组成为c3n6h6·
h3bo3的前驱体。优选条件下,所述搅拌反应的温度为70-110℃,优选为85-105℃,更优选为90-100℃。搅拌反应时间越长,得到的前驱体的尺寸也越大,形貌也越均匀,优选条件下,所述搅拌反应的时间为4-24h,例如可以是4h、6h、8h、10h、12h、14h、16h、18h、20h、22h、24h或上述任意两个数值组成的范围中的任意值,优选为8-16h;进一步优选地,为了得到尺寸均匀的前驱体,所述搅拌反应的转速为200-800r/min;优选为250-500r/min,进一步优选为300-400r/min。
35.本发明中,所述溶剂可以是水,也可以是油水混合液。所述油水混合液为水和油的混合物,所述油水混合液包含20-80vol%的水和20-80vol%的油性溶剂;优选地,所述油水混合液包含30-70vol%的水和30-70vol%的油性溶剂;进一步优选地,所述油水混合液包含40-60vol%的水和40-60vol%的油性溶剂;更优选地,所述油水混合液包含45-55vol%的水和45-55vol%的油性溶剂。其中,vol%为体积百分比。
36.本发明中,所述油性溶剂为不溶于水的溶剂,其种类可以为本领域技术人员所知,包括但不限于液体石蜡、油酸、烷烃溶剂、硅油和石油醚中的至少一种。
37.根据本发明,当采用油水混合液作为反应溶剂时,为了提高水和油混合的均匀性,
使油水混合液达到平衡状态,优选地,所述油水混合液中还含有乳化剂;所述乳化剂的种类可以为本领域技术人员所知,包括阴离子乳化剂和/或非离子乳化剂;所述阴离子乳化剂包括但不限于烷基硫酸盐、烷基苯磺酸盐、脂肪酸盐和磷酸盐;所述非离子乳化剂包括但不限于山梨醇酯、聚氧乙烯醚和聚氧丙烯醚。
38.本发明中,通过对前驱体依次在含氧氛围和氮气氛围中进行两步焙烧,能够得到高结晶度的六方氮化硼。所述含氧氛围是指含有氧气的气体氛围,例如空气氛围。
39.在本发明的一些优选实施方式中,通过在含氧氛围中进行第一焙烧,能够使前驱体c3n6h6·
h3bo3中的三嗪环和b-o键逐渐断裂,形成含有b、n、c元素的中间体。优选地,步骤(2)中,所述第一焙烧的条件包括:温度为600-800℃,时间为2-6h。
40.发明人还发现,第一焙烧的升温速率太快会导致前驱体烧结不完全,使得到的中间产物结晶性较差;进一步优选地,所述第一焙烧的条件还包括:将所述前驱体以不高于1-4℃/min的升温速率从室温条件下升温至600-800℃,其中室温条件为25
±
5℃。
41.本发明中,通过将所述中间体在氮气氛围中进行焙烧,能够去除中间体中多余的基团,得到高纯度和高结晶度的六方氮化硼;发明人还发现,第二焙烧的温度越高,得到h-bn的结晶性也越高,步骤(3)中,所述第二焙烧的温度为1100-1800℃,进一步优选为1300-1700℃,更优选为1500-1600℃;所述第二焙烧的时间为2-10h,进一步优选为4-8h。
42.本发明中,为了使中间产物充分氮化,得到高结晶度的六方氮化硼(h-bn),优选地,所述第二焙烧的条件还包括:将所述中间体以5-8℃/min的升温速率从600-800℃升温至900-1000℃,接着再以1-4℃/min的升温速率从900-1000℃升温至1100-1800℃。
43.在本发明的一个特别优选实施方式中,当以水为溶剂时,六方氮化硼的制备步骤如下:
44.(1)将硼源、氮源溶解于水中,并70-110℃下进行搅拌反应4-16h,然后冷却至室温,得到白色沉淀,将白色沉淀进行离心、洗涤和干燥,得到前驱体;
45.(2)在空气氛围中,将所述前驱体以1-4℃/min的升温速率从室温条件下升温至600-800℃,并保温2-6h,得到中间体;
46.(3)在氮气氛围中,将所述中间体以2-8℃/min的升温速率从600-800℃升温至900-1000℃,接着再以1-4℃/min的升温速率升温至1100-1800℃,并保温4-8h,得到六方氮化硼。
47.通过上述优选实施方式制备得到了分散性好的颗粒状前驱体,粒径范围为3-10μm;所述颗粒状前驱体经焙烧后得到了表面光滑的棒状六方氮化硼,该六方氮化硼的直径为2-16μm,长度为20-100μm,长径比为6:1-12:1。
48.在本发明的另一个优选实施方式中,当以油水混合液为溶剂时,六方氮化硼的制备步骤如下:
49.(1)将硼源、氮源溶解于水中,得到澄清液;将所述澄清液滴加入含乳化剂的油性溶剂中,并在70-110℃下进行搅拌反应4-16h,然后冷却至室温,得到白色沉淀,将所述白色沉淀进行离心、洗涤和干燥,得到前驱体;
50.(2)在空气氛围中,将所述前驱体以1-4℃/min的升温速率从室温条件下升温至600-800℃,并保温2-6h,得到中间体;
51.(3)在氮气氛围中,将所述中间体以2-8℃/min的升温速率从600-800℃升温至
900-1000℃,接着再以1-4℃/min的升温速率升温至1100-1800℃,并保温4-8h,得到六方氮化硼。
52.通过上述优选实施方式制备得到了棒状的前驱体,直径为2-20μm,长度为50-120μm;所述棒状前驱体经焙烧后能够得到片状的氮化硼或表面粗糙的棒状六方氮化硼;所述片状六方氮化硼的粒径为800-900nm,厚度为20-80nm;所述表面粗糙的棒状六方氮化硼的直径为4-20μm,长度为20-100μm,长径比为6:1-12:1。
53.本发明中,以水为溶剂和以油水混合液为溶剂制备得到的前驱体的形貌完全不同,可能的原因是:采用油水混合液作为溶剂时,当水溶液分散到与之不相容的油相中时,水相倾向于形成小液滴,以尽可能减少与油相接触面积,从而使溶液达到平衡状态形成乳液,此时,前驱体晶体(球晶)发生团聚和断裂转化反应,故产生不同形貌前驱体,不同形貌的前驱体经过高温煅烧最终得到不同形貌的h-bn产品。
54.本发明的目的之三在于提供一种导热橡胶,包含35-95wt%的橡胶基体和5-65wt%的导热填料;所述导热填料为前述的六方氮化硼;优选地,所述导热橡胶包含35-60wt%的橡胶基体和40-65wt%的导热填料。
55.本发明中,所述橡胶基体包括但不限于硅橡胶、丁苯橡胶、乙丙橡胶、丁腈橡胶、三元乙丙橡胶、顺丁橡胶和天然橡胶中的至少一种。
56.以下通过实施例对本发明进行详细说明。实施例中室温是指25
±
5℃。
57.热导率:由hot disk热常数分析仪测试得到,测试温度为20℃,测样深度2mm,样品厚度3mm,长宽各4cm,每个样品测试5次,取平均值。
58.导热提高率(tce)的公式为:tce=(k-k1)/k1,其中,k为复合材料热导率,k1为基体本征热导率。
59.粘度由型号为ndj-8s的数字粘度计(上海仪昕科学仪器)测试得到。
60.以下实施例中,液体石蜡通过商购获得,密度为0.84-0.86g/cm3;室温硫化硅橡胶(以下简称为硅橡胶)通过商购获得,粘度(25℃)为1.509
×
103mpa
·
s,挥发份(150℃,3h)≤2%,表干时间≤2h;固化剂通过商购获得。
61.制备例:六方氮化硼(h-bn)的制备
62.1、以纯水作为溶剂
63.制备例1
64.前驱体制备:
65.将0.06mol硼酸和0.02mol三聚氰胺溶解于100ml纯水中,用磁力搅拌器搅拌加热至95℃并辅以350r/min的转速,待溶液透明澄清后继续搅拌反应4h后冷却。待反应液冷却至室温,得到白色沉淀,用无水乙醇对白色沉淀离心洗涤,并在真空干燥箱中60℃下干燥24h,得到bn前驱体。
66.bn合成:
67.将bn前驱体置于刚玉坩埚中然后转移至马弗炉,先以3℃/min升温至700℃并保温4h,随炉冷却,得到中间体。接着将中间体转移至氮气气氛管式炉中,先以5℃/min升温至1000℃,再3℃/min升温至1600℃并保温6h,随炉冷却,得到六方氮化硼(h-bn)。
68.制备例2-4
69.按照制备例1的方法,不同的是:搅拌反应的时间,具体如表1所示。
70.表1
[0071] 产物溶剂搅拌时间制备例1h-bn-a1水4h制备例2h-bn-a2水8h制备例3h-bn-a3水12h制备例4h-bn-a4水16h
[0072]
图1是制备例1-4得到的前驱体的sem图,其中,图1a为制备例1中前驱体的sem图;图1b为制备例2中前驱体的sem图;图1c为制备例3中前驱体的sem图;图1d为制备例4中前驱体的sem图。从图1a至1d中可以看出:在不同反应时间下均得到了分散性良好的前驱体颗粒。
[0073]
图1a和图1b中,当反应4h和8h时(制备例1和制备例2),前驱体颗粒的粒径约为5μm;图1c中,在反应12h时(制备例3),前驱体颗粒的粒径增加至8μm;图1d中,当反应时间为16h时(制备例4),前驱体颗粒的尺寸进一步增大至9μm。由此可以得出:在前驱体合成阶段,延长搅拌反应时间能够增加前驱体的尺寸,但不改变前驱体的整体形貌。
[0074]
图2是制备例1-4得到的六方氮化硼的sem图,其中,图2a为制备例1中h-bn的sem图;图2b为制备例2中h-bn的sem图;图2c为制备例3中h-bn的sem图;图2d为制备例4中h-bn的sem图。从图2可以看出,在水溶剂下合成出的h-bn均为表面光滑且长径比为6-12:1的长棒状形貌。
[0075]
图2a中,当搅拌反应时间为4h时(制备例1),合成的棒状h-bn的直径约为2-8μm,整体长度约为20-85μm,但是此时棒状h-bn的长度以及直径均匀性较差;图2b中,当搅拌反应时间为8h时(制备例2),棒状形h-bn的长度以及直径均匀性得到改善,其直径增加至2-10μm,长度增加至80μm左右;图2c中,当反应时间为12h时(制备例3),棒状形h-bn的长度以及直径均匀性得到进一步改善,其直径增加至2-16μm,长度达到100μm;图2d中,当反应时间为16h时(制备例4),棒状形bn的直径为2-14μm,长度为100μm左右。
[0076]
综上,在水溶剂中,在不同时间下合成的前驱体经过煅烧后得到的h-bn均为表面光滑的长棒状,棒状h-bn的直径、长度及其均匀度均随搅拌反应的时间增加而增加;但是,当搅拌反应的时间达到12h后,得到的棒状h-bn的直径和长度不再增加。
[0077]
2、以水-石蜡作溶剂
[0078]
制备例5
[0079]
前驱体制备:
[0080]
将0.06mol硼酸和0.02mol三聚氰胺溶解于100ml纯水中,用磁力搅拌器搅拌加热至95℃并辅以350r/min的转速,待溶液透明澄清后冷却。然后将该溶液透明澄清液滴加入含有span-80(用量为液体石蜡重量的0.05wt%)的100ml液体石蜡(95℃)中,继续反应4h后冷却。待反应液冷却至室温,得到白色沉淀,用甲苯对白色沉淀离心洗涤,并于真空干燥箱中60℃下干燥24h,即可得到bn前驱体。
[0081]
bn合成:
[0082]
将bn前驱体置于刚玉坩埚中然后转移至马弗炉,先以3℃/min升温至700℃并保温4h,随炉冷却,得到中间体。接着将中间体转移至氮气气氛管式炉中,先以5℃/min升温至1000℃,再3℃/min升温至1600℃并保温6h,随炉冷却,得到六方氮化硼(h-bn)。
[0083]
制备例6-8
[0084]
按照制备例5的方法:不同的是:搅拌反应的时间,具体如表2所示。
[0085]
表2
[0086][0087]
图3是制备例5-8得到的前驱体的sem图,其中,图3a为制备例5中前驱体的sem图;图3b为制备例6中前驱体的sem图;图3c为制备例7中前驱体的sem图;图3d为制备例8中前驱体的sem图。
[0088]
从图3a中可以看出,在搅拌反应时间为4h时(制备例5),制备得到的前驱体中既含有小尺寸的平均粒径为5μm的片状颗粒,又含有形态规则、均匀性良好的细长棒状(直径约2μm,长度为100μm);从图3b中可以看出,当搅拌反应时间为8h时(制备例6),片状的前驱体颗粒明显减少,前驱体多为直径为10μm左右的长棒;从图3c中可以看出,当搅拌反应时间为12h时(制备例7),棒状前驱体的直径进一步增加至10μm以上,且出现晶体生长到一起的现象;从图3d中可以看出,当搅拌反应时间为16h时(制备例8),棒状形貌基本消失,没有清晰的轮廓,晶体已完全团聚。
[0089]
图5a是制备例5制得的中间体的显微镜图;图5b是制备例6制得的中间体的显微镜图;
[0090]
图6是制备例5-8得到的六方氮化硼在不同倍率下的sem图,其中,图6(a-1)至图6(a-3)为制备例5中的h-bn在不同倍率下的sem图;图6(b-1)至图6(b-3)为制备例6中的h-bn在不同倍率下的sem图;图6(c-1)至图6(c-3)为制备例7中的h-bn在不同倍率下的sem图;图6(d-1)至图6(d-3)为制备例8中的h-bn在不同倍率下的sem图。
[0091]
从图6(a-1)至图6(a-3)可以看出,前驱体经氮气煅烧后,形成了尺寸为800nm-1μm的片状h-bn,片状h-bn具有良好的分散性,无明显的团聚现象。从图3a、5a和6a对比可以看出,当搅拌反应的时间为4h时(制备例5),得到了片状前驱体和棒状前驱体的混合物,前驱体经空气煅烧后,形成了球形的中间体(图5a),球形中间体在氮气氛围后,形成了片状的h-bn(图6a);说明在氮气氛围煅烧过程中,存在晶体的团聚和断裂转化反应。
[0092]
图4是制备例5制得片状h-bn的粒径分布图,如图4所示,实施例5制得的片状h-bn的粒径集中分布在800-900nm。
[0093]
从图6(b-1)至图6(b-3)可以看出,当搅拌反应时间为8h时(制备例6),得到了直径为6-20μm、长度为20-80μm的棒状h-bn,其长径比为6-12:1,但是该棒状h-bn均匀性较差,且棒状h-bn的表面疏松多孔的。从图3b、5b和6b对比可以看出,当搅拌反应时间的为8h时(制备例6),制得的前驱体、中间体和产物h-bn的形貌基本一致,均为棒状。
[0094]
从图6(c-1)至图6(c-3)可以看出,当搅拌反应时间为12h时(制备例7),得到的棒状h-bn的均匀性较制备例6明显改善,棒状h-bn的直径为4-12μm、长度为40-80μm,其长径比为6-12:1;
[0095]
从图6(d-1)至图6(d-3)可以看出,当搅拌反应时间为16h时(制备例8),得到的棒状h-bn的尺寸进一步增大,直径为4-10μm,长度为100μm;但是该棒状h-bn的致密性下降,表面出现大量的裂纹。
[0096]
图7是制备例6制得的前驱体、中间体和棒状h-bn的红外光谱图,从图7中可以看出:在前驱体的吸收峰中,3523cm-1
是-oh的伸缩振动;3496cm-1
和3416cm-1
是-nh2的反对称伸缩振动,说明分子间存在氢键。3196cm-1
是三聚氰胺中-nh2伸缩振动峰与硼酸中b-oh的特征峰重叠所致;1577cm-1
和1455cm-1
是三嗪环特征峰和b-o伸缩振动引起的;803cm-1
为bo3的伸缩振动峰;由此可知,前驱体为c3n6h6·
h3bo3化合物。
[0097]
当前驱体经过700℃处理后得到了中间体,与前驱体的红外光谱图比较可以看出:中间体中部分吸收峰消失,说明前驱体中的三嗪环和b-o键逐渐断裂,并化合形成含有b、n、c元素的中间体;
[0098]
中间体在氮气下经过1600℃煅烧后得到的产物显示了1381cm-1
和812cm-1
两处吸收峰,同样对应于b-n和b-n-b的伸缩振动峰,表明在此条件下合成的最终产物是h-bn。
[0099]
图8是制备例3和制备例7中制得的h-bn的xrd图;从图8可以看出,与在水中合成的h-bn(制备例3)相比,在水-石蜡溶剂中合成的h-bn(制备例7)的结晶度更高。
[0100]
制备例9-13
[0101]
按照制备例5的方法,不同的是:第二焙烧的终温,具体如表3所示。
[0102]
表3
[0103][0104]
图9是制备例7、制备例9-13制得的h-bn的xrd图;在1100-1600℃范围内,随着第二焙烧温度的升高,得到的h-bn的结晶度也逐渐提高。
[0105]
制备例14
[0106]
按照制备例5的方法,不同的是:前驱体的制备方法,前驱体的制备方法如下:
[0107]
将0.06mol硼酸和0.02mol三聚氰胺溶解于100ml纯水中,用磁力搅拌器搅拌加热至95℃并辅以350r/min的转速,待溶液透明澄清后冷却。然后将该溶液透明澄清液滴加入含有span-80(用量为液体石蜡重量的0.05wt%)的200ml液体石蜡(95℃)中,继续反应4h后冷却。待反应液冷却至室温,得到白色沉淀,用甲苯对白色沉淀离心洗涤,并于真空干燥箱中60℃下干燥24h,即可得到bn前驱体;
[0108]
bn前驱体经两步焙烧后得到h-bn-b9,其中,两步焙烧的方法同制备例5。
[0109]
制备例15
[0110]
按照制备例5的方法,不同的是:第一焙烧的温度为600℃,时间为4h,得到h-bn-b10。
[0111]
制备例16
[0112]
按照制备例5的方法,不同的是:第一焙烧的温度为800℃,时间为4h,得到h-bn-b11。
[0113]
制备例17
[0114]
按照制备例5的方法,不同的是:将前驱体直接在氮气氛围中进行焙烧,具体如下:
[0115]
将bn前驱体置于氮气气氛管式炉中,以5℃/min从室温下升温至1600℃,保温6h,随炉冷却,得到的产物的xrd图如图10所示,由图10可以看出,直接在氮气氛围中进行煅烧得到的产物不是六方氮化硼,且结晶性能很差。
[0116]
制备例18
[0117]
按照cn111453706a实施例2的方法制备六方氮化硼bn-d,其粒径为16.2μm。
[0118]
实施例1-18
[0119]
将制备例3、制备例5和制备例7制得的bn粉末、硅橡胶和固化剂(用量为硅橡胶用量的4%)在均质机中以3000r/min的转速混料2min,料均匀后放入真空箱中在室温下脱泡排气10min,得到浆料,浆料的粘度如表4所示。将浆料填入不锈钢模具,在平板硫化机(河南商丘橡胶机械厂,型号为xbl-d400)上150℃热压10min,然后冷压10min。最后在室温下继续固化12h,脱模,即可得到bn/sr复合材料,结果如表4所示。
[0120]
表4
[0121][0122][0123]
注:通过有无浮粉,判断h-bn的最大填充量,当出现浮粉,则说明h-bn在橡胶基体中达到了最大填充;浮粉是指橡胶表面析出了导热粉体。
[0124]
从表4中可以看出:通过实施例1、实施例7和实施例14对比可以看出,在填充量为10wt%时,h-bn-a3、h-bn-c和h-bn-b2填充得到的浆料粘度比较接近,浆料均具有良好流动性。
[0125]
通过实施例3、实施例9和实施例16对比可以看出,当填充量提升至30%时,实施例9得到的样品的粘度最小,说明填充h-bn-b2的bn/sr复合材料的粘度上升幅度最小。
[0126]
通过实施例4、实施例10和实施例17对比可以看出,当填充量增加至40%时,得到的浆料均几乎不具有流动性;其中,实施例4得到的浆料粘度为8.662
×
105mpa
·
s,实施例10得到的浆料粘度为8.825
×
105mpa
·
s,实施例12得到的浆料粘度为9.657
×
105mpa
·
s。综上可知:在同等填充量下,片状的h-bn-c增粘效果最严重。
[0127]
当h-bn-a3、h-bn-c或h-bn-b2的填充量达到50%以上时,浆料的粘度超出数字粘
度计的量程,粘度难以测出。
[0128]
通过实施例1-6对比可以看出,bn/sr复合材料的热导率随着棒状h-bn-a3填充量的增大而增大,这是因为随着棒状h-bn-a3的含量逐渐增加,导热填料(棒状h-bn-a3)之间相互接触概率增加,更容易形成完整的导热网络。当填充量在10%-30%之间时,导热增长率上升平稳,这是因为在低填充量下,棒状h-bn-a3粒子被橡胶基体包围,彼此没有接触,不能形成有效的导热通路。当导热填料(棒状h-bn-a3)的填充量增加至40%时,导热增长率开始急剧上升,当填充量达到40%时,开始发生“逾渗”现象。
[0129]
通过实施例1-6与实施例7-13对比可以看出,在同等填充量的前提下,实施例7-12得到的bn/sr复合材料的导热性优于实施例1-6得到的bn/sr复合材料。原因是:棒状h-bn-b2具有粗糙的表面,能够增加颗粒间彼此接触的概率,更容易在橡胶基体中形成完善的导热网络,为声子运输提供更多通道,从而具有更好的导热效果。
[0130]
本发明中,通过有无浮粉,判断h-bn的最大填充量,当出现浮粉,则说明h-bn在橡胶基体中达到了最大填充;浮粉是指橡胶表面析出了导热粉体。从实施例6、实施例13和实施例19可以看出,当棒状h-bn-b2的填充量为65%时,硅橡胶表面没有出现浮粉,说明h-bn-b2在硅橡胶中的填充量高达65%;当棒状h-bn-a3以及片状h-bn-c的填充量为60%时,硅橡胶表面均没有出现浮粉,说明棒状h-bn-a3以及片状h-bn-c在硅橡胶中的填充量能够达到60%。
[0131]
通过实施例1-6与实施例14-19对比可以看出,在同等填充量的前提下,实施例14-19得到的bn/sr复合材料的导热性差于实施例1-6得到的bn/sr复合材料。
[0132]
制备例20-32和对比例1-2
[0133]
按照制备例5的方法,导热填料的填充量均为40wt%,不同的是:导热填料的种类如表5所示。
[0134]
表5
[0135][0136][0137]
对比例3
[0138]
采用百图高新公司市售的粒径为100μm的球形bn(s-bn
100
)作为导热填料。
[0139]
将s-bn
100
、硅橡胶和固化剂(用量为硅橡胶用量的4%)在均质机中以3000r/min的转速混料2min,料均匀后放入真空箱中在室温下脱泡排气10min,得到浆料。将浆料填入不锈钢模具,在平板硫化机(河南商丘橡胶机械厂,型号为xbl-d400)上150℃热压10min,然后冷压10min。最后在室温下继续固化12h,脱模,即可得到bn/sr复合材料。
[0140]
实验发现,当填充量为55%时,bn/sr复合材料表面出现浮粉。说明该s-bn
100
在橡胶中的最大填充量为55%。
[0141]
以上显示和描述了本发明的基本原理和主要特征和本发明的优点。本行业的技术人员应该了解,本发明不受上述实施例的限制,上述实施例和说明书中描述的只是说明本发明的原理,在不脱离本发明精神和范围的前提下,本发明还会有各种变化和改进,这些变化和改进都落入要求保护的本发明范围内。本发明要求保护范围由所附的权利要求书及其等效物界定。