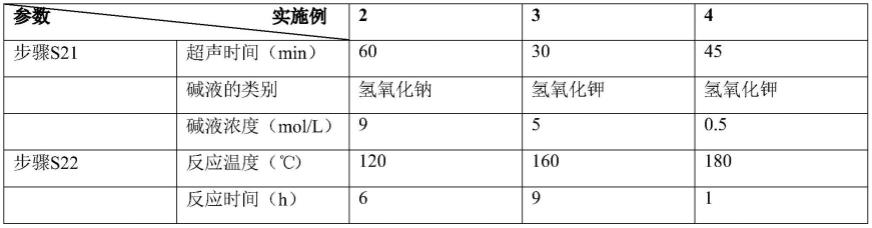
1.本发明属于新能源材料的开发及大宗固废的资源化利用领域,涉及一种气化渣残碳的湿法活化方法及其应用。
背景技术:2.能源问题是推动经济发展的源动力也是制约经济发展的瓶颈,以目前主流储能装置如锂电池和电容器来说,关键性电极材料的制造成本价格高昂。实现储能材料加工利用的技术突破、降低储能用电极材料的成本,是储能实现产业化的关键。由于碳材料具有良好的导电性、机械稳定性、成本低等优势而成为优选的电极材料。
3.另外,煤化工产业龙头的煤气化技术在中国蓬勃发展。随着煤气化技术的大规模推广,煤气化渣的堆存量及产生量越来越大。煤气化渣是煤与氧气或富氧空气发生不完全燃烧生成co与h2的过程中,煤中无机矿物质经过不同的物理化学转变伴随着煤中残留的碳颗粒形成的固态残渣,可分为粗渣和细渣两类。粗渣产生于气化炉的排渣口,占60%~80%;细渣主要产生于合成气的除尘装置,占20%~40%。目前气化渣的处理方式主要为堆存和填埋,尚未大规模工业化应用,造成了严重的环境污染和土地资源浪费,另外还可通过与其他材料复合用于建工建材、土壤水体的改良剂、残碳提质、残碳循环掺烧等可进行低附加值地利用,这对煤化工企业的可持续发展造成不利影响,气化渣的高附加值利用途经的开发迫在眉睫。目前报道的用气化渣残渣、石油焦、沥青颗粒活化后用于超级电容器炭以及用生物质活化后用于钠离子电池的负极材料主要通过高温火法活化的方式进行,但是这种方式制备得到的活化产物效果较差,比电容、循化性能以及可逆性甚至不及市售的超级电容碳,且活化的方法较为复杂,能耗较大,操作过程不易控制。
4.基于此,以制备廉价的电化学性能良好的储能电极材料及开发气化渣的高附加值利用途径为目标,通过将廉价的气化渣残碳(含碳量为40-80%,硅铝等氧化物灰分为60-20%)为原料进行活化获得了高附加值的优质储能电极材料迫在眉睫。
技术实现要素:5.本发明旨在提供一种气化渣残碳的湿法活化方法,该方法依次通过物理活化、化学活化、纯化洗涤等步骤制备得到活化产物,过程简单、能耗少,操作条件温和,过程易于掌握,通过使用廉价的气化渣残碳为原料,采用物理-化学联合活化法制备了电化学性能优异的储能电极材料,兼具环境效益和经济效益,具有较好的推广产业化应用价值。
6.本发明的技术方案如下:
7.一种气化渣残碳的湿法活化方法,按照如下的步骤顺序依次进行:
8.s1、物理活化
9.s11:将含碳量为40-80%的气化渣残碳于100℃下烘干,得a;
10.s12:将a过200目筛,以去除颗粒较大的硅铝等氧化物灰分,得b;
11.s13:b置于球磨罐中,球磨10h,得c;
12.s14:将c过200目筛,将结块的气化渣残碳与粉末状气化渣残碳分离,得 d;
13.s2:化学活化
14.s21:将d倒入聚四氟乙烯反应釜内胆中,加入碱溶液,超声30-60min分散,得e;
15.s22:将盛有e的内胆装入反应釜中密封后放入鼓风干燥箱中,于120-180℃下反应1-9h,反应结束后自然冷却到室温,得f;
16.s3:洗涤纯化
17.s31:将f静置分层,将上层黄绿色溶液用针筒抽出,留下底部黑色液体,向底部液体加入酸醇混合溶液,混合超声30min,得g;
18.s32:将g油浴加热并搅拌,纯化结束后溶液呈强酸性,得h;
19.s33:将h抽滤,并用去离子水洗至中性,结束后真空干燥,得汽化渣残碳活化后的产物。
20.作为本发明的限定:
21.(一)步骤s13中,所述球磨按照如下的程序进行:球磨球料比为10:1,球的直径为6mm,球磨机转速为300r/min,球磨每个周期正转1h,反转1h,间歇20min,如此往复5个周期。
22.该步骤的球磨过程至关重要,通过该球磨过程,活化后产物的粒径被不断细化,且汽化渣残碳在硅铝等氧化物灰分的作用下还可防止由于残碳较软易粘连的性状而发生大量的结块影响晶粒细化过程,另一方面在球磨过程中,晶粒产生晶格缺陷,气化渣残碳的孔结构在球磨的过程中发生调变,实现扩孔并增加孔容,另外在球磨的作用下,硅铝等氧化物灰分镶嵌入残碳晶粒孔隙中,防止在反复的球磨过程中发生孔形变或坍塌,降低其扩孔效应,在后续的化学活化中,通过碱液将镶嵌在孔隙中的硅铝等氧化物灰分进行脱除,进而便于保留残碳的孔隙结构,为其优异的电化学性能奠定基础。
23.(二)步骤s21中,所述的碱溶液为浓度0.5-9.0mol/l的氢氧化钠或氢氧化钾。
24.在本发明中,碱液的浓度影响着其与残碳的反应程度:即造孔过程、sp3无定形碳和sp2石墨化碳的比例、含氧官能团以及氧化物灰分的去除程度,从而影响其孔结构、比表面积、导电性、浸润性以及电化学性能。
25.本发明残碳中含有少量的氧化硅、氧化铝、氧化铁、氧化钙灰分,以及大量反应活性不同的sp3碳与sp2碳,在溶液状态下碱与残碳形成了良好的接触,水热条件下,高温高压的碱性溶液环境进一步增加了碱的反应能力。一方面碱液在氧化物的弱碱性催化环境下可以与活性强的sp3碳进行一系列的氧化反应,不仅可以在碳表面修饰羟基、羧基等亲水的含氧官能团,增加残碳的浸润性,而且可以与sp3碳形成气态的产物,从而可起到扩孔的效果,以增加比表面积,并降低了sp3碳在残碳结构中的含量,进而可调变残碳中sp3无定形碳与sp2石墨化碳的比例,以改善其导电性。另一方面,随着局部反应温度的增加,碱液可以和氧化物灰分形成一些可溶物从而降低了残碳的灰分并提高碳含量的作用。
26.(三)步骤s31中,所述酸醇混合溶液为盐酸和乙醇按照体积比为2:1配置的溶液,其中盐酸浓度为3.0mol/l。
27.在该过程,酸醇溶液用来去除残碳中结构不稳定的碳及氧化钙、氧化铁等氧化物,其体积比及盐酸的浓度用量影响着反应的程度,即残碳的纯度,进而会影响其电化学性能。
28.(四)步骤s32中,所述油浴温度为80℃,时间为6h。
29.在油浴过程中,酸醇溶液会与残碳中结构不稳定的碳及氧化钙、氧化铁等氧化物
发生反应,当其温度大于80℃,时间大于6h,会修饰更多的含氧官能团于碳材料的表面,使电化学性能变差;温度小于80℃,时间小于6h会使产物中含有较多的氧化物而使其导电性变差。
30.(五)步骤s33中,所述干燥的温度为80℃,时间为8h。
31.本发明还有一种限定,所述气化渣残碳活化后的产物可用做储能电极材料,具体的可应用于超级电容器用碳材料、钠离子电池的负极材料以及锂离子电池的负极材料中。
32.本发明上述步骤作为一个整体,各步骤之间相互关联,息息相关,其作为一个整体是无法割裂的。
33.由于采用上述技术方案后,本发明所取得的有益效果如下:
34.本发明所提供的方法过程简单、能耗少,操作条件温和,过程易于掌握,通过使用廉价的气化渣残碳为原料,采用物理-化学联合活化法制备了电化学性能优异的储能电极材料,制备的材料比表面积高达2000m2/g左右,形貌为含孔的片层结构,产物作为电化学储能材料,具有较好的电化学性能,兼具环境效益和经济效益,具有较好的推广和产业化应用价值。
35.本发明适用于利用气化渣残碳为原料制备储能电极材料。
36.下面将结合说明书附图对本发明的具体实施方式作进一步详细说明。
附图说明
[0037][0038]
图1本发明实施例1所制备的活化产物的sem图;
[0039]
图2为本发明实施例1所制备的活化产物用作超级电容器用碳材料时电化学性能测试的cv曲线图;
[0040]
图3为市售的超级电容器用yp80f碳材料电化学性能测试的cv曲线图;
[0041]
图4为本发明实施例1所制备的活化产物、未经活化处理的气化粗渣的残碳、市售yp80f材料分别用作超级电容器碳材料时在0.5a/g的gcd图;
[0042]
图5为本发明对比例中a组和b组制备得到的产物的测试曲线图,其中, (a)图为吸脱附等温曲线图,(b)图为孔径分布曲线图。
[0043]
图6为本发明对比例中a组和b组制备得到的产物的热重测试曲线图,其中,(a)图为热重曲线图,(b)图为微商热重曲线图;
[0044]
图7为本发明对比例中c组制备得到的产物作为超级电容器用碳材料时cv 曲线图;
[0045]
图8为对比例c组所制备的活化产物、未经活化处理的气化粗渣的残碳、市售yp80f材料分别用作超级电容器碳材料时在0.5a/g的gcd图;
[0046]
图9本发明实施例1所制备的活化产物的xrd图。
具体实施方式
[0047]
下述实施例中,所述的试剂如无特殊说明,均采用市售试剂,下述实验方法及检测方法,如无特殊说明均采用现有的实验方法和检测方法。
[0048]
实施例1一种汽化渣残碳的湿法活化方法
[0049]
本实施例为一种汽化渣残碳的湿法活化方法,按照如下的步骤顺序依次进行:
[0050]
s1:气化渣残碳的物理活化工艺
[0051]
s11:将含碳量为40-60%的气化渣残碳100℃下烘干得a;
[0052]
s12:将a过200目筛,以去除颗粒较大的硅铝等氧化物灰分,得b
[0053]
s13:将b放入球磨罐中,球磨球料比为10:1,球的直径为6mm,球磨机转速为300r/min,球磨每个周期正转1h,反转1h,间歇20min,如此往复5个周期,得c;
[0054]
s14:将c再次过200目筛,将结块的气化渣残碳与粉末状气化渣残碳分离,得d;
[0055]
s2:气化渣残碳的化学活化工艺
[0056]
s21:取1g d倒入聚四氟乙烯反应釜内胆中,加入4.5mol/l氢氧化钾使d 分散溶解于其中,超声30min,以更好地将气化渣残碳粉末分散于碱溶液中,得e;
[0057]
s22:装有e的内胆装入反应釜中密封后放入鼓风干燥箱中,于150℃下反应3h,反应结束后自然冷却到室温,得f;
[0058]
s3:气化渣残碳的洗涤纯化工艺
[0059]
s31:将盛有f反应釜内胆取出,静置分层,将上层黄绿色溶液用针筒抽出,留下底部黑色液体,然后加入盐酸和乙醇的混合溶液(盐酸和乙醇体积比为2:1,其中盐酸浓度为3.0mol/l),超声30min后得g;
[0060]
s32:将g于80℃下油浴加热并搅拌6h,纯化结束后溶液呈强酸性,得h;
[0061]
s33:将h抽滤,并用去离子水洗至中性,结束后于80℃下真空干燥8h,制备得到湿法活化后的产品。
[0062]
该产品的sem照片和xrd如图1和图9所示,从图中可以看出,活化后的样品具有明显的孔通道以及大量的碳,具有片层结构,通过本发明的活化方法制备的产物中具有明显的孔道和高含量的碳,这为其良好的电化学性能奠定了基础。
[0063]
实施例2-4汽化渣残碳的湿法活化方法
[0064]
本实施例分别为一种汽化渣残碳的湿法活化方法,制备过程与实施例1相似,不同之处仅在于:制备过程中相应的技术参数不同,具体见表1。
[0065]
表1制备技术参数表
[0066][0067]
实施例2-4所制备的湿法活化后产品具有片层结构,比表面积较大,且具有较好的电化学性能。
[0068]
实施例5性能测试
[0069]
一、超级电容器用材料
[0070]
将实施例1制备得到的产品组装成三电极进行电化学性能测试,具体的涂布及组装过程如下:
[0071]
(1)称取160mg实施例1所制备的产品(标记为c
200q
w-4.5mol/l-3.0 h-150℃)和
20mg的导电剂乙炔黑,先干搅30min。同时将20mg聚四氟乙烯粉末超声溶解于2ml酒精中。将干混结束后的物料倒入上述酒精中,再次超声30min,磁力搅拌10h,转速控制为300r/min;
[0072]
(2)先称量镍片质量,将步骤(1)制备好的涂料涂布到镍片上;
[0073]
(3)将按步骤(3)制备好的电极片于60℃下真空干燥8h;
[0074]
(4)将干燥后的电极片压片,压力10mpa,再次称量质量,得到涂料的质量。
[0075]
(5)组装成三电极体系进行电化学性能的测试,测试方法采用常规方法。
[0076]
如图2所示,c
200q
w-4.5mol/l-3.0h-150℃样品的cv图十分接近于矩形,呈现良好的双电层电容的特性,优于市售的yp80f的cv图(如图3所示),这说明c
200q
w-4.5mol/l-3.0h-150℃的循环性、可逆性均优于市售的yp80f材料。
[0077]
另外,图4显示c
200q
w-4.5mol/l-3.0h-150℃样品在0.5a/g的电流密度下比电容达到了103.0f/g,是cn(实施例6中a组所提供的未经活化处理的气化粗渣的残碳样品)的比电容的8倍多,与yp80f材料相比,也高出了21%。而且,yp80f和c
200q
w-4.5mol/l-3.0h-150℃样品经过2000圈循环后,比电容保持率分别为81%和95%,说明湿法活化的样品具有良好的循环稳定性。
[0078]
本发明所采用的物理-化学湿法改性明显提升了气化渣残碳的电化学性能,这是因为活化过程中明显增加了孔容及比表面积(见表2),提高了对比电容贡献较大的介孔占比。另外,活化过程中,灰分氧化物杂质的去除以及石墨化程度的调变,以及碳质量分数的提高,改善了超级电容用碳材料的导电性及循环稳定性。
[0079]
表2 c
200q
w-4.5mol/l-3.0h-150℃的孔结构与比电容测试表
[0080][0081]
二、钠离子电池用材料
[0082]
将本发明实施例1所制备得到的活化产物按照如下的步骤进行钠离子电池的组装及制备:
[0083]
(1)将本发明实施例制备的活化产物通过蒸汽浸渍法浸渍一定的alcl3;
[0084]
(2)将3ml苯胺溶于30ml乙醇,加入0.5g步骤(1)得到的产物,于 80℃油浴回流6h后蒸干乙醇,将获得的产物于氮气保护下500℃煅烧2h,得到的样品待用;
[0085]
(3)将步骤(2)得到的样品和海藻酸钠按照重量比为9:1的比例分散于水溶液中并形成均匀的浆料,涂于铝箔上,然后在100℃下真空干燥10h,得到的样品作为钠离子电池的负极材料;
[0086]
(4)选用步骤(3)制备的一个电极,钠箔作为对电极,聚丙烯为隔膜,电解液为0.8mol/l napf6及体积比为1:1碳酸乙烯酯(ec)和二甲酯(dmc) 溶液,所有操作均在充氩气的手套箱中完成.
[0087]
将本发明实施例1得到的活化产物用于钠离子电池具有优异的电化学性能,对其充放电测试表明,其首次库伦效率为57.2%;在0.1a/g的电流密度下循环 200次后,其可逆
比容量仍高达270mah/g;大倍率测试表明,在5a/g的大电流密度下循环4500次后,其可逆比容量仍高达110mah/g。
[0088]
三、锂离子电池用材料
[0089]
将本发明实施例1所制备得到的活化产物按照如下的步骤进行锂离子电池的组装及制备:
[0090]
(1)将实施例1制得的活性物质(0.3g)、4.5g sncl2·
2h2o、0.8g石墨, 和2ml浓hcl加入到150ml水中,强烈搅拌下,缓慢滴入6ml甲酸,100℃下回流6h、分离、洗涤、干燥。在600℃氮气保护下热处理1h,自然冷却;
[0091]
(2)将步骤(1)制得的材料、乙炔黑,粘结剂(聚偏氟乙烯pvdf)按质量比8:1:1的比例加入适量n-甲基吡咯烷酮,混合研磨以使浆料混合均匀,并均匀涂布在用砂纸粗化过的铜箔上,制得极片在120℃下真空干燥5h,压片,在手套箱中制作模拟电池;
[0092]
以金属锂片(99.9%)为对电极,聚丙烯膜为隔膜,含1mol/l lipf6的ec +dmc(体积比1:1)为电解液。
[0093]
将本发明实施例1得到的活化产物用于锂离子电池具有优异的电化学性能,对其充放电测试表明,首次充电容量为485mah/g,首次充放电库仑效率为 57.7%,经过50个充放电循环之后,容量保持452mah/g,库仑效率达到93%。
[0094]
实施例6对比例
[0095]
a组:未活化处理的气化粗渣的残碳作为电化学储能材料
[0096]
本组将含碳量为40-60%的气化渣残碳于100℃下干燥得到的气化粗渣的残碳产物(命名为cn)作为空白对照组。
[0097]
b组:经物理活化后的气化粗渣的残碳作为电化学储能材料
[0098]
制备过程与实施例1相似,具体过程如下:
[0099]
s11:将含碳量为40-60%的气化渣残碳100℃下烘干得a;
[0100]
s12:将a过200目筛,以去除颗粒较大的硅铝等氧化物灰分,得b
[0101]
s13:将b放入球磨罐中,球磨球料比为10:1,球的直径为6mm,球磨机转速为300r/min,球磨每个周期正转1h,反转1h,间歇20min,如此往复5个周期,得c;
[0102]
s14:将c再次过200目筛,将结块的气化渣残碳与粉末状气化渣残碳分离,得物理活化的产物,命名为c
200q
。
[0103]
分别将a组和b组所提供的材料分别进行孔结构、比表面积和热重性能测试,具体见图5和图6所示,从图中可以得出,经过筛分-球磨-筛分的物理活化过程可增加孔容和孔径,并增加了含碳量,可有效去除氧化物等灰分。
[0104]
将a组和b组分别提供的材料按照实施例5中第一个超级电容器的组装过程及涂布过程方法进行组装制备相应的电极片并进行相关的电化学性能测试。通过电化学性能测试可得出,cn与c
200q
均呈现良好的双电层电容,在0.5a/g 的电流下,cn与c
200q
的比电容分别为12.0f/g和62.0f/g(见表3),由此可看出经物理活化的方式可明显改善残碳的电化学性能。
[0105]
表3 cn和c
200q
的孔结构与比电容
[0106][0107]
c组:物理-火法活化方法制备电化学储能材料
[0108]
本组采用物理活化和火法活化的方法制备材料,物理活化方法与b组过程一样,火法活化的过程按照如下步骤依次进行:
[0109]
(1)以物理活化的c
200q
为原料,称取一定质量的c
200q
置于氧化镁瓷舟中,并依据表3的比例配制氢氧化钾溶液,采用浸渍法将c
200q
充分浸润,浸渍12h;
[0110]
(2)将步骤(1)的瓷舟于150℃下干燥1h;
[0111]
(3)将步骤(2)的瓷舟放入高温管式炉中,通入氮气,先升温至300℃进行低温活化1h,再升温至活化温度(按照表4参数)进行高温活化,升温速率为5℃/min;
[0112]
(4)将步骤(3)活化完的产物用盐酸和乙醇的混合溶液(盐酸和乙醇体积比例为2:1,其中盐酸浓度为6.0mol/l)油浴搅拌纯化,油浴温度为80℃,时间为6h。
[0113]
(5)将纯化后的产物进行离心洗涤,直至呈现中性,再于-30℃下冷冻干燥12-24h,得到活化产物。
[0114]
表4火法活化条件
[0115][0116]
将该组制备得到的活化产物命名为c
200q
f-x:y-t-t,并按照实施例5中第一个超级电容器的组装过程及涂布过程方法进行组装制备相应的电极片并进行相关的电化学性能测试。
[0117]
通过电化学性能测试可得出,在本组物理-火法活化的一系列活化的产物中,当碳碱比为1:2时,300℃低温活化1.0h,600℃高温活化2.0h下,制备的 c
200q
f-1:2-600℃-2.0h比电容最大。选取其为最佳的参数条件和样品(命名为 c
200q
f-1:2-600℃-2.0h)进行性能测试,在0.5a/g的电流密度下比电容达到了 56.0f/g。循环伏安测试(cv)曲线与恒流充放电(gcd)图(图7和图8)显示了该样品的循环性、可逆性、比电容不及市售的超级电容炭yp80f电极材料 (图3所示)甚至比电容比原料c
200q
(a组所提供材料)的比电容(62f/g)还要低,从该结果可看出火法并不能有效改善气化渣残碳的电化学性能。
[0118]
这主要是因为火法活化过程中氢氧化钾与碳在高温下反应剧烈,致使碳骨架发生坍塌,进而导致产生大量的大孔,致使其电化学性能较差。
[0119]
d组:物理-化学活化方法制备电化学储能材料
[0120]
本组制备过程与实施例1制备过程相似,不同之处仅在于:物理活化过程中,不进行球磨,直接以普通研磨的方式研磨2h并过200筛。
[0121]
该组制备得到的活化产物按照实施例5第一组超级电容器的组装过程组装成电极片并进行电化学性能测试及比表面积等测试,结果发现,比表面积253 m2/g和比电容为32f/g,电化学测试结果均不如本发明实施例1中所提供的材料。因此,在物理活化过程中,球磨过程有助于增加孔容,扩大孔径,这一结构有助于后续化学活化中碱液更易进入孔中为比表面积的增加提供通道,进而形成高比表面积的碳材料。
[0122]
本发明先进行物理活化在进行化学活化,这一顺序是关键的,物理活化可为化学活化打开更多的反应通道,进一步为其活化产物的结构和形貌形成奠定了基础。
[0123]
最后应说明的是:以上所述仅为本发明的优选实施例而已,并不用于限制本发明,尽管参照前述实施例对本发明进行了详细的说明,对于本领域的技术人员来说,其依然可以对前述各实施例所记载的技术方案进行修改,或者对其中部分技术特征进行等同替换。凡在本发明的精神和原则之内,所作的任何修改、等同替换、改进等,均应包含在本发明权利要求保护的范围之内。