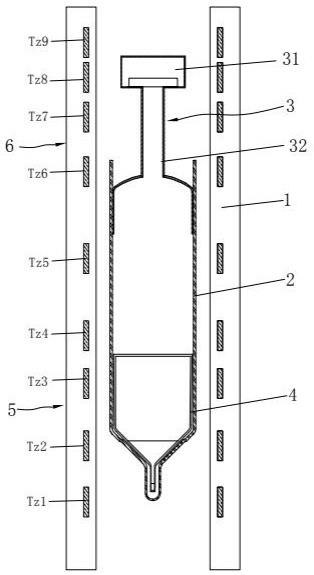
1.本技术涉及单晶化合物领域,尤其是涉及一种半绝缘砷化镓单晶体及其制备方法和生长装置。
背景技术:2.砷化镓(gaas)材料是继硅单晶之后第二代新型化合物半导体中最重要的材料。其性能优异,电子迁移率和光电转化效率高,在微电子和光电子领域应用广泛,尤其在5g商用化进程中,将发挥无可替代的作用。
3.电阻率和迁移率是半绝缘砷化镓(gaas)晶体的主要性能参数,晶体中的碳浓度对电阻率和迁移率具有重要影响。现有的vgf法生长半绝缘砷化镓晶体中,多采用高纯石墨与石英中释放的氧(石英及氧化硼分解产生)或高纯石墨与水(石墨或石英吸附的微量水)的反应来控制碳掺杂量。
4.上述vgf法中,石墨与石英在高温下氧的释放较为缓慢,导致空间气氛中co浓度的提高和扩散极为缓慢,致使砷化镓晶体内部的碳含量存在梯度差异,晶体内部纵向头尾差异尤为明显。最终得到的产品,其电阻率分布于107~108ω
•
cm之间,电性能一致性较差,商业化使用存在较大的局限性。
技术实现要素:5.为提高砷化镓晶体内碳浓度的均匀性,改善其电阻率、迁移率等性能,本技术提供一种半绝缘砷化镓单晶体及其制备方法和生长装置。
6.第一方面,本技术提供一种半绝缘砷化镓单晶体,所述半绝缘砷化镓单晶体的电阻率为0.1
×
108~5
×
108ω
•
cm,晶体内径向电阻率变化小于8%,si的浓度为1.14
×
10
13
~4.5
×
10
15 atoms
•
cm-3
,c的浓度为6
×
10
15
~2.0
×
10
16 atoms
•
cm-3
。
7.该半绝缘砷化镓单晶体具有优异的电阻率和迁移率等电性能,且其电性能的均匀性较为突出。
8.第二方面,本技术提供一种半绝缘砷化镓单晶体的制备方法,其包括如下步骤:s1:将gaas多晶、晶种与氧化硼放入pbn坩埚中,将pbn坩埚转移至石英坩埚内;将石墨放置于石英帽内,将石英帽与石英坩埚密封连接;s2:将步骤s1中密封连接的石英帽与石英坩埚装载至vgf单晶炉中,且石英帽与石英坩埚位于不同温区;s3:控制石英坩埚所在温区升温至化料温度,同时控制石英帽所在温区升温至1000
±
50℃;s4:石英坩埚所在温区达到化料温度后,进行保温化料,并控制石英帽所在温区升温至1200
±
50℃并保温4~50h;s5:化料完成后,控制石英帽所在温区降温至1000℃
±
50℃并保温,进行气氛掺杂,晶体生长;
s6:降温出料。
9.上述技术方案提供了一种新的掺碳量的控制方法,通过将装有石墨的石英帽与石英坩埚设置在不同温区,并控制石英帽所在温区达到合适温度,促使石墨与石英发生如下反应:;反应所产生的co提供气氛掺杂的主要碳源,从而实现微波晶体的有效碳掺杂,并通过对该化学反应进程的控制实现对气氛中碳含量的控制;当然,气氛中由c与h2o或o2反应产生的co也少量存在。
10.在上述反应的控制中,当石墨所在温区的温度≤1000℃温度时,c与sio2的反应基本不进行,即步骤s3与s5中,石墨实质上未与石英反应生成co;而当石墨所在温区的温度≥1200℃时,c与sio2的反应一直进行,即步骤s4中,co持续产生。为确保co含量的稳定,应当控制温度≥1200℃的反应时长。
11.c掺入gaas的主要途径是:2ga+co
→
ga2o+c;gaas中的游离ga与气氛中的co发生上述化学反应,将c引入gaas。
12.而在常规vgf工艺中,气氛掺杂的碳源主要通过石墨与生长装置或石墨自身含有的水分及氧气反应得到,其反应式如下:c+h2o
→
co+h2;2c+o2→
2co;c++o2→
co2;其c掺入gaas的途径为:2ga+co
→
ga2o+c;4ga+co2→
ga2o3+3c;然而在高温环境下,石墨与生长装置(石英)中氧的释放较为缓慢,导致晶体中的碳浓度不大且分布不均,晶体电阻率较低且各部相差较大,应用性能较差。而本技术中,c与sio2的反应速度可通过温度以及石墨与石英的接触面积进行控制,通常石墨所在温区的温度越高,反应向右进行得越剧烈,空间气氛中的co含量越大,相应的晶体中的碳含量越多。同时,石墨与石英的接触面越大,空间气氛中的co含量越大,相应的晶体中的碳含量越多。由此使得气氛中co含量相对容易控制,晶体内c浓度更为均匀,有利于提高晶体内部电阻率与迁移率的均匀性。
13.优选的,放入石英帽前,对所述石墨进行预处理,所述预处理为去除水分。
14.上述技术方案中,可将石墨置于石英容器内,密封并抽真空,然后将石英容器进行烘烤,以尽可能地去除石墨中的水分,降低c和h2o反应产生的co对空间气氛中co浓度的影响,提高晶体中掺碳量的精准性,保障晶体具有较高的电阻率和迁移率。本技术对烘烤温度没有特殊要求,通常在200
±
30℃温度下烘烤可兼顾效率与能耗。
15.优选的,pbn坩埚、石英坩埚、石英帽与vgf单晶炉在使用前进行所述预处理。
16.pbn坩埚、石英坩埚与石英帽在使用前也需进行预处理,严格控制晶体生长所使用的材料以及设备的水分、氧气含量,以获得具有高电阻率的砷化镓晶体。
17.优选的,所述抽真空的真空度为(1~9
×
10-4
)~(1~9
×
10-2
)pa。
18.通过采用上述技术方案,在该真空度下,能够控制石墨原料中水分的充分排出,减少石墨与水的副反应的进行,确保空间气氛中co含量的可控性。在上述真空度下,一般烘烤时间在2~4h左右即可实现水分的有效去除。
19.优选的,步骤s5中,所述晶体生长在冷却速率为0.1~10℃/h,温度梯度为0.1~10℃/cm的条件下进行。
20.在上述技术冷却速率与温度梯度下,有效保障半绝缘砷化镓晶体的生长。
21.第三方面,本技术提供一种半绝缘砷化镓单晶体的生长装置,其包括vgf单晶炉、位于vgf单晶炉内的石英坩埚、设置于石英坩埚内的pbn坩埚,所述石英坩埚的开口上设置有与之盖合的石英帽,所述石英帽内包括有用于放置石墨的容纳槽;所述vgf单晶炉沿其轴向设置有第一温区和第二温区,所述石英帽位于第一温区内,所述石英坩埚位于第二温区内。
22.通过采用上述技术方案,在晶体生长过程中,由于晶体生长所需的温度场与c和sio2的反应温度存在较大的差异,因此本技术中,将放置石墨的石英管与放置砷化镓等原料的石英坩埚置于vgf单晶炉的不同温区中,利用不同热源控制各温区所需的温度。
23.优选的,所述石英帽靠近石英坩埚的一端设置有过渡管,所述过渡管与容纳槽连通。
24.由于石墨的反应温度与石英坩埚内的生长温度区别较大,为减少两个温区间的温度干涉,因此在容纳槽与石英坩埚之间设置过渡管,以保障石墨与石英反应的进行,有利于精确控制气氛中的co含量。
25.优选的,所述过渡管的直径小于容纳槽的宽度。
26.通过采用上述技术方案,过渡管的直径较小,整体呈细长型,有利于减少容纳槽与石英坩埚件的热对流,提高对容纳槽处反应温度的控制精度。
27.优选的,所述第一温区包括沿vgf单晶炉轴向设置的多个温区,所述第二温区包括沿vgf单晶炉轴向设置的多个温区。
28.通过采用上述技术方案,在本技术改进的vgf工艺中,砷化镓晶体的生长需要具备适宜的温度梯度,因此第一温区需在轴向上分隔为多个独立的小温区,用以形成合适的温度场,保障晶体的生长;而石墨与sio2的反应需要区别于第一温区的温度场,为保障对其反应温度的精确控制,第二温区也分隔为多个小的温区。
29.需要说明的是,为了实现温度的有效控制,当前温区之间的距离一般控制在8cm~25cm。本技术优选将第一温区分为6个小的温区,记作tz1~tz6;第二温区分为3个小的温区,记作tz7~tz9。
30.综上所述,本技术具有如下有益效果:1、本技术中通过控制石墨中c与石英帽中sio2反应产生co,为砷化镓晶体的生长提供气氛掺杂的主要碳源,并实现了对气氛中co含量的有效控制,保障了晶体内部碳掺量的均匀性,从而获得电阻率更高的砷化镓单晶。
31.2、本技术中,通过对石墨、生长装置进行预处理,充分降低其含水率,减少石墨与水反应产生的co对晶体碳浓度的影响,保障晶体的高电阻率。
32.3、本技术中通过设置对应石英帽的tz7~tz9,有效保障对c与石英帽中sio2反应进程的精确控制,确保晶体内碳浓度的均匀性,保障其内部电阻率和迁移率等性能的均一
性。
附图说明
33.图1是本技术实施例1中生长装置的结构示意图。
34.图2是本技术实施例2中生长装置的结构示意图。
35.图3是本技术实施例1半绝缘砷化镓晶体的元素含量测试结果图。
36.图4是本技术实施例1半绝缘砷化镓晶体的元素含量测试结果图。
37.附图标记说明:1、vgf单晶炉;2、石英坩埚;3、石英帽;31、容纳槽;32、过渡管;4、pbn坩埚;5、第一温区;6、第二温区。
具体实施方式
38.制备例制备例1,一种石墨柱,其经过预处理得到,所述预处理的具体操作为,将石墨柱放入石英管内,将石英管置于烤炉中,连接真空装置密封,然后对石英管进行抽真空,真空度为9
×
10-4
pa,将石英管置于烤炉中,于200℃下烘烤4h即得。
39.制备例2,一种石墨柱,其经过预处理得到,所述预处理的具体操作为,将石墨柱放入石英管内,将石英管置于烤炉中,连接真空装置密封,然后对石英管进行抽真空,真空度为1
×
10-2
pa,将石英管置于烤炉中,于220℃下烘烤2h即得。
40.制备例3,一种石墨柱,与制备例1的区别在于,该石墨柱未进行预处理。
实施例
41.实施例1本技术公开了一种半绝缘砷化镓单晶体的制备方法,制备过程,采用半绝缘砷化镓单晶体的生长装置进行vgf法晶体生长,参阅图1,该生长装置包括vgf单晶炉1,vgf单晶炉1内装载有石英坩埚2,石英坩埚2内装载有pbn坩埚4,石英坩埚2开口上盖合有石英帽3。石英帽3主体内包括有容纳槽31,石英帽3底部设置有连通于容纳槽31的过渡管32,所述过渡管32的直径小于容纳槽31的宽度。
42.vgf单晶炉1包括有第一温区5和第二温区6,第一温区5对应石英坩埚2设置,第二温区6对应石英帽3设置。进一步的,第一温区5内包含tz1~tz6,第二温区6包含tz7~tz9,且tz1~tz9沿vgf单晶炉1轴向自下而上依次设置,各温区的温度独立控制。
43.该制备方法包括如下步骤:s1:将7n gaas多晶10kg、晶种与氧化硼30g放入4寸pbn坩埚4中,然后将pbn坩埚4转移至石英坩埚2内完成装料;再将直径50mm、厚度(长度)20mm的石墨柱(制备例1制得)放入石英帽3内的容纳槽31中,使石墨柱的圆形底面与容纳槽31保持接触,然后将石英帽3与石英坩埚2密封连接(焊接)。
44.s2:将步骤s1中密封连接的石英帽3与石英坩埚2装载至vgf单晶炉1中,且石英帽3位于vgf单晶炉1的tz7~tz9中,石英坩埚2位于vgf单晶炉1的tz1~tz6中。
45.s3:控制tz1~tz6升温至1238℃(化料温度),同时控制tz7~tz9升温至1000
±
50
℃。
46.s4:tz1~tz6达到1238℃(化料温度)后,保温6~12h进行化料;与此同时,控制tz7~tz9在30min内升温至1200
±
50℃并保温10h。
47.s5:待gaas多晶熔化后,使用vgf法进行晶体生长,其中tz1~tz6的冷却速率为2~6℃/h,温度梯度为0.1~5℃/cm;与此同时,控制温区tz7~tz9在1h内降温至1000℃
±
50℃并保温,保障石墨与石英反应并形成含量稳定的co气氛。
48.s6:降温出料,其中tz1~tz6,在1200~1238℃范围内,降温速率为2
±
1℃/h;在1000~1200℃范围内,降温速率为5~15℃/h;在50~1000℃范围内,降温速率为30
±
10℃/h;tz7~tz9在该过程中逐步降温至出炉温度即可,最终得到长度为200mm的半绝缘砷化镓晶体。
49.按照sj/t 11488-2015中规定的测试方法,对上述制得晶体的电阻率和迁移率进行测试,测试结果如下:晶体内径向电阻变化率(与电阻均值差异)=(测试点阻值/测试片均值)
×
100%晶体头尾电阻比值:头部均值/尾部均值=0.97。
50.元素含量测试结果如图3所示。
51.参照图3可知,si的含量位于1.14*10
13
~4.5*10
15 atoms
•
cm-3
之间,c的含量位于6*10
15
~2.0*10
16 atoms
•
cm-3
之间。
52.实施例2本技术公开了一种半绝缘砷化镓单晶体的制备方法,制备过程,采用半绝缘砷化镓单晶体的生长装置进行vgf法晶体生长,参阅图2,该生长装置包括vgf单晶炉1,vgf单晶炉1内装载有石英坩埚2,石英坩埚2内装载有pbn坩埚4,石英坩埚2开口上盖合有石英帽3。石英帽3主体内包括有容纳槽31,石英帽3底部设置有连通于容纳槽31的过渡管32,所述过渡管32的直径小于容纳槽31的宽度。
53.vgf单晶炉1包括有第一温区5和第二温区6,第一温区5内对应石英坩埚2设置,第二温区6对应石英帽3设置。进一步的,第一温区5内包含tz1~tz6,第二温区6包含tz7~tz9,且tz1~tz9沿vgf单晶炉1轴向自下而上依次设置,各温区的温度独立控制。
54.其制备方法包括如下步骤:s1:将7n gaas多晶24kg、晶种与氧化硼65g放入6寸pbn坩埚4中,然后将pbn坩埚4转移至石英坩埚2内完成装料;再将直径60mm、厚度(长度)20mm的石墨柱(制备例2制得)放入石英帽3内的容纳槽31中,石墨柱圆形底面与容纳槽31接触,然后将石英帽3与石英坩埚2密封连接。
55.s2:将步骤s1中密封连接的石英帽3与石英坩埚2装载至vgf单晶炉1中,且石英帽3
位于vgf单晶炉1的tz7~tz9中,石英坩埚2位于vgf单晶炉1的tz1~tz6中。
56.s3:控制tz1~tz6升温至1238℃(化料温度),同时控制tz7~tz9升温至1000
±
50℃。
57.s4:tz1~tz6达到1238℃(化料温度)后,保温6~10h进行化料;与此同时,控制tz7~tz9在30min内升温至1200
±
50℃并保温50h。
58.s5:待gaas多晶熔化后,使用vgf法进行晶体生长,其中tz1~tz6的冷却速率为5~10℃/h,温度梯度为3~8℃/cm;与此同时,控制tz7~tz9在1h内降温至1000℃
±
50℃并保温,保障石墨与石英反应并形成含量稳定的co气氛。
59.s6:降温出料,其中tz1~tz6,在1200~1238℃范围内,降温速率为2
±
1℃/h;在1000~1200℃范围内,降温速率为5~15℃/h;在50~1000℃范围内,降温速率为30
±
10℃/h;tz7~tz9在该过程中逐步降温至出炉温度即可,最终得到长度为200mm的半绝缘砷化镓晶体。
60.按照sj/t 11488-2015中规定的测试方法,对上述制得晶体的电阻率和迁移率进行测试,测试结果如下:晶体内径向电阻变化率=(测试点阻值/测试片均值)
×
100%晶体头尾电阻比值:头部均值/尾部均值=0.72。
61.元素含量测试结果如图4所示。
62.参照图4可知,si的含量位于1.14*10
13
~4.5*10
15 atoms
•
cm-3
之间,c的含量位于6*10
15
~2.0*10
16 atoms
•
cm-3
之间。
63.实施例3本技术公开了一种半绝缘砷化镓单晶体的制备方法,其与实施例1的区别在于,制备步骤如下:s1:将7n gaas多晶10kg、晶种与氧化硼30g放入4寸pbn坩埚4中,然后将pbn坩埚4转移至石英坩埚2内完成装料;再将直径50mm、厚度20mm的石墨柱(制备例1制得)放入石英帽3内的容纳槽31中,石墨柱圆形底面与容纳槽31接触,然后将石英帽3与石英坩埚2密封连接。
64.s2:将步骤s1中密封连接的石英帽3与石英坩埚2装载至vgf单晶炉1中,且石英帽3位于vgf单晶炉1的tz7~tz9中,石英坩埚2位于vgf单晶炉1的tz1~tz6中。
65.s3:控制tz1~tz6升温至1238℃(化料温度),同时控制tz7~tz9升温至1000
±
50℃。
66.s4:tz1~tz6达到1238℃(化料温度)后,保温6~12h进行化料;与此同时,控制tz7~tz9在30min内升温至1200
±
50℃并保温4h。
67.s5:待gaas多晶熔化后,使用vgf法进行晶体生长,其中tz1~tz6的冷却速率为0.1~5℃/h,温度梯度为2~7℃/cm;与此同时,控制tz7~tz9在1h内降温至1000℃
±
50℃并保温,保障石墨与石英反应并形成含量稳定的co气氛。
68.s6:降温出料,其中tz1~tz6,在1200~1238℃范围内,降温速率为2
±
1℃/h;在1000~1200℃范围内,降温速率为5~15℃/h;在50~1000℃范围内,降温速率为30
±
10℃/h;tz7~tz9在该过程中逐步降温至出炉温度即可,最终得到长度为200mm的半绝缘砷化镓晶体。
69.按照sj/t 11488-2015中规定的测试方法,对上述制得晶体的电阻率和迁移率进行测试,测试结果如下:晶体头尾电阻比值:头部均值/尾部均值=0.65。
70.实施例4本技术公开了一种半绝缘砷化镓单晶体的制备方法,其与实施例1的区别在于,步骤s1中,采用制备例3制得的石墨柱。
71.按照sj/t 11488-2015中规定的测试方法,对上述制得晶体的电阻率和迁移率进行测试,测试结果表明,不处理石墨水分导致同批次晶体的参数一致性差,同等工艺环境下得到的晶体电阻率可能是1
×
108ω
•
cm,也可能是5
×
108ω
•
cm,甚至晶体出现参数不合适而测不出的情况,单个晶体看有参数一致性较好的正常晶体。
72.实施例5,一种半绝缘砷化镓单晶体的制备方法,其与实施例1的区别在于,制备步骤如下:s1:将7n gaas多晶10kg、晶种与氧化硼30g放入4寸pbn坩埚4中,然后将pbn坩埚4转移至石英坩埚2内完成装料;再将直径30mm、厚度(长度)20mm的石墨柱(制备例1制得)放入石英帽3内的容纳槽31中,使石墨柱的圆形底面与石墨槽31保持接触,然后将石英帽3与石英坩埚2密封连接;s2:将步骤s1中密封连接的石英帽3与石英坩埚2装载至vgf单晶炉1中,且石英帽3位于vgf单晶炉1的tz7~tz9中,石英坩埚2位于vgf单晶炉1的tz1~tz6中;s3:控制tz1~tz6升温至1238℃(化料温度),同时控制tz7~tz9升温至1000
±
50℃;
s4:tz1~tz6达到1238℃(化料温度)后,保温6~12h进行化料;与此同时,控制tz7~tz9在30min内升温至1200
±
50℃并保温6h;s5:待gaas多晶熔化后,使用vgf法进行晶体生长,其中tz1~tz6的冷却速率为2~6℃/h,温度梯度为0.1~5℃/cm;与此同时,控制tz7~tz9在1h内降温至1000℃
±
50℃并保温,保障石墨与石英反应并形成含量稳定的co气氛;s6:降温出料,其中tz1~tz6,在1200~1238℃范围内,降温速率为1~3℃/h;在1000~1200℃范围内,降温速率为5~15℃/h;在50~1000℃范围内,降温速率为20~40℃/h;tz7~tz9在该过程中逐步降温至出炉温度即可,最终得到长度为200mm的半绝缘砷化镓晶体。
73.按照sj/t 11488-2015中规定的测试方法,对上述制得晶体的电阻率和迁移率进行测试,测试结果如下:晶体头尾电阻比值:头部均值/尾部均值=0.78。
74.对比例对比例1本技术提供一种半绝缘砷化镓单晶体的制备方法,制备过程中,采用半绝缘砷化镓单晶体的生长装置进行vgf法晶体生长,该生长装置包括vgf单晶炉1,vgf单晶炉1内装载有一石英坩埚2以及与之盖合的石英帽3,其中石英帽3的内设置有一容纳槽31,该容纳槽31的高度小于石英帽3的深度。
75.vgf单晶炉1上沿其轴向依次设置有tz1~tz6,任一温区均设置有独立的加热源,且石英坩埚2以及石英帽3均位于tz1~tz6的范围内。
76.该制备方法包括如下步骤:s1:将7n gaas多晶10kg、晶种与氧化硼30g放入4寸pbn坩埚4中,然后将pbn坩埚4转移至石英坩埚2内完成装料;再将直径50mm、厚度20mm的石墨柱放入石英帽3内的容纳槽31中,将石英帽3与石英坩埚2密封连接。
77.s2:将步骤s1中密封连接的石英帽3与石英坩埚2装载至vgf单晶炉1中。
78.s3:控制tz1~tz6升温至1238℃(化料温度)。
79.s4:tz1~tz6达到1238℃(化料温度)后,保温6~10h进行化料。
80.s5:待gaas多晶熔化后,使用vgf法进行晶体生长,其中tz1~tz6的冷却速率为1~5℃/h,温度梯度为2~6℃/cm。
81.s6:降温出料,其中tz1~tz6,在1200~1238℃范围内,降温速率为2
±
1℃/h;在1000~1200℃范围内,降温速率为5~15℃/h;在50~1000℃范围内,降温速率为30
±
10℃/
h;最终得到长度为200mm的半绝缘砷化镓晶体。
82.按照sj/t 11488-2015中规定的测试方法,对上述制得晶体的电阻率和迁移率进行测试,测试结果如下:由上表可知晶体尾部的数据反型,成为p型半导体晶体,高阻霍尔测不出,显示105。
83.对比例2本技术提供一种半绝缘砷化镓单晶体的制备方法,其与对比例1的区别在于,采用实施例1中半绝缘砷化镓单晶体的生长装置进行晶体生长,且控制tz7~tz9的温度一直在1200
±
50℃范围内。
84.具体制备步骤如下:s1:将7n gaas多晶10kg、晶种与氧化硼30g放入4寸pbn坩埚4中,然后将pbn坩埚4转移至石英坩埚2内完成装料;再将直径50mm、厚度(长度)20mm的石墨柱(制备例1制得)放入石英帽3内的容纳槽31中,石墨柱圆形底面与容纳槽31接触,然后将石英帽3与石英坩埚2密封连接。
85.s2:将步骤s1中密封连接的石英帽3与石英坩埚2装载至vgf单晶炉1中,且石英帽3位于vgf单晶炉1的tz7~tz9中,石英坩埚2位于vgf单晶炉1的tz1~tz6中。
86.s3:控制tz1~tz6升温至1238℃(化料温度),同时控制tz7~tz9升温至1200
±
50℃后保温。
87.s4:tz1~tz6达到1238℃(化料温度)后,保温8h进行化料;与此同时,控制tz7~tz9保持1200
±
50℃的温度。
88.s5:待gaas多晶熔化后,使用vgf法进行晶体生长,其中tz1~tz6的冷却速率为2~6℃/h,温度梯度为0.1~5℃/cm;与此同时,控制tz7~tz9保持1200
±
50℃的温度;保障石墨与石英反应并形成含量稳定的co气氛。
89.s6:降温出料,其中tz1~tz6,在1200~1238℃范围内,降温速率为2
±
1℃/h;在1000~1200℃范围内,降温速率为5~15℃/h;在50~1000℃范围内,降温速率为30
±
10℃/h;tz7~tz9在该过程中逐步降温至出炉温度即可,最终得到长度为200mm的半绝缘砷化镓晶体。
90.按照sj/t 11488-2015中规定的测试方法,对上述制得晶体的电阻率和迁移率进行测试,测试结果如下:
由上表可知晶体尾部的数据反型,成为p型半导体晶体,高阻霍尔测不出,显示105。
91.试验结果分析:(1)结合实施例1~5和对比例1~2可以看出,实施例1~5中,石墨与砷化镓晶体生长的石英坩埚位于不同温区,并通过控制石墨所在温区的温度达到合适的反应温度,从而实现对半绝缘砷化镓的掺碳;而对比例1中,采用常规vgf法进行半绝缘砷化镓的生长。试验结果表明,相比对比例1,实施例1~5所得晶体的电阻率分布明显更为均匀,晶体头尾电阻比值较小。
92.其原因可能在于,在本技术中,空间气氛中co含量通过反应进行控制,反应温度越高,反应向右移动;而反应时间越长,则空间气氛中co含量越高;同时,石墨(c)与石英管(sio2)的接触面积越大,co含量也越高。该反应进程容易控制,能够在生长装置中较为快速的产生co气体,使得生长装置各处的co含量相对均匀,进而保障砷化镓晶体中掺碳量的均匀性。而对比例1中,空间气氛中co含量主要通过石墨与水石英帽中释放的氧(石英帽及氧化硼产生)或石墨与水(石墨或石英帽产生)等反应来控制。由于高温环境下氧的释放速率较慢,导致空间气氛中co含量的提高和扩散极为缓慢,生长出的砷化镓晶体,其内部碳含量均匀性差,致使其电性能也存在差距。
93.对于对比例2,由于tz7~tz9始终处于1200
±
50℃的高温下,且石墨与石英一直接触,反应一直进行,co不断产生,导致晶体碳含量急速变化,晶体参数变化巨大,其波动大于8%,难以控制产品最终电阻率和迁移率。
94.本具体实施例仅仅是对本技术的解释,其并不是对本技术的限制,本领域技术人员在阅读完本说明书后可以根据需要对本实施例做出没有创造性贡献的修改,但只要在本技术的权利范围内都受到专利法的保护。