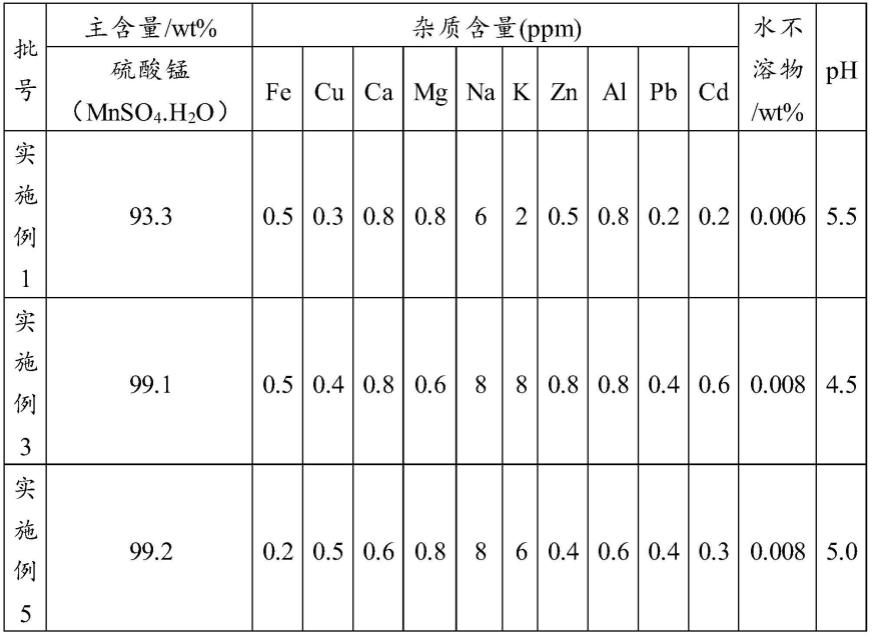
1.本发明涉及废旧正极材料回收技术领域,尤其涉及一种废旧锰酸锂正极材料的综合回收方法。
背景技术:2.近年来,中国电动汽车行业飞速发展,电动汽车销量日益增多。但电动汽车中的动力电池平均使用寿命为10年左右,早期进入市场的电动汽车目前已经进入电池退役阶段。根据市场研究预测,到2020年我国车用锂电池报废量将达32gwh,报废电池折算为质量将达到约50万吨;到2030年,车用锂电池报废量将达300gwh,报废锂电池量约300万吨。锂电池按其正极材料不同主要分为磷酸铁锂电池、三元锂电池、钛酸锂电池和锰酸锂电池等,而锰酸锂电池凭借其倍率性能好,制备比较容易,成本较低等优势,越来越被重视。目前,无论是制备三元正极材料还是锰酸锂正极材料的锂、锰等金属原料价格高昂且需求量大。因此从废旧锂电池中提取锂、锰等金属,既可以解决原材料供应问题,又将为社会创造巨大的利益。
3.对锰酸锂正极材料的回收,关键环节就是将其中的锂与锰进行分离提纯,然后再进一步制备相关锂盐和锰盐。申请号为201710380170.0的中国专利将拆解获得的锰酸锂正极材料加入有机酸进行还原浸出,再通过磷酸类萃取剂从浸出液中萃取锂,反萃液加入碳酸盐制备碳酸锂。该方法采用有机酸浸出,有价金属浸出率低,并且后期废水处理难度和成本也较高;同时通过萃取剂从含锰锂浸出液中萃取锂,其选择性较差,萃取效率低,生产成本较高。申请号为201811093693.8的中国专利利用纳滤膜技术,将酸化浸出液中的锂离子与不同于锂离子的其它阳离子分离,获得含锂溶液和含有其它阳离子的溶液,再采用反渗透技术分别对含锂溶液、含有其它阳离子的溶液进行浓缩富集;该工艺存在锂分离效率低,需要消耗大量水,锂富集浓度低,因此回收流程长,成本也较高。申请号为202110677455.7的中国专利将经预处理好的锰酸锂正极材料放入无机酸中,经高压反应后得到α-mno2或β-mno2或γ-mno2,从而制备出具有较大比表面积和多孔结构mno2,该产物可进一步用于电池正极材料和超级电容器电极材料。该方法虽然能很好地实现锰酸锂正极材料的循环利用,但在处理过程中难以控制杂质离子,所得材料的性能不够稳定,不适合广泛推广使用。
4.综上所述,目前废旧锰酸锂正极材料回收工艺存在有价金属回收率低、工艺流程繁长、生产效率低、回收处理成本高以及产品附加值低等问题。
技术实现要素:5.本发明解决的技术问题在于提供一种废旧锰酸锂正极材料的综合回收方法,该方法可回收电池级硫酸锰和电池级碳酸锂,且回收率高。
6.有鉴于此,本技术提供了一种废旧锰酸锂正极材料的综合回收方法,包括以下步骤:
7.a)将废旧锰酸锂正极材料与水混合,得到浆料,将所述浆料进行还原浸出,得到浸出液;
8.b)向所述浸出液中加入除杂剂进行除杂,再加入氧化剂,得到除杂后液;
9.c)将所述除杂后液进行高温结晶,离心分离后得到粗制硫酸锰晶体和含锂结晶母液;
10.d)将所述粗制硫酸锰晶体溶解后再次进行高温结晶,离心分离后得到精制硫酸锰晶体和结晶母液;
11.e)将所述精制硫酸锰晶体烘干,得到电池级硫酸锰,向所述含锂结晶母液中加入净化剂,反应后得到含锂净化后液;
12.f)将所述含锂净化后液进行沉锂,得到碳酸锂湿料和沉锂母液,将所述碳酸锂湿料进行洗涤、干燥,得到电池级碳酸锂。
13.优选的,步骤a)中,所述还原浸出的试剂为硫酸和还原剂,所述硫酸为98%的浓硫酸,调节体系的ph至0.5~3.0,所述还原剂选自双氧水、亚硫酸钠和硫代硫酸钠中的一种或多种。
14.优选的,步骤a)中,所述水和废旧锰酸锂正极材料的液固比为2:1~5:1。
15.优选的,步骤b)中,所述除杂剂选自碳酸钠、碳酸氢钠、碳酸铵、碳酸氢铵、氢氧化钠和氨水中的一种或多种,所述氧化剂选自双氧水、氯酸钠和次氯酸钠中的一种或多种。
16.优选的,步骤c)中,所述高温结晶的过程具体为:
17.将所述除杂后液打入结晶反应釜中进行高温结晶,待锰浓度达到80~120g/l时,将得到的结晶浆料进行离心分离,得到粗制硫酸锰晶体和含锂结晶母液。
18.优选的,步骤c)中,所述高温结晶的温度为100~200℃,反应压强为0.1~0.5mpa,时间为1~3h。
19.优选的,步骤d)中的高温结晶具体为:
20.将所述粗制硫酸锰晶体加入到纯水中溶解,再次打入结晶反应釜中进行高温结晶,待锰浓度达到80~120g/l时,离心分离后得到精制硫酸锰晶体和结晶母液。
21.优选的,步骤d)中,所述高温结晶的温度为100~200℃,反应压强为0.1~0.5mpa,时间为1~3h。
22.优选的,步骤e)中,所述净化剂选自氢氧化钠、氢氧化钾、氢氧化锂和氨水中的一种或多种,所述净化剂的浓度为5~30%,所述反应的ph值为10.0~12.0,所述反应的时间为0.5~1h。
23.优选的,所述沉锂的试剂为浓度为200~300g/l的碳酸钠溶液,所述沉锂的反应温度为50~100℃,时间为1~5h。
24.本技术提供了一种废旧锰酸锂正极材料的综合回收方法,其以废旧锰酸锂正极材料为回收对象,经过正极黑粉的还原浸出、浸出液的化学除杂、除杂液的结晶分离、粗制硫酸锰的重结晶制备电池级硫酸锰以及结晶分离母液制备电池级碳酸锂等步骤可实现锂和锰的综合回收;上述回收方法无需传统萃取工序和化学沉淀分离工序,本技术利用硫酸锰和硫酸锂的溶解度随温度变化的差异性实现了锂、锰的分离回收;本发明具有工艺简单稳定、生产效率高、生产成本低以及废水可实现零排放等优点,易于实现工业化生产,有价金属锰、锂的回收率高,制备得到的硫酸锰和碳酸锂品质优秀,具有极高的生产收益。
附图说明
25.图1为本发明提供的废旧锰酸锂正极材料的综合回收方法的流程示意图。
具体实施方式
26.为了进一步理解本发明,下面结合实施例对本发明优选实施方案进行描述,但是应当理解,这些描述只是为进一步说明本发明的特征和优点,而不是对本发明权利要求的限制。
27.鉴于现有技术中废旧锰酸锂正极材料回收处理的技术问题,本技术提供了一种废旧锰酸锂正极材料的综合回收方法,其通过废旧锰酸锂正极材料的还原浸出-浸出液通过加入沉淀剂进行铜、铁、铝等杂质的去除-除杂液在高温条件下,对锰和锂进行结晶分离-粗制硫酸锰的再经重结晶制备电池级硫酸锰-结晶分离母液制备电池级碳酸锂,流程如图1所示;经过上述一系列的操作,本技术可制备高品质的硫酸锰和碳酸锂。具体的,本发明实施例公开了一种废旧锰酸锂正极材料的综合回收方法,包括以下步骤:
28.a)将废旧锰酸锂正极材料与水混合,得到浆料,将所述浆料进行还原浸出,得到浸出液;
29.b)向所述浸出液中加入除杂剂进行除杂,再加入氧化剂,得到除杂后液;
30.c)将所述除杂后液进行高温结晶,离心分离后得到粗制硫酸锰晶体和含锂结晶母液;
31.d)将所述粗制硫酸锰晶体溶解后再次进行高温结晶,离心分离后得到精制硫酸锰晶体和结晶母液;
32.e)将所述精制硫酸锰晶体烘干,得到电池级硫酸锰,向所述含锂结晶母液中加入净化剂,反应后得到含锂净化后液;
33.f)将所述含锂净化后液进行沉锂,得到碳酸锂湿料和沉锂母液,将所述碳酸锂湿料进行洗涤、干燥,得到电池级碳酸锂。
34.在本技术提供的废旧锰酸锂正极材料的综合回收方法中,本技术首先进行了还原浸出,即将废旧锰酸锂正极材料与水混合,得到浆料,再将所述浆料进行还原浸出,得到浸出液;在此过程中,废旧锰酸锂正极材料在还原剂的作用下,其中的锰元素还原浸出。所述还原浸出的试剂为硫酸和还原剂,所述硫酸为98%的浓硫酸,调节体系的ph至0.5~3.0,所述还原剂选自双氧水、亚硫酸钠和硫代硫酸钠中的一种或多种;在具体实施例中,所述还原剂选自亚硫酸钠或硫代硫酸钠,调节体系的ph至0.5~2.0。所述水和废旧锰酸锂正极材料的液固比为2:1~5:1,更具体的,所述水和废旧锰酸锂正极材料的液固比为3:1~4:1。所述还原浸出的温度为50~100℃,时间为1~5h;更具体的,所述还原浸出的温度为60~80℃,时间为2~4h。
35.本技术再进行化学除杂,在所述浸出液中加入除杂剂进行除杂,以将浸出液中的铜、铁、铝等杂质去除,再加入氧化剂,搅拌压滤后即得到除杂后液;在此过程中,所述除杂剂选自碳酸钠、碳酸氢钠、碳酸铵、碳酸氢铵、氢氧化钠和氨水中的一种或多种,所述氧化剂将杂质离子如铁等完全氧化,具体选自双氧水、氯酸钠和次氯酸钠中的一种或多种。
36.按照本发明,将上述得到的除杂后液在结晶反应釜中进行硫酸锰的高温结晶,优选待锰浓度达到80~120g/l时,将结晶浆料放入离心机中进行离心分离,得到粗制硫酸锰
晶体和含锂结晶母液;其中,粗制硫酸锰晶体用于制备电池级硫酸锰,含锂结晶母液用于制备碳酸锂;在此过程中,除杂后液中含有锰,在高温结晶的过程中锰以结晶的方式分离出来。然后将所述粗制硫酸锰晶体加入到纯水中进行溶解,搅拌溶解后再次打入结晶反应釜中进行硫酸锰的高温结晶,待锰浓度达到80~120g/l时,将结晶浆料放入离心机中进行离心分离,得到精制硫酸锰晶体和重结晶母液,精制硫酸锰晶体经烘干制得电池级硫酸锰产品,重结晶母液返回步骤一中用于调浆。在上述过程中,所述高温结晶的温度为100~200℃,反应压强为0.1~0.5mpa,时间为1~3h;更具体的,所述高温结晶的温度为120~180℃,反应压强为0.2~0.4mpa,时间为1.5~2.5h。
37.本技术然后向所述含锂结晶母液中加入净化剂,反应后得到含锂净化后液。在上述过程中,所述净化剂选自氢氧化钠、氢氧化钾、氢氧化锂和氨水中的一种或多种,所述净化剂的浓度为5~30%,所述反应的ph值为10.0~12.0,所述反应的时间为0.5~1h;更具体的,所述净化剂的浓度为10~20%,所述反应的时间为0.6~0.8h。上述过程用以净化残余锰以及杂质元素。
38.本技术最后将所述含锂净化后液进行沉锂,得到碳酸锂湿料和沉锂母液,将所述碳酸锂湿料进行洗涤、干燥,得到电池级碳酸锂。在此过程中,所述沉锂的试剂为浓度为200~300g/l的碳酸钠溶液,所述沉锂的反应温度为50~100℃,时间为1~5h,具体的,所述沉锂的试剂为浓度为220~270g/l的碳酸钠溶液,所述沉锂的反应温度为60~80℃,时间为2~4h;所述洗涤的温度为50~100℃,洗涤次数为1~3次,洗涤液固比为1:1~3:1;所述烘干温度为100~200℃,烘干时间为5~10h。
39.在本技术中,所述废旧锰酸锂正极材料为电池拆解厂产出的正极粉料、正极工厂产出正极边角料中的至少一种。
40.为了进一步理解本发明,下面结合实施例对本发明提供的废旧锰酸锂正极材料的综合回收方法进行详细说明,本发明的保护范围不受以下实施例的限制。
41.实施例1
42.将电池拆解厂收购的废旧锰酸锂正极材料(li:3.2%;mn:60%)100kg与水和重结晶母液按液固比为2:1制成浆料,向其中加入98%硫酸调节体系的ph值为0.5,然后按所需理论量的1.1倍加入76.1kg亚硫酸钠,控制反应温度为85℃,搅拌浸出2h后压滤得到400l浸出液和15kg酸浸渣;向浸出液中加入5kg碳酸钠进行除杂,调节体系ph为5.0后再加入1.1kg双氧水,搅拌反应1h后压滤;压滤后得到除杂后液;
43.上述除杂后液打入高温结晶釜中,结晶温度为120℃,保温1.5h,后离心分离,得到的粗制硫酸锰晶体重新打入到新的除杂后液进行浓缩;如此往复多次之后,待锰浓度达到120g/l时,将浓缩液再进行一次高温结晶手段,将粗制硫酸锰晶体再与280l水调浆溶解,待溶解完全后重新打入高温结晶釜中进行高温重结晶,结晶温度为120℃,保温1.5h后离心分离,精制硫酸锰晶体经烘干制得180.7kg电池级硫酸锰产品1#。锰的回收率达98%,硫酸锰主含量为99.3%。
44.实施例2
45.本实施例实在实施例1的基础上做了进一步优化,具体是:
46.得到的含锂结晶母液中加入30%的氢氧化钠溶液6kg,调节体系ph值为11.0,保持温度为50℃,搅拌1h后压滤得到含锂净化后液;净化后液泵入反应釜后,加入按所需理论量
1.1倍的260g/l碳酸钠溶液93.2l,保持温度为80℃,搅拌反应1h后进行离心分离,得到碳酸锂湿料18.42kg;按液固比为1:1,在温度为90℃条件下洗涤两次,再将离心分离出来的物料在120℃烘箱中干燥5h,最终得到16.13kg电池级碳酸锂。锂的回收率达95.2%,碳酸锂主含量为99.6%。
47.实施例3
48.将正极工厂产出的废旧锰酸锂正极边角料(li:3.5%;mn:61%)300kg与水和重结晶母液按液固比为3:1制成浆料,向其中加入98%硫酸调节体系的ph值为1.5,然后按所需理论量的1.8倍加入132kg双氧水,控制反应温度为50℃,搅拌浸出5h后压滤得到1200l浸出液和10kg酸浸渣;向浸出液中加入13.8kg氢氧化钠进行除杂,调节体系ph为4.5后再加入1.6kg氯酸钠,搅拌反应1h后压滤,压滤后得到除杂后液;
49.上述除杂后液打入高温结晶釜中,结晶温度为160℃,保温3h,后离心分离,得到的粗制硫酸锰晶体重新打入到新的除杂后液进行浓缩;如此往复多次之后,待锰浓度达到100g/l时,将浓缩液再进行一次高温结晶手段,将粗制硫酸锰晶体再与1830l水调浆溶解,待溶解完全后重新打入高温结晶釜中进行高温重结晶,结晶温度为160℃,保温2.5h后离心分离,精制硫酸锰晶体经烘干制得557.84kg电池级硫酸锰产品2#。锰的回收率达98.3%,硫酸锰主含量为99.1%。
50.实施例4
51.本实施例实在实施例3的基础上做了进一步优化,具体是:
52.得到的含锂结晶母液中加入10%的氢氧化锂溶液10kg,调节体系ph值为10,保持温度为30℃,搅拌0.5h后压滤得到含锂净化后液;净化后液泵入反应釜后,加入按所需理论量1.3倍的270g/l碳酸钠溶液382.8l,保持温度为95℃,搅拌反应5h后进行离心分离,得到碳酸锂湿料61.66kg;按液固比为3:1加入纯水,在温度为90℃条件下洗涤三次,再将离心分离出来的物料在200℃烘箱中干燥8h,最终得到53.39kg电池级碳酸锂。锂的回收率达96.3%,碳酸锂主含量为99.6%。
53.实施例5
54.将电池拆解厂收购的废旧锰酸锂正极材料(li:3.0%;mn:58.8%)500kg与水和重结晶母液按液固比为5:1制成浆料,向其中加入98%硫酸调节体系的ph值为2.0,然后按所需理论量的1.5倍加入60.45kg硫代硫酸钠,控制反应温度为60℃,搅拌浸出3h后压滤得到3200l浸出液和70kg酸浸渣;向浸出液中加入10kg氨水进行除杂,调节体系ph为5.0后再加入2.5kg次氯酸钠,搅拌反应0.5h后压滤,压滤后得到除杂后液。
55.上述除杂后液打入高温结晶釜中,结晶温度为180℃,保温2h,后离心分离,得到的粗制硫酸锰晶体重新打入到新的除杂后液进行浓缩;如此往复多次之后,待锰浓度达到110g/l时,将浓缩液再进行一次高温结晶手段,将粗制硫酸锰晶体再与9126.3l水调浆溶解,待溶解完全后重新打入高温结晶釜中进行高温重结晶,结晶温度为180℃,保温2h后离心分离,精制硫酸锰晶体经烘干制得887.24kg电池级硫酸锰产品1#。锰的回收率达98.2%,硫酸锰主含量为99.2%。
56.实施例6
57.本实施例实在实施例5的基础上做了进一步优化,具体是:
58.得到的含锂结晶母液中加入20%的氢氧化钾溶液65kg,调节体系ph值为12,常温
下搅拌1h后压滤得到含锂净化后液;净化后液泵入反应釜后,加入按所需理论量1.5倍的280g/l碳酸钠溶液608.4l,保持温度为100℃,搅拌反应3h后进行离心分离,得到碳酸锂湿料88.1kg;按液固比为2:1,在温度为95℃条件下洗涤一次,再将离心分离出来的物料在160℃烘箱中干燥6h,最终得到75.3kg电池级碳酸锂。锂的回收率达94.7%,碳酸锂主含量为99.7%。
59.上述实施例1、实施例3和实施例5制得的硫酸锰的技术指标见表1,实施例2、实施例4和实施例6碳酸锂产品技术指标见表2:
60.表1实施例1、3、5制备的电池级硫酸锰技术指标
[0061][0062]
表2实施例2、4、6制备的电池级碳酸锂技术指标
[0063]
[0064][0065]
根据表1可知,经过实施例提供的方法回收的硫酸锰的含量很高,杂质含量极低,由表2可知,经过实施例提供的方法回收的碳酸锂的含量很高,杂质含量极低,由此可知,本技术提供的回收方法能够得到电池级的硫酸锰和碳酸锂。
[0066]
以上实施例的说明只是用于帮助理解本发明的方法及其核心思想。应当指出,对于本技术领域的普通技术人员来说,在不脱离本发明原理的前提下,还可以对本发明进行若干改进和修饰,这些改进和修饰也落入本发明权利要求的保护范围内。
[0067]
对所公开的实施例的上述说明,使本领域专业技术人员能够实现或使用本发明。对这些实施例的多种修改对本领域的专业技术人员来说将是显而易见的,本文中所定义的一般原理可以在不脱离本发明的精神或范围的情况下,在其它实施例中实现。因此,本发明将不会被限制于本文所示的这些实施例,而是要符合与本文所公开的原理和新颖特点相一致的最宽的范围。