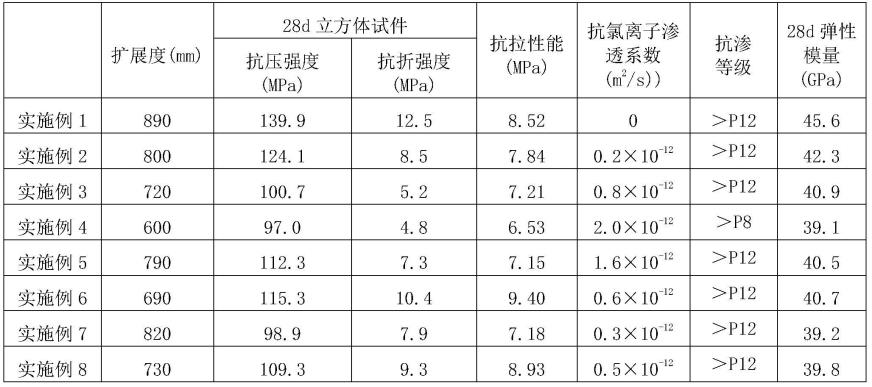
1.本发明涉及混凝土制备领域,具体涉及一种应用机制砂的超高性能混凝土及其制备方法。
背景技术:2.高强混凝土指的是强度等级为c60及其以上的混凝土,c100强度等级以上的混凝土称为超高强混凝土。它是用水泥、砂、石原材料外加减水剂或同时外加粉煤灰、f矿粉、矿渣、硅粉等混合料,经常规工艺生产而获得高强的混凝土。
3.高强混凝土作为一种新的建筑材料,以其抗压强度高、抗变形能力强、密度大、孔隙率低的优越性,在高层建筑结构、大跨度桥梁结构以及某些特种结构中得到广泛的应用。高强混凝土最大的特点是抗压强度高,一般为普通强度混疑土的4~6倍,故可减小构件的截面,因此最适宜用于高层建筑。试验表明,在一定的轴压比和合适的配箍率情况下,高强混凝土框架柱具有较好的抗震性能。而且柱截面尺寸减小,减轻自重,避免短柱,对结构抗震也有利,而且提高了经济效益。高强混凝土材料为预应力技术提供了有利条件,可采用高强度钢材和人为控制应力,从而大大地提高了受弯构件的抗弯刚度和抗裂度。因此世界范围内越来越多地采用施加预应力的高强混凝土结构,应用于大跨度房屋和桥梁中。但是,现有的混凝土仍然具有一些下述的缺陷:
4.现有技术中的超高性能混凝土,大多采用石英砂提高其强度,而石英砂价格较高,进而导致超高性能混凝土的成本较高。
5.高强混凝土是以强度的大小来确定的,单纯地高强度不一定具有高性能,尤其是在严酷的环境下,它的耐久性就更差,从而寿命较短。因此,现有技术中高强度混凝土抗腐蚀性能较差、耐久性差、寿命较短。
6.现有技术中,以管道制品为例,它的设计、使用年限一般都是在50-100年,而该管道通常都是预埋在几米或几十米深的地下,期间经过长期环境影响,导致混凝土开裂、钢筋锈蚀、耐久性降低,从而引发严重后果,以至重新开挖、修复,提高了人工费、材料费等。因此,现有技术中高强混凝土所制产品修复成本高。
7.本技术人发现现有技术至少存在以下问题:
8.1、现有技术中的超高性能混凝土大多采用石英砂提高其强度,导致超高强性能混凝土成本较高。
9.2、现有技术中高强度混凝土抗腐蚀性能较差、长期耐久性差、寿命较短。
10.3、现有技术中高强混凝土所制产品修复成本高。
技术实现要素:11.本发明的目的在于提供一种应用机制砂的超高性能混凝土及其制备方法,以解决现有技术中的高强度混凝土抗腐蚀性能较差、长期耐久性差、寿命较短的技术问题。
12.为实现上述目的,本发明提供了以下技术方案:
13.本发明提供的一种应用机制砂的超高性能混凝土,包括下述重量份的原料:机制砂100-130份;水泥40-60份;硅灰10-20份;微珠15-20份;矿粉8-15份;膨胀剂3-5份;水16-20份;减水剂3-5份;钢纤维5-20份。
14.进一步的,各原料的重量份分别为:机制砂110-120份;水泥45-55份;硅灰12-18份;微珠16-19份;矿粉10-13份;膨胀剂3.5-4.5份;水17-19份;减水剂3.5-4.5份;钢纤维10-15份。
15.进一步的,各原料的重量份分别为:机制砂120份;水泥50份;硅灰15份;微珠18份;矿粉12份;膨胀剂4份;水18份;减水剂4份;钢纤维12份。
16.进一步的,所述机制砂的含泥量≤1%、细度模数3.0~2.3;
17.所述水泥的强度等级≥52.5级、比表面积≥300
㎡
/kg、初凝时间≥45min、终凝时间≤600min;
18.所述矿粉的等级为s95级、流动度比≥95%、7d活性指数≥70%、28d活性指数≥95%;
19.所述硅灰的sio2含量≥90%、需水量比≤125%、活性指数≤105%;
20.所述微珠的需水量比≤105%、28天活性指数≥90%、比表面积≥2000
㎡
/kg;
21.所述减水剂为聚羧酸减水剂,其减水率≥30%、碱含量≤3.5%、含气量《2.0%,且不含有氯离子;
22.所述钢纤维采用表面镀铜微细光圆钢纤维,其抗拉强度≥2850mpa;
23.所述膨胀剂的28d抗压强度≥42.5mpa。
24.本发明提供的应用机制砂的超高性能混凝土的制备方法,包括下述步骤:
25.s1、按配比准备原料;
26.s2、将步骤s1中准备的机制砂、水泥、硅灰、微珠、矿粉和膨胀剂倒入搅拌机中,进行初始搅拌;
27.s3、将步骤s1中准备的水、减水剂继续倒入搅拌机中,连续搅拌4~6min;在连续搅拌的过程中,将钢纤维倒入正在搅拌的拌合物中,将钢纤维均匀分布在拌合物内,得到混凝土成品。
28.进一步的,所述步骤s2中,初始搅拌的时间为0.5~2min。
29.本发明中超高性能混凝土的主要设计原理:先是通过对不同细度的材料进行合理配比,找出最紧密实的状态,后在胶凝材料中掺入具有良好活性的超细粒级材料,使其参与到水化过程中,使整个材料的密实度得到了更加密实状态。最终使材料内部的孔隙减小到最低程度,以获得超高力学性能和超高耐久性。
30.基于上述技术方案,本发明实施例至少可以产生如下技术效果:
31.(1)本发明提供的应用机制砂的超高性能混凝土及其制备方法,得到的超高性能混凝土是一种新型的高技术混凝土,它选用优质原材料、降低水灰比、提高密实度,能最大限度地延长混凝土结构的使用年限,提高工程使用寿命。原料中的水泥与水混合形成水泥浆体,起胶凝作用;加入微珠可以进行二次水化,在整个混凝土中可以改善其和易性;加入的硅灰的分散性较好,它能均匀地填充于水泥颗粒空隙之中,使混凝土中空隙较少,起到增加强度、增加紧密性的作用;加入的膨胀剂代替等量的水泥,起到减少混凝土收缩作用;进一步通过高性能减水剂的使用,使超高性能混凝土获得了极低的水灰比,因此,超高性能混
凝土内部没有多余的水份,混凝土整体的密实度提高;最后,钢纤维以类似钢筋材料进行添加,使材料有一定的加筋体系,进一步使混凝土表现出更好的力学性能和韧性;
32.(2)本发明提供的应用机制砂的超高性能混凝土及其制备方法,得到的超高性能混凝土不仅具有超高的力学性能,还具有抗腐蚀性能良好、长期耐久性好、寿命长的优势,并且避免了石英砂的使用,制备成本低,修复成本也较低。
具体实施方式
33.一、材料说明
34.机制砂:含泥量≤1%、细度模数3.0~2.3;
35.水泥:强度等级≥52.5级、比表面积≥300
㎡
/kg、初凝时间≥45min、终凝时间≤600min;
36.矿粉:等级为s95级、流动度比≥95%、7d活性指数≥70%、28d活性指数≥95%;
37.硅灰:sio2含量≥90%、需水量比≤125%、活性指数≤105%;
38.微珠:需水量比≤105%、28天活性指数≥90%、比表面积≥2000
㎡
/kg;
39.减水剂:聚羧酸减水剂,其减水率≥30%、碱含量≤3.5%、含气量《2.0%,且不含有氯离子;
40.钢纤维:采用镀表面镀铜微细光圆钢纤维,其抗拉强度≥2850mpa;
41.膨胀剂:28d抗压强度≥42.5mpa。
42.二、制备实施例
43.实施例1:
44.1.1、原料
45.按重量份:机制砂120份;水泥50份;硅灰15份;微珠18份;矿粉12份;膨胀剂4份;水18份;减水剂4份;钢纤维12份。
46.1.2、制备方法
47.s1、按配比准备原料;
48.s2、将步骤s1中准备的机制砂、水泥、硅灰、微珠、矿粉和膨胀剂倒入搅拌机中,初始搅拌1.2min,搅拌速率为28r/min;
49.s3、保持搅拌速率为28r/min,将步骤s1中准备的水、减水剂继续倒入搅拌机中,连续搅拌5min;保持搅拌速率为28r/min,将钢纤维倒入正在搅拌的拌合物中,将钢纤维均匀分布在拌合物内,得到混凝土拌合物。
50.1.3、制备混凝土试块
51.s1、试块成型:停止搅拌后,将混凝土拌合物装入试模,成型过程中可以进行适当振动,保证拌合物中的气泡排出,直至完成。
52.s2、静停:成型后,需将与空气直接接触的混凝土拌合物表面采用塑料薄膜覆盖,然后静停(等待混凝土的硬化),静停12h,硬化完成;
53.s3、养护:在静停完成后,对超高性能混凝土试块进行蒸气养护,养护的主要指标包括:蒸汽湿度不低于80%,养护恒温温度在60℃,恒温时间在48小时。养护完成后即可得到完成的超高性能混凝土试块。
54.实施例2:
55.2.1、原料
56.机制砂120份;水泥45份;硅灰18份;微珠16份;矿粉13份;膨胀剂3.5份;水19份;减水剂3.5份;钢纤维15份。
57.2.2、制备方法
58.s1、按配比准备原料;
59.s2、将步骤s1中准备的机制砂、水泥、硅灰、微珠、矿粉和膨胀剂倒入搅拌机中,初始搅拌2min,搅拌速率为20r/min;
60.s3、保持搅拌速率为20r/min,将步骤s1中准备的水、减水剂继续倒入搅拌机中,连续搅拌6min;保持搅拌速率为20r/min,将钢纤维倒入正在搅拌的拌合物中,将钢纤维均匀分布在拌合物内,得到混凝土拌合物。
61.2.3、制备混凝土试块
62.按实施例1中的方法制备。
63.实施例3:
64.3.1、原料
65.机制砂100份;水泥60份;硅灰10份;微珠20份;矿粉8份;膨胀剂3份;水16份;减水剂3份;钢纤维5份。
66.3.2、制备方法
67.s1、按配比准备原料;
68.s2、将步骤s1中准备的机制砂、水泥、硅灰、微珠、矿粉和膨胀剂倒入搅拌机中,初始搅拌0.5min,搅拌速率为35r/min;
69.s3、保持搅拌速率为35r/min,将步骤s1中准备的水、减水剂继续倒入搅拌机中,连续搅拌4min;保持搅拌速率为35r/min,将钢纤维倒入正在搅拌的拌合物中,将钢纤维均匀分布在拌合物内,得到混凝土拌合物。
70.3.3、制备混凝土试块
71.按实施例1中的方法制备。
72.实施例4:
73.4.1、原料
74.机制砂130份;水泥40份;硅灰20份;微珠15份;矿粉15份;膨胀剂5份;水20份;减水剂5份;钢纤维20份。
75.4.2、制备方法
76.s1、按配比准备原料;
77.s2、将步骤s1中准备的机制砂、水泥、硅灰、微珠、矿粉和膨胀剂倒入搅拌机中,初始搅拌2min,搅拌速率为30r/min;
78.s3、保持搅拌速率为30r/min,将步骤s1中准备的水、减水剂继续倒入搅拌机中,连续搅拌5min;保持搅拌速率为30r/min,将钢纤维倒入正在搅拌的拌合物中,将钢纤维均匀分布在拌合物内,得到混凝土拌合物。
79.4.3、制备混凝土试块
80.按实施例1中的方法制备。
81.实施例5:
82.5.1、原料
83.机制砂110份;水泥55份;硅灰12份;微珠19份;矿粉10份;膨胀剂4.5份;水17份;减水剂4.5份;钢纤维10份。
84.5.2、制备方法
85.s1、按配比准备原料;
86.s2、将步骤s1中准备的机制砂、水泥、硅灰、微珠、矿粉和膨胀剂倒入搅拌机中,初始搅拌2min,搅拌速率为25r/min;
87.s3、保持搅拌速率为25r/min,将步骤s1中准备的水、减水剂继续倒入搅拌机中,连续搅拌6min;保持搅拌速率为25r/min,将钢纤维倒入正在搅拌的拌合物中,将钢纤维均匀分布在拌合物内,得到混凝土拌合物。
88.5.3、制备混凝土试块
89.按实施例1中的方法制备。
90.实施例6:
91.6.1、原料
92.机制砂130份;水泥55份;硅灰20份;微珠19份;矿粉8份;膨胀剂5份;水20份;减水剂4.5份;钢纤维15份。
93.6.2、制备方法
94.s1、按配比准备原料;
95.s2、将步骤s1中准备的机制砂、水泥、硅灰、微珠、矿粉和膨胀剂倒入搅拌机中,初始搅拌2min,搅拌速率为30r/min;
96.s3、保持搅拌速率为30r/min,将步骤s1中准备的水、减水剂继续倒入搅拌机中,连续搅拌4min;保持搅拌速率为30r/min,将钢纤维倒入正在搅拌的拌合物中,将钢纤维均匀分布在拌合物内,得到混凝土拌合物。
97.6.3、制备混凝土试块
98.按实施例1中的方法制备。
99.实施例7:
100.7.1、原料
101.机制砂125份;水泥45份;硅灰20份;微珠15份;矿粉10份;膨胀剂4份;水18份;减水剂3.5份;钢纤维10份。
102.7.2、制备方法
103.s1、按配比准备原料;
104.s2、将步骤s1中准备的机制砂、水泥、硅灰、微珠、矿粉和膨胀剂倒入搅拌机中,初始搅拌2min,搅拌速率为30r/min;
105.s3、保持搅拌速率为30r/min,将步骤s1中准备的水、减水剂继续倒入搅拌机中,连续搅拌6min;保持搅拌速率为30r/min,将钢纤维倒入正在搅拌的拌合物中,将钢纤维均匀分布在拌合物内,得到混凝土拌合物。
106.7.3、制备混凝土试块
107.按实施例1中的方法制备。
108.实施例8:
109.8.1、原料
110.机制砂105份;水泥55份;硅灰18份;微珠15份;矿粉10份;膨胀剂3份;水17份;减水剂4.5份;钢纤维18份。
111.8.2、制备方法
112.s1、按配比准备原料;
113.s2、将步骤s1中准备的机制砂、水泥、硅灰、微珠、矿粉和膨胀剂倒入搅拌机中,初始搅拌1min,搅拌速率为35r/min;
114.s3、保持搅拌速率为35r/min,将步骤s1中准备的水、减水剂继续倒入搅拌机中,连续搅拌5min;保持搅拌速率为35r/min,将钢纤维倒入正在搅拌的拌合物中,将钢纤维均匀分布在拌合物内,得到混凝土拌合物。
115.8.3、制备混凝土试块
116.按实施例1中的方法制备。
117.三、实验例
118.1、检测实施例1-8中制备的混凝土试块的性能
119.(1)检测方法或检测标准
120.抗压强度、抗折强度检测标准采用gb/t50081-2019《混凝土物理力学性能试验方法标准》;
121.抗氯离子渗透系数检测标准采用gb/t 50082-2009《普通混凝土长期性能和耐久性能试验方法标准》;
122.弹性模量的检测标准采用gb/t31387-2015《活性粉末混凝土》;
123.抗渗性能、抗拉性能的检测标准采用t/cbmf 37-2018/t/ccpa 7-2018《超高性能混凝土基本性能与试验方法》。
124.(2)检测结果,如下表1所示:
125.表1混凝土试块的性能检测结果
[0126][0127]
由表1可知,本发明实施例1-8中制备的超高性能混凝土具有超高强度,且具有较高的抗氯离子渗透系数和较高的抗渗等级,本发明通过提高密实度,降低内部空隙率,使超高性能混凝土具有极低的渗透性,可大幅度提高混凝土结构的使用寿命,减小修复成本,其优异的抗氯离子渗透性能为混凝土结构在恶劣环境下提供了保护。因此,本发明实施例1-8
中制备的超高性能混凝土具有抗腐蚀性能好、长期耐久性好、使用寿命长。