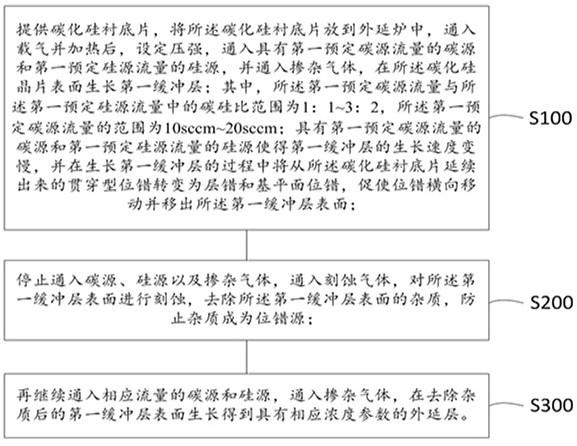
1.本发明涉及碳化硅外延层生长技术领域,具体为一种碳化硅外延层生长方法。
背景技术:2.碳化硅性能优异,在高压大功率应用场景下有巨大的应用价值。但是,由于位错的存在,器件的性能和良率都受到影响。
3.在当前普遍的工艺水平下,在碳化硅衬底表面外延形成碳化硅外延层过程中,会将碳化硅衬底大部分基平面位错转变为贯穿型位错,但是,贯穿型位错基本上全部会延伸进入外延层。因此,常规外延工艺获得的外延层位错密度并不会降低,成为限制碳化硅器件性能优化和成本控制的关键技术问题之一。
技术实现要素:4.本发明的目的在于常规外延工艺获得的外延层位错密度高的问题,提供了一种碳化硅外延层生长方法。
5.为了实现上述目的,本发明提供一种碳化硅外延层生长方法,包括以下步骤:提供碳化硅衬底片,将所述碳化硅衬底片放到外延炉中,通入载气并加热后,设定压强,通入具有第一预定碳源流量的碳源和第一预定硅源流量的硅源,并通入掺杂气体,在所述碳化硅晶片表面生长第一缓冲层;其中,所述第一预定碳源流量与所述第一预定硅源流量中的碳硅比范围为1:1~3:2,所述第一预定碳源流量的范围为10 sccm~20 sccm;具有第一预定碳源流量的碳源和第一预定硅源流量的硅源使得第一缓冲层的生长速度变慢,并在生长第一缓冲层的过程中将从所述碳化硅衬底片延续出来的贯穿型位错转变为层错和基平面位错,促使位错横向移动并移出所述第一缓冲层表面;停止通入碳源、硅源以及掺杂气体,通入刻蚀气体,对所述第一缓冲层表面进行刻蚀,去除所述第一缓冲层表面的碳杂质,防止碳杂质成为位错源;再继续通入相应流量的碳源和硅源,通入掺杂气体,在去除杂质后的第一缓冲层表面生长得到具有相应浓度参数的外延层。
6.作为一种可实施方式,再继续通入相应流量的碳源和硅源,通入掺杂气体,在去除杂质后的第一缓冲层表面生长得到具有相应浓度参数的外延层的步骤具体包括;继续通入具有第二预定碳源流量的碳源和第二预定硅源流量的硅源,通入掺杂气体,在所述第一缓冲层表面形成第二缓冲层,其中,具有第二预定碳源流量的碳源和第二预定硅源流量的硅源使得第二缓冲层的生长速度变快,并在生长第二缓冲层的过程中将从所述第一缓冲层延续出来的残留的基平面位错转化为贯穿型位错,促使位错纵向移动,使得从所述第二缓冲层延伸到后续形成的外延层中的位错为贯穿型位错;再继续通入相应流量的碳源和硅源,通入掺杂气体,在去除杂质后的第二缓冲层表面生长得到具有相应浓度参数的外延层。
7.作为一种可实施方式,所述第二预定碳源流量的范围为:60sccm~100sccm,所述第
二预定碳源流量与所述第二预定硅源流量中的碳硅比范围为4:5~1:1。
8.作为一种可实施方式,在所述碳化硅衬底片表面生长第一缓冲层时设定压强范围为30~80 torr;在所述第一缓冲层表面生长第二缓冲层时设定压强范围为80~120 torr;在所述第二缓冲层表面生长外延层时设定压强范围为80-120 torr。
9.作为一种可实施方式,在生长第一缓冲层时通入的掺杂气体具有第一预定流量,具有第一预定流量的掺杂气体使得形成的所述第一缓冲层具有相应的第一预定掺杂浓度,所述第一预定掺杂浓度与所述碳化硅衬底片的掺杂浓度一致,用于防止所述碳化硅衬底片与所述第一缓冲层之间由于掺杂浓度差异大而导致产生界面位错;在生长第二缓冲层时通入的掺杂气体具有第二预定流量,具有第二预定流量的掺杂气体使得形成的所述第二缓冲层具有相应的第二预定掺杂浓度,其中,所述第二预定掺杂浓度小于所述第一预定掺杂浓度但大于后续形成的所述外延层的掺杂浓度,用于对所述第一缓冲层的掺杂浓度与所述后续形成的外延层的掺杂浓度进行中间过渡,防止因掺杂浓度差异大导致晶格畸变而产生新的缺陷。
10.作为一种可实施方式,所述第一缓冲层的厚度范围为0.5~2.0微米,所述第二缓冲层的厚度范围为0.5~2.0微米。
11.作为一种可实施方式,所述贯穿型位错包括螺位错tsd和刃位错ted。
12.作为一种可实施方式,所述碳化硅衬底片为n型碳化硅晶圆,所述碳化硅衬底片的掺杂浓度范围为10
18
~10
19 cm-3
,所述碳化硅衬底片的总位错密度103~10
4 cm-3
。
13.作为一种可实施方式,所述掺杂气体包括含氮气体,所述含氮气体包括氮气;所述载气为氢气;所述刻蚀气体为氢气。
14.作为一种可实施方式,所述硅源为硅烷和三氯硅烷其中的一种或两种;所述碳源为甲烷、乙烯和丙烯其中的一种或几种。
15.本发明的有益效果:本发明提供了一种碳化硅外延层生长方法,通过通入具有第一预定碳源流量的碳源和第一预定硅源流量的硅源,在碳化硅衬底片表面生成第一缓冲层,使得通过对碳硅流量比以及具体通入的碳源流量的调整,促使从碳化硅衬底片延伸出来的贯穿型位错在第一缓冲层的生长过程中转变为层错和基平面位错,进行横向移动并移出所述晶体的第一缓冲层,从而减少从所述第一缓冲层进入外延层的位错数量;并通过通入具有第一预定碳源流量的碳源和第一预定硅源流量的硅源,在所述第一缓冲层表面生成第二缓冲层,使得通过对碳硅流量比以及具体通入的碳源流量的调整,促使从碳化硅衬底片延伸出来的基平面位错在第一缓冲层的生长过程中转变为贯穿型位错,降低了基平面位错的位错密度,进一步降低了基平面位错对外延层的影响,最终实现降低碳化硅外延层中的位错密度的目的,提高了器件性能。
附图说明
16.图1为本发明实施例碳化硅外延层生长方法步骤流程图;图2为本发明实施例碳化硅外延层生长方法中的位错在不同层之中的示意图;图3为本发明实施例碳化硅外延层生长方法中的位错汇聚消失的过程示意图。
具体实施方式
17.下面将结合本发明实施例中的附图,对本发明实施例中的技术方案进行清楚、完整地描述,显然,所描述的实施例仅仅是本发明一部分实施例,而不是全部的实施例。基于本发明中的实施例,本领域普通技术人员在没有做出创造性劳动前提下所获得的所有其他实施例,都属于本发明保护的范围。
18.参见图1,本实施例提供一种技术方案:一种碳化硅外延层生长方法,包括以下步骤:步骤s100,提供碳化硅衬底片,将所述碳化硅衬底片放到外延炉中,通入载气并加热后,设定压强,通入具有第一预定碳源流量的碳源和第一预定硅源流量的硅源,并通入掺杂气体,在所述碳化硅晶片表面生长第一缓冲层;其中,所述第一预定碳源流量与所述第一预定硅源流量中的碳硅比范围为1:1~3:2,所述第一预定碳源流量的范围为10 sccm~20 sccm;具有第一预定碳源流量的碳源和第一预定硅源流量的硅源使得第一缓冲层的生长速度变慢,并在生长第一缓冲层的过程中将从所述碳化硅衬底片延续出来的贯穿型位错转变为层错和基平面位错,促使位错横向移动并移出所述第一缓冲层表面;步骤s200,停止通入碳源、硅源以及掺杂气体,通入刻蚀气体,对所述第一缓冲层表面进行刻蚀,去除所述第一缓冲层表面的碳杂质,防止碳杂质成为位错源;步骤s300,再继续通入相应流量的碳源和硅源,通入掺杂气体,在去除杂质后的第一缓冲层表面生长得到具有相应浓度参数的外延层。
19.执行步骤s100和步骤s200,在本实施例中,所述碳化硅衬底片为n型碳化硅晶圆,所述碳化硅衬底片的掺杂浓度范围为10
18
~10
19 cm-3
,所述碳化硅衬底片的总位错密度103~10
4 cm-3
,但在其他实施例中,可以实际选择不同的碳化硅衬底片。
20.所述掺杂气包括含氮气体等,所述含氮气体包括氮气等;所述载气为高纯氢气;所述刻蚀气体为氢气;所述硅源可以为硅烷和三氯硅烷其中的一种或两种,或其他可以作为硅源的具体材料;所述碳源为甲烷、乙烯和丙烯和丙烯其中的一种或几种,或其他可以作为碳源的具体材料。
21.在本实施例中,所述第一预定碳源流量的范围为:10 sccm
ꢀ‑
20 sccm,所述第一预定碳源流量与所述第一预定硅源流量中的碳硅比范围为3:1~1:2;而通入的硅源的第一预定硅源流量通过融入的第一预定碳源流量和所述碳硅比进行调整;具体的,本实施例通过通入较低的碳源流量,使得生长第一缓冲层的速度变慢;本实施例通过设置高碳硅流量比,即增大第一预定碳源流量与所述第一预定硅源流量的碳硅比,即碳的比例大于硅的比例,使得生成的第一缓冲层中碳的占比变大,使得在生长第一缓冲层的过程中能够将从所述碳化硅衬底片延续出来的贯穿型位错在转变为层错和基平面位错,并在第一缓冲层的慢速生长下促进层错和位错的横向移动,使得层错和位错在横向运动下能够移出晶体,不上升到第一缓冲层表面,就不会再上升到第一缓冲层表面的外延层中,从而降低外延层中的位错密度。其中,所述层错和基平面位错即为按照台阶流生长方向横向生长,所述贯穿型位错即为会纵向生长的位错;所述贯穿型位错包括螺位错tsd和刃位错ted。
22.具体的,使得生长第一缓冲层的速度变慢即使得生长第一缓冲层的过程为低速台阶流生长模式,在该生长模式下,生长出来的台阶尺寸会增大,从而在生长第一缓冲层的过程中促进所述碳化硅衬底片延续出来的贯穿型位错进行横向移动,从而转化为横向运动的
层错和基平面位错,而位错在台阶表面的横向移动加强,就会促使部分初始的贯穿型位错向晶体侧面移动,另有部分初始的贯穿型位错还会分解出层错,使得直接按照层错的横向生长方向增速移动,均能促进贯穿型位错逸出晶体;而碳化硅衬底片延续出来的基平面位错也会随着慢速生长进一步横向移动,从而移出所述第一缓冲层表面,不再延伸到第一缓冲层表面。
23.同时,部分伯氏矢量相反的位错则会汇聚消失,例如:贯穿型位错tsd是螺旋型位错,一个左旋的贯穿型位错tsd和一个右旋的贯穿型位错tsd碰在一起就会抵消掉,从而汇聚消失,而刃位错ted是半层原子,一个左边多半层的刃位错ted和一个右边多半层的刃位错ted碰在一起,就会汇聚消失;如图3所示,图中黑色实线表示位错线在第一缓冲层表面的运动,箭头表示伯氏矢量的方向,黑色圆点表示垂直于表面,空心圆点表示汇聚位置,随着第一缓冲层外延厚度的增加,一部分贯穿型位错延伸至晶体侧面而逸出,一部分伯氏矢量相反的贯穿型位错相互靠近,最终互相汇聚而消失,一部分贯穿型位错既没有逸出也没有汇聚,而作为残留的位错线也可能在第一缓冲层中沿台阶流方向横向运动,但没有移出第一缓冲层。
24.在本实施例中,工艺中加热温度范围为1500~1700℃;而全过程中的压强都可以设定保持不变,但是,如果为了进一步降低第一缓冲层的生长速度;在所述碳化硅衬底片表面生长第一缓冲层时的压强可以设定为范围为30~80 torr的低压强。
25.需要注意的是,由于在生长第一缓冲层的过程中,碳源流量的占比高,因此在所述第一缓冲层表面会产生碳杂质,如果这些碳杂质不清除掉就在所述第一缓冲层表面生长外延层,则这些碳杂质就会成为所述外延层的位错源,在所述外延层中形成新的位错线,因此为了降低杂质影响,本发明实施例通过对所述第一缓冲层表面进行刻蚀,进一步降低了位错对外延层的影响。同时由于第一缓冲层的厚度较小,碳杂质主要形成在第一缓冲层表面,尚未形成在第一缓冲层内部,因此通过刻蚀工艺将第一缓冲层表面的碳杂质去除,可以有效减少外延层的位错源。
26.执行步骤s300,本发明通入具有相应流量的碳源和相应的流量的硅源进行外延层生长,需要根据实际需要得到的目标浓度参数的外延层确定,而外延层的生长厚度也直接根据实际需要的外延层的目标厚度确定,本实施例不做限定,例如,碳源流量可以为40 sccm~80sccm,碳源流量和硅源流量中的碳硅比可以设定为0.8~1,而硅源流量通过碳源流量和碳硅比进行调整。
27.在本实施例,为了进一步降低第一缓冲层表面残留的位错对外延层的影响,本实施例中再继续通入相应流量的碳源和硅源,通入掺杂气体,在去除杂质后的第一缓冲层表面生长得到具有相应浓度参数的外延层的步骤具体包括;继续通入具有第二预定碳源流量的碳源和第二预定硅源流量的硅源,通入掺杂气体,在所述第一缓冲层表面形成第二缓冲层,其中,具有第二预定碳源流量的碳源和第二预定硅源流量的硅源使得第二缓冲层的生长速度变快,并在生长第二缓冲层的过程中将从所述第一缓冲层延续出来的残留的基平面位错转化为贯穿型位错,促使位错纵向移动,使得从所述第二缓冲层延伸到后续形成的外延层中的位错为贯穿型位错;再继续通入相应流量的碳源和硅源,通入掺杂气体,在去除杂质后的第二缓冲层表面生长得到具有相应浓度参数的外延层。
28.需要注意的是,本实施例在生成第二缓冲层后,并没有对第二缓冲层表面进行刻蚀,这是因为,通入第二缓冲层中所述第一预定碳源流量与所述第一预定硅源流量中的碳硅比中碳源的占比不高,因此不会在第二缓冲层表面形成碳杂质,不需要额外进行刻蚀,而是可以直接生长外延层。
29.在本实施例中,所述第二预定碳源流量的范围为:60sccm~100sccm,所述第二预定碳源流量与所述第二预定硅源流量中的碳硅比范围为4:5~1:1;而通入的第二预定硅源流量通过通入的碳源的第二预定碳源流量和所述碳硅比进行调整;具体的,本实施例通过通入较高的碳源流量,使得生长第二缓冲层的速度变快,另外,本实施例通过设置低的碳源流量占比,即相较于第一缓冲层中碳的含量占比,要将第二缓冲层的碳含量占比降低,使得在生长第一缓冲层的过程中将从所述第一缓冲层表面延续出来的残留的基平面位错在第二缓冲层中转变为贯穿型位错,使得在第二缓冲层的生长速度变快的前提下使得贯穿型位错加快纵向移动,并最终使得移动到外延层中的位错为贯穿型位错,降低基平面位错对外延层的影响。
30.其中,在生长第二缓冲层的过程中将从所述第一缓冲层延续出来的残留的基平面位错转化为贯穿型位错,使得从所述第二缓冲层延伸到后续形成的外延层中的位错为贯穿型位错的目的是,在生长第一缓冲层的过程中,由于可能会存在一些位错还是移不出去,而贯穿型位错相比基平面位错对外延层质量的影响更小,因此为了进一步降低位错对外延层的影响,从而整体降低位错影响,因此本实施例通过设置第二缓冲层再次将从第一缓冲层延伸过来的基平面位错转化为了贯穿型位错;但在其他实施例中,也可以在第二缓冲层中继续设计为促使基平面位错横向移动,从而促进位错移出所述第二缓冲层表面,进一步减少外延层中的位错数量和密度。
31.如图2所示,所述碳化硅衬底片10表面生长有第一缓冲层20,所述第一缓冲层20表面生长有第二缓冲层30,所述第二缓冲层表面生长有外延层40,其中图中所展示的实线可以看做为位错线,箭头所示方向为台阶流方向,可以看出所述碳化硅衬底片10中存在多个位错线,这些位错线直接延伸到了生成的第一缓冲层20中,而由于本实施例通过在生长第一缓冲层20的过程中对通入的碳硅流量占比以及具体通入的碳源流量的调整,使得第一缓冲层20的生长速度变慢,并将从碳化硅衬底片10中的贯穿型位错转变为了第一缓冲层20中横向移动的基平面位错,而其中部分位错线又随着第一缓冲层20的生长延伸出了第一缓冲层20的右侧边,最终使得能够延伸到第一缓冲层20表面的位错线数量减少,而在所述第一缓冲层20表面的第二缓冲层30,可以看出,由于本实施例通过在生长第二缓冲层30的过程中对通入的碳硅流量占比以及具体通入的碳源流量的调整,使得从第一缓冲层表面延伸出来的基平面位错在第二缓冲层30中转变为了贯穿型位错。
32.进一步的,在所述第一缓冲层表面生长第二缓冲层时的压强范围可以设定为80~120 torr,用于进一步提高生长第二缓冲层的速度;在所述第二缓冲层表面生长外延层时的压强范围可以设定为80~120 torr,用于提高生长外延层的速度。
33.进一步的,在生长第一缓冲层时通入的掺杂气体具有第一预定流量,具有第一预定流量的掺杂气体使得形成的所述第一缓冲层具有相应的第一预定掺杂浓度,所述第一预定掺杂浓度与所述碳化硅衬底片的掺杂浓度一致,用于防止所述碳化硅衬底片与所述第一缓冲层之间由于掺杂浓度的差异大而导致产生界面位错;
在生长第二缓冲层时通入的掺杂气体具有第二预定流量,具有第二预定流量的掺杂气体使得形成的所述第二缓冲层具有相应的第二预定掺杂浓度,其中,所述第二预定掺杂浓度小于所述第一预定掺杂浓度但大于后续形成的所述外延层的掺杂浓度,用于对所述第一缓冲层的掺杂浓度与所述后续形成的外延层的掺杂浓度进行中间过渡,防止因掺杂浓度差异大导致晶格畸变而产生新的缺陷。
34.例如:当所述碳化硅衬底片的掺杂浓度范围为10
18
~10
19 cm-3
,而需要生成的外延层的掺杂浓度10
15
cm-3
时,可以通过调整掺杂气体的流量,使得所述第一缓冲层的掺杂浓度为10
18 cm-3
,使得所述第二缓冲层的掺杂浓度降低至10
16 cm-3
,从而使得第一缓冲层和第二缓冲层都能起到相应的作用。
35.具体的,作为一种例子,首先,提供碳化硅衬底片,对所述碳化硅衬底片进行清洗,其中,可以选择4
°
斜切的n型碳化硅晶圆作为碳化硅衬底片,掺杂浓度为10
18
~10
19 cm-3
,总位错密度103~10
4 cm-3
,基于标准rca进行清洗;清洗完成后,将碳化硅衬底片送入外延炉,通入高纯氢气,升高温度至1600℃;将反应腔的压强调整为40 torr,加入三氯硅烷作为硅源和丙烯作为碳源,其中丙烯流量为20 sccm,通过调整三氯硅烷的流量,使得碳、硅的流量比为1:2,获得低速台阶流生长模式,调整高纯氮气的流量,使掺杂浓度为10
18
cm-3
;得到的厚度为1.0微米的第一缓冲层;该模式下,外延台阶尺寸增加,贯穿型位错在台阶表面的横向移动加强,促使部分贯穿型位错向晶体侧面移动,另有部分贯穿型位错分解为层错,横向生长速度增加,均能促进贯穿型位错逸出晶体。同时,部分伯氏矢量相反的位错相互靠近,最终汇聚消失。高掺杂浓度能够降低外延层与衬底的晶格错配,避免新的界面位错的产生。
36.调整反应腔压强为100 torr,丙烯流量为60 sccm,调整三氯硅烷的流量使碳硅比为1:2,调整高纯氮气流量,使第二缓冲层的掺杂浓度为10
5-10
6 cm-3
,生长1.0微米厚度,得到缓冲层b,其中,该生长环境促进基平面位错向贯穿型位错转变。
37.压强保持为100 torr,丙烯流量保持60sccm,调整三氯硅烷的流量使碳硅比降低至0.9,生长目标厚度的外延层,获得低位错密度的外延薄膜。
38.本发明提供了一种碳化硅外延层生长方法,通过通入具有第一预定碳源流量的碳源和第一预定硅源流量的硅源,在碳化硅衬底片表面生成第一缓冲层,使得通过对碳硅流量比以及具体通入的碳源流量的调整,促使从碳化硅衬底片延伸出来的贯穿型位错在第一缓冲层的生长过程中转变为基平面位错,进行横向移动并移出所述晶体的第一缓冲层,从而减少从所述第一缓冲层进入外延层的位错数量;并通过通入具有第一预定碳源流量的碳源和第一预定硅源流量的硅源,在所述第一缓冲层表面生成第二缓冲层,使得通过对碳硅流量比以及具体通入的碳源流量的调整,促使从碳化硅衬底片延伸出来的基平面位错在第一缓冲层的生长过程中转变为贯穿型位错,降低了基平面位错的位错密度,进一步降低了基平面位错对外延层的影响,最终实现降低碳化硅外延层中的位错密度的目的,提高了器件性能。
39.本发明虽然己以较佳实施例公开如上,但其并不是用来限定本发明,任何本领域技术人员在不脱离本发明的精神和范围内,都可以利用上述揭示的方法和技术内容对本发明技术方案做出可能的变动和修改,因此,凡是未脱离本发明技术方案的内容,依据本发明的技术实质对以上实施例所作的任何简单修改、等同变化及修饰,均属于本发明技术方案的保护范围。