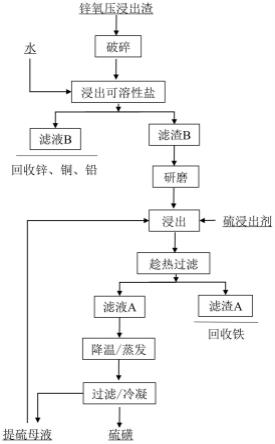
1.本发明属于湿法冶金领域,尤其涉及一种从废渣中回收硫的工艺。
背景技术:2.在锌的冶炼中,目前主要采用的是湿法炼锌,湿法炼锌包含传统湿法炼锌、加压浸出法、富氧直接浸出法和加压富氧浸出法。加压富氧浸出法是有效处理闪锌矿的一种新技术,也是我国重点推广的一种锌冶炼技术。其优点是生产过程中产出元素硫,无烟气硫酸产出,消除了二氧化硫污染,锌浸出率高,共伴生金属如in、cu、ge和ga等回收率高,对锌资源具有良好的适应性。我国从20世纪80年代开始对锌精矿的加压富氧浸出法进行了研究,近年来又有创新发展,加压富氧浸出法应用逐渐扩大。
3.虽然加压富氧浸出法解决了高铁闪锌矿处理过程中二氧化硫污染、锌浸出率低、共伴生金属in、cu、ge和ga等回收率低的问题,但是其浸出渣中依然含有元素s、未浸出的pb和zn、ag等,综合回收价值大。氧压浸出渣如果弃之,元素硫自然氧化会对环境产生严重污染,并且浪费了一种可利用的二次资源。鉴于目前环保压力增加和资源枯竭现状,如何回收利用浸出渣中的单质硫和其他有价金属成为迫在眉睫的问题。
4.目前对浸出渣中单质硫的回收主要包含物理法和化学法两大类。物理法主要包括高压倾析法、热滤法、浮选法、制粒筛分法和真空蒸馏法等。化学法主要包括二甲苯法、二硫化碳法、硫化铵法和煤油法等。物理法虽然有着处理量大,成本低等优点,但是也因为其设备成本高,操作复杂,单质硫品质低等缺点。化学法使用的化学试剂基本上都是含有剧毒的,不仅对操作人员带来身体危害,处理后的废水也要处理排放,并且由于化学试剂中有机溶剂居多,多伴随易燃易爆等缺点。因此,上述方法在应用中均有不足之处。
技术实现要素:5.本发明所要解决的技术问题是克服以上背景技术中提到的不足和缺陷,提供一种提硫效果好、提硫效率高、工艺简单的从锌氧压浸出渣中回收单质硫的工艺。为解决上述技术问题,本发明提出的技术方案为:
6.一种从锌氧压浸出渣中回收单质硫的工艺,包括以下步骤:
7.(1)对浸出渣进行预处理得到溶硫粉料;
8.(2)将步骤(1)中得到的溶硫粉料与硫浸出剂混合,加热、搅拌进行浸出处理得到滤液a与滤渣a;所述硫浸出剂为c10-c18的烷烃中的任一种或多种的混合物;
9.(3)对步骤(2)中的滤液a进行结晶处理,收集结晶即得到单质硫。
10.上述从锌氧压浸出渣中回收单质硫的工艺中,优选的,所述硫浸出剂为正癸烷。本发明采用正癸烷一方面对硫的浸出效果好,另一方面正癸烷的毒性较低,完全符合国标要求,为微毒性溶剂,对人体的危害较小。
11.上述从锌氧压浸出渣中回收单质硫的工艺中,优选的,所述硫浸出剂中还添加有辅助试剂,所述辅助试剂为己二醇、油酸和生物醇油。
12.上述从锌氧压浸出渣中回收单质硫的工艺中,优选的,所述正癸烷、己二醇、油酸和生物醇油的质量比为85:(1-9):(1-10):(0.1-5)。
13.本发明中,我们研究表明,利用正癸烷作为硫出剂,浸出效果好,反应速度快,反应时间短,大大提高了提硫的效率,还可以循环利用,节省原料。此外,为了进一步提高正癸烷的作用效果,本发明还提供辅助试剂与正癸烷协同作用,具体的,利用己二醇、油酸和生物醇油作为辅助试剂,通过添加己二醇、油酸和生物醇油,各种物质与正癸烷协作用,有利于正癸烷作用的发挥,更加有利于正癸烷的浸出率与浸出效率。另外,我们还研究表明,通过添加己二醇、油酸和生物醇油作为辅助试剂,还可以还能提高烷烃的闪点,使操作变得更加安全,可对烷烃进行保护,防止硫出剂的损失,损耗小。但上述辅助试剂的用量需要进行合理限定,否则会影响到硫浸出效果,我们研究表明,控制正癸烷、己二醇、油酸和生物醇油的质量比为85:(1-9):(1-10):(0.1-5)较优,更优选的,控制正癸烷、己二醇、油酸和生物醇油的质量比为85:8:6:1。
14.上述从锌氧压浸出渣中回收单质硫的工艺中,优选的,所述浸出处理时,控制浸出温度为130-150℃,浸出时间为3-30min,硫浸出剂和溶硫粉料的质量比为(8-20):1。上述温度过高会增加硫的粘度,造成分离困难,过低又会降低硫的溶解度,效率不高;浸出时间与质量比和硫的溶解效率成正比,为保证合适的溶解效率,控制在上述浸出时间和质量比有利于保证硫的浸出提取率。
15.上述从锌氧压浸出渣中回收单质硫的工艺中,优选的,所述结晶处理为在-10~20℃范围内进行降温结晶,然后过滤,得到结晶母液和单质硫,结晶母液返回用作硫浸出剂。
16.上述从锌氧压浸出渣中回收单质硫的工艺中,优选的,所述结晶处理为在160-175℃温度下蒸发结晶,得到蒸发冷凝液和单质硫,蒸发冷凝液返回用作硫浸出剂。
17.上述从锌氧压浸出渣中回收单质硫的工艺中,优选的,对浸出渣进行预处理包括以下步骤:将浸出进行破碎得到破碎料;对破碎料进行水洗,调成料浆,然后抽滤得到滤液b和滤渣b,收集滤液b中的有价金属,对滤渣b进行研磨,过筛,即得到溶硫粉料。
18.上述从锌氧压浸出渣中回收单质硫的工艺中,优选的,所述过筛时控制200-270目的颗粒质量占据80%以上。
19.与现有技术相比,本发明的优点在于:
20.1、本发明的从锌氧压浸出渣中回收单质硫的工艺中采用的硫浸出剂为c10-c18的烷烃中的任一种或多种的混合物,相较于现有有机溶剂,具有反应速度快,反应时间短等效果,大大提高了提硫的效率,还可以循环利用,节省原料。
21.2、本发明的从锌氧压浸出渣中回收单质硫的工艺的提硫效果好,提硫后的渣中硫含量低,结晶硫的纯度高,可以不用净化直接出售。
22.3、本发明的从锌氧压浸出渣中回收单质硫的工艺具有工艺步骤较少,设备投资也相对较少,操作简单等优势。
附图说明
23.为了更清楚地说明本发明实施例或现有技术中的技术方案,下面将对实施例或现有技术描述中所需要使用的附图作简单地介绍,显而易见地,下面描述中的附图是本发明的一些实施例,对于本领域普通技术人员来讲,在不付出创造性劳动的前提下,还可以根据
这些附图获得其他的附图。
24.图1为本发明从锌氧压浸出渣中回收单质硫的工艺流程图。
具体实施方式
25.为了便于理解本发明,下文将结合说明书附图和较佳的实施例对本发明作更全面、细致地描述,但本发明的保护范围并不限于以下具体的实施例。
26.除非另有定义,下文中所使用的所有专业术语与本领域技术人员通常理解的含义相同。本文中所使用的专业术语只是为了描述具体实施例的目的,并不是旨在限制本发明的保护范围。
27.除非另有特别说明,本发明中用到的各种原材料、试剂、仪器和设备等均可通过市场购买得到或者可通过现有方法制备得到。
28.以下实施例所采用的原料是锌的氧压浸出渣,此类渣的特点是渣中含有大量的单质硫,除此之外还含有硫酸铁、闪锌矿和石英等。渣中的主要元素是单质硫,因其冶炼厂的不同,渣中的含硫量也有部分差异,其一般维持在30-80%。除了单质硫外,其中还含有一定量的铁、铜、铅、锌等有价金属。实验探究了不同硫含量的浸出渣中硫的提取效果,浸出渣的化学成分如表1。
29.表1:不同硫含量的浸出渣的化学成分(质量含量)
[0030][0031]
从表1中可知,1号样中的硫含量较低,仅有45%,2号样中的硫含量为72.5%,两种样品中大部分是以单质的形式存在,少部分以金属硫化物和硫酸盐形式存在。有价金属多以金属氧化物、金属硫化物和硫酸盐的形式存在。
[0032]
实施例1:
[0033]
如图1所示,一种从锌氧压浸出渣中回收单质硫的工艺,包括以下步骤:
[0034]
(1)将待处理的浸出渣(1号样)进行破碎,得到实验原料。
[0035]
(2)在常温下对实验原料进行水洗,控制液固比为4:1,调成料浆,然后抽滤得到滤液b和滤渣b。
[0036]
(3)滤液b中含有硫酸锌等可溶性物质,对滤液b进行有价金属的回收。
[0037]
(4)对滤渣b进行研磨,并过-230~+270目筛,得到溶硫粉料。
[0038]
(5)将硫浸出剂(配比为正癸烷85重量份、乙二醇8重量份、油酸6重量份、生物醇油1重量份(四川新源素科技有限公司生产,生产批号22-0402,下同))加热到130℃,硫浸出剂体积和滤渣b质量的比值为10:1,转速为300r/min,搅拌反应10min,反应结束后趁热过滤,得到滤液a和滤渣a,硫的浸出率为99.5%。
[0039]
(6)滤液a在0℃进行降温结晶,然后过滤,得到结晶母液和单质硫(纯度99.5%),结晶母液可以循环利用。硫整体回收率在90%以上。
[0040]
实施例2:
[0041]
一种从锌氧压浸出渣中回收单质硫的工艺,包括以下步骤:
[0042]
(1)将待处理的浸出渣(2号样)进行破碎,得到实验原料。
[0043]
(2)在常温下对实验原料进行水洗,控制液固比为4:1,调成料浆,然后抽滤得到滤液b和滤渣b。
[0044]
(3)滤液b中含有硫酸锌等可溶性物质,对滤液b进行有价金属的回收。
[0045]
(4)对滤渣b进行研磨,并过-230~+270目筛,得到溶硫粉料。
[0046]
(5)将硫浸出剂(与实施例1相同)加热到130℃,硫浸出剂体积和滤渣b质量的比值为18:1,转速为300r/min,搅拌反应30min,反应结束后趁热过滤;得到滤液a和滤渣a,硫的浸出率为99.8%。
[0047]
(6)滤液a或在160-175℃温度下蒸发结晶,得到单质硫(纯度99.5%),蒸发液冷凝以便循环使用。硫整体回收率在90%以上。
[0048]
实施例3-10:
[0049]
实施例3-10与实施例2相比,区别在于硫浸出剂不同,具体硫出剂以及硫的浸出率如下表2所示:
[0050][0051]
经过测定,实施例3-10中得到的单质硫的纯度均与实施例2接近,但各实施例3-10中硫的浸出率明显低于实施例2,尤其是采用十二烷作为硫浸出剂的情形,硫的浸出率明显低于采用正癸烷作浸出剂的情形。由上述实施例可知,本发明的辅助试剂需要进行合理优化选择,才能实现较好的硫浸出效果。