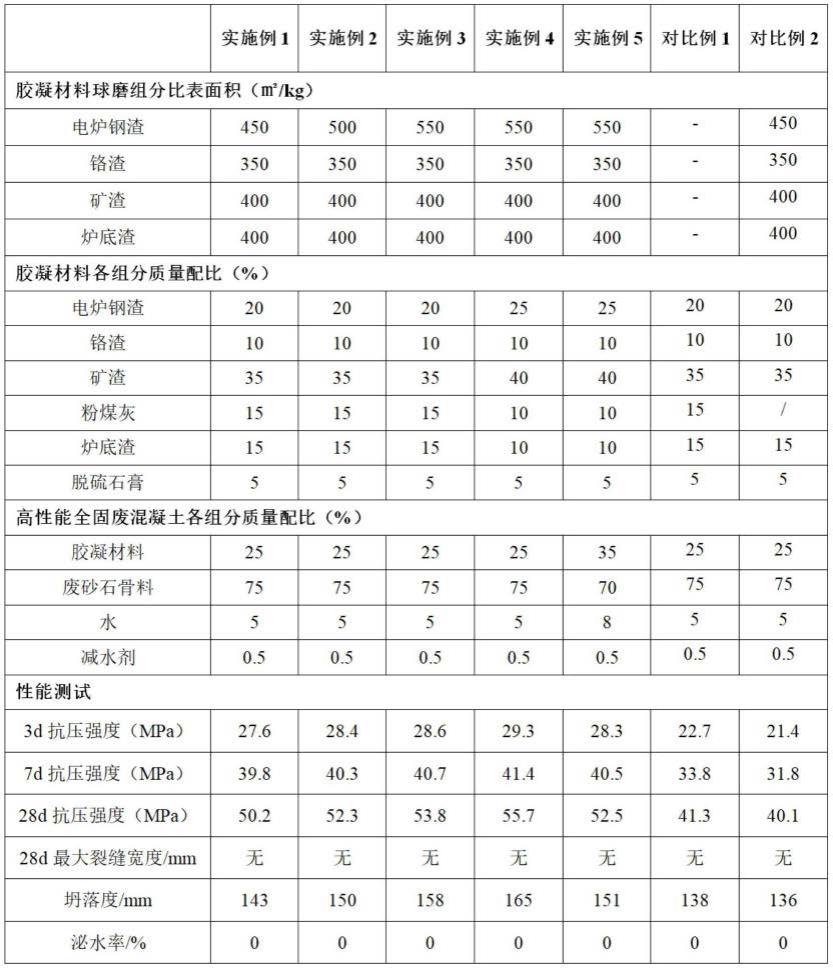
1.本发明属于固废资源化利用技术领域,具体涉及一种高性能全固废混凝土及其制备方法。
背景技术:2.随着我国经济社会的高速发展、城市化进程的加快,水泥混凝土的用量巨大。随之而来的是混凝土优质矿物掺合料资源短缺,如优质硅灰、粉煤灰已是供不应求的状态,价格已接近甚至超过水泥价格。因此,从循环经济和混凝土产业出发,将矿物掺合料从传统工业废渣转向难以利用的低活性工业固废,具有良好的经济及社会效应。
3.在钢铁工业中,高炉矿渣已实现零排放,成为混凝土工业重要的替代水泥材料。然而,同为钢铁工业废弃物的钢渣,由于其活性指数较低、难磨、存在安定性隐患等,致使其利用率长期在低位徘徊。因而,激发钢渣的活性是其推广应用所面临的重要技术问题之一。根据炼钢工艺的不同,钢渣分为转炉钢渣和电炉钢渣,其中电炉钢渣又分为熔炼渣和精炼渣。我国炼钢以转炉为主,对钢渣性能的研究也主要集中在转炉钢渣方面。电炉钢渣在水泥混凝土中的应用需要进一步探究。
4.有研究证明多种掺合料复掺对提高混凝土各方面性能有良好作用,目前可以将各类工业固废及化工废渣用于混凝土的制备中,例如专利cn202111234370.8中公开了一种胶凝材料、全固废混凝土及其制备方法,该全固废混凝土包括胶凝材料、废砂、废石、水和减水剂,其中胶凝材料包括钢渣粉、矿渣粉、脱硫石膏粉和碱渣粉,该固废混凝土将钢铁冶金渣、化工废渣等工业固废应用于混凝土中,而且制得的全固废混凝土材料的力学性能较高,但该全固废混凝土的原料为活性较高、易于利用的工业固废。
技术实现要素:5.针对现有技术中存在的上述不足,本发明提供了一种高性能全固废混凝土,该混凝土对电炉钢渣、铬渣等难以利用的工业固废进行利用,而且制得的混凝土的性能较好。
6.实现本发明上述目的所采用的技术方案为:
7.一种高性能全固废混凝土,所述高性能全固废混凝土各组分及质量配比为:胶凝材料15%~40%,废砂石骨料70%~80%,水5%~9%,减水剂0.5%~1%;
8.其中胶凝材料的各组分及质量配比为:电炉钢渣20%~30%,铬渣10%~15%,矿渣35%~45%,炉底渣10%~15%,粉煤灰10%~15%,脱硫石膏5%~10%。
9.所述废砂石骨料包括废砂35%~40%、废石35%~40%,其中废砂的粒度≤4.75mm,废石粒度为4.75mm~19mm。
10.所述减水剂为聚羧酸高效减水剂。
11.本发明还提供了一种高性能全固废混凝土的制备方法,包括以下步骤:(1)将电炉钢渣、铬渣、矿渣和炉底渣分别破碎后烘干,再分别进行球磨40min~60min;
12.(2)将球磨后的电炉钢渣、铬渣、矿渣和炉底渣与粉煤灰及脱硫石膏按比例混合,
再放入细磨中60min~90min,得到胶凝材料;
13.(3)将步骤(2)中制备的胶凝材料、废砂石骨料、减水剂与水按比例混合,搅拌均匀,制备全固废混凝土。
14.所述步骤(2)中细磨得到胶凝材料通过标椎方石孔筛45μm筛余≤10%,胶凝材料比表面积≥600
㎡
/kg。
15.所述粉煤灰为ⅰ级或ⅱ级粉煤灰。
16.所述脱硫石膏比表面积为300
㎡
/kg~450
㎡
/kg。
17.所述步骤(1)中球磨后的电炉钢渣的比表面积≥450
㎡
/kg。
18.所述步骤(1)中球磨后的铬渣的比表面积≥350
㎡
/kg。
19.所述步骤(1)中球磨后的矿渣的比表面积≥400
㎡
/kg。
20.所述步骤(1)中球磨后的炉底渣的比表面积≥400
㎡
/kg。
21.与现有技术相比,本发明提供的高性能全固废混凝土具有以下优点:(1)本发明中通过电炉钢渣、铬渣、矿渣、炉底渣、粉煤灰和脱硫石膏多固废间的协同作用,解决了电炉钢渣、铬渣及炉底渣等活性指数较低、难以利用的问题,具有良好的经济及社会效应。
22.本发明中对电炉钢渣、铬渣、矿渣和炉底渣进行两次球磨,第一次单独球磨时,电炉钢渣在机械激发方法下进行粉磨,使电炉钢渣的颗粒尺寸减小、发生晶格畸变,进而加速其活性成分的水化。铬渣、矿渣和炉底渣也是如此,粒径更小可以促进渣土中na、k、mg及ca等离子的融出,使其具有更高的反应活性。
23.第二次将全部物料混合后进行超细磨,混凝土中磨细电炉钢渣、磨细铬渣、磨细矿渣和磨细炉底渣与粉煤灰进行复合使用,磨细电炉钢渣中较高的碱含量对磨细矿渣和粉煤灰等进行激发和颗粒填充作用而产生叠加效应,弥补了磨细电炉钢渣、磨细铬渣、磨细炉底渣本身活性的不足。同时炉底渣在制备混凝土时有利于水化硅酸钙的形成量的增加,有利于c-s-h的凝胶纤维的生成,而且与混凝土中减水剂的相容性表现很好。
24.通过两次粉磨,以及与粉煤灰的复配使用,提高电炉钢渣、铬渣等的活性,实现对难以利用的工业固废进行利用,同时提高胶凝材料的活性。
25.(2)本发明提供的全固废混凝土中通过废砂石代替传统粗、细骨料,节约了大量的天然矿物质骨料,减少对矿山的开采和破坏,同时解决了固体废弃砂石堆存问题。胶凝材料中的脱硫石膏分散在废砂石中,增强废砂石的界面性能,而且脱硫石膏的粉末填充在废砂石的孔隙中,增强废砂石之间的粘结。
26.(3)本发明提供的全固废混凝土具有较高的强度,28d抗压强度可以达到50mpa,混凝土无裂缝,坍落度、泌水率等均满足建筑行业对混凝土的使用需求。
具体实施方式
27.为使本领域技术人员更好地理解本发明的技术方案,下面结合实施例对本发明作进一步详细描述。
28.实施例1
29.本实施例中所提供的高性能全固废混凝土的制备方法,包括以下步骤:(1)将电炉钢渣、铬渣、矿渣和炉底渣分别破碎后烘干,再分别进行球磨40min~60min;
30.球磨后的电炉钢渣的比表面积为450
㎡
/kg,铬渣的比表面积为350
㎡
/kg,矿渣的
比表面积为400
㎡
/kg,炉底渣的比表面积400
㎡
/kg。
31.(2)将球磨后的电炉钢渣、铬渣、矿渣和炉底渣与粉煤灰及脱硫石膏按比例混合,再放入细磨中60min~90min,得到胶凝材料,比表面积达到600
㎡
/kg以上;
32.混合质量比为:电炉钢渣20%、铬渣10%、矿渣35%、粉煤灰15%、炉底渣15%、脱硫石膏5%。
33.(3)将步骤(2)中制备的胶凝材料、废砂石骨料、减水剂与水按比例混合,混合质量比为:胶凝材料25%、废砂石骨料75%、水5%、减水剂0.5%。搅拌均匀,于温度20
±
5℃,相对湿度不低于60%的条件下注入100mm
×
100mm
×
100mm的模具中,置于混凝土振动台上振动成型。
34.成型后的试块置于养护温度20
±
2℃,相对湿度不低于95%的标准养护条件下养护24h后脱模,继续置于养护温度20
±
2℃、相对湿度不低于95%的恒温恒湿养护箱内养护至3d、7d、28d龄期。
35.实施例2~3
36.按照实施例1的方法制备实施例2~3,区别在于电炉钢渣、铬渣、矿渣和炉底渣第一次球磨后的比表面积不同,其比表面积以及性能测试如下表所示。
37.实施例4~5
38.按照实施例3的方法制备实施例4~5,区别在于配方不同,其配方组成以及性能测试如下表所示。
39.对比例1
40.按照实施例1的方法制备对比例1,区别在于将电炉钢渣、铬渣、矿渣和炉底渣分别破碎后烘干后直接与粉煤灰及脱硫石膏按比例混合进行一次球磨,不分别单独进行球磨。球磨至得到比表面积达到600
㎡
/kg以上胶凝材料,球磨时间为90min~120min,性能测试如下表所示。
41.对比例2
42.按照实施例1的方法制备对比例2,区别在于制备胶凝材料时不加入粉煤灰,其性能测试如下表所示。
[0043][0044]
参照gbt50080-2016《普通混凝土拌合物性能试验方法标准》、gb/t50081-2002《普通混凝土力学性能试验方法标准》和gb/t50082-2009《普通混凝土长期性能和耐久性能试验方法标准》进行性能测试。
[0045]
由上表可知,本发明制备得的全固废混凝土具有良好性能,28d抗压强度达到50mpa及以上,激发了电炉钢渣、铬渣、炉底渣等固废活性,全固废混凝土强度随电炉钢渣比表面积增大而加强。同时磨细电炉钢渣、磨细铬渣、磨细炉底渣与磨细矿渣和粉煤灰的复合使用对提高胶凝材料的活性大有裨益。