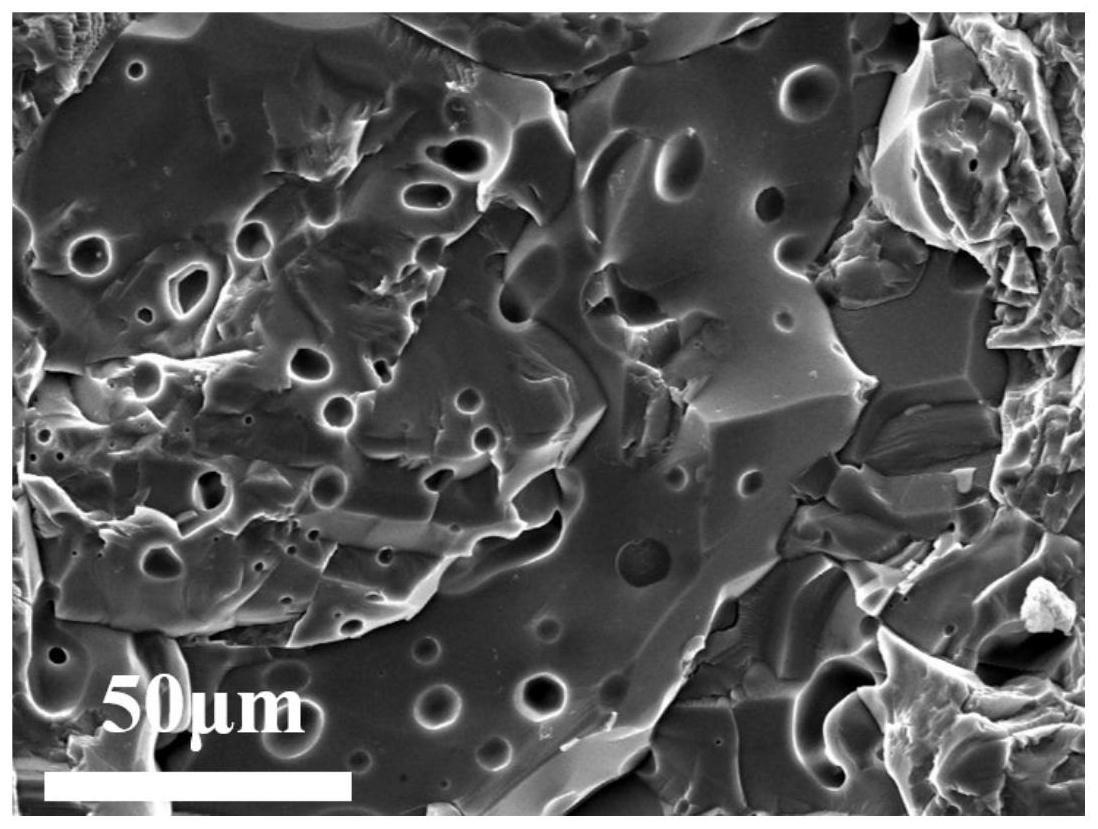
1.本发明属于弥散式闭气孔烧结氧化铝技术领域。具体涉及一种基于水热法预处理的弥散式闭气孔烧结氧化铝及制备方法。
背景技术:2.烧结氧化铝具有结晶粗大、发育良好的α-al2o3晶体结构。由于其在超高温的快速烧结过程中不添加任何助烧结剂,因此在大尺寸α-al2o3晶体中包含一定数量的闭口气孔,使烧结氧化铝具有良好的耐磨性、加热体积稳定性和抗热震性,被广泛应用在黑色冶金等高温领域。由于氧化铝资源分布广泛,不同产地的工业氧化铝生产的烧结氧化铝的性能存在较大差异,甚至在某些制品的生产过程中(如连铸三大件)由于性能指标的提升而严格限制了烧结氧化铝的来源,因此烧结氧化铝的性能需要进一步提升以适应更高的标准。
3.(1)“一种提高板状刚玉体积密度的工艺”(cn108191414a)专利技术,通过先将γ-氧化铝与少量氧化镧共混,再经过成球、干燥和烧结的工艺获得板状刚玉产品,通过氧化镧对于晶界迁移的影响特性实现促进烧结的作用,虽然所得板状刚玉产品的晶体发育良好,体积密度较高,但是氧化镧的引入提高了成本,并且所制备的板状刚玉的晶体内气孔数量少,不利于材料的抗热震性。
4.(2)“烧结板状刚玉的制备工艺”(cn102503448 a)专利技术,采用常规的原料精磨
→
成球
→
干燥
→
煅烧
→
冷却获得烧结板状刚玉产品,通过对成球液和成球工艺参数的严格控制,虽然解决了部分生产工艺的问题,但是所制得的板状刚玉的体积密度较低,仅高出yb/t 4216-2010的烧结刚玉体积密度标准1.41%。
5.现有技术对于烧结氧化铝性能优化的生产工艺,常着眼于外加物或者成球液等方向,虽然工艺简单,但是也为体系引入了新的杂质;并且烧结氧化铝的主要工艺为烧结反应过程,少量的外加物对于整体的烧结反应产生的性能提升效果影响很小。现有的研究中并未有相关技术从原料本身进行处理,以实现烧结氧化铝物理性能的提升及微观结构的优化。
技术实现要素:6.本发明旨在突破现有技术不足,目的是提供一种成本低廉的基于水热法预处理的弥散式闭气孔烧结氧化铝的制备方法。用该方法所制备的基于水热法预处理的弥散式闭气孔烧结氧化铝纯度高、体积密度高和抗热震性强。
7.为实现上述目的,本发明采用的技术方案是:
8.步骤一、将γ-al2o3置于马弗炉内,在400~500℃条件下保温0.5~1小时,自然冷却;再置于球磨机内,研磨至粒度≤50μm,得到高活性γ-al2o3微粉。
9.步骤二、按照所述高活性γ-al2o3微粉∶去离子水的质量比为1∶3~5,将所述高活性γ-al2o3微粉超声分散于去离子水中,再于室温和1500~1700r/min的条件下,搅拌0.5~1小时,获得高静态稳定性的多分散悬浮液。
10.步骤三、将所述高静态稳定性的多分散悬浮液置于工业反应釜中,在100~200℃条件下保温3~6小时,自然冷却,得到预处理的γ-al2o3微粉。
11.步骤四、将所述预处理的γ-al2o3微粉置于造粒机中,按照成球液∶所述预处理γ-al2o3的质量比为1∶4~6,向所述预处理的γ-al2o3喷洒所示成球液,造粒,得到球状物料。
12.所述成球液为去离子水、或为混合溶液;所述混合溶液是按氟化铝∶氟化铵∶去离子水的质量比为(0.1~0.2)∶(0.1~0.2)∶1,将所述氟化铝、所述氟化铵和去离子水混合而成。
13.步骤五、将所述球状物料进行干燥处理,然后置于高温竖窑内,在1850~1950℃条件下保温1~2小时,冷却,制得基于水热法预处理的弥散式闭气孔烧结氧化铝。
14.所述干燥处理的温度为200~350℃,处理时间为0.5~1小时,干燥后残余水分小于2wt%。
15.所述的球磨机的研磨球为刚玉质球。
16.所述的γ-al2o3:al2o3含量≥99.5wt%,na2o含量≤0.5wt%。
17.所述的高压釜内的压强为3.5~6.5mpa。
18.所述的球状物料的粒径为25~35mm。
19.由于采用上述技术方案,本发明与现有技术相比具有以下积极效果:
20.(1)本发明的工艺流程中未加入去离子水以外的其他物质,能最大限度地保证烧结氧化铝的高纯特性,降低了杂质组分对烧结过程的影响,所制备的基于水热法预处理的弥散式闭气孔烧结氧化铝纯度高。
21.(2)本发明通过对γ-al2o3经过低温预烧-细磨-超声分散-搅拌-高压水热-干燥的处理,使γ-al2o3与水充分反应,3~6小时的处理时间控制了alooh晶粒在γ-al2o3表面的生长方式,在γ-al2o3表面生成细小alooh晶粒,小尺寸的水合氧化铝晶粒能使γ-al2o3细粉的表面积从50~80m2·
g-1
增大到75~125m2·
g-1
。在成球阶段有助于吸收更多的成球液以提高成球效率,在干燥阶段更大的表面积可以提升干燥速率,在高温烧结阶段则有助于增大材料在固相烧结过程中的固气表面能,在烧结坯体的烧结初期能提供更大的烧结驱动力,推动烧结坯体的烧结致密化进程,提高了基于水热法预处理的弥散式闭气孔烧结氧化铝的体积密度并降低显气孔率。
22.(3)本发明通过对γ-al2o3低温预烧-细磨-超声分散-搅拌-高压水热-干燥的预处理,在高温烧结阶段能增大材料在固相烧结过程中的固气表面能。增大后的固气表面能提供更多的烧结驱动力作用于烧结氧化铝的烧结中期及烧结后期的晶粒粗化与气孔排除阶段,提高了晶界移动速度,由于晶界移动速度与晶粒长大速度相同,因此可以认为晶界迁移速度与晶粒尺寸成正比,烧结氧化铝的晶粒尺寸也随着晶界移动速度的增大而增大,因此可以得到更大的晶粒尺寸,提高了基于水热法预处理的弥散式闭气孔烧结氧化铝的抵抗热应力的能力,从而提高基于水热法预处理的弥散式闭气孔烧结氧化铝的抗热震性能。
23.同时根据brook的速度判据公式,
[0024]vp
=f
pmp
ꢀꢀꢀꢀꢀꢀꢀꢀꢀꢀꢀꢀꢀꢀꢀꢀꢀꢀꢀꢀꢀꢀꢀꢀꢀꢀꢀꢀꢀꢀꢀꢀꢀꢀꢀꢀ
(1)
[0025]vb
=(f
b-nf
p
)mbꢀꢀꢀꢀꢀꢀꢀꢀꢀꢀꢀꢀꢀꢀꢀꢀꢀꢀꢀꢀꢀꢀꢀꢀꢀꢀꢀꢀꢀꢀꢀꢀ
(2)
[0026]
当v
p
《vb时,过量的烧结驱动力提高了晶界运动速度,因此,
[0027][0028]
式(1)(2)(3)中:
[0029]fi
表示烧结氧化铝内的氧化铝晶粒的晶界或内部孔径曲率施加给气孔运动的驱动力;
[0030]
mi表示由烧结氧化铝内部的原子表面扩散而移动的气孔或晶界迁移率;
[0031]vp
表示烧结氧化铝烧结过程中内部气孔的运动速度;
[0032]vb
表示对应烧结氧化铝烧结过程中氧化铝晶粒的晶界的运动速度。
[0033]
晶界的移动速度vb比气孔的移动速度v
p
快,导致晶界与气孔脱离进行自由移动,这种现象导致气孔在高速运动的过程中被滞留在颗粒中。因此,气孔以弥散形式保留在晶界内,提高了基于水热法预处理的弥散式闭气孔烧结氧化铝的抗热震性。
[0034]
本发明所制备的基于水热法预处理的弥散式闭气孔烧结氧化铝经检测:al2o3含量》99.3wt%;体积密度》3.75g/cm3;显气孔率《3%;晶粒尺寸为70~230μm;且大尺寸的α-al2o3晶体内含有弥散式分布的气孔。
[0035]
因此,本发明成本低,所制备的基于水热法预处理的弥散式闭气孔烧结氧化铝纯度高、体积密度高和抗热震性强。
附图说明
[0036]
图1为本发明的预处理的γ-al2o3微粉sem图片;
[0037]
图2为本发明制备的一种基于水热法预处理的弥散式闭气孔烧结氧化铝sem图片。
具体实施方式
[0038]
下面结合附图和具体实施方式,对本发明作进一步的描述,并非对其保护范围的限制。
[0039]
本具体实施方式中:
[0040]
所述的球磨机的研磨球为刚玉质球;
[0041]
所述的γ-al2o3:al2o3含量≥99.5wt%,na2o含量≤0.5wt%;
[0042]
所述的球状物料的粒径为25~35mm。
[0043]
实施例中不再赘述。
[0044]
实施例1
[0045]
一种基于水热法预处理的弥散式闭气孔烧结氧化铝及制备方法。本实施例的制备方法是:
[0046]
步骤一、将γ-al2o3置于马弗炉内,在400℃条件下保温0.5小时,自然冷却;再置于球磨机内,研磨至粒度≤50μm,得到高活性γ-al2o3微粉。
[0047]
步骤二、按照所述高活性γ-al2o3微粉∶去离子水的质量比为1∶3,将所述高活性γ-al2o3微粉超声分散于去离子水中,再于室温和1500r/min的条件下,搅拌0.5小时,获得高静态稳定性的多分散悬浮液。
[0048]
步骤三、将所述高静态稳定性的多分散悬浮液置于工业反应釜中,在200℃条件下保温3小时,自然冷却,得到预处理的γ-al2o3微粉。
[0049]
步骤四、将所述预处理的γ-al2o3微粉置于造粒机中,按照成球液∶所述预处理γ-al2o3的质量比为1∶4,向所述预处理的γ-al2o3喷洒所示成球液,造粒,得到球状物料。
[0050]
所述成球液为去离子水、或为混合溶液;所述混合溶液是按氟化铝∶氟化铵∶去离子水的质量比为0.1∶0.1∶1,将所述氟化铝、所述氟化铵和去离子水混合而成。
[0051]
步骤五、将所述球状物料进行干燥处理,然后置于高温竖窑内,在1850℃条件下保温2小时,冷却,制得基于水热法预处理的弥散式闭气孔烧结氧化铝。
[0052]
所述干燥处理的温度为270℃,处理时间为0.5小时,干燥后残余水分小于2wt%。
[0053]
所述的高压釜内的压强为3.5mpa。
[0054]
本实施例所制备的基于水热法预处理的弥散式闭气孔烧结氧化铝经检测:al2o3含量为99.4wt%;体积密度为3.77g/cm3;显气孔率为3%;晶粒尺寸为175μm;且大尺寸的α-al2o3晶体内含有弥散式分布的气孔。
[0055]
实施例2
[0056]
一种基于水热法预处理的弥散式闭气孔烧结氧化铝及制备方法。本实施例的制备方法是:
[0057]
步骤一、将γ-al2o3置于马弗炉内,在450℃条件下保温1小时,自然冷却;再置于球磨机内,研磨至粒度≤50μm,得到高活性γ-al2o3微粉。
[0058]
步骤二、按照所述高活性γ-al2o3微粉∶去离子水的质量比为1∶4.5,将所述高活性γ-al2o3微粉超声分散于去离子水中,再于室温和1600r/min的条件下,搅拌0.8小时,获得高静态稳定性的多分散悬浮液。
[0059]
步骤三、将所述高静态稳定性的多分散悬浮液置于工业反应釜中,在180℃条件下保温4小时,自然冷却,得到预处理的γ-al2o3微粉。
[0060]
步骤四、将所述预处理的γ-al2o3微粉置于造粒机中,按照成球液∶所述预处理γ-al2o3的质量比为1∶5,向所述预处理的γ-al2o3喷洒所示成球液,造粒,得到球状物料。
[0061]
所述成球液为去离子水、或为混合溶液;所述混合溶液是按氟化铝∶氟化铵∶去离子水的质量比为0.1∶0.2∶1,将所述氟化铝、所述氟化铵和去离子水混合而成。
[0062]
步骤五、将所述球状物料进行干燥处理,然后置于高温竖窑内,在1900℃条件下保温2小时,冷却,制得基于水热法预处理的弥散式闭气孔烧结氧化铝。
[0063]
所述干燥处理的温度为300℃,处理时间为0.5小时,干燥后残余水分小于2wt%。
[0064]
所述的高压釜内的压强为4.5mpa。
[0065]
本实施例所制备的基于水热法预处理的弥散式闭气孔烧结氧化铝经检测:al2o3含量为99.5wt%;体积密度为3.76g/cm3;显气孔率为2.5%;晶粒尺寸为160μm;且大尺寸的α-al2o3晶体内含有弥散式分布的气孔。
[0066]
实施例3
[0067]
一种基于水热法预处理的弥散式闭气孔烧结氧化铝及制备方法。本实施例的制备方法是:
[0068]
步骤一、将γ-al2o3置于马弗炉内,在500℃条件下保温0.5小时,自然冷却;再置于球磨机内,研磨至粒度≤50μm,得到高活性γ-al2o3微粉。
[0069]
步骤二、按照所述高活性γ-al2o3微粉∶去离子水的质量比为1∶4,将所述高活性γ-al2o3微粉超声分散于去离子水中,再于室温和1650r/min的条件下,搅拌1小时,获得高
静态稳定性的多分散悬浮液。
[0070]
步骤三、将所述高静态稳定性的多分散悬浮液置于工业反应釜中,在150℃条件下保温5小时,自然冷却,得到预处理的γ-al2o3微粉。
[0071]
步骤四、将所述预处理的γ-al2o3微粉置于造粒机中,按照成球液∶所述预处理γ-al2o3的质量比为1∶5,向所述预处理的γ-al2o3喷洒所示成球液,造粒,得到球状物料。
[0072]
所述成球液为去离子水、或为混合溶液;所述混合溶液是按氟化铝∶氟化铵∶去离子水的质量比为0.2∶0.1∶1,将所述氟化铝、所述氟化铵和去离子水混合而成。
[0073]
步骤五、将所述球状物料进行干燥处理,然后置于高温竖窑内,在1950℃条件下保温2小时,冷却,制得基于水热法预处理的弥散式闭气孔烧结氧化铝。
[0074]
所述干燥处理的温度为340℃,处理时间为1小时,干燥后残余水分小于2wt%。
[0075]
所述的高压釜内的压强为5.5mpa。
[0076]
本实施例所制备的基于水热法预处理的弥散式闭气孔烧结氧化铝经检测:al2o3含量为99.4wt%;体积密度为3.81g/cm3;显气孔率为2.0%;晶粒尺寸为180μm;且大尺寸的α-al2o3晶体内含有弥散式分布的气孔。
[0077]
实施例4
[0078]
一种基于水热法预处理的弥散式闭气孔烧结氧化铝及制备方法。本实施例的制备方法是:
[0079]
步骤一、将γ-al2o3置于马弗炉内,在500℃条件下保温1小时,自然冷却;再置于球磨机内,研磨至粒度≤50μm,得到高活性γ-al2o3微粉。
[0080]
步骤二、按照所述高活性γ-al2o3微粉∶去离子水的质量比为1∶5,将所述高活性γ-al2o3微粉超声分散于去离子水中,再于室温和1700r/min的条件下,搅拌1小时,获得高静态稳定性的多分散悬浮液。
[0081]
步骤三、将所述高静态稳定性的多分散悬浮液置于工业反应釜中,在100℃条件下保温6小时,自然冷却,得到预处理的γ-al2o3微粉。
[0082]
步骤四、将所述预处理的γ-al2o3微粉置于造粒机中,按照成球液∶所述预处理γ-al2o3的质量比为1∶6,向所述预处理的γ-al2o3喷洒所示成球液,造粒,得到球状物料。
[0083]
所述成球液为去离子水、或为混合溶液;所述混合溶液是按氟化铝∶氟化铵∶去离子水的质量比为0.2∶0.2∶1,将所述氟化铝、所述氟化铵和去离子水混合而成。
[0084]
步骤五、将所述球状物料进行干燥处理,然后置于高温竖窑内,在1900℃条件下保温1.5小时,冷却,制得基于水热法预处理的弥散式闭气孔烧结氧化铝。
[0085]
所述干燥处理的温度为290℃,处理时间为1小时,干燥后残余水分小于2wt%。
[0086]
所述的高压釜内的压强为6.5mpa。
[0087]
本实施例所制备的基于水热法预处理的弥散式闭气孔烧结氧化铝经检测:al2o3含量为99.3wt%;体积密度为3.83g/cm3;显气孔率为1.7%;晶粒尺寸为210μm;且大尺寸的α-al2o3晶体内含有弥散式分布的气孔。
[0088]
本具体实施方式与现有技术相比具有以下积极效果:
[0089]
(1)本具体实施方式的工艺流程中未加入去离子水以外的其他物质,能最大限度地保证烧结氧化铝的高纯特性,降低了杂质组分对烧结过程的影响,所制备的基于水热法预处理的弥散式闭气孔烧结氧化铝纯度高。
[0090]
(2)本具体实施方式通过对γ-al2o3经过低温预烧-细磨-超声分散-搅拌-高压水热-干燥的处理,使γ-al2o3与水充分反应,3~6小时的处理时间控制了alooh晶粒在γ-al2o3表面的生长方式,在γ-al2o3表面生成细小alooh晶粒如图1所示,图1是实施例4得到的预处理的γ-al2o3微粉sem图片,从图1可以看出:小尺寸的水合氧化铝晶粒能使γ-al2o3细粉的表面积从50~80m2·
g-1
增大到75~125m2·
g-1
。在成球阶段有助于吸收更多的成球液以提高成球效率,在干燥阶段更大的表面积可以提升干燥速率,在高温烧结阶段则有助于增大材料在固相烧结过程中的固气表面能,在烧结坯体的烧结初期能提供更大的烧结驱动力,推动烧结坯体的烧结致密化进程,提高了基于水热法预处理的弥散式闭气孔烧结氧化铝的体积密度并降低显气孔率。
[0091]
(3)本具体实施方式通过对γ-al2o3低温预烧-细磨-超声分散-搅拌-高压水热-干燥的预处理,在高温烧结阶段能增大材料在固相烧结过程中的固气表面能。增大后的固气表面能提供更多的烧结驱动力作用于烧结氧化铝的烧结中期及烧结后期的晶粒粗化与气孔排除阶段,提高了晶界移动速度,由于晶界移动速度与晶粒长大速度相同,因此可以认为晶界迁移速度与晶粒尺寸成正比,烧结氧化铝的晶粒尺寸也随着晶界移动速度的增大而增大,因此可以得到更大的晶粒尺寸,提高了基于水热法预处理的弥散式闭气孔烧结氧化铝的抵抗热应力的能力,从而提高基于水热法预处理的弥散式闭气孔烧结氧化铝抗热震性能。
[0092]
同时根据brook的速度判据公式,
[0093]vp
=f
pmp
ꢀꢀꢀꢀꢀꢀꢀꢀꢀꢀꢀꢀꢀꢀꢀꢀꢀꢀꢀꢀꢀꢀꢀꢀꢀꢀꢀꢀꢀꢀꢀꢀꢀꢀꢀꢀ
(1)
[0094]vb
=(f
b-nf
p
)mbꢀꢀꢀꢀꢀꢀꢀꢀꢀꢀꢀꢀꢀꢀꢀꢀꢀꢀꢀꢀꢀꢀꢀꢀꢀꢀꢀꢀꢀꢀꢀꢀ
(2)
[0095]
当v
p
《vb时,过量的烧结驱动力提高了晶界运动速度,因此,
[0096][0097]
式(1)、(2)和(3)中:
[0098]fi
表示烧结氧化铝内的氧化铝晶粒的晶界或内部孔径曲率施加给气孔运动的驱动力;
[0099]
mi表示由烧结氧化铝内部的原子表面扩散而移动的气孔或晶界迁移率;
[0100]vp
表示烧结氧化铝烧结过程中内部气孔的运动速度;
[0101]vb
表示对应烧结氧化铝烧结过程中氧化铝晶粒的晶界的运动速度。
[0102]
晶界的移动速度vb比气孔的移动速度v
p
快,导致晶界与气孔脱离进行自由移动,这种现象导致气孔在高速运动的过程中被滞留在颗粒中。因此,所制备的基于水热法预处理的弥散式闭气孔烧结氧化铝如图2所示,图2为实施例4制备的基于水热法预处理的弥散式闭气孔烧结氧化铝sem图片;从图2可以看出,气孔以弥散形式保留在晶界内,提高了基于水热法预处理的弥散式闭气孔烧结氧化铝的抗热震性。
[0103]
本具体实施方式所制备的基于水热法预处理的弥散式闭气孔烧结氧化铝经检测:al2o3含量》99.3wt%;体积密度》3.75g/cm3;显气孔率《3%;晶粒尺寸为70~230μm;且大尺寸的α-al2o3晶体内含有弥散式分布的气孔。
[0104]
因此,本具体实施方式成本低,所制备的基于水热法预处理的弥散式闭气孔烧结氧化铝纯度高、体积密度高和抗热震性强。