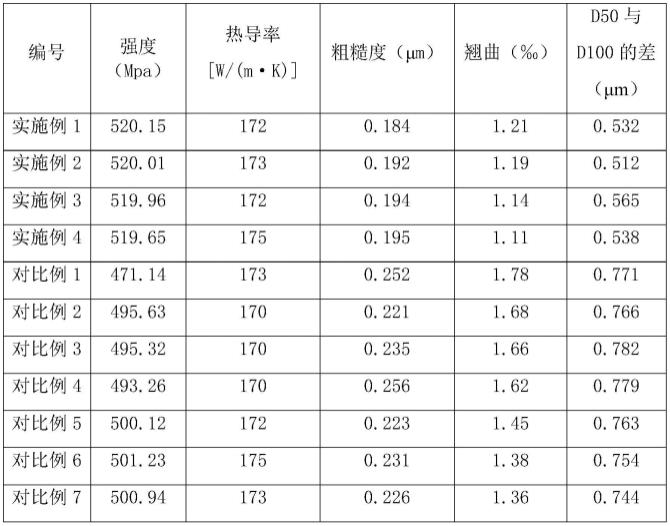
1.本发明属于陶瓷材料技术领域,特别涉及一种氮化铝陶瓷基板的制备方法。
背景技术:2.随着微电子技术的飞速发展,要求器件朝着大容量、高密度、高速度、大功率输出的方向发展,越来越复杂的器件对基板和封装材料的散热提出了越来越高的要求。传统的树脂基板和氧化铝陶瓷基板,最高热导率均仅为30w/(m
·
k)左右,远不能满足当今器件的散热要求。而氮化铝陶瓷具有导热性能优良、与硅相接近的热膨胀系数、较好的绝缘性能、适中的介电常数和介电损耗、室温和高温力学性能良好且无毒等优良特点,其作为集成电路和大功率器件的基板材料和电子封装材料具有广阔的应用前景。
3.传统氮化铝陶瓷基板是通过将氮化铝与烧结助剂混合制成浆料,然后流延成型、排胶、烧结得到的,该工艺制得的氮化铝陶瓷基板强度有限、容易出现翘曲,且粗糙度较高,导热性能距离理论性能尚有一段距离。因此,开发新的方法制备高强度、低翘曲、低粗糙度、高导热性的氮化铝陶瓷基板具有非常重要的意义。
技术实现要素:4.本发明旨在至少解决现有技术中存在的技术问题之一。为此,本发明提出一种氮化铝陶瓷基板的制备方法,通过对烧结助剂进行特定工序的预砂磨,控制烧结助剂在浆料中的粒度,提高烧结助剂在浆料中的分布均匀性,进而能够提高氮化铝陶瓷基板的致密度,减小氮化铝陶瓷基板的翘曲程度和粗糙度,并提高氮化铝陶瓷基板的力学强度。
5.本发明解决上述技术问题所采取的技术方案是:
6.一种氮化铝陶瓷基板的制备方法,包括步骤:
7.对烧结助剂分散液进行砂磨,得到粒度d50在0.4~1μm的烧结助剂浆料;所述砂磨依次在20~35℃、40~55℃、60~75℃三个温度段中进行,并控制循环频率梯度增高;
8.将所述烧结助剂浆料与氮化铝浆料球磨混合,得到混合浆料;
9.所述混合浆料流延成型、排胶、烧结得到所述氮化铝陶瓷基板。
10.相对于现有技术,本发明的制备方法至少具有如下有益效果:
11.本发明通过将烧结助剂预先进行分步砂磨,控制砂磨的循环频率(即转速)和砂磨温度,先使用较低转速使烧结助剂粉体自身发生的软团聚打开,然后梯度升高转速,使烧结助剂粉体中大颗粒首先进行粉碎,保证砂磨颗粒的均匀性,使烧结助剂浆料的粒度分布在纳米范围内,降低了粒度,增加了比表,有助于烧结过程中烧结助剂有效降低烧结温度,同时减少助烧剂在形成液相的过程中产生空隙,烧结成瓷更加致密,从而提高强度,同时改善翘曲和粗糙性。
12.在本发明的一些实例中,在20~35℃中砂磨的循环频率为600~750rpm,优选650~720rpm,包括但不限于600,620,640,650,660,680,700,720,740,750rpm等。
13.在本发明的一些实例中,在20~35℃中砂磨的时间为0.25~0.5h,包括但不限于
0.25,0.3,0.35,0.4,0.45,0.5h等。
14.在本发明的一些实例中,在40~55℃中砂磨的循环频率为760~950rpm,优选780~850rpm,包括但不限于760,780,800,820,840,850,860,880,900,920,940,950rpm等。
15.在本发明的一些实例中,在40~55℃中砂磨的时间为1~1.5h,包括但不限于1,1.2,1.4,1.5h等。
16.在本发明的一些实例中,在60~75℃中砂磨的循环频率为1000~1300rpm,优选1100~1200rpm,包括但不限于1000,1020,1040,1060,1080,1100,1120,1140,1160,1180,1200,1220,1240,1260,1280,1300rpm等。
17.在本发明的一些实例中,在60~75℃中砂磨的时间为1~1.5h,包括但不限于1,1.2,1.4,1.5h等。
18.在本发明的一些实例中,在20~35℃、40~55℃、60~75℃三个温度段砂磨的隔膜泵频率分别独立为30~80hz,优选40~60hz,包括但不限于30,35,40,45,50,55,60,65,70,75,80hz等。
19.在本发明的一些实例中,所述砂磨依次在25~35℃、45~55℃、60~70℃三个温度段进行。
20.在本发明的一些实例中,所述砂磨依次包括如下步骤:
21.第一步:砂磨温度为25~35℃,循环频率600~750rpm,隔膜泵频率30~80hz,砂磨0.25~0.5h;
22.第二步:砂磨温度45~55℃,循环频率760~950rpm,隔膜泵频率30~80hz,砂磨1~1.5h;
23.第三步:砂磨温度60~70℃,循环频率1000~1300rpm,隔膜泵频率30~80hz,砂磨1~1.5h。
24.在本发明的一些实例中,所述砂磨依次包括如下步骤:
25.第一步:砂磨温度为30
±
5℃,循环频率700
±
10rpm,隔膜泵频率50
±
5hz,砂磨0.25~0.5h;
26.第二步:砂磨温度50
±
5℃,循环频率800
±
10rpm,隔膜泵频率50
±
5hz,砂磨1~1.5h;
27.第三步:砂磨温度65
±
5℃,循环频率1100
±
10rpm,隔膜泵频率50
±
5hz,砂磨1~1.5h。
28.在本发明的一些实例中,所述砂磨的总时间为2.25~3.1h。
29.在本发明的一些实例中,所述烧结助剂包括氧化钇、氧化钙、氧化镁、氟化钙、氧化镧中的任意一种或多种。
30.在本发明的一些实例中,所述烧结助剂分散液的固含量≤60%,优选10%~60%,更优选35%~60%,包括但不限于5%,15%,20%,25%,30%,35%,40%,45%,50%,55%,60%等。固含量太高会影响砂磨速率,粒度无法控制在纳米范围内。固含量太低成本太高。
31.在本发明的一些实例中,所述烧结助剂分散液包括组分:烧结助剂、第一溶剂,所述第一溶剂包括异丙醇、无水乙醇、丁醇中的任意一种或多种。所述烧结助剂分散液还包括分散剂,所述分散剂包括蓖麻油、硬脂酸中的任意一种或两种,所述分散剂在烧结助剂分散
液中的质量百分比为0.75%~0.9%。烧结助剂分散液可通过将烧结助剂分散在第一溶剂中,加入适量分散剂,搅拌分散0.5~1h得到。
32.在本发明的一些实例中,所述砂磨结束后还包括过滤的步骤,过滤所采用的过滤网目数为1000~8000目,优选1500~3000目,包括但不限于1000,1500,2000,1500,3000,3500,4000,4500,5000,5500,6000,6500,7000,7500,8000目等。使用过滤网目数比烧结助剂球磨后的粒度大,其主要原因是砂磨过程中会加入分散剂包裹烧结助剂表面,其次烧结助剂浆料具有一定的固含量和黏度,会增加过滤难度,所以选用较大目数。
33.在本发明的一些实例中,所述烧结助剂浆料的d50和d100之差≤0.6um。
34.在本发明的一些实例中,所述氮化铝浆料的固含量为50%~80%。
35.在本发明的一些实例中,所述氮化铝浆料包括组分:氮化铝、第二溶剂、粘结剂,所述第二溶剂包括甲苯、异丙醇、丁酮中的任意一种或多种。
36.在本发明的一些实例中,所述粘结剂包括聚乙烯醇缩丁醛酯(pvb),其分子量为100000~120000。
37.在本发明的一些实例中,所述烧结助剂与氮化铝的质量关系为:m
烧结助剂
:(m
烧结助剂
+m
氮化铝
)=0.04~0.06,优选0.04~0.053。在本发明的一些实例中,所述混合浆料的粒度d50为1.1~1.5μm。
38.在本发明的一些实例中,所述混合浆料的固含量为60~80%。
39.在本发明的一些实例中,所述混合浆料的黏度为11000~12000pa
·
s(20℃,10rpm)。
40.在本发明的一些实例中,所述流延成型、排胶、烧结可采用本领域通用的技术。例如,可以按0.35~0.50m/min的流延速度进行流延成型,然后在80~85℃干燥后进行排胶。排胶后在真空、氮气气氛下,1650~1750℃下烧结3~5h。
41.相对于现有技术,本发明具有如下有益效果:
42.本发明的制备方法通过将烧结助剂进行分步砂磨,控制砂磨的循环频率,砂磨时间和砂磨温度,使其粒度分布在纳米范围内,降低了粒度,增加了比表,同时能够控制烧结助剂的d50和d100差在0.6μm内,增加了其在浆料中分布的均匀性,其次在烧结过程中,本发明得到的烧结助剂颗粒可降低烧结温度,同时在形成液相的过程中空隙产生,烧结成瓷更加致密,强度提高。
附图说明
43.图1为实施例1氮化铝陶瓷基板的制备流程示意图。
44.图2为实施例1和对比例1的氮化铝陶瓷基板的断面电镜图。
45.图3为对比例2~5的氮化铝陶瓷基板的断面电镜图。
46.图4为对比例6和对比例7的氮化铝陶瓷基板的断面电镜图。
具体实施方式
47.以下结合具体的实施例进一步说明本发明的技术方案。以下实施例中所用的原料,如无特殊说明,均可从常规商业途径得到;所采用的工艺,如无特殊说明,均采用本领域的常规工艺。
48.实施例1
49.本实施例制备一种氮化铝陶瓷基板,制备工艺流程图如图1所示,具体包括如下步骤:
50.s1:氧化钇砂磨
51.(1)第一阶段:将氧化钇粉体用异丙醇配制成溶液,加入适量分散剂(蓖麻油)0.8wt%,在搅拌缸内分散0.5小时;
52.(2)第二阶段:砂磨。砂磨分为三步进行,第一步:砂磨温度为30℃,循环频率700rpm,隔膜泵频率50hz,砂磨0.5h;第二步:砂磨温度50℃,循环频率800rpm,隔膜泵频率50hz,砂磨1h;第三步:砂磨温度65℃,循环频率1100rpm,隔膜泵频率50hz,砂磨1h;
53.(3)第三阶段:把分散好的氧化钇溶液过滤2000目滤网,得到氧化钇浆料,固含量为41%左右。
54.s2:氮化铝浆料配制:将氮化铝、甲苯和pvb按照12:3:5质量比配制成氮化铝浆料,固含量60%,将氮化铝浆料球磨分散。
55.s3:将步骤s1和s2的浆料球磨混合,最终浆料粒度d50在1.2μm,固含量设计为60%,黏度:11000pa
·
s。
56.s4:流延成型:将步骤s3得到的浆料流延成型,流延速度:0.50m/min,流延干燥温度:80℃。
57.s5:最后经过排胶,烧结成瓷,除粉得到成型的陶瓷基板。烧结时使用真空烧结炉,在氮气气氛下,1750℃下烧结3h,之后随炉降温。
58.实施例2
59.与实施例1的区别在于改变了步骤s1第二阶段氧化钇砂磨的时间,具体如下:
60.第二阶段:砂磨。砂磨分为三步进行,第一步:砂磨温度为30℃,循环频率700rpm,隔膜泵频率50hz,砂磨0.25h;第二步:砂磨温度50℃,循环频率800rpm,隔膜泵频率50hz,砂磨1.5h;第三步:砂磨温度65℃,循环频率1100rpm,隔膜泵频率50hz,砂磨1h。
61.其他步骤与实施例1相同。
62.实施例3
63.与实施例1的区别在于改变了步骤s1第二阶段氧化钇砂磨的时间,具体如下:
64.第二阶段:砂磨。砂磨分为三步进行,第一步:砂磨温度为30℃,循环频率700rpm,隔膜泵频率50hz,砂磨0.3h;第二步:砂磨温度50℃,循环频率800rpm,隔膜泵频率50hz,砂磨1.3h;第三步:砂磨温度65℃,循环频率1100rpm,隔膜泵频率50hz,砂磨1.5h。
65.其他步骤与实施例1相同。
66.实施例4
67.与实施例1的区别在于改变了步骤s1第二阶段氧化钇砂磨的时间,具体如下:
68.第二阶段:砂磨。砂磨分为三步进行,第一步:砂磨温度为30℃,循环频率700rpm,隔膜泵频率50hz,砂磨0.25h;第二步:砂磨温度50℃,循环频率800rpm,隔膜泵频率50hz,砂磨1h;第三步:砂磨温度65℃,循环频率1100rpm,隔膜泵频率50hz,砂磨1h。
69.其他步骤与实施例1相同。
70.对比例1
71.与实施例1的区别在于将步骤s1第二阶段的砂磨替换为球磨,具体球磨过程为:球
磨使用20l尼龙罐,砂磨球为氧化锆,料球比为1:3(即质量比氮化铝:氧化锆球只=1:3),转速频率50hz,球磨40h。
72.其他步骤与实施例1相同。
73.对比例2
74.与实施例1的区别在于采用如下步骤s1进行氧化钇砂磨,具体如下:
75.s1:氧化钇砂磨
76.(1)第一阶段:将氧化钇粉体用异丙醇配制成溶液,加入适量分散剂,在搅拌缸内分散0.5h;
77.(2)第二阶段:砂磨,砂磨温度65℃,循环频率1100rpm,隔膜泵频率50hz,砂磨2.5h。
78.(3)第三阶段:把分散好的氧化钇溶液过滤2000目滤网。
79.其他步骤与实施例1相同。
80.对比例3
81.与实施例1的区别在于采用如下步骤s1进行氧化钇砂磨,具体如下:
82.s1:氧化钇砂磨
83.(1)第一阶段:将氧化钇粉体用异丙醇配制成溶液,加入适量分散剂,在搅拌缸内分散0.5h;
84.(2)第二阶段:砂磨,砂磨温度30℃,循环频率700rpm,隔膜泵频率50hz,砂磨2.5h。
85.(3)第三阶段:把分散好的氧化钇溶液过滤2000目滤网。
86.其他步骤与实施例1相同。
87.对比例4
88.与实施例1的区别在于采用如下步骤s1进行氧化钇砂磨,具体如下:
89.s1:氧化钇砂磨
90.(1)第一阶段:将氧化钇粉体用异丙醇配制成溶液,加入适量分散剂,在搅拌缸内分散0.5h;
91.(2)第二阶段:砂磨,砂磨温度50℃,循环频率800rpm,隔膜泵频率50hz,砂磨2.5h;
92.(3)第三阶段:把分散好的氧化钇溶液过滤2000目滤网。
93.其他步骤与实施例1相同。
94.对比例5
95.与实施例1的区别在于采用如下步骤s1进行氧化钇砂磨,具体如下:
96.s1:氧化钇砂磨
97.(1)第一阶段:将氧化钇粉体用异丙醇配制成溶液,加入适量分散剂,在搅拌缸内分散0.5h;
98.(2)第二阶段:砂磨,第一步:砂磨温度为30℃,循环频率700rpm,隔膜泵频率50hz,砂磨0.5h;第二步:砂磨温度50℃,循环频率800rpm,隔膜泵频率50hz,砂磨1h;
99.(3)第三阶段:把分散好的氧化钇溶液过滤2000目滤网。
100.其他步骤与实施例1相同。
101.对比例6
102.与实施例1的区别在于采用如下步骤s1进行氧化钇砂磨,具体如下:
103.s1:氧化钇砂磨
104.(1)第一阶段:将氧化钇粉体用异丙醇配制成溶液,加入适量分散剂,在搅拌缸内分散0.5h;
105.(2)第二阶段:砂磨,第一步:砂磨温度50℃,循环频率800rpm,隔膜泵频率50hz,砂磨1h;第二步:砂磨温度65℃,循环频率1100rpm,隔膜泵频率50hz,砂磨1h;
106.(3)第三阶段:把分散好的氧化钇溶液过滤2000目滤网。
107.其他步骤与实施例1相同。
108.对比例7
109.与实施例1的区别在于采用如下步骤s1进行氧化钇砂磨,具体如下:
110.s1:氧化钇砂磨
111.(1)第一阶段:将氧化钇粉体用异丙醇配制成溶液,加入适量分散剂,在搅拌缸内分散0.5h;
112.(2)第二阶段:砂磨,第一步:砂磨温度为30℃,循环频率700rpm,隔膜泵频率50hz,砂磨0.5h;第二步:砂磨温度65℃,循环频率1100rpm,隔膜泵频率50hz,砂磨1h;
113.(3)第三阶段:把分散好的氧化钇溶液过滤2000目滤网。
114.其他步骤与实施例1相同。
115.性能测试:
116.1、氧化钇浆料的d50与d100:测试采用马尔文激光粒度仪,以无水乙醇为分散介质,先超声5分钟后进行测试。
117.2、翘曲测试:使用平行板翘曲仪对成瓷后的陶瓷基板进行翘曲测量,平行板标准间距=基板标准厚度+允许翘曲度值(1.8
‰
),陶瓷基板从平行板之间通过则视为翘曲合格。
118.3、粗糙度:使用粗糙度仪对陶瓷基板薄膜面和空气面进行粗糙度测量。
119.4、强度:将陶瓷基板激光划线为24*40mm规格的小板,然后使用万能电子材料测试机,通过断裂挤压测试出基板强度。
120.5、电镜:将成陶瓷基板断面擦拭干净,在0.8kv下放大1万倍观察晶粒形貌,同时在背散射模式下观察氧化钇分布。
121.6、热导率:采用lfa467导热系数测试仪(10mm*2.0mm规格样品),导热合格范围≥170w/(m
·
k)。
122.其中翘曲、粗糙度和强度均是取100个陶瓷基板进行测试,取测试结果平均值。
123.测试结果如下表所示。
124.表1.性能测试结果
[0125][0126]
根据上表的测试结果可见,实施例1~3采用特定的三步法对氧化钇进行预先分步砂磨后得到的氧化钇浆料具有d50与d100之差≤0.565μm的纳米粒子,具有非常好的均匀性,这样的氧化钇在浆料中分散更加均匀,制备得到的基板翘曲、粗糙度、导热性能都较为优良。
[0127]
相比之下,对比例1采用球磨的方法对氧化钇进行预处理,得到的氧化钇浆料的d50与d100之差增高,均匀性明显降低;同时氮化铝陶瓷基板的强度降低,粗糙度增高、翘曲增高。对比例2~7改变了砂磨的工序,不采用梯度的三步砂磨法,最终也造成氧化钇浆料的均匀性降低,氮化铝陶瓷基板的强度降低,粗糙度增高、翘曲增高。
[0128]
通过对实施例1与各对比例的所得氮化铝陶瓷基板的微观形貌进行观察,得到电镜图如图2~4所示。
[0129]
从电镜结果可以看出,实施例1采用分步砂磨方法得到的氮化铝陶瓷基板中,断面电镜无气孔、穿晶等现象,已达到烧结致密的程度;成瓷晶粒尺寸平均值在4.648μm,较对比例1~7的晶粒尺寸小0.8μm左右,说明通过采用特定的分步砂磨方法有效减少了晶粒过度长大形成的穿晶、断晶现象的发生,提高氮化铝陶瓷基板的致密性,最终改善氮化铝陶瓷基板的强度、粗糙度和翘曲,与表1的测试结果对应。
[0130]
上述实施例为本发明较佳的实施方式,但本发明的实施方式并不受上述实施例的限制,其他的任何未背离本发明的精神实质与原理下所作的改变、修饰、替代、组合、简化,均应为等效的置换方式,都包含在本发明的保护范围之内。