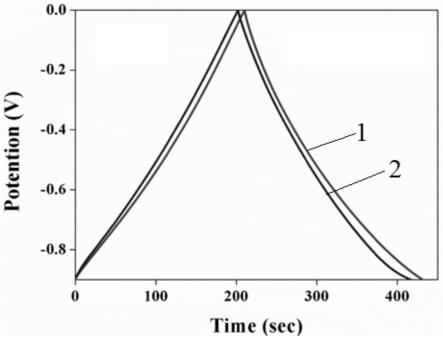
1.本发明属于工业固废处理技术领域。
背景技术:2.煤气化技术通过将煤进行不完全氧化来制备合成气(ch4、co等),近年来为煤炭资源清洁利用和煤化工做出了重要贡献。伴随着煤气化技术的广泛应用,煤气化细灰的产量也在迅速增加(约3000万吨/年)。然而,由于现有处理方式经济效益不高,导致目前煤气化细灰的处理方式依旧以堆存和掩埋为主,无法实现资源化利用,这造成了煤炭资源的浪费和严重的环境污染问题。
3.对于煤气化细灰的处理中,现有专利多采用浮选、重选等物理方法实现碳灰分离。专利《一种煤气化细渣的浮选工艺》(专利号为:201610261413.4、申请公布日:2017年10 月31日、申请公布号:cn107303539a)利用不同组成矿物表面的疏水性差异,分别使用500g/t 过硫酸钾、100g/t七水硫酸亚铁、5000g/t柴油、5000g/t仲辛醇实现煤气化细灰中碳资源的回收,但其使用浮选剂用量过大,存在运行成本较高和浮选回水有机污染物含量超标的问题。专利《利用煤气化细渣制备吸附材料的方法及制得的吸附材料》(专利号为: 201710154400.1、授权公布日:2019年10月11日、授权公布号:cn 107855103 b)通过重力旋流分离得富碳产品,并利用水热活化制备吸附产品提高价值,但由于煤气化细灰粒径较小,碳颗粒与灰分颗粒之间密度差异较小,存在分离效率低的问题。hf处理作为目前脱灰效率最高的方法,最终灰分含量可低于5%。但hf酸具有强腐蚀性以及高毒性,不但过程具有一定危险性,而且脱灰废液难以处理容易造成二次污染,现仅在实验室中使用无法实现大规模应用。
4.煤气化细灰中sio2的含量高,碱熔法能实现高效回收硅。专利《一种以粉煤灰为原料同步合成沸石及ldh的方法》(专利号为:201810906032.6、授权公布日:2021年8月6日、授权公布号:cn109107526b)通过在850℃下的碱熔处理实现了灰分矿物的高效消解,将其转变为可溶性硅酸盐,通过水热处理将硅酸盐产品进行收集,并为制备沸石提供了原料。然而传统碱熔处理温度较高(550~1000℃),远高于煤气化细灰的着火点(460~530℃),残碳存在燃烧损失的情况。因此,如何在保证煤气化细灰中碳回收率的基础上,实现其高效脱灰是煤气化细灰资源化、无害化处理急需解决的难题。
5.煤气化细灰中含有大量无定型二氧化硅,可用来制备水玻璃以实现煤气化的高值化处理。专利《一种利用粉煤灰制备高模数水玻璃的方法》(专利号为:201811395302.8、申请公布日:2019年2月15日、申请公开号:cn109336123a)将粉煤灰与氢氧化钠混合,1400℃下进行高温碱熔处理,将灰分矿物转变为可溶性硅酸盐,然后通过水浸成功制备了水玻璃产品,但由于处理温度高达850℃,熔融态naoh具有极强的腐蚀性,对设备耐腐蚀性要求较高。专利《利用粉煤灰同时制备sio2气凝胶和沸石的方法》(专利号为: 200910010685.7、申请公布日:2009年9月23日、申请公开号:cn101538046)将粉煤灰在600℃~900℃进行高温
活化处理,再与naoh溶液发生水热反应,利用常压干燥法将反应后水洗滤液制备得sio2气凝胶。综上可知,传统碱熔法制备水玻璃温度过高,能耗较大,为降低煤气化细灰制备水玻璃的成本。
6.同时煤气化细灰中灰分含量较高,且多为反应活性较高的无定型二氧化硅,具有作为白炭黑原材料的潜力。专利《一种从粉煤灰中提取高纯度氧化铝及硅胶的方法》(专利号为201010013749.1、授权公开日:2012年12月5日、授权公布号:cn101759210b)将粉煤灰与na2co3混合并通过高温焙烧(700~1000℃)、naoh浸取、选择性分离等步骤成功将粉煤灰中灰分矿物转变为可溶性硅酸盐,为白炭黑制备提供了优质原料,但处理温度较高,并且减压蒸馏能耗较大,存在成本较高的问题。专利《一种从粉煤灰中先提硅后提铝的方法》(专利号为200710062534.7、授权公开日:2010年6月9日、授权公布号: cn101125656b)通过naoh高压水热将粉煤灰中硅以硅酸钠的形式溶出,并利用碳分的方法制备白炭黑,该方法简化了提取工艺,提高了提取率,但由于高压水热处理无法将粉煤灰完全溶解,粉煤灰中硅依旧存在资源浪费的问题。目前,由于煤气化细灰含碳量较高 (10%~50%),若采用水热法制备白炭黑,残碳丰富的孔隙结构会使酸碱的用量提升,成本提高,并且无法实现煤气化细灰中si资源的完全性回收。而传统碱熔制备工艺处理温度较高(800℃以上),制备过程不仅需要投入大量热能,同时也造成了煤气化细灰中多孔碳资源的浪费。
技术实现要素:7.本发明要解决现有难以实现煤气化细灰的高值化利用,同时解决传统碱熔法温度过高,残碳存在燃烧损失的问题,进而提供利用低温碱熔法从煤气化细灰中回收残碳及硅酸钠的方法及应用。
8.利用低温碱熔法从煤气化细灰中回收残碳及硅酸钠的方法,它是按以下步骤进行的:
9.一、预处理:
10.除去煤气化细灰中金属杂质,干燥,得到除杂后的样品;
11.二、碱熔:
12.将除杂后的样品与固体碱混合,然后在温度为200℃~450℃的条件下,碱熔处理 20min~3h,最后取出样品并降低至室温,得到碱熔原样;
13.所述的除杂后的样品与固体碱的质量比为1:(0.5~5);
14.三、水浸处理:
15.将碱熔原样浸渍于水中,在温度为20℃~60℃的条件下,水浸1min~10min,得到水浸体系,将水浸体系进行真空抽滤处理,抽滤后的固体干燥得到残碳,抽滤后的液体为低模数硅酸钠溶液;
16.所述的碱熔原样与水的质量比为1:(1~10)。
17.利用低温碱熔法从煤气化细灰中回收残碳及硅酸钠的应用,利用低模数硅酸钠溶液制备水玻璃或白炭黑,利用残碳制备活性炭。
18.本发明的有益效果是:
19.1、本发明利用碱熔法回收煤气化细灰中残碳。该方法与传统hf酸洗方法相比绿色环保、安全可靠,与传统碱熔法相比,本发明所用低温碱熔处理对煤气化细灰的适用性更
强,能够有效回收其中残碳。本发明的实施不仅实现了煤气化细灰中c、si资源的高效回收(可燃物碳回收率高达80.65%)、同时由于回收的碳具有丰富的孔隙结构,可用来制备多孔材料为煤气化细灰的高值化利用提供了一种方案。本发明通过控制碱熔温度 (200℃~450℃)和时间,诱导熔融态碱与煤气化细灰中灰分矿物发生靶向性反应,使灰分矿物转变为可溶性盐并保留残碳。然后通过水浸处理后得到了灰分含量低于3%、比表面积为445.43m2/g、固定碳含量为91.26%的纯碳样品和低模数硅酸钠溶液。该处理方法避免了二次污染的产生,具有安全性高、反应时间短、易操作和绿色环保的特点。本发明的实施不仅实现了煤气化细灰中c、si资源的高效回收、同时也为煤气化细灰的大规模处理和高效脱灰提供了一种更为绿色的方案。
20.2、本发明提出利用煤气化细灰制备水玻璃。采用煤气化细灰作为硅源代替价格较高的石英砂、硅灰石等硅胶,解决传统水玻璃原材料昂贵、能耗高的缺陷。有利于煤气化细灰的规模化、高值化利用。以煤气化细灰为硅源,充分利用了煤气化细灰的优点。符合国家节能减排、废弃物资源化利用、可持续发展的基本国策,同时解决了传统水玻璃制备过程复杂、污染严重以及成本高的问题。
21.3、本发明提出利用碱熔法从煤气化细灰中制备白炭黑的方法。该方法设备要求不高、能耗低、投资小且通过此方法制备得纳米白炭黑平均粒径可达到20nm,氮吸附平均比表面积为120.9m2/g可投入于商业应用,且采用煤气化为原材料解决环境问题和工业原料经济替代双重问题。这对于实现煤气化细灰高值化、可持续性利用具有重要意义。
22.4、本发明基于低温碱熔法,成功利用煤气化细灰制备了活性炭,与传统活性炭制备工艺相比,本发明所用制备方法无需使用hf酸脱灰,且制备过程无二次污染产生。所得活性炭产品的比表面积高达750m2/g~860m2/g。该样品作为超级电容器活性炭时,在0.5a/g 的电流密度下质量比电容达到了110~125f/g。本发明在实现煤气化细灰高值化利用的同时,活性炭制备工艺更为绿色,对于改进活性炭制备工艺具有重要意义。
附图说明
[0023][0024]
图1为实施例一制备的残碳比表面积测试图;
[0025]
图2为实施例四制备的白炭黑sem图;
[0026]
图3为实施例四制备的白炭黑比表面积测试图;
[0027]
图4为在电流密度为0.5a/g下,以活性炭制备的三电极电池的循环伏安曲线图,1 为ac-zn-8-4-1,2为ac-h3po
4-5-4-1;
[0028]
图5为在电流密度为0.5a/g下,以活性炭制备的三电极电池的充放电曲线图,1为 ac-zn-8-4-1,2为ac-h3po
4-5-4-1。
具体实施方式
[0029]
具体实施方式一:本实施方式利用低温碱熔法从煤气化细灰中回收残碳及硅酸钠的方法,它是按以下步骤进行的:
[0030]
一、预处理:
[0031]
除去煤气化细灰中金属杂质,干燥,得到除杂后的样品;
[0032]
二、碱熔:
[0033]
将除杂后的样品与固体碱混合,然后在温度为200℃~450℃的条件下,碱熔处理20min~3h,最后取出样品并降低至室温,得到碱熔原样;
[0034]
所述的除杂后的样品与固体碱的质量比为1:(0.5~5);
[0035]
三、水浸处理:
[0036]
将碱熔原样浸渍于水中,在温度为20℃~60℃的条件下,水浸1min~10min,得到水浸体系,将水浸体系进行真空抽滤处理,抽滤后的固体干燥得到残碳,抽滤后的液体为低模数硅酸钠溶液;
[0037]
所述的碱熔原样与水的质量比为1:(1~10)。
[0038]
本实施方式中煤气化细灰作为一种煤基工业固废,其具有产量高、碳含量高,且残碳孔隙结构丰富的特征,完全性脱灰(灰分含量<5%)处理后得到的富碳产品是制备活性炭的优质原料,与目前主流的活性炭制备原料—生物质相比,其在制备过程中无需碳化过程。因此,为实现煤气化细灰的高值化和无害化处理同时,降低处理能耗。
[0039]
本实施方式的有益效果是:
[0040]
1、本实施方式利用碱熔法回收煤气化细灰中残碳。该方法与传统hf酸洗方法相比绿色环保、安全可靠,与传统碱熔法相比,本实施方式所用低温碱熔处理对煤气化细灰的适用性更强,能够有效回收其中残碳。本实施方式的实施不仅实现了煤气化细灰中c、si 资源的高效回收(可燃物碳回收率高达80.65%)、同时由于回收的碳具有丰富的孔隙结构,可用来制备多孔材料为煤气化细灰的高值化利用提供了一种方案。本实施方式通过控制碱熔温度(200℃~450℃)和时间,诱导熔融态碱与煤气化细灰中灰分矿物发生靶向性反应,使灰分矿物转变为可溶性盐并保留残碳。然后通过水浸处理后得到了灰分含量低于 3%、比表面积为445.43m2/g、固定碳含量为91.26%的纯碳样品和低模数硅酸钠溶液。该处理方法避免了二次污染的产生,具有安全性高、反应时间短、易操作和绿色环保的特点。本实施方式的实施不仅实现了煤气化细灰中c、si资源的高效回收、同时也为煤气化细灰的大规模处理和高效脱灰提供了一种更为绿色的方案。
[0041]
2、本实施方式提出利用煤气化细灰制备水玻璃。采用煤气化细灰作为硅源代替价格较高的石英砂、硅灰石等硅胶,解决传统水玻璃原材料昂贵、能耗高的缺陷。有利于煤气化细灰的规模化、高值化利用。以煤气化细灰为硅源,充分利用了煤气化细灰的优点。符合国家节能减排、废弃物资源化利用、可持续发展的基本国策,同时解决了传统水玻璃制备过程复杂、污染严重以及成本高的问题。
[0042]
3、本实施方式提出利用碱熔法从煤气化细灰中制备白炭黑的方法。该方法设备要求不高、能耗低、投资小且通过此方法制备得纳米白炭黑平均粒径可达到20nm,氮吸附平均比表面积为120.9m2/g可投入于商业应用,且采用煤气化为原材料解决环境问题和工业原料经济替代双重问题。这对于实现煤气化细灰高值化、可持续性利用具有重要意义。
[0043]
4、本实施方式基于低温碱熔法,成功利用煤气化细灰制备了活性炭,与传统活性炭制备工艺相比,本实施方式所用制备方法无需使用hf酸脱灰,且制备过程无二次污染产生。所得活性炭产品的比表面积高达750m2/g~860m2/g。该样品作为超级电容器活性炭时,在0.5a/g的电流密度下质量比电容达到了110~125f/g。本实施方式在实现煤气化细灰高值化利用的同时,活性炭制备工艺更为绿色,对于改进活性炭制备工艺具有重要意义。
[0044]
具体实施方式二:本实施方式与具体实施方式一不同的是:步骤一中除去煤气化细灰中金属杂质具体是在8000~12000高斯条件下,对煤气化细灰进行磁选脱铁处理。其它与具体实施方式一相同。
[0045]
具体实施方式三:本实施方式与具体实施方式一或二之一不同的是:步骤二中所述的固体碱为naoh、koh、na2co3、k2co3和ca(oh)2中的一种或其中几种的组合;步骤二中碱熔处理的气氛为空气、氮气、氩气和二氧化碳中的一种或其中几种的组合。其它与具体实施方式一或二相同。
[0046]
具体实施方式四:本实施方式与具体实施方式一至三之一不同的是:步骤三中所述的低模数硅酸钠溶液的模数为0.1~0.5。其它与具体实施方式一至三相同。
[0047]
具体实施方式五:本实施方式利用低温碱熔法从煤气化细灰中回收残碳及硅酸钠的应用,利用低模数硅酸钠溶液制备水玻璃或白炭黑,利用残碳制备活性炭。
[0048]
具体实施方式六:本实施方式与具体实施方式五不同的是:利用低模数硅酸钠溶液制备水玻璃时,具体是按以下步骤进行:在室温及搅拌条件下,向低模数硅酸钠溶液中添加调整剂,得到水玻璃;所述的低模数硅酸钠溶液与调整剂的质量比为1:(0.05~0.5);所述的调整剂为硝酸铵、硫酸铵、盐酸和硅酸中的一种或其中几种的组合;所述的水玻璃的模数为0.5~3.5。其它与具体实施方式五相同。
[0049]
具体实施方式七:本实施方式与具体实施方式五或六之一不同的是:利用低模数硅酸钠溶液制备白炭黑时,具体是按以下步骤进行:
[0050]
①
、在室温及搅拌条件下,向低模数硅酸钠溶液中添加调整剂,得到模数为4~5.5 的硅酸钠溶液;所述的低模数硅酸钠溶液与调整剂的质量比为1:(0.5~5.5);所述的调整剂为硝酸铵、硫酸铵和硅酸中的一种或其中几种的组合;
[0051]
②
、对模数为4~5.5的硅酸钠溶液进行老化处理,过滤得到沉淀物,利用去离子水对沉淀物进行洗涤,最后在温度为40℃~60℃的条件下,干燥4h~7h。其它与具体实施方式五或六相同。
[0052]
具体实施方式八:本实施方式与具体实施方式五至七之一不同的是:步骤
②
中所述的老化处理具体为自然条件沉淀12h~72h,或者在温度为40℃~60℃的条件下,水热处理12h~24h。其它与具体实施方式五至七相同。
[0053]
具体实施方式九:本实施方式与具体实施方式五至八之一不同的是:利用残碳制备活性炭时,具体是按以下步骤进行:将残碳与活化剂混合均匀,得到混合物,在特定气氛及升温速度为10℃/min~20℃/min的条件下,将混合物升温至温度为500℃~1000℃,再在特定气氛及温度为500℃~1000℃的条件下,活化0.5h~3h,活化后置于蒸馏水中清洗至中性,抽滤烘干;所述的残碳与活化剂的质量比为1:(1~5);所述的特定气氛为水蒸气、 co2、n2和ar中的一种或其中几种组合,所述的特定气氛流量为100ml/min~1000ml/min;所述的活化剂为koh、naoh、zncl2、znso4和h3po4中的一种或其中几种混合。其它与具体实施方式五至八相同。
[0054]
具体实施方式十:本实施方式与具体实施方式五至九之一不同的是:利用残碳制备活性炭时,具体是按以下步骤进行:在含有活性气体的气氛及升温速度为10℃/min ~20℃/min的条件下,将残碳升温至温度为500℃~1000℃,然后在含有活性气体的气氛及温度为500℃~1000℃的条件下,将残碳活化0.5h~3h,活化后置于蒸馏水中清洗至中性,抽滤
烘干;所述的含有活性气体的气氛为活性气体、或者为惰性气体与活性气体的组合;所述的活性气体为水蒸气和co2中的一种或两种组合;所述的惰性气体为n2和ar中的一种或两种组合;所述的含有活性气体的气氛流量为100ml/min~1000ml/min。其它与具体实施方式五至九相同。
[0055]
采用以下实施例验证本发明的有益效果:
[0056]
实施例一:
[0057]
利用低温碱熔法从煤气化细灰中回收残碳及硅酸钠的方法,它是按以下步骤进行的:
[0058]
一、预处理:
[0059]
除去煤气化细灰中金属杂质,干燥,得到除杂后的样品;
[0060]
所述的煤气化细灰为干灰;
[0061]
二、碱熔:
[0062]
将除杂后的样品与固体碱置于陶瓷研钵中研磨混合均匀,然后在温度为400℃的条件下,碱熔处理35min,最后取出样品并降低至室温,得到碱熔原样;
[0063]
所述的除杂后的样品与固体碱的质量比为1:4.5;
[0064]
三、水浸处理:
[0065]
将碱熔原样浸渍于水中,在温度为40℃的条件下,水浸5min,得到水浸体系,将水浸体系进行真空抽滤处理,抽滤后的固体干燥得到残碳,抽滤后的液体为低模数硅酸钠溶液;
[0066]
所述的碱熔原样与水的质量比为1:8。
[0067]
煤气化细灰包括干灰,水中灰和饼灰,步骤一中干灰是干灰为煤气化细灰中的一种。
[0068]
步骤一中除去煤气化细灰中金属杂质具体是在12000高斯条件下,对煤气化细灰进行磁选脱铁处理。
[0069]
步骤二中所述的固体碱为naoh。
[0070]
步骤二中碱熔处理的气氛为空气。
[0071]
步骤三制备的低模数硅酸钠溶液的模数为0.43。
[0072]
步骤三中将碱熔原样浸渍于水,具体是利用40℃的蒸馏水将碱熔原样冲洗至烧杯中。
[0073]
碱熔处理后可燃物(碳)的回收率高达80.65%,通过碱熔处理后,灰分含量由煤气化细灰中的58.93%降低至残碳中的2.83%,固定碳含量由煤气化细灰中的37.55%增加至残碳中的91.26%,实现了煤气化细灰中残碳的高效回收。
[0074]
图1为实施例一制备的残碳比表面积测试图;由图可知,回收所得残碳的比表面积达到了445.43m2/g,具有丰富的孔隙结构。
[0075]
实施例二:利用实施例一制备的低模数硅酸钠溶液制备水玻璃,具体是按以下步骤进行:在室温及搅拌条件下,向低模数硅酸钠溶液中添加调整剂,搅拌2h,得到水玻璃;所述的低模数硅酸钠溶液与调整剂的质量比为1:0.2;所述的调整剂为硝酸铵;按照国标 gb\t 4209-2008测得水玻璃模数为1.21。
[0076]
实施例三:利用实施例一制备的低模数硅酸钠溶液制备水玻璃,具体是按以下步
骤进行:在室温及搅拌条件下,向低模数硅酸钠溶液中添加调整剂,搅拌2h,得到水玻璃;所述的低模数硅酸钠溶液与调整剂的质量比为1:0.2;所述的调整剂为硅酸;按照国标 gb\t 4209-2008测得水玻璃模数为3.1。
[0077]
实施例四:利用实施例一低模数硅酸钠溶液制备白炭黑时,具体是按以下步骤进行:
[0078]
①
、在室温及搅拌条件下,向低模数硅酸钠溶液中添加调整剂,搅拌2h,得到模数为5.01的硅酸钠溶液;所述的低模数硅酸钠溶液与调整剂的质量比为1:0.5;所述的调整剂为硅酸;
[0079]
②
、对模数为5.01的硅酸钠溶液进行老化处理,过滤得到沉淀物,利用去离子水对沉淀物进行洗涤,最后在温度为50℃的条件下,干燥5h,得到白炭黑;步骤
②
中所述的老化处理具体为自然条件沉淀48h。
[0080]
图2为实施例四制备的白炭黑sem图;由图可知,制备所得白炭黑产品的平均粒度约20nm,已达到纳米级。
[0081]
图3为实施例四制备的白炭黑比表面积测试图;由图可知,白炭黑比表面积达到了 120.9m2/g。
[0082]
实施例五:利用实施例一制备的残碳制备活性炭时,具体是按以下步骤进行:将残碳与活化剂于玛瑙研钵中混合均匀,得到混合物,在特定气氛及升温速度为15℃/min的条件下,将混合物升温至温度为800℃,再在特定气氛及温度为800℃的条件下,活化1h,活化后置于蒸馏水中清洗至中性,抽滤烘干,得到活性炭;所述的残碳与活化剂的质量比为1:4;所述的特定气氛为氮气,所述的特定气氛流量为1l/min;所述的活化剂为zncl2;活性炭记为ac-zn-8-4-1。
[0083]
通过氮气吸附法得到,实施例五制备的活性炭比表面积为860m2/g。
[0084]
实施例六:利用实施例一制备的残碳制备活性炭时,具体是按以下步骤进行:将残碳与活化剂于玛瑙研钵中混合均匀,得到混合物,在特定气氛及升温速度为20℃/min的条件下,将混合物升温至温度为500℃,再在特定气氛及温度为500℃的条件下,活化1h,活化后置于蒸馏水中清洗至中性,抽滤烘干;所述的残碳与活化剂的质量比为1:4;所述的特定气氛为氮气,所述的特定气氛流量为1l/min;所述的活化剂为h3po4。活性炭记为ac-h3po
4-5-4-1。
[0085]
通过氮气吸附法得到,实施例六制备的活性炭比表面积为750m2/g。
[0086]
将24mg ac-zn-8-4-1或ac-h3po
4-5-4-1、3mg乙炔黑及3mg聚四氟乙烯按 80%:10%:10%的质量比混合均匀,然后加入0.5ml n-甲基-2-吡咯烷酮(nmp)溶剂,得到浆料,将浆料均匀涂覆在泡沫镍集电极上(面积为1cm2),涂覆质量约5mg。将涂覆完的电极置于120℃真空干燥箱中干燥12h,降至室温后取出并在10mpa压力下进行压片,得到样品涂覆的集电器,在三电极电池中:铂片用作对电极,饱和甘汞电极用作参比电极,样品涂覆的集电器作为工作电极,6m的koh溶液作为电解液。
[0087]
图4为在电流密度为0.5a/g下,以活性炭制备的三电极电池的循环伏安曲线图,1 为ac-zn-8-4-1,2为ac-h3po
4-5-4-1;图5为在电流密度为0.5a/g下,以活性炭制备的三电极电池的充放电曲线图,1为ac-zn-8-4-1,2为ac-h3po
4-5-4-1;
[0088]
表1
[0089][0090]
由图4可知,制备所得的活性炭表现出双电层超级电容器典型的类矩形cv曲线,说明其具有良好电容特性。由图5及表1可知,制备所得的活性炭产品在电流密度为0.5a/g 时,样品的质量比电容达到了100f/g以上。