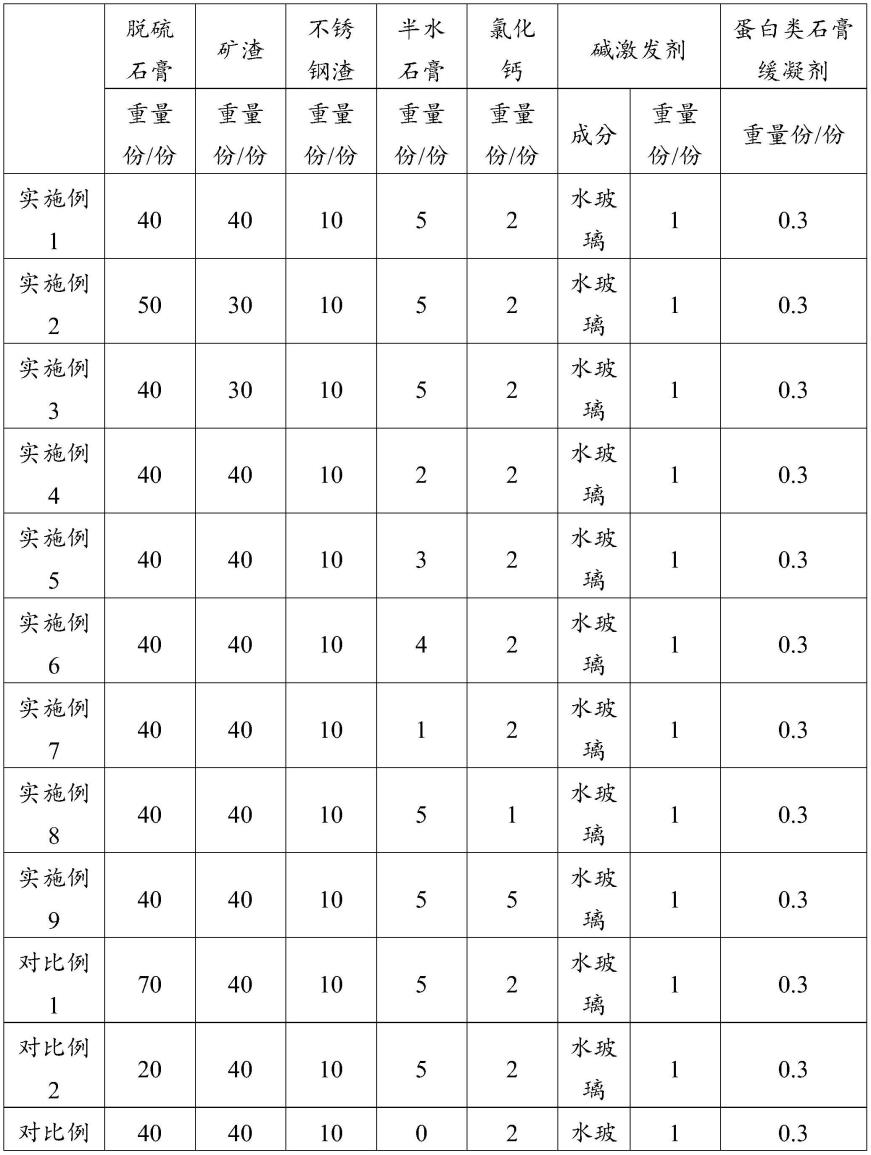
1.本发明属于建筑材料技术领域,具体涉及一种复合胶凝材料及其制备方法和应用。
背景技术:2.脱硫石膏(主要成分为二水硫酸钙,caso4·
2h2o)是火力电厂烟气湿法脱硫产生的工业固废,脱硫石膏的大面积堆放不仅会占用土地资源,还会污染地表水、地下水和大气环境,各国都在加强对脱硫石膏的综合利用研究。目前,脱硫石膏主要应用于建筑材料,可用来生产石膏粉、制备石膏制品;煅烧后的脱硫石膏(又称半水石膏,主要成分为半水硫酸钙,caso4·
0.5h2o)可用于替代水泥,生产脱硫建筑石膏胶凝材料;还可以在硅酸盐水泥生产过程中加入脱硫石膏作为缓凝剂,能够提高硅酸盐水泥的强度。此外,在脱硫石膏中引入激发剂、增强剂、防水剂等改性组分,可以有效改善石膏胶凝材料的耐水性、吸水性,还能提高材料的强度,拓宽石膏胶凝材料的应用领域。
3.然而,由于烟气湿法脱硫工艺中水的循环使用,使脱硫石膏中氯离子含量较高,远超gb/t 37785-2019《烟气脱硫石膏》中规定氯离子含量≤600mg/kg 的要求,并且较高含量的氯离子会导致脱硫石膏品质下降,极大限制了脱硫石膏的应用。采用高氯离子含量的脱硫石膏制备的水泥会导致混凝土的冻融和混凝土中的钢筋锈蚀,严重影响水泥的使用质量和混凝土建筑物的寿命。在石膏制品中采用氯离子含量较高的脱硫石膏还会导致石膏制品出现返潮、泛黄、长毛、开裂等现象。同时,氯离子还会增加石膏制品的含水率,降低其抗压强度,使其受潮变形,造成严重的安全问题。
4.cn101538140b公开了一种脱硫石膏基钢渣复合胶凝材料,该复合胶凝材料由脱硫石膏、钢渣和激发剂制备而成,将两种工业废渣结合在一起,充分提高了钢渣与脱硫石膏的利用率,能够形成一种保温、隔热、隔声性能良好的石膏材料,但是该脱硫石膏基钢渣复合胶凝材料具有较低的早期强度,其3天的抗压强度和抗折强度只有3.555mpa和10.75mpa,严重限制了该脱硫石膏基钢渣复合胶凝材料在混凝土中的应用。
5.因此,急需开发一种能够固化脱硫石膏中含量较高的氯离子、并且具有较高的早期强度和优异的耐水性能的复合胶凝材料。
技术实现要素:6.本发明的目的在于克服现有技术的不足之处而提供一种能够固化脱硫石膏中高含量的氯离子,并且具有较高的早期强度和优异的耐水性能的复合胶凝材料,使用本发明复合胶凝材料能够提高工业固废的利用率。
7.为了实现上述目的,本发明采取的技术方案为:
8.第一方面,本发明提供了一种复合胶凝材料,所述复合胶凝材料包括:脱硫石膏、矿渣、半水石膏、氯化钙、碱激发剂和缓凝剂;所述脱硫石膏和半水石膏的氯离子含量均≥1000mg/kg。
9.本发明在脱硫石膏中加入碱激发剂,一方面能够为复合胶凝材料提供有利于水化的碱性环境,提高脱硫石膏的反应活性,另一方面碱激发剂自身的独特结构和较高的力学性能还可以对复合胶凝材料的力学性能起到增强作用。
10.一般脱硫石膏在建筑材料中的应用限定氯离子含量为≤600mg/kg,以确保建筑材料的性能,而本发明脱硫石膏和半水石膏的氯离子含量≥1000mg/kg,不仅限制了其在建筑材料中的应用,随意堆放还会造成对环境的污染。本发明的发明人在大量的研究中发现,在脱硫石膏中加入矿渣,可以通过物理吸附和化学结合的方法来固化脱硫石膏中含量较高的氯离子。在碱性条件下,矿渣与脱硫石膏共同发生水化反应,生成的水化产物有硅铝酸盐、水化硅酸钙(c-s
‑ꢀ
h)凝胶以及钙矾石相晶体,由于其水化产物中c-s-h凝胶具有很大的比表面积,对脱硫石膏中的氯离子产生较强的物理吸附作用,能够使脱硫石膏中含量较高的氯离子不易渗出来,从而达到固化氯离子的效果;此外,矿渣与脱硫石膏的水化产物可以与氯离子反应生成friedel’s盐与kuzel’s盐,通过化学结合的方法进一步固化脱硫石膏中的氯离子。
11.本发明中加入半水石膏,不仅能够降低复合胶凝材料的凝结时间,还可以增强复合胶凝材料的早期强度。半水石膏主要成分为半水硫酸钙,半水石膏在复合胶凝材料中发生水化反应需要消耗更多的水,与水反应后生成的二水石膏可以增强脱硫石膏的水化反应,从而降低复合胶凝材料的凝结时间,并且半水石膏水化后生成的硫酸钙晶须具有一定的强度,可以提高复合胶凝材料的早期强度。
12.本发明加入氯化钙,一方面可以提高复合胶凝材料中游离钙离子的浓度,在碱激发剂的作用下,游离的钙离子能够与矿渣、不锈钢渣反应生成硅酸钙聚合物,进一步提高水化产物的稳定性;另一方面由于氯化钙具有比较好的吸水性能,在复合胶凝材料中加入少量的氯化钙还可以增强其耐水性。
13.作为本发明所述复合胶凝材料的优选实施方式,所述复合胶凝材料包括以下重量份的组分:脱硫石膏30~50份,矿渣30~50份,半水石膏1~5份,氯化钙1~5份,碱激发剂1~5份,缓凝剂0.2~0.5份。
14.研究表明,当本发明脱硫石膏低于30份时,能够增加复合胶凝材料的早期强度,还会加速凝结复合胶凝材料,导致凝结时间较短,不利于复合胶凝材料的施工应用;但当脱硫石膏高于30份时,会降低复合胶凝材料的早期强度,同时由于脱硫石膏中氯离子的含量较高,导致复合胶凝材料泡水后出现开裂现象。
15.此外,本发明中加入重量份为1~5份的半水石膏,可以改善复合胶凝材料的凝结时间和提高早期强度,而当不加半水石膏时,不仅会导致复合胶凝材料的凝结时间延长,还会使其强度降低。
16.作为本发明所述复合胶凝材料的优选实施方式,所述脱硫石膏和矿渣的重量比为脱硫石膏:矿渣=(3~5):3。
17.本发明的发明人通过对脱硫石膏-矿渣体系用量进行大量研究发现,通过将脱硫石膏与矿渣控制在上述重量比范围内,将矿渣与脱硫石膏混合,在碱激发剂的作用下,能够更好地固化脱硫石膏中的氯离子,提高复合胶凝材料的早期强度和凝结时间。而脱硫石膏-矿渣体系中矿渣的用量低于脱硫石膏的用量时,会导致复合胶凝材料的凝结时间延长和早期强度降低,说明矿渣用量较少不能很好地固化脱硫石膏中含量较高的氯离子;降低脱硫
石膏的用量、增加矿渣的用量,虽然会提升复合胶凝材料的早期强度,但与本发明提高工业固废中脱硫石膏的利用率的目的相反,从而降低复合胶凝材料的经济性。
18.作为本发明所述复合胶凝材料的优选实施方式,所述半水石膏和缓凝剂的重量比为半水石膏:缓凝剂=(3~5):0.3。
19.本发明选用蛋白类石膏缓凝剂,具有更强的表面吸附和钙离子螯合性能,与半水石膏复合使用,可以抑制半水石膏遇水转化为脱硫石膏并减少结晶的析出,从而调节复合胶凝材料的凝结固化时间。研究表明,缓凝剂用量不变,降低半水石膏的用量,会导致本发明复合胶凝材料的凝结时间延长,对其早期强度的影响较大,本发明通过大量试验验证,当半水石膏和缓凝剂优选的重量比为半水石膏:缓凝剂=(3~5):0.3时,本发明复合胶凝材料的凝结时间和早期强度性能较好。
20.作为本发明所述复合胶凝材料的优选实施方式,所述复合胶凝材料还包括不锈钢渣10~20重量份。
21.作为本发明所述复合胶凝材料的优选实施方式,所述碱激发剂为氢氧化钙、氢氧化钠、水玻璃中的至少一种。
22.作为本发明所述复合胶凝材料的优选实施方式,所述缓凝剂为蛋白类石膏缓凝剂。
23.第二方面,本发明还提供了上述复合胶凝材料的制备方法,其包括以下步骤:
24.(1)称取脱硫石膏和碱激发剂,混合,搅拌均匀,陈化≥1天,得到沉降物;
25.(2)将步骤(1)所述沉降物干燥,使得沉降物中水分的质量分数≤1%,得到混合物料;
26.(3)称取脱硫石膏,煅烧,得到半水石膏;
27.(4)称取矿渣、不锈钢渣、氯化钙、缓凝剂、步骤(2)所述混合物料和步骤(3)所述半水石膏,混合,球磨,得到所述复合胶凝材料。
28.作为本发明所述复合胶凝材料的制备方法的优选实施方式,所述步骤 (4)中球磨的料球比为2:3,球磨时间为12~48h,所述复合胶凝材料的比表面积为5500~6000m2/g。
29.本发明所使用的机械球磨是通过物理活化的方式使复合胶凝材料进行细化,不仅能够加速复合胶凝材料的水化反应速率和反应程度、提高混凝土的早期强度,还可以提高复合胶凝材料粉体的表面能,降低粉体参与水化反应所需的能量,从而增强复合胶凝材料的反应活性。
30.第三方面,本发明还提供了上述复合胶凝材料在建筑材料领域中的应用。
31.与现有技术相比,本发明的有益效果为:本发明提供的复合胶凝材料,能够固化脱硫石膏中含量较多的氯离子,还能够增强复合胶凝材料的早期强度和优异的耐水性能;本发明通过机械球磨和碱激发剂从物理活化和化学激发的方法,提高复合胶凝材料的反应活性。本发明提供的复合胶凝材料具有环保、提高固废利用率等特点,能够广泛应用于建筑材料中。
具体实施方式
32.下面结合实施例,对本发明的技术方案作进一步说明。显然,所描述的实施例仅仅是本发明的一部分实施例,而不是全部的实施例。基于本发明中的实施例,本领域普通技术
人员在没有做出创造性劳动前提下所获得的所有其他实施例,都属于本发明保护的范围。实施例所使用的方法或操作,如无特别说明,均为本领域的常规方法或常规操作。
33.下述实施例中,按照gb/t 1346-2011《水泥标准稠度用水量、凝结时间、安定性检验方法》测定初凝时间和终凝时间,按照gb/t 17671-1999《水泥胶砂强度检验方法》测定抗压强度和抗折强度,并将试样块在标准养护箱中养护 3天,放入水中浸泡,观察是否开裂。
34.实施例1~9和对比例1~5
35.本发明实施例1~9和对比例1~5高氯复合胶凝材料的各组分及重量份如下表1所示。
36.本发明实施例1~9和对比例1~5所述高氯脱硫石膏胶凝材料的制备方法包括以下步骤:
37.(1)称取脱硫石膏和碱激发剂,混合,搅拌均匀,陈化1天,得到沉降物;
38.(2)将步骤(1)所述沉降物在50℃烘干,使沉降物中水分质量分数≤ 1%,得到混合物料;
39.(3)称取脱硫石膏,在150℃煅烧,得到半水石膏;
40.(4)按比例称取矿渣、不锈钢渣、氯化钙、缓凝剂、步骤(2)所述混合物料和步骤(3)所述半水石膏,混合投入球磨机中进行机械球磨,料球比为2:3,设定球磨时间为24h,得到所述复合胶凝材料,所述复合胶凝材料的比表面积为5500~6000m2/g。
41.表1
[0042][0043][0044]
表2
[0045][0046][0047]
由表1和表2可知,实施例1~9所述复合胶凝材料具有较好的凝结时间、抗压强度和抗折强度,均能满gb175-2020《通用硅酸盐水泥》中强度等级 32.5的抗压强度和抗折强
度的要求,并且在泡水后均没有开裂的现象,其中实施例1的复合胶凝材料的综合性能最佳。
[0048]
比较实施例1~3与对比例1~2可知,提高脱硫石膏-矿渣体系中脱硫石膏的用量,不仅会使复合胶凝材料的初凝时间和终凝时间延长,还会大幅度的降低其抗压强度和抗折强度;并且由于加入的脱硫石膏中高含量的氯离子使试样块的致密性与反应性变差,从而使胶凝材料耐水性变差,对比例1在泡水后还出现开裂现象;而降低脱硫石膏与矿渣体系中脱硫石膏的用量,虽然会提高复合胶凝材料的早期的抗压强度和抗折强度,但是会大幅度减少复合胶凝材料的低凝结时间,影响复合胶凝材料在混凝土中的应用,并且还会降低工业固废脱硫石膏的利用率。因此,在综合考虑各方面性能的基础上,采用本发明脱硫石膏与矿渣的重量份配比时,能够使复合胶凝材料具有较好的耐水性和凝结时间。
[0049]
比较实施例1、实施例4~7和对比例3可知,半水石膏的用量对复合胶凝材料的凝结时间和早期强度影响较大,半水石膏的用量越多,复合胶凝材料的凝结时间越短,并且3天的抗压强度和抗折强度最高;不加半水石膏导致凝结时间延长,并且降低复合胶凝材料的抗压强度和抗折强度。
[0050]
比较实施例1、实施例8~9和对比例4~5可知,加入适量的氯化钙对复合胶凝材料的后期强度提升较为明显,这是由于氯化钙中的钙离子会加速复合胶凝材料的水化反应,从而使其微观结构更加密实。但在加入氯化钙时需要控制用量,由于复合胶凝材料中脱硫石膏含有较高含量的氯离子,会降低氯化钙的溶解度,若氯化钙的加入量过多,会导致其结晶析出,结构遭到破坏,从而降低复合胶凝材料的抗压强度和抗折强度。
[0051]
最后所应当说明的是,以上是实施例仅用以说明本发明的技术方案而非对本发明保护范围的限制,尽管参照较佳实施例对本发明作了详细说明,本领域的普通技术人员应当理解,可以对本发明的技术方案进行修改或者等同替换,而不脱离本发明技术方案的实质和范围。