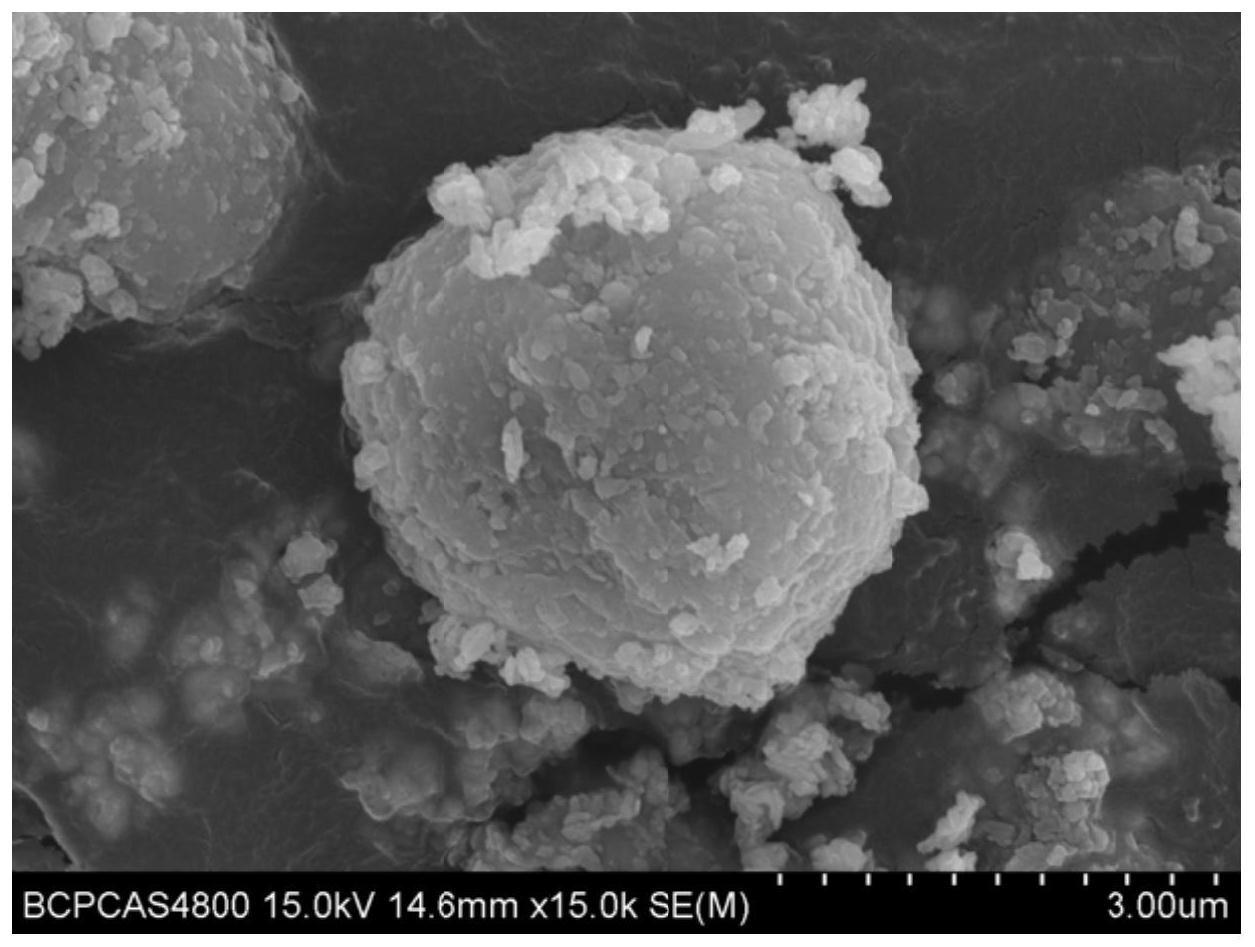
一种杨梅状核壳结构al/ti/cuo微纳复合含能材料及其制备方法
技术领域
1.本发明涉及一种杨梅状核壳结构al/ti/cuo微纳复合含能材料及其制备方法,属于含能复合材料技术领域。
背景技术:2.近年来,在美、俄等国的高能量密度材料应用牵引下,全球掀起了新型含能材料研究热潮,复合含能材料(energetic materials)就是其中高活性和高能量含能材料之一。复合含能材料是一种由al、ti、mg等燃料和cuo、fe2o3、moo3等含氧化合物组成的含能材料,在一定触发条件下可发生快速化学反应,并释放出大量热量,具有热值高、点火引发能量低、能量释放速率快等众多优点,可以通过调节组分、当量比或粒径来控制和改变复合含能材料的燃烧性能,常常用于燃烧剂、点火药、高能炸药和固体火箭推进剂的能量添加剂等,在军事等领域具有广阔的应用前景。
3.复合含能材料性能主要受燃料和氧化剂间传质和热传导距离的影响,目前,研究人员主要通过降低燃料及氧化物的粒径来调控反应物组分间的传质距离,但当燃料及氧化物粒径降低到一定程度时,颗粒间会出现团聚现象,且燃料表面容易被氧化形成氧化层,造成其反应活性降低,极大地影响复合含能材料的性能。同时,研究人员通过制造不同结构的复合含能材料来增加各个组分之间的接触面积来减少传热传质距离,进来提升并调节材料的性能。
4.al/cuo两相复合材料是典型的复合含能材料,然而材料自身理化特性和制备方法在一定程度上限制了其应用发展。s.yu.ananev等(ananev,s.yu,et al."shock-wave initiation of a thermite mixture of al+cuo."combustion,explosion,and shock waves 56.2(2020):220-230)通过机械混合法制备的al/cuo两相复合材料存在各组分混合均匀性差的缺陷;jiaxing song等(song,jiaxing,et al."a comparative study of thermal kinetics and combustion performance of al/cuo,al/fe2o
3 and al/mno
2 nanothermites."vacuum 176(2020):109339.)采用超声波分散法制备了al/cuo纳米铝热剂,但其易存在部分团聚,分散性较差的缺陷;haiyang wang等(wang,haiyang,et al."assembly and reactive properties of al/cuo based nanothermite microparticles."combustion and flame 161.8(2014):2203-2208.)过静电喷雾制备了al/cuo核壳结构复合材料,但因为引入了与原料无关的惰性物质作为粘结剂,导致体系整体反应活性及能量密度降低,且静电喷雾法制备的al/cuo产量较低,无法实现大规模生产。
5.现有技术中有少量钛含能复合材料的报道,但是通常为简单的物理混合,各个组分间分布不均匀,存在团聚现象;或者在制备复合含能材料过程中需要向其中加入硝化纤维度(nc)等惰性组分作为粘结剂,从而影响复合体系的性能;此外,有少量报道ti/cuo复合材料为薄膜结构,各组分之间传质距离和扩散距离大,影响反应活性和放热性能。
6.目前,现有技术中尚未见到al/ti/cuo三元含能复合材料的报道;向两相复合含能
材料中添加第三相燃料组成的三相体系复合含能材料不一定会引起整个体系能量的提升,因为al/cuo体系的热值主要来源于金属铝燃烧的热值,al的热值远远大于ti的热值,需要对两相复合材料中加入第三相物质的比例进行严格计算,才能实现al和ti共同作为燃料的性能高于单相al作为燃料的性能。
技术实现要素:7.为了克服现有技术中存在的缺陷,本发明的目的之一在于提供一种杨梅状核壳结构al/ti/cuo微纳复合含能材料;所述复合含能材料引入了密度和活性更高的ti金属组成al/ti/cuo三元复合体系,具有表面粗糙、内部结构精细的杨梅状核壳结构,不易团聚,反应活性和能量密度高。
8.本发明的目的之二在于提供一种杨梅状核壳结构al/ti/cuo微纳复合含能材料的制备方法;所述方法混合均匀性好,工艺简单,安全可靠,条件温和,适用性强、制备过程易控制、可实现大规模制备生产。
9.为实现本发明的目的,提供以下技术方案。
10.一种杨梅状核壳结构al/ti/cuo微纳复合含能材料,所述材料由燃料和氧化剂组成,所述燃料为金属al和ti,所述氧化剂为cuo;
11.所述al为粒径为1~5μm的颗粒,ti为粒径为100~1000nm的颗粒,cuo为粒径为20~100nm的颗粒;所述杨梅状核壳结构为al颗粒为核,以ti颗粒和cuo颗粒均匀吸附、包裹和镶嵌在al颗粒的表面或次表面作为壳,形成具有完全壳包覆核的复合粒子,复合粒子表面存在颗粒状凸起,形成杨梅状核壳结构。
12.所述微纳复合含能材料的燃氧当量比取值为0.5~4.0;优选的,取值为1~3.5;
13.优选的,所述杨梅状核壳结构为球形或类球形,所述al粒径为1~3μm,ti粒径为200~500nm,cuo粒径为20~40nm;
14.优选的,以所述燃料总体质量为100%计,al的质量分数为10~90%,ti的质量分数为10~90%;进一步优选的,所述al的质量分数为70%,ti的质量分数为30%。
15.一种本发明所述杨梅状核壳结构al/ti/cuo微纳复合含能材料的制备方法,所述方法步骤如下:
16.(1)确定燃氧当量比值和燃料中各组分的质量分数,结合质量守恒定律,能够确定al/ti/cuo三元微纳复合含能材料质量比例,按照所述质量比例称量并加入各组分燃料和氧化剂,再加入溶剂,初步机械分散均匀得到混合分散液;
17.具体的,燃氧当量比为燃氧比实际值(φ
实际值
)和燃氧比化学计量值(φ
化学计量值
)的比值,即:
18.其中,燃氧比实际值(φ
实际值
)为实际加入的燃料总质量与实际加入的氧化剂的质量比值;
19.燃氧比化学计量值(φ
化学计量值
)为燃料中各组分燃氧比化学计量值的加权和,即:φ
化学计量值
=∑kiφ
i,化学计量值
;
20.其中,i为燃料中的某一组分;权重ki为所述组分i在燃料中的质量百分数;φ
i,
为
燃料中某一组分燃氧比化学计量值,为所述组分和氧化剂按照化学计量系数完全反应消耗的质量比;
21.燃料中组分al与氧化铜按照化学方程式(1)反应:
22.2al+3cuo
→
al2o3+cu(1);φ
al,化学计量值
=0.226;
23.燃料中组分ti与氧化铜按照化学方程式(2)反应:
24.ti+2cuo
→
tio2+2cu(2);φ
ti,化学计量值
=0.301;
25.确定燃氧当量比值和所述燃料中al和ti的质量分数后,根据φ
化学计量值
=∑kiφ
i,化学计量值,
可以计算得出φ
化学计量值
;根据可以计算得出φ
实际值
,即实际加入燃料总质量与实际加入氧化剂质量比,而根据质量守恒定律,实际加入燃料质量分数与实际加入氧化剂的质量分数加和为1,可以计算得出,实际加入氧化剂的质量分数和实际加入燃料质量分数,再结合已知的燃料中al和ti的质量分数,从而能够确定所述复合含能材料中实际加入al、ti和cuo的质量比例;所述溶剂为正己烷、环己烷、正庚烷、苯、甲苯或二甲苯,所述溶剂还具有冷却剂和过程控制剂的作用;
26.所述溶剂体积(ml)与燃料和氧化剂质量之和(g)之比为(0.3~1.0):1;
27.优选的,所述机械分散为磁力搅拌10min后再超声分散5min;
28.(2)采用高能球磨法,将步骤(1)得到的混合分散液倒入球磨罐中,再加入直径分别为5、8、10、12和15mm的磨球作为球磨介质,5种磨球质量配比为1:11:25:50:100,磨球与由al、ti和cuo组成的原料的质量比为(10~30):1,磨罐充入保护性气体密封,放入行星式球磨机;
29.所述保护性气体为惰性气体或氮气,纯度为99.999%以上;
30.(3)设置行星式球磨机的参数,转速为150~500r/min,球磨时间为1~4h;每球磨30min后暂停10min,下次球磨机自启动时,互换球磨旋转方向;旋转方向为顺时针方向或逆时针方向;
31.优选的,转速为180~300r/min,球磨时间为1~3h;
32.(4)球磨结束后,继续冷却10min,取出球磨罐,将所得复合金属粉真空干燥至溶剂完全挥发,挑出磨球,得到一种杨梅状核壳结构的al/ti/cuo微纳复合含能材料。
33.优选的,所述真空干燥温度为50~70℃,真空干燥时间为3~6h。
34.有益效果
35.(1)本发明提供了一种杨梅状核壳结构al/ti/cuo微纳复合含能材料,所述复合含能材料体系中引入了密度和活性更高的ti金属组成al/ti/cuo三元复合体系,并通过确定所述复合含能材料中燃氧当量比为0.5~4.0限定了al/ti/cuo三元体系含能复合材料中各个组分的质量比例,进而确定所述比例范围内添加ti得到的三元含能复合材料的燃烧热性能显著优于al/cuo或ti/cuo二元体系含能复合材料的燃烧热性能;当值为3、所述燃料中al的质量分数为70%,ti的质量分数为30%时,al/ti/cuo微纳复合含能材料燃性能最佳,其燃烧热可达6161j/g,显著高于al/cuo或ti/cuo复合含能材料燃烧热值。
36.(2)本发明提供了一种杨梅状核壳结构al/ti/cuo微纳复合含能材料,所述复合材料结构新颖,粒径较小的纳米ti和纳米cuo粒子均匀地吸附、包覆甚至镶嵌在粒径较大的微米al粒子表面或次表层形成杨梅状核壳结构,al/ti/cuo微纳复合含能材料均匀包覆、单分散、没有团聚,各粒子之间接触更加紧密和充分,使其传质距离和扩散距离更短,因此反应
强度更大,燃烧速率也更高。
37.(3)本发明提供了一种杨梅状核壳结构al/ti/cuo微纳复合含能材料的制备方法,所述方法通过优化参数后的高能球磨法,实现了金属燃料al、ti与氧化剂cuo在分子水平上的组装,既不会引入新的杂质,也不会破坏al、ti及cuo粒子的原本结构,为各个组分粒子的均匀分布及充分接触提供了条件,从而能够降低反应热传导距离,提升传质效率,显著提升了所述复合含能材料的燃烧热,使复合材料放热更剧烈,放热效率更高,释能更加完全,添加至火炸药中,有助于火炸药实际能量水平和释能效率的提升。
38.(4)本发明提供了一种杨梅状核壳结构al/ti/cuo微纳复合含能材料的制备方法,所述方法工艺简单,安全可靠,条件温和,适用性强、制备过程易控制、可实现大规模制备生产,同时经济成本低、环保性强。
附图说明
39.图1为实施例1制备得到样品的扫描电子显微镜(sem)图;
40.图2为实施例1制备得到样品的透射电子显微镜(tem)图;
41.图3为实施例1制备得到样品的扫描电子显微镜能谱元素分布图(sem-edsmapping);其中,图(f)为所述样品的sem图片,图(i)~(j)分别对应al、ti、cu和o氧元素;
42.图4为实施例1制备得到样品(al/ti/cuo)及原料al、ti和cuo的x射线衍射图谱(xrd);
43.图5为实施例1制备得到样品(al/ti/cuo)的以及o1s、al2p、ti2p和cu2p的x射线光电子能谱图(xps);
44.图6为实施例1制备得到样品、对比例1制备得到的样品(al/cuo)和对比例2制备得到的样品(ti/cuo)在空气气氛下的热失重曲线(dsc);
45.图7为实施例1制备得到样品(al/ti/cuo)和对比例1制备得到的样品(al/cuo)的燃烧状态高速摄像图;
46.图8为对比例6制备得到样品的透射电子显微镜(tem)图。
具体实施方式
47.下面结合附图和具体实施例来详述本发明,但不作为对本发明专利的限定。
48.金属铝(al),粒径尺寸为1~5μm,纯度为99.5%,购买于上海阿拉丁生化科技股份有限公司。
49.金属钛(ti),粒径尺寸为100nm~1000nm,纯度为99.5%,购买于上海麦克林生化科技有限公司。
50.氧化铜(cuo),粒径尺寸为40nm,纯度为99.5%,购买于上海易恩化学技术有限公司
51.正己烷(gc),纯度为99.5%,分析纯,购买于上海阿拉丁生化科技股份有限公司。
52.jx-4g型行星式球磨机,型号:jx-4gl,上海净信实业发展有限公司。
53.燃烧热测试仪器:氧弹仪,型号:trhw-7000c,鹤壁市天润电子科技有限公司。测试条件为:空气常压,样品质量200
±
10mg,量热弹内超纯水体积为10
±
0.5ml。
54.高速摄像图仪器:千眼狼高速摄像机,型号:x213,合肥富煌君达高科信息技术有限公司。测试条件:开放体系,空气常压,样品质量50
±
5mg,样品状态为散粉,点火方式为co2激光点火。
55.实施例1
56.一种杨梅状核壳结构al/ti/cuo微纳复合含能材料的制备方法,所述方法步骤如下:
57.(1)确定燃氧当量比值为3,以所述燃料总体质量为100%计,al的质量分数为70%,ti的质量分数为30%;根据φ
化学计量值
=∑kiφ
i,化学计量值,
可以计算得出φ
化学计量值
=0.226
×
0.7+0.301
×
0.3=0.2485;根据可以计算得出φ
实际值
=0.7455,即实际加入燃料总质量与实际加入氧化剂质量比为0.7455,而根据质量守恒定律,实际加入燃料质量分数与实际加入氧化剂的质量分数加和为1,可以计算得出,实际加入氧化剂的质量分数为57.3%,实际加入燃料质量分数为42.7%,而燃料中al的质量分数为70%,ti的质量分数为30%,从而确定所述复合含能材料中实际加入al、ti和cuo的质量分数分别为29.89%、12.81%和57.30%,即确定所述复合含能材料各组分质量比例为29.89:12.81:57.30;
58.按所述质量比例分别称取2.989g al粉、1.281g ti粉和5.730g cuo粉末放入烧杯中,加入8ml的正己烷,所述正己烷体积(ml)与燃料和氧化剂质量之和(g)比为0.8:1,将烧杯用密封膜密封后,磁力搅拌10min,超声分散5min,得到混合分散液;
59.(2)采用高能球磨法,将步骤(1)得到的混合分散液倒入干净的玛瑙球磨罐中,再加入直径分别为5、8、10、12和15mm的玛瑙球作为球磨介质,5种磨球质量配比为1:11:25:50:100,磨球与由al粉、ti粉和cuo粉组成的原料的质量比为20:1,磨罐充入纯度为99.999%的ar后密封,放入行星式球磨机;
60.(3)设置行星式球磨机的参数,转速为200r/min,球磨时间为2h,开始球磨;每球磨30min后暂停10min,下次球磨机自启动时,互换球磨旋转方向;旋转方向为顺时针旋转或逆时针旋转;
61.(4)球磨结束后,继续冷却10min,打开球磨机盖,取出球磨罐,将球磨所得的复合金属粉迅速倒入石英培养皿,将培养皿放入60℃真空干燥箱中进行干燥处理4h,待正己烷挥发,挑出玛瑙球,得到粉末状样品。
62.实施例2
63.一种杨梅状核壳结构al/ti/cuo微纳复合含能材料的制备方法,所述方法步骤如下:
64.(1)确定燃氧当量比值为2,以所述燃料总体质量为100%计,al的质量分数为70%,ti的质量分数为30%;根据φ
化学计量值
=∑kiφ
i,化学计量值,
可以计算得出φ
化学计量值
=0.226
×
0.7+0.301
×
0.3=0.2485;
65.根据可以计算得出φ
实际值
=0.497,即实际加入燃料总质量与实际加入氧化剂质量比为0.497,而根据质量守恒定律,实际加入燃料质量分数与实际加入氧化剂的质量分数加和为1,可以计算得出,实际加入氧化剂的质量分数为66.8%,实际加入燃料质量分数为33.2%,而燃料中al的质量分数为70%,ti的质量分数为30%,从而确定
所述复合含能材料中实际加入al、ti和cuo的质量分数分别为23.24%、9.96%和66.8%,即确定所述复合含能材料各组分质量比例为23.24:9.96:66.8;
66.按所述质量比例分别称取4.648g al粉、1.992g ti粉和13.36g cuo粉末放入烧杯中,加入20ml的正己烷,所述正己烷体积(ml)与燃料和氧化剂质量之和(g)比为1:1,将烧杯用密封膜密封后,磁力搅拌10min,超声分散5min,得到混合分散液;
67.(2)采用高能球磨法,将步骤(1)得到的混合分散液倒入干净的玛瑙球磨罐中,再加入直径分别为5、8、10、12和15mm的玛瑙球作为球磨介质,5种磨球质量配比为1:11:25:50:100,磨球与由al粉、ti粉和cuo粉组成的原料的质量比为30:1,磨罐充入纯度为99.999%的ar后密封,放入行星式球磨机;
68.(3)设置行星式球磨机的参数,转速为300r/min,球磨时间为3h,开始球磨;每球磨30min后暂停10min,下次球磨机自启动时,互换球磨旋转方向;旋转方向为顺时针旋转或逆时针旋转;
69.(4)球磨结束后,继续冷却10min,打开球磨机盖,取出球磨罐,将球磨所得的复合金属粉迅速倒入石英培养皿,将培养皿放入70℃真空干燥箱中进行干燥处理6h,待正己烷挥发,挑出玛瑙球,得到粉末状样品。
70.实施例3
71.一种杨梅状核壳结构al/ti/cuo微纳复合含能材料的制备方法,所述方法步骤如下:
72.(1)确定燃氧当量比值为3.5,以所述燃料总体质量为100%计,al的质量分数为70%,ti的质量分数为30%;根据φ
化学计量值
=∑kiφ
i,化学计量值,
可以计算得出φ
化学计量值
=0.226
×
0.7+0.301
×
0.3=0.2485;
73.可以计算得出φ
实际值
=0.8698,即实际加入燃料总质量与实际加入氧化剂质量比为0.8698,而根据质量守恒定律,实际加入燃料质量分数与实际加入氧化剂的质量分数加和为1,可以计算得出,实际加入氧化剂的质量分数为53.5%,实际加入燃料质量分数为46.5%,而燃料中al的质量分数为32.55%,ti的质量分数为13.95%,从而确定所述复合含能材料中实际加入al、ti和cuo的质量分数分别为32.55%、13.95%和53.5%,即确定所述复合含能材料各组分质量比例32.55:13.95:53.5;
74.按所述质量比例分别称取1.628g al粉、0.697g ti粉和2.675g cuo粉末放入烧杯中,加入2.5ml的正己烷,所述正己烷体积(ml)与燃料和氧化剂质量之和(g)比为0.5:1,将烧杯用密封膜密封后,磁力搅拌10min,超声分散5min,得到混合分散液;
75.(2)采用高能球磨法,将步骤(1)得到的混合分散液倒入干净的玛瑙球磨罐中,再加入直径分别为5、8、10、12和15mm的玛瑙球作为球磨介质,5种磨球质量配比为1:11:25:50:100,磨球与由al粉、ti粉和cuo粉组成的原料的质量比为10:1,磨罐充入纯度为99.999%的ar后密封,放入行星式球磨机;
76.(3)设置行星式球磨机的参数,转速为180r/min,球磨时间为1h,开始球磨;每球磨30min后暂停10min,下次球磨机自启动时,互换球磨旋转方向;旋转方向为顺时针旋转或逆时针旋转;
77.(4)球磨结束后,继续冷却10min,打开球磨机盖,取出球磨罐,将复合金属粉迅速倒入石英培养皿,将培养皿放入65℃真空干燥箱中进行干燥处理3h,待正己烷挥发,挑出玛
瑙球,得到粉末状样品。
78.实施例4
79.一种杨梅状核壳结构al/ti/cuo微纳复合含能材料的制备方法,所述方法步骤如下:
80.(1)确定燃氧当量比值为1,以所述燃料总体质量为100%计,al的质量分数为70%,ti的质量分数为30%;根据φ
化学计量值
=∑kiφ
i,化学计量值,
可以计算得出φ
化学计量值
=0.226
×
0.7+0.301
×
0.3=0.2485;
81.可以计算得出φ
实际值
=0.2485,即实际加入燃料总质量与实际加入氧化剂质量比为0.2485,而根据质量守恒定律,实际加入燃料质量分数与实际加入氧化剂的质量分数加和为1,可以计算得出,实际加入氧化剂的质量分数为80.1%,实际加入燃料质量分数为19.9%,而燃料中al的质量分数为13.93%,ti的质量分数为5.97%,从而确定所述复合含能材料中实际加入al、ti和cuo的质量分数分别为13.93%、5.97%和80.1%,即确定所述复合含能材料各组分质量比例为13.93:5.97:80.1;
82.按所述质量比例分别称取6.965g al粉、2.985g ti粉和40.05g cuo粉末放入烧杯中,加入35ml的正己烷,所述正己烷体积(ml)与燃料和氧化剂质量之和(g)比为0.7:1,将烧杯用密封膜密封后,磁力搅拌10min,超声分散5min,得到混合分散液;
83.(2)采用高能球磨法,将步骤(1)得到的混合分散液倒入干净的玛瑙球磨罐中,再加入直径分别为5、8、10、12和15mm的玛瑙球作为球磨介质,5种磨球质量配比为1:11:25:50:100,磨球与由al粉、ti粉和cuo粉组成的原料的质量比为25:1,磨罐充入纯度为99.999%的ar后密封,放入行星式球磨机;
84.(3)设置行星式球磨机的参数,转速为290r/min,球磨时间为2.5h,开始球磨;每球磨30min后暂停10min,下次球磨机自启动时,互换球磨旋转方向;旋转方向为顺时针旋转或逆时针旋转;
85.(4)球磨结束后,继续冷却10min,打开球磨机盖,取出球磨罐,将复合金属粉迅速倒入石英培养皿,将培养皿放入70℃真空干燥箱中进行干燥处理6h,待正己烷挥发,挑出玛瑙球,得到粉末状样品。
86.对比例1
87.对比例1仅在实施例1的基础上,未添加金属钛,制备得到al/cuo复合材料。
88.对比例2
89.对比例2仅在实施例1的基础上,未添加金属铝,制备得到ti/cuo复合材料。
90.对比例3
91.对比例3仅在实施例2的基础上,未添加金属钛,制备得到al/cuo复合材料。
92.对比例4
93.对比例4仅在实施例3的基础上,未添加金属钛,制备得到al/cuo复合材料。
94.对比例5
95.对比例5仅在实施例4的基础上,未添加金属钛,制备得到al/cuo复合材料。
96.对比例6
97.对比例6仅在实施例1的基础上,将步骤(2)中的“高能球磨法”替换为“简单的物理混合”,即“分别称取2.989g al粉、1.281g ti粉和5.730g cuo粉末放入烧杯中,用药匙搅拌
10min后再摇晃烧杯3min”,制备得到al/ti/cuo复合材料。
98.对实施例1和对比例6制备得到的样品的形貌进行表征,可以看出,对比例6简单的物理混合法制备得到al/ti/cuo复合材料样品如图8所示,样品中各个颗粒之间分布的均匀性较差,存在较为明显的自我团聚现象,同时微米al粒子表面光滑;而实施例1采用高能球磨法制备得到的al/ti/cuo微纳复合含能材料样品如图1~2所示,样品总体呈球状,粒径较小的纳米粒子均匀吸附、包裹甚至镶嵌在粒径较大的微粒表面或次表面,形成核壳结构;复合粒子表面略显粗糙且有小颗粒状凸起,类似“杨梅状”,颗粒呈单分散状态,未发生团聚现象。
99.实施例2~4制备得到的样品的形貌表征结果与实施例1相似。
100.对实施例1制备得到的样品元素种类和结构进行分析,结果如图3~5所示,从图3可知,o、ti、cu各个元素在al核表面分布均匀,说明ti和cuo均匀吸附、包覆、甚至镶嵌在微米al粒子表面或次表面,形成“杨梅状”核壳结构;从图4可以看出,对照原料al、ti和cuo的jcpds卡片,实施例1制备得到的样品的xrd曲线特征峰为al、ti、cuo特征峰的叠加,并未出现新的其他衍射峰特征,说明实施例1制备得到的样品为al/ti/cuo微纳复合含能材料为三相体系,即铝粉相、钛粉相以及氧化铜颗粒相,al与cuo、ti为纯物理的“包覆”或“嵌入”作用,整个高能球磨过程各个组分之间并未发生化学反应或合金化作用,整个体系在球磨处理过程中并无能量的提前损失。从图5可知,实施例1制备得到的样品含有al、ti、cu和o四种元素。实施例2~4制备得到的样品的元素和结构表征结果与实施例1相似。
101.综上所述,实施例1~4制备得到的样品为一种杨梅状核壳结构al/ti/cuo微纳复合含能材料。
102.图6从下到上依次为实施例1制备得到的样品(al/ti/cuo)、对比例2制备得到的样品(ti/cuo)和对比例1制备得到的样品(al/cuo)在空气气氛下的热失重曲线。由图6可知,相比于al/cuo二元体系,随着ti的加入,al/ti/cuo三元体系的两个放热峰的起始反应温度和峰值温度均发生提前,热量释放也有了很大改善,两个阶段的峰值温度分别提前3.2℃和47℃,且第二个放热反应的持续时间更久。可见,ti的加入增强了al/cuo体系的放热反应,使al/ti/cuo反应活性及产热增加提升,这对于其应用具有积极意义。实施例2~4制备得到的样品的热重表征结果与实施例1相类似。
103.对实施例1~4和对比例1~5制备得到的样品燃烧热进行测试,结果如表1所示,当值相同的条件下,实施例1制备得到的样品样品(al/ti/cuo)燃烧热值显著高于对比例1(al/cuo)和对比例2(ti/cuo)制备得到复合含能材料的燃烧热值,说明所述al/ti/cuo三相复合含能材料的燃烧热性能显著高于只含钛或铝的二元复合含能材料的燃烧热性能;实施例1~3制备得到的样品(al/ti/cuo)燃烧热较对比例1、4和5相比,有显著提高,说明添加金属钛能够显著提高复合含能材料的燃烧热;燃氧当量比值反应了复合含能材料中,燃料和氧化剂的质量比,当值低于3时,随着值增大,所述复合含能材料中燃料比重增加,氧化剂比重减少,复合含能材料的燃烧热相应提升;当值大于3时,继续增加燃料比重,燃烧热不再继续增加。因此当值等于3时,所述复合含能材料燃烧热最大。根据实施例1和对比例6燃烧热测试结果可知,相对于简单的物理混合,高能球磨法制备得到的al/ti/cuo复合材料中各个组分颗粒之间分布的均匀性好,复合颗粒呈单分散状态,无团聚现象,样品的燃烧热性能更佳。
104.表1实施例1~4和对比例1、对比例3~5制备得到的样品燃烧热值
[0105][0106][0107]
实施例1制备得到样品(al/ti/cuo)及对比例1制备得到的样品(al/cuo)的燃烧状态高速摄像图如图7所示,相比于al/cuo,al/ti/cuo微纳复合含能材料在燃烧时产生的火球直径和光亮均更大,且达到最大火球面积的时间更短,粒子的点火延迟时间更短,说明相较于对比例1,实施例1制备al/ti/cuo微纳复合含能材料的燃烧反应更加迅速和剧烈,反应更加充分;实施例2~4制备得到的样品的燃烧状态高速摄像图与实施例1类似。这主要是因为本发明制备得到的杨梅状核壳结构al/ti/cuo微纳复合含能材料各粒子之间接触更加紧密和充分,使其传质距离和扩散距离更短,因此反应强度更大,燃烧速率也更高。由此可见,本发明中的高能球磨法对于提升复合粒子的反应活性具有积极作用。
[0108]
以上所述实施例仅表达了本发明的实施方式,但并不能因此而理解为对本发明专利的范围的限制,应当指出,对于本领域的技术人员来说,在不脱离本发明构思的前提下,还可以做出若干变形和改进,这些均属于本发明的保护范围。