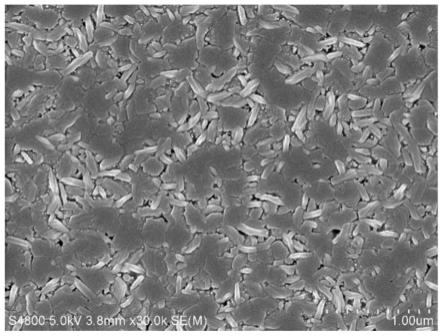
的1.2ev低了85%。从而使得这种基于高价离子取代掺杂钡铁氧体陶瓷体系的介电调制电压仅为<25v/cm,同时在这种超低调制电场下的介电可调性则高达 65%,相关研究发表在j.appl.phys.130(2021),124101上,并已获得专利 zl201910093259.8,zl201910093226.3,zl201910093232.9。
4.很明显,高价离子取代掺杂的钡铁氧体介电可调材料显著降低了直流偏置电场,使得器件在应用时的能耗显著降低。但是,由于在这种材料体系中电子对偶极子实际是控制铁离子上的不同电价形成的,在交变电场作用下偶极子贡献的介电特性是基于不同电价离子上电子的迁移,在一定条件下易于在体系中产生漏电流并导致材料介电损耗有所增加。再则,取代掺杂的高价离子本身由于带入的缺陷电荷易产生漏电流现象;更进一步,由于钡铁氧体体系中相对钡离子易挥发损失而产生缺陷,也会产生显著的漏电流现象,实测中所述掺杂钡铁氧体的介电损耗达到~1左右,该值远高于多数常规的具有离子偶极子的铁电材料。可见,这种高价离子取代掺杂钡铁氧体虽然可以在很小的直流偏置下实现较高的可调性,但其较高的介电损耗仍然限制着这种材料的实际应用;再则,作为块体材料,在目前电子原器件的小型化和集成化大趋势下,在很多领域可能也无法得到很好的应用。因此,探索其它引入fe
2+
/fe
3+
电子偶极子对的方式以实现介电损耗的减小,以及制备具有同样介电性能及介电可调特性的薄膜材料将具有重要的研究意义。
5.仔细分析,在钡铁氧体中,基于铁离子是一种易变价离子,产生的电子对偶极子主要是通过在结构中引入正电荷,即引入高价离子掺杂fe
3+
离子,使体系内为使电荷达到平衡而产生fe
2+
离子。这种fe
2+
离子已被证明可与附近的fe
3+
离子形成电子偶极子对。实际上引入正电荷的方式可以通过上述高价离子取代铁离子掺杂,理论上也可以通过掺入间隙阳离子实现。考虑到在钡铁氧体中存在较大的八面体和三角双锥间隙位,因此可能在不引入其它高价离子作为掺杂离子进行取代,而采用间隙钡离子掺杂的方式在钡铁氧体中引入正电荷缺陷,同样可诱导临近fe
3+
离子转变为fe
2+
离子,进而构造fe
2+
/fe
3+
电子偶极子对。并且,这种掺杂由于过量的钡离子存在,也可能大幅度降低钡离子穴位缺陷的形成,有望降低体系漏电流进而达到降低损耗的目的。
6.实际上,经过实验证明,基于薄膜材料,在间隙钡离子掺杂的钡铁氧体薄膜体系中,鉴于钡空位缺陷的大幅减少以及诱导产生二价铁离子的机制由上述的高价离子取代掺杂改变为钡间隙掺杂,虽然使得其介电损耗得到大幅下降,可以由块体材料中的~1下降至最低的~0.01,最大下降近两个数量级,但是,由于掺杂机制的改变,由掺杂离子控制形成的二价铁离子与附近三价铁离子形成的偶极子对之间的电子迁移能量也同时发生了改变,在此会略有提高。依此,驱动偶极子随外场产生偏转所需的能量,也即介电调制电场,也会产生相应的提高,达到 200~400v/cm,比高价离子取代掺杂的体系要略高。但是,这个驱动电场实际上仍然远低于通常的铁电型介电可调材料的10~100kv/cm,还彻底解决了高损耗无法更好地推广应用的问题。
7.然而,考虑到既然钡离子过量的间隙掺杂可以更好解决损耗问题,高价离子取代掺杂体系则调制电压可以更低,那么是否可能形成一种复合体系,特别是形成一种由两种掺杂相分布并相互隔离的介电可调相,也即由一种漏电流很小的如钡间隙掺杂相将漏电流相对较大的如高价离子取代掺杂相进行隔离,这种利用高阻相来进行的隔离有望既使复合薄膜在外场下的漏电流损耗大幅下降,同时又由于具有低调制电场特性的高价离子取代掺
杂相的存在而有助于降低薄膜整体的调制电场,从而达到适当降低调制电场,又同样解决了损耗较高问题的目的。
8.协同掺杂可能是一种有意义的解决手段。在钡离子过化学计量比配方并保证形成钡间隙掺杂铁氧体微结构的体系中,如果同时考虑存在一种高含量的高价取代离子,则这种过量高价离子有望争夺相应的铁离子而独立形成由高价取代离子控制的不同于钡间隙掺杂铁氧体相微结构的高价离子取代掺杂钡铁氧体相,这是由于已经知道的高价离子取代掺杂同样会通过内部电价平衡原则形成相应的偶极子,这种相的形成应该会同时抑制间隙位钡的产生,基于体系中考虑既有高含量钡离子,又有高含量的高价离子,两者极有可能各自争夺形成相应的掺杂钡铁氧体相,结合这种协同掺杂的工艺过程,进而促使这两种微结构相既独立形成又均匀分布于体系中,从而达到相互隔离形成两种微结构相的目的。
9.本发明利用溶胶凝胶工艺结合多层旋转涂布方法在单晶硅基板上制备钡铁氧体薄膜;本发明通过设计特定的制备工艺,通过超量本征钡离子间隙掺杂和高价离子(如锆离子)取代掺杂的协同,成功形成了一种由蠕虫状和团聚颗粒状晶粒组成的复合微结构的钡铁氧体薄膜,维持了fe
2+
/fe
3+
电子对偶极子及偶极子对在一定外电场下稳定存在及对外电场的响应,提高了性能并实现了在极低调制电压下产生高介电可调特性的目标。本发明可解决钡铁氧体介电可调陶瓷材料的高介电损耗问题和保持极低调制电压的问题,推动其在新型介电可调器件以及集成化小型化领域的更广泛应用。
技术实现要素:10.本发明的目的在于针对现有的介电可调材料调制电场高,以及目前低电场介电可调钡铁氧体基于块体材料不适于在小型化集成化器件领域推广应用及目前高价离子取代掺杂钡铁氧体材料本身介电损耗高的缺点,提供一种具有复合微结构的介电可调协同掺杂钡铁氧体薄膜及其制备方法,该薄膜既具有低的调制电压,又具有高介电调谐率、低介电损耗和高调制优值,该薄膜材料具有蠕虫状和团聚颗粒状晶相复合微结构特征,且两种不同形态颗粒间相互隔离并均匀分布在体系中,既在一定程度上利用了高价离子掺杂具极低调制电场的特点,又解决了高价离子掺杂损耗高的问题。
11.本发明的蠕虫状和团聚颗粒状晶相复合微结构的介电可调钡铁氧体薄膜,所述薄膜为由间隙型钡离子和取代型高价离子协同掺杂的钡铁氧体薄膜,是利用溶胶凝胶方法,并采用钡离子并高价离子过量的协同掺杂和多层制备手段制备制得,其前驱体溶液中钡和铁的摩尔比例为x:12,其中x=2~3;前驱体溶液中高价离子和铁的摩尔比例为y:12,其中y=1~4。所述的钡铁氧体薄膜,ba
2+
占据bafe
12o19
晶胞中的八面体和三角双锥间隙位点,高价离子则取代fe
3+
的4f1位置,且基于掺杂离子引入的正电荷,近邻fe
3+
转变为fe
2+
,使得钡铁氧体中两种不同形态晶相中都同时存在fe
3+
和fe
2+
,并成功形成fe
2+
/fe
3+
电子对偶极子。所述的高价取代离子可以是锆离子,也可以是如钛离子ti、铌离子nb等相关的能在钡铁氧体中成功进行取代掺杂的其它高价离子,或高、低价复合取代掺杂离子体系,如铌
ꢀ‑
镍复合掺杂离子等体系。其基本条件是能在铁氧体中形成稳定偶极子对。本发明中,考虑到高温热处理时ba离子易于挥发,设计掺入超量的钡离子,且这些超量钡离子需足够进行间隙掺杂,形成钡间隙掺杂的钡铁氧体晶格结构和形成 fe
2+
/fe
3+
电子对偶极子;考虑到锆掺杂相要能够以独立的晶相形态存在,同样必需设计较大过量的掺杂,以确保有足够的锆离子以生
成锆取代掺杂为主的晶相形态,形成锆取代掺杂的钡铁氧体晶格结构和形成fe
2+
/fe
3+
电子对偶极子。
12.本发明的具有复合微结构的介电可调协同掺杂钡铁氧体薄膜材料的制备方法,具体包括如下步骤:
13.(1)在乙二醇中溶解硝酸钡,在50℃水浴加热条件下搅拌直至溶剂完全溶解,得到浓度为0.16mol/l的硝酸钡溶液a;称取硝酸铁和硝酸氧锆并分别溶解在乙二醇和乙二醇甲醚中,在50℃水浴加热条件下搅拌直至溶剂完全溶解,得到0.88mol/l浓度的硝酸铁溶液b和0.24mol/l浓度的硝酸氧锆溶液c;
14.(2)对每100ml溶液a 100ml,取溶液b100~75ml,和将溶液c30~100ml 先加乙二醇甲醚70~0ml定容到100ml后,再将这三种溶液进行混合,然后加入117.7g柠檬酸,并继续用乙二醇定容为400ml,最后水浴加热搅拌6h,得到需要的前驱体溶胶d,其中ba:fe摩尔比为(2~3):12和zr:fe摩尔比为(1~ 4):12;
15.(3)清洗硅片:以硅片为基板清洗吹干备用,如:将厚度为525
±
25μm的单面抛光n型si(100)基板割成2cm
×
2cm的正方形片,然后在稀释的氢氟酸溶液中超声清洗5min去除表面氧化层,再用肥皂水,去离子水,丙酮,异丙醇,依次分别超声清洗10min,清洗完毕后,用氮气枪吹干备用;
16.(4)将前驱体溶胶d,滴在吹干后的硅片表面,在匀胶机上,控制转速2000 rpm旋涂1min,以匹配组成设计并达到所需厚度要求,随后在150℃固化10min;
17.(5)将固化后的薄膜放置于低温马弗炉中400~450℃热解10~15min,去除其中的有机物;
18.(6)重复上述步骤(4)和(5),获得所需厚度的多层前驱体薄膜,然后在高温马弗炉中烧结,具体多层膜的烧结条件控制如下:
19.从室温开始,以5℃/min的升温速度,升温到820-880℃,然后保温2.5h,之后随炉冷却到室温。获得在单晶硅基板上生长的具有蠕虫状晶粒和团聚状晶粒复合微结构的介电可调的协同掺杂钡铁氧体薄膜。
20.与现有技术相比,本发明具有的有益效果是:
21.本发明控制ba
2+
含量,可在薄膜钡铁氧体晶格结构中一些间隙位掺杂ba
2+
离子;控制过量的zr
4+
离子,在薄膜中取代fe
3+
离子掺杂,两种掺杂同时在晶相结构中形成大量相应的fe
2+
;两种掺杂形式以不同的蠕虫状和团聚颗粒状结晶形态独立存在并均匀分布在薄膜体系中,两种形态间被相互隔离,起到既降低zr
4+
离子掺杂相损耗较高的不足又利用zr
4+
离子掺杂相有更低调制电场的优势,以达到获得较低调制电场和较高性能的目的。通过其与fe
3+
离子耦合形成fe
2+
/fe
3+
缺陷偶极子对,两种晶相结构形态都表现出与传统离子偶极子相似的介电特性且这种偶极子能够在一定外加电场下稳定存在并在外电场下能够得到响应;介电调谐率保持在50~60%的条件下,实际调制驱动电场可达到较低的~60v/cm,远低于现有广泛应用的介电可调材料,也远低于单一钡过量间隙掺杂体系的200~ 400v/cm;同时,这种由间隙ba
2+
离子掺杂的低损耗相隔离由高价离子取代掺杂的高损耗相形成的复合微结构钡铁氧体薄膜,其最低介电损耗在0.05~0.1,远低于高价离子取代掺杂体系钡铁氧体块体材料的~1,与单一钡离子过量掺杂钡铁氧体薄膜几乎相当,其优值最高达到fom~12。本发明工艺过程简单,实验周期短,具有推广性,制备得到的钡铁氧体薄膜可在非常低
的调制电压下得到高的介电调谐性,并且可以与集成电路技术很好的结合,有望在新型低电压介电可调器件中得到广泛应用。
附图说明
22.图1为850℃下烧结、钡/铁比为x=2~3、锆/铁比为y=1~4和经4次涂覆的钡铁氧体薄膜xrd图;
23.图2为850℃下烧结,钡/铁比中x=2.182和锆/铁比中y=1.091经4次涂覆的钡铁氧体薄膜蠕虫状和团聚颗粒状复合微结构sem形貌图;
24.图3表示在为850℃下烧结,钡/铁比中x=2.182和锆/铁比中y=1.091经4 次涂覆的蠕虫状和团聚颗粒状复合微结构钡铁氧体薄膜的介电频谱;
25.图4表示在为850℃下烧结,钡/铁比中x=2.182和锆/铁比中y=1.091经4 次涂覆的蠕虫状和团聚颗粒状复合微结构钡铁氧体薄膜的介电损耗频谱;
26.图5表示在为850℃下烧结,钡/铁比中x=2.182和锆/铁比中y=1.091经4 次涂覆的蠕虫状和团聚颗粒状复合微结构钡铁氧体薄膜的介电常数偏压曲线;
27.图6为850℃下烧结,钡/铁比中x=2.4和锆/铁比中y=2.4经4次涂覆的钡铁氧体薄膜蠕虫状和团聚颗粒状复合微结构sem形貌图;
28.图7表示在为850℃下烧结,钡/铁比中x=2.4和锆/铁比中y=2.4经4次涂覆的蠕虫状和团聚颗粒状复合微结构钡铁氧体薄膜的介电频谱图;
29.图8表示在为850℃下烧结,钡/铁比中x=2.4和锆/铁比中y=2.4经4次涂覆的蠕虫状和团聚颗粒状复合微结构钡铁氧体薄膜的介电损耗频谱;
30.图9表示在为850℃下烧结,钡/铁比中x=2.4和锆/铁比中y=2.4经4次涂覆的蠕虫状和团聚颗粒状复合微结构钡铁氧体薄膜的介电常数偏压曲线;
31.图10为850℃下烧结,钡/铁比中x=2.667和锆/铁比中y=4经4次涂覆的钡铁氧体薄膜蠕虫状和团聚颗粒状复合微结构sem形貌图;
32.图11表示在为850℃下烧结,钡/铁比中x=2.667和锆/铁比中y=4经4次涂覆的蠕虫状和团聚颗粒状复合微结构钡铁氧体薄膜的介电频谱图;
33.图12表示在为850℃下烧结,钡/铁比中x=2.667和锆/铁比中y=4经4次涂覆的蠕虫状和团聚颗粒状复合微结构钡铁氧体薄膜的介电损耗频谱;
34.图13表示在为850℃下烧结,钡/铁比中x=2.667和锆/铁比中y=4经4次涂覆的蠕虫状和团聚颗粒状复合微结构钡铁氧体薄膜的介电常数偏压曲线;
具体实施方式
35.下面是对本发明技术方案进行的清楚、完整的描述。显然,所描述的实施例仅是本发明的一部分实施例,而不是全部的实施例。基于本发明的实施例,本领域普通技术人员在没有做出任何创造性劳动前提下通过简单改变烧结温度、时间和气氛,改变相应的高价掺杂离子等,以及基于相同机理简单改变组成等所获得的所有其他实施例,都属于本发明保护的范围。
36.本发明的薄膜为由间隙型钡离子和取代型锆离子协同掺杂的蠕虫状与团聚颗粒状复合微结构型、具有低调制电场的介电可调钡铁氧体薄膜。所述的钡铁氧体薄膜,通过单
晶硅基板与膜层中氧的作用,诱导在硅基板表面形成钡铁氧体的氧密排面,进而诱导晶型以(00l)取向生长的钡铁氧体薄膜;受不同掺杂离子的控制,薄膜以蠕虫结构和团聚颗粒状结构复合存在;通过ba
2+
的超化学计量配比,形成ba
2+
占据bafe
12o19
晶格中间隙位的间隙掺杂蠕虫微结构晶相,通过zr
4+
取代bafe
12o19
晶格中fe
3+
掺杂,形成团聚颗粒状晶相微结构;通过所述掺杂离子诱导周围近邻位置fe
3+
转化为fe
2+
,并在相关fe
2+
和fe
3+
之间形成稳定的缺陷偶极子对。所述薄膜,具有低调制电场介电可调性,介电调谐率为~60%,调制电压《60v/cm,优值~12。本发明采用溶胶凝胶结合旋转涂布制备方法,过程简单、可控性强、制备周期短、成本低廉,所得薄膜在超低调制电场下表现出高介电调谐率。这种钡铁氧体薄膜在介电可调器件以及集成电路领域有广泛的应用。下面根据具体的实施例详细地描述本发明。
37.实例1
38.(1)在100ml乙二醇中溶解4.18g硝酸钡,在50℃水浴加热条件下搅拌3h,直至溶剂完全溶解,得到浓度为0.16mol/l的硝酸钡溶液a;称取35.56g硝酸铁和5.55g硝酸氧锆并分别溶解在100ml乙二醇和100ml乙二醇甲醚中,在50℃水浴加热条件下搅拌3h,直至溶剂完全溶解,得到0.88mol/l浓度的硝酸铁溶液b和0.24mol/l浓度硝酸氧锆溶液c;
39.(2)将上述溶液a100ml,溶液b100ml和将溶液c 33.3ml先加乙二醇甲醚 66.7ml定容到100ml后,再将这三种溶液进行混合,然后加入117.7g柠檬酸,并继续用乙二醇定容为400ml,最后水浴加热搅拌6h,得到需要的前驱体溶胶 d,其中ba:fe摩尔比为2.182:12和zr:fe摩尔比为1.091:12;
40.(3)清洗硅片:将厚度为525
±
25μm的单面抛光n型si(100)基板割成 2cm
×
2cm的正方形片,然后在稀释的氢氟酸溶液中超声清洗5min去除表面氧化层,再用肥皂水,去离子水,丙酮,异丙醇,依次分别超声清洗10min,清洗完毕后,用氮气枪吹干备用;
41.(4)将前驱体溶胶d,滴在吹干后的硅片表面,在匀胶机上,控制转速2000 rpm旋涂1min,以匹配组成设计并达到所需厚度要求,随后在150℃固化10min;
42.(5)将固化后的薄膜放置于低温马弗炉中400~450℃热解10~15min,去除其中的有机物;
43.(6)重复上述步骤(4)和(5)4次,获得所需厚度的多层前驱体薄膜,然后在高温马弗炉中烧结,具体多层膜的烧结条件控制如下:
44.从室温开始,以10℃/min的升温速度,升温到850℃,然后保温2.5h,随后随炉冷却到室温。最终获得在单晶硅基板上生长的蠕虫状和团聚颗粒状复合微结构的协同掺杂且具极低调制电场的高介电可调钡铁氧体薄膜。
45.本实施例制得的复合微结构钡铁氧体薄膜,其xrd图如图1所示,可见,具有典型的钡铁氧体的(006),(008)和(0014)峰和伴随有(107)和(114)小峰出现,可见薄膜呈现一定的c轴取向。其介电性能和介电可调性能采用agilent 4294a精密阻抗分析仪测试。测试前将本发明实例的薄膜试样表面用酒精冲洗并用氮气枪吹干,再在试样上表面溅射金电极,采用面电极平行于膜面方向的电场进行测试。
46.图2是实施例1获得的钡/铁比x=2.182和锆/铁比y=1.091的钡铁氧体薄膜的微结构形貌sem图,从图可见其形成的晶相为蠕虫状和团聚颗粒状复合微结构特征。图3是实施例1获得的钡/铁比x=2.182和锆/铁比y=1.091的钡铁氧体薄膜的介电频谱,可以看到,4层膜的测试介电常数值在几十千到兆赫兹范围内,在4.5~5.5x107左右。图4是实施例1获
7.4。
57.实例3
58.(1)在100ml乙二醇中溶解4.18g硝酸钡,在50℃水浴加热条件下搅拌3h,直至溶剂完全溶解,得到浓度为0.16mol/l的硝酸钡溶液a;称取35.56g硝酸铁和5.55g硝酸氧锆并分别溶解在100ml乙二醇和100ml乙二醇甲醚中,在50℃水浴加热条件下搅拌3h,直至溶剂完全溶解,得到0.88mol/l浓度的硝酸铁溶液b和0.24mol/l浓度硝酸氧锆溶液c;
59.(2)分别将上述溶液a100ml,溶液b81.8ml和将溶液c100ml三种溶液进行混合,然后加入117.7g柠檬酸,并继续用乙二醇定容为400ml,最后水浴加热搅拌6h,得到需要的前驱体溶胶d,其中ba:fe摩尔比为2.667:12和zr:fe摩尔比为4:12;
60.(3)清洗硅片:将厚度为525
±
25μm的单面抛光n型si(100)基板割成 2cm
×
2cm的正方形片,然后在稀释的氢氟酸溶液中超声清洗5min去除表面氧化层,再用肥皂水,去离子水,丙酮,异丙醇依次分别超声清洗10min,清洗完毕后,用氮气枪吹干备用;
61.(4)将前驱体溶胶d,滴在吹干后的硅片表面,在匀胶机上,控制转速2000 rpm旋涂1min,以匹配组成设计并达到所需厚度要求,随后在150℃固化10min;
62.(5)将固化后的薄膜放置于低温马弗炉中400~450℃热解10~15min,去除其中的有机物;
63.(6)重复上述步骤(4)和(5)4次,获得所需厚度的多层前驱体薄膜,然后在高温马弗炉中烧结,具体多层膜的烧结条件控制如下:
64.从室温开始,以5℃/min的升温速度,升温到850℃,然后保温2.5h,随后随炉冷却到室温。获得在单晶硅基板上生长的蠕虫状晶粒和团聚颗粒状晶粒复合微结构的协同掺杂且具极低调制电场的高介电可调钡铁氧体薄膜。
65.本实施例制得的复合微结构钡铁氧体薄膜,其xrd图如图1所示,可见,具有典型的钡铁氧体的(006),(008)和(0014)峰和伴随有(107)和(114)小峰出现,可见薄膜呈现一定的c轴取向。其介电性能和介电可调性能采用agilent 4294a精密阻抗分析仪测试。测试前将本发明实例的薄膜试样表面用酒精冲洗并用氮气枪吹干,再在试样上表面溅射金电极,采用面电极平行于膜面方向的电场进行测试。
66.图10是实施例3获得的钡/铁比x=2.667和锆/铁比y=4的钡铁氧体薄膜的微结构形貌,从图可见其形成的晶相为蠕虫状和团聚颗粒状复合微结构特征。图 11是实施例3获得的钡/铁比x=2.667和锆/铁比y=4的复合微结构钡铁氧体薄膜的介电频谱,可见,测试介电常数在几十千到几兆赫兹范围内,保持在3.5~ 2.5x107。图12是实施例3获得的钡/铁比x=2.667和锆/铁比y=4的复合微结构钡铁氧体薄膜的介电损耗频谱,可以看到,薄膜的介电损耗在几百khz频率范围内保持在~0.1。图13是实施例3获得的钡/铁比x=2.667和锆/铁比y=4的复合微结构钡铁氧体薄膜在10khz下的测试介电常数-偏压曲线。可以看出,该实施例获得的样品表现出极低调制电场下的介电可调特性,在直流偏置电场~50 v/cm的作用下,可调性达到52%,其优值为5.2。