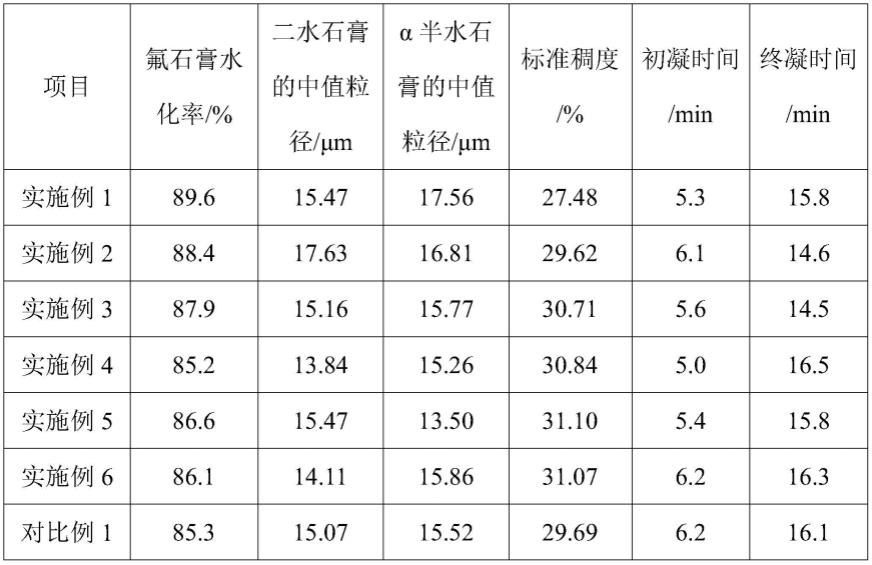
一种氟石膏制备
α
半水石膏的方法
技术领域
1.本发明属于建筑材料技术领域,具体涉及一种一种氟石膏制备α半水石膏的方法。
背景技术:2.氟石膏是生产氢氟酸过程中的副产品,刚出窑时氟石膏中含有残余的萤石与硫酸,浸出液中氟及硫酸的含量较高,属腐蚀性强的有害固体废弃物。企业一般是将其稍加中和处理后作为一般固体废弃物堆存,直接堆存不仅占用土地,还污染土壤和地下水环境,因此企业不得不征用大量土地并要对周围环境加以维护,氟石膏得不到充分的利用,大量堆置的氟石膏给企业生产带来负担的同时,也对周边环境造成了污染。
3.氟石膏属于硬石膏的一种,由于其难溶于水,水化活性极差,凝结硬化时间长,甚至在很长时间里不发生凝结硬化,不具有早期强度,但氟石膏具有潜在的胶凝性,经过改性后同其他石膏制品一样可作为工业生产民用建筑材料。氟石膏主要为无水硫酸钙,在不经处理的情况下,活性较低,很难水化;对氟石膏进行改性研究,将其转变为石膏建筑材料进行综合利用,不仅可以保护环境变废为宝,而且能节约资源。
4.cn102173620a公开了一种利用湿氟石膏改性生产建筑石膏粉的方法,具体步骤如下:湿氟石膏经自然风干或烘干去除部分游离水后,初步破碎至2mm以下,在湿氟石膏中加入一部分由硅铝酸盐、硫酸盐、含钙化合物混和组成的改性剂,在低温80-180℃焙烧1-3h,然后再与剩下的一部分改性剂进行充分混和、细磨,细磨后粉体粒径不大于0.147mm,即得符合《建筑石膏gb/t9776-2008》要求的改性建筑石膏粉材料。其中,湿氟石膏质量百分比为92-98%、改性剂总量为2-8%;前后两次加入的改性剂用量依次为改性剂总用量的65-85%和15-35%。该方法的技术特点是工艺流程短,改性剂分两步添加,焙烧温度低,成本低廉,产品质量稳定。但该方法对细磨粉体的粒径要求较高,且得到的建筑石膏粉的力学性能较差。
5.因此,需要提供一种绿色、环保的氟石膏资源化处理的方法,解决氟石膏堆积浪费的问题,而且能够获得粒度大,强度高的石膏,提高氟石膏的工业应用价值,减少污染。
技术实现要素:6.针对现有技术存在的不足,本发明的目的在于提供一种氟石膏制备α半水石膏的方法,氟石膏、煅烧明矾、钠盐、二水石膏晶种与第一溶剂进行水化反应得到二水石膏;二水石膏、α半水石膏晶种与第二溶剂混合后加入转晶剂进行激发转晶得到α半水石膏;本发明所述氟石膏制备α半水石膏的方法,缓解了氟石膏的环境污染问题,氟石膏在24小时内快速水化且水化率达到85%以上,氟石膏的水化时间大幅缩短;所得α半水石膏的粒度大,强度高,其符合jc/t2038-2010标准规定的α40级别;且初凝时间和终凝时间短。
7.为达此目的,本发明采用以下技术方案:
8.本发明的目的在于提供一种氟石膏制备α半水石膏的方法,所述方法包括如下步骤:
9.(1)将氟石膏、煅烧明矾、钠盐、二水石膏晶种与第一溶剂混合后进行水化反应,经第一次固液分离,得到二水石膏;
10.(2)将α半水石膏晶种、第二溶剂与步骤(1)所述二水石膏混合,得到混合浆料后,加入转晶剂在121-128℃进行激发转晶,经第二次固液分离,得到α半水石膏。
11.本发明所述氟石膏制备α半水石膏的方法,缓解了氟石膏的环境污染问题,氟石膏在24小时内快速水化且水化率达到85%以上,氟石膏的水化时间大幅缩短;所得α半水石膏的粒度大,强度高,其符合jc/t2038-2010标准规定的α40级别;且初凝时间和终凝时间短。
12.值得说明的是,激发转晶的温度为121-128℃,例如可以是121℃,121.5℃,122℃,122.5℃,123℃,123.5℃,124℃,124.5℃,125℃,125.5℃,126℃,126.5℃,127℃,127.5℃,128℃等,但并不仅限于所列举的数值,上述数值范围内其他未列举的数值同样适用。
13.作为本发明优选的技术方案,在步骤(1)所述混合之前,将所述氟石膏研磨至比表面积≥500m2·
kg,例如可以是500m2·
kg,550m2·
kg,600m2·
kg,630m2·
kg,670m2·
kg,700m2·
kg,740m2·
kg,780m2·
kg,800m2·
kg,850m2·
kg,900m2·
kg等,但并不仅限于所列举的数值,上述数值范围内其他未列举的数值同样适用。
14.优选地,步骤(1)所述煅烧明矾的制备过程包括:十二水合硫酸铝钾在600-670℃下煅烧1-2h,煅烧温度为600-670℃,例如可以是600℃,610℃,620℃,630℃,640℃,650℃,660℃,670℃等;煅烧时间为1-2h,例如可以是1h,1.1h,1.2h,1.3h,1.4h,1.5h,1.6h,1.7h,1.8h,1.9h,2h等,但并不仅限于所列举的数值,上述数值范围内其他未列举的数值同样适用。
15.但并不仅限于所列举的数值,上述数值范围内其他未列举的数值同样适用。
16.作为本发明优选的技术方案,步骤(1)所述钠盐包括硫酸钠、氯化钠或硝酸钠中的任意一种或至少两种的组合,所述组合典型但非限制性的实例包括硫酸钠和氯化钠的组合,硫酸钠和硝酸钠的组合,氯化钠和硝酸钠的组合;进一步优选为硫酸钠和氯化钠。
17.优选地,步骤(1)所述第一溶剂包括水。
18.作为本发明优选的技术方案,步骤(1)中,各原料组分按重量份计包括:氟石膏98-103份,例如可以是98份,99份,100份,101份,102份,103份等;煅烧明矾4-6份,例如可以是4份,4.5份,5份,5.5份,6份等;钠盐34-38份,例如可以是34份,34.5份,35份,35.5份,36份,36.5份,37份,37.5份,38份等;二水石膏晶种19-21份,例如可以是19份,19.5份,20份,20.5份,21份等,但并不仅限于所列举的数值,上述数值范围内其他未列举的数值同样适用。
19.值得说明的是,步骤(1)所述钠盐为硫酸钠和氯化钠,按重量份计,硫酸钠为5-7份,例如可以是5份,5.5份,6份,6.5份,7份等,氯化钠为29-31份,例如可以是29份,29.5份,30份,30.5份,31份等,但并不仅限于所列举的数值,上述数值范围内其他未列举的数值同样适用。
20.优选地,步骤(1)所述第一溶剂与所述氟石膏的质量比为(5-7):1,例如可以是5:1,5.2:1,5.5:1,5.7:1,6:1,6.3:1,6.5:1,6.8:1,7:1等,但并不仅限于所列举的数值,上述数值范围内其他未列举的数值同样适用。
21.作为本发明优选的技术方案,步骤(1)所述水化反应的温度为20-35℃,例如可以是20℃,22℃,24℃,26℃,28℃,30℃,32℃,34℃,35℃等,但并不仅限于所列举的数值,上述数值范围内其他未列举的数值同样适用。
22.优选地,步骤(1)所述水化反应的时间为20-24h,例如可以是20h,20.5h,21h,21.5h,22h,22.5h,23h,23.5h,24h等,但并不仅限于所列举的数值,上述数值范围内其他未列举的数值同样适用。
23.优选地,步骤(1)所述水化反应的搅拌速度为100-250r/min,例如可以是100r/min,120r/min,140r/min,160r/min,180r/min,200r/min,210r/min,230r/min,250r/min等,但并不仅限于所列举的数值,上述数值范围内其他未列举的数值同样适用。
24.优选地,步骤(1)所述第一次固液分离的方式为离心分离。
25.作为本发明优选的技术方案,步骤(2)所述α半水石膏晶种与所述二水石膏的质量比为(0.2-0.4):1,例如可以是0.2:1,0.22:1,0.25:1,0.27:1,0.3:1,0.33:1,0.35:1,0.38:1,0.4:1等,但并不仅限于所列举的数值,上述数值范围内其他未列举的数值同样适用。
26.优选地,步骤(2)所述第二溶剂包括水。
27.优选地,步骤(2)所述第二溶剂与所述二水石膏的质量比为(2-3):1,例如可以是2:1,2.1:1,2.2:1,2.3:1,2.4:1,2.5:1,2.6:1,2.7:1,2.8:1,2.9:1,3:1等,但并不仅限于所列举的数值,上述数值范围内其他未列举的数值同样适用。
28.作为本发明优选的技术方案,步骤(2)所述转晶剂包括丁二酸。
29.优选地,步骤(2)所述转晶剂的添加量占所述二水石膏的0.2-0.4wt%,例如可以是0.2wt%,0.22wt%,0.25wt%,0.27wt%,0.3wt%,0.33wt%,0.35wt%,0.38wt%,0.4wt%等,但并不仅限于所列举的数值,上述数值范围内其他未列举的数值同样适用。
30.作为本发明优选的技术方案,步骤(2)所述激发转晶的时间为2-3h,例如可以是2h,2.1h,2.2h,2.3h,2.4h,2.5h,2.6h,2.7h,2.8h,2.9h,3h等,但并不仅限于所列举的数值,上述数值范围内其他未列举的数值同样适用。
31.作为本发明优选的技术方案,步骤(2)所述第二次固液分离的方式为离心分离。
32.优选地,在步骤(2)所述第二次固液分离后,进行干燥得到α半水石膏。
33.优选地,所述干燥的温度为100-160℃,例如可以是100℃,105℃,110℃,115℃,120℃,125℃,130℃,135℃,140℃,145℃,150℃,155℃,160℃等,但并不仅限于所列举的数值,上述数值范围内其他未列举的数值同样适用。
34.作为本发明优选的技术方案,所述方法包括如下步骤:
35.(1)将比表面积≥500m2·
kg的氟石膏98-103份、煅烧明矾4-6份、钠盐34-38份、二水石膏晶种19-21份与水混合,控制水与氟石膏的质量比为(5-7):1;在温度20-35℃、搅拌速度100-250r/min进行水化反应20-24h,经离心分离,得到二水石膏;
36.其中,煅烧明矾由十二水合硫酸铝钾在600-670℃下煅烧1-2h得到;
37.(2)将α半水石膏晶种、水与步骤(1)所述二水石膏混合,得到混合浆料,控制α半水石膏晶种与二水石膏的质量比为(0.2-0.4):1,水与所述二水石膏的质量比为(2-3):1;加入转晶剂丁二酸在121-128℃进行激发转晶2-3h,控制转晶剂的添加量占二水石膏的0.2-0.4wt%;经离心分离后,100-160℃干燥得到α半水石膏。
38.本发明所述的数值范围不仅包括上述例举的点值,还包括没有例举出的上述数值范围之间的任意的点值,限于篇幅及出于简明的考虑,本发明不再穷尽列举所述范围包括的具体点值。
39.与现有技术相比,本发明的有益效果为:
40.(1)本发明所述氟石膏制备α半水石膏的方法,将氟石膏水化、转晶制得α半水石膏,缓解了氟石膏的环境污染问题,氟石膏在24小时内快速水化且水化率达到85%以上,氟石膏的水化时间大幅缩短;
41.(2)本发明所述氟石膏制备α半水石膏的方法,所得α半水石膏的粒度大,强度高,其符合jc/t2038-2010标准规定的α40级别;且初凝时间和终凝时间短。
具体实施方式
42.下面通过具体实施方式来进一步说明本发明的技术方案。本领域技术人员应该明了,所述实施例仅仅是帮助理解本发明,不应视为对本发明的具体限制。
43.值得说明的是,本发明的具体实施方式中使用的氟石膏的化学成分,按重量份数计包括:cao 40.66%、so
3 56.57%、sio
2 0.841%、al2o
3 0.165%、fe2o
3 0.0871%、mgo 0.0448%、k2o 0.0377%、p2o
5 0.0185%、tio
2 0.0119%、cl 0.0108%、sro 0.01%、mno 0.0071%、pbo 0.0048%、loi 1.52%、结晶水1.21%。
44.实施例1
45.本实施例提供了一种氟石膏制备α半水石膏的方法,所述方法包括如下步骤:
46.(1)将比表面积为550m2·
kg的氟石膏100份、煅烧明矾5份、硫酸钠5份、氯化钠29份、二水石膏晶种20份与水混合,控制水与氟石膏的质量比为6:1;在温度25℃、搅拌速度200r/min进行水化反应24h,经离心分离,得到二水石膏;
47.其中,煅烧明矾由十二水合硫酸铝钾在650℃下煅烧1h得到;
48.(2)将α半水石膏晶种、水与步骤(1)所述二水石膏混合,得到混合浆料,控制α半水石膏晶种与二水石膏的质量比为0.2:1,水与所述二水石膏的质量比为2:1;加入转晶剂丁二酸在125℃进行激发转晶3h,控制转晶剂的添加量占二水石膏的0.3wt%;经离心分离后,160℃干燥得到α半水石膏。
49.实施例2
50.本实施例提供了一种氟石膏制备α半水石膏的方法,所述方法包括如下步骤:
51.(1)将比表面积为600m2·
kg的氟石膏103份、煅烧明矾4份、硫酸钠6份、氯化钠30份、二水石膏晶种19份与水混合,控制水与氟石膏的质量比为5:1;在温度20℃、搅拌速度250r/min进行水化反应22h,经离心分离,得到二水石膏;
52.其中,煅烧明矾由十二水合硫酸铝钾在600℃下煅烧2h得到;
53.(2)将α半水石膏晶种、水与步骤(1)所述二水石膏混合,得到混合浆料,控制α半水石膏晶种与二水石膏的质量比为0.3:1,水与所述二水石膏的质量比为3:1;加入转晶剂丁二酸在121℃进行激发转晶2.5h,控制转晶剂的添加量占二水石膏的0.4wt%;经离心分离后,140℃干燥得到α半水石膏。
54.实施例3
55.本实施例提供了一种氟石膏制备α半水石膏的方法,所述方法包括如下步骤:
56.(1)将比表面积为500m2·
kg的氟石膏98份、煅烧明矾6份、硫酸钠7份、氯化钠31份、二水石膏晶种21份与水混合,控制水与氟石膏的质量比为7:1;在温度35℃、搅拌速度100r/min进行水化反应20h,经离心分离,得到二水石膏;
57.其中,煅烧明矾由十二水合硫酸铝钾在670℃下煅烧0.5h得到;
58.(2)将α半水石膏晶种、水与步骤(1)所述二水石膏混合,得到混合浆料,控制α半水石膏晶种与二水石膏的质量比为0.4:1,水与所述二水石膏的质量比为2.5:1;加入转晶剂丁二酸在128℃进行激发转晶2h,控制转晶剂的添加量占二水石膏的0.2wt%;经离心分离后,100℃干燥得到α半水石膏。
59.实施例4
60.本实施例提供了一种氟石膏制备α半水石膏的方法,所述方法参照实施例1所述的方法,区别在于:将步骤(1)中的硫酸钠5份、氯化钠29份替换为硫酸钠34份。
61.实施例5
62.本实施例提供了一种氟石膏制备α半水石膏的方法,所述方法参照实施例1所述的方法,区别在于:步骤(2)转晶剂的添加量占二水石膏的0.1wt%。
63.实施例6
64.本实施例提供了一种氟石膏制备α半水石膏的方法,所述方法参照实施例1所述的方法,区别在于:步骤(2)转晶剂的添加量占二水石膏的0.5wt%。
65.对比例1
66.本对比例提供了一种氟石膏制备α半水石膏的方法,所述方法参照实施例1所述的方法,区别在于:步骤(2)所述激发转晶的温度为112℃。
67.对比例2
68.本对比例提供了一种氟石膏制备α半水石膏的方法,所述方法参照实施例1所述的方法,区别在于:步骤(2)所述激发转晶的温度为135℃。
69.将上述实施例与对比例进行测试,测试内容与方法如下:
70.①
氟石膏水化率:水化到规定龄期的氟石膏用无水乙醇终止水化,在50℃下烘干,准确称量烘干至恒重的氟石膏水化样品,于450℃煅烧30min,测结晶水质量分数,由此计算二水石膏质量分数及氟石膏水化率;
71.②
二水石膏、α半水石膏的中值粒径:使用激光粒度分布仪进行测试;
72.③
α半水石膏的标准稠度:根据gb/t17669.3-1999《建筑石膏力学性能的测定》和gb/t17669.4-1999《建筑石膏净浆物理性能的测定》中的方法进行测定;
73.④
α半水石膏的初凝时间、终凝时间:根据gb/t17669.3-1999《建筑石膏力学性能的测定》和gb/t17669.4-1999《建筑石膏净浆物理性能的测定》中的方法进行测定;
74.⑤
α半水石膏的2h抗折强度:根据gb/t17669.3-1999《建筑石膏力学性能的测定》和gb/t17669.4-1999《建筑石膏净浆物理性能的测定》中的方法进行测定;
75.⑥
α半水石膏的2h抗压强度:根据gb/t17669.3-1999《建筑石膏力学性能的测定》和gb/t17669.4-1999《建筑石膏净浆物理性能的测定》中的方法进行测定;
76.⑦
α半水石膏的干抗压强度:根据gb/t17669.3-1999《建筑石膏力学性能的测定》和gb/t17669.4-1999《建筑石膏净浆物理性能的测定》中的方法进行测定;
77.将上述
①‑④
的测试结果列于表1,
⑤‑⑦
的测试结果列于表2。
78.表1
[0079][0080][0081]
表2
[0082]
项目2h抗折强度/mpa2h抗压强度/mpa干抗压强度/mpa实施例15.426.742.6实施例25.125.340.5实施例35.224.141.2实施例45.023.640.8实施例54.620.838.4实施例64.923.440.1对比例14.724.340.0对比例24.924.839.1
[0083]
由表1和表2可以得出以下几点:
[0084]
(1)由实施例1-3可以看出,本发明所述氟石膏制备α半水石膏的方法中,氟石膏水化率达到85%以上,所得α半水石膏的粒度大,强度高,其符合jc/t2038-2010标准规定的α40级别;且初凝时间和终凝时间短;
[0085]
(2)将实施例1与实施例4进行比较,可以看出,实施例1中钠盐为硫酸钠和氯化钠,与实施例1相比,实施例4中钠盐仅为硫酸钠,导致氟石膏水化率下降,终凝时间增加,2h抗折强度、2h抗压强度和干抗压强度下降;
[0086]
(2)将实施例1与实施例5、6进行比较,可以看出,由于实施例5中转晶剂的添加量占二水石膏的0.1wt%,低于本发明优选的0.2-0.4wt%,导致氟石膏水化率下降,初凝时间增加,2h抗折强度、2h抗压强度和干抗压强度下降;由于实施例6中转晶剂的添加量占二水石膏的0.5wt%,超出本发明优选的0.2-0.4wt%,导致氟石膏水化率下降,终凝时间增加,
2h抗折强度、2h抗压强度和干抗压强度下降;
[0087]
(3)将实施例1与对比例1、2进行比较,可以看出,由于对比例1的激发转晶的温度为112℃,低于本发明优选的121-128℃,导致氟石膏水化率下降,初凝时间和终凝时间增加,2h抗折强度、2h抗压强度和干抗压强度下降;由于对比例2的激发转晶的温度为135℃,超出本发明优选的121-128℃,导致氟石膏水化率下降,初凝时间和终凝时间增加,2h抗折强度、2h抗压强度和干抗压强度下降。
[0088]
以上所述的具体实施例,对本发明的目的、技术方案和有益效果进行了进一步详细说明,所应理解的是,以上所述仅为本发明的具体实施例而已,并不用于限制本发明,凡在本发明的精神和原则之内,所做的任何修改、等同替换、改进等,均应包含在本发明的保护范围之内。