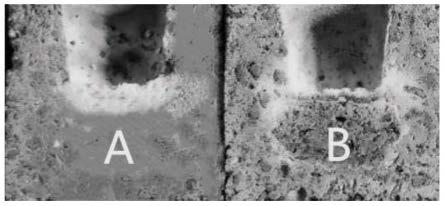
1.本发明涉及耐火材料领域,具体为一种镁质强耐腐蚀性耐火材料及其制备方法。
背景技术:2.耐火材料被广泛应用于化工、石油、冶金、机械制造、动力等工业领域。镁质耐火材料由于具有耐火性能高、高温强度大的特点,随着近年来,我国不锈钢以及洁净钢发展速度较快,而逐渐受到重视,成为冶金行业中广泛应用的辅料之一。目前的镁质耐火材料多以菱镁矿、海水镁砂和白云石等作为原料,以方镁石为主晶相。
3.在炼钢过程中,由于炉渣、钢液与耐火炉衬紧密接触,炉渣对耐火炉衬的腐蚀是造成炉衬损毁的重要原因,现有的镁质耐火材料虽然对炉渣有一定的抵抗能力,但是急冷急热,钢液的循环冲刷以及高碱性渣的长时间侵蚀还是不可避免的造成耐火材料被腐蚀损坏,因此提高耐火材料的耐腐蚀性能逐渐成为目前的研究重点。
技术实现要素:4.发明目的:针对上述技术问题,本发明提出了一种镁质强耐腐蚀性耐火材料及其制备方法。
5.所采用的技术方案如下:
6.一种镁质强耐腐蚀性耐火材料,以重量份数计,包括以下组成成分:
7.镁橄榄石40-60份、镁铝尖晶石40-60份、sialon粉体20-30份、锆酸钙5-10份、氧化锆5-10份、氮化硅-氧氮化硅复合粉体3-6份、硫酸镁晶须10-20份、氧化钴1.5-3份、莫来石溶胶20-30份、纳米铟粉1-2份。
8.进一步地,以重量份数计,包括以下组成成分:
9.镁橄榄石50份、镁铝尖晶石50份、sialon粉体25份、锆酸钙10份、氧化锆5份、氮化硅-氧氮化硅复合粉体5份、硫酸镁晶须12份、氧化钴2份、莫来石溶胶30份、纳米铟粉1份。
10.进一步地,所述sialon粉体的结构通式如下:
11.si
6-z
alzozn
8-z
,z表示固溶量,z为3-3.5。
12.进一步地,z为3。
13.进一步地,所述sialon粉体的制备方法如下:
14.将氯化铝、正硅酸乙酯、二氯甲烷混合,搅拌均匀,反应液于110-120℃中放置14-16h,将生成的凝胶干燥后于450-500℃预焙烧1-2h,然后与炭黑和氟化钙混合,球磨1-3h后干燥,得到前驱体,将前驱体置于管式炉,通入氮气,升温至1450-1500℃反应2-4h,再降温至800-1050℃排碳1-2h即可。
15.进一步地,炭黑用量为氯化铝质量的55-60%。
16.进一步地,所述氮化硅-氧氮化硅复合粉体的制备方法如下:
17.将硫酸加入蔗糖溶液中,搅拌均匀后加入介孔分子筛sba-15,室温搅拌1-2h后,升温至100-120℃继续搅拌,直至水分充分蒸发,升温至230-260℃,预碳化6-8h,然后在氮气
保护下,先升温至800-850℃煅烧4-6h,再升温至1200-1400℃,保温4-8h后冷却至800-850℃排碳1-2h,最后恢复室温即可。
18.进一步地,所述莫来石溶胶的制备方法如下:
19.将硝酸铝加入乙醇中,搅拌溶解后升温至50-70℃加入正硅酸乙酯和稀盐酸溶液,搅拌1-2h后用氨水调节体系ph至3-4,保温静置2-4h即可。
20.本发明还提供了一种镁质强耐腐蚀性耐火材料的制备方法:
21.将镁橄榄石、镁铝尖晶石、sialon粉体、锆酸钙、氧化锆、氮化硅-氧氮化硅复合粉体、硫酸镁晶须、氧化钴、纳米铟粉球磨混合均匀后烘干,再与莫来石溶胶混合,在10-15mpa下预压成型,再用海绵包裹,等静压至130-150mpa后,110-120℃下干燥5-10h,先一段升温至1200-1250℃,通入氮气,再二段升温至1700-1800℃并保温1-2h,然后自然冷却至室温即可。
22.进一步地,一段升温的速率为10-15℃/min,二段升温的速率为3-6℃/min。
23.本发明的有益效果:
24.本发明提供了一种镁质强耐腐蚀性耐火材料,镁橄榄石属碱性耐火材料,化学稳定性好,熔点高,有很好的抗侵蚀作用,高温下同大多数耐火材料的相容性好,镁铝尖晶石具有优良的高温性能,是本发明耐火材料的重要组成成分,镁铝尖晶石中含有的氧化镁有着很好的蠕变特点,能够提高耐火材料的高温韧性、耐冲击性以及耐剥落性,从而有效提高耐火炉衬的使用寿命,sialon粉体是由硅、铝、氧和氮组成的物质,在低温和高温下均具有优异的硬度和机械强度、低热膨胀系数、优异的耐磨损性能和耐化学腐蚀性能,锆酸钙和氧化锆的加入可以提高耐火材料的耐腐蚀性能和抗热震性能,纳米铟粉高温生成的氧化物可阻塞气孔,降低材料的气孔率和透气度,且可与其余组分之间反应生成新的物相,有利于耐火材料烧结更加致密,可增强耐火材料的强度,各组分在莫来石溶胶的作用下压制和烧结过程中形成致密的陶瓷结构,因而具有强耐腐蚀性和力学性能,氮化硅-氧氮化硅复合粉体与硫酸镁晶须相互交织在一起,形成空间致密的网状结构,提升耐火材料的强度,烧结过程中氧化钴中钴离子可以部分取代莫来石[alo6]八面体中铝离子,导致畸变,使其晶格得到活化,促进耐火材料致密化,本发明所制备的耐火材料具有极佳的力学强度、抗热震性能和强耐腐蚀性。
附图说明
[0025]
图1为耐火材料经熔渣热侵蚀后的形貌,其中a为实施例1所制备镁质强耐腐蚀性耐火材料,b为市售耐火材料。
[0026]
图2为本发明实施例1中镁质强耐腐蚀性耐火材料熔渣热侵蚀后的sem图。
具体实施方式
[0027]
实施例中未注明具体条件者,按照常规条件或制造商建议的条件进行。所用试剂或仪器未注明生产厂商者,均为可以通过市售购买获得的常规产品。
[0028]
实施例1:
[0029]
一种镁质强耐腐蚀性耐火材料,以重量份数计,包括以下组成成分:
[0030]
镁橄榄石50份、镁铝尖晶石50份、sialon粉体25份、锆酸钙10份、氧化锆5份、氮化
硅-氧氮化硅复合粉体5份、硫酸镁晶须12份、氧化钴2份、莫来石溶胶30份、纳米铟粉1份。
[0031]
其中,sialon粉体的结构通式如下:
[0032]
si3al3o3n5[0033]
sialon粉体的制备方法如下:
[0034]
按照结构通式si3al3o3n5称取原料,将79.8g氯化铝、124.8g正硅酸乙酯、500ml二氯甲烷混合,搅拌40min使均匀后,反应液于120℃中放置16h,将生成的凝胶干燥后于500℃预焙烧2h,然后与47.8g炭黑和5g氟化钙混合,以乙醇作为球磨介质球磨3h后80℃干燥10h,得到前驱体,将前驱体置于管式炉,通入氮气,氮气流量为100ml/min,升温至1500℃反应4h,再降温至1050℃排碳2h即可。
[0035]
氮化硅-氧氮化硅复合粉体的制备方法如下:
[0036]
将3.8g硫酸加入500ml 6.8wt%蔗糖溶液中,搅拌均匀后加入100g介孔分子筛sba-15,室温搅拌2h后,升温至120℃继续搅拌,直至水分充分蒸发,升温至260℃,预碳化8h,然后在氮气保护下,先升温至850℃煅烧6h,再升温至1400℃,保温8h后冷却至850℃排碳2h,最后恢复室温即可。
[0037]
莫来石溶胶的制备方法如下:
[0038]
将100g硝酸铝加入250ml乙醇中,搅拌溶解后升温至70℃加入32.6g正硅酸乙酯和25ml 1wt%稀盐酸溶液,搅拌2h后用25%氨水调节体系ph至4,保温静置4h即可。
[0039]
上述镁质强耐腐蚀性耐火材料的制备方法:
[0040]
将镁橄榄石、镁铝尖晶石、sialon粉体、锆酸钙、氧化锆、氮化硅-氧氮化硅复合粉体、硫酸镁晶须、氧化钴、纳米铟粉球磨混合均匀后烘干,再与莫来石溶胶混合,在15mpa下预压成型,再用海绵包裹,等静压至150mpa后,120℃下干燥10h,先以15℃/min的速度一段升温至1250℃,通入氮气,再以6℃/min的速度二段升温至1800℃并保温2h,然后自然冷却至室温即可。
[0041]
采用钻孔、切割将耐火材料制成外形尺寸为60mm
×
60mm
×
90mm,内径尺寸为φ30mm的坩锅,并将内孔底端用实心钻头加工平整,实验室配制熔渣,其化学组成(w)为:sio
2 13%,al2o
3 20%,cao 33%,na2o 20%,mgo 4%,mno
2 10%,碱度r=4,将熔渣放入坩锅中,以2℃/min的速率升温至1500℃,保温10h后停炉自然冷却,观察其被煤熔渣渗透和侵蚀的情况,结果见图1(a),从坩锅内底与熔渣接触区域取样制成光片,进行sem分析,结果见图2。
[0042]
另购耐火材料(品牌:红枫湖,镁铁尖晶石砖)制成坩埚并加热侵蚀,具体操作同上,结果见图1(b),通过图1(a)和图1(b)对比可知,本实施例所制备耐火材料的耐腐蚀性能优于市售耐火材料。
[0043]
实施例2:
[0044]
一种镁质强耐腐蚀性耐火材料,以重量份数计,包括以下组成成分:
[0045]
镁橄榄石40份、镁铝尖晶石40份、sialon粉体20份、锆酸钙5份、氧化锆5份、氮化硅-氧氮化硅复合粉体3份、硫酸镁晶须10份、氧化钴1.5份、莫来石溶胶20份、纳米铟粉1份。
[0046]
其中,sialon粉体、氮化硅-氧氮化硅复合粉体、莫来石溶胶同实施例1。
[0047]
上述镁质强耐腐蚀性耐火材料的制备方法:
[0048]
将镁橄榄石、镁铝尖晶石、sialon粉体、锆酸钙、氧化锆、氮化硅-氧氮化硅复合粉
体、硫酸镁晶须、氧化钴、纳米铟粉球磨混合均匀后烘干,再与莫来石溶胶混合,在10mpa下预压成型,再用海绵包裹,等静压至130mpa后,110℃下干燥5h,先以10℃/min的速度一段升温至1200℃,通入氮气,再以3℃/min的速度二段升温至1700℃并保温1h,然后自然冷却至室温即可。
[0049]
实施例3:
[0050]
一种镁质强耐腐蚀性耐火材料,以重量份数计,包括以下组成成分:
[0051]
镁橄榄石60份、镁铝尖晶石40份、sialon粉体30份、锆酸钙5份、氧化锆10份、氮化硅-氧氮化硅复合粉体3份、硫酸镁晶须20份、氧化钴1.5份、莫来石溶胶30份、纳米铟粉1份。
[0052]
其中,sialon粉体、氮化硅-氧氮化硅复合粉体、莫来石溶胶同实施例1。
[0053]
上述镁质强耐腐蚀性耐火材料的制备方法:
[0054]
将镁橄榄石、镁铝尖晶石、sialon粉体、锆酸钙、氧化锆、氮化硅-氧氮化硅复合粉体、硫酸镁晶须、氧化钴、纳米铟粉球磨混合均匀后烘干,再与莫来石溶胶混合,在15mpa下预压成型,再用海绵包裹,等静压至130mpa后,120℃下干燥5h,先以15℃/min的速度一段升温至1200℃,通入氮气,再以6℃/min的速度二段升温至1700℃并保温2h,然后自然冷却至室温即可。
[0055]
实施例4:
[0056]
一种镁质强耐腐蚀性耐火材料,以重量份数计,包括以下组成成分:
[0057]
镁橄榄石40份、镁铝尖晶石60份、sialon粉体20份、锆酸钙10份、氧化锆5份、氮化硅-氧氮化硅复合粉体6份、硫酸镁晶须10份、氧化钴3份、莫来石溶胶20份、纳米铟粉2份。
[0058]
其中,sialon粉体、氮化硅-氧氮化硅复合粉体、莫来石溶胶同实施例1。
[0059]
上述镁质强耐腐蚀性耐火材料的制备方法:
[0060]
将镁橄榄石、镁铝尖晶石、sialon粉体、锆酸钙、氧化锆、氮化硅-氧氮化硅复合粉体、硫酸镁晶须、氧化钴、纳米铟粉球磨混合均匀后烘干,再与莫来石溶胶混合,在10mpa下预压成型,再用海绵包裹,等静压至150mpa后,110℃下干燥10h,先以10℃/min的速度一段升温至1250℃,通入氮气,再以3℃/min的速度二段升温至1800℃并保温1h,然后自然冷却至室温即可。
[0061]
实施例5:
[0062]
一种镁质强耐腐蚀性耐火材料,以重量份数计,包括以下组成成分:
[0063]
镁橄榄石60份、镁铝尖晶石60份、sialon粉体30份、锆酸钙10份、氧化锆10份、氮化硅-氧氮化硅复合粉体6份、硫酸镁晶须20份、氧化钴3份、莫来石溶胶30份、纳米铟粉2份。
[0064]
其中,sialon粉体、氮化硅-氧氮化硅复合粉体、莫来石溶胶同实施例1。
[0065]
上述镁质强耐腐蚀性耐火材料的制备方法:
[0066]
将镁橄榄石、镁铝尖晶石、sialon粉体、锆酸钙、氧化锆、氮化硅-氧氮化硅复合粉体、硫酸镁晶须、氧化钴、纳米铟粉球磨混合均匀后烘干,再与莫来石溶胶混合,在15mpa下预压成型,再用海绵包裹,等静压至145mpa后,120℃下干燥8h,先以10℃/min的速度一段升温至1250℃,通入氮气,再以5℃/min的速度二段升温至1750℃并保温2h,然后自然冷却至室温即可。
[0067]
对比例1:
[0068]
与实施例1基本相同,区别在于,不加入sialon粉体。
[0069]
对比例2:
[0070]
与实施例1基本相同,区别在于,不加入锆酸钙。
[0071]
对比例3:
[0072]
与实施例1基本相同,区别在于,不加入氧化锆。
[0073]
对比例4:
[0074]
与实施例1基本相同,区别在于,不加入氮化硅-氧氮化硅复合粉体。
[0075]
对比例5:
[0076]
与实施例1基本相同,区别在于,不加入纳米铟粉。
[0077]
性能测试:
[0078]
将本发明实施例1-5及对比例1-5所制备的耐火材料作为试样,试样的常温耐压强度按gb/t 5072-2008规定的方法测试,在机械或液压试验机上以规定的加压速率对圆形或者方形的试样加荷,直到试样破碎。根据记录的最大载荷和试样受载荷的面积,试样的高温抗折强度根据gb/t 3002-2004规定的方法进行测试,将经过高温烧成并冷却的条形试样按规定间隔置于可移动间距为125mm的两个下刀口的滑板上装进试验炉内,调节试样与上刀口的间距不小于5mm。加热到1350℃时保温30min后,将试样对称地置于下刀口上,使上刀口在试样的压力面中部垂直均匀加荷直至断裂,记录断裂时的最大载荷。
[0079]
抗热震性能采用冷热循环法测量试样的常温耐压强度残余率加以表征,将试样置于马弗炉中并以5℃/min的升温速率加热到1000℃后保温30min,使得试样受热均匀,然后迅速将试样取出,用冷空气吹30min,待试样完全冷却后,即为一次热循环,按照以上步骤重复进行10次,常温耐压强度残余率的σ计算公式如下:
[0080]
σ=a2/a1*100%
[0081]
其中:σ为常温耐压强度残余率
[0082]
a1为初始常温耐压强度残余率
[0083]
a2为10次冷热循环后的常温耐压强度残余率
[0084]
测试结果如下表1所示:
[0085]
表1:
[0086][0087]
由上表1可知,本发明所制备的耐火材料具有极佳的力学强度和抗热震性能。
[0088]
以上实施例仅用以说明本发明的技术方案,而非对其限制;尽管参照前述实施例对本发明进行了详细的说明,本领域的普通技术人员应当理解:其依然可以对前述各实施例所记载的技术方案进行修改,或者对其中部分技术特征进行等同替换;而这些修改或者替换,并不使相应技术方案的本质脱离本发明各实施例技术方案的精神和范围。