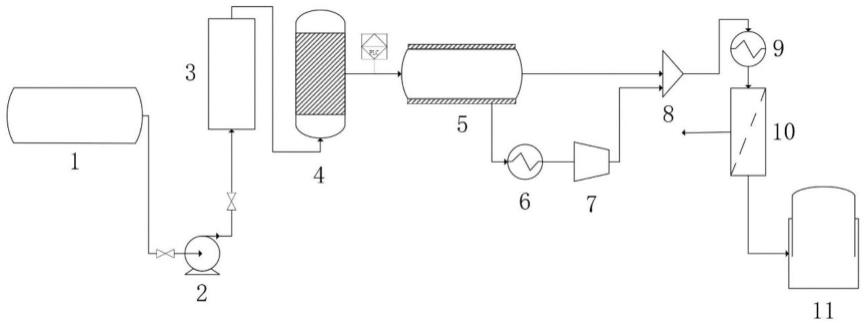
1.本发明涉及一种氨分解制氢装置工艺,具体涉及一种膜分离技术耦合嵌入氨分解制氢装置及工艺流程。
背景技术:2.氢能是一种极具发展潜力的可再生清洁能源,在我国能源体系中占有举足轻重的地位。氢能缓解了化石能源日益枯竭的尴尬地位,并且在使用过程中零碳排放,在“双碳”背景下,发挥着巨大作用。传统氨分解制氢工艺包含液氨气化、氨气裂解,产品气变压吸附提纯等流程,主要存在两个缺点,其一,裂解炉反应温度通常在800~870℃之间,需要巨大热能;其二,虽然变压吸附已成功应用于工业上氨分解制氢技术中粗产品气的分离纯化,但变压吸附必须采用间歇工艺和多个单元以确保连续分离,增加了产品气提纯成本。同时,粗产品气变压吸附提纯过程中,氢气回收率在70~80%之间,氨损失率高且产品氢气纯度相对较低。因此,急需对现有技术进行改进以实现氢气的低能耗生产,并降低氢气的生产成本。
3.膜分离是一种新兴的高效分离技术,具有设备占地面积小、操作简单、运行能耗低等优势。近年来,研究人员将有机膜、分子筛膜以及金属膜等应用于氢气分离纯化方面,取得优异的成果。而在氨分解制氢工艺中,较高的氨分解温度严重限制了有机膜的应用。与大多数有机膜相比,无机膜分离选择性高、耐高温高压、热化学稳定性好,适用于工业环境下氨气分解制氢过程中氢气的分离纯化。
4.因此,本发明尝试将氨裂解炉与无机膜生物反应耦合以实现氢气的低能耗生产,并提高氨分解速率。
技术实现要素:5.针对现有技术的上述问题,本发明提供了一种膜耦合氨分解制氢装置及工艺,解决传统氨分解制氢工艺中裂解炉反应温度过高、氨转化率低、变压吸附成本高以及氢气回收率低等问题。传统氨分解制氢工艺中,氨裂解炉通常在极高温度下获得较为可观的氨分解率。而本发明在氨裂解炉后部耦合嵌入包括分离膜和催化反应器的膜反应器,一方面使制氢反应与氢气分离纯化过程同时进行,突破了反应热力学平衡限制,提高反应转化率和氢气产率,另一方面又可降低反应温度、缓和反应条件,降低了氨裂解炉热能耗。通过在膜反应器渗透侧增设气泵及时移除氢气,进一步提高反应速率。膜反应器渗余侧气体与渗透侧气体经混合器混合后通入膜分离器,可以直接制得纯氢,从而简化制氢工艺,降低制氢成本。增设混合器包含一下几个目的:一是膜反应器渗透侧产品气体纯度未达标,需进一步提纯,与渗余侧气体一同通入膜分离器可降低膜分离器成本;二是渗透侧产品气进入气泵前已降温至气泵工作温度,进入混合器与渗余侧气体混合可在一定程度上换热,从而接近膜分离器所需分离温度。
6.本发明具体技术方案如下:
7.本发明提供一种膜耦合氨分解制氢装置,其包括依次连接的氨裂解炉、膜反应器
和膜分离器,所述膜反应器中采用无机膜。
8.优选的,所述的无机膜为致密膜或多孔膜的一种,其中致密膜包括金属膜、质子导体陶瓷膜、氮化膜,多孔膜包括硅膜、沸石分子筛膜、碳分子筛膜,其中金属膜为钯膜、钯合金膜、铌膜、铌合金膜中的一种;质子导体陶瓷膜为钙钛矿型或其它含氟、含磷金属氧化物;硅膜为氧化硅膜或杂化硅膜;分子筛膜为cha型、ddr型、mfi型、lta型、t型、stt型分子筛膜中的一种。出于通量的考虑,优选采用多孔膜,特别是分子筛膜。
9.优选的,膜分离器中的膜选自有机膜或者无机膜,优选采用无机膜。无机膜的类型优选钯膜或钯合金膜。
10.优选的,所述的膜反应器出口为两条,一条为渗透管路,一条为渗余管路;所述渗透管路上依次设置有冷却器和气泵,所述渗余管路与膜分离器的进料侧连接。
11.优选的,所述渗透管路中气泵的下游与渗余管路的下游连接混合器,混合器的出口经第二冷却器后与膜分离器的进料侧连接。
12.优选的,所述氨裂解炉的上游连接液氮储备罐和汽化器,膜分离器的渗透侧出口连接氢气储罐。
13.本发明还提供了一种利用上述膜耦合氨分解制氢装置的制氢工艺,其特征在于所述工艺包括:汽化的氨气在氨裂解炉中分解成粗产品气,粗产品气输送至膜反应器中实现氨气进一步分解,所述的氨裂解炉温度为400~600℃。优选的,膜反应器的渗透侧产品气通过冷却器降温至50-90℃后经气体泵增压,渗透侧气体经膜分离器进一步提纯。
14.优选的,所述的渗透侧产品气经冷却器降温后进入气泵增压后与渗余侧气体混合后并冷却至膜分离器中膜材料的最佳分离温度后进入膜分离器进一步提纯。例如,当膜分离器采用钯膜作为分离膜时,该冷却温度为300-400℃。
15.优选的,其特征所述的气泵压缩比为4~7,驱动气为空气,驱动压力为0.8~1.7bar,工作温度为50-90℃。
16.优选的,所述的氨裂解炉裂解与膜反应器间至少有一个温度传感器及其控制装置,使用催化剂为镍基催化剂、钌基催化剂或者铁基催化剂。
17.优选的,所述膜反应器操作温度为300~600℃,操作压力为1-10bar。
18.相对于现有技术,本发明具有如下有益效果:
19.首先,本发明采用氨分解炉和无机膜反应器的耦合进行氨的分解制氢,相对于单纯的氨分解炉可以实现在300-600℃的低温下分解,降低了氢气的生产能耗;相对于单纯的膜反应器,氨分解炉相对于一个预分解炉可以加快氨的分解速率。
20.其次,本发明在膜反应器的渗余侧连接膜分离器,可以回收膜渗余侧中的氢气,提高氢气的回收率。而膜反应器渗透侧气泵的设置可以及时移除膜反应器中渗透的氢气,提高膜反应器的氨分解速率,冷却器的设置使得渗透侧气体满足气泵的正常工作温度。
21.另外,由于膜分离器中操作温度低于膜反应器温度,因此第二冷却器的设置可以对膜反应器的渗余侧气体进行降温,需要消耗很多的冷能实现降温,而本发明将渗透侧气体与渗余侧气体混合可以回收冷却器的冷能,也能够弥补膜反应器渗透侧产品气纯度不高的缺点。
附图说明
22.图1为膜耦合氨分解制氢工艺流程示意图。其中,1—液氨储存罐;2—液氨输送泵;3—汽化器;4—氨裂解炉;5—膜反应器;6-冷却器,7—气泵;8—混合器;9—第二冷却器;10—膜分离器;11—氢气储罐
具体实施方式
23.下面将结合附图对本发明的技术方案进行清楚、完整地描述,显然,所描述的实施例是本发明一部分实施例,而不是全部的实施例。基于本发明中的实施例,本领域普通技术人员在没有做出创造性劳动前提下所获得的所有其它实施例,都属于本发明保护的范围。
24.实施例1
25.如图1所示,本发明的膜耦合氨分解制氢装置包括依次连接的液氨储存罐1、液氨输气泵2、汽化器3、氨裂解炉4、膜反应器5、膜分离器10和氢气储罐11,其中膜反应器出口为两条,一条为渗透管路,一条为渗余管路;所述渗透管路上依次设置有冷却器6和气泵7,所述渗余管路与膜分离器10的进料侧连接。渗透管路中气泵7的下游与渗余管路的下游连接混合器8,混合器8的出口经第二冷却器9后与膜分离器10的进料侧连接,膜分离,10的渗透侧出口连接氢气储罐11。
26.实施例2
27.如图1所示的膜耦合氨分解制氢工艺流程,液氨储存罐1中的液氨经液氨输送泵2输送至汽化器3,在汽化器3加压汽化成氨气后,输送至填充有催化剂的氨裂解炉4,裂解温度为500℃,氨裂解炉出口气为包含氨气、氢气、氮气等的粗产品气,此时氨转化率为50%。粗产品气输送至反应温度为450℃的膜反应器5,氨气进一步分解,膜反应器使用的催化剂为钌基催化剂,所用的膜为mfi型分子筛膜。经膜反应器5反应后,氨转化率提高至84%,渗透侧氢气浓度为86%。膜反应器5渗透侧产品经冷却器降温至80℃后进入气泵,气泵的存在使得膜反应器5的渗透气体可以实时移除。在膜反应器5渗余侧下游设置气体混合器,并将渗透侧产品与渗余侧气体混合实现温度平衡,随后经第二冷却器降温至300℃后进入膜分离器,经过钯合金膜分离器提纯产品氢气,膜分离器渗透侧氢气纯度提高至99.999%。经膜耦合后,氢气收率可达90%。
28.实施例2
29.按照实施例2所述的方法,所不同的是膜反应器所用的膜为cha型分子筛膜,膜反应器氨转化率提高至92%,渗透侧氢气浓度提高至97%。为加快反应速率,膜反应器渗透侧设置气泵,渗透气体通过气泵实时移除。在膜反应器后部设置气体混合器,将渗透气与渗余气混合,随后连接至膜分离器,经过钯合金膜分离器提纯产品氢气,膜分离器渗透侧氢气纯度提高至99.999%。经膜耦合后,氢气收率可达92%。
30.实施例3
31.按照实施例2所述的方法,所不同的是膜反应器所用的膜为碳分子筛膜,氨转化率为99%,渗透侧氢气浓度为95%,通过气泵实时移除,加快反应速率。其余气体经过膜分离器提纯,膜分离器所用膜为钯合金膜,渗透侧氢气纯度为99.999%。经膜耦合后,氢气收率可达91%。
32.实施例4
33.按照实施例2所述的方法,所不同的是膜反应器所用的膜为pd-ag合金膜,氨转化率为99%,渗透侧氢气浓度为99.99%,通过气泵实时移除,加快反应速率。其余气体经过膜分离器提纯,膜分离器所用膜为钯合金膜,渗透侧氢气纯度为99.999%。经膜耦合后,氢气收率可达94%。
34.实施例5
35.按照实施例2所述的方法,所不同的是膜反应器不增设混合器,此时氨转化率为99%,渗透侧氢气浓度为99.99%,通过气泵实时移除,加快反应速率。其余气体经过膜分离器提纯,膜分离器所用膜为钯合金膜,渗透侧氢气纯度为99.999%。经膜耦合后,氢气收率可达90%。