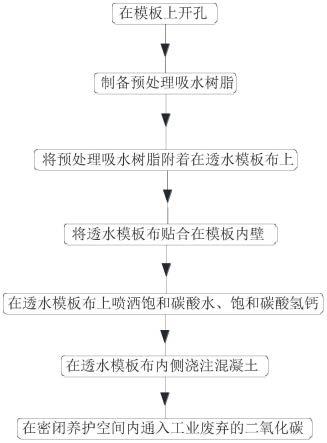
1.本发明涉及混凝土预制构件的养护的技术领域,具体地指一种混凝土预制构件的二氧化碳矿化养护方法。
背景技术:2.水泥和混凝土由于其高强度、显著耐久性和经济效益等因素,是目前世界上使用最为广泛的建筑材料之一,但水泥行业作为二氧化碳的主要生产商之一,创造了全球人造二氧化碳排放量的5%~8%。减少温室气体排放已成为各行业的优先事项,因此对水泥行业进行减排降碳刻不容缓。
3.目前主要是通过开发新的制造工艺、或用辅助胶凝材料取代硅酸盐水泥来减少水泥生产过程中的二氧化碳排放量,但是存在治标不治本的问题,达不到真正地通过利用二氧化碳进行减排降碳的效果。
4.二氧化碳矿化养护是指二氧化碳与水泥基材料发生碳化反应,若将其应用于水泥混凝土常规养护中可以视为碳捕获、利用和封存的一种有效利用方式,但目前二氧化碳矿化养护由于存在矿化不完全、矿化过程繁琐等问题,造成了二氧化碳利用率和混凝土碳化效率低问题。
技术实现要素:5.针对现有技术的不足之处,本发明提出一种混凝土预制构件的二氧化碳矿化养护方法,不仅可以快速地将混凝土表面碳化,提高混凝土早期的表面强度和表面硬度,增强混凝土结构表层的致密性;而且利用了大量的钢渣工业固体废弃物和二氧化碳工业废气。
6.为达到上述目的,本发明所设计的一种混凝土预制构件的二氧化碳矿化养护方法,其特别之处在于,包括如下步骤:
7.步骤1),在混凝土预制构件模板上开设内外贯穿的通孔;
8.步骤2),在吸水树脂中预先吸收饱和碳酸氢钙溶液,然后将吸收饱和碳酸氢钙溶液的吸水树脂进行烘干处理,得到预处理吸水树脂,将预处理吸水树脂附着在透水模板布上;
9.步骤3),将步骤1)中的混凝土预制构件模板表面清洗干净,并将步骤2)中的附着预处理吸水树脂的透水模板布紧密贴合于混凝土预制构件模板内壁,在透水模板布上喷洒制备好的饱和碳酸水、或饱和碳酸氢钙溶液,并将透水模板布的含水率控制在未饱和状态;
10.步骤4),在透水模板布内侧浇筑搅拌后的混凝土,振捣、收面成型,透水模板布上喷洒的碳酸水或碳酸氢钙溶液渗透到混凝土表层,与混凝土水化反应产生的氢氧化钙发生反应,生成碳酸钙沉淀物,提高混凝土早期的表层强度和表面硬度;透水模板布吸收混凝土表层富余的水分,降低表层水胶比,进一步提高混凝土早期的表层强度和表层致密性;另外,预处理吸水树脂吸附混凝土表层的多余水分,预处理吸水树脂内的碳酸氢钙逐渐溶解,补充起到二氧化碳长期矿化养护效果;
11.步骤5),在密闭养护空间内通入工业废弃的二氧化碳气体,二氧化碳气体通过模板通孔渗透到透水模板布上并溶解,形成饱和碳酸水、或碳酸氢钙溶液,对透水模板布中的起到补充作用,更进一步提高二氧化碳养护效果。
12.进一步地,步骤1)中,所述通孔的开孔率为40%~50%。
13.更进一步地,所述通孔直径d为50mm~60mm的圆形孔,且相邻圆形孔之间的间距l为40mm~60mm。
14.进一步地,步骤1)中,所述混凝土预制构件模板为钢模板、或木模板。
15.进一步地,步骤3)中,所述透水模板布的含水率为饱和吸水率的40%~60%。
16.进一步地,步骤4)中,所述混凝土包括粗骨料、细骨料、凝胶材料、水、减水剂。
17.更进一步地,所述凝胶材料包括50~70%重量份的普通硅酸盐水泥、10~20%重量份的粉煤灰、5~15%重量份的活性氧化镁、10~20%重量份的钢渣、10~20%重量份的石灰石粉、0.05~1%重量份的微纳米碳酸钙。
18.更进一步地,所述活性氧化镁粒径为0.5~2μm,其中氧化镁含量大于85%;所述钢渣粒径为10~100μm,其中sio2含量大于10%, cao含量大于40%,fe2o3含量大于20%;所述石灰石粉粒径为 10~50μm,其中caco3含量大于90%;所述微纳米碳酸钙粒径为 1~10μm,其中caco3含量大于90%。
19.进一步地,步骤5)中,所述二氧化碳气体的浓度30%~60%。
20.本发明的优点在于:
21.1.本发明在混凝土预制构件与模板之间设置透水模板布,利用透水模板布具有的较高的吸水率,在透水模板布上喷洒饱和碳酸水、或饱和碳酸氢钙溶液,使混凝土预制构件表面在较短的时间内就可以完成表面碳化,提高混凝土早期的表层强度和表面硬度;同时透水模板布可以吸收混凝土表层富余的水分,降低表层水胶比,进一步提高混凝土早期的表层强度和表层致密性;
22.2.本发明在透水模板布上附着预处理吸水树脂,通过预处理吸水树脂吸附混凝土表层的多余水分,使预处理吸水树脂内的碳酸氢钙逐渐溶解,补充起到二氧化碳长期矿化养护效果;
23.3.本发明在模板上开设通孔,将工业废弃的二氧化碳气体通过模板通孔渗透到透水模板布上并溶解,形成饱和碳酸水、或碳酸氢钙溶液,对透水模板布中的起到补充作用,更进一步提高二氧化碳养护效果。
24.本发明混凝土预制构件的二氧化碳矿化养护方法不仅可以快速地将混凝土表面碳化,提高混凝土早期的表面强度和表面硬度,增强混凝土结构表层的致密性,缩短混凝土预制构件养护时间,实现混凝土预制构件快速脱模,解决了模板周转率不高的问题;而且利用了大量的钢渣工业固体废弃物和二氧化碳工业废气,是一条实现二氧化碳矿化养护的新技术途径。
附图说明
25.图1为本发明混凝土预制构件的二氧化碳矿化养护方法的流程图;
26.图2为本发明混凝土预制构件的二氧化碳矿化养护方法中的模板开孔图;
27.图中:通孔直径d、相邻圆形孔之间的间距l。
具体实施方式
28.以下结合附图和具体实施例对本发明作进一步的详细描述。
29.在本发明的描述中,需要理解的是,术语“长度”、“宽度”、“上”、“下”、“前”、“后”、“左”、“右”、“竖直”、“水平”、“顶”、“底”“内”、“外”等指示的方位或位置关系为基于附图所示的方位或位置关系,仅是为了便于描述本发明和简化描述,而不是指示或暗示所指的装置或元件必须具有特定的方位、以特定的方位构造和操作,因此不能理解为对发明的限制。
30.本混凝土预制构件的二氧化碳矿化养护方法,如图1所示,包括如下步骤:
31.步骤1),在混凝土预制构件模板上开设内外贯穿的通孔。
32.具体地,所述混凝土预制构件模板为钢模板、或木模板,所述通孔的开孔率为40%~50%,所述通孔直径d为50mm~60mm的圆形孔,且相邻圆形孔之间的间距l为40mm~60mm。
33.如图2所示,所述通孔直径d为50mm的圆形孔,相邻圆形孔之间的间距l为50mm。
34.步骤2),在吸水树脂中预先吸收饱和碳酸氢钙溶液,然后将吸收饱和碳酸氢钙溶液的吸水树脂进行烘干处理,得到预处理吸水树脂,将预处理吸水树脂附着在透水模板布上。
35.步骤3),将步骤1)中的混凝土预制构件模板表面清洗干净,并将步骤2)中的附着预处理吸水树脂的透水模板布紧密贴合于混凝土预制构件模板内壁,在透水模板布上喷洒制备好的饱和碳酸水、或饱和碳酸氢钙溶液,并将透水模板布的含水率控制在未饱和状态。
36.具体地,所述透水模板布的含水率为饱和吸水率的40%~60%。
37.步骤4),在透水模板布内侧浇筑搅拌后的混凝土,振捣、收面成型,透水模板布上喷洒的碳酸水或碳酸氢钙溶液渗透到混凝土表层,与混凝土水化反应产生的氢氧化钙发生反应,生成碳酸钙沉淀物,提高混凝土早期的表层强度和表面硬度;透水模板布吸收混凝土表层富余的水分,降低表层水胶比,进一步提高混凝土早期的表层强度和表层致密性;另外,预处理吸水树脂吸附混凝土表层的多余水分,预处理吸水树脂内的碳酸氢钙逐渐溶解,补充起到二氧化碳长期矿化养护效果。
38.具体地,所述混凝土包括粗骨料、细骨料、凝胶材料、水、减水剂。所述凝胶材料包括50~70%重量份的普通硅酸盐水泥、10~20%重量份的粉煤灰、5~15%重量份的活性氧化镁、10~20%重量份的钢渣、10~20%重量份的石灰石粉、0.05~1%重量份的微纳米碳酸钙。
39.所述活性氧化镁粒径为0.5~2μm,其中氧化镁含量大于85%;所述钢渣粒径为10~100μm,其中sio2含量大于10%,cao含量大于 40%,fe2o3含量大于20%;所述石灰石粉粒径为10~50μm,其中caco3含量大于90%;所述微纳米碳酸钙粒径为1~10μm,其中caco3含量大于90%。
40.步骤5),在密闭养护空间内通入工业废弃的二氧化碳气体,二氧化碳气体通过模板通孔渗透到透水模板布上并溶解,形成饱和碳酸水、或碳酸氢钙溶液,对透水模板布中的起到补充作用,更进一步提高二氧化碳养护效果。
41.具体地,所述二氧化碳气体的浓度30%~60%。
42.本发明通过以下三种方式对混凝土预制构件进行二氧化碳矿化养护:
43.第一,在混凝土预制构件与模板之间设置透水模板布,利用透水模板布具有的较高的吸水率,在透水模板布上喷洒饱和碳酸水、或饱和碳酸氢钙溶液,使混凝土预制构件表面在较短的时间内就可以完成表面碳化,提高混凝土早期的表层强度和表面硬度;同时透水模板布可以吸收混凝土表层富余的水分,降低表层水胶比,进一步提高混凝土早期的表层强度和表层致密性;
44.第二,在透水模板布上附着预处理吸水树脂,通过预处理吸水树脂吸附混凝土表层的多余水分,使预处理吸水树脂内的碳酸氢钙逐渐溶解,补充起到二氧化碳长期矿化养护效果;
45.第三,在模板上开设通孔,将工业废弃的二氧化碳气体通过模板通孔渗透到透水模板布上并溶解,形成饱和碳酸水、或碳酸氢钙溶液,对透水模板布中的起到补充作用,更进一步提高二氧化碳养护效果。
46.下面以c55箱梁混凝土预制构件为例进行具体实施。
47.对比例1:
48.未实施二氧化碳矿化养护的混凝土预制构件,仅采用常规养护的混凝土由以下质量组份组成:胶凝材料(60份普通硅酸盐水泥、15 份粉煤灰、10分活性氧化镁、10份钢渣、10份石灰石粉、0.08份纳米碳酸钙)、30份水、190份碎石骨料、128份中砂骨料、1份聚羧酸减水剂。
49.制备过程包含以下步骤:
50.1)将碎石骨料、中砂骨料加入搅拌机中干搅0.5分钟;
51.2)将胶凝材料加入搅拌机中干搅0.5分钟;
52.3)将水和聚羧酸减水剂加入搅拌机中,搅拌2分钟出机,浇筑、振捣、收面成型标准试件后,放入相对湿度50%~70%的空间进行常规养护。
53.实施例1:
54.仅采用在透水模板布上喷洒饱和碳酸水、或饱和碳酸氢钙溶液对对比例1中的混凝土预制构件进行二氧化碳矿化养护。
55.制备过程包含以下步骤:
56.1)与对比例1同样的方式制备混凝土;
57.2)将木模板或钢模板表面清理干净,用胶粘剂把透水模板布附着于模板内侧;
58.3)配制饱和碳酸水、或碳酸氢钙溶液,喷洒于透水模板上,使透水模板布的含水率为饱和吸水率的50%;
59.4)将出机的新拌混凝土浇于透水模板布内侧,振捣、收面成型标准试件后,放置于相对湿度60%的空间进行矿化养护。
60.实施例2:
61.采用在透水模板布上喷洒饱和碳酸水、或饱和碳酸氢钙溶液,以及在透水模板布上附着预处理吸水树脂对对比例1中的混凝土预制构件进行二氧化碳矿化养护。
62.制备过程包含以下步骤:
63.1)与对比例1同样的方式制备混凝土;
64.2)将木模板或钢模板表面清理干净,用胶粘剂把透水模板布附着于模板内侧;
65.3)配制饱和碳酸氢钙溶液,吸水树脂吸收饱和碳酸氢钙溶液进行烘干处理,得到预处理吸水树脂,然后将预处理吸水树脂附着于透水模板布上;
66.4)配制饱和碳酸水、或碳酸氢钙溶液,喷洒于透水模板上,使透水模板布的含水率为饱和吸水率的50%;
67.5)将出机的新拌混凝土浇于透水模板布内侧,振捣、收面成型标准试件后,放置于相对湿度60%的空间进行矿化养护。
68.实施例3:
69.采用在透水模板布上喷洒饱和碳酸水、或饱和碳酸氢钙溶液,在透水模板布上附着预处理吸水树脂,以及在模板上开孔后通入工业废弃的二氧化碳对对比例1中的混凝土预制构件进行二氧化碳矿化养护。
70.制备过程包含以下步骤:
71.1)与对比例1同样的方式制备混凝土;
72.2)对木模板或钢模板进行开孔,开孔率为45%,开孔尺寸为直径50mm的圆形孔,各圆形孔间距为50mm。
73.3)将木模板或钢模板表面清理干净,用胶粘剂把透水模板布附着于模板内侧;
74.4)配制饱和碳酸氢钙溶液,吸水树脂吸收饱和碳酸氢钙溶液进行烘干处理,得到预处理吸水树脂,然后将预处理吸水树脂附着于透水模板布上;
75.5)配制饱和碳酸水、或碳酸氢钙溶液,喷洒于透水模板上,使透水模板布的含水率为饱和吸水率的50%;
76.6)将出机的新拌混凝土浇于模板中,通入浓度40%的工业废弃二氧化碳气体进行矿化养护。
77.根据gb/50204-2015《混凝土结构工程施工质量验收规范》,梁脱模所需的混凝土强度应≥75%(碳化回弹强度),一般需要养护时间超过48h以上,其混凝土相关性能由下表显示。
[0078][0079][0080]
由表试验结果可知:
[0081]
对比例1的脱模时间为48h;实施例1、2、3达到脱模所需抗压强度的时间逐渐减少,养护时间相比于对比例1缩短了近1/3,在脱模后混凝土预制构件的二氧化碳吸收率可达18.9%,碳化深度达到 2.7mm,这说明混凝预制构件通过本专利进行二氧化碳矿化养护,其效果是显著的。本发明混凝土预制构件的二氧化碳矿化养护方法不仅可以快速地将混凝土表面碳化,提高混凝土早期的表面强度和表面硬度,增强混凝土结构表层的致密性,缩短混
凝土预制构件养护时间,实现混凝土预制构件快速脱模,解决了模板周转率不高的问题;而且利用了大量的钢渣工业固体废弃物和二氧化碳工业废气,是一条实现二氧化碳矿化养护的新技术途径。
[0082]
上述实施例为本发明较佳的实施方式,但本发明的实施方式并不受上述实施例的限制,其他的任何未背离本发明的精神实质与原理下所作的改变、修饰、替代、组合、简化,均应为等效的置换方式,都包含在本发明的保护范围之内。