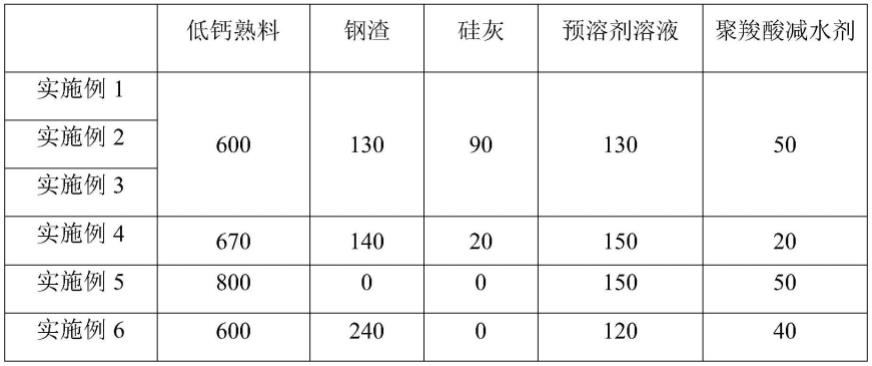
1.本发明属于生态建筑材料技术领域,特别涉及一种二氧化碳驱动硬化的超高性能混凝土及其制备方法。
背景技术:2.超高性能混凝土(uhpc),是近三十年发展起来的最具创新性的水泥基工程材料,超高性能混凝土最大的优势之一在于其具有优良的耐久性和超高的力学性能,现阶段国内外的 uhpc的研究主要应用于桥梁工程、建筑外墙装饰工程等。超高性能混凝土经过20余年的发展已逐步趋向成熟。
3.目前的研究和应用中超高性能混凝土的胶凝材料是普通硅酸盐水泥,辅以超细填料和大量功能性外加剂。水泥生产过程中排放大量co2,对环境造成重要负担。近些年胶凝材料研究领域发展一种新型低钙负碳熟料,与co2反应生成碳酸钙和硅胶。通过短时间碳化养护,可形成优异的力学性能。
4.若能够以新型低钙负碳熟料为胶凝材料制备超高性能混凝土,则将显著降低超高性能混凝土的碳排放,能够获得超高的力学和耐久性能,具备显著的经济效益和社会价值。负碳熟料强度发展离不开co2,一般反应过程是气相co2由外向内扩散,熟料与气相co2反应生成产物以产生强度。混凝土表面和内部的连通孔是气相co2向内扩散的通道。因此,以新型低钙负碳熟料为胶凝材料制备超高性能混凝土的关键难题包括:
5.(1)为获得超高的力学性能,uhpc的孔隙率极低,只有约5%,是普通混凝土的1/4。极低的孔隙率导致气相co2难以向内扩散,熟料无法完成反应导致强度提升困难。
6.(2)超高性能混凝土(uhpc)需要优异的抗折性能,现有方案往往加入钢纤维等。而压力成型条件下,钢纤维的铺装和排布难以实施,导致纤维不能均匀、定向排布,降低超高性能混凝土的抗折强度。
7.因此,急需开发一种以新型低钙负碳熟料为胶凝材料制备超高性能混凝土的材料和制备方法,解决co2驱动下uhpc抗压和抗折强度提升等问题。
技术实现要素:8.针对上述问题,提供一种二氧化碳驱动硬化的超高性能混凝土及其制备方法。降低二氧化碳排放量的同时吸收已有的二氧化碳,实现碳利用。
9.本发明的技术内容如下:
10.一种二氧化碳驱动硬化的超高性能混凝土,按照重量百分比所述超高性能混凝土包括 60-80%低钙负碳熟料、0-30%钢渣粉、0-20%硅灰、10-20%co2预溶剂溶液及0.5-5%减水剂。
11.优选地,所述预溶剂溶液的制备方法为:将含有co2的工业尾气通过设有醇胺水溶液喷淋或喷雾的管道,使所述醇胺水溶液吸收所述尾气中co2,将气相co2转变成稳定的液态。
12.优选地,所述醇胺水溶液为三乙醇胺水溶液、n-甲基二乙醇胺水溶液、二乙醇胺水溶液、 2-氨基-2-甲基-1-丙醇水溶液或乙醇胺水溶液中的一种或两种以上的混合,所述醇胺水溶液中醇胺的质量浓度为10-80%。
13.优选地,所述低钙负碳熟料的主要矿物相为γ-硅酸二钙(γ-c2s)、二硅酸三钙(c3s2)、硅酸一钙(cs)和二硅酸二钙镁(c2ms2);按重量百分比计,熟料中所述四种熟料相之和大于70%。
14.优选地,所述填料包括钢渣粉和硅灰,超细钢渣粉和硅灰的比表面积均大于600m2/kg。
15.优选地,所述减水剂为聚羧酸减水剂。
16.优选地,所述超高性能混凝土的内部包括微米级碳酸钙纤维,纤维直径约2-10微米,纤维长度约5-200微米,长度与直径之比约5-20。
17.所述的超高性能混凝土的制备方法,将co2预溶剂溶液与其他干粉原料混合均匀后,压制成型,然后压力养护。
18.优选地,在10~100mpa的压力下进行压制成型。
19.优选地,压力养护的养护温度为20~60℃,养护湿度范围为50~80%。
20.优选地,碳化养护的co2体积浓度范围为15~99.9%,co2养护压力为0-0.5mpa。
21.本发明的超高性能混凝土的原理及技术优势是:
22.(1)以醇胺溶液预先吸收工业尾气中的co2,将气相co2转化到醇胺溶液中作为拌合水溶液使用。拌合完成后,混凝土内部的熟料与co2的反应开始进行,避免co2无法扩散到内部导致的强度无法提高。
23.(2)醇胺分子修饰产物碳酸钙的形貌,使产物碳酸钙由立方形貌生长为纤维状,纤维直径约2-10微米,纤维长度约5-200微米,长度与直径之比约5-20。使co2驱动硬化的超高性能混凝土内部填充微米级纤维状碳酸钙,替代传统超高性能混凝土的纤维,提升co2驱动硬化的超高性能混凝土的抗折强度。
24.(3)本发明的超高性能混凝土能吸收co2,固碳量约0.15g/g混凝土,显著降低超高性能混凝土的co2排放,具有显著的降碳价值。
附图说明
25.图1为实施例1的产物形貌图。
26.图2为对比例1的产物形貌图。
27.图3为对比例2的产物形貌图。
具体实施方式
28.为了使本发明的目的、技术方案及优点更加清楚明白,以下结合实施例,对本发明进行进一步详细说明。应当理解,此处所描述的具体实施例仅用以解释本发明,并不用于限定本发明。
29.表1和表2分别为以下实施例中所用低钙负碳熟料的化学组成和物相组成。其中,硅酸一钙、二硅酸三钙、二硅酸二钙镁都是碳反应活性物相。
30.表1低钙负碳熟料化学组成(%)
[0031] caosio2al2o3fe2o3mgo其他负碳熟料44.0332.237.196.135.015.41
[0032]
表2低钙负碳熟料的物相组成(%)
[0033] csc3s2c2asc2ms2玻璃相负碳熟料32.334.611.712.98.5
[0034]
以下实施例中所使用的钢渣和硅灰的具体参数为:
[0035]
硅灰的sio2含量大于95%,主要物相是无定型sio2,比表面积约2000m2/kg。
[0036]
超细钢渣粉主要物相是硅酸二钙、铁酸二钙、铁铝酸四钙和玻璃相,四种物相质量百分比之和约80%。比表面积约780m2/kg。
[0037]
表3为实施例1至实施例6的二氧化碳驱动硬化的超高性能混凝土的原料组成与配比。
[0038]
表3 uhpc配比(g)
[0039][0040]
实施例1至实施例3中的原料含量相同,不同之处在于每个实施例中的预溶剂溶液的组成不同,具体不同请参照表4。以预溶co2后,预溶剂溶液质量增加量反映co2预溶量。
[0041]
表4(单位:g)
[0042][0043]
本发明还提供该超高性能混凝土的制备方法,是将co2预溶剂溶液与其他干粉原料混合均匀后,以50mpa的压力下压制成型。成型完成后于99.9%浓度co2,70%相对湿度,25℃, 0.2mpa压力养护。
[0044]
该预溶剂溶液的制备方法为:将含有co2的工业尾气通过设有醇胺水溶液喷淋或喷雾的管道,使所述醇胺水溶液吸收所述尾气中co2,将气相co2转变成稳定的液态。
[0045]
对比例1为去离子水替代预溶剂溶液,其他与实施例1至实施例3相同。
[0046]
对比例2-4分别为实施例1-3中醇胺溶液不预先吸收co2,作为拌合水使用。
[0047]
实施例与对比例得到的超高性能混凝土的力学性能如表5所示。
[0048]
表5 uhpc养护特定龄期下抗压强度(mpa)
[0049][0050]
结合实施例1-3和对比例1,说明co2预溶剂显著提升混凝土的力学性能,抗压强度和抗折强度满足超高性能混凝土标准。
[0051]
结合实施例1-3和对比例2-4,结果说明,不预先吸收co2条件下,虽然醇胺溶液能够提升混凝土的抗压和抗折强度,但是不能满足超高性能混凝土的性能要求。
[0052]
图1-3分别是实施例1、对比例1和对比例2的产物形貌图。结果表明,醇胺溶液存在条件下,产物碳酸钙生长为微米级纤维状。结合实施例1、对比例1和对比例4混凝土抗折强度结果对比,因此微米级纤维状碳酸钙发挥纤维增韧的效果,提升co2驱动硬化超高性能混凝土的抗折强度。
[0053]
上述实施例仅是为了清楚地说明所做的实例,而并非对实施方式的限制。对于所属领域的普通技术人员来说,在上述说明的基础上还可以做出其他不同形式的变化或者变动,这里无需也无法对所有的实施方式予以穷举,因此所引申的显而易见的变化或变动仍处于本发明创造的保护范围之内。